苯-甲苯式精馏塔工艺设计
苯与甲苯的精馏塔设计
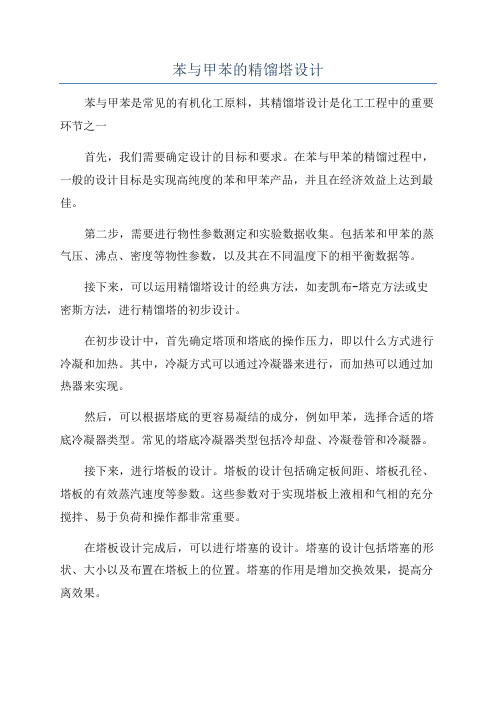
苯与甲苯的精馏塔设计苯与甲苯是常见的有机化工原料,其精馏塔设计是化工工程中的重要环节之一首先,我们需要确定设计的目标和要求。
在苯与甲苯的精馏过程中,一般的设计目标是实现高纯度的苯和甲苯产品,并且在经济效益上达到最佳。
第二步,需要进行物性参数测定和实验数据收集。
包括苯和甲苯的蒸气压、沸点、密度等物性参数,以及其在不同温度下的相平衡数据等。
接下来,可以运用精馏塔设计的经典方法,如麦凯布-塔克方法或史密斯方法,进行精馏塔的初步设计。
在初步设计中,首先确定塔顶和塔底的操作压力,即以什么方式进行冷凝和加热。
其中,冷凝方式可以通过冷凝器来进行,而加热可以通过加热器来实现。
然后,可以根据塔底的更容易凝结的成分,例如甲苯,选择合适的塔底冷凝器类型。
常见的塔底冷凝器类型包括冷却盘、冷凝卷管和冷凝器。
接下来,进行塔板的设计。
塔板的设计包括确定板间距、塔板孔径、塔板的有效蒸汽速度等参数。
这些参数对于实现塔板上液相和气相的充分搅拌、易于负荷和操作都非常重要。
在塔板设计完成后,可以进行塔塞的设计。
塔塞的设计包括塔塞的形状、大小以及布置在塔板上的位置。
塔塞的作用是增加交换效果,提高分离效果。
在塔板和塔塞设计完成后,可以进行填料的设计。
填料的设计包括填料的材料选择、填料的形状和尺寸。
填料的作用是增加表面积,提高蒸馏效率。
最后,进行精馏塔的热力学计算和模拟。
可以通过现有的化工流程模拟软件,如Aspen Plus,对精馏塔进行热力学计算和性能预测。
这可以帮助我们更好地了解在不同操作条件下,塔的性能如何,以及它能否满足设计要求。
总结起来,苯与甲苯的精馏塔设计是一项复杂且精细的工程,需要综合考虑物性参数、操作要求和经济效益等因素。
通过前期的物性参数测定和实验数据收集,结合经典的精馏塔设计方法和现代化工流程模拟软件的应用,可以设计出高效、可靠的精馏塔。
化工原理课程设计苯与甲苯精馏塔

化工原理课程设计苯与甲苯精馏塔本文将针对化工原理课程设计,探讨苯与甲苯精馏塔的工艺设计。
一、工艺流程苯与甲苯精馏塔的工艺流程如下:苯与甲苯混合物在进入塔后,首先通过反应塔抽收制冷剂进行冷却,从而达到冷却效果,然后通过塔顶进入预分离器进行处理,将其中的气相成分与液相成分分离,剩余的液相通过进料口进入塔体,反复上升和下降,与上部的气相进行平衡沸腾,不断提高纯度,最后在顶部凝结出高纯度的甲苯。
二、设计考虑因素1.塔型塔型应根据生产规模和成本考虑。
一般而言,小型的塔型适合处理小流量、高品质的混合物,而大型的塔型则适合处理大流量、低品质的混合物。
2.动力学参数在设计苯与甲苯精馏塔时,要考虑动力学参数,如液相和气相的流速、物料的热量传递效应等等。
这些参数将直接影响塔的效率和产品品质。
3.填料和操作条件由于苯与甲苯混合物具有一定的粘度和密度差异,因此应在填料和操作条件上进行制约,以避免不同成分之间发生混合或分离出现问题。
三、设计基础1.填料设计填料是苯与甲苯精馏塔的重要组成部分,是决定塔效率和塔高的关键因素。
填料材料应具有良好的性能,如高效的传质、良好的气体液体接触、稳定的抗攻击性等等。
常见的填料材料有氧化铝、陶瓷、合金等。
2.除塔器设计除塔器是苯与甲苯精馏塔的一个重要设计组成部分。
它的主要作用是在塔底处收集返回的液相,防止溢出和保持塔内的可控性。
除塔器的设计应根据填料类型、流量、操作温度和压力等多个因素进行综合考虑,以确保塔的正常运行。
3.塔底设计塔底是苯与甲苯精馏塔的重要组成部分,主要用于收集精馏出的液态产品。
由于反应塔存在高温、高压等因素,因此需要考虑塔底的材料和设计。
常见的材料有碳钢、不锈钢、合金等。
此外,塔底还应配备可靠的排放和泄压装置,以确保塔的安全性。
四、结论苯与甲苯精馏塔是一种常见的化工装置,其设计应考虑多种因素,如塔型、填料、动力学参数等等。
从而确保塔的高效、稳定和可靠性。
