浅析鼓式制动器制动性能优化
碟式制动器与鼓式制动器的比较

碟式制动器与鼓式制动器的比较制动系统是车辆安全性能中至关重要的一部分,而制动器作为制动系统中的核心组成部分,在车辆制动过程中起到至关重要的作用。
在众多的制动器类型中,碟式制动器和鼓式制动器是两种常见的制动器类型。
本文将对碟式制动器和鼓式制动器进行比较,探讨它们的优缺点和适用范围。
碟式制动器采用摩擦片与刹车盘之间的摩擦力来实现制动。
它由刹车盘、刹车卡钳、刹车片组成。
而鼓式制动器由刹车鼓、制动鞋、制动缸等部件组成。
虽然二者都是摩擦制动的原理,但在结构和性能上存在一些显著差异。
首先,从制动性能来看,碟式制动器具有较高的制动效率和散热能力。
由于碟式制动器的刹车系数大、制动力矩较稳定,它在制动时的响应速度更快,制动距离更短。
同时,碟式制动器的散热性能更好,不易出现制动衰减现象,因此在高速制动或长时间制动时,碟式制动器表现更为出色。
另一方面,鼓式制动器相对来说在制动性能方面稍显逊色。
由于鼓式制动器的制动力矩较小,制动响应相对较慢,制动距离较长。
此外,鼓式制动器在长时间高温制动的情况下容易出现制动力衰减,降低了制动性能。
因此,鼓式制动器常用于低速车辆或次要制动系统。
从结构设计的角度来看,碟式制动器相对简单易于维修。
碟式制动器的构造较为简单,易于检修和更换制动部件。
而鼓式制动器则因为内部结构较为复杂,以及存在制动鼓与制动鞋接触不均匀的问题,使得其维修和更换工作相对困难。
此外,碟式制动器还具有自清洁功能。
由于刹车片与刹车盘之间存在较大的空隙,碟式制动器相对容易清理,不容易积聚灰尘和水分导致制动力下降。
而鼓式制动器由于封闭性较高,内部容易积聚灰尘和水汽,对制动力产生不利影响。
最后,从成本角度来看,鼓式制动器相对便宜。
由于鼓式制动器的制造工艺相对简单,部件数量较少,因此制造成本较低。
而碟式制动器的制造工艺较复杂,需要更多的材料和精密部件,导致制造成本相对较高。
综上所述,碟式制动器和鼓式制动器在制动性能、结构设计、维修方便性和成本等方面存在一定的差异。
轻型车辆鼓式中央制动器研究及结构优化
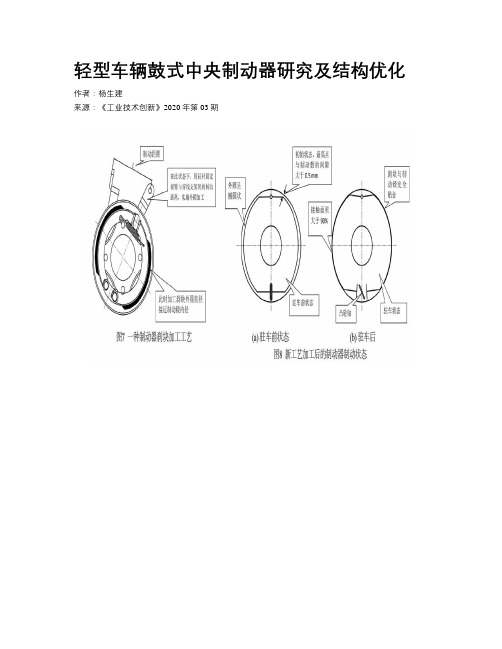
轻型车辆鼓式中央制动器研究及结构优化作者:杨生建来源:《工业技术创新》2020年第03期摘要:轻卡、微卡等车辆技术快速发展,对轻型车辆鼓式中央制动器的驻车制动性能提出了更高的要求。
对现有制动器的结构形式、安装特点等进行分析,表明其存在三大主要问题:内部结构过于紧凑,生产组装工序繁琐;结构连接不牢固,制动力传递受限;刹块加工工艺落后,特性尚待深入挖掘。
据此,提出针对性的结构优化方案:简化制动器内部结构,提高操作人员安装便捷性;板材成形一体化,提高系统整体稳定性;参照实际驻车制动状态对刹块外圆进行加工,提高刹块与制动毂接触面积。
结构优化后,制动性能提升20%左右,有助于推进变速箱制动器的智能化、批量化组装,以及产品性能提升。
关键词:轻型车辆;鼓式中央制动器;驻车制动;刹块;驻车安全;市场竞争力引言随着轻卡、微卡等车辆的优势不断提升,保有量迅猛增加,轻型车辆鼓式中央制动器(以下简称“制动器”)的市场需求量也在不断扩大[1-2]。
