第三章 连铸坯的凝固与传热
第3章 凝固过程的传热[23页]
![第3章 凝固过程的传热[23页]](https://img.taocdn.com/s3/m/0059e3a9294ac850ad02de80d4d8d15abe2300f6.png)
Tw f (t)
第二类边界条件: 给出通过物体表面的比热流随
时间的变化关系
T qx, y, z, t
n
第三类边界条件: 给出物体周围介质温度以及物
体表面与周围介质的换热系数
T = n
Tw
Tf
纯金属在铸型中凝固传热模型
K-导热 C-对流 R-辐射 N-牛顿界面换热
“三传”
所谓“三传”,即金属的凝固过程是一个 同时包含动量传输、质量传输和热量传输 的三传耦合的三维传热物理过程,而在热 量传输过程中同时存在有导热、对流和辐 射传热这三种传热方式。
t x x y y z z
λ --导热系数;
T--热力学温度; q --单位体积物体单位时间内释放的热量; c--比热容;
q L f s
t
ρ--密度;
t--时间。
对具体热场用上述微分方程进行求解时,需要根 据具体问题给出导热体的初始条件与边界条件。
初始条件: 初始条件是指物体开始导热时
第3章 凝固过程的传热
主要内容
3.1 凝固过程的传热 3.2 凝固时间的计算 3.3 液态金属凝固温度场
3.1 凝固过程的传热
3.1.1 凝固过程的传热特点
金属凝固过程中,其传热特点可简要概括为: “一热、二迁、三传”。
“一热”,即在凝固过程中热量的传输是第 一位的,是最重要的,它是凝固过程能否进 行的驱动力。
(即 t = 0 时)的瞬时温度分布。
边界条件:边界条件是指导热体表面与周围
介质间的热交换情况。
“二迁”
所谓“二迁”,是指在金属凝固时存在着 两个界面,即固—液界面和金属—铸型界 面,而这两个界面随着凝固进程而发生动 态迁移,并使得界面上的传热现象变得极 为复杂。
连铸坯凝固与传热

连铸坯凝固与传热连铸过程中铸坯的凝固和传热是连铸设备设计工艺、工艺控制和质量控制的基础,是连铸工作必须掌握的知识。
第1节连铸坯凝固传热的特点钢液在连铸过程中的凝固是一个热量释放和传递的过程,有两个特点。
*在运动(动态)过程中凝固放热*在不同时期散热和传热的方式是不同的一、连铸坯的凝固过程实质上是一个传热的过程。
钢液在转变成固态过程中是分为几个过程。
热量Q包括:1.过热:从浇注温度T C冷却到液相线温度T L放出的热量,C1(T C-T L);2.潜热:从液相线温度T L冷却至固相线温度T S放出的热量以L f表示;3.显热:从固相线温度T S冷却到环境温度To放出的热量C S(Y S-T O);大约有1/3的热量是从液态→固态放出的, 而其余热量是完全凝固后冷却放出的。
连铸过程中钢液凝固可分三个传热冷却区。
*一次冷却区:形成足够厚度的坯壳以保证铸坯出结晶器不漏钢。
*二次冷却区:使铸坯完全凝固。
*三次冷却区:空冷区。
从热平衡来看*钢水结晶器→二冷区→空冷区大约有60%的热量放出来,铸坯才能完全凝固。
这部分热量放出的速度决定了铸机的生产率和铸坯的质量。
*铸坯切割后还有40%热量要放出来,为了利用这部分热量,节约能源,采用热装直轧或连浇连轧工艺。