苯甲苯精馏塔设计
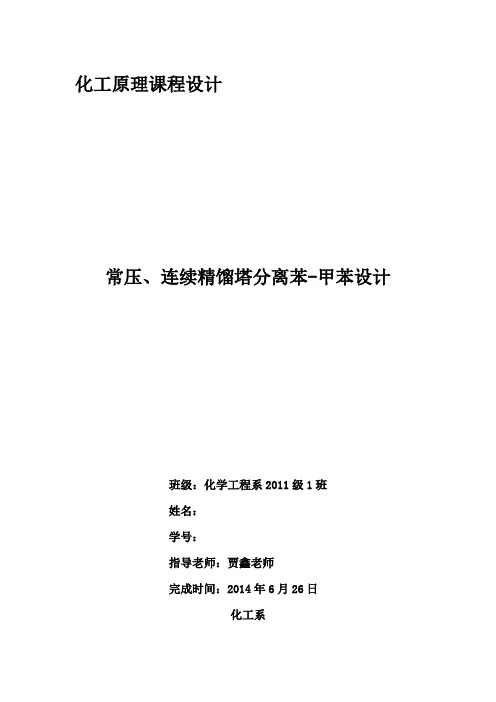
化工原理课程设计常压、连续精馏塔分离苯-甲苯设计班级:化学工程系2011级1班姓名:学号:指导老师:贾鑫老师完成时间:2014年6月26日化工系常压、连续精馏塔分离苯-甲苯设计一、前言1.1设计任务及条件:泡点进料(q=1),塔顶进入全凝器,塔釜间接蒸汽加热,塔板压降:(0.5-0.7)KPa1.2物系用途及性质(1)苯的性质:摩尔质量78.11g/mol,密度0.8786 g/mL,相对蒸气密度(空气=1):2.77,蒸汽压(26.1℃):13.33kPa,临界压力:4.92MPa,熔点278.65 K (5.51 ℃),沸点353.25 K (80.1 ℃),在水中的溶解度 0.18 g/ 100 ml 水,标准摩尔熵So(298.15K):173.26 J/mol·K,标准摩尔热容 Cpo:135.69 J/mol·K (298.15 K),闪点 -10.11℃(闭杯),自燃温度 562.22℃,结构:平面六边形,最小点火能:0.20mJ,爆炸上限(体积分数):8%,爆炸下限(体积分数):1.2%,燃烧热:3264.4kJ/mol,溶解性:微溶于水,可与乙醇、乙醚、乙酸、汽油、丙酮、四氯化碳和二硫化碳等有机溶剂互溶。
它有机化合物,是组成结构最简单的芳香烃,在常温下为一种无色、有甜味的透明液体,并具有强烈的芳香气味。
苯可燃,有毒。
苯难溶于水,易溶于有机溶剂,本身也可作为有机溶剂。
苯是一种石油化工基本原料。
苯的产量和生产的技术水平是一个国家石油化工发展水平的标志之一。
苯具有的环系叫苯环,是最简单的芳环。
(2)苯在工业上的用途:苯是工业上一种常用溶剂,主要用于金属脱脂。
苯有减轻爆震的作用而能作为汽油添加剂。
苯在工业上最重要的用途是做化工原料。
苯可以合成一系列苯的衍生物:苯与乙烯生成乙苯,后者可以用来生产制塑料的苯乙烯与丙烯生成乙丙烯,后者可以经乙丙苯法莱生产丙酮与制树脂和粘合剂的苯酚,制尼龙的环己烷,合成顺丁烯二酸酐,用于制作苯胺的硝基苯,用于农药的各种氯苯,合成用于生产洗涤剂和添加剂的各种烷基苯,合成氢醌、蒽醌等化工产品。
精馏塔课程设计--苯-甲苯板式精馏塔的工艺设计

第一章绪论1.1精馏的特点与分类精馏是分离液体混合物的典型单元操作。
它是通过加热造成气液两相物系,利利用物系中各组分挥发度的不同的特性来实现分离的。
按精馏方式分为简单精馏、平衡精馏、精馏和特殊精馏。
1.1.1蒸馏分离具有以下特点(1)通过蒸馏分离,可以直接获得所需要的产品。
(2)适用范围广,可分离液态、气态或固态混合物。
(3)蒸馏过程适用于各种浓度混合物的分离。
(4)蒸馏操作耗能较大,节能是个值得重视的问题。
1.1.2平衡蒸馏将混合液在压力p1下加热,然后通过减压阀使压力降低至p2后进入分离器。
过热液体混合物在分离器中部分汽化,将平衡的气、液两相分别从分离器的顶部、底部引出,即实现了混合液的初步分离。
1.1.3简单蒸馏原料液在蒸馏釜中通过间接加热使之部分汽化,产生的蒸气进入冷凝器中冷凝,冷凝液作为馏出液产品排入接受器中。
在一批操作中,馏出液可分段收集,以得到不同组成的馏出液。
1.1.4连续精馏操作流程化工生产以连续精馏为主。
操作时,原料液连续地加入精馏塔内,连续地从再沸器取出部分液体作为塔底产品(称为釜残液);部分液体被汽化,产生上升蒸气,依次通过各层塔板。
塔顶蒸气进入冷凝器被全部冷凝,将部分冷凝液用泵(或借重力作用)送回塔顶作为回流液体,其余部分作为塔顶产品(称为馏出液)采出。
1-精馏塔 2-全凝器3-储槽 4-冷却器5-回流液泵 6-再沸器 7-原料液预热器图1连续精馏装置示意图1.2精馏塔的踏板分类1.2.1塔板的结构形式1.泡罩塔板泡罩塔板是工业上应用最早的塔板,它由升气管与泡罩构成。
泡罩安装在升气管的顶部,分圆形和条形两种,以前者使用较广。
泡罩有φ80mm、φ100mm和φ150mm三种尺寸,可根据塔径大小选择。
