应力腐蚀断裂
10-应力腐蚀开裂-氢致开裂

四、氢致开裂的机理——氢鼓泡(生成氢分子)
氢鼓泡机理示意图
➢ H2S是弱酸,在酸性溶 液中主要以分子形式存在;
➢ 在金属表面阴极反应生 成大量的氢原子;
➢ 氢原子渗入金属内部, 通过扩散达到缺陷处,析出 氢气产生高压;
➢ 非金属夹杂物(如Ⅱ型 MnS)为裂纹的主要形核位 置。
34
抑制氢鼓泡的措施
机械原因:材料受力变形时造成钝化 膜破坏。
17
2、溶解(裂纹扩展)
➢ 裂纹扩展的可能途径:预先存在活性通道和应变产生的 活性通道。 ➢ 活性通道理论(拉伸应力较小时)
大的应力作用在裂缝尖端应力集中,使表面膜破裂。 合金中预先存在一条对腐蚀敏感的通道,在特定介质条 件下成为活性阳极。 形成活性通道可能性有:合金成分结构差异;晶界或亚 晶界;局部应力集中及应变引起阳极晶界区;应变引起表面 膜局部破裂;塑性变形引起的阳极区等。
氢原子
d
氢分子
a
c b
表面铁原子
e
h
+
++
++ h’
f
渗碳体或
g
固溶体碳原子
g’
内部铁原子
钢的氢腐蚀机理模型示意图
31
铁素体晶体结构和显微组织 含碳少
奥氏体晶体结构和显微组织 含碳多
抑制氢腐蚀的措施
➢ 温度:各种钢发生氢腐蚀的起始温度为200oC以上。 ➢ 氢分压:氢分压低时,发生表面脱碳难以鼓泡或开裂。 ➢ 介质气体:含氧或水蒸气时,降低氢进入钢中的速度; 含H2S时,孕育期变短。 ➢ 合金元素:碳含量增加,孕育期变短;加入形成碳化物 金属(Ti、Nb、Mo、W、Cr),减少甲烷生成;MnS为裂 纹源的引发处,应去除。 ➢ 热处理和冷加工。
1-5应力腐蚀开裂
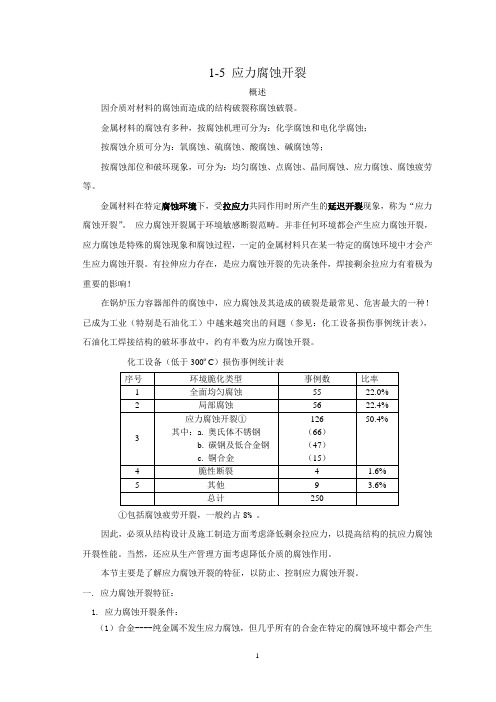
1-5 应力腐蚀开裂概述因介质对材料的腐蚀而造成的结构破裂称腐蚀破裂。
金属材料的腐蚀有多种,按腐蚀机理可分为:化学腐蚀和电化学腐蚀;按腐蚀介质可分为:氧腐蚀、硫腐蚀、酸腐蚀、碱腐蚀等;按腐蚀部位和破坏现象,可分为:均匀腐蚀、点腐蚀、晶间腐蚀、应力腐蚀、腐蚀疲劳等。
金属材料在特定腐蚀环境下,受拉应力共同作用时所产生的延迟开裂现象,称为“应力腐蚀开裂”。
应力腐蚀开裂属于环境敏感断裂范畴。
并非任何环境都会产生应力腐蚀开裂,应力腐蚀是特殊的腐蚀现象和腐蚀过程,一定的金属材料只在某一特定的腐蚀环境中才会产生应力腐蚀开裂。
有拉伸应力存在,是应力腐蚀开裂的先决条件,焊接剩余拉应力有着极为重要的影响!在锅炉压力容器部件的腐蚀中,应力腐蚀及其造成的破裂是最常见、危害最大的一种!已成为工业(特别是石油化工)中越来越突出的问题(参见:化工设备损伤事例统计表),石油化工焊接结构的破坏事故中,约有半数为应力腐蚀开裂。
化工设备(低于300ºC)损伤事例统计表①包括腐蚀疲劳开裂,一般约占8% 。
因此,必须从结构设计及施工制造方面考虑洚低剩余拉应力,以提高结构的抗应力腐蚀开裂性能。
当然,还应从生产管理方面考虑降低介质的腐蚀作用。
本节主要是了解应力腐蚀开裂的特征,以防止、控制应力腐蚀开裂。
