铝合金低压铸造知识整理
铝合金车轮低压铸造工艺讲解
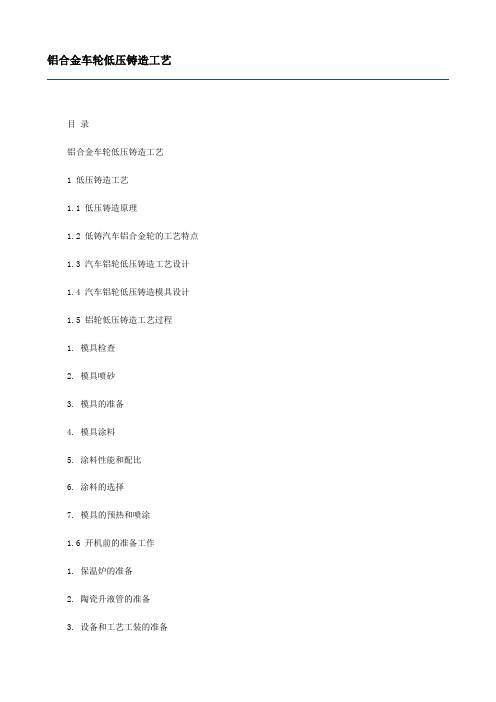
铝合金车轮低压铸造工艺目录铝合金车轮低压铸造工艺1 低压铸造工艺1.1 低压铸造原理1.2 低铸汽车铝合金轮的工艺特点1.3 汽车铝轮低压铸造工艺设计1.4 汽车铝轮低压铸造模具设计1.5 铝轮低压铸造工艺过程1. 模具检查2. 模具喷砂3. 模具的准备4. 模具涂料5. 涂料性能和配比6. 涂料的选择7. 模具的预热和喷涂1.6 开机前的准备工作1. 保温炉的准备2. 陶瓷升液管的准备3. 设备和工艺工装的准备1.7 铝车轮低压铸造液面加压规范1. 加压规范的几种类型2. 铝车轮低压铸造加压规范的设定3. 设计铝轮低铸加压曲线的步骤4. 铝轮低铸工艺曲线实例1.8 铸件缺陷分析,原因及解决办法1. 疏松(缩松)的形成与防止2. 缩孔的形成与防止3. 气孔的形成与防止4. 针孔的形成与防止5. 轮毂的变形原因及防止6. 漏气的产生原因及防止7. 冷隔(冷接,对接),欠铸(浇不足,轮廓不清)的形成与防止8. 凹(缩凹,缩陷)的形成与防止铝合金车轮低压铸造工艺铝合金车轮制造技术是多种多样的,而铝车轮的铸造工艺,目前主要有两种:一种是金属型重力铸造,一种是低压铸造。
我们主要是做汽车铝合金车轮,制造工艺采用的是低压铸造。
我们教材面向的对象主要是我们公司的员工,所以对工艺技术的介绍是有针对性的,介绍的方法也是不一样的。
1 低压铸造工艺1.1 低压铸造原理低压铸造是将铸型放在一个密闭的炉子上面,型腔的下面用一个管(叫升液管)和炉膛里的金属液相通。
如果在炉膛中金属液面上加入带压力的空气,金属液会从升液管中流入型腔。
待金属液凝固以后,将炉膛中的压缩空气释放,未凝固的金属从升液管中流回到炉中。
控制流入炉膛空气的压力、速度,就可以控制金属流入型腔中的速度和压力,并能让金属在压力下结晶凝固,压力一般不超过 1 ??/。
这种工艺特点是铸件在压力下结晶,组织致密,机械性能好;低压另一个特点就是用一个升液管将铸型直接和炉膛连通,在压力的作用下,直接浇注铸型,不用冒口,浇口也很小。
铝合金低压铸造技术

铝合金低压铸造技术随着我国经济的快速发展,铝合金在房屋建铸中的应用越来越广泛,在生产铝合金上,当前应用最广泛的依旧是低压铸造技术,这种技术不仅成本较低,而且操作起来也比较简单。
本文先介绍了低压铸造路合金的基本原理与特点,然后详细分析了路合金低压铸造的过程以及发展前景。
标签:铝合金;低压铸造;生产流程铝合金是非常常用的铸件材料,被应用建铸、机械设备、艺术创作各个方面。
在铝合金的生产上,最常见的生产工业是低压铸造工艺,主要是指铝液在压力的作用下,完成充型与凝固的过程,利用该铸造工艺不仅能使铝合金获得较高的强度,还能塑造出各种复杂的铸件,使金属材料的利用率提高。
1铝合金低压铸造原理及特点铝合金中由于各组元的不同,合金会表现出不同的物理性能及化学性能,并且合金结晶的过程也不尽相同。
因此,在进行铝合金铸造时,必须针对铝合金的特性,选择合理的铸造方法,以便优化铸件。
