亚克力成型技术
常用亚克力制品生产工艺
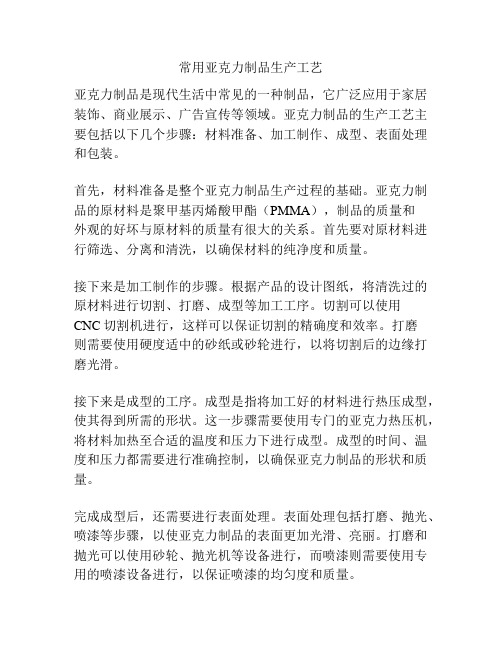
常用亚克力制品生产工艺亚克力制品是现代生活中常见的一种制品,它广泛应用于家居装饰、商业展示、广告宣传等领域。
亚克力制品的生产工艺主要包括以下几个步骤:材料准备、加工制作、成型、表面处理和包装。
首先,材料准备是整个亚克力制品生产过程的基础。
亚克力制品的原材料是聚甲基丙烯酸甲酯(PMMA),制品的质量和外观的好坏与原材料的质量有很大的关系。
首先要对原材料进行筛选、分离和清洗,以确保材料的纯净度和质量。
接下来是加工制作的步骤。
根据产品的设计图纸,将清洗过的原材料进行切割、打磨、成型等加工工序。
切割可以使用CNC切割机进行,这样可以保证切割的精确度和效率。
打磨则需要使用硬度适中的砂纸或砂轮进行,以将切割后的边缘打磨光滑。
接下来是成型的工序。
成型是指将加工好的材料进行热压成型,使其得到所需的形状。
这一步骤需要使用专门的亚克力热压机,将材料加热至合适的温度和压力下进行成型。
成型的时间、温度和压力都需要进行准确控制,以确保亚克力制品的形状和质量。
完成成型后,还需要进行表面处理。
表面处理包括打磨、抛光、喷漆等步骤,以使亚克力制品的表面更加光滑、亮丽。
打磨和抛光可以使用砂轮、抛光机等设备进行,而喷漆则需要使用专用的喷漆设备进行,以保证喷漆的均匀度和质量。
最后一步是包装。
亚克力制品生产完毕后,需要进行包装,以保护制品的完整性和安全性。
常见的包装方式有泡沫箱、塑料薄膜包装等。
根据产品的形状和尺寸,选择适当的包装材料和方式。
包装过程中需要注意保护有易损部分的制品,并使用适当的填充物填充空隙,以避免在运输过程中发生损坏。
综上所述,亚克力制品的生产工艺主要包括材料准备、加工制作、成型、表面处理和包装等步骤。
每个步骤都需要进行精确的操作和严格的控制,以确保亚克力制品的质量和外观。
随着技术的发展和需求的增加,亚克力制品的生产工艺也在不断创新和改进,以满足市场的需求和客户的要求。
亚克力注塑加工方法和工艺
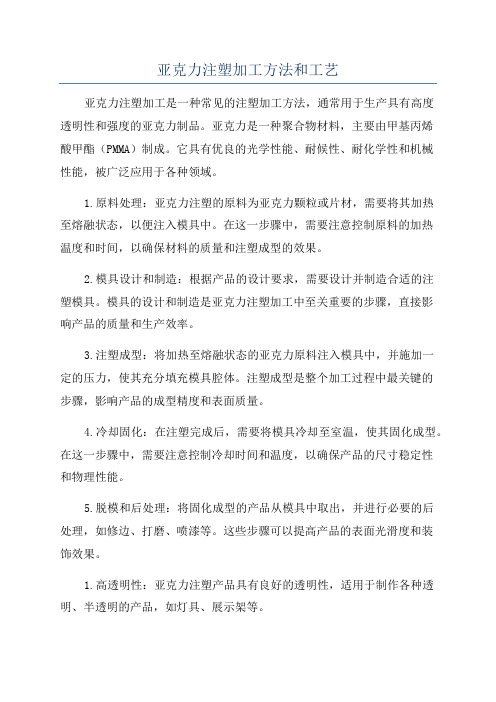
亚克力注塑加工方法和工艺亚克力注塑加工是一种常见的注塑加工方法,通常用于生产具有高度透明性和强度的亚克力制品。
亚克力是一种聚合物材料,主要由甲基丙烯酸甲酯(PMMA)制成。
它具有优良的光学性能、耐候性、耐化学性和机械性能,被广泛应用于各种领域。
1.原料处理:亚克力注塑的原料为亚克力颗粒或片材,需要将其加热至熔融状态,以便注入模具中。
在这一步骤中,需要注意控制原料的加热温度和时间,以确保材料的质量和注塑成型的效果。
2.模具设计和制造:根据产品的设计要求,需要设计并制造合适的注塑模具。
模具的设计和制造是亚克力注塑加工中至关重要的步骤,直接影响产品的质量和生产效率。
3.注塑成型:将加热至熔融状态的亚克力原料注入模具中,并施加一定的压力,使其充分填充模具腔体。
注塑成型是整个加工过程中最关键的步骤,影响产品的成型精度和表面质量。
4.冷却固化:在注塑完成后,需要将模具冷却至室温,使其固化成型。
在这一步骤中,需要注意控制冷却时间和温度,以确保产品的尺寸稳定性和物理性能。
5.脱模和后处理:将固化成型的产品从模具中取出,并进行必要的后处理,如修边、打磨、喷漆等。
这些步骤可以提高产品的表面光滑度和装饰效果。
