正碰结构分析报告
某SUV车型正面40%偏置碰分析及车体结构的优化设计

10.16638/ki.1671-7988.2017.16.057某SUV车型正面40%偏置碰分析及车体结构的优化设计路遥,张超(安徽江淮汽车集团股份有限公司,安徽合肥230601)摘要:运用有限元分析方法对公司的某款SUV车型进行正面40%偏置碰分析,发现存在的问题,通过分析找出问题的原因,并制定相应的车体结构优化设计方案,最后运用有限元分析方法进一步验证方案的有效性,最终获得满足目标设定要求的产品。
关键词:40%偏置碰;有限元分析方法;车体结构中图分类号:U462.1 文献标识码:A 文章编号:1671-7988 (2017)16-163-04Simulation analysis and vehicle body structure optimization of aSUV front 40% offset impactLu Yao, Zhang Chao( Anhui Jianghuai Automobile group Co. Ltd, Anhui Hefei 230601 )Abstract:Thefinte element analysis method is used to simulation analysis a SUV of the company front 40% offset impact, find out the cause of the problem by analyzing and make the corresponding body structure design,and finally use the finte element analysis method to further verify the effectiveness of the program,and ultimately to meet the target set requirements of the product.Keywords: 40% offset impact; The finte element analysis method; body structureCLC NO.: U462.1 Document Code: A Article ID: 1671-7988 (2017)16-163-04前言目前,车辆的正面碰撞试验主要分为完全正面碰撞试验(Full Width Frontal Impact Test) 和偏置碰撞试验(Offset Deformable BarrierForntalImpact Test) ;根据交通事故的统计结果表明[1],偏置碰撞在交通事故中出现的比例极高,同时驾驶员在偏置碰撞事故中受到损伤最为严重[2]。
某轿车正碰安全性分析及优化
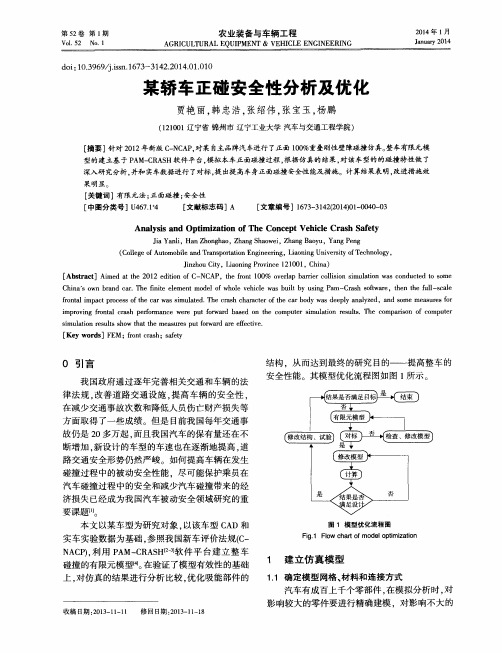
[ 中图分类号]U 4 6 7 . 1 + 4
[ 文献标志码 ] A
[ 文章编号]1 6 7 3 — 3 1 4 2 ( 2 0 1 4 ) 0 1 — 0 0 4 0 - 0 3
An a l y s i s a n d Op t i mi z a t i o n o f Th e Co n c e p t Ve h i c l e Cr a s h S a f e t y
律法规 , 改善道路交通设施 , 提高车辆的安全性 , 在减少交通事故次数和降低人员伤亡财产损失等 方面取得 了一些成绩。但是 目前我 国每年交通事 故仍是 2 0 多万起 , 而且我国汽车的保有量还在不 断增加 。 新设计的车型的车速也在逐渐地提高 , 道 路交通安全形势仍然严峻。如何提高车辆在发生 碰撞过程中的被动安全性能 ,尽可能保护乘员在 汽车碰撞过程中的安全和减少汽车碰撞带来的经 济损 失 已经 成 为我 国汽车 被 动安 全领 域研 究 的重
[ Ke y w o r d s ]F E M; f r o n t c r a s h ;s a f e t y
0 引 言
我 国政府 通 过逐 年 完善 相关 交 通 和车 辆 的法
结 构 ,从 而 达到 最终 的研究 目的— — 提高 整 车 的 安全 性能 。其 模 型优化 流 程 图如 图 1 所示。
