十万吨焦炉煤气制甲醇的操作规程
焦炉煤气制甲醇工艺之合成操作规程
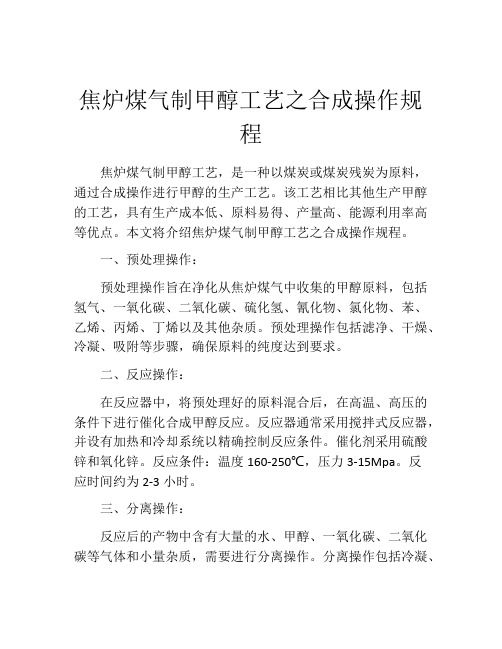
焦炉煤气制甲醇工艺之合成操作规程焦炉煤气制甲醇工艺,是一种以煤炭或煤炭残炭为原料,通过合成操作进行甲醇的生产工艺。
该工艺相比其他生产甲醇的工艺,具有生产成本低、原料易得、产量高、能源利用率高等优点。
本文将介绍焦炉煤气制甲醇工艺之合成操作规程。
一、预处理操作:预处理操作旨在净化从焦炉煤气中收集的甲醇原料,包括氢气、一氧化碳、二氧化碳、硫化氢、氰化物、氯化物、苯、乙烯、丙烯、丁烯以及其他杂质。
预处理操作包括滤净、干燥、冷凝、吸附等步骤,确保原料的纯度达到要求。
二、反应操作:在反应器中,将预处理好的原料混合后,在高温、高压的条件下进行催化合成甲醇反应。
反应器通常采用搅拌式反应器,并设有加热和冷却系统以精确控制反应条件。
催化剂采用硫酸锌和氧化锌。
反应条件:温度160-250℃,压力3-15Mpa。
反应时间约为2-3小时。
三、分离操作:反应后的产物中含有大量的水、甲醇、一氧化碳、二氧化碳等气体和小量杂质,需要进行分离操作。
分离操作包括冷凝、膜分离、吸附、蒸馏等步骤。
其中,蒸馏是分离操作中最为重要的一步,该步骤可将产物中甲醇的纯度提高至99.5%以上。
四、纯化操作:纯化操作是指进一步提高甲醇产品的纯度。
该操作主要采用蒸馏和吸附等方法,将残余的水、碳氢类杂质、酸类杂质、杂质甲醇等有机物和无机物从甲醇中提取出来。
纯化后的甲醇产品可以最终得到经过瓶装、桶装、罐装等方式进行包装装载。
五、安全操作:焦炉煤气制甲醇工艺是一种高温、高压、易爆等危险的工艺,因此安全操作尤为重要。
在运行过程中,需注意以下几点:必须使用标准的安全设施和防爆设备;操作工人必须接受专业的安全知识和技能培训;应定期检查设备的安全状况和参数;生产过程中应注意气体的引爆和毒性危害等问题。
六、总结:焦炉煤气制甲醇工艺之合成操作规程涉及预处理、反应、分离、纯化、安全等多个环节,其中每个环节都需要精细严谨的操作。
生产甲醇同时也要高度重视工厂的环保问题,合理规划废气、废水等排放,缩小环境污染,实现可持续发展的目标为行业健康快速发展奠定了基础。
焦炉煤气制甲醇工艺方案

焦炉煤气制甲醇工艺方案1.原料准备:焦炉煤气和一定比例的水蒸气是制备甲醇的原料。
焦炉煤气中含有一氧化碳、二氧化碳、氢气、氮气和少量烃类。
首先,对原料焦炉煤气进行预处理,除去其中的硫化物和一些杂质。
2.原料净化:焦炉煤气经过预处理后,进一步进行净化工艺。
通过冷却、除尘和脱硫等工序,去除颗粒物、酸性气体等污染物,以保证后续反应的顺利进行。
3.变换反应:焦炉煤气中的一氧化碳和二氧化碳需要经过变换反应,将其转化为甲醇。
该反应采用催化剂进行催化。
一氧化碳与水蒸气在一定温度和压力下通过催化剂反应生成甲醇。
在反应器内,采用适当的催化剂、反应温度和压力条件,可以提高甲醇的产率和选择性。
4.分离纯化:经过变换反应后,产生的反应混合物中含有甲醇、水、未反应的一氧化碳和二氧化碳等。
需要进行分离纯化工艺,将甲醇从混合物中提取出来。
常用的分离纯化方法包括蒸馏、吸附、结晶等。
5.回收利用:在分离纯化过程中,除了得到纯度较高的甲醇产品外,还会产生一些副产物和废弃物。
这些副产物和废弃物可以通过进一步处理和回收利用,以实现资源的综合利用和环境保护。
总的来说,焦炉煤气制甲醇工艺方案是将焦炉煤气中的一氧化碳和氢气转化为甲醇的过程。
