伺服压力机三角连杆式传动机构的仿真与优化
浅析发动机连杆的仿真分析要点

面的应力σ。
其中(式中r为曲柄半径;n为曲柄转速;为连杆中心距,用标准常用单位。
任意截面应力为截面惯性距为小头横截面积,y、r、w见图1。
连杆大头应力连杆大头应力计算方法与连杆小头的相同,的惯性力比连杆小头的大,要同时考虑连杆产生的往复力和旋转惯性力的作用。
连杆杆身应力性力引起的弯曲应力可忽略不计。
由压缩上止点时的气体压力及排气上止点时的惯性力引起的杆身应力分别为:对连杆杆身进行强度校核时,通常按杆身的双应力幅大小来判断,连杆杆身的双应力幅由下式进行计算:式中F p为气缸最大压力,A s为杆身最小截面积。
2.1.4连杆强度评估判断连杆的设计是否安全,主要依靠大小头典型部位的最大应力及杆身的双应力幅。
各典型部位的许用应力见表。
表中的应力集中处指开孔区或大小头与杆身的过渡区等。
考虑应力集中的许用应力要小的多。
图22.2动态分析连杆疲劳强度分析:①分析输入。
有限元计算相关输入参数如表2所示。
轴瓦、衬套的过盈量以及间隙量如表3所示。
图1图5表2密度(g/cm 3)弹性模量MPa泊松比SCM435SCM4207.877.877.837.857.847.872130002110002190002100002100002110000.2860.2770.2670.270.2780.277轴瓦、衬套的过盈量以及间隙量衬套与连杆直径过盈量衬套与活塞销间隙轴瓦与连杆直径过盈量轴瓦与曲轴间隙0.032-0.085mm 0.005-0.011mm 0.04-0.082mm 0.026-0.042mm连杆有限元疲劳强度分析由螺栓预紧力工况、装配工最大爆发压力工况、惯性力工况组成,通过各工况计算结果判定连杆是否满足静强度要求,通过工况联合得到连杆的平均应力及应力幅值,用FAMFAT 软件求解连杆的判断连杆是否满足疲劳特性。
连杆分析模型包括连杆体、连杆盖、连杆螺栓、轴瓦、算时间,只对1/2分析模型进行有限元分析即可。
图3④边界条件处理。
三角肘杆式伺服压力机传动机构的仿真与优化

6
4
作 为 实 际 的 工 程 问 题 ,设 计 变 量 的 取 值 范 围会 受 到 一 系 列 的 约 束 和 限 制 ,为 了 降 低 优 化 设 计 的 复
2 O O
杂 度 , 些 优 化 目标 也 转 换 成 了 约 束 条 件 , 些 约 束 某 这
G, 一
30 o 34 1 56 8
33 6
() a 网野公司的肘杆传动机
下肘杆
驱动杆
表 2
铰链 点
各铰 链 点的初 始位置值
坐 标值 / mm
三角
y
A
B C
-0 50
- 0 5 0 - 0 3 0 0 - 0 5 0 - 6 3 3 - 6 3 3 - 6 3 3 O
90 0 mm , 块 行 程 均 设 定 为 5 0 滑 0 mm 。 计 算 出 两 种 机
构 各 连 杆 铰 链 间 的 长 度 尺 寸 如 表 1所 示 。 为 了 方 便 进 行 运 动 分 析 计 算 , 立 一 笛 卡 尔 坐 标 系 , 标 原 点 设 坐 分 别 设 在 铰 链 点 , 图 2 ) D( 2 处 。 则 各 铰 链 ( a和 图 b)
G
力 和 一 定 的保 压 时 问 。
日 ,
3
虚 拟 样 机 模 型
分 析 采 用 机 械 系 统 仿 真 分 析 软 件 MS . C ADAMS, 方 便 研 究 上 述 连 杆 机 构 的 运 动 和 动 力 学 为
特 性 , 将 图 1中 左 右 完 全 对 称 的 机 构 取 半 边 机 构 简
