美军技术标准MIL-PRF-38534-RevE
美国军用标准
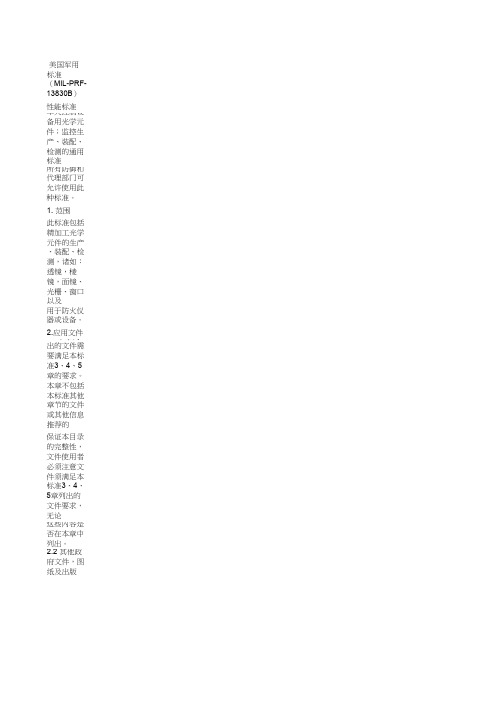
美国军用标准(MIL-PRF-13830B)性能标准军火控制设备用光学元件;监控生产、装配、检测的通用标准所有防御和代理部门可允许使用此种标准。
1. 范围1.1 范围。
此标准包括精加工光学元件的生产、装配、检测,诸如:透镜,棱镜,面镜、光栅、窗口以及用于防火仪器或设备。
2.应用文件2.1本章列出的文件需要满足本标准3、4、5章的要求。
本章不包括本标准其他章节的文件或其他信息推荐的文件。
为了保证本目录的完整性,文件使用者必须注意文件须满足本标准3、4、5章列出的文件要求,无论这些内容是否在本章中列出。
2.2 其他政府文件,图纸及出版下列政府其他文件、图纸和出版组成本文件内容的一部分,扩大本文的范围。
除非另有规定,这些文件、图纸和出版是征求引用的。
图纸 C7641866---光学元件表面质量标准(立约人要求的其他政府文件、图纸、出版复印件及具体的功能应该从签约事宜或签约指示得到。
)2.3 优先顺序本标准内容与其引出的参考有冲突时,以本标准内容为准。
本标准未述内容,可行法律法规代行除非有具体的免除通知。
(看附加有限标准合同条令)3.要求:3.1所有的光学元件,配件以及系统产品都必须符合这一标准的要求,除非具体的仪器标准或合同之可行图纸另有要求与定义。
3.2所用的材料也必须与图纸的说明以及使用文件的标准相一致3.2.1玻璃光学元件在规格,以及级别必须与图纸要求相一致。
允许使用玻璃材料时,应提供给合同管理人员相关的玻璃光学特性及设计数据完整的信息。
3.2.1.1 放射性材料本文中要求的光学材料应不含钍或其他加入的超过0.05%重量的放射性材料。
3.2.2 粘着力除非合同和定单中有特殊说明,光学粘合剂必须同附录A的要求相一致。
3.2.3 粘连材料对于玻璃同金属相粘连,必须与附录D的要求相一致3.2.4密封材料用于密封的材料必须与附录E的要求相一致3.2.5 增透膜用于光学表面镀膜的增透膜必须与附录C的要求相一致3.2.5.1 反射表面铝化反射面必须与附录B的要求相一致3.3机械尺寸大小光学元件必须与合同以及图纸的要求的尺寸和光学数据相一致3.3.1边所有光学元件都应当倒边在(0.020-0.005英寸在45度+/-15度),沿面宽进行测量,除非有特殊指定。
舰船中压配电设备美军标研究

舰船中压配电设备美军标研究杨青(海军驻上海711所军事代表室,上海201108)摘要:对舰船中压配电设备美军标的概况进行了分析;对中压交流配电板、中压交流真空断路器、中压交流真空断路器用保护继电器等美军标进行了研究;并结合相 关产品的情况,得出了舰船中压配电设备美军标的技术特点,提出了我国舰船中压配 电设备标准化的建议。
可为我国舰船中压配电设备研制和标准化工作提供参考。
关键词:中压;配电设备;舰船;M IL 标准中图分类号:TM 64文献标志码:A 文章编号:2095-8188(2017)06-0083-06D O I : 10.16628/j. cnki. 2095-8188. 2017. 06. 016Research on American Military Standards for MediumVoltage Electrical Distribution Equipment on ShipsYANG Qing(Naval Representatives Office at No . 711 Research Institute , Shanghai 201108, China )Abstract : The general profile of American military standards for medium voltage electrical distributionequipment on ships was introduced, and American military standards for medium voltage switchgear, medium voltage AC vacuum circuit breaker and its protection relay were analyzed. Combined with the status of corresponding products, after the technical features of American military standards for medium voltage electrical distribution equipment are summarized, the suggestions for developing Chinese standards for medium voltage electrical distribution equipment on ships were proposed, which would provide reference for the design, manufacture and standardization of medium voltage electrical distribution equipment on ships in China.Key words : medium voltage ; electrical distribution equipment ; ship ; military standard杨青(1967—),男,高级工程师,博 士,主要从事舰船 电力系统和电气设 备方面的工作。
美国军用标准MIL

美国军⽤标准MIL柔性可热封静电防护材料特性规范美国军⽤标准MIL-PRF-81705D上海防静电⼯业协会王福良译本规范已批准⽤于军队的所有部门与国防部承包商。
1 范围1.1范围本规范建⽴了⼀套军⽤微电路、敏感半导体器件,敏感电阻和相关⾼档部件的柔性可热封静电防护包装材料的要求。
另外I型材料可提供防⽔防电磁辐射的性能(见6.1)。
1.2分类防护材料有以下三种类型:I类防⽔、防静电、静电屏蔽和电磁屏蔽。
1型⽆使⽤限制。
2型仅适⽤于⾃动制袋机。
II类透明、防⽔、静电耗散型。
1型⽆使⽤限制。
2型仅适⽤于⾃动制袋机。
III类透明、防⽔、防静电、静电屏蔽。
1型⽆使⽤限制。
2型仅适⽤于⾃动制袋机。
2 应⽤⽂件2.1 概述本节列出的⽂件由本规范第3、4节作出详细规定与说明。
本节所列⽂件不包括本规范其他章节引⽤的⽂件或附加建议的信息和例⼦。
尽管已努⼒做到确保所列⽂件的完整性,但⽂件使⽤者应注意必须满⾜本规范第3、4节所规定的要求。
不管它们是否已被列⼊表中。
2.2 政府⽂件2.2.1 规范、标准和⼿册下⾯的规范、标准和⼿册是本⽂件的组成部分。
除⾮另有规定,这些已列⼊国防部规范,标准和附录索引的⽂件均可被引⽤。
规范联邦⽂件QQ-S-698 ⽚状和条状低碳钢QQ-A-250/4 铝合⾦、板状和⽚状标准FED-STD-101 包装材料的测试程序2.3 ⾮政府出版物下列⽂件是本规范的扩展部分。
除⾮另有规定,国防部已采⽤的列⼊索引的⽂件可以被引⽤,没被列⼊索引的要求可参见6.2。
ANSI(美国国家标准协学会)J-STD-006焊料合⾦等级,有助焊剂和⽆助焊剂。
固体焊料应⽤要求。
ASQC(美国质量协会)ASQC-Z1.4 程序,检验抽样表(国防部已采⽤)ASTM-B451 ⽤于印刷板的铜箔,铜棒,铜⽚和传送带规范ASTM-D257 绝缘材料的直流电阻或传导率(国防部已采⽤)ASTM-F15 铁-镍-钴封焊合⾦规范ASTM(美国试验与材料协会)EIA(电⼦⼯业协会)EIA-541 静电敏感物体的包装材料标准2.4 优先权当本⽂件与引⽤的参考⽂件发⽣⽭盾时,则本⽂件优先。
国外军用电子元器件质量等级与国内对应一览表
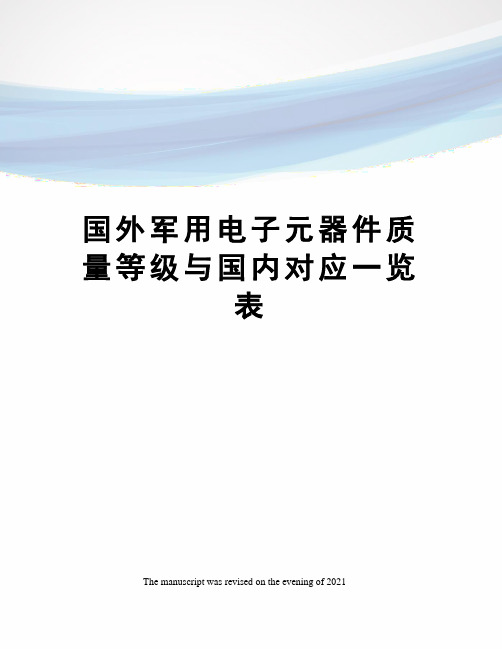
国外军用电子元器件质量等级与国内对应一览表The manuscript was revised on the evening of 2021国外军用电子元器件质量等级与国内对应一览表为了保证元器件的质量,我国制定了一系列的元器件标准。
在上世纪70年代末期制定了“七专”7905技术协议和80年代初制定了“七专”8406技术协议,已具备了军用器件标准的雏形,但标准是在改革开放之前制定的,有很多局限性,很难与国际接轨。
从80年代开始,我国标准化部门参照了美国军用标准(MIL)体系建立了GJB 体系,元器件的标准有规范、标准、指导性文件等三种形式。
一、国内军用元器件质量分级二、美国军标质量等级体系:MIL-PRF-19500半导体器件试验总规范(依次低→高等级)单片微电路规范(依次低→高等级)B-2级:不完全符合MIL-STD-883的节的要求,并按照政府批准文件,包括卖方等效的B级要求进行采购。
B-1级:完全符合MIL-STD-883(微电子器件试验方法和程序)的节所要求,并按照标准军用图样(SMD – Standard Microcicuit Drawing),国防电子供应中心(DESC –DefenceElectronic Supply Center)图样或政府批准的其它文件进行采购。
即通常称883级,器件上有5962 – xxx号。
S-1级:完全按照MIL-STD-975(NASA标准的电子电气和机电源器件目录)或MIL-STD-1547(航天飞行器和运载火箭用元器件、材料和工艺技术要求)进行采购,并有采购机关的规范批准。
MIL-PRF-38534D混合集成电路规范(依次低→高等级)电阻、电容、电感元件 MIL 标准中有可靠性指标的元件失效等级分五级MIL 标准中有可靠性指标的失效率等级和失效率的对应关系三、欧空局元器件半导体分立器件:ESA/SCC(Europe SpaceAgency/Space Componet Cooperation)5000标准试验等级:B级、C级(从高到低)批接收等级:1级、2级、3级(从高到低)微电路:ESA/SCC(Europe SpaceAgency/Space Componet Cooperation)9000标准试验等级:B级、C级(从高到低)批接收等级:1级、2级、3级(从高到低)电阻、电容、电感器件:ESA/SCC(Europe SpaceAgency/Space Componet Cooperation)3000和4000标准试验等级:B级、C级(从高到低)批接收等级:1级、2级、3级(从高到低)四、国外军用元器件与我国军用元器件质量等级对应关系半导体分立器件质量等级对应关系微电路质量对应等级阻容电感失效率等级对应参考来源:融融网及网络资料。
【应知概念】mil-prf-38535k中的质量等级

【应知概念】mil-prf-38535k中的质量等级1. 引言1.1 概述本文旨在介绍mil-prf-38535k中的质量等级。
随着电子技术的发展和应用领域的扩大,对电子元器件质量的要求越来越高。
而mil-prf-38535k作为一项国际公认的质量标准,对于确保电子元器件在各类应用中的可靠性和稳定性具有重要意义。
因此,了解mil-prf-38535k中不同质量等级的定义、分类以及其在实际应用中的重要性是非常必要且有益的。
1.2 文章结构本文主要分为引言、mil-prf-38535k中的质量等级、结论三个部分。
引言部分将对文章进行概述,介绍本文撰写目的并提供整体文章结构框架。
第二部分将详细探讨mil-prf-38535k中的质量等级,包括其定义与分类、重要性以及应用领域等方面内容。
第三部分将总结各个质量等级特点和应用场景,并对mil-prf-38535k中质量等级进行评价与展望。
1.3 目的本文旨在帮助读者全面了解mil-prf-38535k中的质量等级,从而加深对该标准的认识和理解。
通过详细介绍每个质量等级的特点、要求、适用范围以及质量控制措施和测试标准等关键内容,读者可以更好地选择合适的质量等级,并在实际应用中确保电子元器件的性能和可靠性。
同时,本文也旨在为mil-prf-38535k 标准提供评价与展望,以促进质量等级的持续改进和发展。
2. mil-prf-38535k中的质量等级2.1 什么是mil-prf-38535k?mil-prf-38535k是一种军用电子元器件标准,由美国国防标准化委员会(DSCC)制定和管理。
它涉及到电子元器件的生产和测试,并确保它们能够满足军事需求的特定要求。
这个标准定义了不同质量等级,并对每个等级规定了相关的要求和测试标准。
2.2 质量等级的定义和分类mil-prf-38535k标准中定义了五个不同的质量等级,分别为:一、二、三、四和S。
每个等级都具有不同的要求,用于区分元器件的质量水平。
mil-prf-8805标准

一、介绍mil-prf-8805标准mil-prf-8805标准是美国国防部颁布的一项军用产品规范标准,旨在保证军用产品的质量和可靠性,确保其能够在特殊条件下正常工作。
该标准适用于航空航天领域的各类设备和零部件,其要求严格而全面,被广泛应用于军工行业。
二、mil-prf-8805标准的内容根据mil-prf-8805标准的规定,产品必须符合一系列严格的指标和测试要求,包括但不限于以下几个方面:1. 材料和制造工艺要求:对产品所采用的材料以及制造工艺有着详细的规定,确保产品的质量和可靠性。
2. 性能要求:产品在各种特殊环境下的性能表现有着具体的测试要求,包括温度、湿度、振动、冲击等方面。
3. 可靠性和耐久性要求:标准中对产品的可靠性和耐久性有着具体的要求,包括寿命测试、可靠性评估等。
4. 安全性要求:产品必须符合相应的安全标准,确保不会对使用者造成伤害。
三、mil-prf-8805标准对军工行业的影响mil-prf-8805标准的制定和执行,对军工行业有着积极的促进作用:1. 保障产品质量:标准的严格要求确保了军用产品的质量和性能稳定,使其能够在特殊条件下正常工作。
2. 促进产业升级:产品必须符合标准要求,要求生产企业不断提升技术和制造工艺水平,推动了产业的升级和发展。
3. 提升国防实力:优质的军用产品是国防实力的重要组成部分,mil-prf-8805标准的执行有助于提升国防实力和军事装备的先进程度。
四、mil-prf-8805标准的国际应用除了在美国国防部内部广泛应用外,mil-prf-8805标准在国际上也产生了一定的影响:1. 吸引外国企业合作:美国军工企业生产的产品必须符合mil-prf-8805标准,这也带动了国外企业与其合作,提高了产品的全球竞争力。
2. 影响国际标准制定:mil-prf-8805标准的制定和执行情况,也会对其他国际标准的制定产生一定的影响和借鉴作用。