一. 应力腐蚀开裂特征:1. 应力腐蚀开裂条件:(1)合金----纯金属不发生应力腐蚀,但几乎所有的合金在特定的腐蚀环境中都会产生应力腐蚀裂纹。
极少量的合金或杂质都会使材料产生应力腐蚀。
各种工程实用材料几乎都有应力腐蚀敏感性。
(2)拉应力-----引起应力腐蚀的应力必须是拉应力,且应力可大可小,极低的应力水平也可能导致应力腐蚀破坏(不管拉应力多么小,只要能引起变形滑移,即可促使产生应力腐蚀开裂)。
应力既可由载荷引起,也可是焊接、装配或热处理引起的残余应力。
(3)腐蚀性介质----产生应力腐蚀的材料和腐蚀性介质之间有选择性和匹配关系,即当二者是某种特定组合时才会发生应力腐蚀。
金属的应力腐蚀断裂与腐蚀疲劳断裂
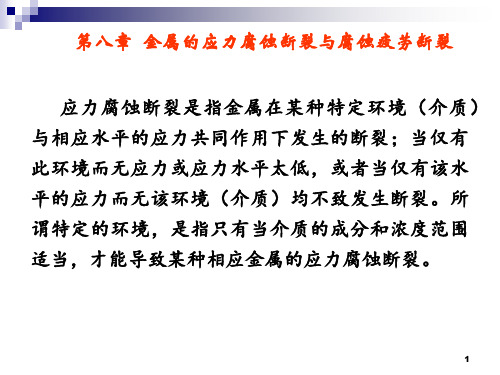
( 3 )裂纹截面金相分析可见,氢脆裂纹为单支; 应力腐蚀和腐蚀疲劳裂纹则多有分支。其分枝程度 与应力比R、载荷水平和频率有关。
( 4 )区分应力腐蚀和腐蚀疲劳的依据有二:一是 调查和计算分析应力性质;二是断口上是否有疲劳 辉纹。但须注意,断口上有辉纹的面积份额可能很 小,并且辉纹可能短而少,尤其是低周的条件下, 故往往不易发现。
30
三、断口微观特征 (1)若腐蚀产物不是很厚或被清 洗掉后,在适当的(例如数百倍 )倍率下,沿晶断口的形貌是颗 粒状的,如图8-19和图8-20, 可以看到沿晶的二次裂纹。
31
( 2 )穿晶型的应力腐蚀断口有羽毛状花样或明显的 类似解理形貌, ( 3 )在腐蚀产物很厚的情况下,断口形貌可能被掩 盖。
钛合金在甲醇蒸气中比浸在甲醇液体中更易发生应
力腐蚀。且当试样在无应力状态下置于甲醇蒸气或
液体中一段时间再在空气中拉断,也表现出同SCC
相似的穿晶脆断。经时效处理可以消除这种脆性。
据认为钛和钛合金的SCC直接与钛的氢化物有关。
消除构件中的残余应力,在溶液中添加缓蚀剂以及 进行阴极保护是防止钛和钛合金发生应力腐蚀的可 行办法。
能发生应力腐蚀,其敏感温度为15~30℃,<10℃及
>40℃刚敏感性大降。微量的氧,大大促进该SCC,故
在装液氨前必须排净空气而充。微量水(达0.2%以上) 可防止该种SCC。
13
碳钢还可能在其它许多酸环境中,在中、在
高压的水溶液中、在HCN的含水气体中发生应力
腐蚀断裂。碳钢的应力腐蚀大多是沿晶的。少数
镀锌与镀锡:对于镀锌铁,镀锌层破损处的腐蚀轻微,
这是由于Zn作为阳极并发生钝化;对于镀锡铁,镀锡
层破损处的腐蚀严重,这是由于Sn作为阴极,Fe作阳 极而钝化膜不致密、不稳定所致。 (2)浓差电池 一般氧浓度低的区域为阳极。
应力腐蚀形成条件、危害性及裂纹特征
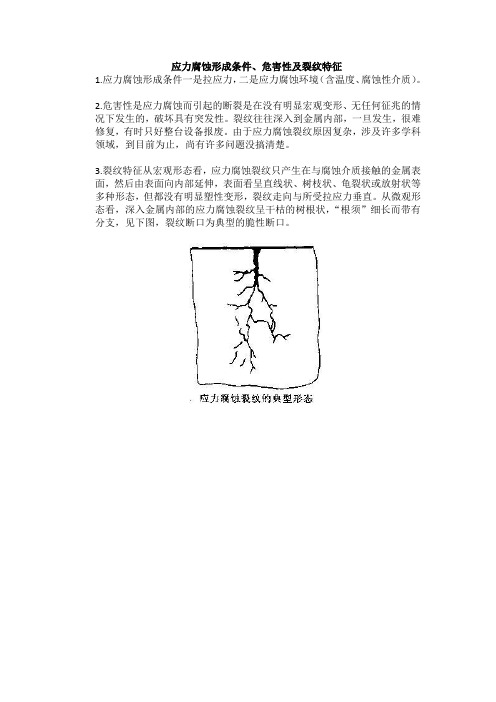
应力腐蚀形成条件、危害性及裂纹特征
1.应力腐蚀形成条件一是拉应力,二是应力腐蚀环境(含温度、腐蚀性介质)。
2.危害性是应力腐蚀而引起的断裂是在没有明显宏观变形、无任何征兆的情
况下发生的,破坏具有突发性。
裂纹往往深入到金属内部,一旦发生,很难修复,有时只好整台设备报废。
由于应力腐蚀裂纹原因复杂,涉及许多学科领域,到目前为止,尚有许多问题没搞清楚。