泡罩下部周边开有很多齿缝,齿缝一般为三角形、矩形或梯形。
泡罩在塔板上为正三角形排列。
它的优点是操作弹性适中塔板不易堵塞。
缺点是生产能力与板效率较低结构复杂、造价高。
图2泡罩塔板(a)操作示意图 (b)塔板平面图 (c)圆形泡罩2.筛孔塔板筛孔塔板简称筛板,其结构特点是在塔板上开有许多均匀小孔,孔径一般为3~8mm。
苯甲苯精馏塔设计
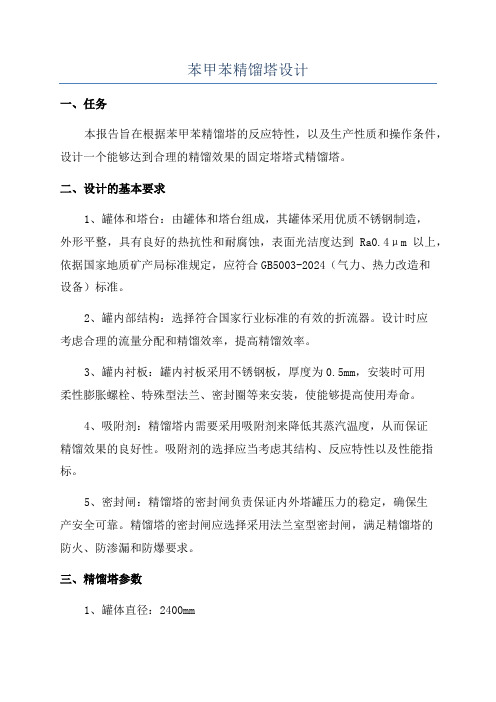
苯甲苯精馏塔设计
一、任务
本报告旨在根据苯甲苯精馏塔的反应特性,以及生产性质和操作条件,设计一个能够达到合理的精馏效果的固定塔塔式精馏塔。
二、设计的基本要求
1、罐体和塔台:由罐体和塔台组成,其罐体采用优质不锈钢制造,
外形平整,具有良好的热抗性和耐腐蚀,表面光洁度达到Ra0.4μm以上,依据国家地质矿产局标准规定,应符合GB5003-2024(气力、热力改造和
设备)标准。
2、罐内部结构:选择符合国家行业标准的有效的折流器。
设计时应
考虑合理的流量分配和精馏效率,提高精馏效率。
3、罐内衬板:罐内衬板采用不锈钢板,厚度为0.5mm,安装时可用
柔性膨胀螺栓、特殊型法兰、密封圈等来安装,使能够提高使用寿命。
4、吸附剂:精馏塔内需要采用吸附剂来降低其蒸汽温度,从而保证
精馏效果的良好性。
吸附剂的选择应当考虑其结构、反应特性以及性能指标。
5、密封闸:精馏塔的密封闸负责保证内外塔罐压力的稳定,确保生
产安全可靠。
精馏塔的密封闸应选择采用法兰室型密封闸,满足精馏塔的
防火、防渗漏和防爆要求。
三、精馏塔参数
1、罐体直径:2400mm
2、罐体长度:8400mm
3、塔底压力:2MPa。
苯和甲苯精馏塔课程设计
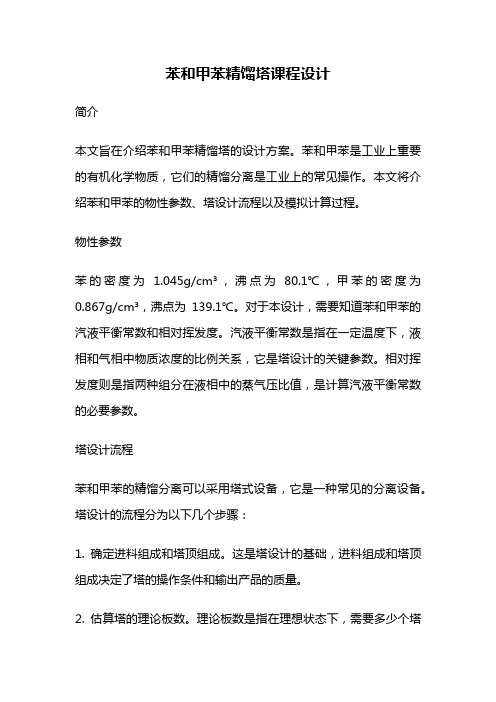
苯和甲苯精馏塔课程设计简介本文旨在介绍苯和甲苯精馏塔的设计方案。
苯和甲苯是工业上重要的有机化学物质,它们的精馏分离是工业上的常见操作。
本文将介绍苯和甲苯的物性参数、塔设计流程以及模拟计算过程。
物性参数苯的密度为 1.045g/cm³,沸点为80.1℃,甲苯的密度为0.867g/cm³,沸点为139.1℃。
对于本设计,需要知道苯和甲苯的汽液平衡常数和相对挥发度。
汽液平衡常数是指在一定温度下,液相和气相中物质浓度的比例关系,它是塔设计的关键参数。
相对挥发度则是指两种组分在液相中的蒸气压比值,是计算汽液平衡常数的必要参数。
塔设计流程苯和甲苯的精馏分离可以采用塔式设备,它是一种常见的分离设备。
塔设计的流程分为以下几个步骤:1. 确定进料组成和塔顶组成。
这是塔设计的基础,进料组成和塔顶组成决定了塔的操作条件和输出产品的质量。
2. 估算塔的理论板数。
理论板数是指在理想状态下,需要多少个塔板才能完成分离。
估算理论板数是塔设计的关键步骤,它涉及物性参数和操作条件。
3. 选择填料类型和填料高度。
填料是塔内部的一种结构,它能够增加液相和气相之间的接触面积,从而增加精馏效率。
填料的选择和高度决定了塔的性能。
4. 确定塔的尺寸。
塔的尺寸包括直径、高度和塔板间距等参数。
这些参数是根据填料类型、操作条件和理论板数等因素来确定的。
5. 进行塔的模拟计算。
模拟计算是为了验证前面步骤中的估算和选择是否正确。
模拟计算可以通过计算机程序或实验来进行。
模拟计算苯和甲苯的精馏塔设计需要进行模拟计算,以验证前面步骤中的估算和选择是否正确。
模拟计算可以通过计算机程序或实验来进行。
在计算机程序中,可以采用化工流程模拟软件来进行塔设计。
这些软件可以模拟塔的运行过程,包括传热、传质和反应等过程。
通过这些软件,可以得到塔的操作条件和输出结果。
在实验中,可以采用塔的模型进行实验。
塔的模型是一种缩小的实验装置,它可以模拟塔的运行过程。
化工原理课程设计苯与甲苯精馏塔

化工原理课程设计:苯与甲苯精馏塔简介本文主要探讨化工原理课程设计中的苯与甲苯精馏塔。
通过对苯和甲苯进行精馏分离,我们可以获得纯度较高的苯和甲苯产品。