l 2 3 4 5 6
条 件 函数可 表示 为 :
基于SolidWorks的连杆机构的运动分析与仿真
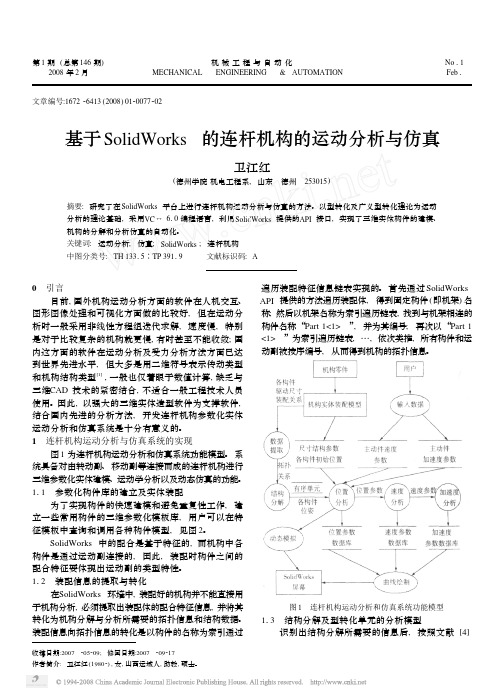
第1期(总第146期)2008年2月机械工程与自动化MECHANICAL ENGINEERING & AUTOMATION No 11Feb 1文章编号:167226413(2008)0120077202基于SolidWorks 的连杆机构的运动分析与仿真卫江红(德州学院机电工程系,山东 德州 253015)摘要:研究了在SolidWorks 平台上进行连杆机构运动分析与仿真的方法。
以型转化及广义型转化理论为运动分析的理论基础,采用VC ++610编程语言,利用SolidWorks 提供的API 接口,实现了三维实体构件的建模、机构的分解和分析仿真的自动化。
关键词:运动分析;仿真;SolidWorks ;连杆机构中图分类号:TH 13315∶TP 39119 文献标识码:A收稿日期:2007205209;修回日期:2007209217作者简介:卫江红(19802),女,山西运城人,助教,硕士。
0 引言目前,国外机构运动分析方面的软件在人机交互、图形图像处理和可视化方面做的比较好,但在运动分析时一般采用非线性方程组迭代求解,速度慢,特别是对于比较复杂的机构就更慢,有时甚至不能收敛;国内这方面的软件在运动分析及受力分析方法方面已达到世界先进水平,但大多是用二维符号表示传动类型和机构结构类型[1],一般也仅着眼于数值计算,缺乏与三维CAD 技术的紧密结合,不适合一般工程技术人员使用。
因此,以强大的三维实体造型软件为支撑软件,结合国内先进的分析方法,开发连杆机构参数化实体运动分析和仿真系统是十分有意义的。
1 连杆机构运动分析与仿真系统的实现图1为连杆机构运动分析和仿真系统功能模型。
系统具备对由转动副、移动副等连接而成的连杆机构进行三维参数化实体建模、运动学分析以及动态仿真的功能。
111 参数化构件库的建立及实体装配为了实现构件的快速建模和避免重复性工作,建立一些常用构件的三维参数化模板库,用户可以在特征模板中查询和调用各种构件模型,见图2。
伺服压力机传动机构有限元分析

大 尺 寸 4 mm, 图 1所 示 。所 受 载 荷 除 机 身 作 用 力 0 如 外 , 曲柄 输 入 扭 矩 T作 用 下 , 公 称 力 点 位 置 滑 块 在 在
上 输 出 力 为 4 0 k 因 此 , 块 加 载 反 作 用 力 F为 0 0 N, 滑
力机 为例 , 完 成其传 动机构 结构件设 计基 础上 , 在 利 用 UG高 级 仿 真 模 块 ,对 其 整 体 结 构 进 行 静 力 学 有
情 况 即可 。 因此 , 先 按 其 装 配 结 构 和 运 动 关 系 , 首 完
高 级 仿 真 模 块 是 一 个 集 成 化 、全 相 关 、直 观 易 用 的
C AE 工 具 , 设 计 过 程 中 可 进 行 快 速 的 有 限 元 前 处 在
成该 传动机 构装 配 , 后 进行 有限元分 析前处 理 。 然 有
优 化 , 仅 可 大 幅度 降 低 伺 服 电机 功 率 , 可 提 高 传 不 还 动 效 率 、 加 机 构 承 载 能 力 。 因此 , 为 解 决 伺 服 压 增 成
力 机 研 发 中关 键 技 术 问 题 的有 效 途 径 之 一 J 。
运 动 特 性 在 机 身 导 轨 内做 上 下 往 复 直 线 运 动 并 输 出
中 图 分 类 号 :H121 T 1.