3.裂纹特征从宏观形态看,应力腐蚀裂纹只产生在与腐蚀介质接触的金属表
面,然后由表面向内部延伸,表面看呈直线状、树枝状、龟裂状或放射状等多种形态,但都没有明显塑性变形,裂纹走向与所受拉应力垂直。
从微观形态看,深入金属内部的应力腐蚀裂纹呈干枯的树根状,“根须”细长而带有分支,见下图,裂纹断口为典型的脆性断口。
应力腐蚀断裂
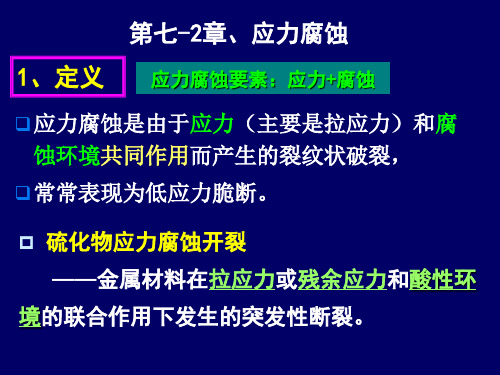
裂纹扩展速率(da/dt)与K1的关系——三阶段:
lg da dt
Ⅰ
Ⅱ
Ⅲ
K1SCC
K1C K1
图2 裂纹扩展速率(da/dt)与K1的关系
试验原理
疲劳裂纹扩展速率da/dN表达式
② 当整体金属仍是弹性 变形状态时,裂纹尖 端的前沿为塑性区。
③ 裂纹尖端前具有三向 拉伸应力区,氢可在 此处富集。
裂纹尖端易于继续阳 极溶解,裂纹壁上阴 极反应析出的氢易于 进入金属。
位错与氢结合;运动 的位错快速输送氢。
指出富集部位,三向 拉伸区较疏松,富集 氢可降低应变能。
硫化物应力(SSC)腐蚀
K1
=
P
C3
(a W
B a
)
3)硫化氢环境门限应力强度因子KISCC的测定
材料在硫化氢环境下的 抗断裂特性
实验方法 用螺栓对试样加载P0 ,
用引伸计测量加载过程 中试样裂纹开口位移, 记录中止时位移量V0
试件放入H2S溶液中,经过一定 时间,试件裂纹扩展 ,螺栓力
松弛,载荷下降, 则KI下降,
三向受拉处,物质最稀松,有空穴产生,氢集中 在空穴中。
焊接时,氢离子结合呈氢原子或氢分子,形 成107的大气压。高的压力使钢材表面出现 氢鼓包,内部产生裂纹。
要求焊接时焊条要烘干,不得受潮。
3.硫化物应力腐蚀性能试验方法
美国腐蚀工程协会NACE TM0177—2005规定了四种标准 方法:
W - a 2.5( Ke )2 0.2
K1SCC/s>0.3,视为合格
应力腐蚀

应力腐蚀(一)应力腐蚀现象金属在拉应力和特定的化学介质共同作用下,经过一段时间后所产生的低应力脆断现象,称为应力腐蚀断裂。
应力腐蚀断裂并不是金属在应力作用下的机械性破坏与在化学介质作用下的腐蚀性破坏的迭加所造成的,而是在应力和化学介质的联合作用下,按持有机理产生的断裂。
其断裂抗力比单个因素分别作用后再迭加起来的要低很多。
由拉伸应力和腐蚀介质联合作用而引起的低应力脆性断裂称为应力腐蚀(常用英文的三个字头SCC表示)。
不论是韧性材料还是脆性材料都可能产生应力腐蚀断裂。
应力腐蚀断裂一般都是在特定的条件下产生的:1.只有在拉伸应力作用下才能引起应力腐蚀开裂(近来有研究说压应力下也可能产生)。
这种拉应力可以是外加载荷造成的应力;也可以是各种残余应力,如焊接残余应力,热处理残余应力和装配应力等。
一般情况下,产生应力腐蚀时的拉应力都很低,如果没有腐蚀介质的联合作用,机件可以在该应力下长期工作而不产生断裂。
2.产生应力腐蚀的环境总是存在特定腐蚀介质,这种腐蚀介质一般都很弱,如果没有拉应力的同时作用,材料在这种介质中腐蚀速度很慢。
