CAE仿真分析报告
cae分析报告

cae分析报告随着工业化进程的加速和人们生活水平的不断提高,各种设备的使用和生产增加,对于设备的质量和安全性的要求也越来越高。
而在这种背景下,各类计算机辅助工程软件(CAE)不断涌现,为人们提供了更为方便和精确的设备分析和设计方法。
在使用CAE分析工具进行设备分析时,报告是最终呈现的结果,而CAE分析报告的质量和准确性对于工程设计和安全性意义重大。
一、CAE分析的意义在进行工程设备的设计和分析过程中,传统的方法主要是基于经验和试验来确定设备的结构和性能。
然而这种方法的缺点就在于它比较消耗时间和精力,并且容易出现误差。
而CAE分析的方法则不同,在CAE分析中,我们可以先假定一些初步的方案,并通过计算机辅助工程软件对其进行分析和比较,最终选择最优的方案。
这种方法的优点是显而易见的:既可大大缩短设计的周期,又可减小出现错误的概率,同时还能够更准确地预测设备的性能和安全性。
二、CAE分析报告的特点和采用传统方法不同的是,CAE分析报告的报告内容需要符合数据的准确性、完整性、时效性、可读性与易懂性等要求,其特点主要包括以下方面:1.数据和结果可靠性CAE分析报告是通过计算机模拟实现的,因此数据和结果可靠性非常重要。
报告中的所有数据和模型都必须经过仔细的检查和验证,并遵循必要的准确性和完整性要求。
除此之外,毕竟计算机辅助工程是在虚拟环境中进行,因此其他情况会对计算产生影响,因此需要在报告中考虑这种影响。
2.简明扼要而又完整性任何一个设计和分析报告都需要足够的详细和表述,以便他人正确理解和理解。
较大型的CAE分析报告容易出现部分不完整或需要一些特殊知识的技术名称问题,因此报告中最好设立本材料、分析方法、分析结果和结论等。
3.使用免费软件一些自由开源软件可以免费使用,在处理一些小问题的时候,进行分析非常方便。
因为通常使用免费软件分析时,需要离线计算。
三、CAE分析报告的重要性CAE分析报告对于工程设计和安全性意义重大。
CAE仿真分析报告
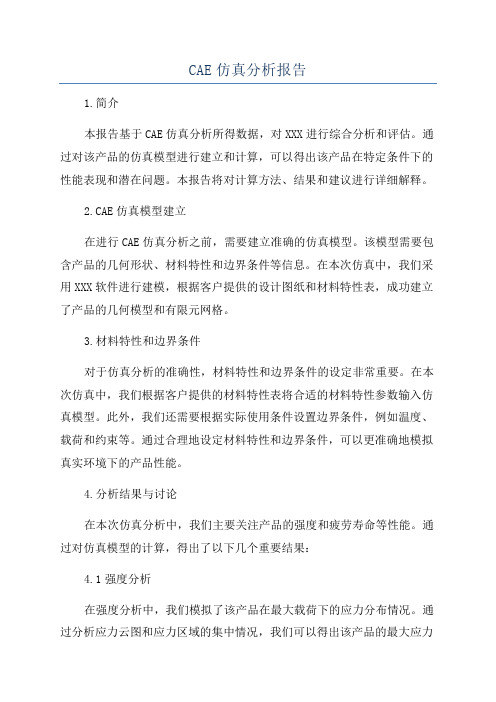
CAE仿真分析报告1.简介本报告基于CAE仿真分析所得数据,对XXX进行综合分析和评估。
通过对该产品的仿真模型进行建立和计算,可以得出该产品在特定条件下的性能表现和潜在问题。
本报告将对计算方法、结果和建议进行详细解释。
2.CAE仿真模型建立在进行CAE仿真分析之前,需要建立准确的仿真模型。
该模型需要包含产品的几何形状、材料特性和边界条件等信息。
在本次仿真中,我们采用XXX软件进行建模,根据客户提供的设计图纸和材料特性表,成功建立了产品的几何模型和有限元网格。
3.材料特性和边界条件对于仿真分析的准确性,材料特性和边界条件的设定非常重要。
在本次仿真中,我们根据客户提供的材料特性表将合适的材料特性参数输入仿真模型。
此外,我们还需要根据实际使用条件设置边界条件,例如温度、载荷和约束等。
通过合理地设定材料特性和边界条件,可以更准确地模拟真实环境下的产品性能。
4.分析结果与讨论在本次仿真分析中,我们主要关注产品的强度和疲劳寿命等性能。
通过对仿真模型的计算,得出了以下几个重要结果:4.1强度分析在强度分析中,我们模拟了该产品在最大载荷下的应力分布情况。
通过分析应力云图和应力区域的集中情况,我们可以得出该产品的最大应力点和应力集中区域。
根据计算结果,我们发现产品的强度较高,没有明显的应力集中区域。
4.2疲劳分析在疲劳分析中,我们模拟了该产品在长期使用条件下的疲劳寿命。
通过设定适当的载荷条件和循环次数,我们可以计算出产品的寿命曲线和疲劳寿命。
根据计算结果,我们发现产品在设计寿命内可以正常工作,并且没有出现严重的疲劳损伤。
5.问题与建议通过对仿真结果的分析,我们发现该产品在设计条件下表现良好,没有明显的问题。
5.1强度优化虽然该产品的强度较高,但我们建议客户在设计上进一步考虑一些强度优化的手段,例如增加壁厚或者加强一些关键部位的结构,以进一步提高产品的强度和可靠性。
