材料成型第4章 铸造工艺设计2
材料成型工艺教学大纲
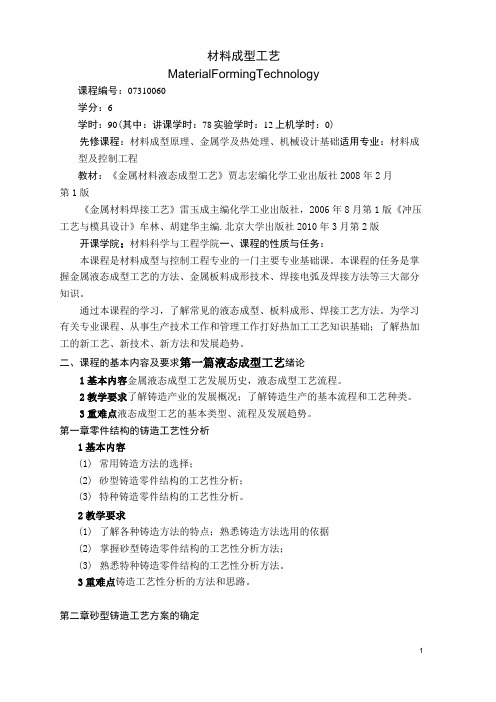
材料成型工艺MaterialFormingTechnology课程编号:07310060学分:6学时:90(其中:讲课学时:78实验学时:12上机学时:0)先修课程:材料成型原理、金属学及热处理、机械设计基础适用专业:材料成型及控制工程教材:《金属材料液态成型工艺》贾志宏编化学工业出版社2008年2月第1版《金属材料焊接工艺》雷玉成主编化学工业出版社,2006年8月第1版《冲压工艺与模具设计》牟林、胡建华主编.北京大学出版社2010年3月第2版开课学院:材料科学与工程学院一、课程的性质与任务:本课程是材料成型与控制工程专业的一门主要专业基础课。
本课程的任务是掌握金属液态成型工艺的方法、金属板料成形技术、焊接电弧及焊接方法等三大部分知识。
通过本课程的学习,了解常见的液态成型、板料成形、焊接工艺方法。
为学习有关专业课程、从事生产技术工作和管理工作打好热加工工艺知识基础;了解热加工的新工艺、新技术、新方法和发展趋势。
二、课程的基本内容及要求第一篇液态成型工艺绪论1基本内容金属液态成型工艺发展历史,液态成型工艺流程。
2教学要求了解铸造产业的发展概况;了解铸造生产的基本流程和工艺种类。
3重难点液态成型工艺的基本类型、流程及发展趋势。
第一章零件结构的铸造工艺性分析1基本内容(1)常用铸造方法的选择;(2)砂型铸造零件结构的工艺性分析;(3)特种铸造零件结构的工艺性分析。
2教学要求(1)了解各种铸造方法的特点;熟悉铸造方法选用的依据(2)掌握砂型铸造零件结构的工艺性分析方法;(3)熟悉特种铸造零件结构的工艺性分析方法。
3重难点铸造工艺性分析的方法和思路。
第二章砂型铸造工艺方案的确定1基本内容(1)工艺设计内容及流程;(2)砂型铸造工艺方案确定的基本原理;2教学要求(1)熟悉铸造工艺设计的依据、内容及流程;(2)掌握砂型铸造工艺方案制定的原理及方法。
3重难点(1)生产纲领、生产条件对工艺方案制定的影响;(2)分型面及浇注位置的确定。
铸造工艺学课程设计案例

成果报告需以PDF格式提交,同时附上所有相关数据和图表。
报告内容
报告需包含设计思路、工艺流程、数据分析及结论等部分,要求 内容详实、逻辑清晰。
成果展示形式和内容安排建议
展示形式
鼓励采用多媒体形式进行展示,如PPT、视频等。
内容安排
建议按照设计背景、设计思路、工艺流程、数据 分析、结论与展望等顺序进行展示。
时间安排
每个小组展示时间不超过20分钟,需提前做好时 间规划。
课程设计评价标准及成绩评定方法
01
评价标准
将从设计创新性、实用性、技术 难度、报告质量等方面进行综合 评价。
02
成绩评定方法
03
优秀作品选拔
采用百分制评分,其中设计创新 性占30%、实用性占20%、技术 难度占20%、报告质量占30%。
铸造材料选择
根据零件使用要求、生产批量和成本 等因素,选择合适的铸造合金,如铸 铁、铸钢、铝合金等。
性能要求
铸造合金应具有良好的流动性、收缩 性、偏析倾向小等性能,以保证铸件 质量。同时,合金成分和性能应符合 相关标准或技术条件的规定。
03
案例分析:典型铸件生产工艺设计