在本文中,我们将从以下几个方面展开讨论:1.背景和目的2.设计流程3.塔设计4.精馏原理5.实验操作6.结果和讨论背景和目的苯和甲苯是常用的工业化学品,广泛应用于加工、涂料、塑料等行业。
苯和甲苯在某些工艺中需要纯度较高,因此需要进行精馏分离。
本课程设计旨在设计一个能有效分离苯和甲苯的精馏塔。
设计流程为了设计一个合适的苯与甲苯精馏塔,我们需要进行以下几个步骤:1.确定原料2.确定塔的类型和结构3.进行塔的热力学计算4.进行实验验证塔设计塔是精馏过程中最关键的组件之一,它可以通过蒸汽冷凝回收馏分。
在苯和甲苯的精馏中,一般采用板式塔。
塔类型在板式塔中,我们可以选择不同的塔类型,如:•始料塔•落料塔•浓差塔•强化塔塔结构塔的结构包括:1.塔筒:用于装载填料或板2.助塔装置:用于改善塔内气液分布精馏原理精馏是利用不同物质的沸点差异进行分离的过程。
在苯与甲苯的精馏过程中,由于苯和甲苯的沸点差异较大,可以有效地进行分离。
实验操作进行苯与甲苯精馏的实验时,我们需要注意以下几个操作步骤:1.准备好实验所需设备和试剂2.开启冷却水,确保设备冷却3.将苯和甲苯加入精馏塔中4.开启加热源,控制温度5.收集馏出的苯和甲苯样品结果和讨论通过实验操作,我们可以得到苯和甲苯的纯度和收率。
根据实验结果,我们可以评估精馏塔的效果,并对塔的设计进行改进。
在进行课程设计时,我们要求学生深入了解苯与甲苯的精馏原理,并通过实验进行验证。
此外,在设计塔的结构和操作过程时,也需要考虑到实际工业生产的要求。
通过本次课程设计,学生不仅能够更好地理解化工原理,还能够培养实验操作和实际问题解决能力。
这对于他们将来的工作和研究具有重要意义。
总结起来,本文对苯与甲苯精馏塔的设计和实验操作进行了详细的讨论。
从背景和目的到实验结果和讨论,我们提供了一个全面的指导,希望能对读者有所帮助。
苯和甲苯精馏塔课程设计
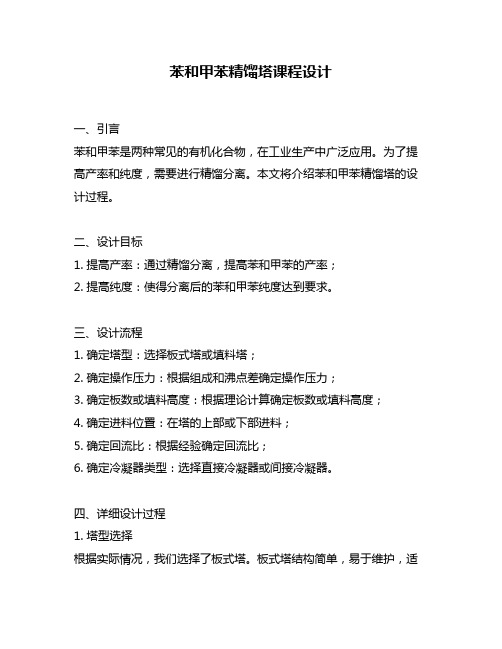
苯和甲苯精馏塔课程设计一、引言苯和甲苯是两种常见的有机化合物,在工业生产中广泛应用。
为了提高产率和纯度,需要进行精馏分离。
本文将介绍苯和甲苯精馏塔的设计过程。
二、设计目标1. 提高产率:通过精馏分离,提高苯和甲苯的产率;2. 提高纯度:使得分离后的苯和甲苯纯度达到要求。
三、设计流程1. 确定塔型:选择板式塔或填料塔;2. 确定操作压力:根据组成和沸点差确定操作压力;3. 确定板数或填料高度:根据理论计算确定板数或填料高度;4. 确定进料位置:在塔的上部或下部进料;5. 确定回流比:根据经验确定回流比;6. 确定冷凝器类型:选择直接冷凝器或间接冷凝器。
四、详细设计过程1. 塔型选择根据实际情况,我们选择了板式塔。
板式塔结构简单,易于维护,适用于小规模生产。
2. 操作压力确定根据苯和甲苯的沸点差,我们确定了操作压力为1 atm。
3. 板数或填料高度确定根据理论计算,我们确定了塔的板数为10个。
每个板的高度为0.5 m。
4. 进料位置确定我们选择在塔的下部进料,以便更好地控制进料速度和分离效果。
5. 回流比确定根据经验,我们选择回流比为2:1。
6. 冷凝器类型选择考虑到成本和维护难度,我们选择了直接冷凝器。
五、设计结果通过以上设计过程,我们得到了苯和甲苯精馏塔的具体参数:1. 塔型:板式塔;2. 操作压力:1 atm;3. 板数:10个;4. 进料位置:下部进料;5. 回流比:2:1;6. 冷凝器类型:直接冷凝器。
六、结论通过本次课程设计,我们成功地设计出了苯和甲苯精馏塔,并得到了具体的参数。
在实际生产中,需要根据实际情况进行调整和优化。
- 1、下载文档前请自行甄别文档内容的完整性,平台不提供额外的编辑、内容补充、找答案等附加服务。
- 2、"仅部分预览"的文档,不可在线预览部分如存在完整性等问题,可反馈申请退款(可完整预览的文档不适用该条件!)。
- 3、如文档侵犯您的权益,请联系客服反馈,我们会尽快为您处理(人工客服工作时间:9:00-18:30)。