1.高透明性:亚克力注塑产品具有良好的透明性,适用于制作各种透明、半透明的产品,如灯具、展示架等。
2.良好的表面质量:亚克力注塑产品表面平整、光滑,具有良好的装饰效果,适用于制作高档产品。
3.高强度和耐冲击性:亚克力注塑产品具有较高的强度和硬度,耐冲击性能优良,适用于制作要求较高的产品。
4.耐候性和耐化学性:亚克力注塑产品具有良好的耐候性和耐化学性,能够在各种环境条件下保持稳定性。
亚克力注塑加工在各种行业中都有广泛的应用,如电子、汽车、家具、灯具等领域。
随着科技的不断进步和市场需求的不断增长,亚克力注塑加工技术也在不断改进和创新,为生产高质量、高性能的亚克力制品提供了更多的可能性。
亚克力生产工艺流程

亚克力生产工艺流程亚克力是一种非晶态透明塑料,因其优异的透明度、韧性和耐候性被广泛应用于制造各种日常用品和工业产品。
下面将介绍一下亚克力的生产工艺流程。
首先,亚克力的生产从原料选择开始。
亚克力的主要成分是甲基丙烯酸甲酯(MMA),生产亚克力的第一步就是合成MMA。
通过合成反应,将甲酸和丙酮制成甲酮醇,再与甲醇进行酯交换反应得到MMA。
接下来,MMA通过聚合反应变成聚甲基丙烯酸甲酯(PMMA)。
聚合反应中,MMA分子中的双键被断裂,形成长链分子结构。
在聚合反应中还需要使用引发剂和催化剂来促进反应的进行。
完成聚合反应后,得到了PMMA树脂。
这个树脂还不能直接用于制品的生产,需要通过加工形成片状的亚克力板。
首先,将PMMA树脂熔化,并添加颜料和增塑剂等辅助材料,使其具有所需的颜色和特性。
然后,将熔化的树脂倒入平板模具中,经过冷却和固化,形成亚克力板。
亚克力板的生产完成后,需要进行后续的加工和处理。
首先,将亚克力板进行修边,使边缘平整光滑。
然后,根据需要,使用切割机、裁断机等设备将亚克力板切割成所需的尺寸和形状。
接着,对亚克力板进行打磨处理,使其表面光滑并去除瑕疵。
最后,对亚克力板进行抛光,使其表面更加光亮。
亚克力制品的生产也需要考虑到成型和拼接的过程。
成型是将亚克力板加热至一定温度后,放入模具或用真空吸附在模具上,通过压制或吸取空气将亚克力板压制成所需的形状。
拼接是将多个亚克力板通过特殊的胶水或溶剂进行粘合,形成更大的亚克力制品。
最后,亚克力制品还需要进行质检和包装。
质检将对亚克力制品进行外观、尺寸和物理性能等方面的检查,确保产品的质量符合要求。
然后,将亚克力制品进行包装,以保护产品在运输和存储过程中不被损坏。
以上就是亚克力生产的大致工艺流程。
亚克力的生产工艺流程相对简单,但需要严格控制各个环节,确保产品质量和生产效率。
亚克力作为一种高透明、高韧性的材料,在现代生活中有着广泛的应用,如家具、灯具、建筑装饰等领域。
亚克力板浇铸法与挤出法的工艺

亚克力板浇铸法与挤出法的工艺亚克力板是一种常用的人造有机玻璃材料,具有耐热、耐候性好、透明度高等特点。
亚克力板的制造工艺主要有浇铸法和挤出法两种。
本文将详细介绍这两种工艺的原理、步骤及特点。
一、亚克力板浇铸法亚克力板浇铸法是通过将亚克力树脂溶液倒入模具中,经过适当的加热和冷却过程,使树脂固化成型,最终得到亚克力板的制造工艺。
下面将详细介绍其具体步骤:1. 模具准备:首先需要准备好适用于浇铸的模具。
模具的形状和尺寸决定了最终亚克力板的形状和尺寸。
2. 树脂配制:将亚克力树脂与溶剂按照一定比例混合,形成树脂溶液。