铸件结构分析与设计优化建议
根据评分结果,选拔出优秀作品 进行表彰和奖励。
THANKS
感谢观看
推广新技术和新材料
积极推广先进的铸造技术和新材料,如3D打印技术、高性能铸造合 金等,提高铸件的精度和性能。
加强人才培养
加强铸造领域的人才培养和引进,提高从业人员的专业素质和技能水 平,为铸造行业的发展提供有力的人才保障。
06
课程设计成果展示与评价标准
课程设计成果提交要求说明
提交时间
所有成果需在课程结束前一周内提交,逾期将不予受理。
材料成型第4章_铸造工艺设计1.答案

(2)尽量使铸件重要加工面或大部分加 工面、加工基准面放在一个砂型内,减少 错箱、披缝和毛刺,提高铸件精度。
床身铸件,其顶部平面为加工基准面。 图中方案a在妨碍起模的凸台处增加了外部型芯,因采用整模造型使加工 面和基准面在同一砂箱内,铸件精度高,是大批量生产时的合理方案。 若采用方案b,铸件若产生错型将影响铸件精度,但在单件、小批生产条 件下,铸件的尺寸偏差在一定范围内可用划线来矫正,故在相应条件下方 案b仍可采用。
25
方案1要考虑采用活块造型或加外型芯才能铸造; 方案2则省去了活块造型或加外型芯。
26
使铸件全部或大部分放在同一砂型
尽量使加工基准面与大部分 加工面在同一砂型内
不合理
合理
尽量使加工基准面与大部分 加工面在同一砂型内
27
(3)使型腔和主要型芯位于下箱,以便于造型、下 芯、合型和检查型腔尺寸。
于垂直或倾斜位置。图为油盘铸件的合理浇注位 置。
图4-2b 大面积薄壁铸件浇注位置
(4)对于容易产生缩孔的铸件,应使厚的 部分放在铸型的上部或侧面,以便在铸件 厚壁处直接安置冒口,使之实现自下而上 的定向凝固
铸钢卷扬筒,浇注时厚端放在上部是合理的; 反之,若厚端放在下部,则难以补缩。
23 图4-2-1 有热节的浇注位置
铸件的造型位置由分型面决定,而铸件的浇注位 置与造型位置通常是一致的。
浇注位置和分型面对铸件质量及铸造工艺都有很 大影响。
选择原则:着眼于控制铸件的凝固顺序
估计到铸件发生缺陷的可能
1.浇注位置的选择原则
(1) 铸件的重要加工面或主要工作面应朝下或位于 侧面,避免砂眼、气孔和夹渣
因为铸件的上表面容易产生砂眼、气孔、夹渣等缺陷,组 织也不如下表面致密。如果这些加工面难以朝下,则应尽 力使其位于侧面。当铸件的重要加工面有数个时,则应将 较大的平面朝下。
金属材料的成型工艺

5
20231/7./17爆炸焊
爆炸焊是以炸药为能源进行金属间焊接的方法。这种焊接是 利用炸药的爆轰,使被焊金属面发生高速倾斜碰撞,在接触面上造 成一薄层金属的塑性变形,在此十分短暂的冶金过程中形成冶金结 合。
爆炸焊的特点是: 1)能将任意相同的、特别是不同的金属材料迅速牢固地焊接起来。 2)工艺十分简单,容易掌握。 3)不需要厂房、不需要大型设备和大量投资。 4)不仅可以进行点焊和线焊,而且可以进行面焊-爆炸复合,从 而获得大面积的复合板、复合管和复合管棒等。 5)能源为低焊速的混合炸药,它们价廉、易得、安全和使用方便。
4
锻造基础知识
锻202造1/7/是17 对金属坯料(不含板材)施加外力,使其产生塑性变形、改变尺
寸、形状及改善性能,用以制造机械零件、工件、工具或毛坯的成形加 工方法。