然而,在实际使用中,这些车辆在道路上出现溜车、追尾、刮蹭等现象,使得人身伤害事故时有发生,因此良好的车辆驻车制动性能显得尤为重要[3]。
从技术层面看,制动器与变速箱相互连接组装时工序繁琐,制动器的关键加工工序还一直沿用传统的工艺形式,不仅影响生产效率,也难以达到理想的驻车制动性能。
为适应现代智能制造水平和提高产品竞争力,制动器产品需要进一步革新改良,以保持自身的专业化、科学化和市场化。
本文根据现有制动器的结构形式、安装特点,研究分析了制动器的内部构造、刹块受力特性和驻车制动实际效果;提出了方便实际安装、提高刹块强度和增加制动力矩的优化方案,使制动器更符合轻型车辆的现实生产需求和安全驻车制动要求。
1 现有鼓式中央制动器现状调研1.1 内部结构过于紧凑,连接安装工序繁琐传统制动器内部结构过于紧凑,使得连接安装工序繁琐,还容易发生操作事故,影响生产的快节奏、高效化。
由于安全的需要,当前的轻卡、微卡驻车制动系统均使用机械结构的制动器。
鼓式制动器相关参数对其制动效能的影响

© 1994-2009 China Academic Journal Electronic Publishing House. All rights reserved.
942
科 学 技 术 与 工 程
9卷
况下 ,本例中 ,三个影响因素依次取 3、3、1 水平 ,则 为该条 件 下 凸 轮 制 动 器 制 动 效 能 因 数 的 最 大 值 (19. 1216) 。与第 9 号试验相比 ,变化量仅是第三 因素 (摩擦片包角 )从 120 变为 105,二者的制动效 能因数之差为 0. 690 2,提高比率仅为 3. 745% ,同 样证明了 (4)的结论 。
7. 981 9 11. 314 0 12. 516 3
11. 376 7 12. 433 9 12. 442 1
17. 202 3 12. 813 0 11. 602 5
9. 220 4 1. 499 0 0. 913 8
3
3
1
19. 121 6
从表 2可以看出 , 3个因素 (相应的 3 列 )的极 差分别为 9. 220 4, 1. 499 0和 0. 913 8,说明以上三 个考察因素对制动器效能因数的影响按大小次序 来说应该是 A (摩擦系数 ) 、B (凸轮转角 ) 、C (摩擦 片包角 ) 。
3 结论
正交仿真试验结果表明 ,上述三个因素对制动 器效能因数的影响按大小次序是摩擦系数 、凸轮偏 置角 、摩擦片包角 ,而且三个因素取值越大 ,则制动 器的效能因数越大 。随着三个因素取值的增加 ,制 动效能因数对摩擦系数的敏感性显著增大的同时 对凸轮转角及摩擦片包角的敏感性却在降低 。这 说明 ,在满足制动性能要求的前提下 ,摩擦系数及 摩擦片的包角取值不宜过大 。另外 ,由于磨损导致 制动效能的降低 ,可以通过少量增大凸轮偏置角借 以较高的提升制动器制动效能 。
17.鼓式制动器设计与效能分析

轻型汽车技术2009(4)总236孙丽(淮阴工学院交通工程系)摘要鼓式制动器的性质及其参数匹配直接影响汽车的安全性。
通过运用传统设计理论与运用Pro/e、Ansys软件设计鼓式制动器、分析效能,并进行对比分析,后者方法简单,参数化设计避免大量的人工计算也不需要单独编制,为复杂结构的设计分析提供了新的方法。
