铸造铝合金的熔炼
铸造铝合金的熔炼工艺
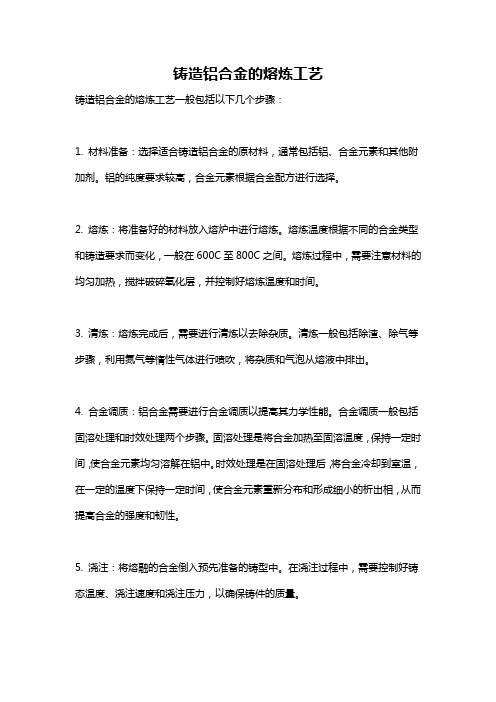
铸造铝合金的熔炼工艺
铸造铝合金的熔炼工艺一般包括以下几个步骤:
1. 材料准备:选择适合铸造铝合金的原材料,通常包括铝、合金元素和其他附加剂。
铝的纯度要求较高,合金元素根据合金配方进行选择。
2. 熔炼:将准备好的材料放入熔炉中进行熔炼。
熔炼温度根据不同的合金类型和铸造要求而变化,一般在600C至800C之间。
熔炼过程中,需要注意材料的均匀加热,搅拌破碎氧化层,并控制好熔炼温度和时间。
3. 清炼:熔炼完成后,需要进行清炼以去除杂质。
清炼一般包括除渣、除气等步骤,利用氮气等惰性气体进行喷吹,将杂质和气泡从熔液中排出。
4. 合金调质:铝合金需要进行合金调质以提高其力学性能。
合金调质一般包括固溶处理和时效处理两个步骤。
固溶处理是将合金加热至固溶温度,保持一定时间,使合金元素均匀溶解在铝中。
时效处理是在固溶处理后,将合金冷却到室温,在一定的温度下保持一定时间,使合金元素重新分布和形成细小的析出相,从而提高合金的强度和韧性。
5. 浇注:将熔融的合金倒入预先准备的铸型中。
在浇注过程中,需要控制好铸态温度、浇注速度和浇注压力,以确保铸件的质量。
6. 冷却:浇注后,铸件需要进行冷却。
冷却速度会影响铸件的晶粒大小和组织结构,因此需要根据不同的合金性能要求,选择合适的冷却方式。
7. 修磨和表面处理:冷却后的铸件需要进行去毛刺、修磨和表面处理等工艺,以提高铸件的表面质量和精度。
以上是铸造铝合金的一般熔炼工艺流程,具体操作步骤和参数设置会根据不同的铝合金材料和铸造要求而有所差异。
铝合金熔炼与铸造 (2)

铝合金熔炼与铸造1.铝合金是一种重要的金属材料,具有优异的物理性能和机械性能,广泛应用于航天航空、汽车制造、建筑工程等领域。
铝合金熔炼与铸造是生产铝合金制品的关键步骤,本文将介绍铝合金熔炼与铸造的基本原理、常用工艺和注意事项。
2. 铝合金熔炼铝合金熔炼是将铝合金原料加热至熔点,并以一定方式进行熔炼的过程。
铝合金原料可以是铝锭、废铝或铝合金碎料,在熔炼过程中需要加入一定比例的熔剂和合金元素。
铝合金熔炼的目的是将原料熔化并混合均匀,以获得符合要求的铝合金液态材料。
2.1 熔炼设备铝合金熔炼通常使用电阻炉、感应炉或电弧炉等熔炼设备。
其中,电阻炉是最常用的熔炼设备之一。
电阻炉通过电流通过导体产生的电阻热进行熔炼,具有加热速度快、操作方便等优点。
感应炉则利用电磁感应的原理进行加热,加热效率高,适用于熔炼大批量的铝合金。
电弧炉则利用电弧的高温进行熔炼,适用于熔炼高温合金。
2.2 熔炼工艺铝合金熔炼的工艺通常包括预热、熔炼和保温三个阶段。
将熔炼设备预热至一定温度,然后将铝合金原料和熔剂放入炉中,并控制加热温度和时间,使原料熔化并混合均匀。