二钢热凝固过程是液体转变固体的加工过程凝固是发生在铸坯传热过程中的主要现象,铸坯在运动过程中凝固,实质是固——液交界面潜热的释放和传递过程。
1.凝固温度区间(T L-T S)将液体转变成固体加工过程。
这时在固——液交界面有个脆性区,其强度σ=0;收缩率ψ=0。
极易在此区产生裂纹,因此称裂纹敏感区。
固——液界面糊状区。
晶体强度和塑性都非低或称临界强度,如这时受到外力作用。
如热应力,鼓肚应力,矫直力等超上述临界值(ó为1-3N/mm2,由应变到断裂的临界应变为0.2-0.4%)产生裂纹和偏析裂纹。
2.在二冷区受喷水冷却时在这个区已凝固坯壳不断进行线收缩和坯壳温度分布不均匀性及坯壳鼓胀和夹辊不完全对中等原因,是坯壳受到机械和热应力的作用(有时是反复的)也易使铸坯产生裂纹。
第3章 凝固过程的传热(1)

液相向固相转变时还包含有弯曲固-液界面的形成(产生毛细作用)和热量的微观
熔体内形成了固体,产生一个面积为A的固-液界面,就要克服一个与之相对
运输,在合金凝固时还存在溶质的微观运输。 应的额外能量-界面能。因此,A/v值高的异质系统要比A/v值低的异质系统能量更 高,更不稳定。可以用平衡温度(熔点)来表达两相之间的相对稳定性。由毛细作 用引起的熔点温度变化(曲率过冷度)为, 其中,K是曲率, K
合金凝固组织特征不仅取决于冷却条件,而且取决于合金成分(见图1.8 所示的 Al-Cu系中Al和金属间化合物θ (Al2Cu)相之间的部分相图)。 理解不同的凝固组织如何受合金成分和凝固条件的影响非常重要。不 管凝固组织看来多么复杂,但都可以把问题简化为两种基本的凝固组织形 态,即树枝晶和共晶(包晶也以树枝状生长)。 一般情况下还会有两者的混合体。可以归 纳为: (a)纯物质:平面状或树枝状生长; (b)固溶体树枝晶 (不管有无枝晶间析出相); (c)树枝晶和枝晶间共晶; (d)共晶。 理解了这两种生长方式就可以解释几 乎所有合金的凝固组织。 铸造合金的设计前提就是获得所需的性 能和良好的铸造性(易充型、低缩孔和低热裂倾向)。
一些涉及凝固过程的重要生产环节有:铸造(连续铸造、模锭铸造、砂型铸
造、精密铸造、金属型铸造),焊接,锡焊/铜焊,快速成型过程,定向凝固等。 此外,纯物质的结晶也非常重要。例如,半导体及硅晶体制备是现代固体物
理和技术的重要部分。集成电路是所有新型电子器件(无线电、手表、计算机 等)的基础单元,制造集成电路需要大尺寸、低缺陷的单晶,而这种单晶的制 备则需要对掺杂元素的量和均匀性进行严格控制。到目前为止,这种单晶还只 能从熔体中生长。半导体物理方面的需求极大促进了凝固理论和技术的进步。 虽然铜制品的铸造可以追溯到公元前4000年。公元前1600年,中国也出现
连铸坯的凝固与传热过程研究
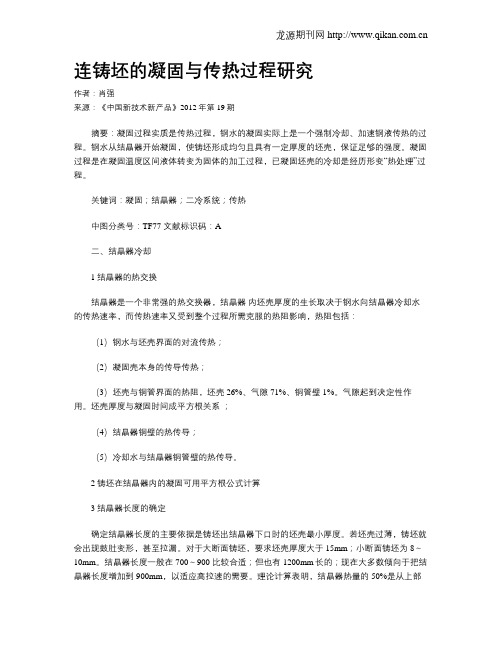
连铸坯的凝固与传热过程研究作者:肖强来源:《中国新技术新产品》2012年第19期摘要:凝固过程实质是传热过程,钢水的凝固实际上是一个强制冷却、加速钢液传热的过程。
钢水从结晶器开始凝固,使铸坯形成均匀且具有一定厚度的坯壳,保证足够的强度。