产生应力腐蚀的介质一般都是特定的,也就是说,每种材料只对某些介质敏感,而这种介质对其它材料可能没有明显作用,如黄铜在氨气氛中,不锈钢在具有氯离子的腐蚀介质中容易发生应力腐蚀,但反应过来不锈钢对氨气,黄铜对氯离子就不敏感。
3.一般只有合金才产生应力腐蚀,纯金属不会产生这种现象.合金也只有在拉伸应力与特定腐蚀介质联合作用下才会产生应力腐蚀断裂。
常见合金的应力腐蚀介质:碳钢:荷性钠溶液,氯溶液,硝酸盐水溶液,H2S水溶液,海水,海洋大气与工业大气奥氏体不锈钢:氯化物水溶液,海水,海洋大气,高温水,潮湿空气(湿度90%),热NaCl,H2S水溶液,严重污染的工业大气(所以不锈钢水压试验时氯离子的含量有很严格的要求)。
马氏体不锈钢:氯化的,海水,工业大气,酸性硫化物航空用高强度钢:海洋大气,氯化物,硫酸,硝酸,磷酸铜合金:水蒸汽,湿H2S,氨溶液铝合金:湿空气,NaCl水溶液,海水,工业大气,海洋大气(二)应力腐蚀断口特征与疲劳相似,应力腐蚀断裂也是通过裂纹形成和扩展这两个过程来进行的,一般认为裂纹形成约占全部时间的90%左右,而裂纹扩展仅占10%左右。
不锈钢的应力腐蚀破裂及其防护
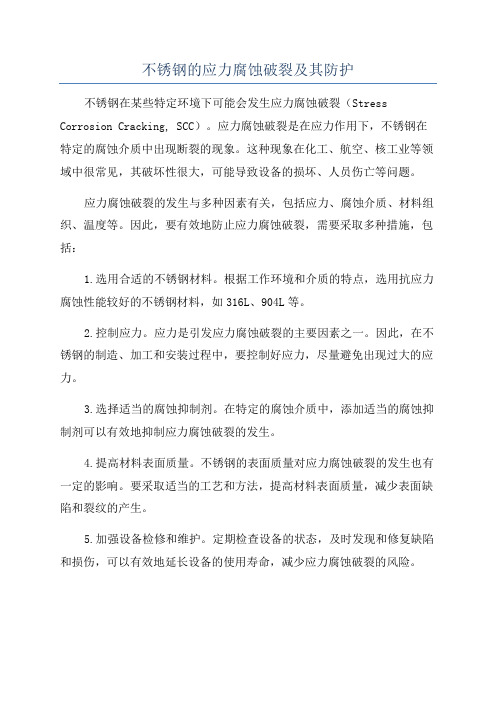
不锈钢的应力腐蚀破裂及其防护
不锈钢在某些特定环境下可能会发生应力腐蚀破裂(Stress Corrosion Cracking, SCC)。
应力腐蚀破裂是在应力作用下,不锈钢在特定的腐蚀介质中出现断裂的现象。
这种现象在化工、航空、核工业等领域中很常见,其破坏性很大,可能导致设备的损坏、人员伤亡等问题。
应力腐蚀破裂的发生与多种因素有关,包括应力、腐蚀介质、材料组织、温度等。
因此,要有效地防止应力腐蚀破裂,需要采取多种措施,包括:
1.选用合适的不锈钢材料。
根据工作环境和介质的特点,选用抗应力腐蚀性能较好的不锈钢材料,如316L、904L等。
2.控制应力。
应力是引发应力腐蚀破裂的主要因素之一。
因此,在不锈钢的制造、加工和安装过程中,要控制好应力,尽量避免出现过大的应力。
3.选择适当的腐蚀抑制剂。
在特定的腐蚀介质中,添加适当的腐蚀抑制剂可以有效地抑制应力腐蚀破裂的发生。
4.提高材料表面质量。
不锈钢的表面质量对应力腐蚀破裂的发生也有一定的影响。
要采取适当的工艺和方法,提高材料表面质量,减少表面缺陷和裂纹的产生。
5.加强设备检修和维护。
定期检查设备的状态,及时发现和修复缺陷和损伤,可以有效地延长设备的使用寿命,减少应力腐蚀破裂的风险。
综上所述,要防止不锈钢应力腐蚀破裂的发生,需要从多个方面入手,综合考虑控制应力、选择合适的材料、添加腐蚀抑制剂、提高表面质量和
加强设备维护等措施。
金属的应力腐蚀断裂与腐蚀疲劳断裂
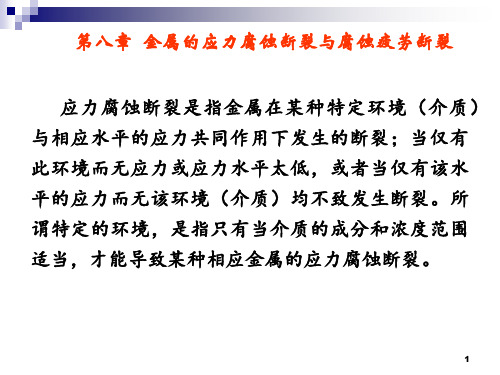
裂。其中许多问题至今还没得到深入的研究,甚
至有的还是很不了解。表8-2是一些金属和合金
的部分应力腐蚀环境。
11
一、碳钢的应力腐蚀 早年的铆接蒸汽锅炉,为减缓铁的腐蚀在水中加
入NaOH调制pH值。结果在铆缝中发生NaOH浓缩(渗
漏、蒸发所致)导致应力腐蚀而引起过爆炸,当时