关键词:鼓式制动器设计效能分析鼓式制动器设计与效能分析鼓式制动器制动效能高、结构紧凑、价格便宜,至今在汽车上仍然广泛应用。
研究鼓式制动器的设计与效能分析方法十分必要。
首先以传统理论为基础,手工设计、分析,然后利用Pro/e进行建模,把Pro/e模型导入Ansys软件进行使用效能的分析,并与传统的设计理论进行对比分析,相互验证,对改进制动器结构、解决制约其性能提高问题具有非常重要的意义。
已知某轿车部分参数如下:满载质量为m=1940Kg,轴距L=2548mm,质心至前桥的距离为L1=1100mm,距后桥为L2=1448mm,轮距B=1422mm,质心高度hg=950mm,同步器。
附着系数φ=0.6,运行路面最大附着系数φm ax=0.8,车轮有效半径r e=0.5m,后轮为鼓式制动器。
1.1制动器主要参数的初选初步设定中间为楔块的领从蹄式鼓式制动器,初定半径R为90mm;根据理论a=0.8R=72mm,c=20mm;制动器中心到张开力F0到作用线的距离e=0.8R=72mm;摩擦衬片的包角θ=96°,即为1.67弧度;摩擦衬片起始角θ0=90°-θ/2=42°;摩擦衬片的宽度b=A p/Rθ;摩擦衬片的面积暂定为200cm2,经计算,b=13.307cm2;根据公式h=a+c,则h=144mm,摩擦因数u暂定为0.4。
1.2主要零件的设计制动鼓的材料多用灰铸铁,一般铸造的制动鼓壁厚,轿车主要为7mm~12mm,中型以上货车为13mm~18mm;轿车和轻型货车的制动蹄广泛用T 型钢碾压或焊接制铸钢铸成,制动蹄腹板和翼缘的厚度,轿车的为3mm~5mm,货车的为5mm~8mm,摩擦衬片的厚度,轿车多用4.5mm~5mm,货车的则在8mm以上;制动底板都冲压成凹凸起伏状。
鼓式制动器与盘式制动器的优缺点
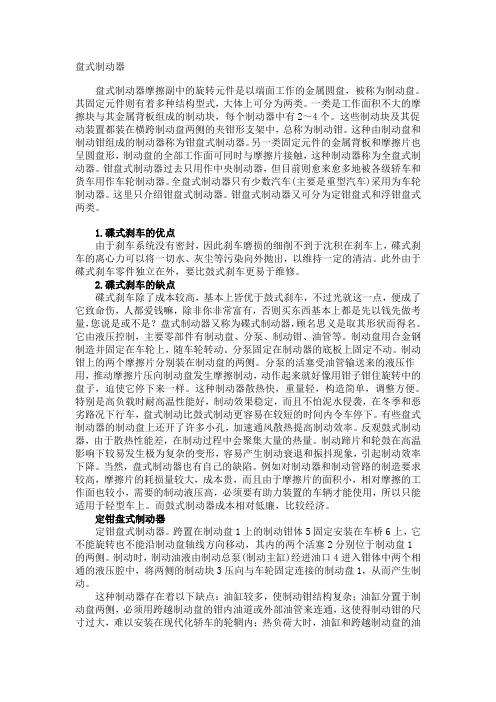
盘式制动器盘式制动器摩擦副中的旋转元件是以端面工作的金属圆盘,被称为制动盘。
其固定元件则有着多种结构型式,大体上可分为两类。
一类是工作面积不大的摩擦块与其金属背板组成的制动块,每个制动器中有2~4个。
这些制动块及其促动装置都装在横跨制动盘两侧的夹钳形支架中,总称为制动钳。
这种由制动盘和制动钳组成的制动器称为钳盘式制动器。
另一类固定元件的金属背板和摩擦片也呈圆盘形,制动盘的全部工作面可同时与摩擦片接触,这种制动器称为全盘式制动器。
钳盘式制动器过去只用作中央制动器,但目前则愈来愈多地被各级轿车和货车用作车轮制动器。
全盘式制动器只有少数汽车(主要是重型汽车)采用为车轮制动器。
这里只介绍钳盘式制动器。
钳盘式制动器又可分为定钳盘式和浮钳盘式两类。
1.碟式刹车的优点由于刹车系统没有密封,因此刹车磨损的细削不到于沈积在刹车上,碟式刹车的离心力可以将一切水、灰尘等污染向外抛出,以维持一定的清洁。
此外由于碟式刹车零件独立在外,要比鼓式刹车更易于维修。
2.碟式刹车的缺点碟式刹车除了成本较高,基本上皆优于鼓式刹车,不过光就这一点,便成了它致命伤,人都爱钱嘛,除非你非常富有,否则买东西基本上都是先以钱先做考量,您说是或不是?盘式制动器又称为碟式制动器,顾名思义是取其形状而得名。