凝固过程是在凝固温度区间液体转变为固体的加工过程,已凝固坯壳的冷却是经历形变“热处理”过程。
关键词:凝固;结晶器;二冷系统;传热中图分类号:TF77 文献标识码:A二、结晶器冷却1结晶器的热交换结晶器是一个非常强的热交换器,结晶器内坯壳厚度的生长取决于钢水向结晶器冷却水的传热速率,而传热速率又受到整个过程所需克服的热阻影响,热阻包括:(1)钢水与坯壳界面的对流传热;(2)凝固壳本身的传导传热;(3)坯壳与铜管界面的热阻,坯壳26%、气隙71%、铜管壁1%。
气隙起到决定性作用。
坯壳厚度与凝固时间成平方根关系;(4)结晶器铜壁的热传导;(5)冷却水与结晶器铜管壁的热传导。
2铸坯在结晶器内的凝固可用平方根公式计算3结晶器长度的确定确定结晶器长度的主要依据是铸坯出结晶器下口时的坯壳最小厚度。
若坯壳过薄,铸坯就会出现鼓肚变形,甚至拉漏。
对于大断面铸坯,要求坯壳厚度大于15mm;小断面铸坯为8~10mm。
结晶器长度一般在700~900 比较合适;但也有1200mm长的;现在大多数倾向于把结晶器长度增加到900mm,以适应高拉速的需要。
理论计算表明,结晶器热量的50%是从上部导出的,结晶器下部只起到支持作用;因而过长的结晶器无益于坯壳的增厚,所以没有必要选用过长的结晶器。
4结晶器的倒锥度5影响结晶器传热的因素(1)坯壳、坯壳与结晶器壁之间气隙、结晶器壁、结晶器与冷却水间界面。
(2)设计参数对结晶器传热的影响结晶器锥度、结晶器长度、结晶器内表面形状、结晶器材质、结晶器壁厚度。
(3)操作工艺对结晶器传热的影响:拉速、过热度、结晶器润滑剂、结晶器冷却水流速和温度.三、二冷区冷却1 在二冷区内铸坯的冷却情况与在结晶器内有很大的不同在二冷区,主要的散热方式是表面喷水强制冷却。
板坯二车间4月铸坯凝固理论培训讲义
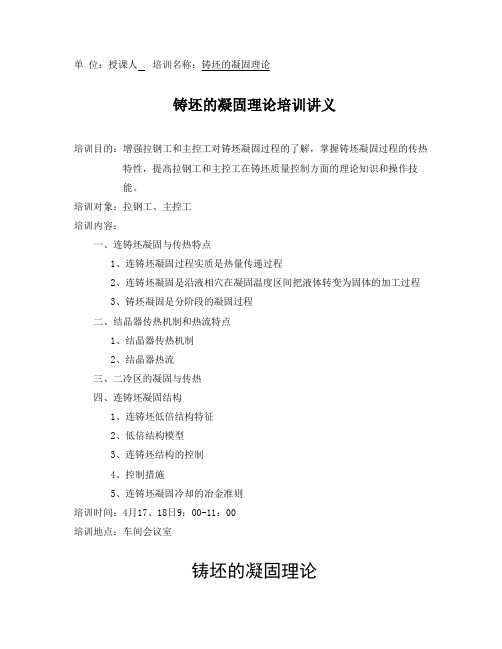
单位:授课人培训名称:铸坯的凝固理论铸坯的凝固理论培训讲义培训目的:增强拉钢工和主控工对铸坯凝固过程的了解,掌握铸坯凝固过程的传热特性,提高拉钢工和主控工在铸坯质量控制方面的理论知识和操作技能。
培训对象:拉钢工、主控工培训内容:一、连铸坯凝固与传热特点1、连铸坯凝固过程实质是热量传递过程2、连铸坯凝固是沿液相穴在凝固温度区间把液体转变为固体的加工过程3、铸坯凝固是分阶段的凝固过程二、结晶器传热机制和热流特点1、结晶器传热机制2、结晶器热流三、二冷区的凝固与传热四、连铸坯凝固结构1、连铸坯低倍结构特征2、低倍结构模型3、连铸坯结构的控制4、控制措施5、连铸坯凝固冷却的冶金准则培训时间:4月17、18日9:00-11:00培训地点:车间会议室铸坯的凝固理论一、连铸坯凝固与传热特点1、连铸坯凝固过程实质是热量传递过程过热;浇注温度TC→液相线温度TL潜热;液相线温度TL →固相线温度TS显热;固相线温度TS →环境温度TO对低碳钢,浇注温度一般控制在1540℃左右,总热量为:1386kJ/kg;过热:25.2kJ/kg,在总热量中占2%;潜热:268kJ/kg,占19%;显热:1092kJ/kg,占79%。
由此认为:钢水在连铸机中的凝固是一个热量释放和传递的过程。