1 前 言
文 献 标 识 码 : A
中 曲 柄 和 上 圆柱 销 与 机 身 相 连 ,滑 块 在 机 身 轨 道 内
伺服 压力机具 有智 能化 、 能 、 效 、 柔 性 、 节 高 高 高 精 度 、 噪环保等诸 多优点 , 现代 锻压 机床 的发展 低 是
件 所 受 应 力 介 于 8 MP ~ 2 MP 0 a 1 0 a之 间且 分 布 均 匀 , 计 满 足 要 求 ; 于 所 设 计 的 异 型连 杆 , 支 撑 臂 中 空 转 设 对 在 角部 位 应 力 高 达 3 0 a 应 力 集 中 引起 ) 5 MP ( 以上 , 增 大 圆 角 进 行 改 进 。 拟 关键 词 : 械 制 造 ; 动机 构 ; 服 压 力机 ; 限 元 机 传 伺 有
伺服压力机三角肘杆传动机构的优化设计

伺服压力机三角肘杆传动机构的优化设计近年来,伺服压力机在工业生产中得到了广泛应用,它具有结构简单、运行稳定、控制精度高等优点。
而三角肘杆传动机构作为伺服压力机的核心部件,对其性能和效率有着重要影响。
因此,对伺服压力机三角肘杆传动机构进行优化设计,提高其传动效率和运行稳定性,具有重要意义。
为了优化伺服压力机三角肘杆传动机构的设计,我们需要对其工作原理进行深入了解。
三角肘杆传动机构主要由驱动轴、驱动杆、从动杆和连接杆组成。
驱动轴通过齿轮传动将驱动力传递给驱动杆,驱动杆通过连接杆将力传递给从动杆,从而实现伺服压力机的工作。
在进行优化设计时,我们需要考虑以下几个方面。
首先是传动效率的提高。
为了减少能量的损失,我们可以选择高质量的齿轮和轴承,减少传动链条的摩擦和磨损。
此外,合理选择传动比例,使驱动力和负载力达到最佳匹配,减少传动过程中的能量损失。
其次是运行稳定性的提高。
在伺服压力机工作中,传动机构的稳定性对其性能有着重要影响。
为了提高运行稳定性,我们可以通过优化传动链条的设计,减少杆件的摆动和变形。
可以选择合适的材料和制造工艺,提高杆件的刚度和强度,减少传动过程中的振动和噪音。
还需要考虑机构的紧凑性和结构的可靠性。
传动机构的紧凑性对于整个伺服压力机的设计和布局有着重要影响。
通过合理的布局和设计,减少传动机构的体积和空间占用,提高整个系统的工作效率。
同时,还需要考虑杆件的连接方式和结构的可靠性,确保传动机构在长时间工作中不会出现松动和断裂等问题。
优化设计伺服压力机三角肘杆传动机构是提高伺服压力机性能和效率的关键。
通过合理选择材料、优化设计传动比例、减少能量损失和振动等措施,可以提高传动效率和运行稳定性,使伺服压力机在工业生产中发挥更大的作用。
在实际应用中,我们还需要根据具体情况进行优化设计。
不同的伺服压力机在应用场景和工作要求上可能存在差异,因此需要根据实际需求进行相应的设计和调整。
同时,还需要考虑成本和制造工艺等因素,确保优化设计的可行性和经济效益。
机构创新设计论文:连杆机构创新设计的建模与仿真
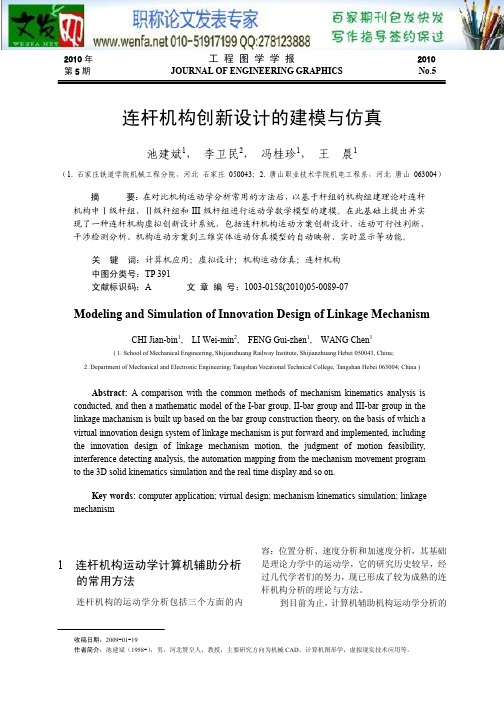
Modeling and Simulation of Innovation Design of Linkage Mechanism
CHI Jian-bin1, LI Wei-min2, FENG Gui-zhen1, WANG Chen1
