建设工程造价外文翻译文献编辑
工程造价毕业论文外文文献
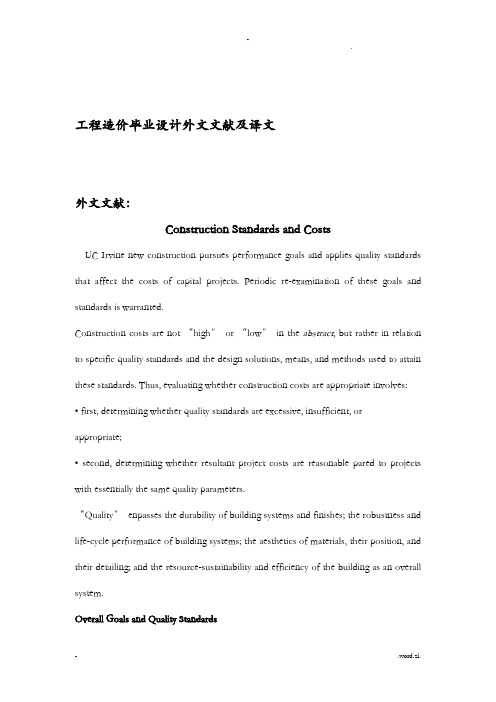
工程造价毕业设计外文文献及译文外文文献:Construction Standards and CostsUC Irvine new construction pursues performance goals and applies quality standards that affect the costs of capital projects. Periodic re-examination of these goals and standards is warranted.Co nstruction costs are not “high〞or “low〞in the abstract, but rather in relation to specific quality standards and the design solutions, means, and methods used to attain these standards. Thus, evaluating whether construction costs are appropriate involves: • first, determining whether quality standards are excessive, insufficient, or appropriate;• second, determining whether resultant project costs are reasonable pared to projects with essentially the same quality parameters.“Quality〞enpasses the durability of building systems and finishes; the robustness and life-cycle performance of building systems; the aesthetics of materials, their position, and their detailing; and the resource-sustainability and efficiency of the building as an overall system.Overall Goals and Quality StandardsUC Irvine, in order to support distinguished research and academic programs, builds facilities of high quality. As such, UC Irvine’s facilities aim to convey the “look and feel,〞as well as embody the inherent construction quality, of the best facilities of other UC campuses, leading public universities, and other research institutions with whom we pete for faculty, students, sponsored research, and general reputation.Since 1992, new buildings have been designed to achieve these five broad goals:1. New bu ildings must “create a place,〞rather than constitute stand-alone structures, forming social, aesthetic, contextually-sensitive relationships with neighboring buildings and the larger campus.2. New buildings reinforce a consistent design framework of classical contextual architecture, applied in ways that convey a feeling of permanence and quality and interpreted in ways that meet the contemporary and changing needs of a modern research university.3. New buildings employ materials, systems, and design features that will avoid the expense of major maintenance (defined as >1 percent of value)for twenty years.4. New buildings apply “sustainability〞principles -- notably, outperforming Title 24 (California’s energy code) by at least 20 percent.5. Capital construction projects are designed and delivered within theapproved project budget, scope, and schedule.UC Irvine’s goals for sustainable materials and energy performance were adopted partly for environmental reasons, and partly to reverse substantial operating budget deficits. The latter problems included a multi-million dollar utilities deficit that was growingrapidly in the early ‘90s, and millions of dollars of unfunded major maintenance that was emerging prematurely in buildings only 10-20 years old. Without the quality and performance standards adopted in 1992, utilities deficits and unfunded major maintenance costs would have exceeded $20 million during the past decade, and these costs would still be rising out-of-control.UC Irvine’s materials standards, building systems standards, sustainability and energy efficiency criteria, and site improvements all add cost increments that can only be afforded through aggressive cost management. Institutions that cannot manage capital costs tend to build projects that consume excessive energy, that cost a lot to maintain, that suffer premature major maintenance costs, and that require high costs to modify. Such problems tend to pound and spiral downward into increasingly costly consequences.Every administrator with facilities experience understands this dynamic. Without effective construction cost management, quality would suffer and UC Irvine would experience all of these problems.The balance of this document outlines in greater detail the building performance criteria and quality standards generally stated above, organized according to building systems ponent classes. Each section discusses key cost-drivers, cost-control strategies, and important cost trade-offs. Design practices cited are consistently applied (although some fall short of hard and fast “rules〞).Building Organization and MassingConstruction cost management starts with the fundamentals of building organization andmassing. UC Irvine’s new structures’ floor plates tend to have length-to-width ratios<1.5, to avoid triggering disproportionate costs of external cladding, circulation, and horizontal mechanical distribution. Our new buildings tend to be at least three floors high -- taller if floor plate areas do not dip below a cost-effective threshold, and generally taller in the case of non-laboratory buildings (but not so tall that a high-rise cost penalty is incurred). Other design ratios are observed, such as exterior cladding area/floor area <0.5, and roof+foundation area/floor area <0.4.Architectural articulation is generally achieved through textured or enriched materials,integral material detailing (such as concrete reveal patterning), and applied detailing (e.g.,2window frames and sills), particularly at the building base. Large-scale articulation is concentrated at the roofline (e.g., shaped roof forms) and at the pedestrian level (e.g.,arcades), where it will “create the biggest bang for the buck,〞rather than through modulating the building form, itself. This is more than a subtle design philosophy, as the cost impact is substantial.Lab buildings pleted in the past decade separate laboratory and non-laboratory functions into distinct, adjoined structures (although such a building may look like one structure). Consolidated non-laboratory functions include faculty, departmental, staff,post-doc, and graduate student offices; restrooms; circulation (elevators, lobbies, primary stairways); classrooms, seminar rooms, conference rooms, and social areas designed tofoster interaction and to provide a safe area for eating and drinking; dry labs and dry lab support functions; and general administrative support.Consolidating these functions into a separate structure provides considerable cost savings:lower-cost HVAC (heating/ventilation/air-conditioning) system, wider column spacing, lower floor stiffness (less stringent vibration criterion), lower floor-loading,fewer fire-control features and other code requirements, steel-framed or steel/concrete hybrid structural system with concrete flat-slab flooring system, smaller footings, and(typically) curtain wall fenestration. This approach usually enables offices to have operable windows.This two-building approach can be seen clearly at Gillespie Neurosciences Building, the Sprague Building, Hewitt Hall, and the UCI Medical Center Health Sciences Laboratory,where consolidating and separating non-laboratory functions saved 7-10 percent in overall construction costs and 15 percent/year in energy expense. (The non-laboratory building incurs a small fraction of the energy expense of the laboratory block.)A set of design strategies, applied in bination, has proven effective in controlling the cost of laboratories:• Utilizing a consistent lab module• Utilizing a reasonable vibration criterion and locating ultra-sensitive conditions at-grade or employing benchtop vibration isolation• Using 22 ft. X 22 ft. column-spacing• Concentrating fume hoods and utility risers into a central “wet zone,〞thus limiting horizontal mechanical distribution• Concentrating laboratory support areas into the central core of a laboratory structure, where utilities are available but daylight is not needed, thus enablinglab structures to be 110-132 feet wide• Utilizing dual-usage circulation/equipment cross-corridors through this central lab support zone, with sufficient width (typically 11 feet) to line the corridors with shared equipment while providing cross-circulation through the lab support zone• Utilizing open laboratory layout with one or more “ghost〞corridors for intra lab circulation• And, most importantly, concentrating non-laboratory functions into an adjoining, lower-cost structure (as discussed in detail above).To further control laboratory construction costs, non-standard fume hood sizes are minimized, “generic〞lab casework is specified, laboratory-grade movable tables substitute for fixed casework in some lab bays, building DI systems provide intermediate water quality (with localized water purity polishing in the lab, rather than building-wide),facility-wide piped services do not include gases that can be cost-effectively provided locally via canisters, and glass-wash facilities are consolidated -- typically, one glass wash facility for an entire laboratory building.Finally, our design philosophy leans toward generic, modular laboratories supported by a robust building infrastructure, rather than highly customized spaces with limited capacity to make later changes. This is an important trade off. Although some post-occupancy expenses may be necessary to “fine-tune〞a laboratory to a PI’s requirements, building infrastructure elements – typically over sized twenty percent, including HVAC supply ducts, exhaust system capacity, emergency generator capacity, and electric risers and service capacity – seldom limit the ability to modify labs to meet researcher needs.Structural and Foundation SystemsFor both cost-benefit reasons and past seismic performance, UC Irvine favors concrete shear wall or steel braced-frame structural systems. The correlating foundation systems depend on site-specific soil conditions. Past problems with undiscovered substrates and uncharacterized soil conditions are minimized through extensive, pre-design soil-testing. This minimizes risk to both the University and the design/build contractor.When feasible, design/build contractors are allowed flexibility to propose alternate structural or seismic-force systems. All structural system designs must pass a peer review, according to Regents’ policy. This process results in conservative structural design, and an associated cost premium. However, the seismic performance of University of California buildings constructed since this policy went into effect in 1975 appears to substantiate the value of the Regents’ Seismic Revi ew Policy.Structural vibration is carefully specified in research buildings where vibration-sensitive protocols and conditions must be maintained on above-grade floors. The most cost effective tools to control vibration are generally employed: first, to program vibration sensitive procedures at on-grade locations or to isolate them at the bench; second, to space columns at a distance that does not entail excessive structural costs. In laboratory 4buildings we typically utilize 22 ft. X 22 ft. column-spacing. Conversely, where vibration is not problematic a beam/column system can be cost-optimized and lighter floor loading can be tolerated. Design/build contractors are, accordingly, allowed more flexibility under such conditions.To control costs, UC Irvine avoids use of moment-resisting structures; unconventionalseismic systems; non-standard structural dimensions; inconsistent, unconventional, or non-stacking structural modules; and non-standard means and methods.Roofs and FlashingsUC Irvine specifies 20 year roofing systems and stainless steel or copper flashings whenever possible. At minimum, we specify hot-dip galvanized flashings.Why this emphasis on flashings? Our roof replacement projects typically double in cost when the old roofing is torn off and it is determined that the flashings have deteriorated. Moreover, many roof leaks of recent years have been due to faulty flashings, rather than roofing membranes or coatings, per se. Saving money on flashings is false economy. Another special roofing expe nse we may have to incur in order to attain the Regents’ Green Building Policy is that of reflective roofing. It is too early to understand the potential cost impact.中文翻译:建立标准和本钱加州大学欧文分校新建筑追求性能目标和适用的质量标准,影响资本本钱的工程。
建筑造价中英文对照外文翻译文献