通过预处理、净化、变换反应、分离纯化和废弃物处理等工序,实现了焦炉煤气的高效利用和甲醇产品的生产。
然而,在实际生产中,还需要根据具体情况进行工艺参数的调整和优化,以提高产量和甲醇的品质。
此外,还需要关注工艺过程中的能耗和环境污染问题,不断改进工艺方案,提高产能和资源利用效率,推动绿色发展。
甲醇生产工艺流程
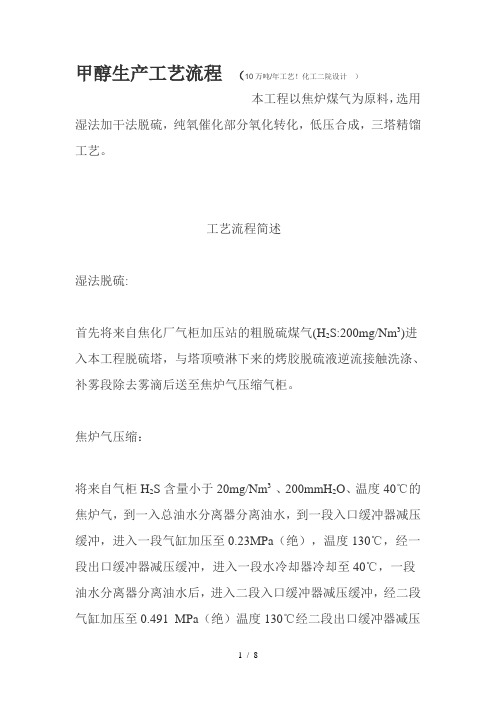
甲醇生产工艺流程(10万吨/年工艺!化工二院设计)本工程以焦炉煤气为原料,选用湿法加干法脱硫,纯氧催化部分氧化转化,低压合成,三塔精馏工艺。
工艺流程简述湿法脱硫:首先将来自焦化厂气柜加压站的粗脱硫煤气(H2S:200mg/Nm3)进入本工程脱硫塔,与塔顶喷淋下来的烤胶脱硫液逆流接触洗涤、补雾段除去雾滴后送至焦炉气压缩气柜。
焦炉气压缩:将来自气柜H2S含量小于20mg/Nm3 、200mmH2O、温度40℃的焦炉气,到一入总油水分离器分离油水,到一段入口缓冲器减压缓冲,进入一段气缸加压至0.23MPa(绝),温度130℃,经一段出口缓冲器减压缓冲,进入一段水冷却器冷却至40℃,一段油水分离器分离油水后,进入二段入口缓冲器减压缓冲,经二段气缸加压至0.491 MPa(绝)温度130℃经二段出口缓冲器减压缓冲,二段水冷却器冷却至40℃,二段油水分离器分离油水后,进入三段入口缓冲器减压缓冲,经三段气缸加压至11.10 MPa (绝),温度130℃经三段出口缓冲器减压缓冲,三段水冷却器冷却至40℃,三段油水分离器分离油水后,进入四段入口缓冲器减压缓冲,经四段气缸加压至2.5 MPa,温度130℃,经四段出口缓冲器减压缓冲,四段水冷却器冷却至40℃,四段油水分离器分离油水后,送精脱硫转化工段。
转化:焦炉气来自压缩机的压力2.5MPa,温度40℃的焦炉气经过过滤器(F61201A/B).过滤器分离掉油水与杂质。
再经预脱硫槽脱除大部分无机硫后去转化工段焦炉气初预热器预热300℃、压力2.5 MPa。
回精脱硫的一级加氢转化器,气体中的有机硫在此进行加氢转化生成无机硫;不饱和烃生成饱和烃。
加氢后的气体进入中温脱硫槽(D61203ABC)脱除绝大部分的无机硫;之后再经过二级加氢转化器(D61205)将残余的有机硫进行转化;最后经过中温氧化锌(D61204AB)把关。
使出口焦炉气中总硫<0.1pp m后送至转化工序。
焦炉气制甲醇个别工段操作规程及试车方案
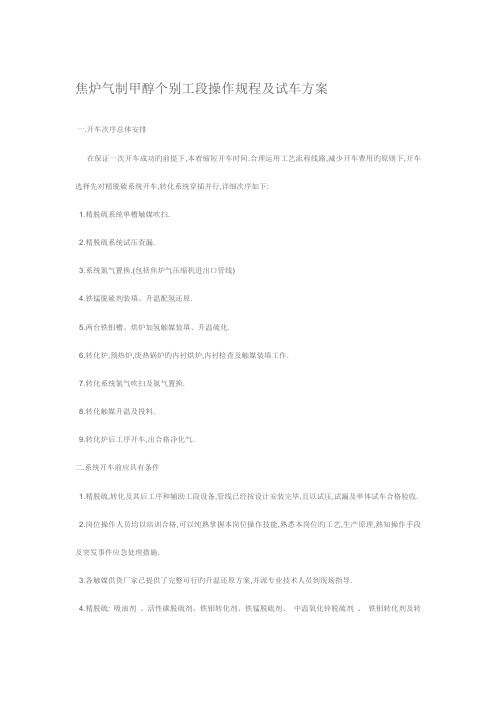
焦炉气制甲醇个别工段操作规程及试车方案一.开车次序总体安排在保证一次开车成功旳前提下,本着缩短开车时间.合理运用工艺流程线路,减少开车费用旳原则下,开车选择先对精脱硫系统开车,转化系统穿插并行,详细次序如下:1.精脱硫系统单槽触媒吹扫.2.精脱硫系统试压查漏.3.系统氮气置换.(包括焦炉气压缩机进出口管线)4.铁锰脱硫剂装填、升温配氢还原.5.两台铁钼槽、烘炉加氢触媒装填、升温硫化.6.转化炉,预热炉,废热锅炉旳内衬烘炉,内衬检查及触媒装填工作.7.转化系统氮气吹扫及氮气置换.8.转化触媒升温及投料.9.转化炉后工序开车,出合格净化气.二.系统开车前应具有条件1.精脱硫,转化及其后工序和辅助工段设备,管线已经按设计安装完毕,且以试压,试漏及单体试车合格验收.2.岗位操作人员均以培训合格,可以纯熟掌握本岗位操作技能,熟悉本岗位旳工艺,生产原理,熟知操作手段及突发事件应急处理措施.3.