五、mil-prf-8805标准的未来发展趋势随着科技的不断进步和军事需求的不断变化,mil-prf-8805标准也在不断进行更新和完善,未来的发展趋势可能包括但不限于以下几个方面:1. 加强对新材料和新工艺的规定:随着新材料和新工艺的不断涌现,标准可能需要对其进行适时的调整和规定,以确保产品的质量和可靠性。
MIL美国军用标准2010年最新目录

MIL美国军用标准标准2010年最新标准目录以下MIL美国标准化组织标准信息只供参考,具体情况,请咨询--中国标准信息网MIL-PRF-22684/8C (1) 2009.02.05 RESISTORS, FIXED, FILM, INSULATED, STYLE RL42鈥?TXMIL-PRF-19500/483D 2009.04.02 SEMICONDUCTOR DEVICE, SILICON, HIGH-POWER, THREE PHASE, FULL WAVE B RIDGE RECTIFIER, TYPES M19500/483-01 THROUGH M19500/483-04, JANTXMIL-PRF-27/111A 2009.09.29 TRANSFORMERS AND INDUCTORS, (AUDIO, POWER AND HIGH-POWER PULSE) INDU CTOR, AUDIOMIL-PRF-19500/169N 2009.11.02 SEMICONDUCTOR DEVICE, DIODE, SILICON, SWITCHING,TYPES 1N3070, 1N3070-1, 1N3070UR-1, 1N4938, 1N4938-1, 1N4938UR-1, JAN, JANTX, JANTXV, JANHC, AND JANKCMIL-PRF-27/79A 2009.11.09 TRANSFORMERS, AUDIO FREQUENCYMIL-DTL-3943/129C 2010.01.08 DECORATION, EXCEPTIONAL ENGINEERING ACHIEVEMENT MEDAL, NASAMIL-DTL-3943/145D 2010.01.15 DECORATION, MERITORIOUS CIVILIAN SERVICE AWARD, DEFENSE INFORMATION S YSTEMS AGENCYMIL-DTL-3943/139C 2010.01.26 DECORATION, NATIONAL COMMUNICATI***** SYSTEMS MEDALMIL-DTL-3943/153B 2010.01.15 DECORATION, SPECIAL ASSIGNMENT AWARD, U.S. PUBLIC HEALTH SERVICEMIL-DTL-3943/186A 2010.03.26 MEDAL, ARMY OF CUBAN OCCUPATIONMIL-PRF-55629/5G 2010.03.10 CIRCUIT BREAKERS, MAGNETIC, UNSEALED TRIP-FREE, THREE POLE (0.2 TO 50 A MPERES)MIL-DTL-11589/493A 2010.04.30 RIBBON, EXCEPTIONAL CIVILIAN SERVICE AWARD, CIVILIAN PERSONNEL MANAGE MENT SERVICE, DEPARTMENT OF DEFENSEMIL-DTL-3943/138D 2010.01.08 DECORATION, EXCEPTIONAL ACHIEVEMENT MEDAL, NASAMIL-DTL-11484/80E 2008.09.30 LAPEL BUTTON, DISTINGUISHED SERVICE AWARD, DEFENSE CONTRACT AUDIT AG ENCYMIL-DTL-11589/583 2003.03.20 RIBBON, EXCEPTIONAL ADMINISTRATIVE ACHIEVEMENT MEDAL, NASAMIL-PRF-914/4B (3) 2010.02.05 RESISTOR NETWORK, FIXED, FILM, SURFACE MOUNT, 20-PIN, LEADLESS CHIP CA RRIER, NONESTABLISHED RELIABILITY AND ESTABLISHED RELIABILITY, STYLE RNS040ARMY MIL-PRF-32271/14 2008.10.30 BATTERY, NON-RECHARGEABLE, LITHIUMMIL-PRF-62546C 2010.01.26 SENSOR, FIRE, OPTICALMIL-DTL-3922/62D 2010.01.08 FLANGES, WAVEGUIDE (CHOKE) (ROUND, 8 HOLE (2 HOLES CENTERED HORIZONTA LLY, 2 HOLES CENTERED VERTICALLY))MIL-DTL-8878K (1) 2009.02.17 TURNBUCKLES, POSITIVE SAFETYING, GENERAL SPECIFICATION FORMIL-DTL-21617/27 VALID NOTICE 1 2008.04.30 Connector, Female Plug Electrical, Rectangular, Polarized Shell, Miniature Type, Mixed Socket Contacts (Style 016C)MIL-M-38510/123B VALID NOTICE 1 2009.02.26 Microcircuits, Linear, Cmos, Negative Logic, Analog Switch, Monolithic SiliconMIL-PRF-19500/624D 2009.06.18 SEMICONDUCTOR DEVICE, DARLINGTON TRANSISTOR, NPN, SILICON, HIGH-POWE R, TYPE 2N7370, JAN, JANTX, JANTXV, AND JANSDOD-A-15707D (2) 1989.01.25 ANCHORS, NAVY, LIGHTWEIGHT TYPE (METRIC)DOD-A-17254A 1985.08.23 ANCHORS, NAVY, LIGHTWEIGHT (HADFIELD MANGANESE CAST STEEL LOW MAGNETIC PERMEABILITY) (METRIC)DOD-A-82720 NOTICE 3 2004.11.23 ADHESIVE, MODIFIED-EPOXY, FLEXIBLE, TWO-PART (METRIC)DOD-C-2687B VALID NOTICE 1 1987.06.02 COMPOUND, BATTERY-SEALING (METRIC)DOD-C-82656 (2) 1978.11.15 CARBON BLACK,THERMALMIL-C-82656 1977.01.31 CARBON BLACK,THERMALDOD-C-82660 (1) 1978.03.01 CHROMIUM 2 ETHYL HEXOATE, TECHNICALMIL-C-82660 1977.01.31 CHROMIUM 2 ETHYL HEXOATE, TECHNICALDOD-C-82665 (1) 1978.11.15 CARBON BLACKMIL-C-82665 1977.01.31 CARBON BLACKDOD-D-23443B (2) 1995.10.27 DI-(2-ETHYLHEXYL) ADIPATE, TECHNICAL (METRIC)DOD-E-8983C VALID NOTICE 1 1992.09.04 ELECTRONIC EQUIPMENT, AEROSPACE, EXTENDED SPACE ENVIRONM ENT, GENERAL SPECIFICATION FORDOD-G-24508A (4) 1998.09.23 GREASE, HIGH PERFORMANCE, MULTIPURPOSE (METRIC)DOD-G-82673 (1) 1978.06.15 GRAPHITE, NATURAL, POWERED, TECHNICALMIL-G-82673 1977.11.23 GRAPHITE, NATURAL, POWERED, TECHNICALDOD-L-25681D VALID NOTICE 2 1991.05.01 LUBRICANT MOLYBDENUM DISULFIDE, SILICONEDOD-L-81846B (2) 2000.03.02 LUBRICATING OIL, INSTRUMENT, BALL BEARING, HIGH FLASH POINTMIL-P-63464/6B VALID NOTICE 1 2005.07.01 PIN, GROOVED, HEADLESS-LONGITUDINAL CENTER GROOVE, CORRO SION-RESISTANT STEEL, METRICMIL-P-63464/6B 1992.01.17 PIN, GROOVED, HEADLESS-LONGITUDINAL CENTER GROOVE, CORROSION-RESISTANT STEEL, METRICDOD-R-23679F 1986.08.08 REAGENTS, STANDARD, WATER TEST CHEMICALS (METRIC)DOD-STD-1399 -301A 1986.07.21 INTERFACE STANDARD FOR SHIPBOARD SYSTEMS SECTION 301A SHIP MOTION AND ATTITUDE (METRIC)DOD-T-17412C 1978.09.20 TEST KIT, WATER, ENGINE COOLING SYSTEMS (METRIC)DOD-T-82666A VALID NOTICE 1 1987.05.13 TRIS-1-(2 METHYL AZIRIDINYL) PHOSPHINE OXIDEDOD-Z-82674 NOTICE 1 1999.07.10 ZIRCONIUM CARBIDE, POWERED, TECHNICALMIL-Z-82674 1977.11.23 ZIRCONIUM CARBIDE, POWERED, TECHNICALMIL-A-159D VALID NOTICE 1 1999.07.14 ANTIMONY SULFIDE (FOR USE IN AMMUNITION)MIL-A-159D 1972.05.16 ANTIMONY SULFIDE (FOR USE IN AMMUNITION)MIL-A-166C VALID NOTICE 2 1999.07.13 AMMONIUM PICRATE (EXPLOSIVE D)MIL-A-166C 1975.01.06 AMMONIUM PICRATE (EXPLOSIVE D)MIL-A-192B VALID NOTICE 2 1999.08.18 AMMONIUM PERCHLORATEMIL-A-192B 1965.09.02 AMMONIUM PERCHLORATEMIL-A-417G VALID NOTICE 1 1988.10.24 ADAPTER, PRIMING, M1A4MIL-A-417G 1983.02.27 ADAPTER, PRIMING, M1A4MIL-A-516J 1981.09.01 AUGER, EARTH, SKIDMOUNTED; AND AUGER, EARTH, TURNTABLE BASE MOUNTED, POWE R DRIVENMIL-A-2334J 1991.03.15 APRON, TOXICOLOGICAL AGENTS PROTECTIVE, M-2MIL-A-3316C (2) 1990.08.23 ADHESIVES, FIRE-RESISTANT, THERMAL INSULATIONMIL-A-3316C 1987.10.20 ADHESIVES, FIRE-RESISTANT, THERMAL INSULATIONMIL-A-3850 VALID NOTICE 1 1986.04.10 ACETYLENE BLACKMIL-A-3850 1952.12.24 ACETYLENE BLACKMIL-A-3962E 1986.05.19 ANCHORS, GROUND, ARROWHEAD WITH DRIVING EQUIPMENTMIL-A-5034B VALID NOTICE 1 1987.03.02 ADAPTER, BOMB RACK, 30 INCH, AERO 1AMIL-A-5034B 1979.11.02 ADAPTER, BOMB RACK, 30 INCH, AERO 1AMIL-A-6752A REINST NOTICE 2 1978.03.01 AMMETERS, VOLTMETERS, AND LOADMETERS; DIRECT CURRENTMIL-A-6752A (3) 1958.03.03 AMMETERS, VOLTMETERS, AND LOADMETERS; DIRECT CURRENTMIL-A-6752A 1953.12.24 AMMETERS, VOLTMETERS, AND LOADMETERS; DIRECT CURRENTMIL-A-6848 VALID NOTICE 1 1955.12.06 ACCELEROMETER; AIRCRAFTMIL-A-6848 1950.08.21 ACCELEROMETER; AIRCRAFTMIL-A-7237B (1) 1981.05.19 AIR INDUCTION SYSTEM, RECIPROCATING ENGINE, GENERAL SPECIFICATION FOR MIL-A-7237B 1975.02.04 AIR INDUCTION SYSTEM, RECIPROCATING ENGINE, GENERAL SPECIFICATION FORMIL-A-7647C VALID NOTICE 2 1971.10.12 AIR