催化裂化再生烟气能量回收的计算
最新万吨年催化裂化反应—再生系统计算
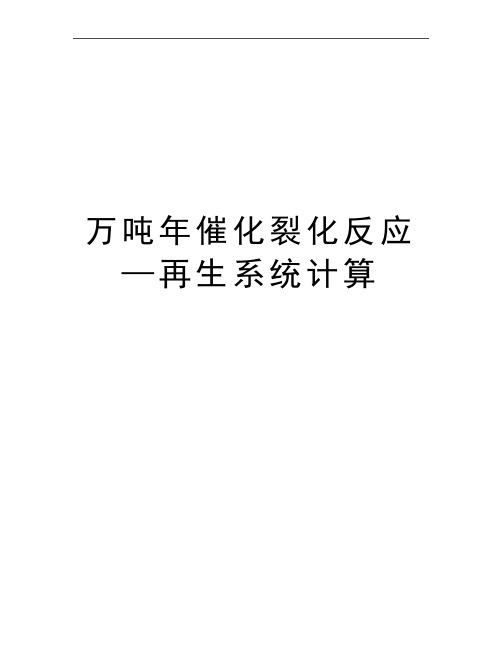
万吨年催化裂化反应—再生系统计算摘要催化裂化装置主要由反应—再生系统、分馏系统、吸收稳定系统和能量回收系统构成,其中反应—再生系统是其重要组成部分,是装置的核心。
设计中以大庆原油的混合蜡油与减压渣油作为原料,采用汽油方案,对装置处理量为250万吨/年(年开工8000小时)的催化裂化反应—再生系统进行了一系列计算。
根据所用原料掺油量低,混合后残炭值较低,其硫含量和金属含量都较小且由产品分布和回炼比较小,抗金属污染能力强,催化剂的烧焦和流化性能较好及在此催化剂作用下,汽油辛烷值较高这些特点,故采用汽油方案。
设计中,采用了高低并列式且带有外循环管的烧焦罐技术,并对烧焦罐式再生器和提升管反应器进行了工艺计算,其中再生器的烧焦量达32500㎏/h,烧焦罐温度为680℃,稀相管温度为720℃,由于烟气中CO含量为0,则采用高效完全再生。
在烧焦罐中,烧焦时间为1.8s,罐中平均密度为100㎏/m3,烧焦效果良好。
在提升管反应器设计中,反应温度为505℃,直径为1.62 m,管长为29 m,反应时间为3s,沉降器直径为2 m,催化剂在两器中循环,以减少催化剂的损失,提高气—固的分离效果,在反应器和再生器中分别装有旋风分离器,旋风分离器的料腿上装有翼阀,在提升管和稀相管出口处采用T型快分器。
由设计计算部分可知,所需产品产率基本可以实现。
关键词:催化裂化,反应器,再生器,提升管,烧焦罐,完全再生AbstractThe catalytic cracker constitutes reaction-regeneration system、fraction system、 absorption-stabilization system and power-recovery system. The most important and core part of the unit is reaction-regeneration system. The DaQing Crude wax oil and vacuumdistillation residue are taken as feedstock. This paper is a series of processing calculation mainly about reaction-regeneration system. With gasoline scheme, capacity is designed to be 150 Mt/a under the condition of 8000 hours’ operating time.After being mixed the contents of blending residuum, sulphur and metal as well as the carbon residue in feedstock are low. As the even distribution of product, superior properties of resisting metal pollution and the catalyst’s coke burning and fluidization as well as the higher octane number of gasoline with the function of this catalyst, the gasoline scheme are taken.In the design, technology of coke-burning drum with outsider-circulation tube is applied. The drum is of high-low parallel style. The processing calculation is about reproducer of coke-burning drum style and riser, coke-burning capacity is 32500㎏/h, the temperatures of coke-burning drum and dilute phase riser are respectively 680℃and 720℃. Accounting that there is no carbon monoxide in off-gase. The high efficient regeneration is applied. In the coke-burning drum, the scorching time is 1.8s and its average density is 100 ㎏/m3, thus the effect of coke-burning is good. The temperature of