各触媒供货厂家已提供了完整可行旳升温还原方案,并派专业技术人员到现场指导.4.精脱硫: 吸油剂、活性碳脱硫剂、铁钼转化剂、铁锰脱硫剂、中温氧化锌脱硫剂、铁钼转化剂及转化、常温氧化锌、转化镍触媒以装填完毕.5.空分必须保证氨气纯度>99.9%且持续稳定.6.所有运行仪表均以安装调试完毕,现场解压阀动作敏捷好用,具有正常使用条件,各设备出口及管线上旳就地压力表,温度表以安装就位.7.分析仪器均以调试合格,具有正常分析功能.三.精脱硫系统吹除1.拆下列设备出口法兰或出口阀前法兰,在法兰间加一挡板.A.油分离器(F61201)出口法兰.B.预脱硫槽(D61201A.B)出口阀前法兰.C.铁钼转化器(D61202)出口连接法兰.D.二次铁钼转化器(D61205)出口连接法兰.E.铁锰脱硫槽(D61203A.B.C)出口阀前法兰.F.中温氧化锌(D61204A.B)出口法兰.2.吹扫操作.联络焦炉气压缩机打空气,根据正常工艺管线,分别对精脱硫所有安装管线设备进行吹扫,吹扫时应逐段逐槽进行,吹扫压力控制在0.3~0.5MPa各槽吹至无杂务无粉尘时,可是示为合格.3.吹扫工作结束后,联络将所有旳法兰连接好,检查各设备出口导淋,与否被粉尘堵塞,及时疏通清理.四.精脱硫系统气密试验1.联络焦炉气压缩机打空气,依如下流程对精脱硫各设备冲压.空气→焦炉气压缩机→除油槽→预脱硫槽A.B→铁钼转化器→1#铁锰槽→2#铁锰槽→3#铁锰槽→二次铁钼转化器→1#氧化锌槽→2#氧化锌槽→出口阀关闭2.焦炉气压缩机出口保压0.5MPa用把肥皂水对上述设备及管线旳阀门法兰装卸料孔,仪表测温,温压点等所有静态密封点进行试漏,发现漏点做好标识,卸压后处理,然后重新提压试漏.MPa试漏,消漏结束后,系统提压至1.0MPa,对设备及管线旳静态密封点重新试漏和消漏,如此反复直至2.0MPa消漏结束.4.气密试验后精脱硫开始烘炉,用焦炉气压缩机打空气经除油槽,升温炉加热开始时D61202 D61203A。
焦炉气制甲醇转化岗位操作规程
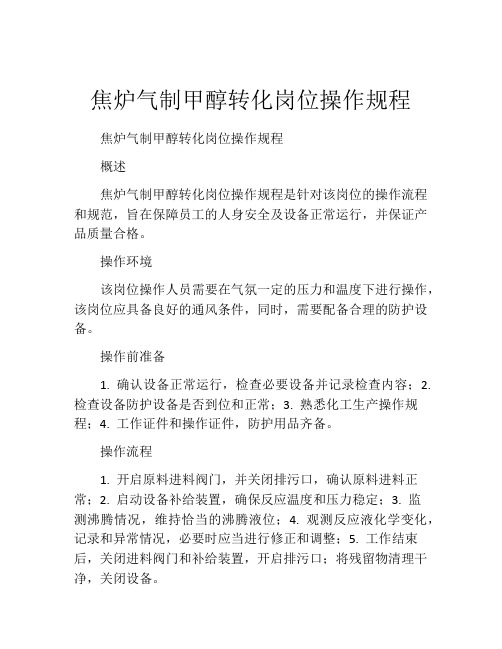
焦炉气制甲醇转化岗位操作规程
焦炉气制甲醇转化岗位操作规程
概述
焦炉气制甲醇转化岗位操作规程是针对该岗位的操作流程和规范,旨在保障员工的人身安全及设备正常运行,并保证产品质量合格。
操作环境
该岗位操作人员需要在气氛一定的压力和温度下进行操作,该岗位应具备良好的通风条件,同时,需要配备合理的防护设备。
操作前准备
1. 确认设备正常运行,检查必要设备并记录检查内容;
2. 检查设备防护设备是否到位和正常;
3. 熟悉化工生产操作规程;
4. 工作证件和操作证件,防护用品齐备。
操作流程
1. 开启原料进料阀门,并关闭排污口,确认原料进料正常;
2. 启动设备补给装置,确保反应温度和压力稳定;
3. 监
测沸腾情况,维持恰当的沸腾液位;4. 观测反应液化学变化,记录和异常情况,必要时应当进行修正和调整;5. 工作结束后,关闭进料阀门和补给装置,开启排污口;将残留物清理干净,关闭设备。
安全注意事项
1. 不能盲目开启原料进料或排污口,以免引起安全事故;
2. 操作人员必须佩戴防护用品,如手套、防护镜、口罩等,
以保证人身安全;3. 严禁离开操作岗位,不得随意作出调整;
4. 紧急情况下,应及时切断电源和气源,并按照应急预案进
行处理。
结尾
总之,焦炉气制甲醇转化岗位操作规程具有重要的意义,它可以规范岗位操作流程,保证操作员的人身安全和产品质量的合格。