CONDITIONER, TRAILER MOUNTED, FREON CYCLE, GASOLINE ENGI NE DRIVEN, 4 TON REFRIGERATING CAPACITY, TYPE A-3MIL-A-7647C 1958.08.22 AIR CONDITIONER, TRAILER MOUNTED, FREON CYCLE, GASOLINE ENGINE DRIVEN, 4 TO N REFRIGERATING CAPACITY, TYPE A-3MIL-A-8625F (1) 2003.09.15 ANODIC COATINGS FOR ALUMINUM AND ALUMINUM ALLOYSMIL-A-8625F 1993.09.10 ANODIC COATINGS FOR ALUMINUM AND ALUMINUM ALLOYSMIL-A-8860B 1987.05.20 AIRPLANE STRENGTH AND RIGIDITY, GENERAL SPECIFICATION FORMIL-A-8861B (1) 1994.12.05 AIRPLANE STRENGTH AND RIGIDITY FLIGHT LOADSMIL-A-8861B 1986.02.07 AIRPLANE STRENGTH AND RIGIDITY FLIGHT LOADSMIL-A-8863C 1993.07.19 AIRPLANE STRENGTH AND RIGIDITY GROUND LOADS FOR NAVY ACQUIRED AIRPLANES MIL-A-8865B 1987.05.20 AIRPLANE STRENGTH AND RIGIDITY MISCELLANEOUS LOADSMIL-A-8866C VALID NOTICE 1 1994.10.03 AIRPLANE STRENGTH AND RIGIDITY RELIABILITY REQUIREMENTS, REPEATED LOADS, FATIGUE AND DAMAGE TOLERANCEMIL-A-8866C 1987.05.20 AIRPLANE STRENGTH AND RIGIDITY RELIABILITY REQUIREMENTS, REPEATED LOADS, FA TIGUE AND DAMAGE TOLERANCEMIL-A-8867C VALID NOTICE 1 1994.10.03 AIRPLANE STRENGTH AND RIGIDITY GROUND TESTSMIL-A-8867C (1) 1993.03.25 AIRPLANE STRENGTH AND RIGIDITY GROUND TESTSMIL-A-8867C 1987.06.10 AIRPLANE STRENGTH AND RIGIDITY GROUND TESTSMIL-A-8869B VALID NOTICE 1 1994.06.20 AIRPLANE STRENGTH AND RIGIDITY NUCLEAR WEAP***** EFFECTSMIL-A-8869B 1987.05.20 AIRPLANE STRENGTH AND RIGIDITY NUCLEAR WEAP***** EFFECTSMIL-A-8870C 1993.03.25 AIRPLANE STRENGTH AND RIGIDITY VIBRATION, FLUTTER, AND DIVERGENCEMIL-A-9132 1953.11.02 AMPLIFIER, STABILIZATION, BOMBING NAVIGATIONAL COMPUTER, TYPE B-1MIL-A-9207B (1) 1956.04.20 ANALYZER, IGNITION AND VIBRATION, AIRCRAFT RECIPROCATING ENGINEMIL-A-9207B 1955.10.12 ANALYZER, IGNITION AND VIBRATION, AIRCRAFT RECIPROCATING ENGINEMIL-A-9410 (1) 1954.06.18 ANTENNAS, FM COMMUNICATION EQUIPMENT, GENERAL SPECIFICATION FOR DESIGN AND PLACEMENT OFMIL-A-9410 1954.04.05 ANTENNAS, FM COMMUNICATION EQUIPMENT, GENERAL SPECIFICATION FOR DESIGN AN D PLACEMENT OFMIL-A-9457A (1) 1959.04.27 AMPLIFIER, ELECTRONIC CONTROL, BOMBING NAVIGATIONAL COMPUTER, TYPE MD-1 MIL-A-9457A 1959.04.27 AMPLIFIER, ELECTRONIC CONTROL, BOMBING NAVIGATIONAL COMPUTER, TYPE MD-1 MIL-A-10516 1950.09.14 ADAPTER, SKATE TEST CLUSTER (100-LB. SIZE)MIL-A-10593A 1953.02.04 AIR SAMPLER MX-1191 ( )/TDQ-1MIL-A-10982F (1) 1969.04.01 ARMING WIRE ASSEMBLIESMIL-A-10982F 1968.08.19 ARMING WIRE ASSEMBLIESMIL-A-11221A NOTICE 2 1997.02.27 ARMING PLUG, MINE, ANTITANK M4 (PRACTICE) AND M4A1MIL-A-11221A VALID NOTICE 1 1988.05.20 ARMING PLUG, MINE, ANTITANK M4 (PRACTICE) AND M4A1MIL-A-11221A (2) 1964.02.14 ARMING PLUG, MINE, ANTITANK M4 (PRACTICE) AND M4A1MIL-A-11221A 1962.02.22 ARMING PLUG, MINE, ANTITANK M4 (PRACTICE) AND M4A1MIL-A-11356F 1987.05.22 ARMOR, STEEL, CAST, HOMOGENEOUS, COMBAT-VEHICLE TYPE (1/4 TO 8 INCHES, INCL USIVE)MIL-A-11557A 1954.08.09 ANTENNA ASSEMBLY AS-574( )/URR (COMPONENTS OF)MIL-A-13338E VALID NOTICE 1 1988.10.24 AIMING CIRCLE, M2 AND M2A2, WITH EQUIPMENTMIL-A-13338E (1) 1983.08.11 AIMING CIRCLE, M2 AND M2A2, WITH EQUIPMENTMIL-A-13338E 1982.03.22 AIMING CIRCLE, M2 AND M2A2, WITH EQUIPMENTMIL-A-13374E NOTICE 4 1998.03.03 ADHESIVE, DEXTRIN, FOR USE IN AMMUNITION CONTAINERSMIL-A-13374E REINST NOTICE 3 1998.03.03 ADHESIVE, DEXTRIN, FOR USE IN AMMUNITION CONTAINERSMIL-A-13374E VALID NOTICE 1 1988.10.31 ADHESIVE, DEXTRIN, FOR USE IN AMMUNITION CONTAINERSMIL-A-13374E 1983.08.25 ADHESIVE, DEXTRIN, FOR USE IN AMMUNITION CONTAINERSMIL-A-13479 1954.06.18 ANEMOMETER ML-497( )/PMMIL-A-14178 1955.10.14 AMPLIFIER, AUDIO FREQUENCY AM-719( )/UMIL-A-14457 1957.12.31 ANTENNA AT-640( )/ARNMIL-A-14641B NOTICE 5 2001.07.21 AIGUILLETTE, AF COMMAND BANDSMIL-A-14641B 1981.06.30 AIGUILLETTE, AF COMMAND BANDSMIL-A-14897 NOTICE 2 1999.07.10 ACTUATOR, ROTARY 1000-34 ASSEMBLYMIL-A-14897 VALID NOTICE 1 1988.08.29 ACTUATOR, ROTARY 1000-34 ASSEMBLYMIL-A-14897 1969.07.20 ACTUATOR, ROTARY 1000-34 ASSEMBLYMIL-A-14898 NOTICE 2 1999.07.10 ACTUATOR, ROTARY 1000-34 REMANUFACTURED METAL PARTS ASSEMBLY MIL-A-14898 VALID NOTICE 1 1986.06.20 ACTUATOR, ROTARY 1000-34 REMANUFACTURED METAL PARTS ASSEM BLYMIL-A-14898 1969.07.20 ACTUATOR, ROTARY 1000-34 REMANUFACTURED METAL PARTS ASSEMBLYMIL-A-15303P 1986.11.19 AUDIBLE SIGNALS: ALARMS, BELLS, BUZZERS, HORNS, AND SIRENS, ELECTRONIC, SHIP BOARDMIL-A-15344J (2) 1990.11.02 AMPLIFIER, SYNCHRO SIGNALMIL-A-15344J 1963.06.07 AMPLIFIER, SYNCHRO SIGNALMIL-A-16749E (2) 1968.06.17 AMPLIFIER, AUDIO FREQUENCY, SOUND POWERED TELEPHONE SYSTEMMIL-A-16749E 1963.05.15 AMPLIFIER, AUDIO FREQUENCY, SOUND POWERED TELEPHONE SYSTEMMIL-A-17196E 1977.10.07 ALARM SWITCHBOARDS, ALARM PANELS, REMOTE SENTRY ALARM SWITCH, SIGNAL UN ITS, AND SPECIAL ALARM CONNECTION BOX, NAVAL SHIPBOARDMIL-A-17367D (1) 1978.09.11 ARMOR, BODY, FRAGMENTATION PROTECTIVE: UPPER TORSO (WITH COLLAR, M-195 5)MIL-A-17367D 1977.10.03 ARMOR, BODY, FRAGMENTATION PROTECTIVE: UPPER TORSO (WITH COLLAR, M-1955) NAVY MIL-A-18001K INT AMD 3 NOTICE 1 2008.08.28 ANODES, SACRIFICIAL ZINC ALLOYMIL-A-18194 1954.09.17 ATTACK DIRECTOR MARK 5 MOD 2MIL-A-18455C VALID NOTICE 1 1991.06.07 ARGON, TECHNICALMIL-A-18455C 1986.12.23 ARGON, TECHNICALMIL-A-18717C 1993.09.20 ARRESTING HOOK INSTALLATION, AIRCRAFTMIL-A-18924 1955.06.29 ARMING CELLS MK 1 MODS 5, 6, 7, AND 8MIL-A-19521B 1992.05.04 ANODE RETAINING SUPPORT PLUGS AND ANODE SELECTION AND INSTALLATION DESI GN CRITERIA FOR SHIPBOARD CONDENSERS AND HEAT EXCHANGERSMIL-A-19736A (2) 1966.03.16 AIR REFUELING SYSTEMS, GENERAL SPECIFICATION FORMIL-A-19736A 1960.08.05 AIR REFUELING SYSTEMS, GENERAL SPECIFICATION FORMIL-A-19865C 1990.03.20 AIR CONDITIONER, MECHANICALLY REFRIGERATEDMIL-A-19879B 1977.11.23 ARMOR, BODY, FRAGMENTATION PROTECTIVE: LOWER TORSOMIL-A-21016F 1990.05.21 ADHESIVE, RESILIENT DECK COVERINGMIL-A-21165A NOTICE 2 2004.08.23 ADAPTER, QUICK DISCONNECT, PASSENGER SEAT TO FLOORMIL-A-21165A 1965.08.27 ADAPTER, QUICK DISCONNECT, PASSENGER SEAT TO FLOORMIL-A-22262B (2) 1996.03.21 ABRASIVE BLASTING MEDIA SHIP HULL BLAST CLEANINGMIL-A-22262B 1993.04.05 ABRASIVE BLASTING MEDIA SHIP HULL BLAST CLEANINGMIL-A-23054A VALID NOTICE 1 1990.12.24 ACOUSTIC ABSORPTIVE BOARD, FIBROUS GLASS PERFORATED FIBRO US GLASS CLOTH FACEDMIL-A-23054A (1) 1984.06.25 ACOUSTIC ABSORPTIVE BOARD, FIBROUS GLASS PERFORATED FIBROUS GLASS CL OTH FACED。