在配制过程中需要注意保持树脂溶液的均匀性和稳定性。
3. 模具涂层:在模具内表面涂覆一层模具涂层,以防止树脂与模具粘连。
4. 浇注:将配制好的树脂溶液缓慢地倒入模具中,使其充分填充整个模具空间。
5. 加热:将装有树脂溶液的模具放入加热设备中,逐渐升温。
加热过程中树脂溶液会逐渐变得粘稠。
6. 冷却:当树脂溶液达到一定黏度时,停止加热并使其自然冷却。
冷却过程中树脂会逐渐固化成型。
7. 脱模:当亚克力板完全固化后,将其从模具中取出。
此时亚克力板已经具备一定的强度和透明度。
二、亚克力板挤出法亚克力板挤出法是将加热熔化的亚克力树脂通过挤出机的螺杆压力,挤出成型的工艺。
下面将详细介绍其具体步骤:1. 树脂熔化:将亚克力树脂颗粒放入挤出机的加热装置中,通过加热使其熔化成流动的树脂。
2. 挤出:熔化的亚克力树脂经过螺杆的推动,被挤出机压力下通过挤出模具的缝隙挤出。
挤出模具的形状和尺寸决定了最终亚克力板的形状和尺寸。
3. 冷却:挤出的亚克力板经过冷却装置的作用,使其迅速冷却和固化成型。
冷却过程中需要控制冷却速度和温度,以保证亚克力板的质量。
4. 切割:冷却固化后的亚克力板经过切割机的切割,得到符合要求的亚克力板尺寸。
亚克力板浇铸法和挤出法在制造工艺上有一些显著的区别和特点。
浇铸法适用于制造较大尺寸和较厚的亚克力板,制造过程中需要使用模具,因此适用于批量生产。
亚克力滴塑工艺

亚克力滴塑工艺亚克力滴塑工艺是一种应用广泛的加工技术,它通过将亚克力材料加热至液态,再通过滴塑的方式使其成型。
这种工艺的主要优势在于可以制作出各种形状复杂、透明度高的产品。
在亚克力滴塑工艺中,首先需要将亚克力材料加热至一定温度,使其变得粘稠。
然后,通过滴塑的方式将亚克力液体滴落到模具中,并等待其自然凝固。
在凝固过程中,亚克力材料会逐渐变硬,并且保持着所滴塑的形状。
最后,将凝固的亚克力产品从模具中取出,经过一系列的后处理工艺,如修边、抛光等,使其表面平整光滑。
亚克力滴塑工艺的应用领域非常广泛。
在建筑领域,亚克力滴塑材料可以用于制作透明的窗户、天花板、墙面等装饰材料。
在家居领域,亚克力滴塑产品可以用于制作各种家具、照明设备等。
此外,亚克力滴塑工艺还可以应用于汽车、电子产品、玩具等行业。
亚克力滴塑工艺的优点不仅在于其制作出的产品形状多样、透明度高,而且亚克力材料本身具有良好的耐候性和耐化学性,能够在各种恶劣的环境中长时间使用。
此外,亚克力滴塑产品还具有良好的表面光泽和触感,给人一种高质量的感觉。
然而,亚克力滴塑工艺也存在一些挑战和限制。
首先,亚克力材料的成本较高,使得滴塑产品的价格相对较高。
其次,亚克力滴塑工艺对操作者的要求较高,需要具备一定的技术和经验。
此外,亚克力滴塑产品的尺寸较大时,可能存在收缩和变形的问题,需要通过优化工艺来解决。
总的来说,亚克力滴塑工艺是一种重要的加工技术,它能够制作出形状复杂、透明度高的产品。
这种工艺的应用广泛,可以满足建筑、家居、汽车等行业的需求。
虽然亚克力滴塑工艺存在一些挑战和限制,但随着技术的不断进步和工艺的不断优化,相信它会在未来得到更广泛的应用。
亚克力加工工艺)

亚克力加工工艺聚甲基丙烯酸甲酯可以采用浇铸、注塑、挤出、热成型等工艺。
1.浇铸成型浇铸成型用于成型有机玻璃板材、棒材等型材,即用本体聚合方法成型型材。