它由液压控制,主要零部件有制动盘、分泵、制动钳、油管等。
制动盘用合金钢制造并固定在车轮上,随车轮转动。
分泵固定在制动器的底板上固定不动。
制动钳上的两个摩擦片分别装在制动盘的两侧。
分泵的活塞受油管输送来的液压作用,推动摩擦片压向制动盘发生摩擦制动,动作起来就好像用钳子钳住旋转中的盘子,迫使它停下来一样。
这种制动器散热快,重量轻,构造简单,调整方便。
特别是高负载时耐高温性能好,制动效果稳定,而且不怕泥水侵袭,在冬季和恶劣路况下行车,盘式制动比鼓式制动更容易在较短的时间内令车停下。
有些盘式制动器的制动盘上还开了许多小孔,加速通风散热提高制动效率。
反观鼓式制动器,由于散热性能差,在制动过程中会聚集大量的热量。
制动器的设计优化与性能改善
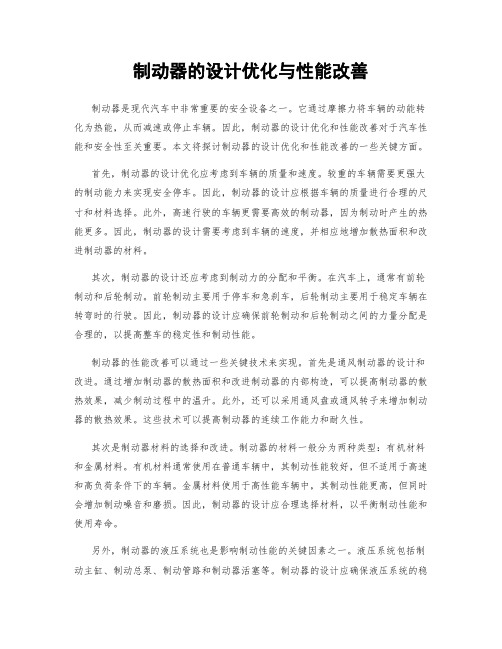
制动器的设计优化与性能改善制动器是现代汽车中非常重要的安全设备之一。
它通过摩擦力将车辆的动能转化为热能,从而减速或停止车辆。
因此,制动器的设计优化和性能改善对于汽车性能和安全性至关重要。
本文将探讨制动器的设计优化和性能改善的一些关键方面。
首先,制动器的设计优化应考虑到车辆的质量和速度。
较重的车辆需要更强大的制动能力来实现安全停车。
因此,制动器的设计应根据车辆的质量进行合理的尺寸和材料选择。
此外,高速行驶的车辆更需要高效的制动器,因为制动时产生的热能更多。
因此,制动器的设计需要考虑到车辆的速度,并相应地增加散热面积和改进制动器的材料。
其次,制动器的设计还应考虑到制动力的分配和平衡。
在汽车上,通常有前轮制动和后轮制动。
前轮制动主要用于停车和急刹车,后轮制动主要用于稳定车辆在转弯时的行驶。
因此,制动器的设计应确保前轮制动和后轮制动之间的力量分配是合理的,以提高整车的稳定性和制动性能。
制动器的性能改善可以通过一些关键技术来实现。
首先是通风制动器的设计和改进。
通过增加制动器的散热面积和改进制动器的内部构造,可以提高制动器的散热效果,减少制动过程中的温升。
此外,还可以采用通风盘或通风转子来增加制动器的散热效果。
这些技术可以提高制动器的连续工作能力和耐久性。
其次是制动器材料的选择和改进。
制动器的材料一般分为两种类型:有机材料和金属材料。
有机材料通常使用在普通车辆中,其制动性能较好,但不适用于高速和高负荷条件下的车辆。
金属材料使用于高性能车辆中,其制动性能更高,但同时会增加制动噪音和磨损。
因此,制动器的设计应合理选择材料,以平衡制动性能和使用寿命。
另外,制动器的液压系统也是影响制动性能的关键因素之一。
液压系统包括制动主缸、制动总泵、制动管路和制动器活塞等。
制动器的设计应确保液压系统的稳定性和灵敏度,以提高制动的响应速度和控制精度。
此外,还可以采用先进的液压控制技术,如电控制动系统或防抱死制动系统,以提高制动的安全性和稳定性。
鼓式制动器与盘式制动器的优缺点

鼓式制动器鼓式制动也叫块式制动,是靠制动块在制动轮上压紧来实现刹车的。
鼓式制动是早期设计的制动系统,其刹车鼓的设计1902年就已经使用在马车上了,直到1920年左右才开始在汽车工业广泛应用。