国外军用电子元器件质量等级与国内对应一览表
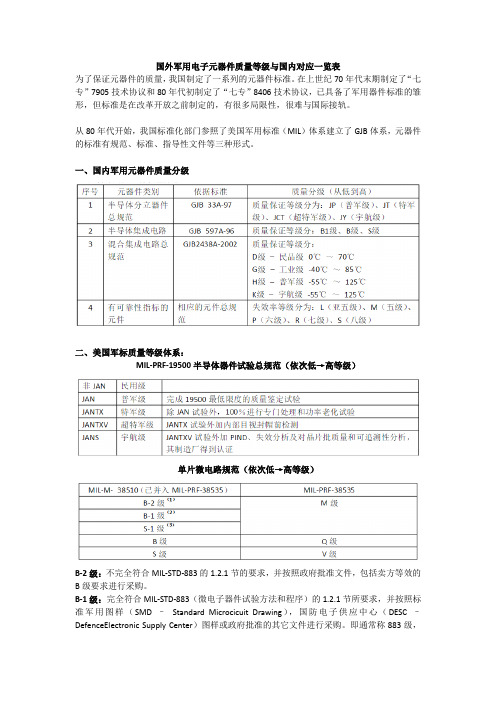
国外军用电子元器件质量等级与国内对应一览表为了保证元器件的质量,我国制定了一系列的元器件标准。
在上世纪70年代末期制定了“七专”7905技术协议和80年代初制定了“七专”8406技术协议,已具备了军用器件标准的雏形,但标准是在改革开放之前制定的,有很多局限性,很难与国际接轨。
从80年代开始,我国标准化部门参照了美国军用标准(MIL)体系建立了GJB体系,元器件的标准有规范、标准、指导性文件等三种形式。
一、国内军用元器件质量分级二、美国军标质量等级体系:MIL-PRF-19500半导体器件试验总规范(依次低→高等级)单片微电路规范(依次低→高等级)B-2级:不完全符合MIL-STD-883的1.2.1节的要求,并按照政府批准文件,包括卖方等效的B级要求进行采购。
B-1级:完全符合MIL-STD-883(微电子器件试验方法和程序)的1.2.1节所要求,并按照标准军用图样(SMD –Standard Microcicuit Drawing),国防电子供应中心(DESC –DefenceElectronic Supply Center)图样或政府批准的其它文件进行采购。
即通常称883级,器件上有5962 –xxx号。
S-1级:完全按照MIL-STD-975(NASA标准的电子电气和机电源器件目录)或MIL-STD-1547(航天飞行器和运载火箭用元器件、材料和工艺技术要求)进行采购,并有采购机关的规范批准。
MIL-PRF-38534D混合集成电路规范(依次低→高等级)电阻、电容、电感元件MIL 标准中有可靠性指标的元件失效等级分五级MIL 标准中有可靠性指标的失效率等级和失效率的对应关系三、欧空局元器件半导体分立器件:ESA/SCC(Europe SpaceAgency/Space Componet Cooperation)5000标准试验等级:B级、C级(从高到低)批接收等级:1级、2级、3级(从高到低)微电路:ESA/SCC(Europe SpaceAgency/Space Componet Cooperation)9000标准试验等级:B级、C级(从高到低)批接收等级:1级、2级、3级(从高到低)电阻、电容、电感器件:ESA/SCC(Europe SpaceAgency/Space Componet Cooperation)3000和4000标准试验等级:B级、C级(从高到低)批接收等级:1级、2级、3级(从高到低)四、国外军用元器件与我国军用元器件质量等级对应关系半导体分立器件质量等级对应关系微电路质量对应等级阻容电感失效率等级对应参考来源:融融网及网络资料。
- 1、下载文档前请自行甄别文档内容的完整性,平台不提供额外的编辑、内容补充、找答案等附加服务。
- 2、"仅部分预览"的文档,不可在线预览部分如存在完整性等问题,可反馈申请退款(可完整预览的文档不适用该条件!)。
- 3、如文档侵犯您的权益,请联系客服反馈,我们会尽快为您处理(人工客服工作时间:9:00-18:30)。
This document and process INCH-POUNDconversion measures necessary tocomply with this revision shall becompleted by 7 July 2003MIL-PRF-38534E6 January 2003SUPERSEDINGMIL-PRF-38534D6 January 1999PERFORMANCE SPECIFICATIONMICROCIRCUITS, HYBRIDGENERAL SPECIFICATION FORThis specification is approved for use by all Depart-ments and Agencies of the Department of Defense.This document is a performance specification. It is intended to provide the device manufacturers an acceptableestablished baseline in order to support Government microcircuit applications and logistic programs. The basicdocument has been structured as a performance specification that is supplemented with detailed appendices.These appendices provide guidance to manufacturers on demonstrated successful approaches to meeting military performance requirements. These appendices are included as a benchmark and are not intended to imposemandatory requirements.1. SCOPE1.1 Scope. This specification establishes the general performance requirements for hybrid microcircuits, Multi-*Chip Modules (MCM) and similar devices and the verification requirements for ensuring that these devices meet the applicable performance requirements. Verification is accomplished through the use of one of two quality programs (Appendix A). The main body of this specification describes the performance requirements and the requirements for obtaining a Qualified Manufacturers List (QML) listing. The appendices of this specification are intended forguidance to aid a manufacturer in developing their verification program. Detail requirements, specific characteristics, and other provisions that are sensitive to the particular intended use should be specified in the applicable deviceacquisition specification.Beneficial comments (recommendations, additions, deletions) and any pertinent data which may be of usein improving this document should be addressed to: Defense Supply Center Columbus (DSCC-VAS), PO Box3990, Columbus, OH 43216-5000, by using the Standardization Document Improvement Proposal (DD Form1426) appearing at the end of this document, or by letterAMSC N/A FSC 5962 DISTRIBUTION STATEMENT A. Approval for public release; distribution is unlimited.121.2 Description of this specification. The intent of this specification is to allow the device manufacturer the flexibility to implement best commercial practices to the maximum extent possible while still providing product which meets the military performance needs. Devices that are compliant to this specification are those that are capable of meeting the verification requirements outlined herein; and are built on a manufacturing line which is controlled by the manufacturer's quality management program and has been certified and qualified in accordance with the requirements herein. The certification and qualification requirements outlined herein are the requirements to be met by a manufacturer to be listed on the Qualified Manufacturers List (QML). The manufacturer may modify, substitute or delete the tests and inspections defined herein. This is accomplished by baselining a flow of tests and inspections that will assure that the devices are capable of meeting the generic verifications provided in this specification. This does not necessarily mean that compliant devices have been subjected to the generic performance verifications provided in this specification, just that compliant devices are capable of meeting them. It is the manufacturer's responsibility to ensure that their devices are capable of meeting the generic performance verifications applicable to each specified product assurance level. Appendix A defines the quality management program that may be implemented by the manufacturer. Appendix A includes an option to use a quality review board concept, hereafter referred to as the Technology Review Board (TRB) in this document, which may be used to modify the generic verification, design and construction criteria provided in this specification. Appendix B is not currently being used. Appendix C defines generic performance verifications. These verifications consist of a series of tests and inspections which may be used to verify the performance of devices. They may be used as is or modified as allowed by this specification. Appendix D is not currently being used. Appendix E defines generic design and construction criteria relative to this technology, including rework limitations and major change testing guidance. Appendix F provides statistical sampling procedures. Appendix G provides the guidelines for a Radiation Hardness Assurance (RHA) program. 1.3 Classification. Five quality assurance levels are provided for in this specification. Four of these classes, in highest to lowest order, are K, H, G, and D, as defined below. The fifth class is Class E, the quality level associated with a Class E device is defined by the acquisition document. 