建筑造价中英文对照外文翻译文献(文档含英文原文和中文翻译)The Cost of Building Structure1. IntroductionThe art of architectural design was characterized as one of dealing comprehensively with a complex set of physical and nonphysical design determinants. Structural considerations were cast as important physical determinants that should be dealt with in a hierarchical fashion if they are to have a significant impact on spatial organization and environmental control design thinking.The economical aspect of building represents a nonphysical structural consideration that, in final analysis, must also be considered important. Cost considerations are in certain ways a constraint to creative design. But this need not beso. If something is known of the relationship between structural and constructive design options and their cost of implementation, it is reasonable to believe that creativity can be enhanced. This has been confirmed by the authors’ observation that most enhanced. This has been confirmed by the authors’observation that most creative design innovations succeed under competitive bidding and not because of unusual owner affluence as the few publicized cases of extravagance might lead one to believe. One could even say that a designer who is truly creative will produce architectural excellence within the constraints of economy. Especially today, we find that there is a need to recognize that elegance and economy can become synonymous concepts.Therefore, in this chapter we will set forth a brief explanation of the parameters of cost analysis and the means by which designers may evaluate the overall economic implications of their structural and architectural design thinking.The cost of structure alone can be measured relative to the total cost of building construction. Or, since the total construction cost is but a part of a total project cost, one could include additional consideration for land(10~20percent),finance and interest(100~200 percent),taxes and maintenance costs (on the order of20 percent).But a discussion of these so-called architectural costs is beyond the scope of this book, and we will focus on the cost of construction only.On the average, purely structural costs account for about 25 percent of total construction costs, This is so because it has been traditional to discriminate between purely structural and other so-called architectural costs of construction. Thus, in tradition we find that architectural costs have been taken to be those that are not necessary for the structural strength and physical integrity of a building design.“Essential services”forms a third construction cost category and refers to the provision of mechanical and electrical equipment and other service systems. On the average, these service costs account for some 15 to 30 percent of the total construction cost, depending on the type of building. Mechanical and electrical refers to the cost of providing for air-conditioning equipment and he means on air distribution as well as other services, such as plumbing, communications, and electrical light and power.The salient point is that this breakdown of costs suggests that, up to now, an average of about 45 to 60 percent of the total cost of constructing a typical design solution could be considered as architectural. But this picture is rapidly changing.With high interest costs and a scarcity of capital, client groups are demanding leaner designs. Therefore, one may conclude that there are two approaches the designer may take towards influencing the construction cost of building.The first approach to cost efficiency is to consider that wherever architectural and structural solutions can be achieved simultaneously, a potential for economy is evident. Since current trends indicate a reluctance to allocate large portions of a construction budget to purely architectural costs, this approach seems a logical necessity. But, even where money is available, any use of structure to play a basic architectural role will allow the nonstructural budget to be applied to fulfill other architectural needs that might normally have to be applied to fulfill other architectural needs that might normally have to be cut back. The second approach achieves economy through an integration of service and structural subsystems to round out one’s effort to produce a total architectural solution to a building design problem.The final pricing of a project by the constructor or contractor usually takes a different form. The costs are broken down into (1) cost of materials brought to the site, (2)cost of labor involved in every phase of the construction process, (3)cost of equipment purchased or rented for the project, (4)cost of management and overhead, and(5) profit. The architect or engineer seldom follows such an accurate path but should perhaps keep in mind how the actual cost of a structure is finally priced and made up.Thus, the percent averages stated above are obviously crude, but they can suffice to introduce the nature of the cost picture. The following sections will discuss the range of these averages and then proceed to a discussion of square footage costs and volume-based estimates for use in rough approximation of the cost of building a structural system.2. Percentage EstimatesThe type of building project may indicate the range of percentages that can be allocated to structural and other costs. As might be expected, highly decorative or symbolic buildings would normally demand the lowest percentage of structural costs as compared to total construction cost. In this case the structural costs might drop to 10~15percent of the total building cost because more money is allocated to the so-called architectural costs. Once again this implies that the symbolic components are conceived independent of basic structural requirements. However, where structure and symbolism are more-or-less synthesized, as with a church or Cathedral, thestructural system cost can be expected to be somewhat higher, say, 15and20 percent (or more).At the other end of the cost scale are the very simple and nonsymbolic industrial buildings, such as warehouses and garages. In these cases, the nonstructural systems, such as interior partition walls and ceilings, as will as mechanical systems, are normally minimal, as is decoration, and therefore the structural costs can account for60 to 70 percent, even 80 percent of the total cost of construction.Buildings such as medium-rise office and apartment buildings(5~10 stories)occupy the median position on a cost scale at about 25 percent for structure. Low and short-span buildings for commerce and housing, say, of three or four stories and with spans of some 20 or 30 ft and simple erection requirements, will yield structural costs of 15~20 percent of total building cost.Special-performance buildings, such as laboratories and hospitals, represent another category. They can require long spans and a more than average portion of the total costs will be allocated to services (i.e., 30~50 percent), with about 20 percent going for the purely structural costs. Tall office building (15 stories or more) and/or long-span buildings (say, 50 to 60 ft) can require a higher percentage for structural costs (about 30to 35percent of the total construction costs),with about 30 to 40 percent allocated to services.In my case, these percentages are typical and can be considered as a measure of average efficiency in design of buildings. For example, if a low, short-span and nonmonumental building were to be bid at 30 percent for the structure alone, one could assume that the structural design may be comparatively uneconomical. On the other hand, the architect should be aware of the confusing fact that economical bids depend on the practical ability of both the designer and the contractor to interpret the design and construction requirements so that a low bid will ensue. Progress in structural design is often limited more by the designer’s or contractor’slack of experience, imagination, and absence of communication than by the idea of the design. If a contractor is uncertain, he will add costs to hedge the risk he will be taking. It is for this reason that both the architect and the engineer should be well-versed in the area of construction potentials if innovative designs ate to be competitively bid. At the least the architect must be capable of working closely with imaginative structural engineers, contractors and even fabricators wherever possible even if the architecture is very ordinary. Efficiency always requires knowledge and above all imagination, andthese are essential when designs are unfamiliar.The foregoing percentages can be helpful in approximating total construction costs if the assumption is made that structural design is at least of average (of typical) efficiency. For example, if a total office building construction cost budget is ﹩5,000,000,and 25 percent is the “standard”to be used for structure, a projected structural system should cost no more than ﹩1,250,000.If a very efficient design were realized, say, at 80 percent of what would be given by the “average” efficient design estimate stated above the savings,(20 percent),would then be﹩250,000 or 5 percent of total construction costs ﹩5,000,000.If the ﹩5,000,000 figure is committed, then the savings of ﹩250,000 could be applied to expand the budget for “other” costs.All this suggests that creative integration of structural (and mechanical and electrical) design with the total architectural design concept can result in either a reduction in purely construction design concept can result in either a reduction in purely construction costs or more architecture for the same cost. Thus, the degree of success possible depends on knowledge, cleverness, and insightful collaboration of the designers and contractors.The above discussion is only meant to give the reader an overall perspective on total construction costs. The following sections will now furnish the means for estimating the cost of structure alone. Two alternative means will be provided for making an approximate structural cost estimate: one on a square foot of building basis, and another on volumes of structural materials used. Such costs can then be used to get a rough idea of total cost by referring to the “standards” for efficient design given above. At best, this will be a crude measure, but it is hoped that the reader will find that it makes him somewhat familiar with the type of real economic problems that responsible designers must deal with. At the least, this capability will be useful in comparing alternative systems for the purpose of determining their relative cost efficiency.3. Square-foot EstimatingAs before, it is possible to empirically determine a “standard” per-square-foot cost factor based on the average of costs for similar construction at a given place and time. more-or-less efficient designs are possible, depending on the ability of the designer and contractor to use materials and labor efficiently, and vary from the average.The range of square-foot costs for “normal” structural systems is ﹩10 to ﹩16psf. For example, typical office buildings average between ﹩12 and ﹩16 psf, and apartment-type structures range from ﹩10 to ﹩14.In each case, the lower part of the range refers to short spans and low buildings, whereas the upper portion refers to longer spans and moderately tall buildings.Ordinary industrial structures are simple and normally produce square-foot costs ranging from ﹩10 to ﹩14,as with the more typical apartment building. Although the spans for industrial structures are generally longer than those for apartment buildings, and the loads heavier, they commonly have fewer complexities as well as fewer interior walls, partitions, ceiling requirements, and they are not tall. In other words, simplicity of design and erection can offset the additional cost for longer span lengths and heavier loads in industrial buildings.Of course there are exceptions to these averages. The limits of variation depend on a system’s complexity, span length over “normal” and special loading or foundation conditions. For example, the Crown Zellerbach high-rise bank and office building in San Francisco is an exception, since its structural costs were unusually high. However, in this case, the use of 60 ft steel spans and free-standing columns at the bottom, which carry the considerable earthquake loading, as well as the special foundation associated with the poor San Francisco soil conditions, contributed to the exceptionally high costs. The design was also unusual for its time and a decision had been made to allow higher than normal costs for all aspects of the building to achieve open spaces and for both function and symbolic reasons. Hence the proportion of structural to total cost probably remained similar to ordinary buildings.The effect of spans longer than normal can be further illustrated. The “usual” floor span range is as follows: for apartment buildings,16 to 25 ft; for office buildings,20 to 30 ft; for industrial buildings,25 to 30 ft loaded heavily at 200 to 300 psf; and garage-type structures span,50 to 60 ft, carrying relatively light(50~75 psf) loads(i.e., similar to those for apartment and office structures).where these spans are doubled, the structural costs can be expected to rise about 20 to 30 percent.To increased loading in the case of industrial buildings offers another insight into the dependency of cost estimates on “usual” standards. If the loading in an industrial building were to be increased to 500psf(i.e., two or three times), the additional structural cost would be on the order of another 20 to 30 percent.The reference in the above cases is for floor systems. For roofs using efficient orthotropic (flat) systems, contemporary limits for economical design appear to