现在鼓式制动器的主流是内张式,它的制动块(刹车蹄)位于制动轮内侧,在刹车的时候制动块向外张开,摩擦制动轮的内侧,达到刹车的目的。
相对于盘式制动器来说,鼓式制动器的制动效能和散热性都要差许多,鼓式制动器的制动力稳定性差,在不同路面上制动力变化很大,不易于掌控。
而由于散热性能差,在制动过程中会聚集大量的热量。
制动块和轮鼓在高温影响下较易发生极为复杂的变形,容易产生制动衰退和振抖现象,引起制动效率下降。
另外,鼓式制动器在使用一段时间后,要定期调校刹车蹄的空隙,甚至要把整个刹车鼓拆出清理累积在内的刹车粉。
当然,鼓式制动器也并非一无是处,它造价便宜,而且符合传统设计。
四轮轿车在制动过程中,由于惯性的作用,前轮的负荷通常占汽车全部负荷的70%-80%,前轮制动力要比后轮大,后轮起辅助制动作用,因此轿车生产厂家为了节省成本,就采用前盘后鼓的制动方式。
不过对于重型车来说,由于车速一般不是很高,刹车蹄的耐用程度也比盘式制动器高,因此许多重型车至今仍使用四轮鼓式的设计。
1.鼓式刹车优点自刹作用:鼓式刹车有良好的自刹作用,由于刹车来令片外张,车轮旋转连带着外张的刹车鼓扭曲一个角度(当然不会大到让你很容易看得出来)刹车来令片外张力(刹车制动力)越大,则情形就越明显,因此,一般大型车辆还是使用鼓式刹车,除了成本较低外,大型车与小型车的鼓刹,差别可能祗有大型采气动辅助,而小型车采真空辅助来帮助刹车。
成本较低:鼓式刹车制造技术层次较低,也是最先用于刹车系统,因此制造成本要比碟式刹车低。
2. 鼓式刹车缺点由于鼓式刹车刹车来令片密封于刹车鼓内,造成刹车来令片磨损后的碎削无法散去,影响刹车鼓与来令片的接触面而影响刹车性能。
鼓刹最大的缺点是下雨天沾了雨水后会打滑,造成刹车失灵这才是其最可怕的领从蹄式制动器增势与减势作用,设汽车前进时制动鼓旋转方向(这称为制动鼓正向旋转)。
一种鼓式制动器的优化设计
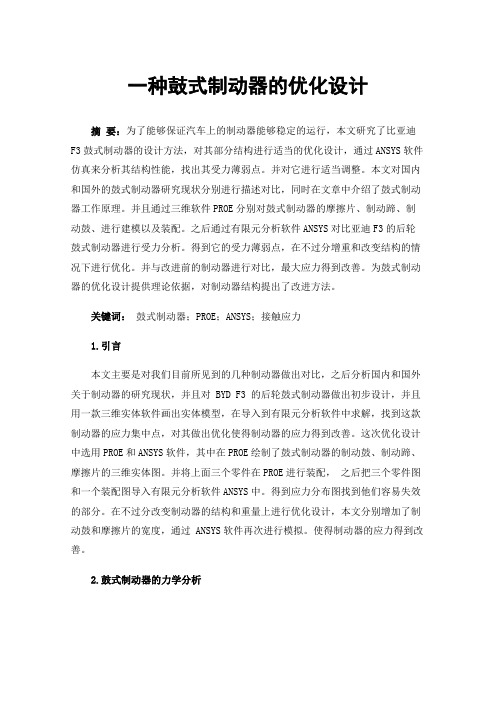
一种鼓式制动器的优化设计摘要:为了能够保证汽车上的制动器能够稳定的运行,本文研究了比亚迪F3鼓式制动器的设计方法,对其部分结构进行适当的优化设计,通过ANSYS软件仿真来分析其结构性能,找出其受力薄弱点。
并对它进行适当调整。
本文对国内和国外的鼓式制动器研究现状分别进行描述对比,同时在文章中介绍了鼓式制动器工作原理。
并且通过三维软件PROE分别对鼓式制动器的摩擦片、制动蹄、制动鼓、进行建模以及装配。
之后通过有限元分析软件ANSYS对比亚迪F3的后轮鼓式制动器进行受力分析。
得到它的受力薄弱点,在不过分增重和改变结构的情况下进行优化。
并与改进前的制动器进行对比,最大应力得到改善。
为鼓式制动器的优化设计提供理论依据,对制动器结构提出了改进方法。
关键词:鼓式制动器;PROE;ANSYS;接触应力1.引言本文主要是对我们目前所见到的几种制动器做出对比,之后分析国内和国外关于制动器的研究现状,并且对 BYD F3 的后轮鼓式制动器做出初步设计,并且用一款三维实体软件画出实体模型,在导入到有限元分析软件中求解,找到这款制动器的应力集中点,对其做出优化使得制动器的应力得到改善。
