塑料成型技术
塑料成型技术现状与发展

塑料成型技术现状与发展塑料成型技术是一种将塑料原料通过一系列加工工艺,加热、压力等作用下,使其变形成为所需形状的方法。
随着塑料在工业生产和日常生活中的广泛应用,塑料成型技术也得到了快速发展。
本文将从塑料成型技术的现状与发展两个方面进行探讨。
一、塑料成型技术的现状1.注塑成型技术注塑成型技术是目前最常用的塑料成型技术之一。
它通过将加热熔化的塑料原料注入模具中,经过冷却后得到所需的产品形状。
注塑成型技术具有生产效率高、成本低、产品精度高等优点,广泛应用于电子、汽车、家电等领域。
2.吹塑成型技术吹塑成型技术主要用于生产中空塑料制品,如瓶子、容器等。
它是将热塑性塑料颗粒加热熔化后注入到吹塑机的模具中,通过气压将塑料吹成所需的形状。
吹塑成型技术具有生产效率高、成本低、产品质量好等特点,被广泛应用于食品、化妆品等行业。
3.挤出成型技术挤出成型技术是将加热熔化的塑料原料通过螺杆挤出机挤出成型。
挤出成型技术可以生产出形状复杂的塑料制品,如管道、板材等。
挤出成型技术具有生产效率高、产品质量稳定、适用范围广等优点,在建筑、包装等领域得到了广泛应用。
二、塑料成型技术的发展1.高速成型技术高速成型技术是近年来发展起来的一种新型塑料成型技术。
它通过增加注塑机的射出速度和压力,缩短冷却时间,实现塑料制品的高速生产。
高速成型技术能够提高生产效率,降低生产成本,适用于大批量生产的需求。
2.微纳米成型技术随着微纳米科技的发展,微纳米成型技术逐渐应用于塑料制品的生产。
微纳米成型技术可以制造出微小尺寸的塑料制品,如微型零件、微流控芯片等。
微纳米成型技术具有高精度、高灵活性等特点,有望在医疗、电子等领域得到更广泛的应用。
3.可持续发展成型技术随着环保意识的增强,可持续发展成型技术成为塑料成型技术的一个重要发展方向。
可持续发展成型技术主要包括生物降解塑料的应用、回收利用塑料原料等。
这些技术可以减少对环境的污染,提高资源利用率,符合可持续发展的要求。
几种特殊的塑胶成型工艺

几种特殊的塑胶成型工艺1.气体(水)辅助注射成型气体辅助注射成型是自往复式螺杆注塑机咨询世以来,注射成型技术最重要的进展之一。
它通过高压气体在注塑制件内部产生中空截面,利用气体积压,减少制品残余内应力,排除制品表面缩痕,减少用料,显示传统注射成型无法比拟的优越性。
气体辅助注射的工艺过程要紧包括三个时期:起始时期为熔体注射。
该时期把塑料熔体注人型腔,与传统注射成型相同,然而熔体只充满型腔的60%-95%,具体的注射量随产品而异。
第二时期为气体注人。
该时期把高压惰性气体注人熔体芯部,熔体前沿在气体压力的驱动下连续向前流淌,直至充满整个型腔。
气辅注塑时熔体流淌距离明显缩短,熔体注塑压力能够大为降低。
气体可通过注气元件从主流道或直截了当由型腔进人制件。
因气体具有始终选择阻力最小(高温、低粘)的方向穿透的特性,因此需要在模具内专门设计气体的通道。
第三时期为气体保压。
该时期使制件在保持气体压力的情形下冷却.进一步利用气体各向同性的传压特性在制件内部平均地向外施压,并通过气体膨胀补充因熔体冷却凝固所带来的体积收缩(二次穿透),保证制品外表面紧贴模壁。
气辅技术为许多原先无法用传统工艺注射成型的制件采纳注塑提供了可能,在汽车、家电、家具、电子器件、日常用品、办公自动化设备、建筑材料等几乎所有塑料制件领域差不多得到了广泛的应用,同时作为一项带有挑战性的新工艺为塑料成型开创了全新的应用领域。
气辅技术专门适用于制作以下几方面的注塑制品:1)管状、棒状制品:如手柄、挂钩、椅子扶手、淋浴喷头等。
采纳中空结构,可在不阻碍制品功能和使用性能的前提下;大幅度节约原材料,缩短冷却时刻和生产周期。
2)大型平板制件:如汽车外表板、内饰件格栅、商用机器的外军及抛物线形卫星天线等。