5.2疲劳寿命提升尽管该产品疲劳性能良好,但我们建议客户在设计上考虑一些疲劳寿命提升的措施,例如使用更高强度的材料或者改变产品的形状,以延长产品的使用寿命。
CAE分析报告流程

CAE分析报告流程CAE分析报告是以有限元分析(CAE)技术为基础的工程分析报告,用于对复杂结构或部件的性能进行深入评估和优化。
本文将详细介绍CAE分析报告的流程,包括前期准备、建模与网格划分、加载和边界条件的定义、求解和后处理等步骤。
一、前期准备阶段在开始CAE分析之前,首先需要明确分析的目标和要求,包括结构的应力、变形、疲劳寿命等指标。
此外,还需收集相关的材料性能参数、工程图纸、边界条件等基础数据,并对其中的约束和假设进行评估。
二、建模与网格划分阶段建模是将真实的结构或部件抽象成数学模型的过程。
在这个阶段,应根据实际情况选择合适的建模方法,如二维平面模型或三维实体模型,并建立相应的几何特征。
此外,还需要根据结构的复杂程度和精度要求选择适当的网格划分方法,如四面体网格、六面体网格或八面体网格等。
三、加载和边界条件的定义阶段加载和边界条件的定义是指对模型施加外部载荷和约束条件,模拟真实工况下的力学行为。
例如,可以通过定义施加载荷的大小、方向和分布方式来模拟实际工作状态下的负荷;同时,还需要定义与其他部件的接触、约束和固定等边界条件。
四、求解阶段在完成加载和边界条件的定义后,即可进行求解过程。
求解是基于有限元法,将结构或部件划分成有限数量的元素,利用数学和力学原理对每个元素进行离散描述,并通过求解相应的线性或非线性方程组得到模型的应力、变形和其他相关结果。
在进行求解之前,还需选择合适的求解器和合理的控制参数,并进行模型的数值稳定性和收敛性分析。
五、后处理阶段求解完成后,需要对计算结果进行后处理和分析。
后处理包括对结果数据的提取、整理和可视化,以便更直观地了解结构的应力、变形分布和其他性能指标。
同时,还可进行数据对比、灵敏度分析和优化设计等后处理工作,从而得到一些有关结构性能和优化可能性的建议。
最后,根据实际情况和需求,可以将最终的结果汇总成CAE分析报告。
该报告将包括前期准备、建模与网格划分、加载和边界条件的定义、求解和后处理等各个阶段的详细过程、结果和分析,以及对结构性能和优化方案的评估和建议。
CAE实验报告

CAE实验报告一、实验目的本次 CAE 实验的主要目的是对某机械结构在特定载荷条件下的力学性能进行分析和评估,以确定其是否满足设计要求,并为优化设计提供依据。
二、实验对象实验对象为某型汽车发动机的连杆结构。
该连杆在发动机工作过程中承受着周期性的拉伸、压缩和弯曲载荷,其力学性能直接影响发动机的可靠性和耐久性。
三、实验原理CAE(Computer Aided Engineering)即计算机辅助工程,是一种利用计算机技术对工程结构进行数值模拟和分析的方法。
本次实验采用有限元分析(Finite Element Analysis,FEA)方法,将连杆结构离散化为有限个单元,并通过求解节点的位移和应力来获得整个结构的力学响应。
有限元分析的基本原理是基于变分原理,将连续的求解域离散为有限个单元,每个单元通过节点相互连接。
通过对每个单元的力学特性进行分析,建立单元刚度矩阵,然后将所有单元的刚度矩阵组装成总体刚度矩阵,再根据边界条件和载荷条件求解总体平衡方程,得到节点的位移和应力。
四、实验设备与软件本次实验使用的硬件设备为高性能计算机工作站,配备多核处理器和大容量内存,以满足有限元分析的计算需求。
实验所使用的软件为 ANSYS Workbench,这是一款功能强大的CAE 分析软件,包含了建模、网格划分、求解和后处理等模块,能够方便地对各种工程结构进行分析。
五、实验过程1、几何建模使用三维建模软件(如 SolidWorks)创建连杆的几何模型,并将其导入到 ANSYS Workbench 中。
2、材料定义为连杆结构定义材料属性,包括弹性模量、泊松比、密度等。
3、网格划分对连杆模型进行网格划分,采用合适的单元类型和尺寸,以保证计算精度和效率。