( 1. School of Mechanical Engineering, Shijianzhuang Railway Institute, Shijianzhuang Hebei 050043, China; 2. Department of Mechanical and Electronic Engineering; Tangshan Vocational Technical College, Tangshan Hebei 063004; China )
第5期
池建斌等:连杆机构创新设计的建模与仿真
·91·
是由四个构件六个低副组成的杆组,称之为 III 级组或 IV 级组……而在基本杆组中又以 II 级和 III 级基本杆组为常见。根据 II 级组中低副的不 同形式是转动副(Revolute-Pair,常用 R 表示) 还是移动副(Prismatic-Pair,常用 P 表示)和它 们所在的不同位置又分成不同的类型。 机构的运动分析可以从 I 级机构开始,通过 逐次求解各基本杆组来完成。这样,把 I 级机构 和各类基本杆组看成各自独立的单元,分别建立 其运动分析的数学模型,然后再编制成通用子程 序,对其位置、速度及加速度和角速度、角加速 度等运动参数进行求解。当对具体机构进行运动 分析时,可以通过调用原动件和机构中所需的基 本杆组的通用子程序来解决,这样,可快速求解 出各杆件及其上各点的运动参数。对各种不同类 型的平面连杆机构都适用杆组法来进行运动分 析[17-18]。 基于杆组的机构组建理论可将连杆机构组 建为Ⅰ级杆组、 Ⅱ级杆组(RRR、 RRP、 RPR、 RPP、 PRP) 和 III 级 杆 组 (RR-RR-RR 、 RR-RR-RP 、 RR-PR-RP)。限于篇幅,以下以 II 级杆组 PRP 为 例说明其数学模型的建立。 2.2 PRP 杆组运动分析模型 由两个构件,两个外移动副和一个内回转副 所组成的 PRPII 级杆组如图 1 所示。已知两杆长
《锻压装备与制造技术》2011年总目次

伺服驱动液压机浅析
30k 0 0 N板材充液成形液压机可靠性分析
李 贵闪(— 7 6 1)
何景 晖(— 9 6 1)
4 /0 55 MN快锻油压机本体结构设计分析 范玉林 , (— 4 等 42 ) 折弯机参数 化建模及优化 肘杆式伺服压力机 的运动分析 潘志华 , (— 6 等 42 ) 朱新武 , (— 9 等 42 )
综 述
浅谈数控节能复合型伺服 压力 机研 发 胡亚 民, 19 等( - ) 潘 品李 , (— 3 等 1 1) 胡 亚民 , (— 1 等 2 1) 多工位压力机在汽车 冲压 生产 中的应用 J2— 3 G 1 6 A开式 压力机机身设计与分析 三辊横轧机轧辊箱 改造设 计
我 国摆 动辗压技术现状及 展望 ( ) 一 大型核 电主管道 制造 技术 的发展 我 国摆动辗压技 术现状及展望 ( ) 二
一
胡明杰 , 12 ) 等(—5
一
1M 0 N万 吨摩擦螺旋压力机研 究开发 0
庄 云霞 , 32 ) 等(—5
杨 静 , 32 ) 等(— 7 俊 , 33 ) 等( — 1
种用 于制 造活性炭棒料 的专 用四柱液压机
