应力腐蚀
应力腐蚀概述
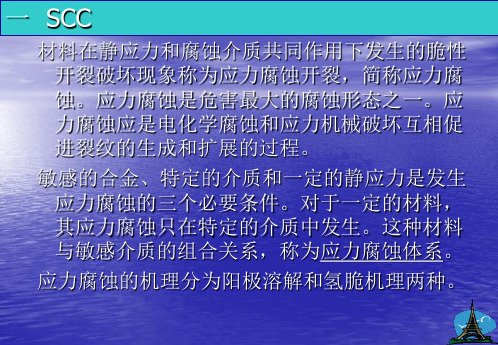
3个阶段Three stages
2 SCC破裂类型
– 裂纹起源 – 介质缓慢攻击产生凹坑 – 慢速裂纹扩展 – 快速断裂
3. 一般过程
Stress corrosion cracking
3. 一般过程
4. 影响因素
1.物理冶金因素 例如,金属材料的冶炼方式、化学成分及其偏析情况 ,组织、晶粒度、晶格缺陷及其分布情况,材料的物理 、化学及机械等方面的性能,材料的热处理状态及表面 状况等等
一 SCC
材料在静应力和腐蚀介质共同作用下发生的脆性 开裂破坏现象称为应力腐蚀开裂,简称应力腐 蚀。应力腐蚀是危害最大的腐蚀形态之一。应 力腐蚀应是电化学腐蚀和应力机械破坏互相促 进裂纹的生成和扩展的过程。 敏感的合金、特定的介质和一定的静应力是发生 应力腐蚀的三个必要条件。对于一定的材料, 其应力腐蚀只在特定的介质中发生。这种材料 与敏感介质的组合关系,称为应力腐蚀体系。 应力腐蚀的机理分为阳极溶解和氢脆机理两种。
Stress corrosion cracking
5. 特点
Stress corrosion cracking
5. 特点
Stress corrosion cracking
5. 特点
低碳钢在硝 酸盐溶液中 的应力腐蚀 破裂是典型 的沿晶破裂 ,呈“冰糖 状”断口
Stress corrosion cracking
4. 影响因素 3. 介质环境因素 金属材料所处的介质的性质、成 分、浓度、pH值、温度等等因素 都对应力腐蚀破裂有很大的影响.
4. 影响因素
4 电极电位的影响 电位对应力腐蚀破裂起决定性作用。应力腐 蚀破裂只发生在一定的电位范围内,这个范围 大约只有几百mv。不同材料在不同介质中发 生应力腐蚀的电位区(敏感电位区)不同。
应力腐蚀概述
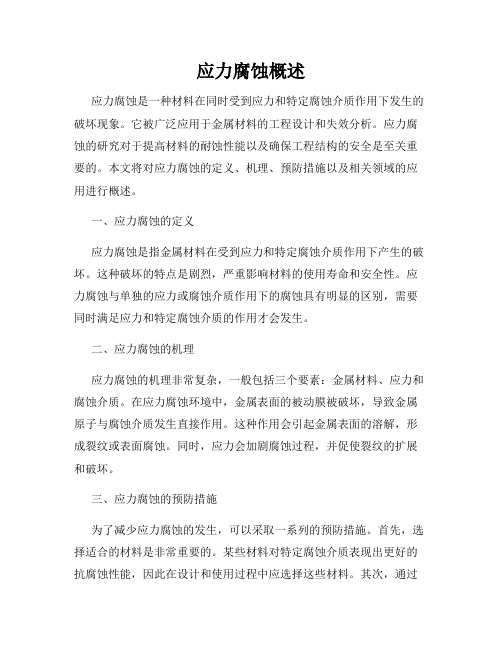
应力腐蚀概述应力腐蚀是一种材料在同时受到应力和特定腐蚀介质作用下发生的破坏现象。
它被广泛应用于金属材料的工程设计和失效分析。
应力腐蚀的研究对于提高材料的耐蚀性能以及确保工程结构的安全是至关重要的。
本文将对应力腐蚀的定义、机理、预防措施以及相关领域的应用进行概述。
一、应力腐蚀的定义应力腐蚀是指金属材料在受到应力和特定腐蚀介质作用下产生的破坏。
这种破坏的特点是剧烈,严重影响材料的使用寿命和安全性。
应力腐蚀与单独的应力或腐蚀介质作用下的腐蚀具有明显的区别,需要同时满足应力和特定腐蚀介质的作用才会发生。
二、应力腐蚀的机理应力腐蚀的机理非常复杂,一般包括三个要素:金属材料、应力和腐蚀介质。
在应力腐蚀环境中,金属表面的被动膜被破坏,导致金属原子与腐蚀介质发生直接作用。
这种作用会引起金属表面的溶解,形成裂纹或表面腐蚀。