Ch i n a S o wn b r a n d c a r . T h e f i n i t e e l e me n t mo d e l o f wh o l e v e h i c l e wa s b u i l t b y u s i n g P a m- Cr a s h s o f t wa r e ,t h e n t h e f u l l - s c a l e f r o n t a l i mp a c t p r o c e s s o f t h e c a r w a s s i mu l a t e d . T h e c r a s h c h a r a c t e r o f t h e c a r b o d y wa s d e e p l y a n a l y z e d,a n d s o me me a s u r e s f o r
某车型多种正面碰撞安全性能性分析

10.16638/ki.1671-7988.2020.06.030某车型多种正面碰撞安全性能性分析周洋,樊海龙(电动汽车安全评价重庆市工业和信息化重点实验室,重庆401122)摘要:实际生活中的正面碰撞事故往往形式复杂,因此,文章结合2018版C-NCAP和C-IASI两大规程中规定的工况以及生活中常见的正碰事故类型情况,通过仿真分析总结了某车型在四种正面碰撞工况下的安全性能,能够为全面研究汽车正面碰撞的安全性能提供参考借鉴。
关键词:正面碰撞;C-NCAP;C-IASI;安全性能中图分类号:U467 文献标识码:B 文章编号:1671-7988(2020)06-93-03Analysis on the Safety Performance of Multiple Header Collisions in a ModelZhou Yang, Fan Hailong( Key Laboratory of Industry and Informatization in Chongqing, Chongqing 401122 )Abstract: Frontal impacts in life are often complex, therefore, by combining the working conditions specified in two major regulations of the 2018 edition of C-NCAP and the C-IASI as well as a common collision accident in daily life, this paper analyzes and summarizes the safety performance of a vehicle in four frontal collision conditions, which is able to provide a reference for researching the overall frontal impact safety performance.Keywords: Frontal impacts; C-NCAP; C-IASI; Safety performanceCLC NO.: U467 Document Code: B Article ID: 1671-7988(2020)06-93-03前言近年来我国汽车工业发展势头强劲,2017年累计有33352万辆机动车在公安交通管理部门注册登记,其中新车数量达到2813万辆,创造历史新高[1];但同时,随着车流量的增大,中国近几年的交通事故也不断增多,已成为全球道路交通安全事故最多的国家之一[2]。
碰撞安全分析结构篇课件

侵入量测量位置
前围板 CCB
A柱后移量
方向盘 脚踏板
左上 左下 右上 右下
X 测量值 263.9 (279)
116.1 107.7 (170)
33 (33) 8.4 3.9
87.2 (87) 154.2
目标值 150 80
100
80 150
Z 测量值
∕ ∕ ∕ ∕ ∕ ∕
63.3 (68) 75.7
碰撞安全分析-结构篇
编制:
上海世科嘉设计验证部CAE科 2008-9-18
碰撞安全分析结构篇
1
整车主要结构
碰撞过程中能量吸收主要是通 过车身实现,底盘零件吸收的能量 不起主要作用,但底盘零件传递力 对车身加速度有重要影响。