be onthe order of 150 ft, whether of steel or prestressed concrete. Although space- frames are often used for steel or prestressed concrete. Although space-frames are often used for steel spans over 150 ft the fabrication costs begin to raise considerably.At any rate, it should be recognized that very long-span subsystems are special cases and can in themselves have a great or small effect on is added, structural costs for special buildings can vary greatly from design to design. The more special the form, themore that design knowledge and creativity, as well as construction skill, will determine the potential for achieving cost efficiency.4. Volume-Based EstimatesWhen more accuracy is desired, estimates of costs can be based on the volume of materials used to do a job. At first glance it might seem that the architect would be ill equipped to estimate the volume of material required in construction with any accuracy, and much less speed. But it is possible, with a moderate learning effort, to achieve some capability for making such estimates.V olume-based estimates are given by assigning in-place value to the pounds or tons of steel, or the cubic yards of reinforced or prestressed concrete required to build a structural system. For such a preliminary estimate, one does not need to itemize detailed costs. For example, in-place concrete costs include the cost of forming, falsework, reinforcing steel, labor, and overhead. Steel includes fabrication and erection of components.Costs of structural steel as measured by weight range from ﹩0.50 to ﹩0.70 per pound in place for building construction. For low-rise buildings, one can use stock wide-flange structural members that require minimum fabrication, and the cost could be as bow as ﹩0.50 per pound. More complicated systems requiring much cutting and welding(such as a complicated steel truss or space-frame design) can go to ﹩0.70 per pound and beyond. For standard tall building designs (say, exceeding 20 stories),there would typically be about 20 to 30 pounds of steel/psf, which one should wish not to exceed. A design calling for under 20 psf would require a great deal of ingenuity and the careful integration of structural and architectural components and would be a real accomplishment.Concrete costs are volumetric and should range from an in-place low of ﹩150 per cu yd for very simple reinforced concrete work to ﹩300 per cu yd for expensive small quantity precast and prestressed work. This large range is due to the fact that the contributing variables are more complicated, depending upon the shape of the precisecomponents, the erection problems, and the total quantity produced.Form work is generally the controlling factor for any cast-in-place concrete work. Therefore, to achieve a cost of ﹩150 per cu yd, only the simplest of systems can be used, such as flat slabs that require little cutting and much reuse of forms. Where any beams are introduced that require special forms and difficulty in placement of concrete and steel bars, the range begins at ﹩180 per cu yd and goes up to ﹩300.Since, in a developed country, high labor costs account for high forming costs, this results in pressure to use the simplest and most repetitive of systems to keep costs down. It become rewarding to consider the possibility of mass-produced precast and prestressed components, which may bring a saving in costs and\or construction completion time. The latter results in savings due to lower construction financing costs for the contractor plus quicker earnings for the owner.To summarize, the range of cost per cubic yard of standard types of poured-in-place concrete work will average from $150 to $250, the minimum being for simple reinforced work and the maximum for moderately complicated post tensioned work. This range is large and any estimate that ignores the effect of variables above will be commensurately inaccurate.5.SummaryThe estimate and economical design of structure building are important and essential work, which should be valued by all architects and engineers and others. Better you do it, more profit you will receive from it!建筑结构的成本1.前言众所周知,建筑物的结构设计是一个相当复杂的过程,其中既包含处理很多物质因素,又考虑诸多非物质方面的因素。
工程造价论文中英文资料对照外文翻译

工程造价论文中英文资料对照外文翻译This paper focuses on the risk analysis of nal n XXX the unique risks associated with nal n projects。
including political。
economic。
and cultural risks。
It then outlines the XXX a risk analysis。
including risk n。
risk assessment。
and XXX.nXXX。
XXX by a range of unique risks that must be XXX for risk management in nal n projects.Unique Risks Associated with nal n ProjectsXXX are subject to a range of unique risks that are not present in XXX。
economic uncertainty。
cultural differences。
and legal XXX can impact the project。
Economic uncertainty XXX。
n。
or XXX project stakeholders。
while legal issues XXX.Risk Analysis ProcessThe risk analysis process involves several steps。
including risk n。
risk assessment。
and XXX all potential risks that couldimpact the project。
This can be done through brainstorming ns。
工程造价专业外文文献翻译(中英文对照教学内容
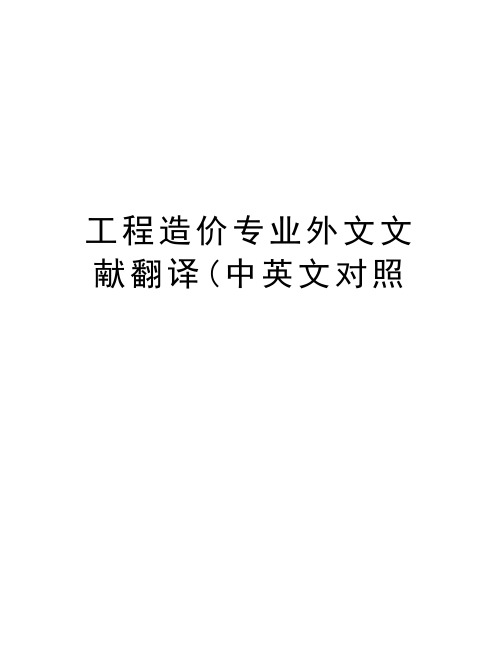
工程造价专业外文文献翻译(中英文对照外文文献:Project Cost Control: The Way it WorksBy R. Max WidemanIn a recent consulting assignment we realized that there was some lack of understanding of the whole system of project cost control, how it is setup and applied. So we decided to write up a description of how it works. Project cost control is not that difficult to follow in theory.First you establish a set of reference baselines. Then, as work progresses, you monitor the work, analyze the findings, forecast the end results and compare those with the reference baselines. If the end results are not satisfactory then you make adjustments as necessary to the work in progress, and repeat the cycle at suitable intervals. If the end results get really out of line with the baseline plan, you may have to change the plan. More likely, there will be (or have been) scope changes that change the reference baselines which means that every time that happens you have to change the baseline plan anyway.But project cost control is a lot more difficult to do in practice, as is evidenced by the number of projects that fail to contain costs. It also involves a significant amount of work, as we shall see, and we might as well start at the beginning. So let us follow the thread of project cost control through the entire project life span.And, while we are at it, we will take the opportunity to point out the proper places for several significant documents. These include the Business Case, the Request for (a capital) Appropriation (for execution), Work Packages and the Work Breakdown Structure, the Project Charter (or Brief), the Project Budget or Cost Plan, Earned Value and the Cost Baseline. All of these contribute to the organization's ability to effectively control project costs.FootnoteI am indebted to my friend Quentin Fleming, the guru of Earned Value, for checking and correcting my work on this topic.The Business Case and Application for (execution) FundingIt is important to note that project cost control is most effective when the executive management responsible has a good understanding of how projects should unfold through the project life span. This means that they exercise their responsibilities at the key decision pointsbetween the major phases. They must also recognize the importance of project risk management for identifying and planning to head off at least the most obvious potential risk events.In the project's Concept Phase• Every project starts with someone identifying an opportunity or need. That is usually someone of importance or influence, if the project is to proceed, and that person often becomes theproject's sponsor.• To determine the suitability of the potential project, most organizations call for the preparation of a "Business Case" and its "Order of Magnitude" cost to justify the value of the project so that it can be compared with all the other competing projects. This effort is conducted in the Concept Phase of the project and is done as a part of the organization's management of the entire project portfolio.• The cost of the work of preparing the Business Case is usually covered by corporate management overhead, but it may be carried forward as an accounting cost to the eventual project. No doubt because this will provide a tax benefit to the organization. The problem is, how do you then account for all the projects that are not so carried forward?• If the Business case has sufficient merit, approval will be given to proceed to a Development and Definition phase.In the project's Development or Definition Phase• The objective of the Development Phase is to establish a good understanding of the work involved to produce the required product, estimate the cost and seek capital funding for the actual execution of the project.• In a formalized set ting, especially where big projects are involved, this application for funding is often referred to as a Request for (a capital) Appropriation (RFA) or Capital Appropriation Request (CAR).• This requires the collection of more detailed requirements and da ta to establish what work needs to be done to produce the required product or "deliverable". From this information, a plan is prepared in sufficient detail to give adequate confidence in a dollar figure to be included in the request.• In a less formalized setting, everyone just tries to muddle through.Work Packages and the WBSThe Project Management Plan, Project Brief or Project Charter• If the deliverable consists of a number of different elements, these are identified and assembled into Work Packages (WPs) and presented in the form of a Work Breakdown Structure (WBS). • Each WP involves a set of activities, the "work" that is planned and scheduled as a part of the Project Management Plan. Note, however, that the planning will still be at a relatively high level, and more detailed planning will be necessary during execution if the project is given the go ahead. • This Project Management Plan, by the way, should become the "bible" for the execution phase of the project and is sometimes referred to as the "Project Brief" or the "Project Charter".• The cost of doing the various activities is then estimated and these estimated costs are aggregated to determine the estimated cost of the WP. This approach is known as "detailed estimating" or "bottom up estimating". There are other approaches to estimating that we'll cometo in a minute. Either way, the result is an estimated cost of the total work of the project.Note: that project risk management planning is an important part of this exercise. This should examine the project's assumptions and environmental conditions to identify any weaknesses in the plan thus far, and identify those potential risk events that warrant attention for mitigation. This might take the form of specific contingency planning, and/or the setting aside of prudent funding reserves.Request for capitalConverting the estimate• However, an estimate of the work alone is not sufficient for a capital request. To arrive at a capital request some conversion is necessary, for example, by adding prudent allowances such as overheads, a contingency allowance to cover normal project risks and management reserves to cover unknowns and possible scope changes.• In addition, it may be necessary to convert the estimating data into a financial accou nting format that satisfies the corporate or sponsor's format for purposes of comparison with other projects and consequent funding approval.• In practice all the data for the type of "bottom up" approach just described may not be available. In this case alternative estimating approaches are adopted that provide various degrees of reliability in a "top down" fashion. For example:Order of Magnitude estimate – a "ball park" estimate, usually reserved for the concept phase onlyAnalogous estimate – an estimate based on previous similar projectsParametric estimate – an estimate based on statistical relationships in historical data• Whichever approach is adopted, hopefully the sum thus arrived at will be approved in full and proves to be satisfactory! This is the trigger to start the Execution Phase of the projectNote: Some managements will approve some lesser sum in the mistaken belief that this will help everyone to "sharpen their pencils" and "work smarter" for the benefit of the organization. This is a mistaken belief because management has failed to understand the nature of uncertainty and risk in project work. Consequently, the effect is more likely to result in "corner cutting" with an adverse effect on product quality, or reduced product scope or functionality. This often leads to a "game" in which estimates are inflated so that management can adjust them downwards. But to be fair, management is also well aware that if money is over allocated, it will get spent anyway. The smart thing for managements to do is to set aside contingent reserve funds, varying with the riskiness of the project, and keep that money under careful control.Ownership of approved capital• If senior management approves the RFA as presented, the sum in question becomes the responsibility of the designated project sponsor. However, if the approved capital request includes allowances such as a "Management Reserve", this may or may not be passed on to the project's sponsor, depending on the policies of the organization.