浇铸成型后的制品需要进行后处理,后处理条件是60℃下保温2h,120℃下保温2h2.注塑成型注塑成型采用悬浮聚合所制得的颗粒料,成型在普通的柱塞式或螺杆式注塑机上进行。
表1是聚甲基丙烯酸甲酯注塑成型的典型工艺条件。
工艺参数螺杆式注塑机柱塞式注塑机料筒℃温度后部180-200 180-200 中部190-230 前部180-210 210-240 喷嘴温度℃ 180-210 210-240 模具温度℃ 40-80 40-80 注射压力MPa 80-120 80-130 保压压力MPa 40-60 40-60 螺杆转速rp.m-1 20-30 注塑制品也需要后处理消除内应力,处理在70-80℃热风循环干燥箱内进行,处理亚克力棒时间视制品厚度,一般均需4h左右。
3.挤出成型聚甲基丙烯酸甲酯也可以采用挤出成型,用悬浮聚合生产的颗粒料制备有机玻璃板材、棒材、管材、片材等,但这样制备的型材,特别是板材,由于聚合物分子量小,力学性能、耐热性、耐溶剂性均不及浇注成型的型材,其优点是生产效率高,特别是对于管材和其它用浇注法时模具。
难以制造的型材。
挤出成型可采用单阶或双阶排气式挤出机,螺杆长径比一般在20-25。
表2是挤出成型的典型工艺条件。
工艺参数片材棒材螺杆压缩比 2 2 料筒℃温度后部150-180 150-180 中部170-200 170-200 前部170-230 170-200 挤出压力MPa 2.8-12.4 0.7-3.4 进料口温度℃50-80 50-80 口模温度℃ 180-200 170-1904.热成型热成型是将有机玻璃板材或片材制成各种尺寸形状制品的过程,将裁切成要求尺寸的坯料夹紧在模具框架上,加热使其软化,再加压使其贴紧模具型面,得到与型面相同的形状,经冷却定型后修整边缘即得制品。
PMMA工艺技术对比

PMMA工艺技术对比PMMA (Polymethyl Methacrylate),也称为亚克力或有机玻璃,是一种常用的聚合物材料,具有优异的透明度、耐候性和耐化学性。
由于其广泛应用于建筑、汽车、通信等领域,对PMMA工艺技术的研发和改进具有重要意义。
在下面的文章中,我们将对两种常见的PMMA工艺技术进行对比。
一种常见的PMMA工艺技术是注射成型。
注射成型是一种将熔融PMMA注入模具中,通过冷却和硬化形成特定形状的工艺。
该工艺具有以下优点:首先,注射成型可以制造具有高精度和复杂形状的产品,如透明的塑料零件。
与其他制造方法相比,注射成型更适用于大批量生产,能够提高生产效率。
其次,注射成型可以实现高度的自动化和智能化,减少了人力成本和错误的可能性。
此外,注射成型具有良好的表面质量和一致性,可以减少二次加工的需求。
然而,注射成型也存在一些缺点。
首先,注射成型的设备和工艺要求较高,需要投资较多。
其次,注射成型过程中,PMMA材料可能由于温度过高而氧化分解,降低了产品的质量。
此外,注射成型的消耗品如模具等需要定期更换,增加了生产成本。
而且,注射成型的生产过程中产生的废气和废料处理也需要额外的成本和技术。
另一种常见的PMMA工艺技术是挤出成型。
挤出成型是将熔融的PMMA通过挤出机挤出成特定的形状,再通过冷却和切割形成产品的工艺。
挤出成型具有以下优点:首先,挤出成型具有较低的设备和工艺投资,适用于小规模生产和定制生产。
其次,挤出成型可以制造较大的产品尺寸范围,如厚板、管材等。