碰撞安全分析结构篇
2
全封闭式承载车身结构
碰撞安全分析结构篇
3
主要NCAP比较
1 2
MV02
Fti Sti
ⅲ 优化kickdown区间结构,保证力分配路径合理
B11 Mxx
MXX
B11
INJURY AIRBAG+PT AIRBAG+PT
DRV PAS DRV PAS
HIC
305 270 354 351
第一阶段加速度 第二阶段加速度
碰撞C安H全E分ST析g结构篇35 34 40.8 41.2
Fuel filler side
Honeycomb deformable barrier V = 80 km/h – Mass=1368 Kg.
70% Overlap on fuel filler side A 301 NEW regulation
Rigid plate barrier M = 1100 Kg.
车身结构正面抗撞性
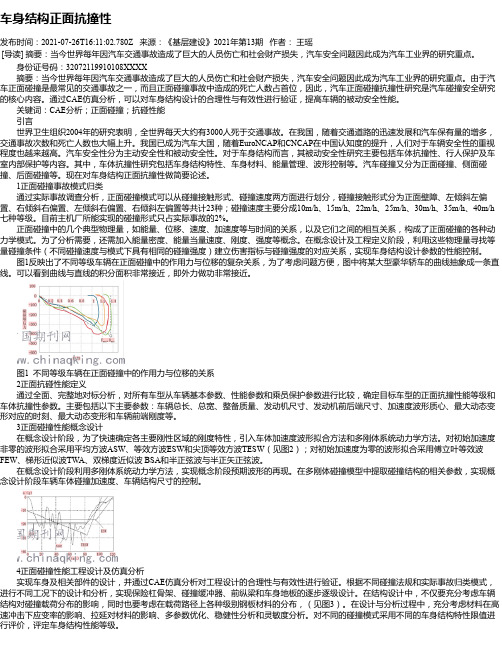
车身结构正面抗撞性发布时间:2021-07-26T16:11:02.780Z 来源:《基层建设》2021年第13期作者:王瑶[导读] 摘要:当今世界每年因汽车交通事故造成了巨大的人员伤亡和社会财产损失,汽车安全问题因此成为汽车工业界的研究重点。
身份证号码:32072119910108XXXX 摘要:当今世界每年因汽车交通事故造成了巨大的人员伤亡和社会财产损失,汽车安全问题因此成为汽车工业界的研究重点。
由于汽车正面碰撞是最常见的交通事故之一,而且正面碰撞事故中造成的死亡人数占首位,因此,汽车正面碰撞抗撞性研究是汽车碰撞安全研究的核心内容。
通过CAE仿真分析,可以对车身结构设计的合理性与有效性进行验证,提高车辆的被动安全性能。
关键词:CAE分析;正面碰撞;抗碰性能引言世界卫生组织2004年的研究表明,全世界每天大约有3000人死于交通事故。
在我国,随着交通道路的迅速发展和汽车保有量的增多,交通事故次数和死亡人数也大幅上升。
我国已成为汽车大国,随着EuroNCAP和CNCAP在中国认知度的提升,人们对于车辆安全性的重视程度也越来越高。
汽车安全性分为主动安全性和被动安全性。
对于车身结构而言,其被动安全性研究主要包括车体抗撞性、行人保护及车室内部保护等内容。
其中,车体抗撞性研究包括车身结构特性、车身材料、能量管理、波形控制等。
汽车碰撞又分为正面碰撞、侧面碰撞、后面碰撞等。
现在对车身结构正面抗撞性做简要论述。
1正面碰撞事故模式归类通过实际事故调查分析,正面碰撞模式可以从碰撞接触形式、碰撞速度两方面进行划分,碰撞接触形式分为正面壁障、左倾斜左偏置、右倾斜右偏置、左倾斜右偏置、右倾斜左偏置等共计23种;碰撞速度主要分成10m/h、15m/h、22m/h、25m/h、30m/h、35m/h、40m/h 七种等级。
目前主机厂所能实现的碰撞形式只占实际事故的2%。
正面碰撞中的几个典型物理量,如能量、位移、速度、加速度等与时间的关系,以及它们之间的相互关系,构成了正面碰撞的各种动力学模式。
客车前部结构正碰仿真与改进
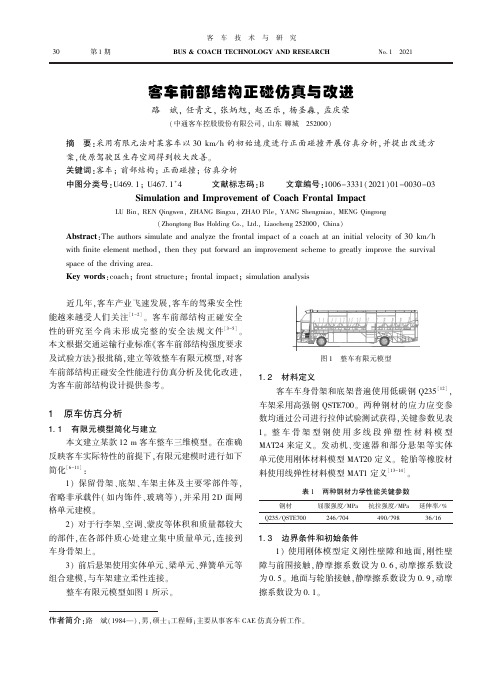
客 车 技 术 与 研 究第1期 BUS &COACH TECHNOLOGY AND RESEARCH No.1 2021作者简介:路 斌(1984 ),男,硕士;工程师;主要从事客车CAE 仿真分析工作㊂客车前部结构正碰仿真与改进路 斌,任青文,张炳旭,赵丕乐,杨圣淼,孟庆荣(中通客车控股股份有限公司,山东聊城 252000)摘 要:采用有限元法对某客车以30km /h 的初始速度进行正面碰撞开展仿真分析,并提出改进方案,使原驾驶区生存空间得到较大改善㊂关键词:客车;前部结构;正面碰撞;仿真分析中图分类号:U469.1;U467.1+4 文献标志码:B文章编号:1006-3331(2021)01-0030-03Simulation and Improvement of Coach Frontal ImpactLU Bin,REN Qingwen,ZHANG Bingxu,ZHAO Pile,YANG Shengmiao,MENG Qingrong(Zhongtong Bus Holding Co.,Ltd.,Liaocheng 252000,China)Abstract :The authors