根据在不同的温度区域进行的锻造,针对锻件质量和锻 造工艺要求的不同,可分为冷锻、温锻、热锻三个成型温 度区域。一般地讲,在有再结晶的温度区域的锻造叫热锻, 不加热在室温下的锻造叫冷锻。
的工件,形状和尺寸精度高,表面光洁,加工工序少, 便于自动化生产。当加工工件大、厚,材料强度高、 塑性低时,都采用热锻压。
(4)等温锻压 工件在整个成形过程中温度保持
不变。等温锻压是为了充分利用某些金属在某一温度 下所具有的高塑性,或为了获得特定的组织和性能, 所需费用较高,仅用于特殊的锻压工艺,如超塑成形。
7
4.冲压 2021/7/17
冲压:金属板料在冲压模之间受压产生分离或产生塑
性变形的加工方法。
按加工温度分类:热冲压和冷冲压。前者适合变 形抗力高,塑性较差的板料加工;后者在室温 下进行,是薄板常用的冲压方法。
8
•冲压基础知识
材料成型工艺基础——铸造

机器造型铸件精度高,余量小;手工造型误差大,余量 也大。灰铸铁加工余量小,铸钢加工余量大。
(3) 拔模斜度
(4) 铸造圆角 圆角半径一般约为相交两壁平均厚度的1/4
(5) 型芯头
型芯头的作用:定位、支撑和固定砂芯
(6) 最小铸出孔及槽
最小铸出孔直径 灰口铸铁件 12~15 15~30 30~50 铸钢件 30~50 50
(2) 对于一些需要补缩的铸件,为防止铸件产生缩孔、缩松的 缺陷,应使铸件较厚的部位放在铸型的上部或侧面。 (3) 应将面积较大的薄壁部位置于铸型下部,或使其倾斜位置
(4) 铸件的大平面应朝下
2. 分型面的选择 (1)分型面应选在铸件的最大截面处。
(2)应尽量减少分型面的数量,并尽可能选择平面分型。
(2) 冷裂 冷裂的特征是:裂纹细小,呈连续直线状,缝内有金属 光泽或轻微氧化色。 冷裂的防止: 1)使铸件壁厚尽可能均匀; 2)采用同时凝固的原则; 3)对于铸钢件和铸铁件,必须严格控制磷的 含量,防止冷脆性。
作 业
1.铸件的凝固应遵循什么基本原则?优缺点是 什么?各适用于什么范围? 2.在生产中,为什么要选择共晶成分、近共晶 成分或凝固温度范围小的合金作为铸造合金?
2)给定成分的铸件,缩孔和缩松的总容积是一定值,适 当增大铸件的冷却速度可促进缩松向缩孔转化; 3)合金收缩越大,铸件的缩孔体积越大; 4)浇注温度越高,液态收缩越大,缩孔的体积越大; 5)缩孔和缩松总是存在于铸件的最后凝固部位。如果铸 件设计壁厚不均匀,则在厚壁处易于出现缩孔或缩松。
2)缩孔和缩松的防止 防止缩孔和缩松常用的工艺措施就是控制铸件的凝固
提高25~30%,但伸长率有所下降。
(3) 可压铸出形状复杂的薄壁件。 (4) 生产率高。国产压铸机每小时可铸
端盖零件铸造工艺课程设计说明书

课程设计说明书(论文)课程名称:成型工艺及模具课程设计II设计题目:端盖零件铸造工艺设计院系:班级:设计者:学号:指导教师:设计时间:1、设计任务1.1、设计零件的铸造工艺图1.2、设计绘制模板装配图1.3、设计并绘制所需芯盒装配图1.4、编写铸造工艺设计说明书2、生产条件和技术要求2.1、生产性质:大批量生产2.2、材料:HT2002.3、零件加工方法:零件上有多个孔,除中间的大孔需要铸造以外,其他孔在考虑加工余量后不宜铸造成型,采用机械方法加工,均不铸出。