同时,应力会加剧腐蚀过程,并促使裂纹的扩展和破坏。
三、应力腐蚀的预防措施为了减少应力腐蚀的发生,可以采取一系列的预防措施。
首先,选择适合的材料是非常重要的。
某些材料对特定腐蚀介质表现出更好的抗腐蚀性能,因此在设计和使用过程中应选择这些材料。
其次,通过适当的设计和加工可以减少应力的集中和作用时间,从而降低应力腐蚀的风险。
此外,应在设计和施工中注意腐蚀控制和材料保护,定期检测和维护工程结构的完整性。
四、应力腐蚀在相关领域的应用应力腐蚀广泛应用于金属材料的工程设计和失效分析。
在航空航天领域,应力腐蚀是导致飞机、火箭和导弹等航天器件失效的主要原因之一。
在核能领域,应力腐蚀研究对于保证核反应堆的安全运行至关重要。
此外,应力腐蚀还在化工、石油、冶金等工业领域具有重要意义,对于设备的正常运行和人们的生命财产安全具有重要的保障作用。
结论应力腐蚀是金属材料在应力和特定腐蚀介质作用下发生的破坏现象。
它需要同时满足应力和腐蚀介质的作用才会发生,具有剧烈的破坏性。
为了减少应力腐蚀的发生,可以采取材料选择、设计和加工、腐蚀控制等预防措施。
金属的应力腐蚀和氢脆断裂

第六章金属的应力腐蚀和氢脆断裂§6.1应力腐蚀一、应力腐蚀及其产生条件1、定义与特点(1)定义(2)特点特定介质(表6-1)低碳钢、低合金钢——碱脆、硝脆不锈钢——氯脆铜合金——氨脆2、产生条件应力:外应力、残余应力;化学介质:一定材料对应一定的化学介质;金属材料:化学成分、显微组织、强化程度等。
二、应力腐蚀1、机理(图6-1)滑移——溶解理论(钝化膜破坏理论)a)应力作用下,滑移台阶露头且钝化膜破裂(在表面或裂纹面);b)电化学腐蚀(有钝化膜的金属为阴极,新鲜金属为阳极);c)应力集中,使阳极电极电位降低,加大腐蚀;d)若应力集中始终存在,则微电池反应不断进行,钝化膜不能恢复。
则裂纹逐步向纵深扩展。
(该理论只能很好地解释沿晶断裂的应力腐蚀)2、断口特征宏观:有亚稳扩展区,最后瞬断区(与疲劳裂纹相似);断口呈黑色或灰色。
微观:显微裂纹呈枯树枝状;腐蚀坑;沿晶断裂和穿晶断裂。
(见图6-2,和p2)三、力学性能指标1、临界应力场强度因子K ISCC恒定载荷,特定介质,测K I~t f曲线。
将不发生应力腐蚀断裂的最大应力场强度因子,称为应力腐蚀临界应力场强度因子。
2、裂纹扩展速度da/dtK I>K ISCC,裂纹扩展,速率da/dtDa/dt~ K I|曲线上的三个阶段(初始、稳定、失稳)由(图6-7,P152)可以估算机件的剩余寿命。
四、防止应力腐蚀的措施1、合理选材;2、减少拉应力;3、改善化学介质;4、采用电化学保护,使金属远离电化学腐蚀区域。
§6-2 氢脆由于氢和应力的共同作用,而导致金属材料产生脆性断裂的现象,称为氢脆断裂(简称氢脆)一、氢在金属中存在的形式内含的(冶炼和加工中带入的氢);外来的(工作中,吸H)。