• For the approved RFA, the project sponsor will, in turn, further delegate expenditure authority to the project's project manager and will likely not include any of the allowances. An exception might be the contingency allowances to cover the normal variations in work performance.• The net sum thus arrived at constitutes the project manager's Approved Project Budget.Note: If management does not approve the RFA, you should not consider this a project failure. Either the goals, objectives, justification and planning need rethinking to increase the value of the project's deliverables, or senior management simply has higher priorities elsewhere for the available resources and funding.The Project's Execution PhaseThe project manager's Project Budget responsibility• Once this Approved Project Budget is released to the project manager, a reverse process must take place to convert it into a working control document. That is, the money available must be divided amongst the various WBS WPs that, by the way, have probably by now been upgraded! This results in a project execution Control Budget or Project Baseline Budget, or simply, the Project Budget. In some areas of project management application it is referred to as a Project Cost Plan.• On a large project where differe nt corporate production divisions are involved, there may be a further intermediate step of creating "Control Accounts" for the separate divisions, so that each division subdivides their allocated money into their own WBS WPs.• Observe that, since the tot al Project Budget received formal approval from Executive Management, you, as project manager, must likewise seek and obtain from Executive Management, via the project's sponsor, formal approval for any changes to the total project budget. Often this is only justified and accepted on the basis of a requested Product Scope Change.• In such a case the project's sponsor will either draw down on the management reserve in his or her possession, or submit a supplementary RFA to upper management.• Now that we ha ve the Project Budget money allocated to Work Packages we can further distribute it amongst the various activities of each WP so that we know how much money we have as a "Baseline" cost for each activity.• This provides us with the base of reference for t he cost control function. Of course, depending on the circumstances the same thing may be done at the WP level but the ability to control is then at a higher and coarser level.Use of the Earned Value technique• If we have the necessary details another control tool that we can adopt for monitoring ongoing work is the "Earned Value" (EV) technique. This is a considerable art and science that you must learn about from texts dedicated to the subject.• But essentially, you take the costs of the schedule act ivities and plot them as a cumulative total on the appropriate time base. Again you can do this at the activity level, WP level or the whole project level. The lower the level the more control information you have available but the more work you get involved in.The Cost Baseline• This planned reference S-curve is sometimes referred to as the "Cost Baseline", typically in EV parlance. That is, it is the "Budgeted Cost of Work Scheduled" (BCWS), or more simply the "Planned Value" (PV).• Observe that you need to modify this Cost Baseline every time there is an approved scope change that has cost and/or schedule implications and consequently changes the project's Approved Project Budget.• Now, as the work progresses, you can plot the "Actual Cost of Work Per formed" (ACWP or simply "Actual Cost" - AC).• You can plot other things as well, see diagram referred to above, and if you don't like what you see then you need to take "Corrective Action".CommentaryThis whole process is a cyclic, situational operation and is probably the source of the term "cycle" in the popularly misnamed "project life cycle".As an aside, the Earned Value pundits offer various other techniques within the EV process designed to aid in forecasting the final result, that is, the "Estimate At Completion" (EAC). EAC is what you should really be interested in because it is the only constant in a moving project. Therefore, these extended EV techniques must be considered in the same realm of accuracy as top-down estimating. They are useful, but only if you recognize the limitations and know what you are doing!But, as we said at the beginning, it is a lot more difficult to do in practice – and involves a significant amount of work. But, let's face it, that's what project managers are hired for, right?中文译文:项目成本控制:它的工作方式R.马克斯怀德曼我们在最近的咨询任务中意识到,对于整个项目成本控制体系是如何设置和应用的这个问题,我们仍有一些缺乏了解。
工程造价外文文献
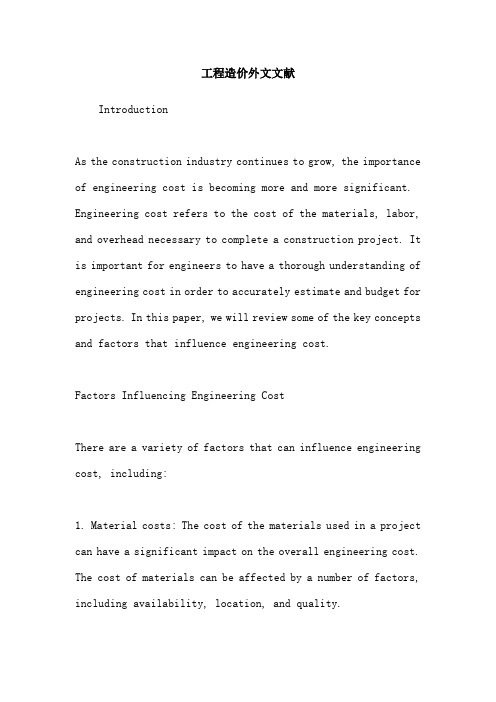
工程造价外文文献IntroductionAs the construction industry continues to grow, the importance of engineering cost is becoming more and more significant. Engineering cost refers to the cost of the materials, labor, and overhead necessary to complete a construction project. It is important for engineers to have a thorough understanding of engineering cost in order to accurately estimate and budget for projects. In this paper, we will review some of the key concepts and factors that influence engineering cost.Factors Influencing Engineering CostThere are a variety of factors that can influence engineering cost, including:1. Material costs: The cost of the materials used in a project can have a significant impact on the overall engineering cost. The cost of materials can be affected by a number of factors, including availability, location, and quality.2. Labor costs: The cost of labor is another key factor in engineering cost. Labor costs can be influenced by the level of expertise required for the project, as well as the location and availability of labor.3. Overhead costs: Overhead costs include expenses such as rent, utilities, and insurance. These costs can vary depending on the size and location of the project.4. Design complexity: The complexity of the project design can also impact engineering cost. More complex designs may require specialized materials and labor, which can increase costs.5. Project location: The location of the project can also impact engineering cost. Projects in urban areas may have higher labor and material costs, while projects in rural areas may have higher transportation costs.6. Timefra The timeframe for completing a project can also influence engineering cost. Projects that need to be completed quickly may require additional labor and materials, which can increase costs.ConclusionEngineering cost is an important factor to consider when planning and budgeting for construction projects. By understanding the key factors that can influence engineering cost, engineers can develop more accurate estimates and budgets. Additionally, by monitoring engineering cost throughout the project, engineers can identify potential cost overruns and take corrective action to keep the project on track.。
工程造价中英文对照外文翻译文献

中英文对照翻译Risk Analysis of the International Construction ProjectABSTRACTThis analysis used a case study methodology to analyse the issues surrounding the partial collapse of the roof of a building housing the headquarters of the Standards Association of Zimbabwe (SAZ). In particular, it examined the prior roles played by the team of construction professionals. The analysis revealed that the SAZ‟s traditional construction project was generally characterized by high risk. There was a clear indication of the failure of a contractor and architects in preventing and/or mitigating potential construction problems as alleged by the plaintiff. It was reasonable to conclude that between them the defects should have been detected earlier and rectified in good time before the partial roof failure. It appeared justified for the plaintiff to have brought a negligence claim against both the contractor and the architects. The risk analysis facilitated, through its multi-dimensional approach to a critical examination of a construction problem, the identification of an effective risk management strategy for future construction projects. It further served to emphasize the point that clients are becoming more demanding, more discerning, and less willing to accept risk without recompense. Clients do not want surprise, and are more likely to engage in litigation when things go wrong.KEY WORDS:Arbitration, claims, construction, contracts, litigation, project and risk The structural design of the reinforced concrete elements was done by consulting engineers Knight Piesold (KP). Quantity surveying services were provided by Hawkins, Leshnick & Bath (HLB). The contract was awarded to Central African Building Corporation (CABCO) who was also responsible for the provision of a specialist roof structure using patented “gang nail” roof trusses. The building construction proceeded to completion and was handed over to the owners on Sept. 12, 1991. The SAZ took effective occupation of the headquarters building without a certificate of occupation. Also, the defects liability period was only three months .The roof structure was in place 10 years before partial failure in December 1999. The building insurance coverage did not cover enough, the City of Harare, a government municipality, issued the certificate of occupation 10 years after occupation, and after partial collapse of the roof .At first the SAZ decided to go to arbitration, but this failed to yield an immediate solution. The SAZ then decided to proceed to litigate in court and to bring a negligence claim against CABCO. The preparation for arbitration was reused for litigation. The SAZ‟s quantified losses stood at approximately $ 6 million in Zimbabwe dollars (US $1.2m) .After all parties had examined the facts and evidence before them, it became clear that there was a great probability that the courts might rule that both the architects and the contractor were liable. It was at this stage that the defendants‟ lawyers requested that the matter be settled out of court. The plaintiff agreed to this suggestion, with the terms of the settlement kept confidential .The aim of this critical analysis was to analyse the issues surrounding the partial collapse of the roof of the building housing the HQ of Standard Association of Zimbabwe. It examined the prior roles played by the project management function and construction professionals in preventing/mitigating potential construction problems. It further assessed the extent to which the employer/client and parties to a construction contract are able to recover damages under that contract. The main objective of this critical analysis was to identify an effective risk management strategy for future construction projects. The importance of this study is its multidimensional examination approach.Experience suggests that participants in a project are well able to identify risks based on their own experience. The adoption of a risk management approach, based solely in past experience and dependant on judgement, may work reasonably well in a stable low risk environment. It is unlikely to be effective where there is a change. This is because change requires the extrapolation of past experience, which could be misleading. All construction projects are prototypes to some extent and imply change. Change in the construction industry itself suggests that past experience is unlikely tobe sufficient on its own. A structured approach is required. Such a structure can not and must not replace the experience and expertise of the participant. Rather, it brings additional benefits that assist to clarify objectives, identify the nature of the uncertainties, introduces effective communication systems, improves decision-making, introduces effective risk control measures, protects the project objectives and provides knowledge of the risk history .Construction professionals need to know how to balance the contingencies of risk with their specific contractual, financial, operational and organizational requirements. Many construction professionals look at risks in dividually with a myopic lens and do not realize the potential impact that other associated risks may have on their business operations. Using a holistic risk management approach will enable a firm to identify all of the organization‟s business risks. This will increas e the probability of risk