一序言化工原理课程设计是综合运用《化工原理》课程和有关先修课程(《物理化学》,《化工制图》等)所学知识,完成一个单元设备设计为主的一次性实践教学,是理论联系实际的桥梁,在整个教学中起着培养学生能力的重要作用。
通过课程设计,要求更加熟悉工程设计的基本内容,掌握化工单元操作设计的主要程序及方法,锻炼和提高学生综合运用理论知识和技能的能力,问题分析能力,思考问题能力,计算能力等。
精馏是分离液体混合物(含可液化的气体混合物)最常用的一种单元操作,在化工,炼油,石油化工等工业中得到广泛应用。
精馏过程在能量剂驱动下(有时加质量剂),使气液两相多次直接接触和分离,利用液相混合物中各组分的挥发度的不同,使易挥发组分由液相向气相转移,难挥发组分由气相向液相转移,实现原料混合液中各组分的分离。
根据生产上的不同要求,精馏操作可以是连续的或间歇的,有些特殊的物系还可采用衡沸精馏或萃取精馏等特殊方法进行分离。
本设计的题目是苯-甲苯连续精馏筛板塔的设计,即需设计一个精馏塔用来分离易挥发的苯和不易挥发的甲苯,采用连续操作方式,需设计一板式塔将其分离。
第二章设计任务书一、设计题目苯-甲苯连续精馏筛板塔的设计。
二、设计任务(1)原料液中苯含量:质量分率:w F=35%(质量),其余为甲苯。
(2)塔顶产品中苯含量:w D=95%。
(3)釜底苯含量:w D=8.5%。
(4)生产能力:20000t/a,年工作日300天。
三、操作条件(1)精馏塔顶压强:101.13kPa(常压) (2)进料热状态:泡点进料(3)回流比:R=1.3Rmin (4)单板压降压:0.7kPa四、设计内容及要求(1)设计方案的确定及流程说明(2)塔的工艺计算(3)塔和塔板主要工艺尺寸的设计塔高、塔径以及塔板结构尺寸的确定;塔板的流体力学验算;塔板的负荷性能图。
(4)编制设计结果概要或设计一览表(5)辅助设备选型与计算(6)绘制塔设备结构图:采用绘图纸徒手绘制五、参考书目[1]王志奎、刘丽英、刘伟化工原理(第四版)下册•北京:化学工业出版社,2012.7[2]化工原理课程设计书第三章设计内容3.1 设计方案的确定及工艺流程的说明本设计任务为分离苯-甲苯混合物。
对于该二元混合物的分离,应采用连续精馏过程。
设计中采用泡点进料,将原料液通过预热器加热至泡点后送入精馏塔内。
塔顶上升蒸汽采用全凝器冷凝,冷凝液在泡点下一部分回流至塔内,其余部分经产品冷却器冷却后送至储罐。
该物系属易分离物系,最小回流比较小,故操作回流比取最小回流比的2倍。
塔釜采用间接蒸汽加热,塔底产品经冷却后送至储罐。
3.2 全塔的物料衡算3.2.1原料液及塔顶底产品含苯的摩尔分率苯和甲苯的相对摩尔质量分别为78.11 kg/kmol和92.14kg/kmol,原料含苯的质量百分率为35%,塔顶苯含量不低于95 %,塔底苯含量不大于0.05%,则:原料液含苯的摩尔分率:0.35/78.110.3880.35/78.110.65/92.14Fx==+塔顶含苯的摩尔分率:0.95/78.110.9960.95/78.110.05/92.14Dx==+塔底含苯的摩尔分率:0.05/78.110.05850.05/78.110.95/92.14Wx==+3.2.2原料液及塔顶底产品的平均摩尔质量由3.1.1知产品中甲苯的摩尔分率,故可计算出产品的平均摩尔质量:原料液的平均摩尔质量:M F=78.11×0.388+(1-0.388)×92.14=860696kg/kmol塔顶液的平均摩尔质量:M D =78.11×0.957+(1-0.957)×92.14=78.712kg/kmol塔底液的平均摩尔质量:M W=78.11×0.0585+(1-0.0585)×92.14=91.291kg/kmol3.2.3料液及塔顶底产品的摩尔流率依题给条件:一年以300天,一天以24小时计,得:F ,=20000t/(300×24)h =2777.78kg/h ,全塔物料衡算:进料液: F=2777.78(kg/h )/86.696(kg/kmol )=32.04kmol/h 总物料恒算: F=D+W苯物料恒算: F×0.388=D×0.957+W ×32.040 联立解得: W =9.640kmol/hD =22.400kmol/h3.3 塔板数的确定理论塔板数T N 的求取苯-甲苯物系属理想物系,可用梯级图解法(M·T),求取N T ,步骤如下: 3.3.1平衡曲线的绘制根据苯-甲苯的相平衡数据,利用泡点方程和露点方程求取。