这次优化设计中选用PROE和ANSYS软件,其中在PROE绘制了鼓式制动器的制动鼓、制动蹄、摩擦片的三维实体图。
并将上面三个零件在PROE进行装配,之后把三个零件图和一个装配图导入有限元分析软件ANSYS中。
得到应力分布图找到他们容易失效的部分。
在不过分改变制动器的结构和重量上进行优化设计,本文分别增加了制动鼓和摩擦片的宽度,通过 ANSYS软件再次进行模拟。
使得制动器的应力得到改善。
2.鼓式制动器的力学分析本文的研究优化是比亚迪F3的后轮鼓式制动器,所以基于不过分改变重量和尺寸的原则,因此本文主要是对比亚迪F3后轮鼓式制动器进行初步的设计和优化。
2.1制动系统主要参数数值2.1.1相关主要技术参数查阅BYD的设计手册我们得到这款轿车的参数,具体如下;整车质量:空载:1200kg 满载:1600kg质心位置: a=1.04mb=1.56m质心高度:空载:hg=0.60m 满载:hg=0.55m轴距: L=2.6m轮距 : L =1.48m最高车速: 180km/h最大功率/转速:78/6000 kw/rpm最大转矩/转速:134/4500 N·m/rpm轮胎:195/60R152.2制动器有关计算根据汽车制动时的整车受力分析,考虑到制动时的轴荷转移,可求得地面对前、后轴车轮的法向反力Z1,Z2 。
- 1、下载文档前请自行甄别文档内容的完整性,平台不提供额外的编辑、内容补充、找答案等附加服务。
- 2、"仅部分预览"的文档,不可在线预览部分如存在完整性等问题,可反馈申请退款(可完整预览的文档不适用该条件!)。
- 3、如文档侵犯您的权益,请联系客服反馈,我们会尽快为您处理(人工客服工作时间:9:00-18:30)。
浅析鼓式制动器制动性能优化
摘要随着汽车行业的快速发展,对其制动性能提出了较高的要求,而鼓式制动器属于柔性多体系统,在汽车领域得到了广泛的应用。
然而,鼓式制动器在制动过程中,各个零件的受力情况和运动规律比较复杂,导致其性能无法得到有效的发挥。
本文将借助刚柔耦合模型来对鼓式制动器进行仿真制动模拟,这样不仅可以获得相对比较准确的动力学分析结果,而且还可以优化鼓式制动器制动性能,提高鼓式制动器研发效率,更好地推动鼓式制动器在汽车领域的发展。
关键词鼓式制动器;制动性能;优化
1 鼓式制动器概述
鼓式制动器又被称之为块式制动器,其一般是通过制动块在制动轮上压紧以达到刹车的效果。
实际上,鼓式制动器主流是内张式,在制动轮内侧分布有制动块(刹车蹄),在刹车过程中制动块向外张开,并对制动轮的内侧进行摩擦,从而实现刹车目的。
在鼓式制动器制动过程中,所存在的优点是:鼓式制动器符合传统设计,而且造价便宜。
在制动过程中,四轮轿车由于惯性的影响,致使前轮制动力要比后轮大,而且在前轮的负荷占据了汽车总负荷的70%-80%,在该过程中后轮起辅助制动作用。
对于重型车来说,车速一般比较低,与盘式制动器相比,刹车蹄的耐用程度高,因此至今大多数的重型车还在采用四轮鼓式的设计。
2 鼓式制动器制动性能优化
本文根据“试验设计一样本点获取一优化数学模型构建一优化算法的选择一优化设计一优化结果验证”的流程来对鼓式制动器制动性能优化进行研究[1]。