此外,挤出成型可以实现较高的生产效率和连续生产,减少了生产时间和成本。
然而,挤出成型也存在一些缺点。
首先,挤出成型的产品精度较低,不适用于要求高精度和复杂形状的产品。
其次,挤出成型的表面质量较差,需要进行后续的加工和处理。
此外,挤出成型的废料较多,对环境造成了一定的影响。
综上所述,注射成型和挤出成型是两种常见的PMMA工艺技术。
注射成型适用于大批量生产、高精度和复杂形状的产品,具有较高的生产效率和良好的表面质量。
有机玻璃浇铸成型工艺

有机玻璃浇铸成型工艺有机玻璃,又称亚克力,是一种常见的透明塑料材料,具有高透明度、耐候性好、表面硬度高等特点,被广泛应用于家具、建筑、装饰等领域。
有机玻璃制品的生产过程中,浇铸成型是其中一种主要的工艺方法。
本文将介绍有机玻璃浇铸成型工艺的工艺流程、特点以及应用领域。
工艺流程有机玻璃浇铸成型工艺的主要流程包括以下几个步骤:1.准备原材料:首先需要准备好有机玻璃颗粒、添加剂等原材料,确保原材料的质量符合要求。
2.配方调制:根据产品的要求,将原材料按照一定比例进行混合和调配,确保配方的准确性和稳定性。
3.加热熔化:将混合好的有机玻璃颗粒在一定的温度下进行加热,使其熔化成液体状态。
4.浇注成型:将熔化的有机玻璃液体倒入预先设计好的模具中,待其冷却凝固后,即可得到成型的有机玻璃制品。
5.后续加工:根据需要对成型的有机玻璃制品进行切割、打磨、抛光等后续加工处理,以满足不同的产品要求。
特点有机玻璃浇铸成型工艺具有以下几个显著特点:•成型自由度高:有机玻璃浇铸成型可以根据不同的设计要求,制作出各种形状、尺寸的制品,具有较高的成型自由度。
•制品透明度高:经过浇铸成型的有机玻璃制品表面光滑,透明度高,能够有效展现材料的优美质感。
•耐候性强:有机玻璃制品经过浇铸成型后,具有良好的耐候性和耐候性,能够在室内外环境下长时间保持良好的外观表现。
•生产效率高:相较于其他加工工艺,有机玻璃浇铸成型工艺生产效率较高,能够快速制作大批量的有机玻璃制品。
应用领域有机玻璃浇铸成型工艺广泛应用于各个领域,主要包括以下几个方面:1.家具制造:有机玻璃浇铸成型工艺可以制作出透明、高光泽度的家具配件,如桌面、椅背等,为家居空间增添现代感。
2.建筑装饰:在建筑领域,有机玻璃制品可以用于制作玻璃幕墙、室内隔断、天花板等装饰材料,营造出通透明亮的空间氛围。
3.展示器具:有机玻璃浇铸成型工艺可以制作出各种展示器具,如展示盒、展示架等,用于商场、博物馆等场所展示商品或文物。
- 1、下载文档前请自行甄别文档内容的完整性,平台不提供额外的编辑、内容补充、找答案等附加服务。
- 2、"仅部分预览"的文档,不可在线预览部分如存在完整性等问题,可反馈申请退款(可完整预览的文档不适用该条件!)。
- 3、如文档侵犯您的权益,请联系客服反馈,我们会尽快为您处理(人工客服工作时间:9:00-18:30)。
压克力成型技术的概念亚克力介绍亚克力是一种经过特殊处理的有机材料,由于其优异的强韧性及良好的透光性,早期曾用于制造飞机和坦克的玻璃,现代的亚克力材料表面覆涂了高强度紫外线吸收剂并拥有丰富多彩的颜色。
夜间色彩艳丽并极具穿透力。
抗日晒雨淋,使用寿命长达十多年,是目前国际上最流行的户外标识招牌制作材料之一。
在巴黎、纽约、东京等国际大都市的繁华商业区,处处可见亚克力标识的靓丽身影,为无数国际知名企业品牌形象增添无穷魅力。