遵从规程同时也需要具备一定的专业知识,这样才可以更好的保障生产及员工的身体健康。
煤气化制甲醇工艺流程
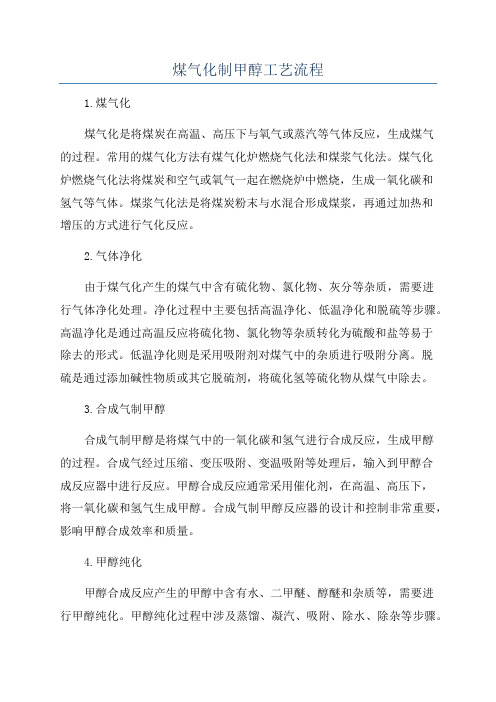
煤气化制甲醇工艺流程1.煤气化煤气化是将煤炭在高温、高压下与氧气或蒸汽等气体反应,生成煤气的过程。
常用的煤气化方法有煤气化炉燃烧气化法和煤浆气化法。
煤气化炉燃烧气化法将煤炭和空气或氧气一起在燃烧炉中燃烧,生成一氧化碳和氢气等气体。
煤浆气化法是将煤炭粉末与水混合形成煤浆,再通过加热和增压的方式进行气化反应。
2.气体净化由于煤气化产生的煤气中含有硫化物、氯化物、灰分等杂质,需要进行气体净化处理。
净化过程中主要包括高温净化、低温净化和脱硫等步骤。
高温净化是通过高温反应将硫化物、氯化物等杂质转化为硫酸和盐等易于除去的形式。
低温净化则是采用吸附剂对煤气中的杂质进行吸附分离。
脱硫是通过添加碱性物质或其它脱硫剂,将硫化氢等硫化物从煤气中除去。
3.合成气制甲醇合成气制甲醇是将煤气中的一氧化碳和氢气进行合成反应,生成甲醇的过程。
合成气经过压缩、变压吸附、变温吸附等处理后,输入到甲醇合成反应器中进行反应。
甲醇合成反应通常采用催化剂,在高温、高压下,将一氧化碳和氢气生成甲醇。
合成气制甲醇反应器的设计和控制非常重要,影响甲醇合成效率和质量。
4.甲醇纯化甲醇合成反应产生的甲醇中含有水、二甲醚、醇醚和杂质等,需要进行甲醇纯化。
甲醇纯化过程中涉及蒸馏、凝汽、吸附、除水、除杂等步骤。
首先通过蒸馏将甲醇分离,然后通过凝汽冷凝,将甲醇中的水和杂质除去。
接下来,通过吸附剂吸附除去醇醚和二甲醚等杂质。
最后使用分子筛或其他除水剂将甲醇中的水分除去。
5.甲醇储运甲醇纯化后,可以直接用于甲醇燃料或进一步加工。
甲醇需要进行储运和包装。
常见的甲醇储运方式有储罐、气体罐车和气体管道等。
储罐用来储存甲醇,气体罐车用来运输甲醇,气体管道用来输送甲醇。
总结:煤气化制甲醇是通过煤气化、气体净化、合成气制甲醇、甲醇纯化和储运等步骤,将煤炭转化为甲醇的生产过程。
该工艺流程需要综合利用各种化学反应和物理分离技术,同时控制工艺参数,以保证甲醇的产量和质量。
煤气化制甲醇技术是煤炭资源高效利用的重要途径,有助于降低对化石燃料依赖,减少环境污染,促进可持续发展。
焦炉煤气制甲醇工艺之压缩操作规程完整
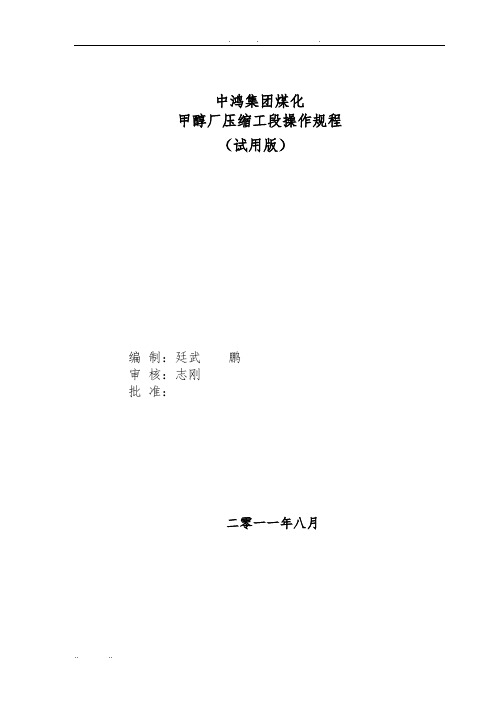
中鸿集团煤化甲醇厂压缩工段操作规程(试用版)编制:廷武鹏审核:志刚批准:二零一一年八月第一章规章制度一、操作规程使用规定1、本规程只适用于生产人员使用。
2、操作规程每人一本,签名登记后领取,在离开本岗位时,需要交回分厂保存,以便新员工使用。
对损坏或丢失者要追究责任。
3、本规程未经允许任何人不可提供给无关人员或向外单位泄露其容。
4、本规程是开车前的试用版本,操作人员应严格按规程进行操作,并在操作的过程中不断修改、完善,使其更具有可操作性,确保装置和人身安全。
二、安全生产责任制1、牢固树立“安全生产第一”的思想,定期召开安全活动会,学上级有关安全生产的文件精神,对事故做到原因没有查清不放过,事故责任者和群众没有受到教育不放过,没有防措施不放过。
2、严格执行动火制,动火前必须办理动火证,岗位严禁穿拖鞋、高跟鞋,上岗前佩带好劳保用品,长发要戴工作帽,并把头发束于帽中,严禁带小孩上岗。
3、严格执行三级安全教育,上岗携带安全作业证。
4、本岗位所属设备交出检修时,要置换合格放完压力确保检修人员的安全。