造型方法:机器造型造芯方法:手工制芯2.4、主要技术要求:满足HT200的机械性能要求,去毛刺及锐边,未注明圆角为R3-R5,未注明的筋和壁厚为8,铸造拔模斜度不大于2度,铸造表面不允取有缺陷。
3、零件图及立体图结构分析3.1、零件图如下:图1.零件主视图图2.零件左视图3.2三维立体图如下:图3.三维图(1)图4.三维图(2)4、工艺设计过程4.1、铸造工艺设计方法及分析4.1.1铸件壁厚为了避免浇不到、冷隔等缺陷,铸件不应太薄。
铸件的最小允许壁厚与铸造的流动性密切相关。
在普通砂型铸造的条件下,铸件最小允许壁厚见表1。
表1. 铸件最小允许壁厚引【1,表1-3】查得灰铁铸件在100~200mm的轮廓尺寸下,最小允许壁厚为5~6mm。
由零件图可知,零件中不存在壁厚小于设计要求的结构,在设计过程中,也没有出现壁厚小于最小壁厚要求的情况。
4.1.2造型、制芯方法造型方法:该零件需批量生产,为中小型铸件,应创造条件采用技术先进的机器造型,暂选取水平分型顶杆范围可调节的造型机,型号为Z145A。
制芯方法:由生产条件决定,采用手工制芯。
4.1.3砂箱中铸件数目的确定当铸件的造型方法、浇注位置和分型面确定后,应当初步确定一箱中放几个铸件,作为进行浇冒口设计的依据。
一箱中的铸件数目,应该是在保证铸件质量的前提下越多越好。
本铸件在一砂箱中高约52mm,长约130mm,宽约100mm,重约2.75Kg。
大学本科机械专业泵盖铸造工艺毕业设计
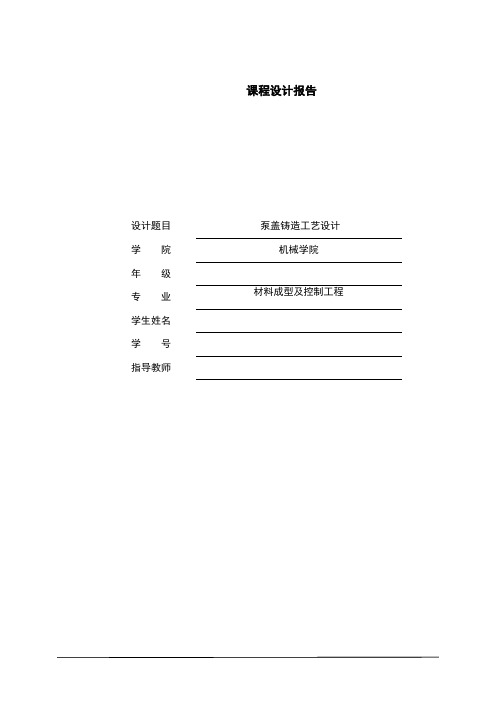
课程设计报告设计题目泵盖铸造工艺设计学院机械学院年级材料成型及控制工程专业学生姓名学号指导教师目录1 设计任务 (1)1.1设计任务 (1)1.2 设计的技术要求12 铸造工艺方案的确定 (2)2.1 零件结构分析 (2)2.2 分型面的确定 (3)2.3.加工余量和铸造圆角 4 2.4工艺参数的确定 5 2.5.1工艺补正量 6 2.5.2分型负数 6 2.5.3砂芯设计 62.5.4铸件毛胚质量 73. 浇注系统(包括冒口)的选择 (7)3.1浇注系统和冒口7 4铸造工艺图 (11)5 铸造工艺卡 (13)6 参考文献 (14)1 设计任务1 1设计任务泵盖铸造工艺设计图11 2设计的技术要求设计应达到的技术要求:实际主要用于零件的外部,起密封,阻挡灰尘的作用,故其在机器中只是起辅助作用,对机器的稳定运行影响不是很大,其在具体加工的时候,精度要求也不是很高,加工起来也十分容易。
依据图纸要满足下列要求:1、材质灰铁150、未注铸造圆角均为R3;2、铸件表面不得有沙眼、缩孔等缺陷;3、泵盖底部Φ132表面Ra为3.2,Φ100表面Ra为6.3,二者之间台阶Ra1.6。
Φ14中心孔内表面Ra为1.6,Φ25中心孔内表面Ra为6.3,其余为Ra12.5;4、两个圆柱孔分别为中心大圆柱Φ25H9基本尺寸为Φ25mm,公差带为H8的孔;中心小圆柱Φ14H92铸造工艺方案的确定2.1零件结构分析名称:泵盖材料: HT150生产批量:大批量生产图2泵盖立体图3泵盖零件2.2分型面的确定在生产中考虑选择分型面时应注意以下原则:1、应使铸件全部或大部置于同一半型内,以保证铸件精度。