riser is 505℃. Its diameter is 1.62m and the length is 29m. While its reaction time is 3s and the diameter of settling vessel is 2m. Catalysts circulate in the drum and reactor. In order to reduce the loss of catalyst and improve the effect of gas-solid separation, cyclones are equipped in both reactor and reproducer. There is trickle vavle on the dipleg of the latter, whilethe T-rapid separation unit is fitted in the exit of riser and dilute phase riser. From the date, the unit can substantially reach the required yield. Keywords: Catalystic cracking, Reactor, Reproducer, Riser, Coke-burning drum毕业设计(论文)原创性声明和使用授权说明原创性声明本人郑重承诺:所呈交的毕业设计(论文),是我个人在指导教师的指导下进行的研究工作及取得的成果。
重油催化裂化装置的能耗分析

“ 五 ” 末 降低 2 % 左 右 。炼 油 、 工 、 金 等 十 期 0 化 冶 工 业 的 耗 能 约 占全 国 总 能 耗 的 一半 , 炼 油 工 业 而 又是 其 中 的耗 能大 户 。我 国炼 油 装置 的 能耗 与 国 外先 进 水 平 有 较 大 差 距 。 催化 裂 化 装 置是 炼 油 ]
仍 有 较 大 的 节 能 潜 力 , 进 一 步 提 高 再 生 器 及 烟 气能 量 回收 系 统 的 能 量 利 用 效 率 。根 据 计 算 和 分 需
析结果探讨该装置进一步 的节能措施 。
关 键 词 : 油 催 化 裂 化 装 置 MI 重 P技 术 能耗
1 前
言
为 外提 升管 形 式 , 再生 器为 两段 串联形 式 , 有烟 设
力为 01MP , 对 湿 度 为 7 %。装 置 反应 器 、 . a相 7 再
生器和 烟 气能量 回收 系统 的主 要操 作数据 见表 3 。
表 3 装置主要操 作条 件
项
反 应 压 力/ P M a
目
数
值
反 应 温 度/ ℃
进 料量 / ・ t h 回炼 质量 比
进料温 度
摘 要 某 公 司 重 油 催 化 裂 化 装 置 采 用 MI 术 改 造 后 能 耗 下 降 , 主要 原 因是 由于 反应 需 热 P技 其
减 少 、 出 蒸 汽 量 增 加 。采 用 能 量 转 换 与 传 输 、 艺 利 用 和 能 量 回 收 三 环 节 模 型 对 该 装 置 的 能 量 输 工 平 衡 和 有 效 能 进 行 计 算 , 析 装 置 目前 能 量 利 用 的 合 理 程 度 。结 果 表 明 , 装 置 f ̄ 量 回收 环 节 分 该 l E O ,
毕业设计250万吨年催化裂化反应再生系统计算
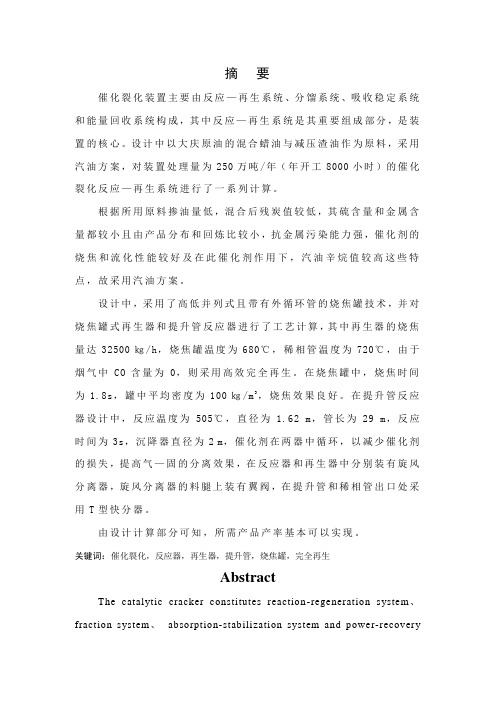
摘要催化裂化装置主要由反应—再生系统、分馏系统、吸收稳定系统和能量回收系统构成,其中反应—再生系统是其重要组成部分,是装置的核心。
设计中以大庆原油的混合蜡油与减压渣油作为原料,采用汽油方案,对装置处理量为250万吨/年(年开工8000小时)的催化裂化反应—再生系统进行了一系列计算。
根据所用原料掺油量低,混合后残炭值较低,其硫含量和金属含量都较小且由产品分布和回炼比较小,抗金属污染能力强,催化剂的烧焦和流化性能较好及在此催化剂作用下,汽油辛烷值较高这些特点,故采用汽油方案。
设计中,采用了高低并列式且带有外循环管的烧焦罐技术,并对烧焦罐式再生器和提升管反应器进行了工艺计算,其中再生器的烧焦量达32500㎏/h,烧焦罐温度为680℃,稀相管温度为720℃,由于烟气中CO含量为0,则采用高效完全再生。
在烧焦罐中,烧焦时间为 1.8s,罐中平均密度为100㎏/m3,烧焦效果良好。
在提升管反应器设计中,反应温度为505℃,直径为 1.62 m,管长为29 m,反应时间为3s,沉降器直径为2 m,催化剂在两器中循环,以减少催化剂的损失,提高气—固的分离效果,在反应器和再生器中分别装有旋风分离器,旋风分离器的料腿上装有翼阀,在提升管和稀相管出口处采用T型快分器。
由设计计算部分可知,所需产品产率基本可以实现。