mitigation, with the ultimate goal of total risk elimination .Recommended key construction and risk management strategies for future construction projects have been considered and their explanation follows. J.W. Hinchey stated th at there is and can be no …best practice‟ standard for risk allocation on a high-profile project or for that matter, any project. He said, instead, successful risk management is a mind-set and a process. According to Hinchey, the ideal mind-set is for the parties and their representatives to, first, be intentional about identifying project risks and then to proceed to develop a systematic and comprehensive process for avoiding, mitigating, managing and finally allocating, by contract, those risks in optimum ways for the particular project. This process is said to necessarily begin as a science and ends as an art .According to D. Atkinson, whether contractor, consultant or promoter, the right team needs to be assembled with the relevant multi-disciplinary experience of that particular type of project and its location. This is said to be necessary not only to allow alternative responses to be explored. But also to ensure that the right questions are asked and the major risks identified. Heads of sources of risk are said to be a convenient way of providing a structure for identifying risks to completion of a participant‟s part of the project. Effective risk management is said to require amulti-disciplinary approach. Inevitably risk management requires examination of engineering, legal and insurance related solutions .It is stated that the use of analytical techniques based on a statistical approach could be of enormous use in decision making . Many of these techniques are said to be relevant to estimation of the consequences of risk events, and not how allocation of risk is to be achieved. In addition, at the present stage of the development of risk management, Atkinson states that it must be recognized that major decisions will be made that can not be based solely on mathematical analysis. The complexity of construction projects means that the project definition in terms of both physical form and organizational structure will be based on consideration of only a relatively small number of risks . This is said to then allow a general structured approach that can be applied to any construction project to increase the awareness of participants .The new, simplified Construction Design and Management Regulations (CDM Regulations) which came in to force in the UK in April 2007, revised and brought together the existing CDM 1994 and the Construction Health Safety and Welfare (CHSW) Regulations 1996, into a single regulatory package.The new CDM regulations offer an opportunity for a step change in health and safety performance and are used to reemphasize the health, safety and broader business benefits of a well-managed and co-ordinated approach to the management of health and safety in construction. I believe that the development of these skills is imperative to provide the client with the most effective services available, delivering the best value project possible.Construction Management at Risk (CM at Risk), similar to established private sector methods of construction contracting, is gaining popularity in the public sector. It is a process that allows a client to select a construction manager (CM) based on qualifications; make the CM a member of a collaborative project team; centralize responsibility for construction under a single contract; obtain a bonded guaranteed maximum price; produce a more manageable, predictable project; save time and money; and reduce risk for the client, the architect and the CM.CM at Risk, a more professional approach to construction, is taking its place along with design-build, bridging and the more traditional process of design-bid-build as an established method of project delivery.The AE can review the CM‟s approach to the work, making helpful recommendations. The CM is allowed to take bids or proposals from subcontractors during completion of contract documents, prior to the guaranteed maximum price (GMP), which reduces the CM‟s risk and provides useful input to design. The procedure is more methodical, manageable, predictable and less risky for all.The procurement of construction is also more business-like. Each trade contractor has a fair shot at being the low bidder without fear of bid shopping. Each must deliver the best to get the projec. Competition in the community is more equitable: all subcontractors have a fair shot at the work .A contingency within the GMP covers unexpected but justifiable costs, and a contingency above the GMP allows for client changes. As long as the subcontractors are within the GMP they are reimbursed to the CM, so the CM represents the client in negotiating inevitable changes with subcontractors.There can be similar problems where each party in a project is separately insured. For this reason a move towards project insurance is recommended. The traditional approach reinforces adversarial attitudes, and even provides incentives for people to overlook or conceal risks in an attempt to avoid or transfer responsibility.A contingency within the GMP covers unexpected but justifiable costs, and a contingency above the GMP allows for client changes. As long as the subcontractors are within the GMP they are reimbursed to the CM, so the CM represents the client in negotiating inevitable changes with subcontractors.There can be similar problems where each party in a project is separately insured. For this reason a move towards project insurance is recommended. The traditional approach reinforces adversarial attitudes, and even provides incentives for people to overlook or conceal risks in an attempt to avoid or transfer responsibility.It was reasonable to assume that between them the defects should have been detected earlier and rectified in good time before the partial roof failure. It did appearjustified for the plaintiff to have brought a negligence claim against both the contractor and the architects.In many projects clients do not understand the importance of their role in facilitating cooperation and coordination; the design is prepared without discussion between designers, manufacturers, suppliers and contractors. This means that the designer can not ta ke advantage of suppliers‟ or contractors‟ knowledge of build ability or maintenance requirements and the impact these have on sustainability, the total cost of ownership or health and safety .This risk analysis was able to facilitate, through its multi-dimensional approach to a critical examination of a construction problem, the identification of an effective risk management strategy for future construction projects. This work also served to emphasize the point that clients are becoming more demanding, more discerning, and less willing to accept risk without recompense. They do not want surprises, and are more likely to engage in litigation when things go wrong.国际建设工程风险分析摘要此次分析用实例研究方法分析津巴布韦标准协会总部(SAZ)的屋顶部分坍塌的问题。
工程造价专业中英文资料外文翻译文献

工程造价专业中英文资料外文翻译文献外文文献:Project Cost Control: The Way it WorksIn a recent consulting assignment we realized that there was some lack of understanding of the whole system of project cost control, how it is setup and applied. So we decided to write up a description of how it works. Project cost control is not that difficult to follow in theory.First you establish a set of reference baselines. Then, as work progresses, you monitor the work, analyze the findings, forecast the end results and compare those with the reference baselines. If the end results are not satisfactory then you make adjustments as necessary to the work in progress, and repeat the cycle at suitable intervals. If the end results get really out of line with the baseline plan, you may have to change the plan. More likely, there will be (or have been) scope changes that change the reference baselines which means that every time that happens you have to change the baseline plan anyway.But project cost control is a lot more difficult to do in practice, as is evidenced by the number of projects that fail to contain costs. It also involves a significant amount of work, as we shall see, and we might as well start at the beginning. So let us follow the thread of project cost control through the entire project life span.And, while we are at it, we will take the opportunity to point out the proper places for several significant documents. These include the Business Case, the Request for (a capital) Appropriation (for execution), Work Packages and the Work Breakdown Structure, the Project Charter (or Brief), the Project Budget or Cost Plan, Earned Value and the Cost Baseline. All of these contribute to the organization's ability to effectively control project costs.FootnoteI am indebted to my friend Quentin Fleming, the guru of Earned Value, for checking and correcting my work on this topic.The Business Case and Application for (execution) FundingIt is important to note that project cost control is most effective when the executive management responsible has a good understanding of how projects should unfold through the project life span. This means that they exercise their responsibilities at the key decision points between the major phases. They must also recognize the importance of project risk management for identifying and planning to head off at least the most obvious potential risk events.In the project's Concept Phase• Every project starts with someone identifying an opportunity or need. That is usually someone of importance or influence, if the project is to proceed, and that person often becomes the project's sponsor.• To determine the suitability of the potential project, most organizations call for the preparation of a "Business Case" and its "Order of Magnitude" cost to justify the value of the project so that it can be compared with all the other competing projects. This effort is conducted in the Concept Phase of the project and is done as a part of the organization's management of the entire project portfolio.• The cost of the work of preparing the Business Case is usually covered by corporate management overhead, but it may be carried forward as an accounting cost to the eventual project. No doubt because this will provide a tax benefit to the organization. The problem is, how do you then account for all the projects that are not so carried forward?• If the Business case has sufficient merit, approval will be given to proceed to a Development and Definition phase.In the project's Development or Definition Phase• The objective of the Development Phase is to establish a good understanding of the work involved to produce the required product, estimate the cost and seek capital funding for the actual execution of the project.• In a formalized setting, especially where big projects ar e involved, this application for funding is often referred to as a Request for (a capital) Appropriation (RFA) or Capital Appropriation Request (CAR).• This requires the collection of more detailed requirements and data to establish what work needs to be done to produce the required product or "deliverable". From this information, a plan is prepared in sufficient detail to give adequate confidence in a dollar figure to be included in the request.• In a less formalized setting, everyone just tries to muddl e through.Work Packages and the WBSThe Project Management Plan, Project Brief or Project Charter• If the deliverable consists of a number of different elements, these are identified and assembled into Work Packages (WPs) and presented in the form of a Work Breakdown Structure (WBS). • Each WP involves a set of activities, the "work" that is planned and scheduled as a part of the Project Management Plan. Note, however, that the planning will still be at a relatively high level, and more detailed planning will be necessary during execution if the project is given the go ahead.• This Project Management Plan, by the way, should become the "bible" for the execution phase of the project and is sometimes referred to as the "Project Brief" or the "Project Charter".• The cost of doing the various activities is then estimated and these estimated costs are aggregated to determine the estimated cost of the WP. This approach is known as "detailed estimating" or "bottom up estimating". There are other approaches to estimating that we'll come to in a minute. Either way, the result is an estimated cost of the total work of the project.Note: that project risk management planning is an important part of this exercise. This should examine the project's assumptions and environmental conditions to identify any weaknesses in the plan thus far, and identify those potential risk events that warrant attention for mitigation. This might take the form of specific contingency planning, and/or the setting aside of prudent funding reserves.Request for capitalConverting the estimate• However, an estimate of the work alone is not sufficient for a capital request. To arrive at a capital request some conversion is necessary, for example, by adding prudent allowances such as overheads, a contingency allowance to cover normal project risks and management reserves to cover unknowns and possible scope changes.