通过在制件内设置式气道,能够显著提高制品的刚度和表面质量,减小翘曲变形和表面凹陷,大幅度降低锁模力,实现用较小的设备成型较大的制件。
3)厚、薄壁一体的复杂结构制品:如电视机、运算机、打印机外壳及内部支撑和外部装饰件等。
塑料封装的成型技术

塑料封装的成型技术塑料封装的成型技术主要有以下几种:1.注射成型(简称注塑):将热塑性塑料或热固性料利用塑料成型模具制成各种形状的塑料制品的主要成型设备,注塑成型是通过注塑机和模具来实现的。
2.挤出:物料通过挤出机料筒和螺杆间的作用,边受热塑化,边被螺杆向前推送,连续通过机头而制成各种截面制品或半制品的一种加工方法。
3.旋转成型(又称滚塑成型、旋塑、旋转模塑、旋转铸塑、回转成型等):该成型方法是先将计量的塑料(液态或粉料)到加入模具中,在模具闭合后,使之沿两垂直旋转轴旋转,同时使模具加热,模内的塑料原料在重力和热能的作用下,逐渐均匀地涂布、熔融粘附于模腔的整个表面上,成型为与模腔相同的形状,再经冷却定型、脱模制得所需形状的制品。
4.吹塑:热成型Thermoforming 片材夹在框架上加热到软化状态,在外力作用下,使其紧贴模具的型面,以取得与型面相仿的形状。
5.模压成型:压延成型。
6.低压注塑:将聚酰胺材料放入低压注塑机的胶池内;将待处理的PCB放入与该PCB对应的模具中;将步骤2)所述的PCB和模具一起放到低压注塑机的操作台上;启动低压注塑机,在低压状态下,向模具内注入液态的聚酰胺材料(低压注塑胶料),填满PCB周围的空间,完成低压注塑操作;快速固化,完成PCB封装;如PCB需外壳,则将低压注塑处理后的PCB装入与所述PCB对应的外壳内,完成封装。
7.超临界流体微孔发泡成型:首先是将超临界流体(二氧化碳或氮气)溶解到热融胶中形成单相溶体;然后通过开关式射嘴射人温度和压力较低的模具型腔,由于温度和压力降低引发分子的不稳定性从而在制品中形成大量的气泡核,这些气泡核逐渐长大生成微小的孔洞。
8.纳米注塑成型(NMT):是金属与塑胶以纳米技术结合的工法,先将金属表面经过奈米化处理后,塑胶直接射出成型在金属表面,让金属与塑胶可以一体成形。
塑料挤出成型技术
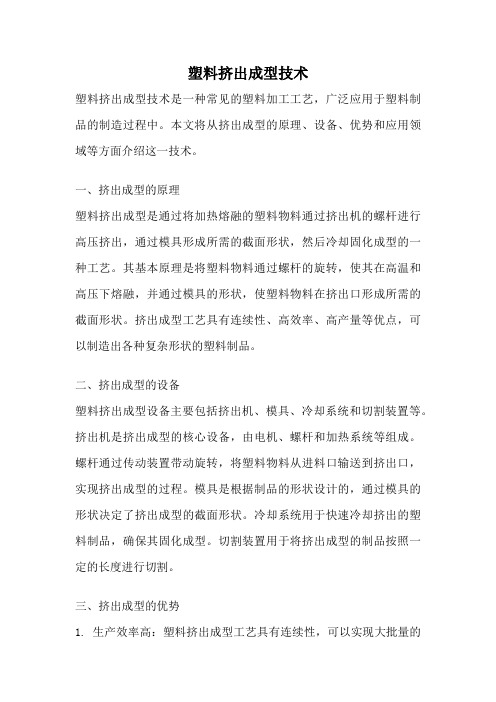
塑料挤出成型技术塑料挤出成型技术是一种常见的塑料加工工艺,广泛应用于塑料制品的制造过程中。
本文将从挤出成型的原理、设备、优势和应用领域等方面介绍这一技术。
一、挤出成型的原理塑料挤出成型是通过将加热熔融的塑料物料通过挤出机的螺杆进行高压挤出,通过模具形成所需的截面形状,然后冷却固化成型的一种工艺。
其基本原理是将塑料物料通过螺杆的旋转,使其在高温和高压下熔融,并通过模具的形状,使塑料物料在挤出口形成所需的截面形状。
挤出成型工艺具有连续性、高效率、高产量等优点,可以制造出各种复杂形状的塑料制品。
二、挤出成型的设备塑料挤出成型设备主要包括挤出机、模具、冷却系统和切割装置等。
挤出机是挤出成型的核心设备,由电机、螺杆和加热系统等组成。
螺杆通过传动装置带动旋转,将塑料物料从进料口输送到挤出口,实现挤出成型的过程。
模具是根据制品的形状设计的,通过模具的形状决定了挤出成型的截面形状。
冷却系统用于快速冷却挤出的塑料制品,确保其固化成型。
切割装置用于将挤出成型的制品按照一定的长度进行切割。
三、挤出成型的优势1. 生产效率高:塑料挤出成型工艺具有连续性,可以实现大批量的生产,提高生产效率。
2. 制品质量稳定:挤出成型的制品形状稳定,尺寸精确,质量可靠。
3. 适用范围广:挤出成型工艺适用于各种塑料,可以制造出各种形状的制品,如管材、板材、型材等。
4. 设备投资少:相对于其他塑料加工工艺,挤出成型设备投资较少,生产成本较低。
5. 可塑性强:挤出成型的塑料物料可根据需要选择,可以加入各种填充剂、增强剂等,增加塑料的性能。
四、挤出成型的应用领域塑料挤出成型技术广泛应用于建筑、包装、汽车、电子、家电等行业。