关键词:催化裂化,反应器,再生器,提升管,烧焦罐,完全再生AbstractThe catalytic cracker constitutes reaction-regeneration system、fraction system、absorption-stabilization system and power-recoverysystem. The most important and core part of the unit is reaction-regeneration system. The DaQing Crude wax oil and vacuum distillation residue are taken as feedstock. This paper is a series of processing calculation mainly about reaction-regeneration system. With gasoline scheme, capacity is designed to be 150 Mt/a under the condition of 8000 hours’ operating time.After being mixed the contents of blending residuum, sulphur and metal as well as the carbon residue in feedstock are low. As the even distribution of product, superior properties of resisting metal pollution and the catalyst’s coke burning and fluidization as well as the higher octane number of gasoline with the function of this catalyst, the gasoline scheme are taken.In the design, technology of coke-burning drum with outsider-circulation tube is applied. The drum is of high-low parallel style. The processing calculation is about reproducer of coke-burning drum style and riser, coke-burning capacity is 32500㎏/h, the temperatures of coke-burning drum and dilute phase riser are respectively 680℃and 720℃. Accounting that there is no carbon monoxide in off-gase. The high efficient regeneration is applied. In the coke-burning drum, the scorching time is 1.8s and i ts average density is 100 ㎏/m3, thus the effect of coke-burning is good. The temperature of riser is 505℃. Its diameter is 1.62m and the length is 29m. While its reaction time is 3s and the diameter of settling vessel is 2m. Catalysts circulate in the drum and reactor. In order to reduce the loss of catalyst and improve the effect of gas-solid separation, cyclones are equipped inboth reactor and reproducer. There is trickle vavle on the dipleg of the latter, while the T-rapid separation unit is fitted in the exit of riser and dilute phase riser. From the date, the unit can substantially reach the required yield.Keywords: Catalystic cracking, Reactor, Reproducer, Riser, Coke-burning drum毕业设计(论文)原创性声明和使用授权说明原创性声明本人郑重承诺:所呈交的毕业设计(论文),是我个人在指导教师的指导下进行的研究工作及取得的成果。
关于催化裂化装置主风机组烟机能量回收系统的思考