如果做不到上述要求,必须尽可能把铸件的加工面和加工基准放在同一半型内。
2、应尽量减少分型面的数目。
分型面越少,铸件精度容易保证且砂箱数目少减少工人劳动量。
3件精度。
4填砂、紧实、起模、下芯都不方便,劳动强度大。
56就本次的泵盖而言:将铸件大部分---重要部分(泵盖圆盘底部)置于下部且分型面为最大截面。
材料成型技术-铸造四(冒口设计)

4)煤气加热冒口; )煤气加热冒口; 5)电弧加热冒口; )电弧加热冒口;
6)发热保温冒口: 发热保温冒口: 利用保温剂和发热剂等专门材料制成发热套, 保温剂和发热剂等专门材料制成发热套 利用保温剂和发热剂等专门材料制成发热套,构成冒口 型腔内表面,浇注后发热套材料产生化学反应激烈发热, 型腔内表面,浇注后发热套材料产生化学反应激烈发热, 使冒口金属液温度提高,凝固时间延长。 使冒口金属液温度提高,凝固时间延长。
冒口设计
一、冒口的作用 1、冒口:铸型中能储存一定的金属液,可对铸件进行 冒口:铸型中能储存一定的金属液, 补缩的专门工艺“空腔”称之为冒口。 补缩的专门工艺“空腔”称之为冒口。 铸件在凝固过程中需要补偿的体积变化有: 铸件在凝固过程中需要补偿的体积变化有: 铸型的胀大(体积膨胀) (1)铸型的胀大(体积膨胀) (2)金属液的液态收缩(高温到低温) )金属液的液态收缩(高温到低温) 金属的凝固收缩(液态到固态) (3)金属的凝固收缩(液态到固态)
冒口设计
3.冒口的设计内容 选择冒口的形状及安放位置; (1)选择冒口的形状及安放位置; 初步确定冒口的数量; (2)初步确定冒口的数量; 计算冒口的尺寸; (3)计算冒口的尺寸; 校核冒口的补缩能力; (4)校核冒口的补缩能力; 校核工艺出品率。 (5)校核工.冒口的类型: 冒口的类型: 按位置分类:顶冒口和边冒口; 1)按位置分类:顶冒口和边冒口; 2)按覆盖情况分类:明冒口和暗冒口。 按覆盖情况分类:明冒口和暗冒口。
三 、 冒口的有效补缩距离
冒口的有效补缩距离:致密的冒口作用区与致 冒口的有效补缩距离: 密的末端区之和称为冒口的有效补缩距离, 密的末端区之和称为冒口的有效补缩距离,即 冒口区+ b = 冒口区+末端区 = c + e 如果被补缩部分的长度大于这个距离, 如果被补缩部分的长度大于这个距离,就 会产生缩孔和缩松;小于b时铸件才是健全的。 会产生缩孔和缩松;小于b时铸件才是健全的。 冒口有效补缩距离是指长度方向的, 冒口有效补缩距离是指长度方向的,实际 上冒口的补缩作用是一个范围。 上冒口的补缩作用是一个范围。 以圆柱冒口为例:以冒口中心为圆心, 以圆柱冒口为例:以冒口中心为圆心,用 冒口半径加上有效补缩距离为半径做圆,圆内 冒口半径加上有效补缩距离为半径做圆, 就是冒口的有效补缩范围 有效补缩范围。 就是冒口的有效补缩范围。
- 1、下载文档前请自行甄别文档内容的完整性,平台不提供额外的编辑、内容补充、找答案等附加服务。
- 2、"仅部分预览"的文档,不可在线预览部分如存在完整性等问题,可反馈申请退款(可完整预览的文档不适用该条件!)。
- 3、如文档侵犯您的权益,请联系客服反馈,我们会尽快为您处理(人工客服工作时间:9:00-18:30)。
型芯是铸件的一个 型芯是铸件的一个 重要的组成部分。 重要的组成部分。