1.1 低压铸造原理铝合金低压铸造的原理是将干燥的空气压缩到一个密封的容器中,容器中事先装有铝液,铝液在气体压力的作用下就会沿着深液管铸件上升,通过铸型浇口平稳的进入到铸件的腔内,在铸液过程中,铝液的气体压力一直保持同一水平,一直到铝液完全凝固后终止。
在铝液完全凝固后,就可以接触铝液表面的气体压力,使多余的铝液返回到容器中,铸型内凝固的铝液形状就是最终所需要的铸件。
因为该工艺所需要的容器压力较低,故被称为低压铸造工艺。
1.2 低压铸造特点低压铸造的特点是成分简单,铸造性能好,能够很方便的进行铸造,在铸造过程中也可以自由的控制压力与铝液的流速,这中铸造工艺可以应用于其他的浇铸作业中。
低压铸造所使用的容器是底注式充型容器,铝液的金属液面能够保持平稳的状态,在铸造过程中不存在溅射的情况,因此在铸造时也就能够避免卷入气体或者颗粒粉尘的情况,提高逐渐的密实度与合格率。
因为铸件是在空气压力的作用下完成凝固的,所以铸件的轮廓往往会比较清晰,表面呈光滑状,铸件的力学性能较高,这有利于大薄壁的铸型。
铝合金低压铸造

低压机
机架
坩埚炉
实用精品培训课件PPT
池式
16
实用精品培训课件PPT
17
实用精品培训课件PPT
18
实用精品培训课件PPT
19
低压机控制台
实用精品培训课件PPT
20
控制
实用精品培训课件PPT
21
控制面板
实用精品培训课件PPT
22
控制曲线
实用精品培训课件PPT
23
保温炉温度显示
实用精品培训课件PPT
4:附助装置(含尾气处理装置、平台、气罐等);
实用精品培训课件PPT
36
冷芯制芯车间
冷芯制芯车间
冷芯机
实用精品培训课件PPT
37
发生器
控制柜
实用精品培训课件PPT
38
实用精品培训课件PPT
39
实用精品培训课件PPT
40
实用精品培训课件PPT
41
实用精品培训课件PPT
42
实用精品培训课件PPT
求比较高)
5:只能生产型腔简单的铸件(目前) 6:只能生产中小型铸件
7:生产效率高 8:铸件内部有气孔 9:铸件不能热处理强化
实用精品培训课件PPT
4
低压铸造的原理图
实用精品培训课件PPT
5
工艺流程
1:熔化工艺流程 2:低压铸造工艺流程 3:模具准备工艺流程(浇注模具) 4:热芯工艺流程 5:壳芯工艺流程 6:冷芯工艺流程 7:震动去芯工艺流程
43
实用精品培训课件PPT
44
混砂机
实用精品培训课件PPT
45
实用精品培训课件PPT
46
实用精品培训课件PPT
低压铸造法的指导手册
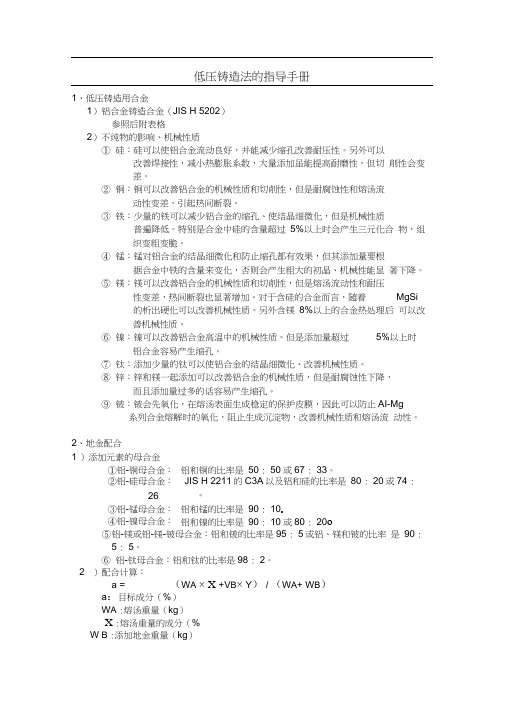
低压铸造法的指导手册1、低压铸造用合金1)铝合金铸造合金(JIS H 5202)参照后附表格2)不纯物的影响、机械性质①硅:硅可以使铝合金流动良好,并能减少缩孔改善耐压性。
另外可以改善焊接性,减小热膨胀系数,大量添加虽能提高耐磨性,但切削性会变差。
②铜:铜可以改善铝合金的机械性质和切削性,但是耐腐蚀性和熔汤流动性变差,引起热间断裂。
③铁:少量的铁可以减少铝合金的缩孔、使结晶细微化,但是机械性质普遍降低。
特别是合金中硅的含量超过5%以上时会产生三元化合物,组织变粗变脆。
④锰:锰对铝合金的结晶细微化和防止缩孔都有效果,但其添加量要根据合金中铁的含量来变化,否则会产生粗大的初晶、机械性能显著下降。