间隙原子状,固溶在金属中;分子状,气泡中;化学物(氢化物)。
二、氢脆类型及其特征1、氢蚀(或称气蚀)高压气泡(对H,CH4)宏观断口:呈氧化色,颗粒状(沿晶);微观断口:晶界明显加宽,沿晶断裂。
3.6 应力腐蚀
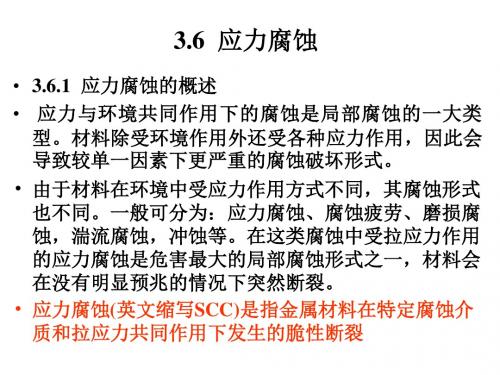
3.6.2.5 应力敏感系数
• 慢应变速率法(SSRT)是测定材料的SCC敏感性的快速 试验法。评价合金应力腐蚀敏感性的参数可用应力腐 蚀敏感系数ε f来表示: ε f = Efh/Efk (3-17) • Efh—介质中塑性应变率; Efk—空气中塑性应变率。 • ε f 值愈大,愈耐应力腐蚀。 •
SCC在一定的临界电位范围内产生
• 一般发生在钝化—活化过渡区或钝化—过钝化区。
3.6.2.2 应力腐蚀断裂特征
• 应力腐蚀断裂从宏观上属于脆性断裂。即使塑性很 高的材料也无颈缩、无杯锥状现象。 • 腐蚀介质作用,断口表面颜色呈黑色或灰黑色。 • SCC 方式有穿晶断裂、晶间型断裂、穿晶与晶间混 合型断裂。 • 晶间断裂呈冰糖块状;穿晶断裂具有河流花样等特征。 SCC断口微观特征较复杂,视具体合金与环境而定. • 微断口上往往可见腐蚀坑及二次裂纹。 • 断裂的途径与具体的材料-环境有关。裂纹走向与主 拉伸应力的方向垂直。 • 腐蚀裂缝的纵深比其宽度要大几个数量级。裂纹一 般呈树枝状
应力腐蚀发生的条件
2)特定的腐蚀介质。对于某种合金,能发生应力腐蚀断 裂与其所处的特定的腐蚀介质有关。 • 而且介质中能引起SCC物质浓度一般都很低. • 如N2O4中含有痕量的O2就可使Ti合金贮罐发生破型,
• 在核电站高温水介质中仅含质量分数为ppmCl-和O2时,
奥氏体不锈钢就可发生应力腐蚀开裂。 •
3.6.2 应力腐蚀发生的条件和特征
• 3.6.2.1 应力腐蚀发生的条件 • 发生应力腐蚀断裂需要具备三个基本条件: 1)敏感材料。合金比纯金属更易发生应力腐蚀开裂。 • 一般认为纯金属不会发生应力腐蚀断裂。 • 据报导,纯度达 99.999 %的钢在含氨介质中没有发生 腐蚀断裂,但含有W(P)=0.004%或W(Sb)=0.01%时, 则发生了应力腐蚀开裂; • 纯铁中碳的质量分数为0.04%C时,在热硝酸盐溶液中 就容易产生硝脆等,说明合金比纯金属更易产生应力 腐蚀开裂。
金属设备的应力腐蚀及预防措施

金属/设备的应力腐蚀及预防措施一、应力腐蚀的机理和特点1.应力腐蚀----金属/设备在拉应力和腐蚀介质同时作用下产生脆性破裂,叫应力腐蚀破裂。
2.应力腐蚀破裂的裂缝形态----主要有二种:a.沿晶界发展,称晶间破裂。
b.裂缝穿过晶粒,称穿晶破裂。
也有混合型,主逢为晶间型,支缝或尖端为穿晶型。
3.应力腐蚀的特征----a.必须存在拉应力(外加载核、热应力、冷/热加工或焊接后的残余应力等),若存在压应力则可抑制这种腐蚀。