在关键部位(如连杆大头与小头的过渡区域)采用较细密的网格,而在非关键部位采用较粗疏的网格。
4、边界条件与载荷施加根据实际工作情况,确定连杆的约束条件和所承受的载荷。
约束连杆大头孔的周向位移和轴向位移,在小头孔处施加周期性的拉伸和压缩载荷。
CAE-整车碰撞仿真分析

整车碰撞仿真分析完成整车建模、设置好相应的测试单元,并核对模型整车情况与试验完全一致后即可将模型提交计算,完成计算后即可对结果进行分析。
正面刚性壁碰撞仿真分析内容主要包括:仿真计算可信性分析;整车和关键部件变形分析;B柱速度/加速度分析;A柱折弯分析;前侵入分析;假人伤害情况分析。
1 仿真计算可行性分析在整车碰撞仿真中虽然顺利完成计算,但由于有以下三个原因的存在并不能保证该计算结果完全准确可靠。
(1)在有限元仿真计算中涉及多种积分算法和不同的接触算法,系统为保证计算正常进行有时会自动增加某些部件的质量,如果该质量增加太多则会导致后期计算结果不可信。
(2)为节约计算时间计算中更多时候采用了非全积分的积分算法,这时将有可能在计算中发生沙漏,导致系统总体能力不守恒。
(3)在接触计算中如果接触设置不合理,将有可能产生较大的界面滑移能,这也是导致系统总能量不守恒的重要因素。
所以在顺利完成仿真计算后,需要对计算结果进行分析。
只有由于上述因素导致的质量增加和能量变化在可接受的范围内,再能认为该模型仿真计算结果是可信的,值得分析的。
打开计算输出的glstat文件或binout文件的glstat选项(见图1. 1),可以方便查看模型计算中涉及的以上因素变化曲线。
图1.1binout文件glstat选项菜单质量增加和能量变化查看内容为added_mass、energy_ratio,一般要求最终质量增加和能量变化不得超过5%,通常计算中初始质量增加在10kg以内,随着计算的进行整车质量还将有所增加。
关于能量变化曲线一般查看hourglass_energy、internal_energ y、kinetic_energy、interface_energy、total_energy这五项。
通常情况这五条曲线形状大致如图1.2。
图1.2仿真过程中能量变化曲线如图1.2可以观察到系统动能逐步转换为内能的过程,图中几条曲线一般应该为光滑过渡,如果在某位置发生突变则有可能是这个位置发生了较大的沙漏或质量增加。
CAE-分析报告样板详解

A
Page 21 of 24
CAE Group – Forming Simulation Report (成型分析报告)
Forming process:5mm to the draw home
A
Page 22 of 24
CAE Group – Forming Simulation Report (成型分析报告)
Forming process:The binder closing
试模时首先保证重力状态和压边圈闭合 状态和模拟情况一致是非常重要的,复 杂曲面的压边圈和闭合情况对最终的成 型结果影响很大,但复杂压边圈闭合的 精确模拟也是成型模拟的难点之一
A
Page 13 of 24
CAE Group – Forming Simulation Report (成型分析报告)
CAE Group – Forming Simulation Report (成型分析报告)
Dynaform Simulation
Project Name(项目名称): BBDC 300C Panel Number (产品号):05065358AD Part Description(产品名称):前围板 Analyst(分析):焦雷魁 Process layout (工艺规划) :刘宏俊 Date(日期): 11.01.2005 Sim File(模拟文件版本);V02
CAE Group – Forming Simulation Report (成型分析报告)
料厚,减薄量和表示材料变形状态的成形极限图(是衡量材料成型性(破裂) 的3个重要指标
好的模拟结果(Safe)应该是
cae分析报告