武新柱 , 1 2 ) 等( — 9
种用 于汽车 u型梁切割的激光机器人系统
D vcnt eiee 现场总线在压力机 中的应用
我 国锻压机 械行 业现状概况
我 国锻压行业近况及前景 浅析
刘 振堂( — ) 4 9
于晓红 (— 4 5 1)
邓玉 山, (— 4 等 24 ) 秦 剑(— 7 24 )
断 电保护式压力 机用安全控制双联 阀
荣 防 ( — 0 6 1)
全 国塑性 工程理事换届大会 、 国塑性工程学 术年会暨第 四 全 届全球华 人塑性加工技术研讨会在重庆 召开 2 1 上海 中国国际金属成形 展览会举 办 01 (— ) 4 2 (— ) 44
伺服压力机三角连杆式传动机构的仿真与优化

字 化控 制系 统 , 使 滑块 在运 行 过程 中 , 可 自 由
控 制加 速 、 减速 、 停 止 等动作 。 除此之 外 , 伺 服
压力机还拥有高精度 、 低 噪声 、 低能耗等特点7 2 7 。
现 有 的伺 服 压 力 机 传 动 形 式 有 螺 杆 式 、 连 杆
的加工 工艺 , 目前 的 传 动 方 式 存 在 各 种 缺 陷 和 不 足 , 所 以 需 要 对 现 有 的 传 动 机 构 进 行 优 化 , 以 满 足 成 形 T 艺 的要 求 。本 文 主 要 针 对 一 种 三 角 连 杆 式 的 传 动 机构 , 对 其进 行动 态仿 真 和结构 优化 , 得 到能 满足 特
构 简单 、 载 荷 放 大 效 果 好 等 特 点 。但 是 , 由于其采 用 速 一 定 的情 况 不 能 满足 某些 文 作 者 提 出一 肘 杆 之 间 的 直 机 构 , 即 将 原
位 于 下 死 点 的 位 置 , 两 种 机 构 的 行 程 均 设 定 为
5 0 0 mm, 机 构高 度 均 为 9 0 0 mm。 在 两 个 机 构 中 选 择 点 0、 0 设 置 为 原 点 建 立 笛 卡 尔 坐 标 系 ,计 算 出 各 铰 链 点 的 初 始 坐 标 如 表 1所 示 ,各 连 杆 初 始 长 度 如
中图分 类号 : T G3 1 5 . 5
0 引言
文献标 识码 : A
近 年 来 ,伺 服 压 力 机 在 制 造 业 得 到 了 越 来 越 多 的 发 展 与 应 用 。 由 于 取 消 了 飞 轮 和 离
合器, 伺 服压力 机在 结 构上 更 加简 洁 ; 在 性 能 上, 与传统 机 械压力 机 相 比 , 伺 服 压 力 机 不 仅 具有 高柔 性 、 高速 度 、 高效率 的特点 l I 1 , 而 且 由
- 1、下载文档前请自行甄别文档内容的完整性,平台不提供额外的编辑、内容补充、找答案等附加服务。
- 2、"仅部分预览"的文档,不可在线预览部分如存在完整性等问题,可反馈申请退款(可完整预览的文档不适用该条件!)。
- 3、如文档侵犯您的权益,请联系客服反馈,我们会尽快为您处理(人工客服工作时间:9:00-18:30)。