1.3.1 Class K. Class K is the highest reliability level provided for in this specification. It is intended for space applications. 1.3.2 Class H. Class H is the standard military quality level. 1.3.3 Class G. Class G is a lowered confidence version of the standard military quality level (H) with QML listing per 4.5.2.2, a possibly lower temperature range (-40o C to +85o C), a manufacturer guaranteed capability to meet the Class H Conformance Inspection and Periodic Inspection testing, and a vendor specified incoming test flow. The device must meet the Class H requirements for In-Process Inspections and Screening. 1.3.4 Class E. Class E designates devices which are based upon one of the other classes (K, H, or G) with exceptions taken to the requirements of that class. These exceptions are specified in the device acquisition document, therefore the device acquisition document should be carefully reviewed to ensure that the exceptions taken will not adversely affect the performance of the system. 1.3.5 Class D. Class D is a vendor specified quality level available to this specification. This is a possibly lower temperature range (0o C to +70o C) part with a vendor specified test flow available from a QML listed manufacturer. * * * **32. APPLICABLE DOCUMENTS 2.1 Government specifications, standards, and handbooks. The following specification and standard form a part of this document to the extent specified herein. Unless otherwise specified, the issue of these documents are those listed in the issue of the Department of Defense Index of Specifications and Standards (DODISS) and supplement thereto, cited in the solicitation (see 6.2).SPECIFICATIONDEPARTMENT OF DEFENSEMIL-I-46058 - Insulating Compound, Electrical (For Coating Printed Circuit Assemblies)STANDARDDEPARTMENT OF DEFENSEMIL-STD-883 - Test Methods and Procedures for Microelectronics(Unless otherwise specified copies of military standards are available from the Standardization Documents Order Desk, Building 4D, 700 Robbins Avenue, Philadelphia, PA 19111-5094. Copies of military standards are also available online from the Acquisition Streamlining and Standardization Information System (ASSIST) at /online/new/.2.2 Other Government documents, drawings, and publications. The following other Government documents, drawings, and publications form a part of this document to the extent specified herein. Unless otherwise specified, the issues are those cited in the solicitation.Handbook H4/H8 - Commercial and Government Entity (CAGE) Handbook.NAVSHIPS 0967-190-4010 - Manufacturer's Designating Symbols.QML-38534 - Qualified Manufacturer's List of Custom Hybrid Microcircuits QualifiedUnder Military Specification MIL-PRF-38534(Unless otherwise specified copies of military standards are available from the Standardization Documents Order Desk, Building 4D, 700 Robbins Avenue, Philadelphia, PA 19111-5094.)2.3 Order of Precedence. In the event of a conflict between the text of this document and the references cited herein (except for related associated detail specifications, specification sheets, or MS standards), the text of thisdocument takes precedence. Nothing in this document, however, supersedes applicable laws and regulations unless a specific exemption has been obtained.3. REQUIREMENTS3.1 Performance Requirements for Class K Devices. Class K devices shall be capable of meeting the Class K tests and inspections of Appendices C and E (see Table I). This shall include the incoming inspection flow, the in-process inspection flow, the screening flow, and the Conformance Inspection and Periodic Inspection flow. These devices shall be specified over the temperature range of -55o C to +125o C or as specified in the device acquisition document. Manufacturers of these devices shall be fully certified and qualified in accordance with this specification. Verification of these Performance Requirements shall be performed as described in paragraph4.3.2 Performance Requirements for Class H Devices. Class H devices shall be capable of meeting the Class H tests and inspections of Appendices C and E (see Table I). This shall include the incoming inspection flow, the in-process inspection flow, the screening flow, and the Conformance Inspection and Periodic Inspection flow. These devices shall be specified over the temperature range of -55o C to +125o C or as specified in the device acquisition document. Manufacturers of these devices shall be fully certified and qualified in accordance with this specification. Verification of these Performance Requirements shall be performed as described in paragraph4. **4 3.3 Performance requirements for Class G devices. Class G devices shall be capable of meeting the Class H tests and inspections of Appendices C and E, except incoming inspection (see Table I). This shall include the In-Process Inspection flow, the screening flow, and the Conformance Inspection and Periodic Inspection flow. Compliance with the Conformance Inspection and Periodic Inspection flow must be guaranteed by the manufacturer. Actual completion of Conformance Inspection and Periodic Inspection tests and inspections are optional and at the manufacturer's discretion. DSCC approval or notification is not required to eliminate Conformance Inspection and Periodic Inspection tests and inspections for this class of device, however it is the manufacturer's responsibility to ensure that their devices are capable of passing these tests and inspections. These devices shall be specified over the temperature range of -40o C to +85o C or a wider range. Manufacturers of these devices shall be fully certified and QML listed in accordance with this specification. Verification of these Performance Requirements shall be performed as described in paragraph 4. 3.4 Performance requirements for Class E devices. Class E devices are devices which meet all of the requirements of one of the other classes (K, H, or G) with some exceptions taken. The device acquisition document shall clearly state which class the device is based upon (K, H, or G) and what exceptions are being taken. The users of these devices should carefully examine the device acquisition document to verify that the exceptions being taken will not adversely affect the system performance. Manufacturers of these devices shall be fully certified in accordance with this specification. Verification of the performance requirements shall be performed as described in paragraph 4. 