b.发生应力腐蚀开裂(SCC)必须同时满足材料、环境、应力三者的特定条件。
也就是说一般只发生在一定的体系,如奥氏体不锈钢/CI-体系,碳钢/NO-3体系,铜合金/NH+4体系等。
根据介质主要成分为氯化物、氢氧化物、硝酸盐、氨、含氧水及硫化物等,而分别称为氯裂(氯脆)、碱裂(碱脆)、硝裂(硝脆)、氨裂(氨脆)、氧裂(氧脆),还有硫化物应力开裂等。
c. 应力腐蚀开裂与单纯由机械应力造成的开裂不同,它在极低的负荷应力下也能产生开裂。
d. 应力腐蚀开裂与单纯由腐蚀引起的开裂也不同,腐蚀性极弱的介质也能引起应力腐蚀开裂。
其全面腐蚀常常很轻,而且没有变形预兆,即发生突然断裂,应力腐蚀是工业生产中危害性最大的一种恶性腐蚀类型。
4.应力腐蚀的机理----应力腐蚀的机理很复杂,按照左景伊提出的理论,破裂的发生和发展可区分为三个阶段:a.金属表面生成钝化膜或保护膜。
b. 钝化膜或保护膜局部破裂,产生孔蚀或裂缝源。
c.裂缝内发生加速腐蚀,在拉应力作用下,以垂直于应力的方向深入金属内部。
裂缝多半有分枝,裂缝端部尖锐,端部的扩张速度很快,断口具有脆性断裂的特征。
二、应力腐蚀试验方法根据应力的加载方法不同,应力腐蚀试验方法主要可分为以下四类:恒变形法----给予试样一定的变形,对其在试验环境中的开裂敏感性进行评定恒载荷法(SSCC)----方法有拉伸试验、弯梁试验、C形环试验、双悬臂梁试验,常用拉伸试验,即把单轴拉伸型的试样进行H2S水溶液应力腐蚀试验,试验介质为%HAc+5%NaCl+饱和H2S水溶液,试验在恒负荷拉伸应力腐蚀试验机上进行。
应力腐蚀形成条件、危害性及裂纹特征
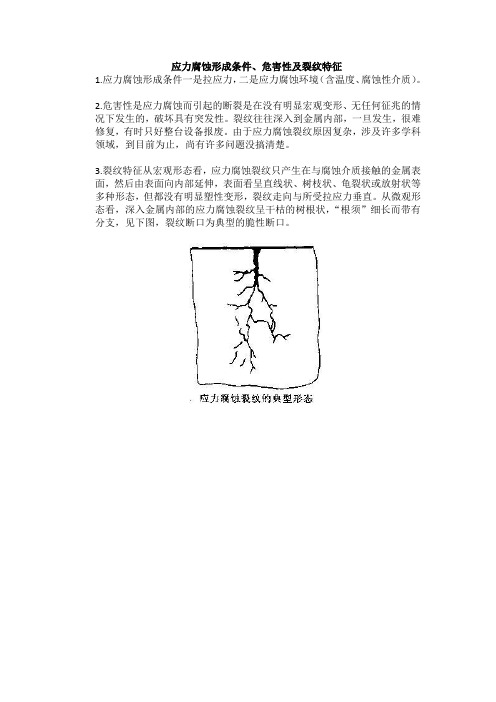
应力腐蚀形成条件、危害性及裂纹特征
1.应力腐蚀形成条件一是拉应力,二是应力腐蚀环境(含温度、腐蚀性介质)。
2.危害性是应力腐蚀而引起的断裂是在没有明显宏观变形、无任何征兆的情
况下发生的,破坏具有突发性。
裂纹往往深入到金属内部,一旦发生,很难修复,有时只好整台设备报废。
由于应力腐蚀裂纹原因复杂,涉及许多学科领域,到目前为止,尚有许多问题没搞清楚。
3.裂纹特征从宏观形态看,应力腐蚀裂纹只产生在与腐蚀介质接触的金属表
面,然后由表面向内部延伸,表面看呈直线状、树枝状、龟裂状或放射状等多种形态,但都没有明显塑性变形,裂纹走向与所受拉应力垂直。
从微观形态看,深入金属内部的应力腐蚀裂纹呈干枯的树根状,“根须”细长而带有分支,见下图,裂纹断口为典型的脆性断口。
应力腐蚀断裂
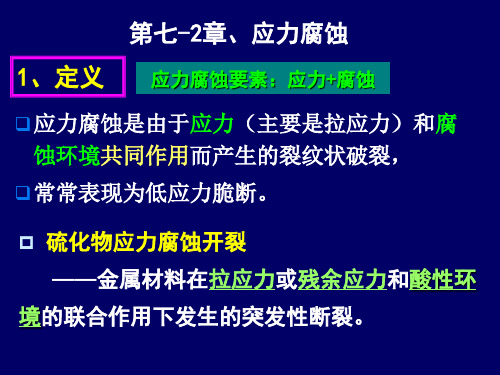
裂纹扩展速率(da/dt)与K1的关系——三阶段:
lg da dt
Ⅰ
Ⅱ
Ⅲ
K1SCC
K1C K1
图2 裂纹扩展速率(da/dt)与K1的关系
试验原理