cae分析报告CAE(计算机辅助工程)是一种通过计算机模拟和仿真技术来分析物体性能和行为的方法。
它在各个领域都得到了广泛的应用,例如汽车工程、航空航天、建筑结构等。
本篇文章将对CAE分析报告进行探讨,介绍其意义、内容和编写要点。
一、概述CAE分析报告是基于对实际物体进行仿真和模拟后得到的结果,用于评估物体的性能、强度、对环境的响应等。
它提供了全面的分析结果和可行的改进方案,为工程师和设计师在产品开发和优化过程中提供指导意见。
因此,编写一份准确、详细的CAE分析报告对于工程项目的成功和效率至关重要。
二、内容1. 建模与网格划分CAE分析的第一步是建立物体的数学模型,并进行网格划分。
模型的精确度和网格质量将对计算结果的准确性产生重要影响。
因此,在报告中需要详细描述建模过程,包括采用的软件和方法、模型的几何特征、所选网格类型和质量等。
2. 载荷和约束条件在进行CAE分析前,需要确定物体所受的外部载荷和内部约束条件。
比如,在汽车工程中,载荷可以是行驶在不同路况下的动态载荷,约束条件可以是车轮在地面上的接触条件。
在报告中,需清晰地描述这些载荷和约束条件,并给出计算依据和分析原理。
3. 结果分析CAE分析的核心是得到准确的结果,并进行深入的分析与解释。
在报告中,应包括物体的应力分布、变形情况、疲劳寿命、流体流动轨迹等相关结果。
同时,需要对结果进行分析,解释其原因和影响,并与实验数据进行对比,以验证模型的准确性。
4. 优化方案根据CAE分析的结果,可以提出改进和优化方案,以提高产品的性能和可靠性。
在报告中,需要详细描述这些方案的设计思路和实施步骤。
同时,对于每个方案,应进行CAE分析以评估其效果,并给出具体的指导建议。
三、编写要点1. 语言简洁明了:CAE分析报告通常是给工程师和设计师阅读的,因此要避免使用过于专业或晦涩的术语和定量方法。
尽可能使用简单明了的语言,使读者能够轻松理解和掌握分析结果。
2. 图表展示清晰:在CAE分析报告中,经常使用图表来展示结果和数据。
CAE分析报告(2024)
引言概述:正文内容:一、材料特性分析1.材料力学性质测试:介绍材料力学性质测试的方法和流程,包括拉伸、压缩、弯曲等力学性能的测试。
2.材料疲劳寿命预测:介绍疲劳寿命预测的方法和模型,包括SN曲线、疲劳损伤积累等参数的计算和分析。
3.材料失效模式分析:讨论材料在极限负荷下的失效模式,包括拉伸失效、疲劳失效和断裂失效等。
4.材料可靠性评估:介绍材料可靠性评估的方法和指标,包括可靠性指数、可靠度和安全系数的计算和分析。
5.材料工程应用案例:通过实际工程案例,展示CAE分析在材料特性分析中的应用和效果。
二、结构优化设计1.结构初始设计:介绍结构的初始设计流程和方法,包括草图设计、选择材料和确定约束条件等。
2.结构分析模型构建:讨论结构分析模型的建立方法,包括网格划分、节点连接和加载条件的定义。
3.结构优化算法:介绍结构优化算法的原理和分类,包括形状优化、拓扑优化和参数优化等方法。
4.结构优化效果评估:针对不同的优化目标,介绍效果评估指标的选取和考虑因素的分析。
5.结构优化设计案例:通过实际工程案例,展示CAE分析在结构优化设计中的应用和效果。
三、热仿真分析1.热传导分析:介绍热传导分析的原理和计算方法,包括热传导方程和传热边界条件的建立。
2.热应力分析:讨论热应力分析的方法和模型,包括线性热弹性模型和非线性热弹性模型。
3.温度场分布分析:展示CAE分析在温度场分布分析中的应用,包括温度梯度和温度均匀性等指标的计算和评价。
4.热仿真优化设计:介绍热仿真优化设计的原理和流程,包括热网格优化和热传导路径优化等方法。
5.热仿真分析案例:通过实际工程案例,展示CAE分析在热仿真分析中的应用和效果。
四、流体力学分析1.流体流动模拟:介绍流体流动模拟的原理和方法,包括NavierStokes方程和控制方程的求解。
2.流场数值计算:讨论流场数值计算的过程和方法,包括网格划分、边界条件设置和求解器选择等。
3.流场压力分析:分析流体流动中的压力场分布和压力梯度的计算和分析。