型芯的功用是形成 型芯的功用是形成 铸件的内腔, 铸件的内腔,孔洞和 内腔 形状复杂阻碍起模部 分的外形。 分的外形。
图4-6 车轮铸件的型芯方案
对于内腔形状复杂的大铸件, 对于内腔形状复杂的大铸件,常将形成内腔的型芯分割成数 使每块形状简单,尺寸较小,便于操作、搬运、烘干, 块,使每块形状简单,尺寸较小,便于操作、搬运、烘干,简 化芯盒结构。 化芯盒结构。
加工余量选择原则:
– 大量生产时,因采用机器造型,铸件精度高,故余量可减小; 大量生产时,因采用机器造型,铸件精度高, 余量可减小; – 手工造型误差大,余量应加大。 手工造型误差大,余量应加大。 误差大 – 铸钢件表面粗糙、变形较大,其加工余量应比铸铁件大; 铸钢件表面粗糙、变形较大,其加工余量应比铸铁件大 表面粗糙 余量应比铸铁件 – 有色合金铸件价格甚贵且表面较光洁、平整,其加工余量应 有色合金铸件价格甚贵且表面较光洁、平整,其加工余量应 铸件价格甚贵且表面较光洁 余量 比铸铁小 比铸铁小。 – 铸件的尺寸愈大或加工面与基准面的距离愈大,铸件的尺寸 铸件的尺寸愈大或加工面与基准面的距离愈大, 误差也愈大,故余量也应随之加大 加大。 误差也愈大,故余量也应随之加大。 – 浇注时朝上的表面因产生缺陷的机率较大.其加工余量应比 浇注时朝上的表面因产生缺陷的机率较大. 底面和侧面大 底面和侧面大。
垂直型芯一般都有上、下芯头 垂直型芯一般都有上、下芯头; 短而粗的型芯也可省去上芯头。 短而粗的型芯也可省去上芯头。
2)水平型芯
图4-13 水平型芯及芯头
型芯头与铸型型芯座之间应有1~ 的间隙(S1), 型芯头与铸型型芯座之间应有 ~4 mm的间隙 的间隙 , 以便于铸型的装配。 h=20~80mm。 以便于铸型的装配。 ~ 。
当铸件侧面需要加工时: 当铸件侧面需要加工时:
必须采用增加壁厚法; 必须采用增加壁厚法; 增加壁厚法 加工表面上的起模斜度 应在加工余量 上的起模斜度, 加工余量的基础上 加工表面上的起模斜度,应在加工余量的基础上 再给出斜度数值。 再给出斜度数值。
垂直于分型面的孔,当其孔径大于高度时, 可在模样上挖孔,造型起模后,在砂型上形成 吊砂或自带型芯,并由此形成铸件孔。 起模时模样上的孔内壁与型砂的摩擦力较 其外壁大些, 即α1、α2、α3 > α。
2、铸出孔和槽的大小
铸件上的加工孔是否铸出,从可能性、必要性、经济性方面考虑: 较大的孔、槽应当铸出, 较大的孔、槽应当铸出,以减少切削量和热节,提高铸件力学性能。 较小的孔和槽不必铸出, 较小的孔和槽不必铸出,留待以后加工更为经济。 >4时 也为不铸孔。 当孔深与孔径比L/D >4时,也为不铸孔。 正方孔、矩形孔或气路孔深且直径小一般不铸出。 孔深且直径小一般不铸出 正方孔、矩形孔或气路孔深且直径小一般不铸出。 弯曲孔,当不能机械加工时原则上必须铸出 必须铸出。 弯曲孔,当不能机械加工时原则上必须铸出。 正方孔、矩形孔的最短加工边必须大于 大于30 才能铸出。 正方孔、矩形孔的最短加工边必须大于 mm才能铸出。 才能铸出
起模斜度形成方式: 起模斜度形成方式: 增加厚度法、加减厚度法和减小厚度法。 增加厚度法、加减厚度法和减小厚度法。
增加铸件厚度
加减铸件厚度