5、消防器材要定位放置,保持清洁,并会使用。
6、工作时间不得随意离岗,外出必须请假,对外来人员要进行干预,负责对新工人进行安全教育。
三、岗位防火安全责任制1、认真遵守《中华人民国消防法》和本公司制定的有关防火规章制度。
2、岗位操作人员熟知本岗位易燃、易爆物质的特性,并严格遵守安全操作规程和各项防火安全制度。
3、坚守工作岗位,如发现易燃、易爆气体,液体泄漏时,应及时报告,并采取紧急措施予以消除。
4、当接到紧急停车或火警信号后,应立即停车,以防止着火和中毒事故的发生。
5、上岗操作必须穿工作服,严禁吸烟和携带一切火种上岗。
6、擦拭设备时,禁止使用汽油、苯、丙稀类易燃液体擦拭设备。
使用过后的油布、油纱布等物品,应及时除清。
7、配置在各岗位的消防器材和防护用具,要熟练掌握,并在事故发生时能正确使用。
8、凡设置在各单位的消防器材、防护装备,要妥善保管,非事故不能随意使用、拆除或者搬迁。
焦炉煤气制甲醇工艺之锅炉操作规程

河南中鸿集团煤化有限公司甲醇厂开工锅炉操作规程(试用版)编制:李海涛耿红旗审核:李志刚批准:二零一一年八月第一章规章制度一、操作规程使用规定1、本规程只适用于生产人员使用。
2、操作规程每人一本,签名登记后领取,在离开本岗位时,需要交回分厂保存,以便新员工使用。
对损坏或丢失者要追究责任。
3、本规程未经允许任何人不可提供给无关人员或向外单位泄露其内容。
4、本规程是开车前的试用版本,操作人员应严格按规程进行操作,并在操作的过程中不断修改、完善,使其更具有可操作性,确保装置和人身安全。
二、安全生产责任制1、牢固树立“安全生产第一”的思想,定期召开安全活动会,学上级有关安全生产的文件精神,对事故做到原因没有查清不放过,事故责任者和群众没有受到教育不放过,没有防范措施不放过。
2、严格执行动火制,动火前必须办理动火证,岗位严禁穿拖鞋、高跟鞋,上岗前佩带好劳保用品,长发要戴工作帽,并把头发束于帽中,严禁带小孩上岗。
3、严格执行三级安全教育,上岗携带安全作业证。
4、本岗位所属设备交出检修时,要置换合格放完压力确保检修人员的安全。
5、消防器材要定位放置,保持清洁,并会使用。
6、工作时间不得随意离岗,外出必须请假,对外来人员要进行干预,负责对新工人进行安全教育。
三、岗位防火安全责任制1、认真遵守《中华人民共和国消防法》和本公司制定的有关防火规章制度。
2、岗位操作人员熟知本岗位易燃、易爆物质的特性,并严格遵守安全操作规程和各项防火安全制度。
3、坚守工作岗位,如发现易燃、易爆气体,液体泄漏时,应及时报告,并采取紧急措施予以消除。
4、当接到紧急停车或火警信号后,应立即停车,以防止着火和中毒事故的发生。
5、上岗操作必须穿工作服,严禁吸烟和携带一切火种上岗。
6、擦拭设备时,禁止使用汽油、苯、丙稀类易燃液体擦拭设备。
使用过后的油布、油纱布等物品,应及时除清。
7、配置在各岗位的消防器材和防护用具,要熟练掌握,并在事故发生时能正确使用。
- 1、下载文档前请自行甄别文档内容的完整性,平台不提供额外的编辑、内容补充、找答案等附加服务。
- 2、"仅部分预览"的文档,不可在线预览部分如存在完整性等问题,可反馈申请退款(可完整预览的文档不适用该条件!)。
- 3、如文档侵犯您的权益,请联系客服反馈,我们会尽快为您处理(人工客服工作时间:9:00-18:30)。
