石油装备、油管、套管、抽油机加工工艺流程
采油设备
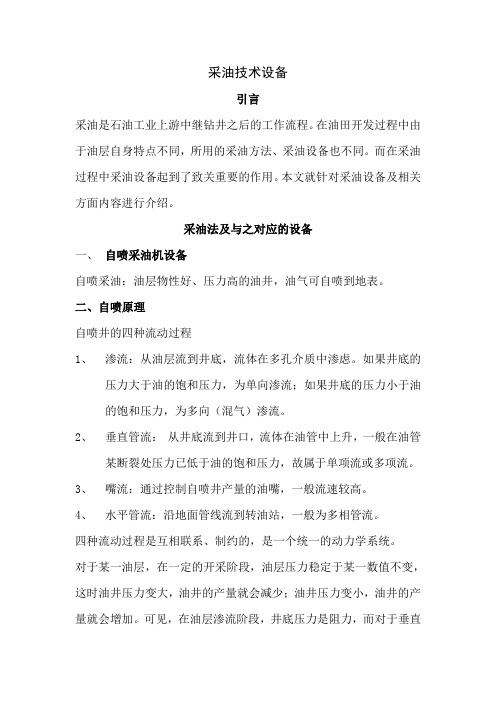
采油技术设备引言采油是石油工业上游中继钻井之后的工作流程。
在油田开发过程中由于油层自身特点不同,所用的采油方法、采油设备也不同。
而在采油过程中采油设备起到了致关重要的作用。
本文就针对采油设备及相关方面内容进行介绍。
采油法及与之对应的设备一、自喷采油机设备自喷采油:油层物性好、压力高的油井,油气可自喷到地表。
二、自喷原理自喷井的四种流动过程1、渗流:从油层流到井底,流体在多孔介质中渗虑。
如果井底的压力大于油的饱和压力,为单向渗流;如果井底的压力小于油的饱和压力,为多向(混气)渗流。
2、垂直管流:从井底流到井口,流体在油管中上升,一般在油管某断裂处压力已低于油的饱和压力,故属于单项流或多项流。
3、嘴流:通过控制自喷井产量的油嘴,一般流速较高。
4、水平管流:沿地面管线流到转油站,一般为多相管流。
四种流动过程是互相联系、制约的,是一个统一的动力学系统。
对于某一油层,在一定的开采阶段,油层压力稳定于某一数值不变,这时油井压力变大,油井的产量就会减少;油井压力变小,油井的产量就会增加。
可见,在油层渗流阶段,井底压力是阻力,而对于垂直管流阶段,井底压力是把油气举出地面的动力。
井口油管压力对于垂直管流是阻力,而对嘴流是动力。
垂直管流中能量的来源与消耗1、单向垂直管流的能量的来源是井底流动压力,能量消耗在克服井深的液柱压力,及液体从井底流到井口过程中垂直管壁之间的摩擦力。
2、多向垂直管流的能量的来源:1、进入井底的液气所具有的压力(流压);2、随同油流进入井底的自由气及举升过程中从油中分离出来的天然气所表现的气体膨胀能,能量消耗:1、气体作用于液体上,垂直的推举液体上升,2、气体与液体之间的摩擦作用,携带液体上升。
三、基本设备1、井口设备(1)套管头:在井口装置的下端,作用连接井内各层套管并密封套管间的环形空间。
(2)油管头:装在套管头的上面,包括油管悬挂器和套管四通。
油管悬挂器作用是悬挂油管管柱,密封油管与油层套管间的环形空间;套管四通作用是正反循环洗井,观察套管压力以及通过油套环形空间进行各项作业。
石油装备、油管、套管、抽油机加工工艺流程

石油装备、油管、套管、抽油机加工工艺流程(1)机械加工机械加工设备主要有车床、钻床、镗铣床、磨床、滚齿机等。
减速箱加工生产工艺流程:根据公司生产计划,进行原材料及外购外协件采购,外购外协件经质量检验合格后入库,原材料经检验入库后,根据生产需要进行加工制造,其成品经检验合格后入库。
所有入库外购外协件、自制成品件出库后转入装配车间,按装配工序进入装配,装配完成经检验合格后入库。
产品零部件、配件机械加工生产工艺流程:根据公司生产计划,进行原材料采购,经质量检验合格后入库,原材料出库后转入机械加工车间,按加工工序进入机床加工,加工完工经检验合格后,入库存放,待发货或者由下道生产环节领用。
图2-1 减速箱生产工艺流程图(2)油套管加工油套管加工包括油套管加工和接箍生产。