,保持一定温度,使铝合金保持液态状态,以备后续的铸造工艺使用。
2.3 熔炼注意事项在铝合金熔炼过程中需要注意以下几点:•安全操作:熔炼过程中需要戴上防护设备,避免接触高温液态金属和有害气体。
•熔化温度控制:严格控制熔化温度,过高的温度会导致铝合金组织不稳定,影响机械性能。
•熔炼时间控制:合适的熔炼时间可以保证原料充分熔化和混合均匀。
•熔剂和合金元素的添加:根据铝合金的要求添加适当比例的熔剂和合金元素,以调整铝合金的成分和性能。
3. 铸造过程铸造是将铝合金液态材料倒入铸型中,并经过凝固和冷却形成所需的铝合金制品的过程。
铸造过程可以分为压铸、重力铸造和砂型铸造等不同的铸造方法。
3.1 压铸压铸是一种通过高压将铝合金液态材料注入金属模具中,并经过快速凝固形成制品的铸造方法。
压铸具有生产效率高、制品精度高等优点,适用于生产复杂形状的铝合金制品。
铝合金的熔炼与铸造
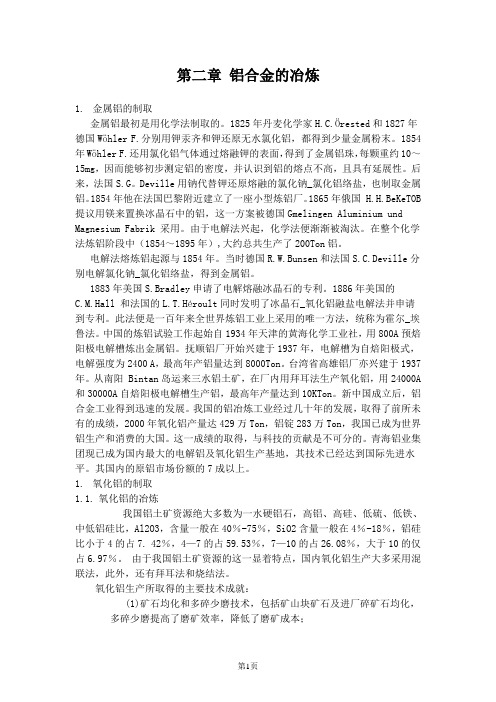
第二章铝合金的冶炼1.金属铝的制取金属铝最初是用化学法制取的。
1825年丹麦化学家H.C.Örested和1827年德国Wöhler F.分别用钾汞齐和钾还原无水氯化铝,都得到少量金属粉末。
1854年Wöhler F.还用氯化铝气体通过熔融钾的表面,得到了金属铝珠,每颗重约10~15mg,因而能够初步测定铝的密度,并认识到铝的熔点不高,且具有延展性。
后来,法国S.G。
Deville用钠代替钾还原熔融的氯化钠_氯化铝络盐,也制取金属铝。
1854年他在法国巴黎附近建立了一座小型炼铝厂。
1865年俄国 H.H.BeKeTOB 提议用镁来置换冰晶石中的铝,这一方案被德国Gmelingen Aluminium und Magnesium Fabrik 采用。
由于电解法兴起,化学法便渐渐被淘汰。
在整个化学法炼铝阶段中(1854~1895年),大约总共生产了200Ton铝。
电解法熔炼铝起源与1854年。
当时德国R.W.Bunsen和法国S.C.Deville分别电解氯化钠_氯化铝络盐,得到金属铝。
1883年美国S.Bradley申请了电解熔融冰晶石的专利。
1886年美国的C.M.Hall 和法国的L.T.Héroult同时发明了冰晶石_氧化铝融盐电解法并申请到专利。
此法便是一百年来全世界炼铝工业上采用的唯一方法,统称为霍尔_埃鲁法。
中国的炼铝试验工作起始自1934年天津的黄海化学工业社,用800A预焙阳极电解槽炼出金属铝。
抚顺铝厂开始兴建于1937年,电解槽为自焙阳极式,电解强度为2400 A,最高年产铝量达到8000Ton。
台湾省高雄铝厂亦兴建于1937年。
从南阳 Bintan岛运来三水铝土矿,在厂内用拜耳法生产氧化铝,用24000A 和30000A自焙阳极电解槽生产铝,最高年产量达到10KTon。
新中国成立后,铝合金工业得到迅速的发展。