3.5 Performance requirements for Class D devices. Class D devices are built and tested in accordance with the manufacturer's specified production and testing flow (see Table I). These devices shall be capable of meeting the specified electrical tests. However, these devices are not required to meet any of the tests and inspections of this specification. These devices shall be specified over the temperature range of 0o C to +70o C or a wider range. Manufacturers of these devices shall be fully certified and QML listed in accordance with this specification. Verification of these Performance Requirements shall be performed as described in paragraph 4. 3.6 Performance requirements for RHA devices. Compliant RHA devices must meet the additional performancerequirements of Appendix G. Detailed information for producing and acquiring RHA devices can be found in JEDEC publication JEP133. * **5TABLE I. Performance Requirements Summary. Class Test Flow or Requirement 1/D E 2/ G 2/ H 2/ K 2/ CertificationRequired Required Required Required (Class H) Required (Class K) QML ListingRequired per 4.5.2.2 Required per 4.5.2.2 Required per 4.5.2.1 Required per 4.5.2.1 Incoming Inspection(App. C)Manufacturer Specified 3/ Manufacturer Specified 3/ Applicable (Class H) 1/ Applicable (Class K) 1/ In-ProcessInspections(App. C)Manufacturer Specified 3/ Applicable (Class H) 1/ Applicable 1/ Applicable 1/ Screening (App. C)Manufacturer Specified 3/ Applicable (Class H) 1/ Applicable (Class H) 1/ Applicable (Class K) 1/ ConformanceInspection andPeriodic Inspection(App. C)Manufacturer Specified 3/ Guaranteed (Class H) 4/ Applicable (Class H) 1/ Applicable (Class K) 1/ Temperature Range 5/ 0o C to +70o C Required per the Applicable device class and the Acquisition Document -40o C to +85o C -55o C to +125o C -55o C to +125o C1/ For test flow implementation and available flexibility see 3.7.1. 2/ Design and construction and rework criteria are as specified in Appendix E and shall be utilized per 3.7.1. 3/ Manufacturer Specified means that the manufacturer does not have to take the generic criteria of this specification into consideration during the establishment of its manufacturing and test flows. The manufacturer's flow may or may not meet the same requirements as the flow of this specification. Furthermore, the manufacturer may specify that they do not perform the particular test or inspection flow. 4/ Guaranteed (Class H) means that the manufacturer is assuring that their devices will meet the Conformance Inspection and Periodic Inspection test flow contained in Tables C-Xa, C-Xb, C-Xc, and C-Xd, but may or may not actually perform the tests and inspections specified. Elimination of these tests and inspections does not necessitate DSCC approval or notification. 5/ Wider temperature ranges are also acceptable for classes D and G. Class H and K shall be -55o C to +125o C unless otherwise specified in the acquisition document.3.7 General. The manufacturer of devices, in compliance with this specification, shall have and use production and test facilities and a verification program adequate to assure successful compliance with the provisions of thisspecification and the associated device acquisition specification. Adequacy of a device manufacturer to meet the requirements of this specification shall be determined by the Government qualifying activity. The individual item requirements shall be as specified in the associated device acquisition specification and herein. Only devices which meet all the performance requirements of this specification and the associated device acquisition specification and have been adequately verified shall be marked as compliant and delivered. Monolithic microcircuits may be built to the Class K, H, G, E, or D performance requirements of this specification, however, monolithic microcircuits offered in compliance with this specification shall be specified on a Standard Microcircuit Drawing (SMD). Facilities andprograms listed on the Qualified Manufacturer's List (QML) may be used for the manufacture of other than compliant devices; however, any use or reference to compliant device marking, Class K, H, G, E, or D certification status or this specification in such a way as to state or imply equivalency (and thereby Government endorsement) in connection with noncompliant devices is prohibited and may be cause for revocation of certification or QML status (or both). Terms, definitions, methods, and symbols are per 6.3. Any military specification or standard referred to in this specification may be replaced by an equivalent commercial standard as determined by the preparing activity.**63.7.1 Implementation of this specification. All devices offered and shipped in compliance with this specification shall meet the performance requirements specified for the applicable device class. The manufacturer shall verify that devices meet the performance requirements of the applicable device class. The manufacturer is responsible for developing a verification program which will meet this requirement. The appendices of this specification give standard methods for verifying that the devices meet the performance requirements (except for Class D). The manufacturer may address the requirements of this specification as written, adapt them to their products, or develop a new methodology. Prior to the manufacturer being certified the actual verification program to be used shall be reviewed and approved by DSCC. Any deletions or changes to the test flow shall also be reviewed and approved by DSCC or the manufacturer's DSCC approved TRB prior to implementation. In this manner a manufacturer may use an alternative method to the method specified in this specification to evaluate their parts if the alternate method verifies the same performance requirement. Furthermore, the manufacturer may eliminate a test or inspection (or decrease the occurrence or sample size of the test or inspection) if it is shown that the test or inspection is not necessary or can