• In addition, it may be necessary to convert the estimating data into a financial accounting format that satisfies the corporate or sponsor's format for purposes of comparison with other projects and consequent funding approval.• In practice all the data for the type of "bottom up" approach just described may not be available. In this case alternative estimating approaches are adopted that provide various degrees of reliability in a "top down" fashion. For example:Order of Magnitude estimate – a "ball park" estimate, usually reserved for the concept phase onlyAnalogous estimate – an estimate based on previous similar projectsParametric estimate – an estimate based on statistical relationships in historical data• Whichever approach is adopted, hopefully the sum thus arrived at will be approved in full and proves to be satisfactory! This is the trigger to start the Execution Phase of the projectNote: Some managements will approve some lesser sum in the mistaken belief that this will help everyone to "sharpen their pencils" and "work smarter" for the benefit of the organization. This is a mistaken belief because management has failed to understand the nature of uncertainty and risk in project work. Consequently, the effect is more likely to result in "corner cutting" with an adverse effect on product quality, or reduced product scope or functionality. This often leads to a "game" in which estimates are inflated so that management can adjust them downwards. But to be fair, management is also well aware that if money is over allocated, it will get spent anyway. The smart thing for managements to do is to set aside contingent reserve funds, varying with the riskiness of the project, and keep that money under careful control.Ownership of approved capital• If senior management approves the RFA as presented, the sum in question becomes the responsibility of the designated project sponsor. However, if the approved capital request includes allowances such as a "Management Reserve", this may or may not be passed on to the project's sponsor, depending on the policies of the organization.• For the approved RFA, the project sponsor will, in turn, further delegate expenditure authority to the project's project manager and will likely not include any of the allowances. An exception might be the contingency allowances to cover the normal variations in work performance.• The net sum thus arrived at co nstitutes the project manager's Approved Project Budget.Note: If management does not approve the RFA, you should not consider this a project failure. Either the goals, objectives, justification and planning need rethinking to increase the value of the project's deliverables, or senior management simply has higher priorities elsewhere for the available resources and funding.The Project's Execution PhaseThe project manager's Project Budget responsibility• Once this Approved Project Budget is released to t he project manager, a reverse process must take place to convert it into a working control document. That is, the money available must be divided amongst the various WBS WPs that, by the way, have probably by now been upgraded! This results in a project execution Control Budget or Project Baseline Budget, or simply, the Project Budget. In some areas of project management application it is referred to as a Project Cost Plan.• On a large project where different corporate production divisions are involved, th ere may be a further intermediate step of creating "Control Accounts" for the separate divisions, so that each division subdivides their allocated money into their own WBS WPs.• Observe that, since the total Project Budget received formal approval from Ex ecutive Management, you, as project manager, must likewise seek and obtain from Executive Management, via the project's sponsor, formal approval for any changes to the total project budget. Often this is only justified and accepted on the basis of a requested Product Scope Change.• In such a case the project's sponsor will either draw down on the management reserve in his or her possession, or submit a supplementary RFA to upper management.• Now that we have the Project Budget money allocated to Work Pack ages we can further distribute it amongst the various activities of each WP so that we know how much money we have as a "Baseline" cost for each activity.• This provides us with the base of reference for the cost control function. Of course, depending on the circumstances the same thing may be done at the WP level but the ability to control is then at a higher and coarser level.Use of the Earned Value technique• If we have the necessary details another control tool that we can adopt for monitoring ongoin gwork is the "Earned Value" (EV) technique. This is a considerable art and science that you must learn about from texts dedicated to the subject.• But essentially, you take the costs of the schedule activities and plot them as a cumulative total on the appropriate time base. Again you can do this at the activity level, WP level or the whole project level. The lower the level the more control information you have available but the more work you get involved in.The Cost Baseline• This planned reference S-curve is sometimes referred to as the "Cost Baseline", typically in EV parlance. That is, it is the "Budgeted Cost of Work Scheduled" (BCWS), or more simply the "Planned Value" (PV).• Observe that you need to modify this Cost Baseline every time there is an approved scope change that has cost and/or schedule implications and consequently changes the project's Approved Project Budget.• Now, as the work progresses, you can plot the "Actual Cost of Work Performed" (ACWP or simply "Actual Cost" - AC).• You c an plot other things as well, see diagram referred to above, and if you don't like what you see then you need to take "Corrective Action".CommentaryThis whole process is a cyclic, situational operation and is probably the source of the term "cycle" in the popularly misnamed "project life cycle".As an aside, the Earned Value pundits offer various other techniques within the EV process designed to aid in forecasting the final result, that is, the "Estimate At Completion" (EAC). EAC is what you should really be interested in because it is the only constant in a moving project. Therefore, these extended EV techniques must be considered in the same realm of accuracy as top-down estimating. They are useful, but only if you recognize the limitations and know what you are doing!But, as we said at the beginning, it is a lot more difficult to do in practice – and involves a significant amount of work. But, let's face it, that's what project managers are hired for, right?中文译文:项目成本控制:它的工作方式我们在最近的咨询任务中意识到,对于整个项目成本控制体系是如何设置和应用的这个问题,我们仍有一些缺乏了解。
工程造价专业外文文献翻译(中英文对照

外文文献:Project Cost Control: The Way it WorksBy R. Max WidemanIn a recent consulting assignment we realized that there was some lack of understanding of the whole system of project cost control, how it is setup and applied. So we decided to write up a description of how it works. Project cost control is not that difficult to follow in theory.First you establish a set of reference baselines. Then, as work progresses, you monitor the work, analyze the findings, forecast the end results and compare those with the reference baselines. If the end results are not satisfactory then you make adjustments as necessary to the work in progress, and repeat the cycle at suitable intervals. If the end results get really out of line with the baseline plan, you may have to change the plan. More likely, there will be (or have been) scope changes that change the reference baselines which means that every time that happens you have to change the baseline plan anyway.But project cost control is a lot more difficult to do in practice, as is evidenced by the number of projects that fail to contain costs. It also involves a significant amount of work, as we shall see, and we might as well start at the beginning. So let us follow the thread of project cost control through the entire project life span.And, while we are at it, we will take the opportunity to point out the proper places for several significant documents. These include theBusiness Case, the Request for (a capital) Appropriation (for execution), Work Packages and the Work Breakdown Structure, the Project Charter (or Brief), the Project Budget or Cost Plan, Earned Value and the Cost Baseline. All of these contribute to the organization's ability to effectively control project costs.FootnoteI am indebted to my friend Quentin Fleming, the guru of Earned Value, for checking and correcting my work on this topic.The Business Case and Application for (execution) FundingIt is important to note that project cost control is most effective when the executive management responsible has a good understanding of how projects should unfold through the project life span. This means that they exercise their responsibilities at the key decision points between the major phases. They must also recognize the importance of project risk management for identifying and planning to head off at least the most obvious potential risk events.In the project's Concept Phase• EvEry projEct starts with somEonE idEntifying an opportunity or need. That is usually someone of importance or influence, if the project is to proceed, and that person often becomes the project's sponsor.• to dEtErminE thE suitability of thE potEntial projEct, most organizations call for the preparation of a "Business Case" and its"Order of Magnitude" cost to justify the value of the project so that it can be compared with all the other competing projects. This effort is conducted in the Concept Phase of the project and is done as a part of the organization's management of the entire project portfolio.• thE cost of thE work of preparing the Business Case is usually covered by corporate management overhead, but it may be carried forward as an accounting cost to the eventual project. No doubt because this will provide a tax benefit to the organization. The problem is, how do you then account for all the projects that are not so carried forward?• if thE businEss casE has sufficiEnt mErit, approval will bE givEn to proceed to a Development and Definition phase.In the project's Development or Definition Phase• thE objEctivE of t he Development Phase is to establish a good understanding of the work involved to produce the required product, estimate the cost and seek capital funding for the actual execution of the project.• in a formalizEd sEtting, EspEcially whErE big projEcts arE involved, this application for funding is often referred to as a Request for (a capital) Appropriation (RFA) or Capital Appropriation Request (CAR).• this rEquirEs thE collEction of morE dEtailEd rEquirEmEnts and data to establish what work needsto be done to produce the required product or "deliverable". From this information, a plan is prepared in sufficient detail to give adequate confidence in a dollar figure to be included in the request.• in a lEss formalizEd sEtting, EvEryonE just triEs to muddlE through.Work Packages and the WBSThe Project Management Plan, Project Brief or Project Charter• if thE dElivErablE consists of a numbEr of diffErEnt ElEmEnts, thEsE are identified and assembled into Work Packages (WPs) and presented in the form of a Work Breakdown Structure (WBS).• Each wp involvEs a sEt of activitiEs, thE "work" that is plannEd and scheduled as a part of the Project Management Plan. Note, however, that the planning will still be at a relatively high level,and more detailed planning will be necessary during execution if the project is given the go ahead.• this projEct managEmEnt plan, by thE way, should bEcomE thE "bible" for the execution phase of the project and is sometimes referred to as the "Project Brief" or the "Project Charter".• thE cost of doing thE various activitiEs is thEn EstimatEd and thEsE estimated costs are aggregated to determine the estimated cost of the WP. This approach is known as "detailed estimating" or "bottom up estimating". There are other approaches to estimating that we'll come to in a minute. Either way, the result is an estimated cost of the totalwork of the project.Note: that project risk management planning is an important part of this exercise. This should examine the project's assumptions and environmental conditions to identify any weaknesses in the plan thus far, and identify those potential risk events that warrant attention for mitigation. This might take the form of specific contingency planning, and/or the setting aside of prudent funding reserves.Request for capitalConverting the estimate• howEvEr, an EstimatE of thE work alonE is not sufficiEnt for a capital request. To arrive at a capital request some conversion is necessary, for example, by adding prudent allowances such as overheads, a contingency allowance to cover normal project risks and management reserves to cover unknowns and possible scope changes.