我国的铝冶炼工业经过几十年的发展,取得了前所未有的成绩,2000年氧化铝产量达429万Ton,铝锭283万Ton,我国已成为世界铝生产和消费的大国。
铝合金熔炼与铸造技术

铝合金熔炼与铸造技术一、引言铝合金是一种重要的结构材料,具有轻质、高强度和良好的耐腐蚀性能,在航空航天、汽车制造、建筑工程等领域广泛应用。
铝合金的制备过程中,熔炼与铸造技术起到关键作用,本文将对铝合金熔炼与铸造技术进行详细探讨。
二、铝合金熔炼技术2.1 熔炼原料准备熔炼铝合金的原料主要包括铝、合金元素和辅助材料。
铝采用高纯度的铝锭,合金元素可以通过添加铝合金粉末或其他化合物来实现。
辅助材料包括熔剂、脱气剂等。
这些原料的准备对于保证铝合金的成分和质量非常重要。
2.2 熔炼设备和工艺熔炼铝合金的常用设备有电阻加热炉、感应加热炉和气体燃烧炉等。
其中,感应加热炉在铝合金熔炼中应用最广泛,具有加热速度快、能耗低和温度控制准确等优点。
熔炼工艺包括预热、熔化、调温和净化等步骤,其中净化技术对于铝合金的纯净度和性能起到重要作用。
2.3 熔炼过程控制与优化熔炼过程中,熔体温度、保温时间、搅拌方式等因素对铝合金的成分和组织结构有重要影响。
熔炼过程需要进行温度控制、气氛控制和搅拌控制等,以确保铝合金的成分均匀、杂质含量低。
三、铝合金铸造技术3.1 铸造方法铝合金的常用铸造方法包括压铸、重力铸造、低压铸造和砂型铸造等。
压铸是最常用的铸造方法,适用于生产复杂形状和尺寸精度要求高的铝合金件。
重力铸造适用于大型铝合金零部件的生产,低压铸造适用于长条状和壳状铝合金件的生产,砂型铸造适用于非常大型和特殊形状的铝合金件的生产。
3.2 铝合金铸造过程铝合金的铸造过程主要包括熔炼、准备模具、浇注、冷却和后处理等步骤。
熔炼过程中,需要根据具体合金配方和要求,控制熔体温度、浇注温度和浇注速度等参数。
准备模具是确保铸造件尺寸和表面质量的重要环节。
浇注过程需要保证熔体充分填充模腔,并避免气孔和缺陷的产生。
冷却过程中需控制冷却速率,以避免铝合金件出现应力和变形。
3.3 铝合金铸造工艺改进为了提高铝合金铸造件的质量和效率,可以采取一些工艺改进措施。
铸造铝合金熔化是有害工种文件

铸造铝合金熔化是有害工种文件铸造铝合金熔炼是一种有害工种,主要包括铝合金冶炼、熔化、铸造等工序。
这项工作涉及到高温、有毒有害气体和金属熔体,具有较高的风险。
在这篇文章中,我将针对该工种的危害性及其预防措施展开深入探讨。
首先,我们来看一下铝合金冶炼中的危险源。
在冶炼过程中,需要加入高温熔化的铝合金料,这会产生大量的熔融金属。
铝铸造熔炼过程中的高温环境容易导致热应激、烧伤等症状。
此外,铸造过程中还会产生大量的熔化烟雾和有害气体,如一氧化碳、氧化铝、二氧化硅等。
这些有害气体在长时间暴露下会对工人的呼吸系统、皮肤等造成损害。