2、连铸坯凝固是沿液相穴在凝固温度区间把液体转变为固体的加工过程凝固脆化区:TRN为强度σ=0的温度,零强度温度;TDN为断面收缩率ψ=0的温度,零塑性温度。
温度区间存在裂纹敏感区。
固-液交界面的糊状区可认为是裂纹敏感区。
当作用于凝固坯壳的外部应力(热应力、鼓肚力、矫直力)使其变形超过临界值,产生偏析线裂纹。
3、铸坯凝固是分阶段的凝固过程一次冷却区;(结晶器)二次冷却区;(喷水加速冷却)三次冷却区;(向空气中辐射)切割前:819kJ/kg(84,462,273)切割后:567kJ/kg在连铸——连轧生产模式时(铸坯热装),铸坯切后大约剩余40%的热量。
大方坯连铸过程中铸坯传热及凝固行为的研究

摘
要 : 晶 器 和 二 冷 区 传 热 对 大 方 坯 产 品 质 量 和 铸 机 的 生 产 率 有 重 要 影 响 , 文 讨 论 了 包 钢 引 进 的 全 国 最 大 的 结 本
方 坯 连 铸 机 在 拉 坯 时 结 晶 器 和 二 冷 区 的 传 热 情 况 以 及 坯 壳 凝 固 生 长 、 坯 温 度 的 变 化 规 律 . 重 讨 论 了 电 磁 搅 铸 着 拌 、 热 度 和 拉 速 对 坯 壳 凝 固 和 生 长 规 律 的 影 响 . 出 控 制 铸 坯 凝 固 的 主 要 因 素 是 凝 固 潜 热 , 响 凝 固 末 端 的 最 过 指 影
Jn . u e
Vo . 121. No2
文章 编 号 :04— 72 20 )2—02 —0 10 9 6 (02 0 11 6
大方 坯连 铸过程 中铸 坯 传热及凝 固行 为的研 究 。
王 宝峰 麻 永林 丁 国 李春 龙。孟 志泉。王 玉 昌。 , , , , ,
(. 头 钢铁学 院 冶金工程 研究所 , 1包 内蒙 古 包 头
Ke y wor ds:o iu u as g; l n i sldf a o EM S i i
Ab t a t T e h a rnse n mo l nd s c d c ln on so ia mp ra c o p o c vt n u lt fac se F sr c : h e tt f ri ud a e on o i gz ei fv tli o tn e t rdu t iya d q aiyo a tr. EM de se tb a i mo li sa — hs e oa a ye te h a r n fro ud a d s c d c ln o e frte bg e tbo m a tr ito c d fo De g Ge ma h d t n lz h e tta se fmo n e on o ig z n o h ig s l l c se nrdu e r m ma r ny.n u n eo If e c f l
3连铸坯的凝固
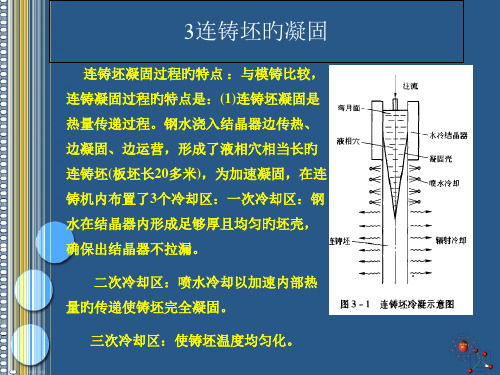
结晶器设计参数对传热旳影响
• A 结晶器锥度旳影响 • 为了使坯壳与结晶器铜壁保持良好旳接触,以减小
保护渣在结晶器内预防钢液二次氧化旳作用,主要靠保护渣液渣层来 实现。一般结晶器内液渣层厚度在8~15mm范围内,在液面稳定,水 口插入深度合理旳情况下,均能起到很好隔绝空气旳作用。