伺服压力机三角连杆式传动机构的仿真与优化第一章:绪论1.1 研究背景和意义1.2 国内外研究现状及发展趋势1.3 研究目的和内容1.4 研究方法和流程第二章:伺服压力机三角连杆式传动机构的设计原理和参数选取2.1 传动机构的功能和要求2.2 三角连杆式传动机构的工作原理2.3 参数选取和计算方法2.4 传动机构模型的建立第三章:传动机构的仿真分析3.1 仿真分析的目的和意义3.2 传动机构的动力学分析3.3 传动机构的运动仿真3.4 仿真结果的分析与评价第四章:传动机构的优化设计4.1 优化设计的目的和原则4.2 变量的选取和范围确定4.3 优化算法的选择和设计4.4 优化结果的分析与比较第五章:结论和展望5.1 主要研究工作总结5.2 研究成果和贡献5.3 不足和展望5.4 建议和未来研究方向第一章:绪论1.1 研究背景和意义伺服压力机是一种广泛应用于金属加工、塑料加工、锻压和冲压等领域的机械设备,其压力传递和动力转换等核心部件的性能和可靠性对整个设备的工作效率和工艺质量都具有重大影响。
传动机构作为伺服压力机重要的组成部分,直接关系到其动力传递的高效性和精度,因此对传动机构进行仿真和优化设计研究具有重要的科学意义和工程实践价值。
1.2 国内外研究现状及发展趋势三角连杆式传动机构是一种常用的传动方式,在伺服压力机、数控机床等高精度设备中得到了广泛的应用。
目前,国内外对三角连杆式传动机构的研究已经有了较为深入的探讨,针对其动力学、运动学、强度等方面进行了众多的仿真和实验研究。
同时,传动机构优化设计方面,智能算法和多目标优化方法也逐渐引起了人们的关注和重视。
因此,当前的研究趋势就是更加深入地研究三角连杆式传动机构的特性和性能,并结合智能算法和优化设计方法进行优化设计。
1.3 研究目的和内容本文旨在对伺服压力机三角连杆式传动机构进行仿真分析和优化设计,通过建立仿真模型和实施优化设计,增进对传动机构结构特性和性能的认识,从而提高伺服压力机的工作效率和精度。
主要研究内容如下:(1)分析传动机构的结构和工作原理,确定传动机构模型和参数选取方法。
(2)建立传动机构的仿真模型,并进行动力学分析和运动仿真,评价传动机构的性能。
(3)采用智能算法和多目标优化方法对传动机构进行优化设计,分析和比较不同优化结果的优缺点。
1.4 研究方法和流程本文主要采用仿真分析和优化设计相结合的方法,具体流程如下:(1)确定传动机构的结构和参数选取方法,建立仿真模型,并进行动力学分析和运动仿真。
(2)获取仿真数据,分析评价传动机构的特性和性能,并对传动机构进行初步优化设计。
(3)采用智能算法和多目标优化方法对传动机构进行进一步的优化设计和分析,比较不同优化结果的优缺点,得出优化结论。
(4)根据优化结论,对传动机构进行一定的改进和优化,并进行仿真验证。
第二章:伺服压力机三角连杆式传动机构的设计原理和参数选取2.1 传动机构的功能和要求伺服压力机三角连杆式传动机构是一种将电机的旋转运动转化为拉力或压力的机构,其作用是控制压实过程中的压力和速度,从而实现对压制件的成型和生产质量的控制。
传动机构的主要功能包括:传递电机输出的扭矩和速度,转化电机的旋转运动为杆的直线运动,实现伺服控制和快速响应等。
传动机构的要求主要包括两方面:一方面是转化效率高、能量损失小,即要求传动机构的动力学特性和结构设计具有高效性和节能性;另一方面是传动精度高,可靠性强,即要求传动机构的结构设计和材料选择能够提高传动精度和传动稳定性,且其使用寿命要长,维护方便。