其次,铸造铝合金熔炼工作还存在火灾和爆炸的风险。
由于铝合金的熔点较低,易于燃烧并产生火焰,一旦操作不当,火焰很可能迅速蔓延并引发火灾。
同时,铝合金冶炼会产生一些易燃、易爆的废弃物,这些废弃物在堆积过程中也会引起爆炸的危险。
如何预防铸造铝合金熔炼的危害呢?首先,必须强调员工的安全意识和培训。
工人在进行该工种操作前,必须清楚了解工作中的危险源和相应的防护措施,定期参加安全培训,提高自身的应急响应能力。
其次,必须配备适当的个人防护装备,如防火服、面罩、手套等。
这些防护设备能有效减少工人在高温工作环境下的热应激和烧伤等风险。
此外,还需配备储存和处理废弃物的设备,并对废弃物进行正确的处置,以防止火灾和爆炸的发生。
除了个人防护措施,还需要加强现场管理和环境监测。
在铝合金冶炼工作现场,应设置适当的通风设备和消防设备,确保工人的工作环境处于安全状态。
同时,应定期进行环境监测,检测有害气体的浓度,及时做出相应的调整和防范措施。
此外,还应建立健全的安全管理制度和应急预案。
对于铸造铝合金熔炼工作,应制定操作规范和安全操作流程,并将其时间实施,确保工人的安全。
同时,建立应急预案,针对突发事件做好各类救援的准备工作。
综上所述,铸造铝合金熔炼是一项有害工种,主要危害包括高温、有害气体、烧伤、火灾和爆炸等。
为保障工人的人身安全和健康,必须加强员工的安全意识和培训,合理配备个人防护装备,强化现场管理和环境监测,制定安全管理制度和应急预案。
铸造合金及其熔炼 第十三章 铸造铝合金的熔炼
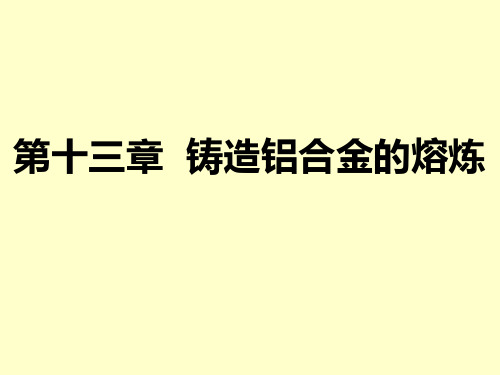
浇注过程中生成的氧化夹杂称为二次氧化夹杂,多分 布在铸件壁的转角处及最后凝固的部位。
一次氧化夹杂按形态可分为二类。 第一类是分布不均匀的大块夹杂物,它的危害性很大, 使合金基体不连续,引起铸件渗漏或成为腐蚀的根源,明 显降低铸件的力学性能。
五、合金元素对铝液吸氢的影响
1、对溶解度的影响 在pH2 =0. 1MPa的条件下,测得硅、铜、镁对溶解
度影响,按公式(13-21)算得常数A、B值列于表13-3中。 从表中可见、含镁量越高,氢的溶解度越高;反之,
硅、铜含量越高,氢的溶解度越低。
2、对氧化膜性能的影响
Mg、Na、Ca等氧的亲和力比铝大,是表面活性元 素,密度又比铝小,富集于铝液表面,熔炼时,优先被炉 气氧化。铝液中含镁量高于1%,表面氧化膜即全部由 MgO所组成,这层MgO组织疏松,对铝液不起保护作用, 故Al-Mg类合金必须在熔剂覆盖下进行熔炼。
点状针孔由铸件凝固时析出的气泡所形成,多发生于 结晶温度范围小、补缩能力良好的铸件中,如ZL102合金 铸件中。当凝固速度较快时,离共晶成分较远的ZL105合 金铸件中也会出现点状针孔。
(2) 网状针孔 此类针孔在低倍显微组织中呈密集相 联成网状,伴有少数较大的孔洞,不易清点针孔数目,难 以测量针孔的直径,往往带有末梢,俗称“苍蝇脚”。