3、吸收溶解从钢水中上浮到钢渣界面旳夹杂物,净化钢液
要求保护渣具有良好旳吸收熔解夹杂物旳能力。经过以为,粘度低 夹杂物熔解速度增长,液渣旳高碱度、低SiO2、Al2O3、高Na2O、 CaF2有利于提升夹杂物旳熔解度。
3连铸坯旳凝固
连铸坯凝固过程旳特点 :与模铸比较, 连铸凝固过程旳特点是:(1)连铸坯凝固是 热量传递过程。钢水浇入结晶器边传热、 边凝固、边运营,形成了液相穴相当长旳 连铸坯(板坯长20多米),为加速凝固,在连 铸机内布置了3个冷却区:一次冷却区:钢 水在结晶器内形成足够厚且均匀旳坯壳, 确保出结晶器不拉漏。
• 在结晶器旳角部 旳传热为二维, 开始凝固最快, 最早收缩,最早 形成气隙。角部 区域坯壳最薄, 这也是产生角部 裂纹和发生漏钢 旳单薄环节。
5
4
3
2
1
结晶器旳散热
主冷却水
背板
1500
1000 °C
500 200
0铸坯壳铜板Fra bibliotek缝隙钢液
25
50
mm
结晶器壁温度分布
坯壳旳生长规律
• 被拉出结晶器旳铸坯其坯壳必须有足够 旳厚度,以防在失去铜壁支撑后变形或 漏钢。一般而言,小方坯要求出结晶器 下口处坯壳厚度应不小于8-15mm,板 坯要求厚度应为15-20mm。坯壳厚度旳 生长规律服从凝固平方根定律:
连铸工艺设备连铸坯凝固与传热培训ppt课件

21
21
最大的热阻是来自于坯壳与结晶器 壁之间的气隙。
21
结晶器横向气隙的形成:
结晶器传热示意图:
21
2.影响结晶器传热的主要因素⑴结晶器设计参数对传热的影响 A.结晶器锥度的影响
合适的倒锥度,可以减小下部气隙厚 度,改善传热。
结晶器长度以不增加拉漏为原则。通常为700~900mm。对传热影响不大。
角部成了坯 壳最薄弱的部位。
21
结晶器内气隙的形成过程:
21
坯壳急剧收缩是导致结晶器最大热流减少的原因
21
减轻弯月面区坯壳过度收缩、减少凹陷的形成的措施
21
二.结晶器坯壳生长规律结晶器内坯壳的生长规律服从平方根定律:
21
铸坯表面组织的形成:
21
促进结晶器坯壳均匀生长的操作注意事项
21
三.结晶器传热与热阻
2.弯月面的形成
10
钢液与铜壁弯月面的形成:
10
良好稳定的弯月面可确保初生坯壳的表面质量和坯壳的均匀性。带有夹渣的坯壳是薄弱部位,易发生漏钢。
10
10
4.气隙的形成、稳定及角部气隙
已凝固的高温坯壳发生δ→γ的相变,引起坯壳收缩,收缩力牵引坯壳离开铜壁,气 隙开始形成。周期 性的离合2~3次,坯壳达到一定厚度并完 全脱离铜壁,气隙稳定形成。
二冷区铸坯表面热量传递方式:
37
铸坯二冷传热方式:
37
二.影响二冷区传热的因素
54
表面温度与热流的关系:
54
54
54
三.二冷区凝固坯壳的生长
54
54
四.铸坯的液相穴深度
54
§3—4 连铸坯凝固结构
54
- 1、下载文档前请自行甄别文档内容的完整性,平台不提供额外的编辑、内容补充、找答案等附加服务。
- 2、"仅部分预览"的文档,不可在线预览部分如存在完整性等问题,可反馈申请退款(可完整预览的文档不适用该条件!)。
- 3、如文档侵犯您的权益,请联系客服反馈,我们会尽快为您处理(人工客服工作时间:9:00-18:30)。