simulate and analyze the frontal impact of a coach at an initial velocity of 30km /h with finite element method,then they put forward an improvement scheme to greatly improve the survival space of the driving area.Key words :coach;front structure;frontal impact;simulation analysis 近几年,客车产业飞速发展,客车的驾乘安全性能越来越受人们关注[1-2]㊂客车前部结构正碰安全性的研究至今尚未形成完整的安全法规文件[3-5]㊂本文根据交通运输行业标准‘客车前部结构强度要求及试验方法“报批稿,建立等效整车有限元模型,对客车前部结构正碰安全性能进行仿真分析及优化改进,为客车前部结构设计提供参考㊂1 原车仿真分析1.1 有限元模型简化与建立本文建立某款12m 客车整车三维模型㊂在准确反映客车实际特性的前提下,有限元建模时进行如下简化[6-11]:1)保留骨架㊁底架㊁车架主体及主要零部件等,省略非承载件(如内饰件㊁玻璃等),并采用2D 面网格单元建模㊂2)对于行李架㊁空调㊁蒙皮等体积和质量都较大的部件,在各部件质心处建立集中质量单元,连接到车身骨架上㊂3)前后悬架使用实体单元㊁梁单元㊁弹簧单元等组合建模,与车架建立柔性连接㊂整车有限元模型如图1所示㊂图1 整车有限元模型1.2 材料定义客车车身骨架和底架普遍使用低碳钢Q235[12],车架采用高强钢QSTE700㊂两种钢材的应力应变参数均通过公司进行拉伸试验测试获得,关键参数见表1㊂整车骨架型钢使用多线段弹塑性材料模型MAT24来定义㊂发动机㊁变速器和部分悬架等实体单元使用刚体材料模型MAT20定义㊂轮胎等橡胶材料使用线弹性材料模型MAT1定义[13-14]㊂表1 两种钢材力学性能关键参数钢材屈服强度/MPa 抗拉强度/MPa 延伸率/%Q235/QSTE700246/704490/79836/161.3 边界条件和初始条件1)使用刚体模型定义刚性壁障和地面,刚性壁障与前围接触,静摩擦系数设为0.6,动摩擦系数设为0.5㊂地面与轮胎接触,静摩擦系数设为0.9,动摩擦系数设为0.1㊂032)车身骨架与各零部件之间的接触算法采用自动单面接触方式,以防止接触穿透㊂3)刚性墙与整车前围平行,初始距离为10mm,初始碰撞速度设置为30km /h㊂1.4 仿真结果及分析由仿真结果可知,随着碰撞时间的增加,前围骨架弯梁逐渐被压溃向后侵入,同时带动方向盘管柱也随之向后移动;同时车架弯曲幅度增大,导致驾驶员椅向前倾斜,直至方向盘边缘与驾驶员椅接触㊂图2为客车正面碰撞T =0.03s 和T =0.12s 时刻时的前部骨架部分变形图㊂T =0.03s 时刻时,驾驶区段车架开始出现向内弯曲现象;最大变形时刻T =0.12s 时,车头整体下沉严重,轮胎受压变形明显,前围骨架弯梁被压溃至与前围立柱平齐㊂因此,一旦发生碰撞,驾驶区生存空间持续减小,极易导致驾驶员受到挤压伤害㊂(a)T =0.03s (b)T =0.12s图2 碰撞不同时刻客车前部骨架变形对比通过仿真分析发现,整车碰撞过程中,冲击载荷主要作用于客车前部骨架结构,即通过前围骨架传递至侧围㊁顶盖㊁底架和车架前部㊂前围骨架㊁驾驶区段底架和车架为主要变形吸能区,前悬架之后的骨架塑性变形较小㊂2 结构改进及效果2.1 结构改进由前述仿真结果可知,驾驶区段局部骨架容易发生较大的弯曲变形,导致桁架结构失稳,严重影响驾驶区生存空间㊂因此,需要综合考虑前部结构刚度匹配和桁架结构的设计,改进思路如下:1)在车架前段增加吸能装置(如图3序号1位置)㊂吸能装置选择屈服强度较小的材料,使其在碰撞过程中先于车架发生屈服变形,合理设计吸能装置结构,并统筹考虑吸能装置与车架前段的刚度匹配,保证在碰撞最大变形时刻吸能装置能被完全压溃,实现其最大吸能效果,而此时车架前段产生最大弹性变形,达到即将屈服但未屈服的状态,使得大部分碰撞总能量都通过吸能装置与前段车架进行耗散㊂2)前围仪表台支撑弯梁壁厚由原来的2mm 