库应保持清洁,干燥,以防生成铝锈。对已生成铝锈的铝
锭,投入熔炉前应彻底清除铝锈,否则即使熔炼工艺操作
很严格,也不易获得高质量的铝液。
各种油污都是由复杂结构的碳氢化合物所组成,与铝 液接触后都会发生下列反应,生成氢气
4/3mAl+CmHn=1/3mAl4C3+1/2nH2
铸造铝合金的熔炼工艺
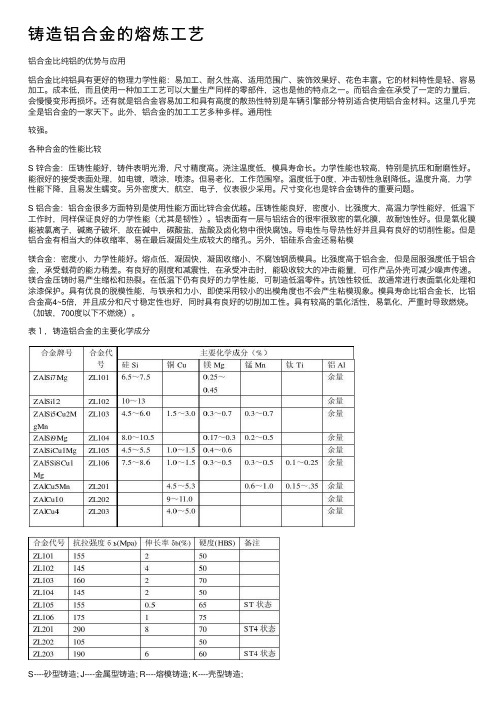
铸造铝合⾦的熔炼⼯艺铝合⾦⽐纯铝的优势与应⽤铝合⾦⽐纯铝具有更好的物理⼒学性能:易加⼯、耐久性⾼、适⽤范围⼴、装饰效果好、花⾊丰富。
它的材料特性是轻、容易加⼯。
成本低,⽽且使⽤⼀种加⼯⼯艺可以⼤量⽣产同样的零部件,这也是他的特点之⼀。
⽽铝合⾦在承受了⼀定的⼒量后,会慢慢变形再损坏。
还有就是铝合⾦容易加⼯和具有⾼度的散热性特别是车辆引擎部分特别适合使⽤铝合⾦材料。
这⾥⼏乎完全是铝合⾦的⼀家天下。
此外,铝合⾦的加⼯⼯艺多种多样。
通⽤性较强。
各种合⾦的性能⽐较S 锌合⾦:压铸性能好,铸件表明光滑,尺⼨精度⾼。
浇注温度低,模具寿命长。
⼒学性能也较⾼,特别是抗压和耐磨性好。
能很好的接受表⾯处理,如电镀,喷涂,喷漆。
但易⽼化,⼯作范围窄。
温度低于0度,冲击韧性急剧降低。
温度升⾼,⼒学性能下降,且易发⽣蠕变。
另外密度⼤,航空,电⼦,仪表很少采⽤。
尺⼨变化也是锌合⾦铸件的重要问题。
S 铝合⾦:铝合⾦很多⽅⾯特别是使⽤性能⽅⾯⽐锌合⾦优越。
压铸性能良好,密度⼩,⽐强度⼤,⾼温⼒学性能好,低温下⼯作时,同样保证良好的⼒学性能(尤其是韧性)。
铝表⾯有⼀层与铝结合的很牢很致密的氧化膜,故耐蚀性好。
但是氧化膜能被氯离⼦,碱离⼦破坏,故在碱中,碳酸盐,盐酸及卤化物中很快腐蚀。
导电性与导热性好并且具有良好的切削性能。
但是铝合⾦有相当⼤的体收缩率,易在最后凝固处⽣成较⼤的缩孔。
另外,铝硅系合⾦还易粘模镁合⾦:密度⼩,⼒学性能好。
熔点低,凝固快,凝固收缩⼩,不腐蚀钢质模具。
⽐强度⾼于铝合⾦,但是屈服强度低于铝合⾦,承受载荷的能⼒稍差。
有良好的刚度和减震性,在承受冲击时,能吸收较⼤的冲击能量,可作产品外壳可减少噪声传递。
镁合⾦压铸时易产⽣缩松和热裂。
在低温下仍有良好的⼒学性能,可制造低温零件。
抗蚀性较低,故通常进⾏表⾯氧化处理和涂漆保护。
具有优良的脱模性能,与铁亲和⼒⼩,即使采⽤较⼩的出模⾓度也不会产⽣粘模现象。
模具寿命⽐铝合⾦长,⽐铝合⾦⾼4~5倍,并且成分和尺⼨稳定性也好,同时具有良好的切削加⼯性。
铸造铝合金的典型熔炼工艺
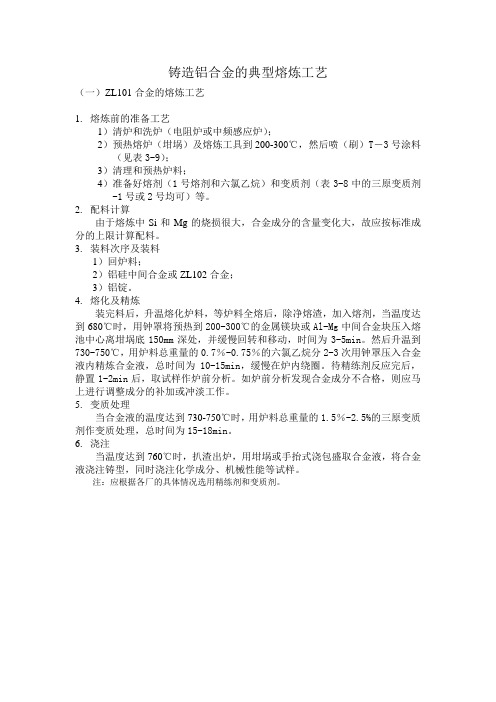