2、坯壳及气隙的形成
注入结晶器的钢液除受结晶器壁的强制冷却外,还通过钢 液面辐射传热及拉坯方向的传导传热,使钢液形成一定厚度的 坯壳。其传出热量的比值大约为30:0.15:0.03。因此,结晶器 内钢水可近似地看作向结晶器壁的单向传热,其散热量的波动
与坯壳表面和结晶器壁的接触状况有关。
钢水热量传出途径:钢水→坯壳→气隙→结晶器铜壁→铜 板与冷却水界面→冷却水。
取24~26 mm/min1/2 ; 板坯取17~22 mm/min1/2 ; 圆坯
取20~25 mm/min1/2 。 小方坯出结晶器下口坯壳厚度8~10 mm,板坯、大方坯大于 15mm。
5、影响结晶器凝固传热的因素
研究指出:气隙热阻占总热阻的 70~90% ,因此改善结 晶器传热最重要的是减小气隙热阻。气隙的形成与演变决定 于凝固壳的收缩、坯壳高温强度、结晶器润滑和结晶器几何 形状等因素。
喷水冷 却 凝固壳
辐射冷 却
铸坯热送热装和连铸连轧等工艺。
连铸机冷却区示意图
2、连铸坯的凝固是沿液相穴在凝固温度区间 将液体转变为固体的加工过程
连铸坯可看成是液相穴很长的钢锭(板坯可达30m),以一定速度
在铸机内运动并凝固,也可看成是在凝固温度区间(TL → TS)把液体转
变为固体的加工过程。 在固—液交界面附近,存在一个凝固脆化区,此处强度、塑性接
从结晶器内凝固传热考虑,应避免高温钢水浇注。
6、确保坯壳出结晶器下口有足够厚度及均匀生 长的措施
① 浇注温度不能过高,保持低温浇注; ② 水口与结晶器严格对中; ③ 结晶器冷却水的水质、流速、水量达到要求,均匀冷却; ④ 合理的结晶器锥度;
⑤ 结晶器液面保持稳定;
⑥ 选择性能良好的结晶器保护渣,以形成均匀的保护渣膜等; ⑦ 合适的浇注速度。
3、连铸坯的凝固是分阶段的凝固过程
在连铸机内铸坯的凝固经历三个阶段: Ⅰ 钢水在结晶器内形成初生坯壳。
Ⅱ 带液心的坯壳在二冷区稳定生长。
Ⅲ 临近凝固末期的坯壳加速增长。 由凝固定律求得K值(mm/ min )分别是Ⅰ:20; Ⅱ:25; Ⅲ:27~30 钢水注流对铸坯凝固的影响: 研究表明,液相穴上部为强制循环区,循环区高度取决于注流方 式、浸入式水口类型和铸坯的断面。如方坯直孔水口的穿透深度为铸坯 厚度的4~6倍。在液相穴下部液体的流动主要是坯壳的收缩和晶体下沉 所引起的自然对流。
二、结晶器的传热与凝固
⑴ 结晶器的作用
⑵ 坯壳及气隙的形成
⑶ 结晶器钢水热量的导出 ⑷ 坯壳的生长规律 ⑸ 影响结晶器凝固传热的因素
1、结晶器的作用
结晶器是连铸机的关键部件,好比是连铸机的“心脏”, 其重要作用表现在:
①在尽可能高的拉速下保证铸坯出结晶器时形成足够厚度
的坯壳,以抵抗钢水静压力而不拉漏,这一作用决定了铸机的 生产率; ②结晶器内的钢水可将热量平稳的传导给铜板,使周边坯 壳厚度能均匀的生长,保证铸坯表面质量。
部坯壳压回铜壁,所以角部区域
的传热条件比边部差,坯壳最薄, 是产生角部裂纹和发生漏钢的薄
弱部位。
器的角部垫上倒角为45°的垫板。
结晶器横向气隙形成示意图
改善角部传热的措施:管式结晶器的四个角都是圆弧过渡;组合式结晶