油套管生产工艺流程:管材经过漏磁探伤机探伤,合格产品依次经数控管螺纹车床进行机械加工,检验合格备用;接箍坯料由数控管螺纹车床进行螺纹加工,检验后经漏磁探伤机探伤,合格后打标;接下来接箍拧接机将管材与接箍连接,检验合格后用打标机进行打标,经过静水试压机进行压力检测(水压为0~70MPa,管径不同压力不同),测长称重,管两端上保护环,用自动刷漆机在管外壁均匀涂刷环氧沥青防腐漆,后进行喷标,最后成品检验合格后打包,放到产品存放区。
油管、套管生产工艺流程见图2-2。
图2-2 油套管加工工艺流程图(3)抽油机制造主要生产设备为数控切割机、仿形切割机、锯床、组装焊接台架、电焊机等。
抽油机生产工艺流程:根据公司生产计划,进行原材料及外购外协件采购,经质量检验合格后入库,原材料出库后转入机械加工工序,加工完工后,转入铆焊组装工位进行组焊、装配,外购外协件出库后转入组装工序,整机装配完成后整机试机,合格后入库。
工艺流程见图2-3。
图2-3抽油机生产工艺流程图(4)抽油杆制造抽油杆生产工艺流程:①抽油杆圆钢料经检验合格后经矫直机校直、磁粉探伤机探伤、镦锻。
②清洁接头及抽油杆杆体焊接端面,用摩擦焊机进行摩擦焊接。
石油工程技术 井下作业 检泵工序及操作规程
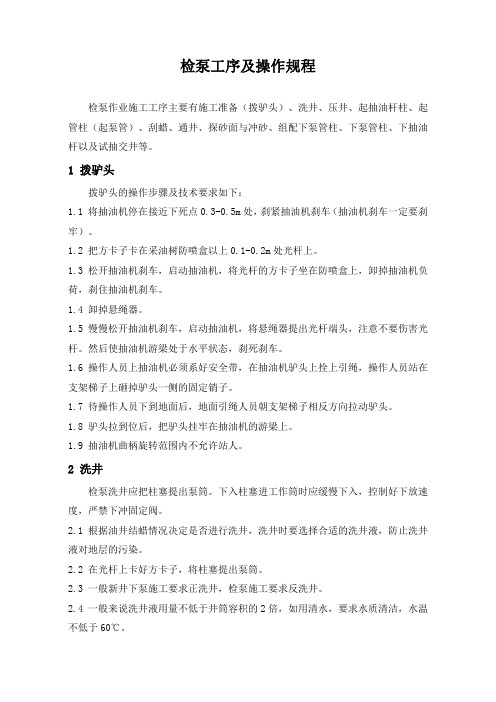
检泵工序及操作规程检泵作业施工工序主要有施工准备(拨驴头)、洗井、压井、起抽油杆柱、起管柱(起泵管)、刮蜡、通井、探砂面与冲砂、组配下泵管柱、下泵管柱、下抽油杆以及试抽交井等。
1拨驴头拨驴头的操作步骤及技术要求如下:1.1将抽油机停在接近下死点0.3-0.5m处,刹紧抽油机刹车(抽油机刹车一定要刹牢)。
1.2把方卡子卡在采油树防喷盒以上0.1-0.2m处光杆上。
1.3松开抽油机刹车,启动抽油机,将光杆的方卡子坐在防喷盒上,卸掉抽油机负荷,刹住抽油机刹车。
1.4卸掉悬绳器。
1.5慢慢松开抽油机刹车,启动抽油机,将悬绳器提出光杆端头,注意不要伤害光杆。
然后使抽油机游梁处于水平状态,刹死刹车。
1.6操作人员上抽油机必须系好安全带,在抽油机驴头上拴上引绳,操作人员站在支架梯子上砸掉驴头一侧的固定销子。
1.7待操作人员下到地面后,地面引绳人员朝支架梯子相反方向拉动驴头。
1.8驴头拉到位后,把驴头挂牢在抽油机的游梁上。
1.9抽油机曲柄旋转范围内不允许站人。
2洗井检泵洗井应把柱塞提出泵筒。
下入柱塞进工作筒时应缓慢下入,控制好下放速度,严禁下冲固定阀。
2.1根据油井结蜡情况决定是否进行洗井,洗井时要选择合适的洗井液,防止洗井液对地层的污染。
2.2在光杆上卡好方卡子,将柱塞提出泵筒。
2.3一般新井下泵施工要求正洗井,检泵施工要求反洗井。
2.4一般来说洗井液用量不低于井筒容积的2倍,如用清水,要求水质清洁,水温不低于60℃。
2.5若用清水洗压井,则应大排量洗井,洗井、压井两周以上,将井筒内的原油及脏物清洗干净,出口进排污系统。
2.6对于漏失严重的井,可采用液氮或二氧化碳混汽水洗井。
3压井检泵井的油层压力都不太大,除少数井油层压力高于静水柱压力外,一般情况下油层压力都低于或等于静水柱压力。