2018年05月关于催化裂化装置主风机组烟机能量回收系统的思考姚金磊胥瑞林(中石油云南石化有限公司,云南昆明650300)摘要:云南石化重油催化裂化装置自开工运行以来,受到烟机轴功率、主风机轴功率以及装置处理量的制约,电动机一直处于耗电做功状态,显现出提高烟机能量回收效率的重要性与迫切性。
关键词:烟机轴功率;主风机轴功率;电机轴功率;节能降耗主风机组承担着再生器烧焦的流化风量以及烟气能量回收的主要作用,是装置节能降耗的主要设备。
本装置主风机组采用三机组配置形式,采用烟气轮机+轴流风机+增速箱+电机的连接方式。
按年平均正常工况考虑,主电机20000KW 无法满足解除烟机后的主风机组-30891KW 低负荷运行功率要求,烟机33000KW 理论上可以单独带动主风机做功,但由于烟机并不能达到理想状态的功率输出,因此主风机组电机长期处于耗电做功的状态,电机发电的可能性不大。
故提高烟机能量回收效率尤其显得重要与迫切。
1主风机组能量回收的影响因素及其处理措施烟机输出轴功率计算公式:N =1.634∗P 1V 1K []1-(P 2/P 1)(K -1)/K η/(K -1)(1)其中N-烟机轴功率KW ,P 1-烟机入口压力KG/CM 2,P 2-烟机出口压力KG/CM 2,V 1-烟机入口流量,K-烟气的绝热系数,η-烟机总效率。
1.1烟机入口压力对于能量回收的影响及建议从某种程度上来看,可以将烟机类比成为一个降压孔板,当烟机入口温度变化不大时,可以用下列公式计算烟机入口压力与流量的关系[1]:P 12=(G +A )/C(2)其中P 1是烟机入口压力KG/CM 2,G 烟气质量流量kg/S ,C,A 均是常熟。
可以看出,当烟机入口温度变化不大时,烟机入口流量与烟机入口压力存在一一对应的关系。
由(1)可以看出,在其他因素不变的情况下烟机入口压力P 1与烟机功率基本呈现出正比关系,提高烟机入口压力可以显著的增加烟机输出轴功率N 。
催化裂化装置设计工艺计算方法

1.3.3稀相段直径
稀相段中点压力=0.3315MPa 稀相段温度=675+273=946K 气体体积流率=46.84m3/s 取稀相直径=9.7m 稀相线速=0.62m/s
1.3.4稀相段高度 取稀相段高度为12m
1.3.5过渡段高度 取过渡角为45度
1.3.6催化剂的停留时间
过渡段高度为1.25m
195973.42
1.3.1密相床直径
取密相床密度300kg/m3稀相段平均密度25kg/m3 密相段高度为9m 稀相段高度为12 m 密相段中点压力=0.3465MPa 密相段温度=273+671=943k 气体体积流率=44.67m3/s 取密相段线速为1.1m/s
密相段直径=7.19m
1.3.2 密相段的高度 再生器密相床体积==222cm3 密相段高度==5.45m
1.2.13再生器物料平衡
入方 kg/h
I段干烟气
174422.8
II段干烟气
37492.1
待生剂待入烟 1080 气
I段主风带水 汽
3488.5
II段主风带水 670.8 汽
I段松动吹扫 汽
1500
II段松动吹扫 500 汽
焦炭
17000
循环催化剂 1010000
合计
1250100
出方kg/h
I段干烟气
1.1.2理论干空气量的计算
Ⅰ段碳燃烧生成二氧化碳需O2量706.1×1=706.1kmol/h Ⅰ段碳燃烧生成一氧化碳需O2量413.7×0.5=206.9kmol/h Ⅰ段氢燃烧生成水需O2量595×0.5=297.5kmol/h 理论需O2量=706.1+206.9+297.5=1210.5kmol/h=38736kg/h 理论需N2量=1210.5×79/21=4553.8kmol/h=127506.4kg/h Ⅰ段理论干空气量=O2+N2 =5764.3kmol/h=166242.4kg/h Ⅱ段碳燃烧生成CO2需O2量=197.6kmol/h=6323.2kmol/h Ⅱ段碳燃烧生成CO2需N2=197.6×79/21=743.4kmol/h=20813.9kg/h Ⅱ段碳燃烧生成CO2需N2== O2+ N2=941kmol/h=23137.1kg/h 1.1.3 实际干空气量
催化裂化装置再生烟气醇胺法回收CO2技术模拟研究

催化裂化装置再生烟气醇胺法回收CO2技术模拟研究摘要:炼油企业的CO2排放主要分为直接排放和间接排放,前者包括燃料燃烧过程、工艺过程等产生的CO2排放;后者指企业使用由石化能源转化的外购能源(包括电力、热力、蒸汽等)所产生的碳排放。
在国内炼油企业中,CO2的直接排放量占总排放量的85%左右,其中催化裂化装置的CO2排放量占比最高,占直接排放量的25%~50%。
本文对催化裂化装置再生烟气醇胺法回收CO2技术模拟进行分析,以供参考。
关键词:催化裂化;再生烟气;醇胺法引言催化裂化再生烟气是炼厂生产装置中最大的气体排放源。
再生烟气中含有大量的氮氧化物、二氧化硫,已成为我国炼厂主要的空气污染源。
随着催化裂化装置工况的调整,再生器出口烟气的污染物浓度波动范围较大,原料属性、运行参数、污染物进出口浓度等参数之间未建立关联关系。
催化裂化脱硝装置的进口浓度发生波动时,容易出现出口烟气无法稳定达标、脱硝剂浪费等问题。