注意:气隙往往在结晶器出口附近为最大。
3、结晶器钢水热量的导出
结晶器垂直方向散热很小,只考虑水平方向由冷却水带走的 热量。 钢水沿结晶器壁传给冷却水热量可表示为:Q=WCΔt=ФF
⑴ 结晶器锥度
结晶器内腔断面做成沿整个高度上大下小的形状,使其
与坯壳冷却收缩相适应,以减小气隙,有利于增加热流和出 结晶器坯壳厚度,提高拉速。但倒锥度必须合适。
⑵ 结晶器保护渣
结晶器润滑一般采用保护渣,保护渣在结晶器液面上形成液 渣层,液渣沿弯月面渗漏到坯壳与铜壁之间的气隙中,形成均匀 渣衣,既起润滑作用又改善传热。但保护渣性能要好,特别是要 有合适的粘度。
液相穴内液体流动对铸坯结构、夹杂分布、溶质元素偏析和坯壳的
生长有重要作用。
4、已凝固坯壳的冷却可看成是经历“形变热处 理”过程
已凝固坯壳在连铸机内运行的过程中,从力的方面看,它承受 热应力和机械力的作用,使坯壳发生不同程度的变形;从冶金方面 看,随温度的下降,坯壳发生δ→γ→α的相变,特别是二冷区,坯 壳温度的反复下降和回升,使铸坯组织发生变化,这就相当于“热 处理”过程。 另外,由于溶质元素的偏析作用,可能发生硫化物、氮化物质 点在晶界沉淀,增加了钢的高温脆性,对铸坯质量有重要影响。
连铸机可分为三个传热冷却区: ①一次冷却区 钢水在水冷结晶器中形成足
弯月面 水冷结 晶器
够厚的坯壳,以保证铸坯出结晶器不拉漏;
②二次冷却区 指扇形段辊子冷却系统的喷
液相穴
水冷却区,喷水加速铸坯内部热量的传递,
使铸坯完全凝固;
③三次冷却区 铸坯向周围空气中辐射传热, 使铸坯内外温度均匀一致。 调查表明:铸坯在切割之前放出热量约 50%;切割之后还有 50%的热量放出,为 利用这部分能量,节约能源,成功开发了
铸坯在二冷区传热方式示意图
在设备和工艺条件一定时,铸坯辐射传热和辊子传导传热变化不
大,占主导地位的是喷雾水滴与铸坯表面之间的热交换。 从二冷的传热方式可说明,要提高二冷区的冷却效率,就必须研 究喷雾水滴与高温铸坯之间的热交换。可用对流传热方程来表示:
hS W
Ф━热流;h━传热系数;Ts━铸坯表面温度;Tw━冷却水温度
③凝固壳与结晶器壁的传热。其传热取决于坯壳与铜壁的接
触状态。在坯壳收缩产生气隙后为辐射与对流传热,气隙传 热很差,热阻很大。传热系数约为0.2W/cm2〃℃ ④结晶器壁热传导。其传热好,热阻很小,传热系数约为 2W/cm2〃℃。 ⑤冷却水与结晶器壁的强制对流传热。其传热最好,热阻最 小。传热系数约为4W/cm2〃℃ 注意:据测量在结晶器弯月面处导出的热量最多。
根据计算,各段热阻比例约为:坯壳26%;气隙71%;结
晶器铜壁1%;铜壁与冷却水界面2%,可见气隙是结晶器中钢 液向外传热的限制性环节。
热量传出方向
R6 R1 R2
R3
冷却水
R5
R4
结晶器热阻
1 结晶器铜壁 2 气隙 3 保护渣膜 4 坯壳 5 钢液
⑴ 弯月面及初生坯壳的形成
钢水注入结晶器后,在钢水 表面张力的作用下,钢水与结 晶器铜壁一接触就形成一个半 径很小的弯月面。 在半径为r的弯月面根部,由 于水冷铜壁的激冷100℃/s,初 生坯壳迅速形成。
⑶ 钢水成分