叫做碱脆。能导致碳钢碱脆的介质还包括KOH、
27
二、断裂的途径
( 1 )根据金属和合金的种类及介质不同, SCC 可以
是沿晶的或穿晶的,碳钢和铬不锈钢多系沿晶的;
奥氏体不锈钢则多为穿晶的;铝,钛、镍也多为沿
晶的。一般说来,发生平面滑移的材料倾向于穿晶
断裂;易发生交滑移的材料更倾向于沿晶断裂。
(2)裂纹扩展的宏观方向与应力有关,大体垂直于
主应力。
几何特征区分为全面腐蚀、局部腐蚀和集中腐蚀
。
3
就腐蚀的理化机制分类而论,物理腐蚀主要指金
属在介质中被溶解,例如Cu被Zn熔体腐蚀,铁被铜
熔体溶解,铜被钎料溶解……等。这里,腐蚀的一
级(直接)产物主要是溶液而不是化合物。化学腐
蚀和电化腐蚀的直接生成物都是化合物。
4
二、电化腐蚀原理(腐蚀电池)
当两块不同金属置于同一电解液中,例如 Cu和 Zn 同 插入 Cu2SO4溶液中,由于Zn和 Cu的电极电位不同,就 构成了一个电池。此时若接通电池的外电路,就有电 流通过。 这时: Zn→Zn2++2e↓(传导)
15
高铬的铁素体不锈钢的应力腐蚀敏感性较奥 氏体钢低得多。过去由于一般方法冶炼的铁素体 不锈钢表现出强烈的低温脆性,故在有氯脆的化
工设备中不能代替奥氏体钢。近十多年来,真空
法生产出低杂质(主要是O、C、N)的高铬钢,克
- 1、下载文档前请自行甄别文档内容的完整性,平台不提供额外的编辑、内容补充、找答案等附加服务。
- 2、"仅部分预览"的文档,不可在线预览部分如存在完整性等问题,可反馈申请退款(可完整预览的文档不适用该条件!)。
- 3、如文档侵犯您的权益,请联系客服反馈,我们会尽快为您处理(人工客服工作时间:9:00-18:30)。
应力腐蚀断裂一.概述应力腐蚀 是材料、或在静 (主要是拉应力 )和腐蚀的共同作用下产生的失效现 象。
它常出现于用钢、黄铜、高强度铝合金和中,凝汽器管、矿山用钢索、飞机紧 急刹车用高压气瓶内壁等所产生的应力腐蚀也很显着。
常见应力腐蚀的机理是:零件或构件在应力和腐蚀介质作用下,表面的氧化膜 被腐蚀而受到破坏 , 破坏的表面和未破坏的表面分别形成阳极和阴极 , 阳极处的金属 成为离子而被溶解,产生电流流向阴极。
由于阳极面积比阴极的小得多,阳极的电 流密度很大,进一步腐蚀已破坏的表面。
加上拉应力的作用,破坏处逐渐形成裂纹, 裂纹随时间逐渐扩展直到断裂。
这种裂纹不仅可以沿着金属晶粒边界发展,而且还 能穿过晶粒发展。
应力腐蚀过程试验研究表明:当金属加上阳极电流时可以加剧应 力腐蚀, 不大。
应力腐蚀的机理仍处于进一步研究中。
为防止零件的应力腐蚀,首先应合避免使用对应力腐蚀敏感的材料 , 可以采用抗应力腐蚀开裂的不锈钢系列 工作状态下构件所承受的外加载荷形成的抗应力。
加工,制造,热处理引起的内应力。
装配,安装形成的内应力。
温差引起的热应力。
裂纹内因腐蚀产物的体积效应造成的楔入作用也能产生裂纹扩展所需要 的应力。
(2)每种合金的应力腐蚀开裂只对某些特殊介质敏感。
一般认为纯金属不易发生应力腐蚀开裂,合金比纯金属更易发生应力腐蚀开裂。