在我国,亚克力标识招牌产品的使用尚属初期阶段,但随着麦当劳、肯德基等国际知名企业的示范性使用,在各大中城市已有越来越多的企业钟情于以亚克力面板材料的内置光源标识产品,因为原有的金属、喷绘,无论在材质上还是在工艺上都是很难达到商家的一系列要求,而亚克力成型字(灯箱)则可以满足商家兼顾白天与夜间效果,色彩艳丽,能提供个性化服务,又能提供统一标准尺寸,统一配送等诸多服务,因而备受青睐。
我公司通过不断研发探索,已形成众多产品系列,如吸塑立体发光字、双吸塑立体灯箱、镶边立体发光字、多色拼接吸塑立体灯箱等,并提供了个性的标识产品,得到了客户的一致肯定,市场反应强烈。
我们制作的产品具有优越的可塑性、透光性及表面平整性,其出色的空间表现明显优于其他广告表现形式,它采用新型聚脂材料,经高温立体热成型,金属托底,内置光源,极具视觉冲击力,已成为国际品牌户外宣传的首选。
它具有以下特性:1 观赏性材料晶莹剔透、光洁度高、极具质感、美感2 耐气候性面板覆涂高强度紫外线吸收剂,金属底座喷涂进口汽车漆,可保长耐候,永不褪色,硬度强,使用年限长达15年,优良的抗变形能,高温70度,低温-50度不变形。
3 合理性防雨防潮,开启式结构,便于维修。
4 耐冲击性是玻璃产品的16倍,几乎没有断裂的危险。
5 透光性高达93%以上,光线柔和,璀璨夺目,对光线的需求小,节省电能。
6 耐燃性不自燃并具有自熄性。
7 节能性采用LED光源极其省电,降低了使用成本。
亚克力又称特殊处理的有机玻璃,系有机玻璃换代产品,用亚克力制作的灯箱具有透光性能好、颜色纯正、色彩丰富、美观平整、兼顾白天夜晚两种效果、使用寿命长、两天不影响使用等特点,此外,亚克力板材与铝塑板型材、高级丝网印等可以完美结合,满足商家的需求,亚克力吸塑是提高营业店面档次,统一企业形象最好的户外广告形式,由此可见亚克力灯箱正逐步取代原始的喷绘、写真灯箱等广告形式,成为室内外主导。
但亚克力的优异性能要通过精湛的工艺,才能让它完美体现;我公司有着丰富的户外亚克力制作经验,内照明备用高亮度冷阴灯管,可根据不同要求做出不同的效果,满足客户的需要。
广告字的做法亚克力字制作亚克力字按其造型分,标准有三种称呼1:A:平鼓字B:尖鼓字C:圆鼓字其它的造型基本上都是从这三种演变过来的。
譬如尖鼓可演变菱形、圆鼓可演变弧形,只是刀具的选择、下刀的深浅不同,字的造型也就截然不同。
A:平鼓字的制作及要求:把所要的字样用复印纸描在密度板上,四边各留5cm,用手动雕刻机安上相应的直刀,沿字的外线开出模具(内部走里线,其它走外线)。
模具开出后,用锉刀把模具挫平整。
然后再用锉刀和砂纸把字的阴阳模各边及各角磨成圆弧状,一定要圆滑、均匀,最后用砂纸磨平。
也可用电脑雕刻机刻模具,加够高度后高棱角处理圆滑即可。
B:尖鼓字的制作及要求:第一步:同平鼓字的制作方法相同,只是各边及各角暂不磨成圆弧状。
第二步:加高、成型。
根据字的大小、笔划的宽窄(以最宽笔划算,从第二层算起划一条中间线看两侧的倾斜度是否为90度直角,以此角来定位加高的厚度,然后选择适当的45度斜角刀安在多功能铣床上,字面朝下开出尖鼓来,用502胶水或三秒胶水在打出尖渐渐的各部位滴上胶水,使其坚硬些不至于压制时损坏模具,没有出现尖的部位,该加高的加高,该修理的修理到位,特大字买不到刀具只能手工来做,修理成形。
C:圆鼓字的制作及要求:第一步:同平鼓字的制作方法相同,只是各边及各角暂不磨成圆弧状。