疲劳裂纹扩展速率da/dN表达式
② 当整体金属仍是弹性 变形状态时,裂纹尖 端的前沿为塑性区。
③ 裂纹尖端前具有三向 拉伸应力区,氢可在 此处富集。
裂纹尖端易于继续阳 极溶解,裂纹壁上阴 极反应析出的氢易于 进入金属。
位错与氢结合;运动 的位错快速输送氢。
指出富集部位,三向 拉伸区较疏松,富集 氢可降低应变能。
硫化物应力(SSC)腐蚀
K1
=
P
C3
(a W
B a
)
3)硫化氢环境门限应力强度因子KISCC的测定
材料在硫化氢环境下的 抗断裂特性
实验方法 用螺栓对试样加载P0 ,
用引伸计测量加载过程 中试样裂纹开口位移, 记录中止时位移量V0
试件放入H2S溶液中,经过一定 时间,试件裂纹扩展 ,螺栓力
松弛,载荷下降, 则KI下降,
三向受拉处,物质最稀松,有空穴产生,氢集中 在空穴中。
焊接时,氢离子结合呈氢原子或氢分子,形 成107的大气压。高的压力使钢材表面出现 氢鼓包,内部产生裂纹。
要求焊接时焊条要烘干,不得受潮。
3.硫化物应力腐蚀性能试验方法
美国腐蚀工程协会NACE TM0177—2005规定了四种标准 方法:
W - a 2.5( Ke )2 0.2
K1SCC/s>0.3,视为合格
应力腐蚀

应力腐蚀(一)应力腐蚀现象金属在拉应力和特定的化学介质共同作用下,经过一段时间后所产生的低应力脆断现象,称为应力腐蚀断裂。
应力腐蚀断裂并不是金属在应力作用下的机械性破坏与在化学介质作用下的腐蚀性破坏的迭加所造成的,而是在应力和化学介质的联合作用下,按持有机理产生的断裂。
其断裂抗力比单个因素分别作用后再迭加起来的要低很多。
由拉伸应力和腐蚀介质联合作用而引起的低应力脆性断裂称为应力腐蚀(常用英文的三个字头SCC表示)。
不论是韧性材料还是脆性材料都可能产生应力腐蚀断裂。
应力腐蚀断裂一般都是在特定的条件下产生的:1.只有在拉伸应力作用下才能引起应力腐蚀开裂(近来有研究说压应力下也可能产生)。
这种拉应力可以是外加载荷造成的应力;也可以是各种残余应力,如焊接残余应力,热处理残余应力和装配应力等。
一般情况下,产生应力腐蚀时的拉应力都很低,如果没有腐蚀介质的联合作用,机件可以在该应力下长期工作而不产生断裂。
2.产生应力腐蚀的环境总是存在特定腐蚀介质,这种腐蚀介质一般都很弱,如果没有拉应力的同时作用,材料在这种介质中腐蚀速度很慢。
产生应力腐蚀的介质一般都是特定的,也就是说,每种材料只对某些介质敏感,而这种介质对其它材料可能没有明显作用,如黄铜在氨气氛中,不锈钢在具有氯离子的腐蚀介质中容易发生应力腐蚀,但反应过来不锈钢对氨气,黄铜对氯离子就不敏感。
3.一般只有合金才产生应力腐蚀,纯金属不会产生这种现象.合金也只有在拉伸应力与特定腐蚀介质联合作用下才会产生应力腐蚀断裂。