Hale Waihona Puke 图4-10 起模斜度的形式减少铸件厚度
当侧面不加工时: 当侧面不加工时:
壁厚< 增加壁厚法 壁厚<8mm时,可采用增加壁厚法; 时 可采用增加壁厚法; 加减壁厚法 壁厚为8~ 壁厚为 ~16mm时,可采用加减壁厚法 时 可采用加减 壁厚> 减小壁厚法 壁厚>16mm时,可采用减小壁厚法 时 可采用减小
芯头的形式
a) 一般式
b) 联合芯头
c) 加长加大芯头,d) 型芯撑。 加长加大芯头, 型芯撑。
表4-4 铸件的最小铸出孔直径
生产批量 大量生产 成批生产 单件、 单件、小批生产 最小铸出孔直径 灰口铸铁件 12~15 ~ 15~30 ~ 30~50 ~ 铸钢件 -30~50 ~ 50
(1)若是加工孔,则孔的直径应为加上加工余量的数值; 若是加工孔,则孔的直径应为加上加工余量的数值; 有特殊要求的铸件例外。 (2)有特殊要求的铸件例外。
通常灰铸铁为0.7~1.0%, , 通常灰铸铁为 铸造碳钢为0.3~2.0%, , 铸造碳钢为 铝硅合金为0.8~1.2%, 锡青铜为 , 锡青铜为1.2~1.4%。 铝硅合金为 。
五、芯头及芯座
型芯的功用:是形成铸件的内腔、孔洞和形状复杂阻碍起模部 型芯的功用:是形成铸件的内腔、孔洞和形状复杂阻碍起模部 内腔 分的外形。 分的外形。 型芯头:是型芯的定位、支撑和排气的部分。 型芯头:是型芯的定位、支撑和排气的部分。 设计时需考虑:保证定位准确、能承受砂芯自身重量和 设计时需考虑:保证定位准确、能承受砂芯自身重量和 定位准确 自身重量 液态合金的冲击 浮力等外力的作用 冲击、 的作用, 液态合金的冲击、浮力等外力的作用,浇注时砂芯内部产生的 气体能顺畅引出铸型等 引出铸型等。 气体能顺畅引出铸型等。 制作时型芯及模样上须做出型芯头,对应造型时要在砂型中 制作时型芯及模样上须做出型芯头,对应造型时要在砂型中 型芯及模样上须做出型芯头 砂型 凹坑“座位” 使型芯定位。 做凹坑“座位”,使型芯定位。 主要确定: 主要确定: 定位作用; 1)定位作用; 固定作用; 芯头长度、斜度和间隙。 型芯头的作用: 型芯头的作用: 2)固定作用; 芯头长度、斜度和间隙。 3)排气作用。 长度取决于型芯的直径和长度 排气作用。
二、起模斜度
为了使模样(或型芯)便于从砂型(或芯盒)中取出, 为了使模样(或型芯)便于从砂型(或芯盒)中取出,凡垂直 于分型面的立壁在制造模样时必须留出一定的倾斜度, 于分型面的立壁在制造模样时必须留出一定的倾斜度,此倾斜 度称为起模斜度。 度称为起模斜度。 起模斜度的大小取决于: 起模斜度的大小取决于: 立壁的高度、造型方法、模样材料等 立壁的高度、造型方法、 因素,通常为 ~ ° 因素,通常为15’~3°。 立壁愈高,斜度愈小; 立壁愈高,斜度愈小; 机器造型应比手工造型小, 机器造型应比手工造型小, 木模应比金属模斜度大。 木模应比金属模斜度大。 为使型砂便于从模样内腔中脱出、以形成自带型芯, 为使型砂便于从模样内腔中脱出、以形成自带型芯,内壁的起 模斜度应比外壁大,通常为3° 模斜度应比外壁大,通常为 °~10°。 °
K=
L模-L件 -L L件
×100%