下表列出了各种合金风应力腐蚀开裂的环境介质体系,介质有特点:即金属或合金 可形成纯化膜,弹介质中有有破坏纯化膜完整性的离子存在。
而且介质中的有害物 质浓度往往很低,如大气中微量的 H 2S 和NH 可分别引起钢和铜合金的应力腐蚀开裂。
空气中少量NH 是鼻子嗅不到而加上阴极电流时则能停止应力腐蚀。
一般认为压应力对应力腐蚀的影响理选材,如高镍奥氏体钢、高纯奥氏体钢、超纯高铬铁素体钢等。
其次应合理设计零件和构 件,减少。
改善腐蚀环境,如在腐蚀介质中添加缓蚀剂,也是防止应力腐蚀的措施。
采用金属或非金属保护层,可以隔绝腐蚀介质的作用。
此外,采用阴极保护法见也 可减小或停止应力腐蚀。
本篇文章将重点介绍应力腐蚀断裂失效机理与案例研究, 并分析比较应力腐蚀断裂其他环境作用条件下发生失效的特征。
,由于应力腐蚀的 测试方法与本文中重点分析之处结合联系不大,故不再本文中加以介绍。
二.应力腐蚀开裂特征(1)引起应力腐蚀开裂的往往是拉应力。
这种拉应力的来源可以是:1.2.3. 4.的,却能引起黄铜的氨脆。
再如奥氏体不锈钢在含有几个ppm氯离子的高纯水中就会出现应力腐蚀开裂。
再如低碳钢在硝酸盐溶液中的“硝脆”,碳钢在强碱溶液中的“碱脆”都是给定材料和特定环境介质结合后发生的破坏。
氯离子能引起不锈钢的应力腐蚀开裂,而硝酸根离子对不锈钢不起作用,反之,硝酸根离子能引起低碳钢的应力腐蚀开裂,而氯离子对低碳钢不起作用。
表1.常见材料应力腐蚀开裂发生的介质(3)应力腐蚀开裂是材料在应力和环境介质共同作用下经过一段时间后,萌生裂纹,裂纹扩展到临界尺寸,此时由于裂纹尖端的应力强度因子K达到材料的断裂韧性K c,发生失稳断裂。
即应力腐蚀开裂过程分为三个阶段:裂纹萌生,裂纹扩展,失稳断裂。
1.裂纹的萌生裂纹源多在保护膜破裂处,而膜的破裂可能与金属受力时应力集中与应变集中有关,此外,金属中存在孔蚀,缝隙腐蚀,晶间腐蚀也往往是SCC裂纹萌生处。
萌生期长短,少则几天,长达几年,几十年,主要取决于环境特征与应力大小。
2.裂纹扩展应力腐蚀开裂的裂纹扩展过程有三种方式。
应力腐蚀开裂裂纹的扩展速率da/dt与裂纹尖端的应力强度因子K的关系具有图示的三个阶段特征。
在第一阶段da/dt随K i降低而急剧减少。
当K降到K scc以下时应力腐蚀开裂裂纹不再扩展。
在第二阶段,裂纹扩展与应力强度因子K大小无关,主要受介质控制。
在这阶段裂纹出现宏观和微观分枝。
但在宏观上,裂纹走向与抗应力方向是垂直的。
第三阶段为失稳断裂,纯粹由力学因素K I 控制,da/dt 随K I 增大迅速增加直至断裂。
(3)应力腐蚀开裂属于脆性断裂。
即使塑性很高的材料也是如此。
其断口呈多种形貌。
有沿晶断裂,准解理,韧性断裂等。
图1. 应力腐蚀开裂da/dt 与K I 关系三. 应力腐蚀开裂机制应力腐蚀开裂现象很多,目前尚未有统一的见解,不同学派的观点可能从电化学,断裂力学,物理冶金进行研究而强调了它们的作用。
(1 )电化学理论1,活性通道理论该理论认为,在金属或合金中有一条易于腐蚀的基本上是连续的通道,沿着这条活性通道优先发生阳极溶解。