首先根据鼓式制动器的实际情况来构建性能优化的数学模型,优化算法选择了多岛遗传算法,以制动力矩最大为目标对滚轮中心坐标A、内盖板宽度的一半、滚轮中心坐标P、滚轮半径、摩擦片起始角、摩擦片包角等六个参数进行优化,根据优化所得结果来构建汽车鼓式制动器刚柔耦合模型与仿真平台,实施动力学仿真验证,所得到目标函数优化前后及设计变量的变化情况如表1所示。
通过对表1中的数据进行分析可以发现,在整个性能优化实验中,只有滚轮中心坐标位置所发生的变化比较小,其余变量所出现的变化均比较大,反映出设计变量的改变情况对制动力矩所产生的影响,从中获得最佳搭配的参数,以更好地提高鼓式制动器制动性能。
从本次研究结果中可以发现,在保持凸轮促动力固定不变的情况下,制动力矩提高了25.60%,但是优化后制动器的质量却降低了,从而反映出制动力矩的提升主要是结构优化的结果,通过对结构进行有效的优化能够使整个制动器的受力情况变得更加科学、更加合理,从而有效提高其制动力矩。
鼓式制动器制动性能优化后,滚轮半径和滚轮中心坐标的变化都会导致制动蹄的张开力方向的改变,并对优化前制动阶滚轮中心连线与段滚轮与凸轮接触力作用线夹角较大的情况进行了有效的改善,而且制动器中心与张开力作用线的距离也随之增大,使制动蹄具有非常好的张开效果[2]。
摩擦片包角变小,会导致其摩擦片起始角变大,从而使摩擦片与制动鼓的接触压力均匀分布。
内盖板宽度的一半变小会导致制动蹄刚度降低,在制动过程中会出现比较大范围的变形,致使制动鼓与摩擦片的接触压力均匀分布,这些都可以有效提高鼓式制动器制动性能。
在进行鼓式制动器制动性能优化研究阶段,借助代理模型来反映目标函数与变量之间的关系,而且所有优化过程的研究,均满足约束条件的点和目标函数,但是在实际情况中有可能不满足。
此时就需要根据优化结果来构建真实的仿真模型来分析鼓式制动器的动力学性能,查看优化后的鼓式制动器制动性能是否真正的提升。
同时还需要对制动器制造成本及设计变量与目标函数的高度所存在的非线性关系来对按照四舍五入的原则将优化后的设计变量保留一位小数,所得到的修正后设计变量数值见表1。
最后,将修正后的数据结果代入刚柔耦合模型与仿真平台之中,验证结果发现优化后鼓式制动器的制动力矩为24699.56/Nm,但是优化过程中未对动力矩的波动情况给予考虑,从而导致优化后制动力矩的波动范围增大,而且导致动减速度大小的平均值提高至6.75m/s2,制动距离为22.35m,减小了5.54m。
两滚轮中心连线与接触力作用线之间的夹角为11.95°,与优化前相比降低了4.77°,此外凸轮对制动蹄的张开效果得到了明显的改善,从而使鼓式制动器的制动性能大大提升。
3 结束语
综合所述,鼓式制动器属于汽车结构体系中比较重要的组成部分,而且滚轮中心坐标、内盖板宽度的一半、滚轮中心坐标、滚轮半径、摩擦片起始角、摩擦片包角等参数都会对鼓式制动器的制动性能产生影响,因此需要根据实际情况来对其参数进行调整,以更好提高鼓式制动器的使用性能。
参考文獻
[1] 席传鹏,王凯,马雅茹.鼓式制动器和轮式制动器的制动性能对比分析[J].西安理工大学学报,2017,4(1):35-36.
[2] 章菊,徐伟杰,李鹏.某汽车鼓式制动器虚拟样机的建模与仿真分析[J].汽车零部件,2016,4(12):117-118.。