常见合金的应力腐蚀介质:碳钢:荷性钠溶液,氯溶液,硝酸盐水溶液,H2S水溶液,海水,海洋大气与工业大气奥氏体不锈钢:氯化物水溶液,海水,海洋大气,高温水,潮湿空气(湿度90%),热NaCl,H2S水溶液,严重污染的工业大气(所以不锈钢水压试验时氯离子的含量有很严格的要求)。
马氏体不锈钢:氯化的,海水,工业大气,酸性硫化物航空用高强度钢:海洋大气,氯化物,硫酸,硝酸,磷酸铜合金:水蒸汽,湿H2S,氨溶液铝合金:湿空气,NaCl水溶液,海水,工业大气,海洋大气(二)应力腐蚀断口特征与疲劳相似,应力腐蚀断裂也是通过裂纹形成和扩展这两个过程来进行的,一般认为裂纹形成约占全部时间的90%左右,而裂纹扩展仅占10%左右。
- 1、下载文档前请自行甄别文档内容的完整性,平台不提供额外的编辑、内容补充、找答案等附加服务。
- 2、"仅部分预览"的文档,不可在线预览部分如存在完整性等问题,可反馈申请退款(可完整预览的文档不适用该条件!)。
- 3、如文档侵犯您的权益,请联系客服反馈,我们会尽快为您处理(人工客服工作时间:9:00-18:30)。
1.应力腐蚀的机理:阳极溶解和氢致开裂机理
阳极溶解机理应力腐蚀断裂必须首先发生选择性腐蚀,而金属的腐蚀又受图4所示的阳极极化曲线的影响。
以不锈钢为例,增加介质中Cl-含量,降低介质中O2含量及pH值,都会使图4a中阳极极化曲线从左向右移动,这四根曲线分别对应于蚀坑或裂纹区(图4b)的不同位置。
应力的主要作用在于使金属发生滑移或使裂纹扩展,这两种力学效应都可破坏钝化膜,从而使阳极过程得以恢复,促进局部腐蚀。
钝化膜破坏以后,可以再钝化。
若再钝化速度低于钝化膜破坏速度,则应力与腐蚀协同作用,便发生应力腐蚀断裂。
氢致开裂机理或称氢脆机理,是应力腐蚀断裂的第二种机理。
这种机理承认SCC必须首先有腐蚀,但是,纯粹的电化学溶解,在很多情况下,既不易说明SCC速度,也难于解释SCC的脆性断口形貌。
氢脆机理认为,蚀坑或裂纹内形成闭塞电池,局部平衡使裂纹根部或蚀坑底部具备低的pH值,这是满足阴极反应放氢的必要条件。
这种氢进入金属所引起的氢脆,是SCC的主要原因。
这种机理取决于氢能否进入金属以及金属是否有高度的氢脆敏感性。
高强度钢在水溶液中的SCC以及钛合金在海水中的SCC是氢脆引起的。
2.应力腐蚀开裂的断口形貌:穿晶断口开裂图
3.氢鼓泡产生机理,文字图
通过实验和理论分析研究了氢鼓泡形核、长大和开裂的过程. 在充氢试样中发现直径小于100 nm未开裂的孔洞, 它们是正在长大的氢鼓泡, 也发现已开裂的鼓泡以及裂纹多次扩展导致破裂的鼓泡.分析表明, 氢和空位复合能降低空位形成能, 从而使空位浓度大幅度升高, 这些带氢的过饱和空位很容易聚集成空位团.H在空位团形成的空腔中复合成H2就使空位团稳定, 成为氢鼓泡核.随着H 和过饱和空位的不断进入, 鼓泡核不断长大, 内部氢压也不断升高.当氢压产生的应力等于被氢降低了的原子键合力时, 原子键断开, 裂纹从鼓泡壁上形核.