活性通道可以是晶界,亚晶界或由于塑性变形引起的阳极区等。
电化学腐蚀就沿着这条通道进行,形成很窄的裂缝裂纹,而外加应力使裂纹尖端发生应力集中,引起表面膜破裂,裸露的金属成为新的阳极,而裂纹两侧仍有保护膜为阴极,电解质靠毛细管作用渗入到裂纹尖端,使其在高电流密度下加速裂尖阳极溶解。
该理论强调了在拉应力作用下保护膜的破裂与电化学活化溶解的联合作用。
2.快速溶解理论。
该理论认为活性通道可能预先是不存在的,而是合金表面的点蚀坑,沟等缺陷,由于应力集中形成裂纹,裂纹一旦形成,其尖端的应力集中很大,足以使其尖端发生塑性变形到一个塑性,该塑性具有很大的溶解速度。
这种理论适用于自纯化金属,由于裂纹两侧纯化膜存在,更显示裂纹尖端的快速溶解,随着裂纹向前发展,裂纹两侧的金属重新发生纯化(再纯化),只有当裂纹中纯化膜的破裂和再纯化过程处于某种同步条件下才能使裂纹向前发展,如果纯化太快就不会产生裂纹进一步腐蚀,若再纯化太慢,裂纹尖端将变圆,形成活性较低的蚀孔。
图2. 快速溶解理论机理图3.膜破裂理论该理论认为金属表面有一层保护膜(吸附膜,氧化膜,腐蚀产物膜),在应力作用下,被露头的滑移台阶撕破,使表面膜发生破裂(图 3 (b))局部暴露出活性裸金属,发生阳极溶解,形成裂纹(图3(C))。
同时外部保护膜得到修补,对于自纯化金属裂纹两侧金属发生再纯化,这种再纯化一方面使裂纹扩展减慢,一方面阻止裂纹向横向发展,只有在应力作用下才能向前发展。
4.闭塞电池理论该理论是在活性通道理论的基础上发展起来的。
腐蚀就先沿着这些活性通道进行,应力的作用在于将裂纹拉开,以免被腐蚀产物堵塞,但是闭塞电池理论认为,由于裂纹内出现闭塞电池而使腐蚀加速(这类似于缝隙腐蚀)即在裂纹内由于裂纹内金属想要发生水解:FeCl2+2HO2Fe(OH)2+2HCI,使Ph值下降,甚至可能产生氢,外部氢扩散到金属内部引起脆化。
闭塞电池作用是一个随催化腐蚀过程,在拉应力作用下使裂纹不断扩展直至断裂。
(2)吸氢变脆理论。
该理论是从一些塑性很好的合金在发生应力腐蚀开裂时具有脆性断裂的特征提出的(变脆是否由氢脆引起)该理论认为裂纹的形成与发展主要与裂纹尖端氢被引入晶格有关,如奥氏体不锈钢在裂纹尖端,Cr阳极氧化生成CrO3使其酸度增大。
2Cr+3H28Cr2O3+6H++6e当裂纹尖端的电位比氢的平衡电位负时,氢离子有可能在裂纹尖端被还原,变成吸附的氢原子,向金属内部扩展,从而形成氢脆。
(3)应力吸附破裂理论。
该理论认为由于环境中某些破坏性组分对金属表面内表面的吸附,削弱了金属原子间的结合力,在抗拉力作用下引起破裂。
四.影响应力腐蚀开裂的因素影响应力腐蚀开裂的因素可以大致分为环境因素、应力因素以及冶金因素,现整理为图4 框图所示。
图4. 影响应力腐蚀的因素五、应力腐蚀的防护措施从应力腐蚀的机理来看,从材料与环境介质、力学因素三方面因素考虑防护措施。
从防护的方法来分防止应力腐蚀应从减少腐蚀和消除拉应力两方面来采取措施。
1.要尽量避免使用对应力腐蚀敏感的材料;2.在设计设备结构时要力求合理,尽量减少应力集中和积存腐蚀介质;3.是在加工制造设备时,要注意消除残余应力。