第二步:加高、成型。
所加高的厚度要跟字的大小成比例、协调一致做出来的东西才美观,步骤与尖鼓字制作大致相同,只是刀具用的是圆角刀。
五、亚克力灯箱底板的制作要求1、底板的阳模四边要处理圆滑、四角要磨成圆弧度和倾斜度(即四角上窄下宽),以方便脱模。
2、底板的阴模底部用砂纸磨一下即可,角度不要太大,这样可以缩小两块底板拼接时的缝隙。
六、亚克力灯箱底板模具的计算方法亚克力灯箱底板模具的计算方法有两种情况,此两种算法针对于等份分割成若干块的底板而言。
第一种情况:模具横向或竖向分割成若干块的算法如下:1、用总长度减掉底板两侧的留边尺寸等于剩下要制作模具的总长度2、用剩下要制作模具的总长度除以等份分割的块数等于要制作底板模具的尺寸3、用总宽度减掉底板两侧的留边尺寸等于要制作底板模具的尺寸4、把2算出的尺寸减掉5毫米,是两块底板拼接时缝隙的损耗(也就是拼接不严的损耗)5、最后总尺寸的长短,由成型后的多块亚克力底板拼接在一起后,在底板的两侧边上找。
第二种情况:模具横、竖向均全部分割成若干块时的算法如下:1、用总长度减掉底板两侧的留边尺寸等于剩下要制作模具的总长度2、用剩下要制作模具的总长度除以等份分割的块数等于要制作底板模具的尺寸3、用总宽度减掉底板两侧的留边尺寸等于剩下要制作模具的总宽度4、用剩下要制作模具的总宽度除以等份分割的块数等于要制作底板模具的尺寸5、把2和4算出的尺寸分别减掉5毫米,是两块底板拼接时缝隙的损耗(也就是拼接不严的损耗)6、最后总尺寸的长短,由成型后的多块亚克力底板拼接在一起后,在底板的两侧边上找。
七、成型后的亚克力字和底板的留边尺寸1、成型后的亚克力字在不同的情况下的留边尺寸有三种情况:A:字与底板拼接时,留3毫米左右的边。
B:字单独做箱体时,留1公分左右的边。
C:字压制后需要人工再围几公分的边,字的留边尺寸为5毫米左右。
2、底板的留边尺寸在2至3公分左右。
八、字粘接底板后的镂空1、第一步:把粘好字的底板反过来放在阴模上,底部放一个日光灯管照明。
2、第二步:灯光发光后,可以看到字的空心部位,用手电钻把需要镂空的地方钻个比修边刀刀刃直径略大点的孔,然后在木工修边机上安上修边刀,放进钻好的孔中间位置(刀下进的深度的略大于板材的厚度),进行镂空。
九、箱体中安装日光灯和LED最佳数量和安装方法1、日光灯的数量是每平方米4-5根,靠箱体两边的灯管尽量离箱体近些,因其箱体两侧反光能力较弱。
2、LED的数量几安装:A:数量:LED与LED 的间距标准为8cm X8cm,也可适当的放到8cm X 10cm或10cm X 10cm的距离。
因目前国内市场LED的生产厂家很多,其选材上的不一致,导致其质量也参差不齐。
所以具体有关安装及箱体的高度请跟购买商或我公司耗材部咨询为妥,以上的内容仅供参考。
B:安装:把LED在箱体底部选好位置后,先用502胶水或三秒胶水粘牢,再用快干胶或玻璃胶打在LED的两侧即可。
十、LED的性能及注意事项1、LED具有低功耗、高亮度、抗震动、可靠性高、寿命长、无污染、和色彩艳丽等优点,是真正的绿色照明。
使用寿命达10万小时。
2、LED能发出红、黄、蓝、绿、白色、橙色、琥珀色、蓝绿双色、红绿双色、黄绿色、纯绿色、翠绿色等,通过数控可变成红、黄、蓝、绿、白、青、紫色。
3、金属外壳封装的LED光源模块有“ZLS-PMB、ZLS-PMBC”两种类型。