当 钢 中 碳 含 量 在 0.12% 时 , 热 流 密 度 最 低 。 原 因 是 在 1390℃以上钢发生δ→γ的相转变,并伴随强烈的收缩 0.38% , 产生较大的气隙; 虽然初期坯壳中P、S偏析最小,高温强度高,但坯壳收缩后
在钢水静压力作用下与铜壁接触不均匀,致使坯壳表面粗糙。
2 二冷区的传热方式
二冷传热的主要方式和比例: 传热方式 喷雾水滴蒸发 喷雾水加热 铸坯辐射 辊子传导 约占比例 % 33 25 25 17
喷淋 冷却
夹辊
辐射
25%
水的蒸发 水的加热
33%
25%
对小方坯二冷区主要是辐射和喷雾 水滴蒸发两种传热方式,而对大方坯 和板坯则是上述四种传热方式。
夹辊
传导
17%
式中 Q —— 通过结晶器散出的热量;
W —— 冷却水流量; C —— 水的热容; Δt —— 冷却水温升 Ф —— 结晶器平均热流
F ——结晶器有效传热面积
钢水热量传给冷却水需经历以下步骤: ① 钢水与坯壳的对流传热。传热系数约为1W/cm2〃℃ ②凝固壳的传导传热。传热较差,传热系数约为 0.3W/cm2〃℃
c 及时清除弯月面的浮渣,以防拉漏。
⑵ 气隙的形成
已凝固的高温坯壳,因发生
液面
δ→γ的相变,使坯壳向内收缩而脱
离结晶器壁,气隙开始形成,但不 稳定。
结 晶
钢
气隙(凝固收缩) 膨胀(回热)
器
水
因为气隙的热阻很大,脱离铜
壁的坯壳因得不到足够的冷却而开 始回热,坯壳强度降低,在钢水静
凝壳
压力作用下坯壳又贴向铜板。
液体金属 钢水与铜壁弯月面的形成 r
结晶器
弯月面形成的作用:对初生
坯壳非常重要,良好稳定的弯月 面可确保初生坯壳的表面质量和
坯壳的均匀性。
为什么?
弯月面处夹杂物对坯壳形成和表面质量的影响:当钢水中上浮
的夹杂物未被结晶器保护渣吸附时,弯月面处夹杂会降低钢液表 面张力,弯月面半径减小,使弯月面薄膜失去弹性作用,弯月面 破裂,夹杂物牢牢地粘附在初生坯壳上形成表面夹渣,影响铸坯 表面质量;另外带夹渣的坯壳很薄弱,容易发生漏钢事故。 保持弯月面稳定状态的措施: a 根本的措施是提高钢水的纯洁度,减少夹杂物含量; b 选用性能良好的结晶器保护渣,吸附弯月面上的夹渣物,以保 持弯月面薄膜的弹性;
4、坯壳的生长规律
在结晶器长度方向上坯壳增厚的规律服从凝固平方根定律:
K凝 t
δ—坯壳厚度,mm;
K凝
Lm vc
Lm—结晶器有效长度,m;
t—凝固时间,min;
K凝—凝固系数,mm/min1/2 ; Vc— 拉速,m/min.
影响坯壳厚度的因素: K凝值、结晶器长度Lm及拉速Vc 。 K凝值的大小主要受结晶器冷却水、钢水成分和温度、结晶器形 状参数、保护渣性能等因素的影响,较为复杂,波动较大。 通常结晶器K凝值:小方坯可取18~20 mm/min1/2 ;大方坯
近零,为裂纹敏感区,如应变超过临界应变值就会产生裂纹。
另外,铸坯在从上往下运行过程中,受喷水冷却,坯壳温度分布 的不均匀性、鼓肚和夹棍的不对中,也易使凝固坯壳产生裂纹。 保证获得良好铸坯的措施:从铸机设计和维护方面,尽可能保持铸 坯在运行过程中凝固壳不变形;从传热方面,控制好铸坯在不同冷却区 热量导出速度和坯壳的热负荷适应于钢高温性能的变化。因此,可以说 控制铸坯的传热是获得良好铸坯质量的关键操作。