在建筑行业中,挤出成型制造的塑料管材、型材、板材等被广泛应用于室内装饰、给排水系统、电线电缆等方面。
在包装行业中,挤出成型用于制造各种塑料包装盒、瓶子、袋子等。
在汽车行业中,挤出成型的塑料制品用于汽车内饰、外饰等部件。
在电子和家电行业中,挤出成型的塑料制品用于电线电缆的保护管、电器外壳等。
八大塑料注塑成型技术及特点
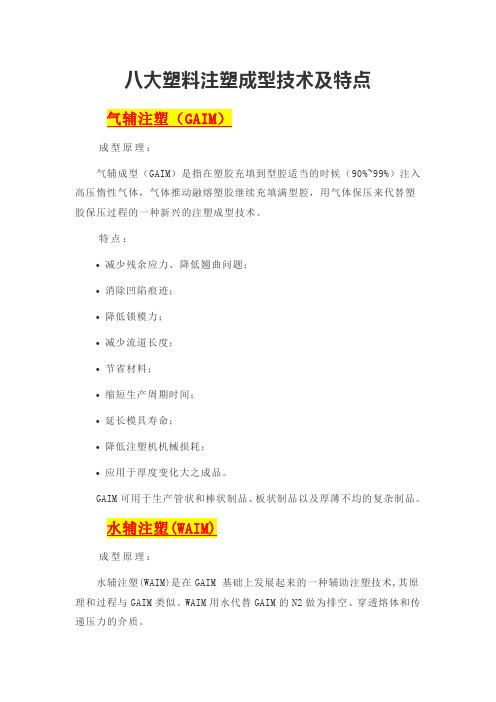
八大塑料注塑成型技术及特点气辅注塑(GAIM)成型原理:气辅成型(GAIM)是指在塑胶充填到型腔适当的时候(90%~99%)注入高压惰性气体,气体推动融熔塑胶继续充填满型腔,用气体保压来代替塑胶保压过程的一种新兴的注塑成型技术。
特点:•减少残余应力、降低翘曲问题;•消除凹陷痕迹;•降低锁模力;•减少流道长度;•节省材料;•缩短生产周期时间;•延长模具寿命;•降低注塑机机械损耗;•应用于厚度变化大之成品。
GAIM可用于生产管状和棒状制品、板状制品以及厚薄不均的复杂制品。
水辅注塑(WAIM)成型原理:水辅注塑(WAIM)是在GAIM 基础上发展起来的一种辅助注塑技术,其原理和过程与GAIM类似。
WAIM用水代替GAIM的N2做为排空、穿透熔体和传递压力的介质。
特点:与GAIM相比,WAIM具有不少优势•水的热传导率和热容量比N2大得多,故制品冷却时间短,可缩短成型周期;•水比N2更便宜,且可循环使用;•水具有不可压缩性,不容易出现手指效应,制品壁厚也较均匀;•气体易渗入或溶入熔体而使制品内壁变粗糙,其至在内壁产生气泡,而水不易渗入或溶入熔体,故可制得内壁光滑的制品。
精密注塑成型原理:精密注塑是指能成型内在质量、尺寸精度和表面质量均要求很高的产品的一类注塑技术。
其生产出来的塑胶制品的尺寸精度,可以达到0.01mm 以下,通常在0.01~0.001mm之间。
特点:•制件的尺寸精度高,公差范围小,即有高精度的尺寸界限精密塑胶制件的尺寸偏差会在0.03mm以内,有的甚至小到微米级,检测工具依赖于投影仪。
•制品重复精度高主要表现在制件重量偏差小,重量偏差通常在0.7%以下。
•模具的材料好,刚性足,型腔的尺寸精度、光洁度以及模板间的定位精度高•采用精密注射机设备•采用精密注射成型工艺精确控制模具温度、成型周期、制件重量、成型生产工艺。
•适用的精密注射成型材料PPS、PPA、LCP、PC、PMMA、PA、POM、PBT、加玻纤或碳纤的工程材料等。
塑料成型技术现状与发展
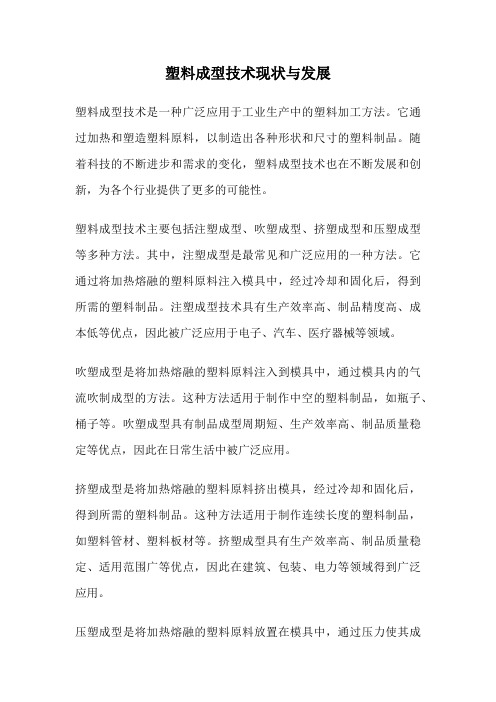
塑料成型技术现状与发展塑料成型技术是一种广泛应用于工业生产中的塑料加工方法。
它通过加热和塑造塑料原料,以制造出各种形状和尺寸的塑料制品。
随着科技的不断进步和需求的变化,塑料成型技术也在不断发展和创新,为各个行业提供了更多的可能性。
塑料成型技术主要包括注塑成型、吹塑成型、挤塑成型和压塑成型等多种方法。
其中,注塑成型是最常见和广泛应用的一种方法。
它通过将加热熔融的塑料原料注入模具中,经过冷却和固化后,得到所需的塑料制品。
注塑成型技术具有生产效率高、制品精度高、成本低等优点,因此被广泛应用于电子、汽车、医疗器械等领域。
吹塑成型是将加热熔融的塑料原料注入到模具中,通过模具内的气流吹制成型的方法。
这种方法适用于制作中空的塑料制品,如瓶子、桶子等。
吹塑成型具有制品成型周期短、生产效率高、制品质量稳定等优点,因此在日常生活中被广泛应用。
挤塑成型是将加热熔融的塑料原料挤出模具,经过冷却和固化后,得到所需的塑料制品。
这种方法适用于制作连续长度的塑料制品,如塑料管材、塑料板材等。
挤塑成型具有生产效率高、制品质量稳定、适用范围广等优点,因此在建筑、包装、电力等领域得到广泛应用。
压塑成型是将加热熔融的塑料原料放置在模具中,通过压力使其成型的方法。
这种方法适用于制作大型、复杂形状的塑料制品,如汽车外壳、家电外壳等。