A:ZLS-PMB型光源板实现侧面发光,适于安装在发光字的侧壁,通过反射均匀照亮出光面。
安装简单,要求字的内壁涂反光材料。
一般距灯箱3cm高,箱体高一般要求在7cm以上B:ZLS-PMBC型光源板,实现正面发光,适于安装在发光字的底部,直接照亮出光面。
要求字槽宽度在4cm以上,箱体高4cm以上。
光源板与灯箱接触部位应良好散热。
4、每块光源板中心距一般为10cm。
5、字槽宽度小于等于10时,使用ZLS-PMBC型光源板时,一般可只安装单侧,即可保证足够亮度;宽度在10-20cm之间时,应在两侧安装光源板,并尽量交错排布;若字槽宽度大与20cm,需要字槽底部中间以10cm左右的间距加装ZLS-PMBC型光源板。
6、光源板标准封装为5个一串,红色光源板最多可并6串(30块)多余30块应另起回路;其它颜色的光源板最多并10串(50块)多余50块的应另起回路,电源接在开关电源上,电源于光源的距离尽量小。
7、用接线子相连电线,线头无须剥线,只需要把线头剥至接线子底部,再用钳子压紧即可。
8、最后一个光源板块接线终端的线头应用防水胶带缠好。
以上内容仅供参考十一、制作模具时的刀具选择刀具的选择是根据亚克力板材的厚度来选择的,有几种情况如下:1、用手工做模具:A:模具的厚度在3.5公分以下,刀具选择于板材厚度相同的刀具。
B:模具的厚度在3.5公分以上,刀具选择比板材厚度略大1-2mm的刀具,其略大多少是根据模具的厚度高低来选择的。
2、用电脑雕刻机做模具:A:模具的厚度在3.5公分以下,刀具选择于板材厚度相同的刀具(因雕刻机配置的刀具大小和板材厚度略有差别可选择和所用板材厚度相近的刀具,只能不板材厚度大的不选择小的)。
B:模具的厚度在3.5公分以上,刀具选择比板材厚度略大1-2mm的刀具,其略大多少是根据模具的厚度高低来选择的。
十二、字的大小与模具厚度的关系1、尖鼓字:可根据模具的尖度成90度直角的比例下,厚度可做到设备允许加工制作范围内的高度。
2、圆鼓字:在字的大小与厚度成比例、协调一致美观的情况下,厚度可做到设备允许加工制作范围内的高度。
3、平鼓字:A:60-70公分的字模具厚度能做到4公分左右,模具略有倾斜度;90公分-1米的字模具厚度能做到`6公分左右,模具有倾斜度;1米以上的字模具厚度能做到8公分左右模具略有倾斜度;2米的字模具厚度能做到十几公分左右,模具略有倾斜度。
以上的参数仅供参考。
十三、字为20公分以下亚克力字的吸塑要求1、模具的厚度为1.5公分。
2、模具要用雕刻机做。
3、阴阳模的空隙即亚克力板材的厚度。
4、字的内部阴模雕出后,磨小些。
让内部阴阳模之间的空隙比亚克力板材的厚度略大。
5、阴阳模的四边即各角要用砂纸打磨一下,笔划小或窄的阴阳模用502胶水或3秒胶水点一下,使表面变硬不至于压碎。
6、阴阳模修好后,把字的阳模和阴模分别粘在两块大小与字模略大点的密度板上对好位置。
平台压制快接触模具时,点触开关让平台慢慢下直到压实板材位置,起模时同样要点触开关直到阴阳模脱离在稳步上升或下降平台。
对于小字挤压板更容易吸压成型模具高度也可适当增高。
十四、亚克力板材厚度适用多大尺寸亚克力灯箱底板1、3个厚的板材只适合1米左右的亚克力灯箱底板。
2、如果面积过大在1.5米以上这要考虑到板材的本身的承重力、伸缩性和拉伸力等物理特性,根据当地天气状况、风力的大小等情况可选择4-5个厚的板材。