更改为3mm,加强弯梁的刚度;弯梁与前围立柱连接位置增加加强板,防止连接部位发生弯折㊂在方向机管柱右侧增加斜撑(如图3序号2位置),与车架相连,碰撞时可以有效阻止方向机管柱向后侵入㊂3)驾驶区段上下两层骨架之间增加空间斜撑(如图3序号3位置),形成稳定的三角结构,防止骨架弯曲变形㊂4)优化驾驶区上层底架结构(如图4所示),将上层骨架纵梁改为大截面型钢,优化驾驶员椅侧骨架的型钢布局,减小局部应力集中㊂图3 客车前部部分骨架结构改进示意图图4 驾驶区上层底架结构改进示意图2.2 改进后效果改进后得到的最大变形时刻T =0.09s 的前部骨架变形情况如图5所示㊂与原始方案的最大变形量(如图2(b)所示)相比,改进后的驾驶区段骨架整体向下倾斜,驾驶区上层骨架未发生弯曲失稳㊂主要原因一是由于驾驶区段骨架刚度增大,上下两层之间的型钢形成稳定的三角结构,不易发生弯曲变形㊂二是因为改进后整车骨架吸收能量减少,整车内能增加量降低了约1.6e +02kJ(如图6所示),约占整车碰撞能量的1/3㊂该部分能量全部由吸能装置吸收耗散,吸能装置吸收能量变化曲线如图7所示㊂由于吸能装置的吸能作用,降低了整车碰撞能量,减弱了客车前部结构的碰撞冲击,导致碰撞总时间减少,使得提前0.03s,达到最大变形,同时整车最13 第1期 路 斌,任青文,张炳旭,等:客车前部结构正碰仿真与改进大变形量降低㊂另外,前围后侵入量减小,方向机管柱与方向盘均未触及驾驶员椅,驾驶区生存空间得到了有效改善㊂图5 改进后最大变形时刻(T =0.09s)的前部骨架图6 改进前后整车骨架内能变化曲线图7 吸能装置吸收能量变化曲线图在驾驶员椅腿处选取加速度测量点,得到改进前后该点的加速度变化曲线,如图8所示㊂由图可知,在前0.04s 的时间内,改进后测量点处的加速度值相比改进前的急剧减小,主要原因是此处由于吸能装置被压溃变形,起到了缓冲作用,从而快速降低整车动能㊂此外,加速度峰值与乘员二次伤害呈正相关㊂改进前测量点处的加速度峰值为-39g ,而改进后加速度峰值降为-34g ,减弱了对乘员的伤害㊂图8 改进前后加速度变化曲线在前围骨架和车架最前端位置分别选择测量点,测量该点在碰撞完成后与初始位置的距离,距离越小表明后侵入量越小,安全空间越大㊂同时测量方向盘边缘与驾驶员椅靠背㊁方向机管柱与驾驶员椅坐垫的最小水平距离,距离越大代表部件侵入量越小,安全空间越大㊂改进前后驾驶区生存空间相关参数见表2㊂由表2可知,改进后前围骨架侵入量减小37.9%,车架侵入量减小89.6%,驾驶区生存空间各项参数均优于原始方案㊂表2 改进前后最大变形时刻驾驶区生存空间对比侵入量/mm 安全距离/mm 前围车架方向盘管柱改进前/后422/26296/100/3060/1523 结束语本文基于有限元法对某客车以30km /h 的初始速度进行正面碰撞,开展仿真分析,并分别对前围骨架㊁驾驶区段骨架进行优化分析,提出改进方案,增大了驾驶区的生存空间,为客车前部骨架结构设计提供参考㊂参考文献:[1]朱守胜.基于事故树分析的营运客车交通安全风险研究[D].西安:长安大学,2016.[2]王若平,陈豫.基于LS-dyna 和HyperWorks 的大客车正面碰撞仿真分析[J].机械科学与技术,2014,33(3):419-422.[3]杨延功,张钦超,张立常,等.某11米全承载客车正面碰撞分析及结构优化[J].农业装备与车辆工程,2019,57(3):66-68.[4]畅世为.大客车正碰安全性及法规评价方法研究[D].长沙:湖南大学,2010.[5]贺志瑛.大客车正面碰撞安全性技术研究[D].西安:长安大学,2016.[6]彭旺,张雅鑫.客车正面碰撞仿真分析及性能优化[J].客车技术与研究,2019,41(4):9-11.[7]颜长征,王欣,赵东旭,等.客车正面碰撞乘员保护分析[J].机械研究与应用,2017,30(3):78-80.[8]张建,范体强,何汉桥.客车正面碰撞安全性仿真分析[J].客车技术与研究,2009,31(3):7-9.