压塑成型具有制品强度高、制品表面光滑等优点,因此在汽车、电子等领域得到广泛应用。
随着科技的不断进步和需求的变化,塑料成型技术也在不断发展和创新。
一方面,随着新型材料的涌现,塑料成型技术得到了更多的应用。
例如,高性能塑料、环保塑料等新型材料的使用,使得塑料制品在耐高温、耐腐蚀等方面有了更好的性能。
另一方面,随着数字化技术的应用,塑料成型技术也向着智能化、自动化方向发展。
例如,通过机器人技术实现自动化生产,通过模具设计软件进行数字化设计等,都使得塑料成型技术更加高效和精确。
随着人们对环境保护意识的增强,塑料成型技术也面临着挑战和发展。
塑料挤出成型技术
塑料挤出成型技术塑料挤出成型技术是一种常见的塑料加工方法,广泛应用于塑料制品的生产中。
本文将从塑料挤出成型技术的原理、工艺步骤、应用领域等方面进行介绍。
一、原理塑料挤出成型技术是将塑料颗粒通过加热和融化,然后通过挤出机将熔融塑料挤出成型的一种方法。
其原理主要包括以下几个步骤:1. 加料:将预先配好的塑料颗粒投入挤出机的料斗中。
2. 加热:通过电加热或燃气加热,将塑料颗粒加热到熔点以上,使其融化成熔融塑料。
3. 挤出:通过螺杆的旋转,将熔融塑料从模具的出口挤出,形成所需的截面形状。
4. 冷却:通过冷却装置对挤出的塑料进行快速冷却,使其固化成型。
5. 切割:将冷却固化的塑料通过切割设备切割成所需的长度。
二、工艺步骤塑料挤出成型技术的工艺步骤一般包括以下几个环节:1. 塑料颗粒预处理:对塑料颗粒进行筛选、干燥等预处理工作,以保证挤出过程的质量。
2. 挤出机操作:将预处理好的塑料颗粒投入挤出机的料斗中,经过加热、融化、挤出等操作,得到所需的塑料制品。
3. 模具设计与制造:根据所需的制品形状和尺寸,设计和制造相应的模具。
4. 挤出成型:将熔融塑料从模具的出口挤出,形成所需的截面形状。
5. 冷却与固化:通过冷却装置对挤出的塑料进行快速冷却,使其固化成型。
6. 切割与包装:将冷却固化的塑料通过切割设备切割成所需的长度,并进行包装。
三、应用领域塑料挤出成型技术广泛应用于各个领域的塑料制品生产中,例如:1. 建筑行业:生产塑料管道、塑料板材、塑料薄膜等建筑材料。
2. 包装行业:生产塑料袋、塑料瓶、塑料容器等包装制品。
3. 汽车行业:生产汽车零部件,如塑料车门、塑料仪表盘等。
4. 家电行业:生产电视机外壳、冰箱内胆等家电配件。
5. 日用品行业:生产塑料梳子、塑料杯子、塑料衣架等日用品。
总结:塑料挤出成型技术是一种常见的塑料加工方法,通过加热和融化塑料颗粒,然后通过挤出机将熔融塑料挤出成型。
该技术具有工艺简单、生产效率高、适用范围广等优点,被广泛应用于各个领域的塑料制品生产中。
塑料成型工艺与模具设计概述
2. 收缩性
塑料在成型及冷却过程中发生的体积收缩性 质称为收缩性,塑料在熔融状态下的体积总比 其固态下的体积大。
影响塑料收缩性的因素有:塑料的组成及结 构、成型工艺方法、工艺条件、塑件几何形状 及金属镶件的数量、模具结构及浇口形状与尺 寸等。
三、塑料特性与应用 (一)热塑性塑料
热塑性塑料
主要性能
酸性
主要应用
PE聚乙烯
耐化学腐蚀、电绝 缘、吸水性小
小载荷齿轮、容器、轴承、阀件、 涂层、化工管道
PP聚丙烯
密度最小、耐腐蚀、 吸水性小、耐热
PVC聚氯乙烯 PS聚苯乙烯
耐腐蚀、电绝缘、 耐燃
电绝缘、透光、吸 湿低、硬度高、易
燃
ABS丙烯腈-丁 二烯-苯乙烯
(1)热收缩 (2)结构变化引起的收缩 (3)弹性恢复 (4)塑性变形
影响热固性塑料收缩率的原因还有:原材料、 模具结构、成型方法及成型工艺条件等。
2.流动性
热固性塑料的流动 性通常以拉西格流动性 来表示。
影响热固性塑料流 动性的主要因素有: (1)塑料原料 (2)模具及工艺条件的 影响
3.水分及挥发物含量 一是来自生产、运输和储存,二是来自化