依据 , 将所得计算结果如列表2:表2苯(x )-甲苯(y )的相平衡数据本方案中,塔内压力接近常压(实际上略高于常压),因操作压力偏离常压很小,所以其对x~y 平衡关系的影响完全可以忽略。
将上表中数据作图得x~y 曲线:()()oo o B A B t p p p p x --=/tA p x p y /o =3.3.2操作回流比的确定表3 苯--甲苯物系在某些温度t 下的a 值(附x 值)可见随着温度的升高,α变化不大,可对表中两端数据取平均值2.60 2.56 2.53 2.49 2.46 2.43 2.40 2.37 2.35/9 2.466α=++++++++=()在y-x 图上,因1=q ,查得660.0e =y ,而q 0.388F x x ==,0.957D x =。
故由式(3-53a )得最小回流比:也可根据课本中公式(10-45)得,考虑到精馏段操作线离平衡线较近,取实际操作的回流比为最小回流比的1.2倍,即: R=1.3R min =1.3*1.522=2.018精馏塔的汽、液相负荷:精馏段:液相流量:L=RD=2.018×22.4=45.203kmol/h气相流量:V=(R+1)D=(2.018+1)×22.4=67.603kmol/h提镏段:液相流量:L ′=L+F=45.203+35.040=77.243kmol/h气相流量:V ′=V=67.603kmol/h3.3.3理论塔板数的确定精馏段操作线为: 1+n y =11+++R x x R R D n =0.669n x +0.317平衡方程:x 11x y )(-+=αα提馏段操作线可由b(x W ,x W )及精馏段操作线和q 线的交点d 决定。
min 0.9570.6111.5520.6110.388D e e e x y R y x --===--】)(【FD F D min x 1x 1x x 11R ----=αα泡点加料时q=1 F RD qF L L +=+=' (1) D R F q V V )1()1('+=-+= (2) 对全塔物料横算 D+W=F (3) D D x +W W x =F F x (4) 由(1)、(2)式得0.3380.05850.3670.9570.0585F W D W x x D F x x --===-- (5) FD R x F D x x F D R R F D D R Dx Fx x D R F RD V W x x V L y DF m DF m w m m)1()1(1)1()1(''''1+--++=+--++=-=+ (6)将(5)式值带入(6)中得提留段操作线为 '1 1.570.0332m m y x +=-将x=0.389代入精馏段操作线,求得y=0.5772,即有d(0.389,0.5772)。
(1)精馏段利用平衡方程和精馏段操作线方程计算精馏段的塔板数:110.9570.900D y x x ==−−−→=相平衡;220.9200.823y x =−−→=; 330.8680.727y x =−−→=; 440.8040.625y x =−−→=; 550.7350.529y x =−−→=; 660.6710.453y x =−−→=; 770.6200.398y x =−−→=;880.5830.362y x =−−→=0.389f x <=.故精馏板为7块,第8块为进料板以下交替使用提馏线操作线方程语相平衡方程得:990.5350.318y x =−−→=;10100.4660.193y x =−−→=; 11110.2700.130y x =−−→=. 12120.1710.077y x =−−→=;13130.0880.038y x =−−→=0.0585W x <=..因此,理论板数为13层,进料位置为第8层板。