⑤镁:镁可以改善铝合金的机械性质和切削性,但是熔汤流动性和耐压性变差,热间断裂也显著增加。
对于含硅的合金而言,随着MgSi的析出硬化可以改善机械性质。
另外含镁8%以上的合金热处理后可以改善机械性质。
⑥镍:镍可以改善铝合金高温中的机械性质。
但是添加量超过5%以上时铝合金容易产生缩孔。
⑦钛:添加少量的钛可以使铝合金的结晶细微化、改善机械性质。
⑧锌:锌和镁一起添加可以改善铝合金的机械性质,但是耐腐蚀性下降,而且添加量过多的话容易产生缩孔。
⑨铍:铍会先氧化,在熔汤表面生成稳定的保护皮膜,因此可以防止AI-Mg系列合金熔解时的氧化,阻止生成沉淀物,改善机械性质和熔汤流动性。
2、地金配合1 )添加元素的母合金①铝-铜母合金:铝和铜的比率是50 : 50或67 : 33。
②铝-硅母合金:JIS H 2211的C3A以及铝和硅的比率是80 : 20或74 :26③铝-锰母合金:。
铝和锰的比率是90 : 10o④铝-镍母合金:铝和镍的比率是90 : 10或80 : 20o⑤铝-镁或铝-镁-铍母合金:铝和铍的比率是95 : 5或铝、镁和铍的比率是90 :5 : 5。
⑥铝-钛母合金:铝和钛的比率是98 : 2。
2 )配合计算:a = (W A × X +V B×Y)/ (W A+ W B)a:目标成分(%)W A :熔汤重量(kg)X :熔汤重量的成分(%W B :添加地金重量(kg)丫:添加地金的成分(%3、熔解作业1 )熔解方法熔解时最需要注意的是气体吸收和氧化。
[化学]铸造铝合金及低压铸造知识
![[化学]铸造铝合金及低压铸造知识](https://img.taocdn.com/s3/m/3801da0748d7c1c708a145c3.png)
h
34
二、AL-SI合金的熔炼
• 按作用机理的不同,精炼工艺可分为吸附精炼和非吸附精 炼两大类。
• 1、吸附精炼 • 吸附净化是指通过铝液直接与吸附剂(如各种气体、液体、
• 通氮温度控制在710℃~720 ℃,并且氮气中一定不能有 水蒸气。氮气在通入铝液之前要通过干燥器处理,进行严 格的脱水处理。
h
37
h
38
h
39
三:铝硅合金的变质和细化
• 变质前的力学性能低,切削性能差,必须 进行变质处理,使板片状的共晶硅转变成 纤维状,并消除初晶硅。
• 变质方法:加入变质剂(变质元素有Na、 Sr、Ba、Sb、Re)。
h
15
• 铝硅二元相图(状态图): • 共晶温度为577℃, • 共晶点的硅含量为12.6%, • 共晶温度时硅的溶解度最大,可达1.65%, • 在室温只有0.05%
h
16
• 356 • A356.0 • A356.1 • A356.2 • ZL101A • AC4CH
h
17
h
18
• Si含量对中金的影响
h
25
Cu、Zn对合金的影响 Cu会使A356合金的伸长率和耐蚀性降低;
锌 (Zn)也会降低合金的耐蚀性。 因此,炉料中应尽量避免Cu元素和Zn元素的混入。
h
26
二、AL-Si合金的熔炼
• 铝合金熔炼基本工艺流程: • 配料——预热——加料——熔化——调整成分——出炉——
调整成分——除气——除渣——静置——浇注
[化学]铸造铝合金及低压铸造知识