成型CAE实验报告完整版
成型CAE实验报告完整版引言实验目的1.使用CAE软件进行实际产品的成型仿真分析;2.评估成型过程中的变形、应力分布等工艺参数;3.提供数据支持,为产品工艺设计提供参考。
实验原理成型仿真分析主要借助CAE软件,通过建立产品的几何模型、材料属性及边界条件等,对成型过程中的变形、应力分布进行仿真预测。
常见的CAE软件有ANSYS、ABAQUS、LS-DYNA等。
实验内容本实验选择一种实际产品进行成型仿真分析,以下是具体步骤:1.准备工作:收集实际产品的设计图纸、材料参数等;2.建立几何模型:使用CAE软件导入设计图纸,建立三维几何模型;3.材料属性:根据实际产品的材料参数设置材料属性;4.网格划分:对几何模型进行网格划分,生成有限元网格;5.设置边界条件:根据实际情况设置边界条件,如加热温度、压力等;6.进行仿真分析:运行仿真计算,获取成型过程中的变形、应力分布等数据;7.结果分析:对仿真结果进行分析,评估成型过程中的工艺参数。
实验结果根据仿真分析,我们可以得到成型过程中的变形、应力分布等工艺参数。
这些数据可以为产品工艺设计提供参考,例如优化几何形状、调整材料参数等,以提高产品的成型质量和工艺效率。
结论通过本实验的成型CAE仿真分析,我们可以全面了解实际产品在成型过程中的工艺参数,为产品工艺设计提供参考。
这种基于计算机辅助的工程方法能够有效提高产品设计的准确性和工艺的优化程度,为实际工程提供有力的支持。
[1]张三,李四.CAE在零件成型工艺设计中的应用研究[J].机械工程学报。
[3]孙五,王六.成型CAE分析方法研究综述[J].计算机辅助工程。
cae分析报告
CAE分析报告1. 引言CAE(Computer-Aided Engineering,计算机辅助工程)是一种利用计算机仿真和数值计算方法对工程问题进行分析和求解的技术。
本文将针对CAE分析进行详细介绍和步骤解析。
2. CAE分析的步骤CAE分析通常包括以下步骤:2.1. 问题定义在进行CAE分析之前,首先需要明确分析的问题是什么。
例如,可以是构件的强度分析、传热分析、流体力学分析等。
问题定义的准确性和明确性对后续分析的有效性至关重要。
2.2. 几何建模几何建模是CAE分析的基础,它用于将实际工程问题转化为计算机可处理的几何形状。
常用的几何建模软件包括CATIA、SolidWorks等。
在几何建模过程中,需要考虑几何形状的精度和模型的尺寸。
2.3. 网格划分网格划分是将几何模型划分为小的离散单元,以便进行数值计算。
不同的分析问题需要不同类型的网格划分,例如结构分析通常使用四面体网格,流体分析常使用三角网格。
网格划分的质量会直接影响分析结果的准确性。
2.4. 材料属性定义材料的物理属性是进行CAE分析的重要输入参数。
通常,需要定义材料的弹性模量、屈服强度、热导率等属性。
这些属性可以通过实验测试获得,也可以通过材料数据库进行查找。
2.5. 边界条件设置边界条件是指系统在分析过程中与外界交互的条件。
它包括施加在系统上的力、约束条件等。
边界条件的设置需要根据实际工程问题进行合理选择,以保证分析结果的可靠性。
2.6. 求解模型求解模型是指利用数值方法对系统进行求解,得到系统的响应结果。
常用的数值方法包括有限元法、有限差分法等。
求解模型的准确性和稳定性对分析结果的可信度具有重要影响。
2.7. 结果分析与评估在完成求解后,需要对分析结果进行分析和评估。
这包括对应力、应变、温度等物理量的分析,以及对系统性能和安全性的评估。
分析报告应清晰地呈现分析结果,并提供有效的解决方案。
3. CAE分析的应用领域CAE分析在工程领域有着广泛的应用。
- 1、下载文档前请自行甄别文档内容的完整性,平台不提供额外的编辑、内容补充、找答案等附加服务。
- 2、"仅部分预览"的文档,不可在线预览部分如存在完整性等问题,可反馈申请退款(可完整预览的文档不适用该条件!)。
- 3、如文档侵犯您的权益,请联系客服反馈,我们会尽快为您处理(人工客服工作时间:9:00-18:30)。