图5 氢鼓泡形核、长大示意图
(a) 空位V和原子氢H聚集成为空位-原子氢集团; (b) 原子氢在空位
团中复合成分子氢H2, 使其稳定, 鼓泡核形成; (c) 空位和氢不断进
入鼓泡核使其长大; (d) 当鼓泡核内氢压产生的应力等于原子键合力时, 在鼓泡壁形成裂纹
首先, 氢(H)进入金属和空位(V)复合, 使空位形成能大大降低, 从而大幅度升高空位浓度, 这些过饱和空位容易聚集成空位团. 当4个或以上的空位或空位-氢复合体(V-H)聚集成空位四面体或空位团时, 内部形成空腔, 如图5(a). 空位所带的氢在空腔中就会复合成H2, 形成氢压. 由于室温时H2不能分解成H, 故含H2的空位团在室温是稳定的, 它就是鼓泡核, 如图5(b). 随着H和空位不断进入鼓泡核, 就导致鼓泡在充氢过程中不断长大, 同时氢压不断升高, 如图5(c). 当鼓泡中的氢压在内壁上产生的应力等于被氢降低了的原子键合力时, 原子键断裂, 裂纹沿鼓泡壁形核, 如图5(d). 随着氢的不断进入, 裂纹扩展, 直至鼓泡破裂4.氢进入金属材料的途径P129
5.氢致脆断类型:可逆和不可逆,第一类和第二类
6.第一类氢脆里的三种形式:氢腐蚀,氢鼓泡、白点,氢化物型氢脆7.第二类氢脆两种形式:应力诱发氢化物型氢脆,可逆氢脆
8.氢脆的特征:氢蚀,白点宏观断口形貌
9.氢的延迟断裂,氢致开裂过程
10.氢致脆断的断口形貌特征P131
11.减少氢脆倾向的途径:降低内氢的措施,降低环境氢的活性
12.氢脆的特点
(1)实验室中识别氢脆与应力腐蚀的一种办法是,当施加一小的阳极电流,如使开裂加速,则为应力腐蚀,而当施加一小阴极电流,使开裂加速者则为氢脆。
(2)在强度较低的材料中,或者虽为高强度材料但受力不大,存在的残余拉应力也较小,这时其断裂源都不在表面,而是在表面以下的某一深度,此处三向拉应力最大,氢浓集在这里造成断裂。
(3)断裂的主裂纹没有分枝的情况,这和应力腐蚀的裂纹是截然不同的。
氢脆的断裂可以是穿晶的也可以是沿晶的,或者从一种裂纹扩展型式转变成另一种型式,但就具体的金属-环境组合来说,氢脆有特定的裂纹形态。
例如,在淬火回火钢中氢脆常沿着原奥氏体晶界扩展;而在钛合金中容易形成氢化物,裂纹是沿着氢化物与基体金属的界面上发展。
(4)氢脆断口上一般没有腐蚀产物或者其量极微。
(5)大多数的氢脆断裂(氢化物的氢脆除外),都表现出对温度和形变速率有强烈的依赖关系。
氢脆只在一定的温度范围内出现,出现氢脆的温度区间决定于合金的化学成分和形变速率。
形变速度愈大,氢脆的敏感性愈小,当形变速率大于某一临界值后,则氢脆完全消失。
氢脆对材料的屈服强度影响较小,但对断面收缩率则影响较大。