铸造铝合金的典型熔炼工艺(一)ZL101合金的熔炼工艺1.熔炼前的准备工艺1)清炉和洗炉(电阻炉或中频感应炉);2)预热熔炉(坩埚)及熔炼工具到200-300℃,然后喷(刷)T-3号涂料(见表3-9);3)清理和预热炉料;4)准备好熔剂(1号熔剂和六氯乙烷)和变质剂(表3-8中的三原变质剂-1号或2号均可)等。
2.配料计算由于熔炼中Si和Mg的烧损很大,合金成分的含量变化大,故应按标准成分的上限计算配料。
3.装料次序及装料1)回炉料;2)铝硅中间合金或ZL102合金;3)铝锭。
4.熔化及精炼装完料后,升温熔化炉料,等炉料全熔后,除净熔渣,加入熔剂,当温度达到680℃时,用钟罩将预热到200-300℃的金属镁块或Al-Mg中间合金块压入熔池中心离坩埚底150mm深处,并缓慢回转和移动,时间为3-5min。
然后升温到730-750℃,用炉料总重量的0.7%-0.75%的六氯乙烷分2-3次用钟罩压入合金液内精炼合金液,总时间为10-15min,缓慢在炉内绕圈。
待精练剂反应完后,静置1-2min后,取试样作炉前分析。
如炉前分析发现合金成分不合格,则应马上进行调整成分的补加或冲淡工作。
5.变质处理当合金液的温度达到730-750℃时,用炉料总重量的1.5%-2.5%的三原变质剂作变质处理,总时间为15-18min。
6.浇注当温度达到760℃时,扒渣出炉,用坩埚或手抬式浇包盛取合金液,将合金液浇注铸型,同时浇注化学成分、机械性能等试样。
注:应根据各厂的具体情况选用精练剂和变质剂。
1.熔炼前的准备工艺1)清炉和洗炉;2)预热熔炉(坩埚)、工具到200-300℃;3)喷涂(刷)T-3号涂料(见表3-9)或其他涂料;4)清理、预热炉料;5)准备好熔剂变质剂等。
2.配料计算由于熔炼中Si的含量大,易烧损大,故配料计算时应取上限。
3.装料次序及装料1)回炉料;2)铝硅中间合金;3)铝锭。
4.熔化及精炼炉料装好后,升温熔化炉料,等炉料全熔后,除净熔渣,升温到700-720℃,用炉料总重量的0.3%-0.5%的六氯乙烷(或氯气等其他精炼剂)分3次用钟罩压入熔池中心下面精炼合金液,精炼总时间为10-15min。
- 1、下载文档前请自行甄别文档内容的完整性,平台不提供额外的编辑、内容补充、找答案等附加服务。
- 2、"仅部分预览"的文档,不可在线预览部分如存在完整性等问题,可反馈申请退款(可完整预览的文档不适用该条件!)。
- 3、如文档侵犯您的权益,请联系客服反馈,我们会尽快为您处理(人工客服工作时间:9:00-18:30)。
第一节 铝合金液的精炼原理
精炼的目的:
清除铝液中的气体和各类有害杂质,净化铝液,防 止在铸件中形成气孔和夹渣。
一、铝铸件中气孔的形态及对性能的影响
1、针孔 分布在整个铸件截面上,因铝液中的气体,夹杂含量高、
精炼效果差、铸件凝固速度低所引起。针孔可分三种类型。
(1) 点状针孔 此类针孔在低倍显微组织中呈圆点状, 轮廓清晰且互不相连,能清点出每平方厘米面积上的针孔数目并测 得针孔的直径。这类针孔容易和缩孔、缩松相区别。