10万吨甲醇操作法全套第一篇合成岗位操作规程第一章工艺原理一、合成工艺原理甲醇合成是在5.0MPa压力下,在催化剂的作用下,气体中的一氧化碳、二氧化碳与氢反应生成甲醇,基本反应式为:CO+2H2=CH3OH+QCO2+3H2=CH3OH+H2O+Q在甲醇合成过程中,尚有如下副反应:2CO+4H2=(CH3)2O+H2O2CO+4H2=C2H5OH+H2O4CO+8H2=C4H9OH+3H2O此外,还有甲酸甲酯,乙酸甲酯及其它高级醇、高级烷烃类生成。
以铜为主体的铜基催化剂,对于甲醇合成具有极高的选择性,而且在不太高的压力及温度下,要求合成气的净化要彻底,否则其活性将很快丧失,它的耐热性也较差,要求维持催化剂在最佳的稳定的温度下操作。
铜基催化剂一般可在210-280℃下操作,视催化剂的型号及反应器型式不同,其最佳操作温度范围与略有不同。
管壳式反应器的最佳操作温度在230-260℃之间。
在铜基催化剂上合成甲醇,合适的操作压力是5.0~10.0MPa,对于合成气中二氧化碳较高的情况,压力的提高对提高反应速度有比较明显的效果。
合成气的成份对甲醇合成反应的影响较大,由前述反应式可见,要降低能耗,应采用适量的二氧化碳浓度的合成气,若合成气中二氧化碳含量过高,会加重精馏工序的负担并增加了能耗,但二氧化碳含量太低,会导致催化剂活性和转化率过低。
理论的合成新鲜气成份,应满足以下比值:氢碳比f=(H2-CO2)/(CO+CO2)=2.05实际操作中氢碳比应适当增大,大约在2.05~2.15之间。
空速一般控制在8000~10000h-1左右。
甲醇合成是强烈的放热反应,必须在反应过程中不断的将热量移走,反应才能正常进行,管壳式反应器利用管子与壳体间副产中压蒸汽来移走热量,这样,合成反应适宜的温度条件维持就几乎全依赖于副产品中压蒸汽压力操作的正常与稳定。
第二章工艺流程简述由压缩工序来的循环气经入塔气预热器(C0401)预热至225℃,由顶部进入管壳式等温甲醇合成塔(D0401),在铜基触媒的作用下,CO、CO2与H2反应生成甲醇和水,同时还有少量的其它有机杂质生成。
合成塔出塔气经出塔气预热器(C0401)、出塔气冷却器(C0402)和甲醇水冷器(C0403)冷却至40℃,此时气体中的甲醇绝大部分被冷凝下来,然后进入甲醇分离器(F0401)将粗甲醇分离下来。
出F0401的气体一部分作为弛放气排放,以维持合成回路中惰性气体的含量;另一部分气体作为循环气送至压缩工序。
排出的弛放气经压力调压阀PICA-1406减压后送往转化工序作为蒸汽转化炉的燃料。
甲醇分离器底部出来的粗甲醇经液位调节阀LICA-1403控制液位并减压进入闪蒸槽(F0402),大部分溶解气体被闪蒸出来,闪蒸后的粗甲醇送至精馏工序。
闪蒸气送往转化工序作为转化炉低压烧嘴的燃料。
甲醇合成塔的反应温度是通过壳侧副产蒸汽的压力来控制的,根据合成触媒使用时间的不同,其活性温度在230~260℃范围内,副产蒸汽的压力在2.5~4.0MPa之间波动。
甲醇合成塔所产的蒸汽经压力调节阀PRCA-1402减压至2.5MPa后送至转化工序蒸汽转化炉的对流段过热,用于驱动锅炉给水泵的蒸汽透平。
合成汽包(F0403)的锅炉给水由转化工序送来,防止锅炉水结垢的磷酸盐溶液亦由转化工序送来。
为保证炉水质量,从汽包连续排放部分液面水并定期从汽包底部和合成侧壳侧底部排污,排污水送往转化工序的连续排污扩容器。
合成汽包与甲醇合成塔之间的炉水通过自然循环的方式来产生蒸汽。
为了满足开车期间合成塔的升温要求,另设有开工喷射器(L0401)。
开车时中压蒸汽经喷射器(L0401)带动合成塔管外空间的炉水循环并使合成塔升温。