3.1在检泵作业时,必须要注意保护油层,防止油层污染。
3.2在检泵井压井时,对采用的压井液,必须根据油层压力系数和油层深度计算、选择一定密度的压井液,压井液用量为井筒容积的1.5-2倍。
油田工艺流程

主要工艺设施
(2)
污 水 处 理 站 及 系 统 工 程
站内
污水缓冲罐 浮选净化装置 压力滤罐 升压缓冲罐 反冲洗缓冲罐 污油罐 污水回收池 污水泵房 加药间等
站外
污水管道 阀井等
(3)
转 油 放 水 、 污 水 站 及 系 统 工 程
系统主要功能
转油放水系统:
接收站外计量间输来的油、气、 水混合物,在转油放水系统经缓冲、 沉降、加热,分离出的含水油及含水 天热气(湿气)经计量后分别外输至 联合站进行深化处理,含油污水进入污水系统进一步处理。
主要工艺设施
(6)
站内
聚
聚合物母液储罐
合
聚合物母液阀组
物 注
聚合物注入泵
入
聚合物注阀组
站
化验室
及 系
值班室
统
维修间等
工
程
站外
注聚合物井口 配注间 注聚合物管网等
系统主要功能
(7)
供 热 站 及 系 统 工 程
向转油站、联合站供热,在油气集输加工过程中 起供热、保温、拌热和厂房采暖作用,解决大庆地 区采暖期长(全年达6个月)和原油三高(即:高 粘度、高含蜡、高凝固点)采出后的热力补偿。
1 按油田地面产能工程系统功能(单位工程)的不同, 可以划分为集输油、集输气、供热、给排水、变配电、 风净化、外输管网、辅助、联合站、中转站、注水变电 站、油库、道路及其它系统。
如: (1) 中转站及系统工程 (2) 污水处理站及系统工程 (3) 转油放水站及系统工程 (4) 注水变电站及系统工程 (5) 聚合物配置站系统工程 (6) 聚合物注入站及系统工程 (7) 供热站及系统工程 (8) 给、排水及系统工程 (9) 联合站及系统工程 (10) 油库系统工程 (11) 其它系统工程
石油化工行业炼油工艺流程资料

石油化工行业炼油工艺流程资料石油化工行业是世界上最重要的工业之一,其炼油工艺流程是整个石油加工过程中的关键环节。
本文将为您介绍石油炼油工艺的基本流程、常见的工艺方法以及炼油过程中的关键技术。
一、基本流程石油炼油工艺的基本流程可分为原油处理、初级加工、中级加工和深加工四个阶段。
1. 原油处理原油处理是炼油的第一步,旨在除去原油中的杂质,提高原油的质量。
常见的原油处理方法包括沉淀、过滤和加热等。
2. 初级加工初级加工阶段是将原油分割成不同的组分,例如汽油、柴油和润滑油等。
这通常通过蒸馏来完成,根据组分的沸点进行分离。
3. 中级加工中级加工阶段是对初级产品进行进一步的改性和加工,以满足不同类型和等级的需求。
常见的中级加工方法包括裂化、重整和氢化等。
4. 深加工深加工是指对中级产品进行更复杂的化学反应和处理,以生产出高附加值的产品。
例如石化产品、润滑油添加剂和蜡等。
二、常见的工艺方法炼油工艺中常用的方法包括蒸馏、分离、裂化、反应和合成等。
1. 蒸馏蒸馏是根据不同组分的沸点将原油分割成不同的馏分。
这是最基本的分离方法,可将原油分成汽油、柴油和润滑油等馏分。