安全在于心细,事故出在麻痹。20.10.2020.10.2017: 02:0517:02:05October 20, 2020
踏实肯干,努力奋斗。2020年10月20 日下午5 时2分2 0.10.20 20.10.2 0
追求至善凭技术开拓市场,凭管理增 创效益 ,凭服 务树立 形象。2020年10月20日星期 二下午5时2分5秒17:02:0520.10.20
塑料材料的加工与成型技术
塑料材料的加工与成型技术塑料材料是一种非常重要的工业材料,广泛应用于各个领域。
塑料的加工与成型技术在塑料制品的生产过程中起着至关重要的作用。
本文将介绍塑料材料的加工与成型技术的基本原理、常见方法和应用领域,帮助读者更好地了解和掌握相关知识。
一、塑料材料的加工与成型技术的基本原理塑料材料的加工与成型技术主要基于其独特的物理性质。
塑料材料在一定的温度范围内可以通过外力加工,并保持一定的形状。
主要的基本原理包括以下几个方面:1. 熔融性:塑料材料可在一定温度下熔化成流动的液体,使其能够通过模具或挤压机械加工成所需形状。
2. 可塑性:塑料材料易于塑性变形,即能够被挤压、压延、吹制等加工方法改变其形状。
3. 固化性:一旦塑料材料冷却,液态塑料就会迅速固化成固体,保持特定的形状。
4. 高分子链结:塑料材料由高分子链组成,链与链之间有一定的交联力,可使塑料具有一定的韧性和强度。
以上原理为塑料材料加工与成型提供了基础,下面将介绍塑料常见的加工与成型方法。
二、常见的塑料材料加工与成型方法1. 注塑成型:注塑成型是将熔化的塑料材料通过注塑机注入模具中,在一定的压力和温度下让其固化成型的过程。
注塑成型方法广泛应用于塑料制品的生产,如塑料家具、电子产品外壳等。
2. 吹塑成型:吹塑成型是通过先使塑料挤压成膜状,再通过对薄膜进行吹气、拉伸等操作,使其成形为中空物体的方法。
吹塑成型主要用于制造塑料瓶、塑料容器等。
3. 挤出成型:挤出成型是将塑料料柱加热熔融,通过挤压机将其挤出成型的方法。
挤出成型适用于制造塑料管、塑料板等。
4. 压延成型:压延成型是将熔化的塑料通过挤压机械挤压成薄板状,然后通过冷却固化成所需形状的方法。
压延成型通常用于制造塑料薄膜、塑料片等。
除了以上常见的成型方法,还有其它方法如注塑拉伸吹塑、热成型、压力成型等。
不同的加工与成型方法适用于不同的塑料制品,具体应根据实际情况选择最适合的方法。
三、塑料加工与成型技术的应用领域塑料加工与成型技术广泛应用于各个领域,如电子、汽车、家居、医疗等。
塑料的制作工艺
塑料的制作工艺塑料是一种常见的合成材料,广泛应用于各个领域,包括日常生活用品、工业制品以及建筑材料等。
塑料的制作工艺涉及到多个环节,包括原料处理、塑料成型技术以及后续处理等,本文将对这些方面进行详细介绍。
一、原料处理塑料的制作过程中,首先需要对原料进行处理。
常见的塑料原料有聚乙烯、聚丙烯、聚氯乙烯等,它们通常以颗粒或者粉末的形式存在。
原料处理的主要目的是清洁和干燥原料,以确保制作出的塑料制品具有高质量和良好的性能。
在原料处理的过程中,首先需要将原料进行筛选,去除其中的杂质和不符合要求的颗粒。
随后,将干净的原料送入塑料挤出机或注塑机中进行熔融。
二、塑料成型技术1. 挤出成型挤出成型是一种常见的塑料成型技术,适用于制作连续性的塑料制品,如管道、板材、薄膜等。
在挤出成型过程中,先将原料送入到挤出机中,经过高温和高压下的熔融处理,然后通过模具进行形状的塑造,最后通过冷却装置进行固化和冷却。
2. 注塑成型注塑成型是一种常用的塑料成型技术,适用于制作各种复杂形状的塑料制品,如密封件、零部件等。
注塑成型过程中,将熔化的塑料原料注入到注塑机的注射筒中,经过高压注塑成形,然后通过模具冷却、固化和脱模。
3. 吹塑成型吹塑成型主要用于制作空心的塑料制品,如瓶子、容器等。