![[化学]铸造铝合金及低压铸造知识](https://img.taocdn.com/s3/m/3801da0748d7c1c708a145c3.png)
h
23
• Mn对合金的影响
• Mn可以在铝合金热处理时起到固熔强化的作用,同时可 以改变针状的富Fe相的形状,形成骨架状的相,改善塑性。 但对于Fe≤0.1%的高纯合金,加Mn将形成(Fe、Mn)Al6, 降低塑性。
h
24
• Mn对合金的影响
• Mn可以在铝合金热处理时起到固熔强化的作用,同时可 以改变针状的富Fe相的形状,形成骨架状的相,改善塑性。 但对于Fe≤0.1%的高纯合金,加Mn将形成(Fe、Mn)Al6, 降低塑性。
度不宜过低。多次重熔炉料要适当控制。 • 2)炉料要烘干燥、干净,去除锈及油污。 • 3)熔炼及浇注工具要烘干。 • 4)金属型必须干净,要预热至规定温度。 • 5)可在适当位置加排气塞。
h
34
二、AL-SI合金的熔炼
• 按作用机理的不同,精炼工艺可分为吸附精炼和非吸附精 炼两大类。
• 1、吸附精炼 • 吸附净化是指通过铝液直接与吸附剂(如各种气体、液体、
• 通氮温度控制在710℃~720 ℃,并且氮气中一定不能有 水蒸气。氮气在通入铝液之前要通过干燥器处理,进行严 格的脱水处理。
h
37
h
38
h
39
三:铝硅合金的变质和细化
• 变质前的力学性能低,切削性能差,必须 进行变质处理,使板片状的共晶硅转变成 纤维状,并消除初晶硅。
• 变质方法:加入变质剂(变质元素有Na、 Sr、Ba、Sb、Re)。
h
3
一、铝及铝合金的基础知识
合金: 是两种或两种以上的金属或金属元素与非金属元素熔合 在一起所得到的具有金属特性的物质。
相: 合金中具有同一化学成份、同一聚集状态并以界面互相分 开的各个均匀的组成部分。合金中所有的相可分为固溶体 和金属化合物两大类。
铝合金低压铸造

7:生产效率高 8:铸件内部有气孔 9:铸件不能热处理强化
低压铸造的原理图
工艺流程
1:熔化工艺流程 2:低压铸造工艺流程 3:模具准备工艺流程(浇注模具) 4:热芯工艺流程 5:壳芯工艺流程 6:冷芯工艺流程 7:震动去芯工艺流程
铝合金熔化工艺流程
2:喷砂机(含喷砂房、除尘器、模具放置小车、压送罐、 喷砂枪)
3:主要作用:用来清理模具表面的过期涂料层及新模具表 面的油污等杂物。
铸造模具(1)
常用铸造模具的分类 1:砂型铸造用模具 2:特种铸造模具 3:精密铸造模具 金属型低压铸造模具 1):金属型低压铸造模具的结构
金属型低压铸造模具一般可分为:上模、下模、侧模、 及抽芯(模具结构中可以没有侧模、抽芯);
件(可以生产200kg以上铸铝件) 7:生产效率比高压铸造低 8:铸件内部没有气孔 9:铸件可以热处理强化
高压铸造 1:压力高,可达到上百兆帕
2:金属液在行腔中的速度快,可达到 60m/s,最高可到120m/s.金属液 对型腔的冲刷大
3:金属液在型腔的流动不平稳 4:型腔只能是金属型(对型腔材料要
求比较高)
铝合金低压铸造
主要内容:
一 :低压铸造介绍: 1:铝合金低压铸造在我国的发展状况; 2:低压铸造的特点; 3:铝合金低压铸造与铝合金压铸的区别;
二:低压铸造 : 1:低压铸造的原理; 2:低压铸造的工艺流程;