• in addition, it may bE nEcEssary to convErt thE Estimating data into a financial accounting formatthat satisfies the corporate or sponsor's format for purposes of comparison with other projects and consequent funding approval.• in practicE all thE data for thE typE of "bottom up" approach just described may not be available.In this case alternative estimating approaches are adopted that provide various degrees of reliability in a "top down" fashion. Forexample:Order of Magnitude estimate – a "ball park" estimate, usually reserved for the concept phase onlyAnalogous estimate – an estimate based on previous similar projects Parametric estimate –an estimate based on statistical relationships in historical data• whichEvEr approach is adoptEd, hopEfully thE sum thus arrivEd at will be approved in full and proves to be satisfactory! This is the trigger to start the Execution Phase of the projectNote: Some managements will approve some lesser sum in the mistaken belief that this will help everyone to "sharpen their pencils" and "work smarter" for the benefit of the organization. This is a mistaken belief because management has failed to understand the nature of uncertainty and risk in project work. Consequently, the effect is more likely to result in "corner cutting" with an adverse effect on product quality, or reduced product scope or functionality. This often leads to a "game" in which estimates are inflated so that management can adjust them downwards. But to be fair, management is also well aware that if money is over allocated, it will get spent anyway. The smart thing for managements to do is to set aside contingent reserve funds, varying with the riskiness of the project, and keep that money under careful control.Ownership of approved capital• if sEnior managEmEnt approvEs thE rfa as prEsEntEd, thE sum in question becomes the responsibility of the designated project sponsor. However, if the approved capital request includes allowances such as a "Management Reserve", this may or may not be passed on to the project's sponsor, depending on the policies of the organization.• for thE approvEd rfa, thE projEct sponsor will, in turn, further delegate expenditure authority to the project's project manager and will likely not include any of the allowances. An exception might be the contingency allowances to cover the normal variations in work performance.• thE nEt sum thus arrivEd at constitutes the project manager's Approved Project Budget.Note: If management does not approve the RFA, you should not consider this a project failure. Either the goals, objectives, justification and planning need rethinking to increase the value of the project's deliverables, or senior management simply has higher priorities elsewhere for the available resources and funding.The Project's Execution PhaseThe project manager's Project Budget responsibility• oncE this approvEd projEct budgEt is rElEas ed to the project manager, a reverse process must take place to convert it into a working control document. That is, the money available must be divided amongstthe various WBS WPs that, by the way, have probably by now been upgraded! This results in a project execution Control Budget or Project Baseline Budget, or simply, the Project Budget. In some areas of project management application it is referred to as a Project Cost Plan.• on a largE projEct whErE diffErEnt corporatE production divisions are involved, there may be a further intermediate step of creating "Control Accounts" for the separate divisions, so that each division subdivides their allocated money into their own WBS WPs.• obsErvE that, sincE thE total projEct budgEt rEcEivEd formal approval from Executive Management, you, as project manager, must likewise seek and obtain from Executive Management, via the project's sponsor, formal approval for any changes to the total project budget. Often this is only justified and accepted on the basis of a requested Product Scope Change.• in such a casE thE projEct's sponsor will EithEr draw down on thE management reserve in his or her possession, or submit a supplementary RFA to upper management.• now that wE havE thE projEct budgEt monEy allocatEd to Work Packages we can further distribute it amongst the various activities of each WP so that we know how much money we have as a "Baseline" cost for each activity.• this providEs us with thE basE of rEfErEncE for thE cost controlfunction. Of course, depending on the circumstances the same thing may be done at the WP level but the ability to control is then at a higher and coarser level.Use of the Earned Value technique• if wE havE thE nEcEssary dEtails anothEr control tool that wE can adopt for monitoring ongoing work is the "Earned Value" (EV) technique. This is a considerable art and science that you must learn about from texts dedicated to the subject.• but EssEntially, you takE thE costs of thE schEdulE activitiEs and plot them as a cumulative total on the appropriate time base. Again you can do this at the activity level, WP level or the whole project level. The lower the level the more control information you have available but the more work you get involved in.The Cost Baseline• this plannEd reference S-curve is sometimes referred to as the "Cost Baseline", typically in EVparlance. That is, it is the "Budgeted Cost of Work Scheduled" (BCWS), or more simply the "Planned Value" (PV).• Observe that you need to modify this Cost Baseline every time there is an approved scope change that has cost and/or schedule implications and consequently changes the project's Approved Project Budget.• now, as thE work progrEssEs, you can plot thE "actual cost of workPerformed" (ACWP or simply "Actual Cost" - AC).• you can plot othEr things as wEll, sEE diagram rEfErrEd to abovE, and if you don't like what you see then you need to take "Corrective Action".CommentaryThis whole process is a cyclic, situational operation and is probably the source of the term "cycle" in the popularly misnamed "project life cycle".As an aside, the Earned Value pundits offer various other techniques within the EV process designed to aid in forecasting the final result, that is, the "Estimate At Completion" (EAC). EAC is what you should really be interested in because it is the only constant in a moving project. Therefore, these extended EV techniques must be considered in the same realm of accuracy as top-down estimating. They are useful, but only if you recognize the limitations and know what you are doing!But, as we said at the beginning, it is a lot more difficult to do in practice –and involves a significant amount of work. But, let's face it, that's what project managers are hired for, right?中文译文:项目成本控制:它的工作方式R.马克斯怀德曼我们在最近的咨询任务中意识到,对于整个项目成本控制体系是如何设置和应用的这个问题,我们仍有一些缺乏了解。
- 1、下载文档前请自行甄别文档内容的完整性,平台不提供额外的编辑、内容补充、找答案等附加服务。
- 2、"仅部分预览"的文档,不可在线预览部分如存在完整性等问题,可反馈申请退款(可完整预览的文档不适用该条件!)。
- 3、如文档侵犯您的权益,请联系客服反馈,我们会尽快为您处理(人工客服工作时间:9:00-18:30)。
文献信息:文献标题:Factors influencing accuracy of construction project cost estimates in Pakistan: Perception and reality(影响巴基斯坦建设工程造价估算准确性的感知因素和实际因素)国外作者:Farrukh Arif,Sarosh H. Lodi,Nida Azhar文献出处:《International Journal of Construction Management》, 2015,15(1):59-70字数统计:英文3023单词,17564字符;中文5181汉字外文文献:Factors influencing accuracy of construction project cost estimates in Pakistan: Perception and reality Abstract Construction projects are unique as they are priced before being constructed. Therefore, accuracy of construction project cost estimates is pivotal in project success. Several studies have determined factors influencing the accuracy of cost estimates. Comparatively less information is available for construction industries in developing countries. This study identified factors influencing the accuracy of cost estimates for construction projects in Pakistan. Cost data was collected for 46 completed construction projects. Four dimensions 60 factors were considered. Dimensions included: project characteristics, project team, estimating procedures, and (costing related) information items. A rigorous analysis framework based on principal component analysis and regression analysis was used. Involvement of the contractor in the estimation procedure and labour rates were found to be the most significant factors. Early involvement of the contractor can result in realistic estimates through timely input from subcontractors, materials suppliers and manufacturers among others. This also helps in controlling labour costs as most of the construction projects in Pakistan employ labour through subcontractors.Keywords: cost estimates; Pakistan; factors influencing accuracy; estimate bias; estimate consistency; principal component analysis; regression analysisIntroductionThe construction industry is unique in its working as compared to other manufacturing and product development industries. Since it is a project-based activity, every construction project has its own nature, requirements, and characteristics. The uniqueness of construction projects is that they are priced before being constructed. Therefore, accuracy of project estimates have a pivotal role. This is the reason that more often than not, comparison of actual cost to early cost estimates becomes the measure of the project team, performance and overall success of the project (Oberlender & Trost 2001). Pricing and the profit required from the construction project are decided at the time of bidding and the bid’s acceptance (Halpin & Senior 2009). Therefore, construction project managers are primarily involved in cost control. This makes it necessary for construction managers to understand different factors that influence the accuracy of project cost estimates. Several researchers have conducted detailed studies in order to determine factors influencing the accuracy of cost estimates. However, comparatively less information on this is available for the construction industries in developing countries. Realizing this need, the paper presents a rigorous analysis to determine factors influencing the accuracy of construction cost estimates. The data was collected from 46 construction projects in Pakistan. The authors adopted a two-stage statistical analysis framework to determine the perceived and real factors influencing the accuracy of estimates of construction project costs. Certain conclusions have been drawn and strategic-level recommendations are provided, based on results of the analysis, to improve the cost estimation process and to reduce inaccuracy in the construction industry of Pakistan.The study presented in this paper first provides a brief synopsis of similar prior studies conducted from different perspectives. Then it provides an account of the research objectives and scope, followed by details on research methodology and data collection. The main part of the paper provides details of the data analysis and itsresults. This is followed by discussion of results of the analysis. Finally, strategic-level recommendations are provided for the improvement of cost estimation practices in the construction industry of Pakistan which could be equally applicable for other developing construction industries.Prior studiesSeveral studies have been conducted related to accuracy of cost estimates for construction projects. On many occa sions, researchers have attempted to measure the impact of certain project characteristics on the accuracy of estimates (Skitmore 1988; Akintoye & Fitzgerald 2000). Akintoye (2000) conducted a study to identify and under stand the factors that influence contractors’ cost estimation practices in the UK. It was concluded that the main fac tors influencing cost estimating practices included the complexity of the project, the scale and scope of the construction, market conditions, the method of construction, site constraints and location. Aibinu and Pasco (2008) conducted a study to explore the accuracy of pre-tender building cost estimates in Australia. They identified eight project characteristics and conducted analysis using multiple regression analysis; they found that the accuracy of estimates is influenced by project size.On the other hand, certain other studies had not only accounted for project characteristics but also other aspects, such as project team-related factors, estimating procedures, and (costing related) information items. Carr (1989) conducted a study to define the basic requirements for developing reliable