吹塑成型过程中,首先将塑料原料进行熔化,然后将融化的塑料吹入模具中,并采用压缩空气使其充分填充模具中的空腔,最后通过冷却和脱模来得到成型的塑料制品。
三、后续处理1. 表面处理塑料制品在成型过程中可能会出现表面缺陷,为了提升外观质量和光泽度,常常需要进行表面处理。
常见的表面处理方式有研磨、抛光、喷漆等,以使塑料制品具有更好的外观效果。
2. 附加工艺根据不同的需求,塑料制品可能需要进行附加工艺的处理。
例如,某些制品需要进行喷涂、丝印、雷雕等工艺来增加标识或装饰效果;某些制品还可能需要进行层叠、组装等工艺来满足实际使用需求。
3. 塑料废料处理在塑料制作过程中,会产生大量的废料。
- 1、下载文档前请自行甄别文档内容的完整性,平台不提供额外的编辑、内容补充、找答案等附加服务。
- 2、"仅部分预览"的文档,不可在线预览部分如存在完整性等问题,可反馈申请退款(可完整预览的文档不适用该条件!)。
- 3、如文档侵犯您的权益,请联系客服反馈,我们会尽快为您处理(人工客服工作时间:9:00-18:30)。
塑料成型技术数据一、前言在射出成形过程中,从试模到大量生产的这一段期间内,因成形不良,致使成品产生暇疵,而造成不良品或报废品的因素有很多,其中主要原因大致可归纳为以下数点:1.成形作业过程中品管人员或作业人员疏忽。
2.成形材料使用不当。
3.射出成形机能力不足。
4.成形作业条件设定不当。
5.模具设计上制作不完备。
6.成形品设计上下不完善。
形成成形不良之原因,除上述第一项纯属品管人员或作业人员之疏忽,而造成之错失外,其余若详加分析的话则可得知实际上造成成品不良的原因,并不单纯,因为在上述诸项原因中有的不良原因之形成,并非是单独由某一种原因所产生的,而是有许多项状况之消除,常有赖于实际作业者多年的经验与直觉的判断。
二、成形品不良状况1.充填不足(SHORT SHOT)2.毛边(FLASH)3.缩水(SINK MARK)4.流痕(FLOW MARK)5.喷痕(JETT ING)6.银条(SILVER STREAKS)7.表面模糊状(DULLSURFACE)8.接合线(WELD LINE)9.气泡(BUBLE)10.黑条与烧焦(BLACK STREAKS)11.裂痕与破裂(CRAGING CRACKING))12.变形(WARPAGE)13.顶白(白化、挽白)14.颤纹(CHATTER MARK)15.表面剥离(层裂)三、形成不良的原因1.充填不足(SHORT SHOT)又称为缺料、短料、未饱料……,系指成形时所射出的熔融塑料【註1】未能完全充满整个模窝【註2】而言,发生充填不足的原因大都是成形条件设定不当,成品壁厚设计太薄,模具设计制作不完备成形机本身容量不足。
2.毛边(FLASH)又称之为溢料、毛头、过饱料……,系指熔融树脂流入分模面(P.L 面) 里,或渗入模仁【註3】之嵌合处内,致使成品产生不应有的料。
形成毛边的原因,除成形机的能力不足外,大致上可以说是模具的问题比较多。
【註1】塑膠原料在料管中加溫至最宜成形的溫度時融解成流體的現象,稱之為熔融樹脂。
【註2】雄(公) 模與雌(母) 模,合模後所留下之間隙亦是將來成形後,所得之成品形狀,此一空間稱之為模窩。
【註3】一組模具之組成很少是由一塊鋼材一體加工成形的,大部份是由許多種鋼材及配件嵌合而成的,除了本體以外之配件,稱之為模仁或仁仔或CORE 配件模塊等。
3.缩水(SINK MARK)也称为收缩下陷、凹陷、酒窝、耐凹…,是指成品表面产生凹陷的现象。
形成缩水的原因是熔融树脂于冷却固化时,其体积因热胀冷缩之原理产生收缩,在成品的肉厚比较厚的地方发生此种现象。
比较容易产生收缩的地方大多是在成品有RIB (肋) 或是BOSS (毂) 的背部,亦或是肉厚相差悬殊的地方。
4.流痕(FLOW MARK)是指熔融树脂流动后的痕迹,以浇口为中心,而呈现年轮状的条纹。