三:低压铸造机及主要附属设备的: 1:低压机铸造机; 2:制芯设备; 2.1:冷芯机; 2.2:壳芯机; 2.3:热芯机; 3:振动去芯机; 4:模具预热炉、喷砂机
3:制芯系统(冷芯盒射芯机、三乙胺发生器); 冷芯盒射芯机(含射砂机构、吹气机构与上顶芯机构 一体、开合模机构、下顶芯机构)
铝合金铸造基础-2

• 充型速度低,造 成层流状双层膜
• 浇注系统设计不良造 成铸件四处存在双层
膜缺陷,力学性能大 大降低
双层膜卷入例子
• 一旦氧化膜破坏,铝合金液会与环境气体发生剧烈反应: • 在铝合金液静止时,上述反应基本只发生在其接触面上。 • 当铝合金液表面膜破裂,环境空气会被卷入到铝合金液里
面; • 氧化膜的卷入造成双层膜进入铝合金液中 • 只要没有氧化膜破坏或双层膜卷入,铝合金液能保持纯净
• 铝合金液两大克星:氧化膜破坏与水/油接触,氧化膜被机 械性地卷入形成双层膜
3H2O+2AL=AL2O3+6[H] • 因此铝锭不宜储存在潮湿的库房内或在雨季露天堆放。
铝合金与环境的反应
• 氧: --氧与固态/液态铝収生剧烈反应生成 Al2O3(铝粉末在空气中会爆炸); 4AL+3O2=2A2O3 --铝表面的氧化膜Al2O3有钝化作用, 可阻止铝进一步氧化 •氢 --氢溶亍铝,不与铝収生反应。 •油 --油污等碳氢化合物与液态铝収生反应 4/3mAl+CmHn=1/3mAl4C3+1/2nH2
任一截面处,单位体积内的动能、势能及压强之和保持不变, 即单位体积内总能量是一恒量
二、避免金属液上表面膜的湍流卷入
• 底注时铝合金液经过内浇口的临界速度为0.5m/s; • 超过临界速度,铝合金 液会卷入双层膜。卷入缺 陷是空气气泡和 氧化膜; • 速度越大,双层膜卷入 越严重; • 氧化膜折叠形成双层膜, 双层膜中包裹着空气泡。
氧,镁,锶氧化物等 c)固体夹杂物
涂料,氧化皮等
一、获得纯净的金属液
如图所示的平衡图: 在1大气压的水蒸汽环 境中, 750°C的铝 合金液中H含10ml/kg 相对湿度为30%的环 境中,750°C的铝 合金液中H含1ml/kg; 如果铝中有杂质,则氢 含量会高得多
- 1、下载文档前请自行甄别文档内容的完整性,平台不提供额外的编辑、内容补充、找答案等附加服务。
- 2、"仅部分预览"的文档,不可在线预览部分如存在完整性等问题,可反馈申请退款(可完整预览的文档不适用该条件!)。
- 3、如文档侵犯您的权益,请联系客服反馈,我们会尽快为您处理(人工客服工作时间:9:00-18:30)。
第一章铝合金低压铸造知识整理2.1低压铸造概论2.1.1低压铸造定义铸型一般安置在密封的坩埚上方,坩埚中通入压缩空气,在熔融金属的表面上造成低压力(0.06~0.15MPa),使金属液由升液管上升填充铸型和控制凝固的铸造方法。
2.1.2基本原理在密闭的保持炉的熔汤表面上施加0.01~0.05Mpa的空气压力或惰性气体压力,熔汤通过浸放在熔汤里的给汤管上升,被充填进连接着的炉子上方的模具内。
因此熔汤是从型腔的下部慢慢开始充填,保持一段时间的压力后凝固。
凝固是从产品上部开始向浇口方向转移,浇口部分凝固的时刻就是加压结束的时间。
然后冷却至可以取出产品的强度后从模具中脱离。
于是就凭借浇口的方向性凝固和从浇口开始的冒口压力效果得到了完美的铸件。