(下转第52页)开口尺寸误差控制在正公差1~2mm 以内,结构如图2(a)所示;,结构如图2(b)所示㊂ (a)C 型槽 (b)异形螺栓图2 C 型槽和异形螺栓结构示意图C 型槽和异形螺栓组合后的结构示意图如图3所㊂组合后C 型槽起着 限位”的作用,预埋固定时在C 型槽上施焊,避免了在固定螺栓上施焊㊂C 型槽采用普通碳钢,焊接性可靠㊂在C 型槽及异形螺栓设计时,根据装配过程中实际公差需求,通过调整C 型槽的深度可改变异形螺栓的偏转角度琢,来吸收车顶器件安装孔㊁固定螺栓位置度的偏差,从而实现了固定螺栓相对可调,对固定螺栓的垂直度不再有要求,降低了焊装作业难度的效果㊂同时固定螺栓的相对可调也降低了总装装配时的作业难度㊂图3 固定螺栓预埋结构改进后示意图3 结束语C 型槽及异形螺栓的设计避免了直接在固定螺栓上施焊,解决了螺栓与普通碳钢之间焊接性差的问题,且不再需要控制固定螺栓的垂直度,大大降低了焊装的作业难度㊂同时,固定螺栓的位置和角度由原来的不可调变成可调,也方便了总装的装配作业㊂目前这种工艺已被广泛应用㊂参考文献:[1]招国辉,马正培.大客车空调系统的安装与调试[J].客车技术与研究,2007,29(6):30-32.[2]周海涛,刘庚林,李德华.客车空调固定螺栓预埋工艺及控制方法[J].客车技术与研究,2009,31(5):46-47.[3]陶恩树.顶置空调引起的漏水问题分析及其解决措施[J].客车技术与研究,2005,27(2):28-29.[4]方栋,陈继志.高强度螺栓螺纹根部应力集中的有限元分析[J].材料开发与应用,2007,22(2):37-39.[5]霍立兴.焊接结构的断裂行为及评定[M].北京:机械工业出版社,2000:49-66.[6]陈祝年.焊接设计简明手册[M].北京:机械工业出版社,1997:992-1000.[7]韩志良,马红卫,丁燕君.高强度螺栓断裂失效分析[J].理化检验-物理分册,2003,39(9):477-480.[8]吴自龙.焊接和敲对空调固定螺栓强度影响的实验验证[J].客车技术,2018(4):43-44.收稿日期:2020-05-18(上接第32页)[9]曹立波,周登科,朱结,等.全承载式客车正面碰撞安全性的改进[J].汽车安全与节能学报,2015,6(1):58-65.[10]胡韶文,宋年秀,许津,等.基于LS DYNA 的汽车保险杠低速碰撞仿真研究[J].公路与汽运,2016(3):14-17.[11]许津,宋年秀,胡韶文,等.保险杠壁厚对低速碰撞性能的影响研究[J].公路与汽运,2016(5):4-6.[12]吴靖.基于承载式客车的正面碰撞性能仿真研究[J].汽车科技,2013(4):37-41.[13]黎勇,吴长风,蓝平辉.等.大客车正面碰撞结构耐撞性分析与改进[J].客车技术与研究,2017,39(1):10-13.[14]王开松,彭新宇,谢有浩,等.基于LS-dyna 的整车正面碰撞仿真分析及优化[J].安徽理工大学学报,2019,39(1):54-58.收稿日期:2020-06-29。
基于LSDYNA的汽车正碰分析

中图分类号:U467.1+4
0前言
在汽车被动安全性研究中,汽车碰撞是一个 十分复杂的力学问题,它是一个动态的大位移和 大变形的瞬态接触过程。接触和高速冲击载荷影 响碰撞的全过程,碰撞系统具有大位移、大转动 和大应变的非线性特征,以材料弹塑性变形为典 型特征的材料非线性和以接触摩擦为特征的接 触非线性的多重非线性特点。这些非线性物理陛 能的综合,使得利用传统的手段对汽车碰撞过程 的精确描述和求解变得非常复杂和困难。文中进 行的是汽车100%ODB正面碰撞的仿真分析。采 用动态显式非线性有限元技术,利用NX、ANSA、 LS.DYNA等有限元软件对某汽车进行几何建 模、网格建模和计算求解,依据计算结果分析了 汽车正面主要结构在碰撞中的耐撞性,并将计算 结果与试验结果进行对比,以验证仿真模型的准 确性。
1碰撞模型的建立
1.1汽车几何模型 建立汽车整车几何模型是进行有限元分析
的第一步,模型质量的好环对后续的有限元分析
·34·
文献标识码:A
起着至关重要的作用,直接决定有限元模型网格 的质量和分析时间的长短以及分析进展是否顺 利,尤其在碰撞分析中尤为突出。另外,在保证模 型正确及几何元素相关联的基础上,可以进行简 化,以达到事半功倍的效果。文中利用NX软件建 立某汽车整车的几何模型,该汽车三维几何模型 如图1所示。
[2]陈海树,赖征海,邸建卫.Ls—DYNA在汽车碰撞模拟过程 中的应用[J].沈阳大学学报,2006.
[3]何涛,杨竞.ANSYS/LS—DYNA非线性有限元分析实例指 导教程[M].机械工业出版社.
[4]张金换,杜汇良,马春生.汽车碰撞安全性设计[M].清华 大学出版社.
[5]Oaryl L.Logan.有限元方法基础教程[M].北京电子工业 出版社.