六、应力腐蚀断裂的典型案例案例1:CO2 高压热交换器管的破裂材质:0Cr18Ni10尺寸及结构:? 19 X,共232根,每根长米。
管与管板采用胀焊连接。
工作环境:管内:湿CO。
进口温度:180C ;出口温度40〜50 r ;压力:80〜90kgf。
管外:冷却水(含氧6〜10ppm Cl-80〜100ppm进口温度:32〜34 r ;出口温度:80 C;压力:4 kgf。
损坏情况:运转2 月后发现泄漏,运转3 个月检修时发现70 多根管子破裂。
破裂多发生在高温侧管板缝隙附近。
分析检验:裂纹从管外壁产生,向内壁扩展,属穿晶型应力腐蚀裂纹特征。
断口扫描电镜发现,破裂是典型的脆性解理断裂,是由氯化物应力腐蚀造成的。
图5. 67 管与管板连接及管上应力腐蚀裂纹示意图(a)00Cr18Ni10 尺寸:? 19 x 2 管内-高温 CO 2 ;管外-冷却水 运转不到半年,发生多处破损事故。
裂纹以横裂为主。
裂纹由外壁产生,向内壁扩展,属典型的穿晶型应力腐蚀裂纹。
图 7. 冷却器管外部裂纹特征 案例三:金属材料中氢致开裂断口案例 材质: 33CrNiMoA 工艺情况:850r 保温2h 后炉冷,超声波探伤发现内部有缺陷;图 1:经淬火处理 浸蚀方法: 图 8:未浸蚀;图 9: 50%盐酸水溶液浸蚀;图 10: 4%硝酸酒精溶液浸蚀 组织说明:图8: 20mn 切片压开裂成(纵向)断口,其中有许多圆形、卵形白斑 缺陷。
白点表面呈粗晶状。
图 9:横向截面低倍组织形貌,有许多辐射状短裂纹,它们在纵向即为白点。
图 3: 裂纹处横向金相试样形貌,白点为锯齿状裂纹,裂纹细小、刚挺、穿晶。
白点产生 的原因,一般认为与钢中氢含量较高有关。
由于钢中氢原子脱溶、聚集结合成氢分 子,产生极大压力,在热加工中与热应力、组织应力叠加造成裂纹。
图8. 20mm 切片压开裂成(纵向)断口图 9. 横向截面低倍组织形貌图 10. 4% 硝酸酒精溶液浸蚀组织图材料: 20MnMo工艺情况: 锻造后空冷,冲击试验组织说明: 冲击断口试样,断口上有白点,透射电镜碳二次复型图像,白点区为准 解理断裂,通常称之为氢致解理。
图 11. 冲击断口试样断口组织图材料: 20钢(螺钉)工艺情况: 冷镦成型合镀锌组织说明: 螺钉断口。
螺钉经酸洗后表面电镀锌,在安装时发生断裂。
断口宏 观形貌光滑平坦。
扫描电镜观察具有准解理特征,并有发纹等,属氢脆断裂。
低碳 钢虽对氢脆不像高强度钢那样敏感,但如酸洗后未经除氢处理,也有可能会引起氢 脆。
图 12. 螺钉断口组织图材料: 35钢(螺钉)(c ) 图 6. 管板缝隙处破裂的管子 案例二:化肥厂冷却器管的破损 材质: 工作环境 损坏情况 分析检验 (b)即白点工艺情况: 热锻、调质后镀锌组织说明: 螺钉断口。
螺钉经酸洗后表面电镀锌,在安装时发生断裂。
断口呈脆性特征,微观形貌为准解理断裂,并有发纹等特征,为氢脆断裂。
图 13. 螺钉断口组织图材料: 65Mn工艺情况: 淬火、回火后酸洗、电镀组织说明:由65Mn 钢制作的弹簧片,在安装时发生断裂。