此种现象在粘度高而流动性不良的树脂较容易出现造成流痕的原因是因为最初流入模窝内的熔融树脂冷却过快,而与后续的熔融树脂产生交界而残留下的痕迹。
5.喷痕(JETTING)亦称为喷射流,是指熔融树脂从浇口往模窝内射进时成纽带状固化,在成形品表面呈蛇行弯曲状的模样,喷痕也可视为流痕的一种。
产生喷痕的原因是塑料充填的过快,而呈现树脂的流痕,在使用侧面浇口的模具时,若没有设熔渣滞留部【註2】或是熔渣滞留部过小时就容易产生喷痕,原因是通过浇口的较冷树脂会直入模窝,碰到模窝的壁面而固化,继而被后续的热树脂推流而残留痕迹。
此种现象应追加熔渣滞留部或加大浇口断面积或选择其他的浇口形状来防止。
6.银条(SILVER STREAKS)俗称白花或起昌。
系指成形品外观面上,沿树脂流动的方向所产生的条纹,由于反射光的关系而呈现银白色条纹,所以称为银条。
形成银条的原因是树脂中含有水份【註4】或挥发物或者是模具表面附着有水份、油等挥发物,亦或者射出成形机的螺杆卷入空气等诸原因都会发生银条,因为当溶融树脂进入模窝内时,若空气无法完全被排挤出,则残留的气体就会附着在成品的外表上,或内部里面。
附着在外表上的就会形成银条,在成品内的就会形成气泡。
7.表面模糊状(DULL SURFACE)也叫起雾是指成形品表面失去树脂本来的光泽,像罩有一层乳白色层膜,成为模糊状态。
形成光泽不良的原因,大都是模具表面状态所引起的,因为模具表面若研磨不良时,则形成品的表面当然得不到充分的光泽。
其他如成形过程中,使用过多的离模剂或油脂性离模具剂,也都会有损成形品表面的光泽。
8.接合线(WELD LINE)俗称接水痕、水痕、接料痕、熔接线…,系指熔融塑料分成二道以上流动于最后再会合时,由于流动树脂的前端部冷却固化致使于会合时,无法完全融合,所形成的细线或条纹。
举凡二个进料口一定会有一条接合线,每个顶破孔无论是方孔或圆孔,也一定会有一条接合线【註4】只是接合处,线条、深度粗细之差异而已。
接合线不仅有碍美观,也易误认为是裂痕,更不利成品之强度,故应设法消除或减轻。
9.气泡(BUBLE)是指成形品的内部包入空气或气体而言。
形成气泡的原因为形成品在冷却时,因为体积收缩差(热胀冷缩),以至在成品内壁较厚的地方产生的空隙,这一空隙或空洞我们称之为气泡。
熔融树脂中的水份或挥发物因含量过高于成形时,变为气泡而部份封入内部亦是造成气泡的原因,一般在染色过的材料比较不易看得到气泡,最容易看到气泡的是在透明的材质上。
例如:PS 硬胶PMMA 或PA。
10.黑条与烧焦(BLACK STREAKS)黑条是指成形品有黑色条纹的现象形成黑条的主要原因是熔融树脂在料管内,因过热分解而形成的常见于热安定不良的树脂或难燃性树脂。
一般所谓的烧焦其黑条以外,尚包括成形品表面因树脂过热所致的变色或制品的突角部份或BOSS 或RIB 的前端等有焦黑的现象。
形成烧焦的原因是加热筒(料管) 温度过高或树脂在料管中,滞留时间过长而致使树脂产生分解或是滞留在雌模的空气,因在熔解树脂射入时未能迅速排出被压缩,而升温以致将树脂烧焦。
(射出机有自动purge 的工功能;射出中断之后重新射料要purge部份旧料;冷机升温亦同)【註4】我們可以用自來水的流動試驗得知。
例如將自來水打開任其流在平面上時,然後在整片的水流中放置一根手或筷子,可以看出自來水必定會在手指或筷子處後兩邊流,然後再會合因為塑料於射出成形前,須先在料管加溫至半流體狀態,故其流動原理一樣。
11.裂痕与破裂(CRAGING CRACKING)破裂系指成形品表面的痕迹或成品脱模时部份卡在模具中无法取出等等都属于破裂。
产生破裂的主要原因有:(1)脱模不良所致。
(2)模温过低所致。
(3)过度充填所致。
(4)制品构造上缺陷所致。
脱模时若脱模斜度不足或模具表面粗糙或顶针排列不均匀或模具的装配不良致产生UNDER CUT 在在都会加大脱模的阻力,若脱模阻力大于材料所能承受的抗加强度则破裂是必然的。