2.2 三角连杆式传动机构的工作原理伺服压力机三角连杆式传动机构是一种采用三根杆件相连的机构,其中两个杆的一端与电动机输出轴相连,另一个杆的一端与油缸相连。
其工作原理如下:电动机通过输出轴旋转产生转矩和速度,经过多段三角连杆的转换和输出,使油缸的柱塞内液体产生高压和大力,实现对工件的加工或成型。
其中,三角连杆式传动机构的关键点在于杆的长度和角度设计的合理性,因为唯有在两杆之间传递力和矩的方向完全相反、大小平衡,运动完全一致的情况下,才能实现传动的高效化和稳定性。
2.3 参数选取和计算方法在三角连杆式传动机构的参数选取和计算方法方面,通常需要考虑以下几个方面:(1)选取传动机构的结构形式和连接方式,一般可采用主从动体、等速、等角或等长连杆等形式,从而实现直接、间接等多种传动方式。
(2)根据传动机构的要求和工作条件,确定传动比和传动方式,一般可采用链传动、带传动或齿轮传动等方式。
(3)根据杆的长度和连接角度的设计要求,选取合适的杆件,一般可采用不锈钢、工程塑料或碳纤维等材料。
(4)采用动力学理论和运动学分析方法计算传动机构的运动学参数和动力学参数,包括速比、位置比、角加速度、质量中心等。
2.4 传动机构模型的建立伺服压力机三角连杆式传动机构的建模是建立仿真模型的基础,也是进行仿真分析和优化设计的关键点。
在模型建立过程中,需要明确机构的结构形式和参数选取方法,然后针对其动力学、运动学和强度等特性进行建模和分析。
因此,在进行传动机构模型建立时,需要考虑以下几方面:(1)选取适合的建模软件,一般可以采用Solidworks、Pro/E等常用的三维设计软件或Virtual Lab等虚拟仿真软件。
(2)根据伺服压力机的实际工作要求和传动机构的参数选取,建立传动机构的三维模型,包括杆件、连接件、支撑件等组成部分。
(3)采用动力学方法对传动机构的运动学参数和动力学参数进行计算和分析,从而验证模型的合理性和可靠性。
(4)在模拟分析时,需考虑传动机构的工作环境和负载变化等实际条件,进行有限元分析和动力学仿真,以评价传动机构的特性和性能。
第三章:传动机构的仿真分析3.1 仿真分析的目的和意义仿真分析是传动机构设计和优化的重要手段,通过建立仿真模型和运行仿真,可以对传动机构的运动规律和特性进行评价和分析,为机构的优化设计提供科学依据。
3.2 传动机构的动力学分析在进行传动机构的动力学分析时,需要考虑以下几方面:(1)杆件的运动学参数,如位置、速度和加速度等。
(2)传动机构的动力学参数,如角加速度、质量和惯性等。
(3)传动机构的应力分析,考虑负载变化的情况下机构杆件受到的应力和变形等。
3.3 传动机构的运动仿真传动机构的运动仿真是通过将伺服压力机的传动机构模型转化为仿真模型,再进行运动仿真分析的过程。
在进行仿真时,需要考虑传动精度、运动平稳性,以及整个传动系统的稳定性和可靠性等要素。
3.4 仿真结果的分析与评价通过对仿真结果的分析和评价,可以评判传动机构的特性和性能,为传动机构的优化设计提供依据。
仿真结果的评价主要包括传动效率、运动精度、传动稳定性和杆件应力等方面,并综合分析,得出传动机构的优化改进方案。
第四章:传动机构的优化设计4.1 优化设计的原理和目标传动机构的优化设计是为了提高其性能,实现传动效率的最大化和传动精度的最优化。