苯--甲苯在某些温度下的粘度:μ=Σx i μi =0.388*0.284+0.612*0.291=0.2883mPa.s) μ表示以加料摩尔组成为准的液体的平均摩尔粘度。
可以简单的用以下近似公式计算塔的总效率: E=0.17-0.616lg (μm )=0.50274精馏段的实际板数为:7140.5N ==精 (层) 取14(层)提馏段的实际板数为:5100.5N ==提(层) 取10(层) 实际是在第15块塔板进料的。
3.4 塔的精馏段操作工艺条件及计算3.4.1平均压强p m塔顶压强: 取每层塔板的压降0.7KPa进料板: 塔底压强:W F P P 250.7125.1kPa =+⨯=平均压强: 3.4.2平均温度t m依据操作压力,由泡点方程通过试差法,计算出泡点温度,其中苯、 甲苯的饱和蒸()kPa 4.1172/1.1257.109=+=m p F P 101.30.714112.5kPa =+⨯=kPa 3.101P =D汽压由安托尼方程计算,计算结果如下:塔顶温度: t D =81.0℃ 进料板温度: t F =94.1℃。
平均温度:t m ()81.094.1/287.55=+=℃3.5 塔的提馏段操作工艺条件及计算3.5.1平均压强p m平均压强: 3.5.2平均温度t m依据操作压力,由泡点方程通过试差法,计算出泡点温度,其中苯、 甲苯的饱和蒸汽压由安托尼方程计算,计算结果如下:塔底温度: t D =108.1℃ 进料板下一块温度: t F =96.5℃。
平均温度:t m ()96.5+108.1/2102.3==℃3.5.3平均分子量m M塔顶: 10.957D y x ==,10.900x =(),0.95778.1110.95792.1478.713g/kmol VD m M =⨯+-⨯= (),0.90078.1110.90092.1479.513kg/kmol LD m M =⨯+-⨯=加料板:0.577F y =,0.388F x =(),0.57778.1110.57792.1484.045kg/kmol VF m M =⨯+-⨯= (),0.38878.1110.38892.1486.696kg/kmol LF m M =⨯+-⨯=精馏段:(),78.71384.045/283.103kg/kmol V m M =+=(),79.51386.696/283.103kg/kmol L mM =+=提顶: 80.535y =,80.318x =(),0.53578.1110.53592.1384.63g/kmol VD m M =⨯+-⨯= (),0.31878.1110.31892.1492.13kg/kmol LD m M =⨯+-⨯=釜底:130.088y =,130.038x ==108.8kPa m p(),0.08878.1110.08892.1390.90kg/kmol VF m M =⨯+-⨯= (),0.03878.1110.03892.1491.60kg/kmol LF m M =⨯+-⨯=提馏段:(),84.6390.90/287.77kg/kmol V m M =+=(),87.6791.60/289.67kg/kmol L mM =+=4.3.2平均密度计算 (4)平均密度计算 ①气相平均密度计算由理想气体状态方程计算,精馏段的平均气相密度即,3,106.981.8792.928.314(273.1587.55)m v m v m mP M kg m RT ρ⨯===⨯+提馏段的平均气相密度,'3,108.887.773.068.314(273.15102.3)m v m v