低压铸造装置如图1所示。
缓慢地向坩埚炉内通入干燥的压缩空气,金属液受气体压力的作用,由下而上沿着升液管和浇注系统充满型腔,如图1b所示。
开启铸型,取出铸件,如图1c所示。
图12.1.3与其他铸造法的比较与压力铸造比较:1)低压铸造适用的合金范围广,而压力铸造一般只适用于铸造性能较好的合金;2)压力铸造一般用于生产批量大的中小铸件,而低压铸造可适用于不同大小,不同批量的铸件;3) 压力铸造是在高速高压下充型,型腔中的气体不易被排除,易于产生气孔,而低压铸造则与此相反;4) 低压铸造的设备比压力铸造的设备简单,制造容易;5) 低压铸造比压力铸造生产效率低。
与金属型铸造比较:1) 低压铸造可以大大简化浇注系统;2) 低压铸造更易于实现机械化自动生产;3) 低压铸造的设备比金属型铸造稍高。
与一般砂型重力铸造比较1) 低压铸造浇包中的合金液自下而上的从底部注入型腔,浇注平稳,因此成品率比砂型铸造高;2) 低压铸造是在低压下充型,又在较高的压力下结晶凝固,使铸件的组织、机械性能、气密性、耐压性能均比砂型重力铸造好;3) 低压铸造浇注系统比砂型重力铸造简单,并可以大大减小冒口,有的铸件甚至可以不设置冒口,从而简化了工艺,节省了金属材料;2.2 铝合金低压铸造工艺铝合金低压铸造的工艺过程如图2所示。
图22.2.1铸型种类的选择1)铸型质量精度要求高,形状一般,生产批量较大的有色金属铸件,可选用金属型或石墨型。
2)铸型内腔结构复杂,不能用金属芯时,可采用砂芯。
3)铸件的精度要求不高的大型铸件在生产批量不大时或小于批量生产,可采用砂型。
4)铸件精度要求较高结构有很复杂时可用熔模壳型、石膏型。
2.2.2铸件凝固方式的选择充型时,液态金属从内浇口引入,并由上而下地充填铸型;凝固过程中,升液管中的炽热金属液经由浇注系统向铸件提供补缩。
为了充分体现低压铸造方法中铸件在一定的压力作用下结晶,获得的铸件组织致密的优点,充分发挥升液管的补缩作用,针对低压铸造的特点,通常情况下,实现“自上而下顺序凝固”的方式是历来公认的原则。
2.2.3金属型壁厚的确定金属型壁厚的选择与许多因素有关。
问题比较复杂,所以,到目前为止仍然是根据经验数据来确定的。
参考数据如表1所示。
表1 铝合金铸件金属型壁厚(mm)铸件的平均厚度3—5 5—6 6—8金属型的最小壁厚15—20 20—25 25—30 2.2.4浇注系统的选择1)浇口面积的大小是作为不引起熔汤乱流的截面积,内浇口最小面积计算公式如下:a=G×1000/t×u×r×√(2×g×h)a—浇口的最小面积G—含浇口的铸件重量(kg)t —到浇口之前的浇铸时间(sec)u —阻力系数(0.3-0.4)r —熔汤的比重(2.3-2.4)g —重力加速度9.8m/sh —从熔汤面到铸件上部的高度cm2)应充分发挥浇注系统的补缩作用,为此保证截面积:升液管出口>横浇道>内浇道。
3)尽量避免液态金属直接冲击型壁和型芯(尤其是热导率大的部位),以防止局部过热。
4)当有多个内浇道与横浇道相连时,为了使各内浇道流量分配的均匀,应根据具体的情况来确定各个内浇道的面积。
一般说来,远离升液管的盲端及紧靠升液管的内浇道面积较小。