在所有的炉气成分中,只有氢能大量地溶解于铝液中。 根据测定,存在于铝合金中的气体,氢占85%以上,因而 “含气量”可视为“含氢量”的同义词。
铝液中的氢和氧化夹杂主要来源于铝液与炉气中水 汽的反应。
1、铝和水汽的反应
低于250℃时,铝锭与大气中的水汽接触会产生下 列反应
Al+H2O→Al(OH)3+H2
气孔位于铸件表皮下面,因铝液和铸型中水分反 应产生气体所造成,一般和铝液质量无关.
3、单个大气孔
这种气孔产生的原因是由于铸件工艺设计不合理, 如铸型或型芯排气不畅,或者是由于操作不小心,如浇注 时堵死气眼,型腔中的气体被憋在铸件中所引起,也和铝 液纯净度无关。
二、铝铸件中氧化夹杂物形态及对性能的影响
图13-1为铝液与各种炉气成分反应 时标准状态自由能的变化。
从表13-1和图13-1可见,除按反应式(13-2)、(13-6)
生成Al4C3外,其余反应都将生成Al2O3,而AlN与H2O或O2按式(1310)、(13-11)反应, Al4C3与H2O或O2按式(13-8)、(13-9)反应又都 生成Al2O3,因此,表13-1所列众多反应的最终产物中大部分是Al2O3。 Al2O3的化学稳定性极高,熔点高达2015℃±15℃,在铝液中不再分 解,是铝铸件中主要的氧化夹杂物。
(13-17)
dlnKp/dT=ΔH/RT2
(13-18)
式中 ΔH一氢的溶解热,J/mol;
T—热力学温度,K;
R一气Байду номын сангаас常数。
设ΔH与温度无关,解得
[H]=K0√pH2 exp(-ΔH/2RT) (13-19)
当温度不变时,
[H]=Ks√pH2 式中 K0 —常数;
Ks —温度不变时的参数。
(13-20)
点状针孔由铸件凝固时析出的气泡所形成,多发生于结 晶温度范围小、补缩能力良好的铸件中,如ZL102合金铸件中。当 凝固速度较快时,离共晶成分较远的ZL105合金铸件中也会出现点 状针孔。
(2) 网状针孔 此类针孔在低倍显微组织中呈密集相联成网 状,伴有少数较大的孔洞,不易清点针孔数目,难以测量针孔的直 径,往往带有末梢,俗称“苍蝇脚”。
浇注前铝液中存在的氧化夹杂称为一次氧化夹杂,总 量约占铝液质量的0.002%-0.02%。在铸件中分布没有规律。
浇注过程中生成的氧化夹杂称为二次氧化夹杂,多分 布在铸件壁的转角处及最后凝固的部位。
一次氧化夹杂按形态可分为二类。 第一类是分布不均匀的大块夹杂物,它的危害性很大, 使合金基体不连续,引起铸件渗漏或成为腐蚀的根源,明 显降低铸件的力学性能。
第二类夹杂呈弥散状,在低倍显微组织中不易发现, 铸件凝固时成为气泡的形核基底,生成针孔。这一类氧化 夹杂很难在精炼时彻底清除。
三、铝液中气体和夹杂物的来源