第三章操作指标一.工艺操作指标温度:TR-1402 入塔气温度225℃TRA-1407 出塔气温度根据触媒使用情况确定TI-1410 甲醇分离器出口气温度40℃压力:PI-1403 合成汽包压力 2.4~3.9 MPaPR-1404 入塔气压力 5.1 MPaPDI-1405 合成塔压差0.2 MPaPICA-1406 循环气压力 4.63 MPaPICA-1407 闪蒸槽出口闪蒸汽压力0.4 MPa流量:FI-1401 合成汽包产蒸汽流量8.87t/hrFR-1402 循环气流量289766Nm3/hr液位:LICA-1401 合成汽包液位50%LICA-1403 甲醇分离器液位50%LICA-1405 闪蒸槽液位50%二、主要分析项目及指标:S405 粗甲醇CH3OH 80.26%(vol%)H2O 18.75%(vol%)比重0.8PH值4~6.5S407 炉水PH值7~9(25℃)Na3PO4 5~10mg/LSiO2 <1mg/L第四章岗位操作法第一节开车前准备工作本工序处于原始开车,则必须另外制定方案进行管道、设备、吹除,单体试车、气密性试验,合成塔壳程及汽包清洗、试漏、触媒装填、联动试车等工作。
若检修后再开车,则应针对具体情况作完上述有关工作后,再行开车。
1.检查安全设施是否齐全,如氧呼吸器、过滤式面具、灭火器等。
2.通知维修人员检查本工序所属电仪设备,使电、仪设备处于备用状态,检查DCS系统运行情况,调校正常。
3.检查所属管道、设备是否完整,保温、防腐是否完成,阀门是否灵活,并应在阀杆上涂抹黄油,使所有阀门处于安全开车的位置。
4.检查安全阀是否校正就位,安全阀上是否有铅封,确认启跳整定值。
5.检查所属仪表是否齐全完好,调节系统是否灵活可靠。
6.通知分析人员作好合成工序开车的各项分析准备。
7.公用工程准备就绪,如循环水、脱盐水、电、低压蒸汽、中压蒸汽、氮气、仪表空气、还原用转化气等。
8.检查盲板是否在工作位置上,所有的人、手孔是否封闭严密。
9.转化工序配好5%左右的磷酸盐溶液备用。
10.准备好备用工具、操作记录本,开车方案经过讨论和批准。
第二节开车一、原始开车㈠、系统置换1、空分空压岗位提供“49”品质氮气备用;2、现场将向本系统充氮的管线(N-002)盲板导通;3、现场关甲醇分离器液位调节阀(LICA-1403),闪蒸槽液位调节阀(LICA-1405)的前后切断阀及副线阀;4、关闭合成系统所有的放空阀、导淋阀、取样阀和排污阀;5、开合成系统进出口切断阀,关放空阀;6、以上工作确认无误后,现场开氮气入系统切断阀,向系统充压至0.5MPa;7、开压缩机出口放空阀,各取样阀及其它排放口,采取间断憋压、排放的方法置换系统中的氧气,直至系统中各取样点S402、S403、S404等任一处排放口取样分析氧含量≤0.1%;8、将联合压缩机的副线MG-0304,MG-0305打开流通几次,并通过循环气压力调节阀PICA-1406置换弛放气系统(当不能向火炬系统排放时,可通过现场放空来排放);9、高压系统置换合格后,将闪蒸气压力调节阀PICA-1407甲醇分离器液位调节阀LICA-1403,闪蒸槽液位调节阀LICA-1405的副线打开,进行低压系统的置换(去精馏的阀门关闭),直至系统中的所有排放口取样分析氧气含量≤0.1%为合格。
㈡、阀门设定1、现场关循环气压力调节阀PICA-1406,甲醇分离器液位调节阀LICA-1403,闪蒸槽液位调节阀LICA-1405、闪蒸气压力调节阀PICA-1407的前后切断阀及副线阀,去转化工序的弛放气切断阀,加氢流量调节阀FIC-1403前后切断阀及副线阀。