be performed less frequently. It is the manufacturer's responsibility to show how their verification program (and any changes to it) meets the requirements of this specification. The manufacturer shall analyze the impact of major changes and their effect on previously approve modifications of test (test optimization). See Table II for clarification. TABLE II. Implementation Summary. Option Definition Typical Examples Implementation Procedures Meet requirement as written The manufacturer performs the test or requirement as specified Self explanatory The manufacturer implements the test or requirement into internal documentation, verified during certification For TRB companies, alternate method and appropriate justification are approved by the manufacturer's TRB. Alternate method to the requirement The manufacturer assures that the intent of the requirement is met, but does not perform the Test/requirement exactly as written - Replacement of a test with SPC or alternate method - Historical data analysis shows that the requirement is met -Design verification/validation shows that the process is capable of meeting the requirement - Requirement does not address new materials, technologies, designs For traditional companies, manufacturer proposes the alternate method and justification to the Qualifying Activity for approval. The manufacturer proves that the test or requirement is either: Non-value added - Test does not stress the process adequately (e.g., PIND for encapsulated parts) - Historical data analysis shows that the test does not induce failures Elimination is achieved in the same manner as alternate methods described above The product will not comply with the test or requirement due to technology limitations - configuration of the product (i.e., size, mass, package, etc.) is incompatible with the test method The exception shall be documented in the applicable acquisition document. Product is classified as Class E Elimination of the requirement Application has no need of the requirementThe device will not experience theparticular stress in the application The exception shall be documented in the applicable acquisition document. Productis classified as Class E3.7.2 Device acquisition specification. The preferred device acquisition document for devices built in full compliance with this specification is a Standard Microcircuit Drawing (SMD). Monolithic microcircuits built in compliance with this document shall be documented on an approved SMD.**3.7.3 Design and Construction. The design and construction of compliant devices shall address the limitations and guidelines of Appendix E.3.7.3.1 Lead finish. Appendix E provides the general interface requirements for lead finishes.3.7.4 Workmanship. Devices shall be manufactured, processed, and verified to meet the performance requirements of this specification, and with the production practices, workmanship instructions, inspection and test procedures, and training aids prepared by the manufacturer in fulfillment of the Baseline Process Flow.3.7.4.1 Rework and repair provisions. All rework and repair operations shall address the limitations and guidelines of Appendix E.3.7.5 Marking of devices. Marking shall be in accordance with the requirements of this specification or the device procurement specification. The marking shall be legible and complete, and shall meet the resistance to solvents requirements of MIL-STD-883, method 2015. When mechanical or laser marking is performed it shall be clearly visible through those conformal coatings approved for use in MIL-I-46058 (see method 2015 of MIL-STD-883 if contrasting material or ink is used to highlight the trace). Mechanical or laser marked metal surfaces shall meet all applicable microcircuit finishes and shall not degrade the performance requirements of the device. Mechanical or laser marking shall be approved by the qualifying activity. If any special marking is used, it shall in no way interfere with the marking required herein, and shall be visibly separated therefrom. The following marking shall be included on each microcircuit unless otherwise specified.a. Part or Identifying Number (PIN) (see 3.7.5.1).b. Index point (see 3.7.5.2).c. Lot identification code or date code (see 3.7.5.3).d. Device manufacturer's identification (see 3.7.5.4).e. Device manufacturer's designating symbol (see 3.7.5.5).f. Country of manufacture (see 3.7.5.6).g. Serialization, when applicable (see 3.7.5.7).h. Special marking (see 3.7.5.8).i. ESD sensitivity identifier (see 3.7.5.8.2).j. Certification mark (see 3.7.5.8.3).Unless otherwise specified, the certification mark, the PIN, the inspection lot identification code, and the ESD identifier shall be located on the top surface of flat packages or dual-in-line configurations and on either the top or the side of cylindrical packages (TO configurations and similar configurations).3.7.5.1 Part or Identifying Number (PIN). Each Standard Microcircuit Drawing (SMD) microcircuit shall be marked with the complete PIN, as specified in the SMD. The number sequence for MIL-PRF-38534 is 5962-XXXXXZZHYY, where:5962 - XXXXX ZZ H Y YFederal RHA Device QML Case Leadstock class designator type no. device outline finishdesignator (see 3.7.5.1.1) class (see 3.7.5.1.3) designator\ / designator (see 3.7.5.1.4)\/ (see 3.7.5.1.2)Drawing number73.7.5.1.1 Device type. The device type shall identify the circuit function as indicated in the SMD.3.7.5.1.2 Device class designator. This device class designator shall be a single letter identifying the quality level in accordance with the SMD.3.7.5.1.3 Case outline. The case outline shall be designated by a single letter assigned to each outline within each SMD.3.7.5.1.4 Lead finish. Lead frame or terminal material and finish shall be as specified (see Appendix E). The lead finish shall be designated by a single letter as follows:Finish letter Lead finish (see note)A hot solder dipB tin-lead plateC gold plateX finishes A, B, or C (see note)NOTE: Finish letter "X" shall not be marked on the microcircuit or its packaging. This designation is provided for use in drawings, part lists, purchase orders, or other documentation where lead finishes A, B, andC are all considered acceptable and interchangeable