一、概述许多学者们致力于探究催化裂化出口烟气与过程参量的影响因素。
通过研究脱硝剂、助燃剂的作用机理,分析了氮氧化物超标的影响因素,并提出相应解决措施,可有效控制烟气氮氧化物的排放浓度。
以上研究方法主要是针对催化裂化出口烟气相关因素的辨识,但催化裂化出口烟气的智能建模仍然是一个亟需解决的难题。
建立了一种基于热力学平衡算法的烟气析碳反应模型,验证了模型的析碳量与烟气温度、压力、空气配比、水蒸气配比的影响。
提出了一种前置烧焦式催化裂化装置的稳态机理模型,探究烧焦罐气固流动的复杂性。
以上研究方法无法实现出口再生烟气浓度的直接表达,因此,利用机理模型直接预测出口烟气浓度存在困难。
近年来,神经网络是一种广泛应用于各种复杂环境的智能预测手段。
提出了一种基于卷积神经网络的长短期记忆网络模型,用于预测催化裂化装置再生烟气氮氧化物的浓度值,实验结果表明该模型表现出了很好的预测性能。
通过一种结合卷积神经网络的长短期记忆网络模型,实现了再生烟气氮氧化物的预测,实验结果表明该方法能够高效准确地处理大量高维数据。
催化裂化装置再生系统设备壁温及散热计算_张荣克

催化裂化装置再生系统设备壁温及散热计算张荣克中国石化集团北京设计院 100011 摘 要 催化裂化装置再生系统设备(包括再生器、三级旋风分离器和烟道等)连续出现应力腐蚀开裂问题,引起有关部门的普遍关注。
论文从传热的基本准则出发,结合多年的设计和使用经验,给出了设备器壁温度与隔热衬里参数、环境温度之间的关联式和计算图表,以供工程设计参考。
关键词 催化裂化 再生系统设备 壁温 散热计算 随着重油催化裂化工艺的发展,催化裂化原料中N,S ,Cl 化合物的含量比过去的馏份油催化裂化原料高得多。
这些化合物在裂化反应过程中大部分都沉积于焦炭里,随着待生催化剂进入再生系统。
在催化剂烧焦过程中,一部分转化为N,S 的氧化物及盐类。
因再生烟气中含有一定量的水分,当再生设备的壁温低于烟气的酸露点时,器壁内面会出现冷凝液。
N,S,Cl 的盐类大都是可溶性的,因此冷凝液中含有N O -2,NO -3,SO =3,SO =4,Cl -等离子,这种介质将会引起设备的腐蚀,尤其应力腐蚀开裂对设备的危害极大。
近几年来,我国有多套重油催化裂化装置的再生设备出现了应力腐蚀开裂事故。
重油催化裂化装置再生设备产生应力腐蚀开裂的原因较复杂,其中器壁温度过低,出现结露是直接原因。
但如果器壁温度过高,装置热损失会加大。
因此,正确地选择器壁温度,是重油催化裂化装置一项重要的设计内容。
本文从传热的基本准则出发,结合多年来设计和使用经验,导出了器壁温度与设备隔热衬里参数、环境温度之间的关联式,以解决目前工程设计的需要。
1 传热计算的基本关联式高温烟气的热量由再生器内部通过隔热衬里和器壁传到大气中,图1表示了这种热传导过程。
根据热量平衡,烟气传给衬里的热量Q 1=衬里排放到大气中的热量Q 2。
总传热方程可用式(1)表示:q = t /R (1)式中:q ——单位时间内,单位面积上所传出的热量或称热流密度,W/m 2; t ——传热推动力, t =t 1-t 0,℃;R ——传热热阻,R =R 1+R i +R b +R 0,m2・℃/W ;其中:t 1——再生烟气温度,℃;t 0——大气温度,℃;R 1——烟气对衬里壁的传热热阻,m 2・℃/W ;R i ——衬里热阻,m 2・℃/W;R b ——器壁的传热热阻,m 2・℃/W ;R 0——器壁对大气的放热热阻,m 2・℃/W 。
炼油工艺学第十章 催化裂化第七节 反应-再生系统工艺计算 共15页

油品升温热 反应热 合计
18.07.2019
78.72 100.00
9.05 11.5
18.16 23.06
1.26 1.61
5.51 7.00
44.74 56.83
/
/
/
/
78.72 100.00
石油加工工程
78.72 /
18.16 1.90 10.23
/ 36.40 12.04 78.72
18.07.2019
石油加工工程
13
再生-待生线路压力平衡
推动力
阻
项目 再 生 再生器顶压(表) 剂 再生器稀相蓄压 线 再生器过渡段蓄压 路 再生器密相段蓄压
再生斜管蓄压 合计
MPa kg/cm2
项目
0.1474 1.5027 0.0010 0.0102 0.0112 0.1140 0.0155 0.1585 0.0160 0.1632 0.1911 1.9486
万t/a 15.87 3.81 19.68 1.38 1.90 8.46 5.80 0.61 1.53 19.68
6
再生器物料平衡计算有两种情况:
通过再生器物平确定主风量和烟气量
由现场标定数据通过燃烧计算确定焦炭量,从而确定全装
置物平
入方,kg/h
出方,kg/h
干空气
136380
干烟气
137520
待生立管蓄压 合计
MPa kg/cm2
0.1224 1.2479 0.0001 0.0014 0.0017 0.0173 0.0311 0.3175 0.0577 0.5887 0.2130 2.1728
阻
项目