众泰某车型15kph正面碰撞cae分析
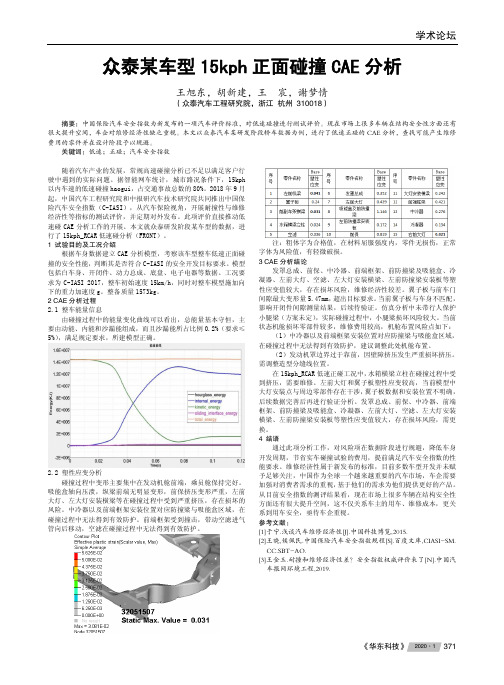
学术论坛371众泰某车型15kph 正面碰撞CAE 分析王旭东,胡新建,王 宸,谢梦情(众泰汽车工程研究院,浙江 杭州 310018)摘要:中国保险汽车安全指数为新发布的一项汽车评价标准,对低速碰撞进行测试评价。
现在市场上很多车辆在结构安全性方面还有很大提升空间,车企对维修经济性缺乏重视。
本文以众泰汽车某研发阶段轿车数据为例,进行了低速正碰的CAE 分析,查找可能产生维修费用的零件并在设计阶段予以规避。
关键词:低速;正碰;汽车安全指数随着汽车产业的发展,常规高速碰撞分析已不足以满足客户行驶中遇到的实际问题。
据智能网车统计,城市路况条件下,15kph 以内车速的低速碰撞haogui,占交通事故总数的80%。
2018年9月起,中国汽车工程研究院和中报研汽车技术研究院共同推出中国保险汽车安全指数(C-IASI),从汽车保险视角,开展耐撞性与维修经济性等指标的测试评价,并定期对外发布。
此项评价直接推动低速碰CAE 分析工作的开展。
本文就众泰研发阶段某车型的数据,进行了15kph_RCAR 低速碰分析(FRONT)。
1 试验目的及工况介绍根据车身数据建立CAE 分析模型,考察该车型整车低速正面碰撞的安全性能,判断其是否符合C-IASI 的安全开发目标要求。
模型包括白车身、开闭件、动力总成、底盘、电子电器等数据。
工况要求为C-IASI 2017,整车初始速度15km/h,同时对整车模型施加向下的重力加速度g。
整备质量1573kg。
2 CAE 分析过程2.1 整车能量信息由碰撞过程中的能量变化曲线可以看出,总能量基本守恒,主要由动能、内能和沙漏能组成,而且沙漏能所占比例0.2%(要求≤5%),满足规定要求,所建模型正确。
2.2 塑性应变分析 碰撞过程中变形主要集中在发动机舱前端,乘员舱保持完好。
吸能盒轴向压溃,纵梁前端无明显变形,前保挤压变形严重,左前大灯、左大灯安装横梁等在碰撞过程中受到严重挤压,存在损坏的风险。
- 1、下载文档前请自行甄别文档内容的完整性,平台不提供额外的编辑、内容补充、找答案等附加服务。
- 2、"仅部分预览"的文档,不可在线预览部分如存在完整性等问题,可反馈申请退款(可完整预览的文档不适用该条件!)。
- 3、如文档侵犯您的权益,请联系客服反馈,我们会尽快为您处理(人工客服工作时间:9:00-18:30)。
目录
1 分析目的和意义 (1)
2 使用软件说明 (1)
3 整车参数 (1)
3.1整车基本参数 (1)
3.2有限元基本参数 (2)
3.3边界条件定义 (3)
4 正面100%刚性壁障碰撞分析结果 (4)
4.1能量检查 (4)
4.2全局技术指标 (5)
4.3整车变形情况 (6)
4.4前纵梁变形情况 (7)
4.5B柱下方加速度 (9)
4.6A柱侵入量 (9)
4.7转向管柱侵入量 (10)
4.8踏板侵入量 (11)
4.9前围板侵入量 (11)
5 总结 (12)
6 误差分析 (12)
1 分析目的和意义
在车辆的设计阶段进行车辆的碰撞仿真模拟,可以将车辆所需要的碰撞性能考虑在结构设计中,为顺利通过实车碰撞试验做一些先导性的工作,同时碰撞性能是国家相关安全标准所强制要求,准确的模拟碰撞过程,并将结果反馈设计部门,做好车辆的碰撞安全设计是出于对驾乘人员安全的考虑,同时,优秀的车辆碰撞性能也是车辆占有市场的重要的技术资本。
2 使用软件说明
在本次模拟中,主要使用了HYPERMESH前处理软件和LS-DYNA求解器,HYPERMESH是世界领先的、功能强大的CAE前处理软件,由ALTIAR公司开发,目前在世界上的应用非常广泛。
HYPERMESH具有强大的有限元网格前处理功能,并且与众多的主流CAE求解器具有良好的接口。
LS-DYNA是一款功能强大的显式通用分析有限元程序,可以求解各种二维、三维非线性结构的高速碰撞、爆炸和金属成型等非线性问题。
3 整车参数
3.1 整车基本参数
QQ基本参数如下所示:
表1 Q基本尺寸
3.2 有限元基本参数
本次根据项目组提供的Q整车数模、零部件明细表及质量、材料特性等数据进行CAE 分析,考察整车100%正面刚性壁障碰撞安全性能。