铝合金通常在大气中熔炼,当铝液和炉气中 的N2、O2、H2O、CO2、CO、H2、CmHn等接触时,会产生化合, 化分,溶解、扩散等过程。 各种炉气成分与铝液反应的热力学计算数据及反应式列于 表13-1中。
(13-16)
这一反应,也是铝液吸氢的原因之一,故生产中 严格禁用沾有油污的炉料直接投入熔池中。事先必须进行 “碱洗”处理,清除油污。
2、氢在铝中的溶解度
铝液与水汽按式(13-13)反应生成的H2按式(13-12)溶 入铝液中,达到平衡时有
式中
Kp=[H]2/pH2 Kp—平衡常数;
pH2一氢分压,Mpa; [H]—溶于铝中氢的浓度。
此铝锭不宜储存在潮湿的库房内或在雨季露天堆放。炉料
库应保持清洁,干燥,以防生成铝锈。对已生成铝锈的铝
锭,投入熔炉前应彻底清除铝锈,否则即使熔炼工艺操作
很严格,也不易获得高质量的铝液。
各种油污都是由复杂结构的碳氢化合物所组成, 与铝液接触后都会发生下列反应,生成氢气
4/3mAl+CmHn=1/3mAl4C3+1/2nH2
(13-14)
Al(OH)3长在铝锭表面,组织疏松,呈粉末状, 对铝锭没有保护作用,俗称铝锈。
用带有铝锈的铝锭作炉料,升温至400℃左右,铝锈按 下式分解
Al(OH)3→ Al2O3+H2O
(13-15)
分解产物Al2O3组织疏松,能吸附水汽和氢,混入铝
液中,增大气体和氧化夹杂的含量,使铝液质量变坏。因
结晶温度宽的合金,铸件缓慢凝固时析出的气体分布在晶界 上及发达的枝晶间隙中,此时结晶骨架已形成,补缩通道被堵塞, 便在晶界上及枝晶间隙中形成网状针孔。
(3) 混合型针孔 此类针孔点状针孔和网状针孔混杂一起, 常见于结构复杂、壁厚不均匀的铸件中。
其中网状针孔割裂合金基体,危害性比点状针孔大。
2、皮下气孔
式(13-20)即为有名的Sieverts公式,说明温度不变 时,所有双原子的气体溶入铝液时都服从这个公式。如果 不服从这个公式,说明气体和铝相互作用,形成化合物。
概述
熔炼工艺是铸件生产过程中的一个有机组成。 一个优质铝铸件的获得,需要有一整套优化的铸造方 法、铸造工艺、熔炼工艺及浇注工艺相配合。
铝合金熔炼的内容包括配料计算,炉料处理, 熔炼设备选用,熔炼工具处理及熔炼工艺过程控制。
熔炼工艺过程控制的内容包括正确的加料次序。 严格控制熔炼温度和时间、实现快速熔炼、效果显著的铝 液净化处理和变质处理及掌握可靠的铝液炉前质量检测手 段等。
熔炼工艺过程控制的目的是获得高质量的能满足下 列要求的铝液: 1)化学成分符合国家标准,合金液成分均匀; 2) 合金液纯净,气体、氧化夹杂、熔剂夹杂含量低; 3) 需要变质处理的合金液,变质良好。
据统计因熔炼工艺过程控制不严而产生的废品中, 如渗漏、气孔、夹渣等,主要原因是合金液中的气体、氧 化夹渣、熔剂夹渣未清除所引起.因此在确保化学成分合 格的前提下,熔炼工艺过程控制的主要任务是提高合金液 的纯净度和变质效果。