without preference. For Government logisticsupport, the A lead finish will be acquired and supplied to the end user when the X is included in thePIN for lead finish. If the PIN is not available with the A lead finish, the same PIN will be acquiredexcept with the C or B lead finish designator as determined by availability. Type C terminal material isa fired on metallization used with leadless chip carriers.3.7.5.2 Index point. The index point, tab, or other marking indicating the starting point for numbering of leads or for mechanical orientation shall be as specified and shall be applied so that it is visible from above when the microcircuit is installed in its normal mounting configuration. The outline of an equilateral triangle (i.e., ∆), which may be used as an electrostatic identifier (see 3.7.5.8.2), may also be used as the pin 1 identifier.3.7.5.3 Lot identification code (date code). Devices shall be marked by a unique code to identify the week of final seal. The first two numbers in the code shall be the last two digits of the number of the year, the third and fourth numbers shall be two digits indicating the calendar week of the year. When the number of the week is a single digit, it shall be preceded by a zero. Reading from left to right or from top to bottom, the code number shall designate the year and week, in that order (e.g., 8806 equals week 6 of 1988).3.7.5.4 Manufacturer's identification. Devices shall be marked with the name or trade mark of the manufacturer. The identification of the equipment manufacturer may appear on the device only if the equipment manufacturer is also the device manufacturer.3.7.5.5 Manufacturer's designating symbol. When space permits, the manufacturer may mark the CAGE code on devices. The manufacturer's designating symbol or CAGE code number shall be as listed on NAVSHIPS0967-190-4010 or cataloging Handbook H4/H8. The designating symbol shall be used only by the manufacturer to whom it has been assigned and only on those devices manufactured at the manufacturer's plant. In the case of small devices, the manufacturer's designating symbol may be abbreviated by omitting the first "C" in the series of letters.3.7.5.6 Country of manufacture. The manufacturer shall indicate the country where the device was manufactured(i.e., substrate and element attach, interconnect, seal). At the option of the manufacturer the country of manufacture marking may be omitted from the body of the device but shall be retained on the initial container.3.7.5.7 Serialization. Serialization allows traceability of electrical tests results (variables data) to an individual device.3.7.5.7.1 Class K serialization. Prior to the first recorded electrical measurement in screening, each Class K device shall be marked with a unique serial number assigned consecutively. Lot records shall be maintained to provide traceability from the serial number to the specific incoming inspection lots from which the elements originated.83.7.5.7.2 Class H, G, and D serialization. Serialization of Class H, G, and D devices shall only be required whenspecified in the device acquisition specification.3.7.5.8 Special marking. When the size of a package is insufficient to allow marking of special process identifierson the top surface, the back side of the package may be used for these markings except the ESD identifier shall be marked on the top. Button cap flat packs with less than or equal to 16 leads may have the identifier marked on the ceramic. Back side marking with conductive or resistive ink shall be prohibited on nonconductive surfaces.3.7.5.8.1 Beryllium oxide package identifier. If a device package contains beryllium oxide, the device shall bemarked with this designation: BeO.NOTE: Packages containing beryllia will not be ground, sandblasted, machined, or have other operations performed on them which will produce beryllia or beryllium dust. Furthermore, beryllium oxidepackages will not be placed in acids that will produce fumes containing beryllium.3.7.5.8.2 Electrostatic discharge (ESD) sensitivity identifier. ESD classification levels are defined as follows whentested in accordance with MIL-STD-883, method 3015.PriorESD class designation Part Electrostaticdesignator category marking voltage1 A ∆ 0-1,999 V2 B ∆∆ 2,000-3,999 V*3 --- --- ≥ 4,000 VESD class marking is not required. However at the manufacturers option devices not yet ESD classified may be marked as class 1 until testing determines the appropriate class. Devices previously classed by test as category A may be marked as class 1. Devices previously classified as category B may be marked as class 2.3.7.5.8.3 Certification mark. All devices acquired to and meeting the requirements of this specification and theapplicable associated device acquisition specification, and which are approved for listing on QML-38534 shall bear a certification mark as shown in Table III.Table III. Certification Mark.Acquisition document Class Certification MarkSMD All QML or Q for small devicesK CKNon-SMD dated after this documentH CHG CGE CED CDNon-SMD dated prior to this document All CH or C for small devicesThese certification marks or the abbreviations "Q" or "C" shall not be used for any device acquired under contracts or orders which permit or require any changes to this specification except as allowed in 3.7.1. In the event that a lot fails to pass inspection, the manufacturer shall remove or obliterate the certification mark from the sample tested and also from the devices represented by the sample.3.7.5.9 Marking option for controlled storage of Class H and G. Where devices are subjected to testing andscreening in accordance with some portion of the quality assurance requirements and stored in controlled storage areas pending receipt of orders requiring conformance to the same or a different level, the inspection lot identification code shall be placed on the device package along with the other markings specified in 3.7.5 sufficient to assureidentification of the material. As an alternative, if the microcircuits are stored together with sufficient data to assure traceability to processing and inspection records, all markings may be applied after completion of all inspection to the specified level.9。