其中,优化设计的原理和目标如下:(1)结合实际工作环境和负载变化情况,通过改进传动机构的结构设计和参数选取,实现传动效率的最大化。
(2)通过调整传动机构的结构参数和优化设计方法,提高传动精度和传动稳定性,并降低能耗和振动等不良影响。
(3)采用合理的设计和制造工艺,保证传动机构的使用寿命和维护性能,提高伺服压力机的工作效率和工艺质量。
4.2 优化设计的方法和步骤在进行传动机构的优化设计时,一般采用智能算法和多目标优化方法。
其具体步骤如下:(1)建立传动机构的数学模型,包括运动学和动力学方程,并确定优化目标和约束条件。
(2)采用智能算法和多目标优化方法,对设计变量进行优化设计。
(3)分析比较不同优化结果的优缺点,确定最终的优化方案。
(4)采用优化方案进行传动机构的优化改进和仿真分析,验证优化效果的可行性和有效性。
4.3 优化设计方法的比较和应用在对传动机构进行优化设计时,常用的方法主要有如下几种:遗传算法、粒子群优化算法、蚁群算法等。
(1)遗传算法是一种基于生物遗传进化原理的优化算法,其优点在于可以全局搜索并对多个目标进行优化设计,缺点在于收敛速度较慢。
(2)粒子群优化算法是一种基于粒子群模拟行为的优化算法,其优点在于具有全局搜索和局部搜索能力,缺点在于容易陷入局部最优解。
(3)蚁群算法是一种基于蚁群行为的优化算法,其优点在于具有全局搜索能力和自适应能力,缺点在于计算复杂度较高。
在应用优化设计方法时,需要结合传动机构的特性和优化目标进行选取,比较不同方法的适用性和效果,并结合实际情况进行调整和改进。
第五章:传动机构的仿真验证5.1 仿真验证的目的和意义传动机构的仿真验证是指通过对仿真模型的运行仿真和实验验证,评价传动机构的性能和可靠性,并判断其优化改进效果的可行性和有效性。
因此,仿真验证的目的是为了确保传动机构的设计和优化满足实际要求和工作环境,并提供优化改进的科学基础。
5.2 仿真验证的步骤和方法在进行传动机构的仿真验证时,需要采用仿真模型进行模拟分析,并对仿真结果进行实验验证。
具体步骤如下:(1)根据传动机构的优化设计方案和参数选取,建立仿真模型,并进行动力学分析和运动仿真。
(2)获取仿真数据,并分析评价传动机构的特性和性能,包括传动效率、运动精度、传动稳定性等。
(3)根据仿真结果,进行传动机构的改进和优化,并进行仿真验证。
(4)通过实验测试和仿真对比,分析和评价传动机构的优化改进效果,并探讨其将来的发展趋势和应用前景。
5.3 仿真验证的实验方法和结果分析在进行传动机构的仿真验证时,需要采用适当的实验方法和测量技术进行验证。
一般可采用光电编码器、位移传感器等测量装置和数控机床等实验设备,以对传动机构进行实验验证和性能评价。
验证结果分析主要包括以下几方面:(1)传动机构的运动行程、速度和加速度等参数,是否符合仿真分析的预期效果。
(2)传动机构的传动效率、运动精度、传动稳定性等性能参数,是否得到有效提高和优化改进。
(3)传动机构的负载承载能力、杆件应力和变形情况等安全性评价,是否满足实际工作需求。
5.4 仿真验证的结论和展望通过对传动机构的仿真验证,可以得出以下结论:(1)传动机构的优化设计和改进能够有效提高传动效率、运动精度和传动稳定性,同时降低能耗和振动等不良影响。
(2)采用智能算。