射出压力过大或材料计量过多,会使成品内部产生过大的应力及收缩率减少,致使原先预留的收缩率不足,而造成脱模困难、裂纹或破裂就容易产生。
模温过低也是造成收缩减小的主要原因之一。
在制品中浇口部常易残留过大的内部应力,该部份转易脆化,特别是直接浇口的附近时时都处在过度充填的状态中更容易因内部应力破裂。
12.变形(WARPAGE)又称为翘曲、扭曲,在射出成形中若制品有内部应力产生时则会造成变形。
平形方向的变形称为翘曲,对负方向的变形称为扭曲,产生内部应力主要系为制品冷却不均匀,因冷却不均匀,所以致使热收缩不均匀。
其次为成形时树脂配向性【註5】也会是造成成形品变形的原因。
13.白化顶白或挽白都属白化的一种。
成形品在离型脱模时遭受顶出销的强力顶出,或在UNDER CUT 【註6】处受到强制脱模时则该处会变白,此变白的部份称之为顶白,此外雌模若比雄模粗糙(当成品顶出侧在雌模侧时) 或是保压压力过大,会造成成品内应力过大,而在成品之边缘产生白色的痕迹,此一种痕迹称之为挽白。
白化并非裂纹,然而却是裂纹的预兆在ABS Hips 硬质PVC 等塑料制品中,较容易发生白化的现象。
【註5】塑膠以熔融狀態高速通過澆口的狹處時樹脂分子被拉伸,而配列一定的方向,這就是高分子的流動配向或分子配向。
【註6】從模具取出製品之際相對於取出的方向(亦即成品頂出之方向),製品的側面若有凸出或凹入的部份,而致使製品無法從模具內取出時,此種在模具取出製品時對模具的開閉方向造成牽制的部份稱之為UNDER UCT 或是清角。
14.颤纹(CHATTER MARK)是属于流痕的一种只是其所产生的痕迹不是年轮状的形状是波浪形的条纹。
形成原因是因为熔融树脂冲撞到较冷的模壁,而反弹在垂直流动的方向所留下的痕迹。
15.表面剥离(层裂)系指成形品表面形成云母状薄层剥离的现象,形成表面剥离的原因,主要是不同材质塑料相混合,或成形条件设定不当所引起的。
例如一般级PS 与ABS、PE 与PP、PS 与PP 相混合来使用时,因为相互间无相熔性,所以成形后会产生表面剥离层裂的状态。
还有树脂温度太低时,流动树脂的内部会发生交界层也是造成表面剥离的原因。
四、成形品不良状况4-1充填不足(SHORT SHOT)1.与成形机有关者:(1)射出能力不足。
(改换到射出容量足够之机台)(2)喷咀与浇口未对正。
(3)材料供给量不足。
(4)喷咀堵塞。
(5)喷咀口径太小。
(6)料斗下料不顺畅。
(检查是否料筒内之干燥温度过高或是下料口处附近温度过高,而产生黏块状,堵住下料口)(7)加热料管(CYLINDER) 温度过低。
(8)射出速度过慢。
(9)射出压力过低。
2.与模具有关者:(1)浇口(GATE) 分配不平衡。
(2)下浇道(SPRUE)、横浇道(RUNNER)、进胶点(GATE) 过小。
(3)成品肉厚太薄。
(4)模温过低。
(5)排气不良。
(6)进胶口被杂质堵住。
3.与成形材料有关者:(1)材料流动性不良。
(2)润滑剂(添加剂) 不足或处理不当。
4-2毛边(FLASH)1.与成形机有关者:(1)闭模力不足(亦即合模压力不够)。
(2)材料供给量过多。
(3)树脂温度过高。
(4)射出压力过大。
(5)射出压力保持时间过长。
2.与模具有关者:(1)模具温度过高。
(2)模具表面吻合不良。
(3)模具配件(模块) 加工精度不良。
(4)模具装配精度不良。
(5)配件变形或磨耗。
(6)冷却管路不顺畅。
(7)有异物附着在模面上。
(8)模具设计不当。
3.与成形材料有关者:(1)树脂流动性过佳。
(2)树脂黏度过低。
4-3缩水(SINK MARK)1.与成形机有关者:(1)树脂供给量过小。
(2)射出成形机容量不足。
(3)树脂温度过高。
(4)冷却时间不足。
(5)射出压力过低。
(6)射出速度过慢。
(7)射出压力保持时间过短。
(8)喷咀(NOZZLE) 与浇口(SPRUE) 未对正。