式中: L模──模样尺寸; 模样尺寸; 式中: 模样尺寸 L件──铸件尺寸。 铸件尺寸。 铸件尺寸
铸造收缩率主要取决于合金的种类 同时与铸件 合金的种类, 铸造收缩率主要取决于合金的种类,同时与铸件 的结构、大小、壁厚及收缩时受阻碍情况有关 有关。 的结构、大小、壁厚及收缩时受阻碍情况有关。
工艺参数
一、机械加工余量和铸孔
1. 加工余量
—指在铸件表面上留出的准备切削去的金属层厚度。 指在铸件表面上留出的准备切削去的金属层厚度。 指在铸件表面上留出的准备切削去的金属层厚度 零件图上所有标注粗糙度符号的表面均需机械加工,均应 零件图上所有标注粗糙度符号的表面均需机械加工, 标注机械加工余量 加工余量。 标注机械加工余量。 机械加工余量的具体数值取决于铸件的材料性质、造型方 机械加工余量的具体数值取决于铸件的材料性质、 材料性质 加工要求、生产批量、 法、加工要求、生产批量、铸件的结构的复杂程度和尺寸 及加工面在铸型中的位置等 在铸型中的位置等。 及加工面在铸型中的位置等。 加工余量大→浪费金属→ 加工余量大→浪费金属→切去了晶粒细致性能较好的铸件 表层。 表层。 余量过小→制品会因残留黑皮而报废,或者, 余量过小→制品会因残留黑皮而报废,或者,因铸件表层 影响甚至达不到加工要求。 过硬而加速刀具磨损→影响甚至达不到加工要求。
或宽度a( 或宽度 (mm)表示。 )表示。 用机械加工方法加工模 具时,用角度标注; 具时,用角度标注; 用手工加工模具时, 用手工加工模具时,用 图4-11 自带型芯的起模斜度 宽度标注。 宽度标注。
起模斜度在工艺图上用α
三、铸造圆角
制造模样时, 铸造圆角 — 制造模样时,壁的连接和转角处要做成 圆弧过度。 圆弧过度。 目的: 目的: 可使转角处不产生脆弱面; ① 可使转角处不产生脆弱面; 可减少应力集中; ② 可减少应力集中; 可避免产生冲砂、缩孔和裂纹。 ③ 可避免产生冲砂、缩孔和裂纹。 圆角半径一般约为相交两壁平均厚度的1/3~1/2。 圆角半径一般约为相交两壁平均厚度的 。 一般小型铸件: 一般小型铸件: 外圆角半径取2~ 外圆角半径取 ~8mm,内圆角半径取 ~16mm。 ,内圆角半径取4~ 。
芯头的分类: 芯头的分类:
1)垂直型芯; 垂直型芯; 芯头必须留有一定的斜度α。 芯头必须留有一定的斜度 。
图4-12 垂直型芯及芯头
下芯头的斜度应小些(5°~10°), 下芯头的斜度应小些 ° °, 上芯头的斜度为便于合箱应大些 (6°~15°)。h=15~150mm ° °。 ~ 型芯头与铸型型芯座之间应有 1~4 mm的间隙 ,以便于铸型的装配。 的间隙(S),以便于铸型的装配。 ~ 的间隙 形式:上下都有芯头;只有下芯头,无上芯头; 形式:上下都有芯头;只有下芯头,无上芯头; 上下都无芯头。 上下都无芯头。
图4-7 复杂内腔的型芯分块
为了增加型 芯稳定性, 芯稳定性,常 采用两个或多 个铸件共一个 型芯的方法。 型芯的方法。
图4-8 悬臂式型芯及挑担式型芯
四件合铸
图4-9 联合式型芯
第二节 铸造工艺参数的确定
加工余量 拔模斜度 铸造圆角 收缩率 型芯头及型芯座
5/16/2009 4:29 PM 6
三、铸造圆角
凝固特 性 热节、 热节、 充型
不同转角 处的热节
30
四、铸造收缩率