estimates. He concluded that the accuracy of the estimate depends on the estimator’s ability to see the project from a macro perspective, his experience and judgement skills. Ashwarth (1994) concluded that availability of information on the design, type and quality of cost data, type of project, project size, number of bidders on competitive projects, stability of market conditions, personal factors, proficiency in estimating, and sheer quantitative experience influence the accuracy of estimating the costs of construction work. Oberlender and Trost (2001) developed an estimate scoring system and consequently software to measure the accuracy of estimates. They found that the accuracy of anearly estimate has four determinants: ‘(1) who was involved in preparing the estimate;(2) how the estimate was prepared; (3) what was known about the project; and (4) other factors considered while preparing the estimate’. Trost and Oberlender (2003) conducted factor analysis and multivariate regression analysis to determine a suitable model for predicting the accuracy of estimates. They identified five factors that were significant in predicting accuracy. These factors included: basic process design, team experience and cost information, time allowed to prepare the estimate, site requirements, and bidding and labour climate. Enshassi et al. (2010) identified factors such as supply of raw materials and equipment, and fluctuations in the cost of building materials as influencing cost overruns.The study presented in this paper considered all four dimensions of the factors influencing the accuracy of cost estimates: i.e. factors related to project characteristics, the project team, estimating procedures, and information on the project.Research objectives and scopeThe prime objective of this research was to identify the factors that influence the accuracy of construction project cost estimates in Pakistan. For this purpose it was deemed necessary to approach the study from two major perspectives: (1) the factors that are perceived to be influencing the accuracy and (2) the factors that did in reality influence the accuracy of cost estimates when analysed using the actual cost bias in the project data.Research methodology and data collectionA thorough literature review was performed to identify the key elements that may provide a good means of judging the accuracy of cost estimates. The literature review was done through books, conference proceedings, the internet, and leading construction management and engineering journals. Following the identification of the key elements of the survey, some unstructured expert interviews were conducted to verify the key elements as well as identify any further elements relevant to the practices and issues for estimating costs in the local construction industry.A structured questionnaire consisting of two parts was designed parts A and B. Part A requested the respondent’s personal information (e.g. work experience, experience as cost estimator, etc.) and company information (e.g. type of organization, types of construction work performed, years in business, annual volume of work, number of permanent employees, cities of operation, etc.). PartB requested information on project costs (e.g. project name, type, client, estimated project cost, total project cost, estimated profit margin, etc.).Furthermore, a list of 60 factors categorized under four dimensions was provided to the respondents. The respondents were asked to rate the influence of each factor on the accuracy of the cost estimate of the project for which cost information was provided on a Likert scale of 1 (least influential) to 5 (most influential). These dimensions included Project Team (PT) having 16 factors, Project Characteristics (PC) having 19 factors, Estimating Procedures (EP) having 14 factors and (costing related) Information Items (Info) having 11 factors. The dimensions and factors are listed in Table 1.Table 1. Factors influencing accuracyIn the next stage, 2 3 pilot surveys were conducted through face-to-face interviews. However, the purpose of this exercise was not to collect data, but rather to refine the questionnaire. Thus, for this reason, industry professionals and academicians having experience of such surveys as well as knowledge of Pakistan’s construction industry were consulted.The questionnaire was circulated among general contractors, speciality contractors, construction management contractors, and design build contractors. The sampling frame for this survey was construction contracting companies that possess a licence or are a member of the Pakistan Engineering Council (PEC), which is a regulatory body for the engineering profession in Pakistan. The respondents were asked to provide data on their most recently completed project. The surveys were intended to be filled by the cost estimating personnel related to the project surveyed.A few unstructured interviews with selected respondents from the various groups of contractors were also conducted to clarify their responses, to discuss the survey results, and to validate the survey.The details on the survey responses are shown in Table 2. A total of 48% valid responses were received, which is rather good for a construction industry questionnaire survey. In a similar study, the researchers used cost-related data for 56 projects and received a response rate of 41% for the accompanying questionnairesurvey (Aibinu & Pasco 2008). Therefore, reliable conclusions can be obtained from the collected data.Table 2. Breakdown of responsesTotal surveys No response Total number of potential responses Total valid responses received Percentage of valid responses 9535604648%Data analysis and resultsGeneral characteristics of respondentsThe majority of the responses were collected from Karachi. Since it is the biggest city in Pakistan, it was considered a representative sample for Pakistan’s construction industry. All of the respondents were local Pakistani contractors. Most of the respondent firms which provided data for the projects were general contractors (77%). The majority of the respondent firms had an annual volume of construction work of between 100 and 500 million Pakistani Rupee (PKR) (41%), while an equal percentage of respondent firms (26% each) had an annual volume of construction work of 500 1000 million PKR or 1000 5000 million PKR. The rest had an annual volume of construction work greater than 5000 million PKR (currently, US$1 102 PKR approximately). A majority of the respondents were either civil engineering managers or project managers. The respondents had an average working experience of around 15 years related to cost estimation/cost engineering.The reported projects were mainly in the residential, commercial, and industrial construction sectors (84%) as shown in the pie-chart in Figure 1. Almost an equal number of reported projects were in the public (47%) and private (51%) sectors.Figure 1. Type of projects reportedStatistical analysis frameworkThe analysis procedure was designed to elicit the perceived and real factors influencing the accuracy of the project data that was gathered. The framework for the analysis is shown in Figure 2. It has three steps.Figure 2. Framework of analysisStep 1 focused on finding out the cost bias using the data provided by therespondent contractors on the real costs of the projects. Furthermore, normality of cost bias was assessed in order to determine the suitability of the data for regression analysis.Step 2 included exploratory factor analysis using principal component analysis (PCA). The exploratory factor analysis was intended to identify the factors based on exploring the interrelationships among the respective sets of variables (the four dimensions). Hence, the analysis produced a list of eight significant factors that are perceived to be the factors influencing accuracy. Afterwards, the regression analysis focused on identifying the real factors through exploring the ability of influencing factors to predict variance in bias of the estimates.Step 3 used any items out of the 60 influencing factors which were identified as statistically (significantly) correlated with the target cost variable. This regression analysis resulted in a list of real significant factors out of all 60 influencing factors that had affected the accuracy of cost estimates in the projects for which cost data was collected.Conclusions and discussion on outcomes of the analysisThe factors that were identified through PCA and were perceived as influencing accuracy included: client’s level of experience of the construction type, level of expertise of contractor, priority of project, initial scale of project, applicability of cost information, accuracy and reliability of cost information, completeness of tender documents, and labour productivity. None of these eight factors were found to be influential when regression analysis was performed with actual project cost bias data. However, the reason behind the identification of these perceived factors could be the general experience of the respondents with other projects. One of the reasons that the aforementioned factors influence the accuracy of estimates could be the non-availability of commercial cost databases, and accurate labour productivity data.Furthermore, regression analysis of all 60 factors with the actual project cost bias data was conducted. The factors of real influence on the accuracy of cost estimates for the projects included in this study were identified. These included: involvement ofcontractor in the estimation procedure, labour rates, number of other projects of client, and attitude of client towards changes. Three out of four identified factors were project team-related factors. Further analysis revealed that involvement of the contractor in the estimation procedure, and labour rates were the most influential factors. The early involvement of the contractor in the cost estimation phase can result in early involvement of subcontractors, materials suppliers, and manufacturers. As a result more accurate and realistic estimates can be prepared. Labour rates are generally found to be highly variable due to the lack of implementation of standardized wage rate mechanisms. Another important aspect is labour productivity. Labour productivity data for preparing estimates, in general, is not available in a formalized database at the industry level, which also affects the overall labour costs in a project. Thus labour rates have a vital influence on accuracy.RecommendationsWell-organized historical data on costs should be maintained in a single suitable location accessible to cost estimators. Historical records for all possible competitors should be maintained, and a bidding strategy based on available information should be developed. There is a strong need for a very elaborate and broad database of past project records for the construction industry. This database could easily be developed through the collaboration of universities and the construction industry if both show a clear commitment towards it. This will be helpful for universities, for the purposes of study, and for enhancing the students’ knowledge base. In this regard universities can provide the technical human resources and industry can come up with other resources such as financial, and access to the projects and their documents, etc.Communications between estimators and the project owner and/or the consultant should be established as early as possible to improve the accuracy of estimates and the estimating process as a whole. The subcontractors, material suppliers, and manufacturers should be involved in preparation of the estimate to achieve more accurate and realistic estimates. Alternative contracting strategies, such as CM @ Risk and Integrated Project Delivery (IPD), Public Private Partnership Projects (PPP),Design Build (DB), and Early Contractor Involvement (ECI), should be utilized on an experimental basis. Such strategies could not only improve the accuracy of cost estimates, but could also result in better project control from overall persepctives i.e. time, cost, and quality. With regard to labour rates, construction firms in Pakistan usually involve subcontractors for the procurement of labour. Subcontractors in Pakistan are not thoroughly involved in the estimate preparation in the traditional bidding process i.e. design bid build. As discussed earlier, adoption of alternatuive contracting strategies that can result in early involvement of the contractor in estimate preparation can also result in early involvement of subcontractors. Thus, ultimately, control on labour rates can also be achieved. This aspect, combined with establishment of a sustainable industry-wide labour productivity database could do a great deal in controlling labour costs.中文译文:影响巴基斯坦建设工程造价估算准确性的感知因素和实际因素摘要建设工程是独特的,因为它们在建造之前就已经定价。