5)在生产较大的等壁厚铸件时,当金属型壁厚设计合理,并保证能够充填性的前提时,应将内浇道开设在铸件的短边面的中部,以便造成高度上的单向的温度梯度,从而有利于补缩的进行。
此时,内浇道的开设应使充型的液态金属均匀的注入型腔,避免减少横向液流,达到减小或消除水平方向的温度梯度。
6)连接升液管与铸型的输液通道的管壁应尽可能薄些,以减少液态金属在该处的热量损失,这有利于补缩的进行。
7)应尽量减少用设置在充型末端,由冷金属液聚集而成的冒口。
这样的冒口补缩效率低,并有出现“倒补缩”的危险。
2.2.5分型面的选取1)分型面应尽量是一个平面。
2)尽可能不使分型面通过铸件本身,即将铸件尽量放在一侧型腔中。
3)尽可能使活块数量减少。
4)尽可能减少型芯数量,并使其安装方便稳固。
5)使起模斜度尽可能地小,以保证铸件尺寸精度。
6)便于安放冒口,并利于型内气体的排出。
7)便于铸件取出,不致拉裂或变形。
8)便于铸件顺序凝固,保证补缩,以使其组织致密。
2.2.6铸型的排气在低压铸造中,要特别注意型腔中气体的排出。
一般低压铸造没有冒口,顶部又是封闭的,所以铸型排气更显得重要。
砂型低压铸造除了砂型本身具有透气性外,还可考虑在铸型顶部扎细的通气眼或设通气芯子。
对于金属型低压铸造的型腔排气可采用下述措施:1)在分型面上开排气槽,它既能迅速地排出型腔中的气体,又不使合金液从排气槽中溢出。
常在分型面开设片状缝隙和三角形排气槽。
目前,金属型的排气槽的尺寸选择还是根据经验数据进行的。
对于铝合金,片状缝隙排气槽的厚度一般为0.5mm,宽度为10~15mm;三角形排气槽的尺寸:深度一般为0.3~1.0mm,两边夹角为60~90°,间距一般取10mm。
2)在型腔的凹处及个别凸起部分应打入排气塞。
●当凹面是圆形的搭子时,则按圆的直径大小安排排气塞。
圆的直径在25mm以内按一只塞子就行了。
如果圆的直径太大,则应该专门设计一个大的排气塞,中间再套一个小的排气塞。
●当凹面为非圆形的搭子,不论其凹面朝上、朝下或是垂直于水平面,均须安排气塞。
3) 利用金属型与型腔连通的各配合面如芯座、活块、顶杆等开设排气槽。
4) 利用拼块模具排气。
5) 除了排气塞,排气槽以外,也可以在需要的大平面上开设蓄气槽;或在金属型工作表面喷涂一定厚度的涂料,涂料层中的孔隙具有一定的蓄气作用和排气作用。
2.2.7 机械加工余量的选择铸件的加工余量与所采用的铸型材料有关。
一般砂型的尺寸精度和表面粗糙度都较差,铸件需放较多的加工余量,而金属型和石墨型的尺寸精度和表面粗糙度较高,铸件的加工余量可以减少,一般可取0.5~4mm 。
加工余量的选取还需考虑以下因素:1) 加工表面的粗糙度要求越小时,所留的机械加工余量应越大。
2) 尺寸精度要求越高时,对该尺寸的加工余量越大。
3) 加工面的面积越大时,机械加工余量越大。
4) 加工表面距离机械加工基准面越远时,机械加工余量越大。
5) 如有砂芯,那么由砂芯形成的铸件表面部分的机械加工余量应大于由金属型(芯)直接形成的铸件表面部分的机械加工余量。
6) 冒口或浇口和铸件连接的表面,其加工余量应该放大一些。
7) 下表面、侧表面、上表面的加工余量应依次适当加大。