目录
1 说明 (1)
2 分析过程 (1)
2.1 分析类型 (1)
2.2 分析流程 (1)
2.3 模型说明 (2)
2.3.1 几何信息 (2)
2.3.2 单元类型 (2)
2.3.3 材料属性 (2)
2.3.4 网格划分 (3)
2.3.5 连接设置 (3)
2.3.6 载荷及约束设置 (4)
2.3.7 计算设置 (4)
2.4 分析结果 (4)
2.4.1 40g过载 (4)
2.4.2 8000g过载 (6)
3 改进意见 (8)
4 硬件最低要求 (8)
1 说明
依照客户委托,对客户提供模型进行响应谱分析。
2 分析过程
2.1 分析类型
基于ansys13.0的响应谱分析。
2.2 分析流程
分析流程如下图所示:
图1 分析流程
2.3 模型说明
2.3.1 几何信息
原始几何模型由客户提供。
几何清理便于更好的分析问题,去除细小特征,例如小孔等。
单位制:毫米,如图2。
2.3.2 单元类型
分析对象为实体模型采用SOLID92单元。
SOLID92单元精度高,适应性好,能够满足分析需求。
图2 原始几何模型
2.3.3 材料属性
除图2中绿色部分外,其余都按铝合金计算,LY12。
绿色部分为PCB板。
依据机械设计手册Ver.2012和网上资料,LY12和PCB板的属性分别取如下数据:
●LY12的机械性能
➢抗拉强度:σb (MPa) ) ≥425
➢屈服强度:σ0.2 (MPa) )≥275
➢密度:2.78g/cm3
➢弹性模量:73000MPa
●PCB板的机械性能
➢密度:2g/cm3
➢弹性模量:50400 MPa
➢泊松比:0.231
2.3.4 网格划分
基于hypermesh11.0处理,单元尺寸3mm,该尺寸能较好的表现模型特征。
由于模型局部特征较多,故采用四面体单元划分。
网格最终效果如图3
图3 网格模型
2.3.5 连接设置
本分析类型为动力学,故零件间连接方式采用线性BONDED处理,位置由客户图纸提供。
连接示例模型如图4所示
图4 连接示例图
2.3.6 载荷及约束设置
约束采用固定约束,位置由客户图纸确定
载荷谱由客户提供,见表1
正交坐标系3个方向。
2.3.7 计算设置
依照客户要求,输出6种工况文件(加速度40g,8000g各三个方向),基于ansys13.0动力学求解器计算。
2.4 分析结果
2.4.1 40g过载
首先以40g,X方向模型响应为例,观察PCB板应力分布图(图5),整体应力分布图(图6),X、Y、Z方向变形图(图7,8,9)。
图5 PCB板应力分布图
图6整体应力分布图
图7 X方向变形图
图8 Y方向变形图
图9 Z方向变形图
在此工况下,最大应力值远远小于屈服强度,变形量也较小,设备结构安全稳定,符合要求。
同理40g,Y、40g,Z工况。
2.4.2 8000g过载
其次以8000g,X方向模型响应为例,观察PCB板应力分布图(图10),整体应力分布图(图11),X、Y、Z方向变形图(图12,13,14)。
图10 PCB板应力分布图
图11整体应力分布图
图12 X方向变形图
图13 Y方向变形图
图14 Z方向变形图
在此工况下,最大应力值大大高于抗拉强度,但变形量较小,说明设备存在应力集中;同时观察PCB板应力分布可知,连接部位应力集中,产生结构性破坏,设备结构不符合要求。
同理8000g,Y、8000g,Z工况。
注意:以上分析基于本文确定的网格划分尺度、方法和边界条件,结果可能会因采用计算参数设置不同而有所差异。
若追求精度更高的计算结果,需进一步细化网格,改善网格质量,细化边界条件等。
3 改进意见
1.在整体应力集中区域采用平滑过渡,减少应力集中。
2.PCB板连接区域改善连接方式,降低局部应力。
4 硬件最低要求
●模型处理:
➢操作系统:WINDOW7
➢内存:8G,
➢独立显卡:1G
➢CPU:Intel四核心,核心频率2GHz
●仿真计算
➢操作系统:WINDOW7
➢内存:32G
➢独立显卡:1G
➢CPU:intel十六核心,核心频率3GHz。