2. 分离分离是将原油中的各种组分进行分离和提纯。
常见的分离方法包括萃取、吸附和膜分离等。
3. 裂化裂化是将较重的油品转化为较轻的产品,增加汽油产量的方法。
常见的裂化方法有催化裂化和热裂化等。
4. 反应反应是指通过化学反应改变原料的性质,以生产具有特定功能的产品。
例如重整反应可以将低辛烷值的石脑油转化为高辛烷值的汽油。
5. 合成合成是指通过化学合成方法将原料转化为更高价值的产品。
例如合成柴油可以通过合成气转化为合成甲醇,再经过合成过程得到柴油。
三、关键技术在石油炼油过程中,有几个关键技术对于工艺的顺利进行非常重要。
1. 催化技术催化技术是指通过催化剂促进化学反应的进行,提高反应速率和选择性。
常见的催化技术包括催化裂化和催化重整等。
2. 氢化技术氢化技术是将氢气与油品进行反应,以降低硫、氮及其他杂质含量的方法。
采油工艺流程图及各分工艺流程图(精)

管理控制技术要领井口憋压单量(单量车单量1、从井口考克泄完压力,排完残液;2、倒好正确流程;连接好单量输油管线,丝扣不斜,对接严实,不刺不漏;3、检查电缆是否完好无损;4、启动离心泵时是否顺时针转动;5、检查液位计和温度计显示是否有效;6、准确记录单量时间和流量计底数;7、检查加温口温度是否正常;8、单量过程中记准瞬时流量。
1、单量前检查单量设备;2、防止电路或液位计等出现故障而发生溢流等事故;3、电路故障必须由专业电工维修;4、抽油机开抽1小时后计单量数量,单量时间段必须百分之百准确,单量计算数据准确无误;5、各单井每月定期至少完成3次以上的单量;6、做好单量详细记录。
1、蹩压过程中应严格控制井口压力;2、不正常井,根据情况加密憋压次数;3、如果上冲程时油压增高而下冲程时油压稍稳定,或略有下降,说明泵工作正常,油管无渗漏;4、如果蹩压开始时压力上升快,而后缓慢上升、待十多分钟(或更长后压力又上升,甚至达到1兆帕以上时,说明油井是间歇出油:5、如果油压开始上升缓慢,经十多分钟时间油压的数值仍然上升,甚至又回降,则说明油管漏失,油管上部漏失的功图宽于油管下部漏失的功图6、有详细的憋压记录(憋压日期、憋压时间、憋压井号、憋压结果;管理控制1、憋压时选用合适的压力表,并经校验合格;2、采油树各部位不渗不漏,阀门灵活好用;3、憋压时间不少于10min ;4、拆装压力表时操作要缓慢、平稳;5、憋压压力的下限值应高于本井组回压,最高值控制在高于本井组回压2Mpa 以内;6、憋压值不得超过压力表量程的2/3;7、读压力值时,眼睛、指针、刻度成一条垂直于表盘的直线。
日常工作单井录取抽油机井口油、套压1、录取油压(读压力表要使眼睛位于压力表盘正前方,眼睛、指针和刻度线在同意水平位置上;2、检查压力表时放空或卸表要缓慢,特别是放空时要准备放空筒,防止放空时油花四溅。
1、有详细的录取记录(录取日期、井号、油套压值;2、录取的压力值必须在量程1/3-2/3之间,否则要更换量程合适的压力表。
抽油机井热洗工艺流程浅析
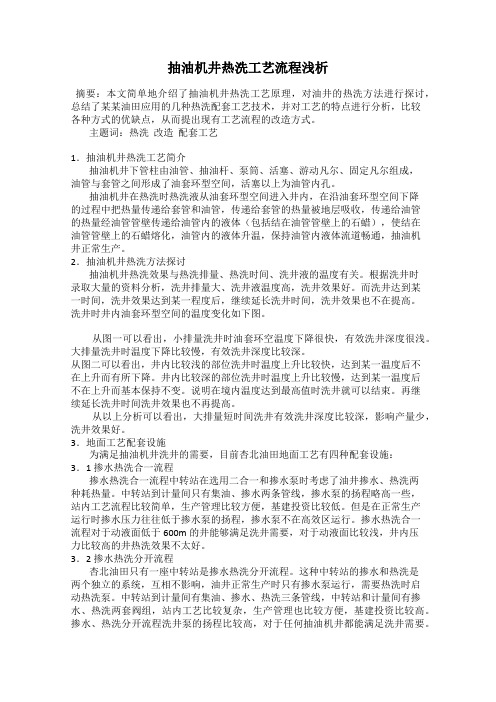