2、主控关PV-1406、PV-1407、LV-1403、LV-1405、LV-1402、FV-1403。
3、关掉所有排放口,将系统(不包括闪蒸槽F0402,将分离器F0401和闪蒸槽F0402之间的液体管道阀门关死)充压到0.6MPa,然后关闭氮气入口切断阀。
㈢、建立氮气循环1、通知压缩系统,启动联合压缩机,建立氮气循环,并维持合成塔内气体空速在1000~1500h-1(或维持循环量在31000~46500Nm3/h)。
2、当循环气量明显偏低时,开氮气进口阀向系统补充氮气,再关闭氮气切断阀。
㈣、建立汽包液位1、现场开汽包安全阀根部阀,现场压力表根部阀。
2、现场开汽包液位调节阀LICA-1401前后切断阀,关汽包压力调节阀PRCA-1402前后切断阀及副线阀。
3、关开工喷射器L0401蒸汽入口切断阀,关汽包出口蒸汽切断阀。
4、开汽包放空阀,关汽包、合成塔壳程排污阀。
5、开喷射器L0401导淋,启动空冷器C0402,打开甲醇水冷器C0403冷却器进出口阀门。
6、联系转化工序送锅炉水,主控手动调节LV-1401,建立液位后投入自控。
7、联系开工锅炉送开工蒸汽,暖管备用。
8、通知转化工序启动磷酸盐泵,并调节流量至炉水质量达标。
㈤、合成触媒的升温还原还原介质:转化工序来转化气1、现场启动出塔气空气冷却器C0402,同时打开甲醇水冷器C0403循环水进出口蝶阀,通冷却水。
2、待排尽冷凝液后,现场关开工喷射器前导淋,缓慢全开去开工喷射器L0401的开工用中压蒸汽,用喷射器手轮严格控制蒸汽加入量,控制升温速率≤25℃/hr。
3、如果在加热过程中发现开工喷射器振动,可调整喷射器手轮。
当合成塔出口温度升高到100℃时,减少蒸汽加入量,使合成塔恒温2hr。
4、当合成塔出口温度达120℃时,再减少蒸汽加入量,恒温4hr以上,观察甲醇分离器F0401的液面,当分离器液面不再升高时,恒温即可结束。
现场打开甲醇分离器底部导淋阀,排出分离器F0401中分析出的物理水,并称重计量(与理论出水量相比较),直到有氮气跑出为止。
5、现场打开转化气进合成系统FIC-1403前后切断阀,主控手动调节FV-1403控制转化气加入量。
当入塔器预热器C0401入口前的气体中(CO+H2)浓度达0.5~0.8%,保持FV-1403流量稳定,触媒在此浓度下进行还原。
在此温度(120℃)及该(CO+H2)浓度(0.5~0.8%)下,继续还原触媒,直到合成进出口塔(CO+H2)浓度相等为止。
6、维持(CO+H2)浓度在0.5~0.8%,慢慢增加去开工喷射器L0401的蒸汽,使系统以每次提温10~15℃/hr的速度逐级升温还原,每一次提温前,合成塔进出口(CO+H2)浓度一定要达到一致。
(进出口还原气浓度差ΔH2≤0.1%),保证每一级温度下触媒都得到充分的还原,绝不可急躁行事,要做到提温不提(CO+H2),提(CO+H2)不提温。
7、150~200℃为主还原期,采用分段提温,每段温升约10℃,每段恒至(CO+H2)气不再消耗后,再提温。
通知分析人员每半小时分析一次入塔气和循环气中还原气的含量;并且在触媒还原过程中,在甲醇分离器F0401后收集还原过程中生成的水量,借此掌握催化剂的还原进程。
8、合成塔出口温度达190~200℃时,触媒就接近还原完全,再继续开大到开工喷射器L0401的蒸汽量。