使用的主要材料有DC01、DC03、BLD、20#、B340/590DP、BUSD、ABS、PP等。
模型基本参数如下:
表格2 Q 有限元模型信息
图1 整车有限元模型
300m
图2 压溃空间计算: Crashable Space300mm
图3 白车身板材厚度分布(mm)
图4 开闭件板材厚度分布(mm)
3.3 边界条件定义
km/的速度与固定刚性障碍壁表面垂直相撞。
在本次模拟中,撞击接试验车辆以50h
km/(沿x轴负向),碰撞角即垂直于壁障前表面触方式为刚性墙,碰撞时速度为50 h
的直线与车辆纵向行进方向线之间的夹角为0度,同时对整车模型施加向下的重力加速度g=9.812
/s
m,如下所示:
图5 QQ 正面碰撞模型
4 正面100%刚性壁障碰撞分析结果 4.1 能量检查
碰撞过程中能量的变化以及质量增加情况是评价模型是否正确的重要指标。
表格 3 能量检查
图6 能量曲线
正碰刚性壁障
图7 质量增加曲线
4.2 全局技术指标
刚墙反力曲线反映碰撞过程中刚墙受冲击力的大小,同时也可以看出整车加速度的变化情况,如果刚性墙反力峰值过大,可能会导致车架乃至整车加速度过大,这对于乘员的保护是不利的。
刚性墙最大反力为488KN,在35ms左右处出现,如下所示:
图8 刚性墙反力时间历程曲线
要满足碰撞法规试验的要求,从技术指标上来讲,就是使车体的碰撞性能及乘员的损伤指标都在一定的限制范围以内。
其中,乘员头部、胸部等的碰撞加速度受车体碰撞加速度的影响较大。
在生产实际中,降低车体碰撞加速度是设计需要重点考虑的一个方面。
整车加速度峰值为40 g。
图9 整车加速度时间历程曲线
4.3 整车变形情况
碰撞模拟过程中各个时段的变形情况可以反映出整车在碰撞过程中的变形情况,0ms、20ms、40ms、60ms、80ms整车碰撞变形如下所示:
图10 0ms整车碰撞变形情况
图11 20ms整车碰撞变形情况
图12 40ms整车碰撞变形情况
图13 60ms整车碰撞变形情况
图14 80ms整车碰撞变形情况
4.4 前纵梁变形情况
碰撞过程中,前纵梁吸收了碰撞的大部分能量,为主要吸能部件,其变形情况如下:
图15 0ms前纵梁变形情况
图16 20ms前纵梁变形情况
图17 40ms前纵梁变形情况
图18 60ms前纵梁变形情况
图19 80ms前纵梁变形情况
4.5 B柱下方加速度
B柱下方加速度在碰撞过程中最能反应假人加速度状态,直接影响假人碰撞过程中的各项伤害值,是整车碰撞安全性能优化的重要指标。
其峰值分别为39.5g 39.8g。
图20 B柱下端加速度曲线
4.6 A柱侵入量
在纵向冲击力的作用下,A柱主要承受与车辆坐标系XZ平面平行的纵向冲击力的作用,主要表现为纵向压缩的状况。
图21 A柱侵入量测量示意图
如图21所示,取门框上中下三处参考点,分别测出左右侧的AB柱间距变化量,来判断A柱侵入程度。
图22 左侧A柱侵入量
图23 右侧A柱侵入量
A柱侵入量总结:
表4 A柱侵入量/mm
4.7 转向管柱侵入量
转向管柱向上向后移动量过大,可能导致驾驶员头部、胸部等的伤害增加。
图24 转向管柱侵入量测量示意图
图25 转向管柱向上向后侵入量
转向管柱侵入量总结:
表5 转向管柱侵入量
4.8 踏板侵入量
在正面碰撞过程中,踏板侵入过大可能增加假人大腿、小腿、脚踝等的伤害。
图25 踏板侵入量
踏板侵入量总结:
表6 踏板侵入量
4.9 前围板侵入量
在正面碰撞中,前围的侵入是造成假人胸部、腹部以及大腿受到伤害的重要原因之一,
如果侵入量过大,则可能导致这些部位伤害过大。
Q前围最大侵入量为139.5mm。
图26 前围侵入量位移图
5 总结
本文根据提供Q数据,进行了该车的正面100%刚性壁障碰撞安全性能分析,在分析过程中,严格按照项目组提供的数据,真实反映了实车的结构形式,根据项目组提供的材料特性、密度、质量设置参数等进行计算。
表7 总结
6 误差分析
由于如下原因,分析存在误差:
A.材料参数获取的实验误差;
B.实际整车金属部件在成型加工过程中由于形状、表面积等的变化,存在局部材料特性
与厚度的变化;
C.其他输入数据误差;
D.CAE分析计算误差。