抽油机井热洗工艺流程浅析摘要:本文简单地介绍了抽油机井热洗工艺原理,对油井的热洗方法进行探讨,总结了某某油田应用的几种热洗配套工艺技术,并对工艺的特点进行分析,比较各种方式的优缺点,从而提出现有工艺流程的改造方式。
主题词:热洗改造配套工艺1.抽油机井热洗工艺简介抽油机井下管柱由油管、抽油杆、泵筒、活塞、游动凡尔、固定凡尔组成,油管与套管之间形成了油套环型空间,活塞以上为油管内孔。
抽油机井在热洗时热洗液从油套环型空间进入井内,在沿油套环型空间下降的过程中把热量传递给套管和油管,传递给套管的热量被地层吸收,传递给油管的热量经油管管壁传递给油管内的液体(包括结在油管管壁上的石蜡),使结在油管管壁上的石蜡熔化,油管内的液体升温,保持油管内液体流道畅通,抽油机井正常生产。
2.抽油机井热洗方法探讨抽油机井热洗效果与热洗排量、热洗时间、洗井液的温度有关。
根据洗井时录取大量的资料分析,洗井排量大、洗井液温度高,洗井效果好。
而洗井达到某一时间,洗井效果达到某一程度后,继续延长洗井时间,洗井效果也不在提高。
洗井时井内油套环型空间的温度变化如下图。
从图一可以看出,小排量洗井时油套环空温度下降很快,有效洗井深度很浅。
大排量洗井时温度下降比较慢,有效洗井深度比较深。
从图二可以看出,井内比较浅的部位洗井时温度上升比较快,达到某一温度后不在上升而有所下降。
井内比较深的部位洗井时温度上升比较慢,达到某一温度后不在上升而基本保持不变。
说明在境内温度达到最高值时洗井就可以结束。
再继续延长洗井时间洗井效果也不再提高。
从以上分析可以看出,大排量短时间洗井有效洗井深度比较深,影响产量少,洗井效果好。
3.地面工艺配套设施为满足抽油机井洗井的需要,目前杏北油田地面工艺有四种配套设施:3.1掺水热洗合一流程掺水热洗合一流程中转站在选用二合一和掺水泵时考虑了油井掺水、热洗两种耗热量。
中转站到计量间只有集油、掺水两条管线,掺水泵的扬程略高一些,站内工艺流程比较简单,生产管理比较方便,基建投资比较低。
采油工艺流程图及各分工艺流程图精

管理控制技术要领井口憋压单量(单量车单量1、从井口考克泄完压力,排完残液;2、倒好正确流程;连接好单量输油管线,丝扣不斜,对接严实,不刺不漏;3、检查电缆是否完好无损;4、启动离心泵时是否顺时针转动;5、检查液位计和温度计显示是否有效;6、准确记录单量时间和流量计底数;7、检查加温口温度是否正常;8、单量过程中记准瞬时流量。
1、单量前检查单量设备;2、防止电路或液位计等出现故障而发生溢流等事故;3、电路故障必须由专业电工维修;4、抽油机开抽1小时后计单量数量,单量时间段必须百分之百准确,单量计算数据准确无误;5、各单井每月定期至少完成3次以上的单量;6、做好单量详细记录。