m mP M kg m RT ρ⨯===⨯+②液相平均密度计算液相平均密度依下式计算,即塔顶液相平均密度的计算 由t D =87.55℃,查手册得 33812.78,808.2A B kg m kg m ρρ== 进料板液相平均密度的计算0.36278.110.330.36278.1192.130.638A α⨯==⨯+⨯,,10.33793.80.67791.83L Dm L Dm kg kmol ρρ=+=塔底液相平均密度的计算 由t w =102.3℃,查手册得 33706.8,799.9A B kg m kg m ρρ==塔底液相的质量分率0.31878.110.060.31878.1192.130.682A α⨯==⨯+⨯,,10.28/706.80.72/799.9,799.0L wm L wm kg kmol ρρ=+=提馏段液相平均密度为,790.3799.0794.652L m kg kmol ρ+==精馏段液相平均密度为',813.0791.83802.42L m kg kmol ρ+==(5) 液体平均表面张力计算液相平均表面张力依下式计算,即塔顶液相平均表面张力的计算σLDm=0.95×21.40+(1-0.95)×21.46=21.4 mN/m 进料板液相平均表面张力的计算σLFm=0.362×18.8+0.638×20.6=19.95 mN/m 塔底液相平均表面张力的计算σLwm=0.088×17.44+0.912×18.23=18.16mN/m 精馏段液相平均表面张力为σLm=(20.98+19.86)/2=20.42 mN/m 提馏段液相平均表面张力为σ‘Lm=(21.4+19.95)/2=20.68 mN/m (6) 液体平均粘度计算液相平均粘度依下式计算,即 lg μLm=Σxi lg μi塔顶液相平均粘度的计算lg μLDm=0.957×lg(0.300)+ (1-0.95)×lg(0.304) 解出μLDm=0.304 mPa ·s 进料板液相平均粘度的计算 由tF =94.2℃,查手册得μA=0.269 mPa ·s μB=0.277 mPa ·slg μLFm=0.409×lg(0.269)+ (1-0.409)×lg(0.277) 解出μLFm=0.262 mPa ·s 塔底液相平均粘度的计算 由tw =105.1℃,查手册得μA=0.244 mPa ·s μB=0.213 mPa ·slg μLwm=0.07×lg(0.244)+ (1-0.07)×lg(0.213) 解出μLwm=0.260 mPa ·s 精馏段液相平均粘度为μLm=(0.304+0.272)/2=0.283 mPa ·s 提馏段液相平均粘度为μ‘Lm=(0.272+0.260)/2=0.266 mPa ·s(7) 气液负荷计算 精馏段:()1(2.0181)22.4067.60/V R D Kmol h =+=+⨯=367.6080.8791.606/360036002.92Vm S vm V M V m s ρ⨯⨯===⨯2.01822.4045.20/L RD Kmol h ==⨯=345.2083.1030.0013/36003600802.4Lm Lm LM Ls m s ρ⨯===⨯30.00133600 4.68/h L m h =⨯=提馏段:'(1)67.60/V V q F Kmol h =+-='367.6089.670.54/36003600 3.06Vm S vm V M V m s ρ⨯⨯===⨯'45.20132.0477.24/L L qF Kmol h =+=+⨯='377.2489.670.0024/36003600794.65Lm Lm LM Ls m s ρ⨯===⨯'30.002436008.72/h L m h =⨯=5 精馏塔的塔体工艺尺寸计算(1) 塔径的计算塔板间距H T 的选定很重要,它与塔高、塔径、物系性质、分离效率、塔的操作弹性,以及塔的安装、检修等都有关。