2.2.8 金属型型腔尺寸的确定金属型型腔及型芯尺寸的确定,除根据铸件外形和内腔的公称尺寸以外,还要考虑到铸件的线收缩、涂料层的厚度、以及金属型材料从室温升至预热温度时的膨胀率。
金属型型腔和型芯的尺寸可用以下公式确定:()2x p p x A A A K A δ=++±∆()2x p p x D D D K D δ=+-±∆x A 、x D —型腔、型芯的尺寸;p A 、p D —件外形、内孔的公称尺寸;K —综合线收缩率;δ—涂料层厚度(一般取0.1~0.3mm )x A ∆、x D ∆—金属型制造公差对于铝合金铸件,综合线收缩率可参考表2确定。
表2 不同情况下的K 值受阻情况K ×100 有型芯、无阻碍有型芯、有阻碍有邻近二凸台0.8~1.2 0.7~0.9 0.5~0.72.2.9 金属型的合型力、抽芯力以及开型力 1) 合型力的确定 采用金属型进行低压铸造时,为保证工艺过程的顺利进行,铸型除具有足够的强度、刚度外,合型之后,对铸型的分型面还应施加足够的锁紧力(合模力)。
根据帕斯卡原理,锁紧力必须大于增压阶段液态金属在合模方向上对分型面的总压力,即p kp F =∑合式中 F ∑—铸件(包括浇注系统)在合模方向上的正投影面积之和p —增压阶段最高压力(Kpa )k —安全系数,一般取值为1~1.3。
.2) 抽芯力的确定 根据铸件结构特点,低压铸造用的金属型有时也设有抽芯机构,以便开型时及时从铸件中将活动芯或活块取出。
此时要预先计算所需要的抽芯力的大小。
其大小可用下面的经验公式计算:c m b p F p LKμ=+ 式中c p —抽芯力(N );m μ—考虑到摩擦阻力的系数,对于铝合金为0.25;b F —被铸件包住的型芯部分表面积(㎡); p —挤压应力,对于铝合金,单面铸造斜度1%(约40′)时,为10MPa ; L —铸件包紧型芯的长度(m )K —常数,依合金种类及铸件包紧型芯处的厚度,对铝合金,壁厚为3~5mm 时,K 取70,壁厚大于5mm 时,K 取140。
3) .开型力的确定 影响开型力的因素很多,一般是根据生产中积累的经验数据来进行计算,有如下经验公式可用于开型力的估算:P F p =⨯式中 F —型腔在分型面上的投影面积(㎡)P —型腔在分型面上的投影单位面积所需的开型力(铝合金值如表3)表3 铸铝时的p 值铸件的类型简单 一般 复杂 P/MPa0.5~1.0 >1.0~1.5 >1.5~5.9 2.2.10 充型压力的确定充型压力p 充是指充型阶段中,金属液上升至铸型型腔顶部(即完全充满型腔)时所需提供的气体压力。
其值可根据帕斯卡原理确定,即:2==p p H μγ充 式中 H — 型腔顶部与坩埚中金属液的距离;γ—金属液重度; μ—充型阻力系数,一般取值1.2~1.5。
(其值与型内反压力,铸件的平均壁厚,充型速度有关)。
2.2.11 充型速度的确定充型速度v 充是指充型过程中,金属液在型腔中的平均上升速度。
v 充数值选择的恰当与否对铸件质量有直接影响。
在升液管出口截面积一定的情况下,充型速度就取决于作用在合金液面上的气体压力的增长速度(称为加压速度)。
加压速度越快,合金液的充型速度也越快。
恰当的充型速度v 充应当是一个适当的数值,即应满足下面的不等式max min v v v 充充充>>。