1、蹩压过程中应严格控制井口压力;2、不正常井,根据情况加密憋压次数;3、如果上冲程时油压增高而下冲程时油压稍稳定,或略有下降,说明泵工作正常,油管无渗漏;4、如果蹩压开始时压力上升快,而后缓慢上升、待十多分钟(或更长后压力又上升,甚至达到1兆帕以上时,说明油井是间歇出油:5、如果油压开始上升缓慢,经十多分钟时间油压的数值仍然上升,甚至又回降,则说明油管漏失,油管上部漏失的功图宽于油管下部漏失的功图6、有详细的憋压记录(憋压日期、憋压时间、憋压井号、憋压结果;管理控制1、憋压时选用合适的压力表,并经校验合格;2、采油树各部位不渗不漏,阀门灵活好用;3、憋压时间不少于10min ;4、拆装压力表时操作要缓慢、平稳;5、憋压压力的下限值应高于本井组回压,最高值控制在高于本井组回压2Mpa 以内;6、憋压值不得超过压力表量程的2/3;7、读压力值时,眼睛、指针、刻度成一条垂直于表盘的直线.日常工作单井录取抽油机井口油、套压1、录取油压(读压力表要使眼睛位于压力表盘正前方,眼睛、指针和刻度线在同意水平位置上;2、检查压力表时放空或卸表要缓慢,特别是放空时要准备放空筒,防止放空时油花四溅。
1、有详细的录取记录(录取日期、井号、油套压值;2、录取的压力值必须在量程1/3-2/3之间,否则要更换量程合适的压力表。
- 1、下载文档前请自行甄别文档内容的完整性,平台不提供额外的编辑、内容补充、找答案等附加服务。
- 2、"仅部分预览"的文档,不可在线预览部分如存在完整性等问题,可反馈申请退款(可完整预览的文档不适用该条件!)。
- 3、如文档侵犯您的权益,请联系客服反馈,我们会尽快为您处理(人工客服工作时间:9:00-18:30)。
(1)机械加工
机械加工设备主要有车床、钻床、镗铣床、磨床、滚齿机等。
减速箱加工生产工艺流程:
根据公司生产计划,进行原材料及外购外协件采购,外购外协件经质量检验合格后入库,原材料经检验入库后,根据生产需要进行加工制造,其成品经检验合格后入库。
所有入库外购外协件、自制成品件出库后转入装配车间,按装配工序进入装配,装配完成经检验合格后入库。
产品零部件、配件机械加工生产工艺流程:
根据公司生产计划,进行原材料采购,经质量检验合格后入库,原材料出库后转入机械加工车间,按加工工序进入机床加工,加工完工经检验合格后,入库存放,待发货或者由下道生产环节领用。
生产工艺流程见图2-1
图2-1减速箱生产工艺流程图
(2)油套管加工
油套管加工包括油套管加工和接箍生产。
油套管生产工艺流程:
管材经过漏磁探伤机探伤,合格产品依次经数控管螺纹车床进行
机械加工,检验合格备用;接箍坯料由数控管螺纹车床进行螺纹加工,
检验后经漏磁探伤机探伤,合格后打标;接下来接箍拧接机将管材与接箍连接,检验合格后用打标机进行打标,经过静水试压机进行压力检测(水压为0〜70MPa管径不同压力不同),测长称重,管两端上保护环,用自动刷漆机在管外壁均匀涂刷环氧沥青防腐漆,后进行
喷标,最后成品检验合格后打包,放到产品存放区。
油管、套管生产工艺流程见图2-2。
图2-2油套管加工工艺流程图
(3)抽油机制造
主要生产设备为数控切割机、仿形切割机、锯床、组装焊接台架、电焊机等。
抽油机生产工艺流程:
根据公司生产计划,进行原材料及外购外协件采购,经质量检验合格后入库,原材料出库后转入机械加工工序,加工完工后,转入铆焊组装工位进行组焊、装配,外购外协件出库后转入组装工序,整机装配完成后整机试机,合格后入库。
工艺流程见图2-3
图2-3抽油机生产工艺流程图
(4)抽油杆制造
抽油杆生产工艺流程:
①抽油杆圆钢料经检验合格后经矫直机校直、磁粉探伤机探伤、镦锻。
②清洁接头及抽油杆杆体焊接端面,用摩擦焊机进行摩擦焊接。
摩擦焊机的焊接参数:
一级摩擦压力:2.2MPa,时间10s;
二级摩擦压力:5.5MPa,时间14s;
顶锻压力:10.5MPa
③对焊接部位进行淬火及回火热处理,以消除内应力。
淬火热处理参数:淬火温度900C 士10%加热时间为100s;保温时间
60s ;冷却采用循环水冷却。
回火热处理推荐参数:回火温度625C 士10%加热时间120s; 保温时间180s。
④用校直机对管材进行校直。
⑤用抛丸机清除表面的氧化皮、渣孔后由磁粉探伤机对摩擦焊缝进行探伤;
⑥用数控车床进行杆头加工并装配。
⑦涂刷防腐层进行防腐处理,检验合格包装入库
抽油杆生产工艺流程见图2-4。
杆体检验一>校直一►探伤一►镦锻一>摩擦焊接一►热处理* 热校直
入库一包装—防腐---------------------- 装配——杆头加工 ------------------- 抛丸
图2-4抽油杆生产工艺流程图
(5)连续油管
连续油管工程专用作业设备主体部件主要采用外购或委外加工的方式,本厂区内主要完成零部件检查、零部件组装、整车组装、整车检查及整车试验工序。
具体生产工艺流程见图2-5。
图2-5连续油管工程专用作业设备生产工艺流程图
(6)特种管业
特种管业主要生产玻璃钢复合管和环氧玻璃钢复合管两类复合管,主要用于油田油气地面输送、井下油管等。
1)玻璃钢复合管主要工艺流程
将PVC与着色剂加入混料器中密封混合,送入挤出机,挤出PVC 管。
冷
却后用切割机切割成规定长度。
将切好的PVC t固定在缠绕机上。
称量一定量的聚酯、过氧化甲乙酮,加入搅拌机中搅拌,搅拌均匀后用容器运送到聚酯槽中,玻璃纤维通过聚酯槽,粘上聚酯,然后均匀缠绕到PVC 管上,缠绕到规定的厚度后形成玻璃钢复合管,按要
求切割成规定长度,送至磨锥机打磨锥度,然后人工上端头,后进行翻边、100満水压试验(压力6〜7MPa,检验合格后打包放到产品存放区。
原材料混合PVC管挤出内衬管缠绕切割平端面
磨锥面上端头翻边水压试压打包存放。
2)环氧玻璃钢复合管主要工艺流程称量一定的环氧树脂及固化剂(甲基四氢苯酐)加入到搅拌机中搅拌,搅拌均匀后送至环氧树脂储槽。
玻璃纤维通过环氧树脂储槽使环氧树脂粘在玻璃纤维上,在转动的模具上缠绕到规定的厚度形成玻璃钢管。
向密封的模具管中通入蒸汽使玻璃钢管固化,脱去模具,将玻璃管送至机加工区,用数控车床进行螺纹加工,然后进行100%静
水压试验,合格后打包存放到产品区。
原材料搅拌玻璃纤维缠绕固化、脱模制作内(外)螺纹水压试压
打包存放。
(7)电控制系统钻机、防爆供电及抽油机螺杆泵电控系统的生产流程为首先根据客户需要进行电气及机械系统设计,按照设计要求进行主要电气及机械元件采购,部分元件由厂内机械加工单元进行机械加工制作,然后进行电气装配,装配完成后进行检验及电气调试,合格后交付使用。
钻机、防爆供电及抽油机螺杆泵电控系统的生产流程
电气及机械设计部分机械部件加工元器件采购、制作电气装配检验测试现场调试交付使用。