刮板机日常保养及维护
刮板机操作规程
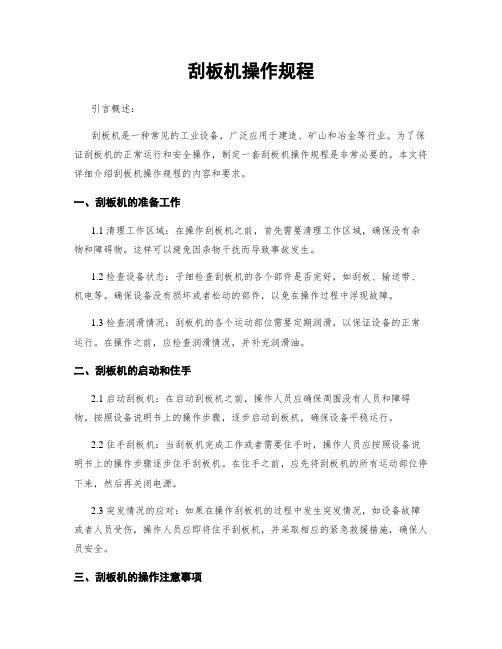
刮板机操作规程引言概述:刮板机是一种常见的工业设备,广泛应用于建造、矿山和冶金等行业。
为了保证刮板机的正常运行和安全操作,制定一套刮板机操作规程是非常必要的。
本文将详细介绍刮板机操作规程的内容和要求。
一、刮板机的准备工作1.1 清理工作区域:在操作刮板机之前,首先需要清理工作区域,确保没有杂物和障碍物。
这样可以避免因杂物干扰而导致事故发生。
1.2 检查设备状态:子细检查刮板机的各个部件是否完好,如刮板、输送带、机电等。
确保设备没有损坏或者松动的部件,以免在操作过程中浮现故障。
1.3 检查润滑情况:刮板机的各个运动部位需要定期润滑,以保证设备的正常运行。
在操作之前,应检查润滑情况,并补充润滑油。
二、刮板机的启动和住手2.1 启动刮板机:在启动刮板机之前,操作人员应确保周围没有人员和障碍物。
按照设备说明书上的操作步骤,逐步启动刮板机,确保设备平稳运行。
2.2 住手刮板机:当刮板机完成工作或者需要住手时,操作人员应按照设备说明书上的操作步骤逐步住手刮板机。
在住手之前,应先将刮板机的所有运动部位停下来,然后再关闭电源。
2.3 突发情况的应对:如果在操作刮板机的过程中发生突发情况,如设备故障或者人员受伤,操作人员应即将住手刮板机,并采取相应的紧急救援措施,确保人员安全。
三、刮板机的操作注意事项3.1 严禁超负荷操作:刮板机在工作过程中需要承受一定的负荷,但是超负荷操作会导致设备损坏或者人员伤亡。
因此,操作人员应根据设备的额定负荷进行操作,严禁超负荷工作。
3.2 规范操作动作:操作人员应按照设备说明书上的操作步骤进行操作,不得随意更改或者省略任何步骤。
特殊是在刮板机启动和住手时,应按照规定的步骤进行操作,确保设备的安全性。
3.3 定期检查维护:刮板机是一种重要的生产设备,为了保证其正常运行,操作人员应定期检查和维护设备。
包括清洁设备、润滑设备、检查电气路线等,确保设备的稳定性和可靠性。
四、刮板机的安全防护措施4.1 佩戴个人防护装备:在操作刮板机时,操作人员应佩戴符合要求的个人防护装备,如安全帽、护目镜、防护手套等。
刮板输送机维护保养规程

刮板输送机维护保养规程刮板输送机是一种常用的输送设备,用于输送各种散料、块状物料,有着传输距离长、装载量大等优点。
为了保证刮板输送机在运行中的稳定工作,必须对其进行定期的维护保养工作,这也是延长设备寿命、提高产能的必要措施。
下面就为大家介绍一下刮板输送机的维护保养规程。
定期检查电气和液压系统刮板输送机的电气和液压系统是设备正常运转的重要保障,因此,在刮板输送机每次工作之前,须要检查电气和液压系统的工作状态。
检查电气系统时,可以检查电动机有无异响或过热现象,电线接线是否牢固,控制器按钮是否灵敏,电缆接头是否有裂缝等问题。
检查液压系统时,可以检查液压油是否充足,各液压管路是否完好,油泵是否有异常声响等问题。
清洁和清理为保证刮板输送机的正常运行,必须保持设备的清洁,避免灰尘、杂物等进入设备通道,造成设备故障。
定期对设备进行清洁,可以有效地预防和减少设备故障。
在清洁时,应注意不要使清洁液、水进入设备控制箱、电气部件和液压系统内部。
清理时,还应对刮板输送机的刮板和链条进行清理,保持其表面清洁,防止链条张紧不良或卡住,影响设备的正常运行。
更换易损件和维修刮板输送机在运行中,部分易损件经常需要更换。
因此,在设备运行期间,要随时注意检查刮板输送机的重要部件,如刮板、链条、轴承、齿轮、机油等部件的磨损情况,及时更换或进行维修。
对于较严重的故障,最好由专业的技术人员进行处理,以保证修理的质量和设备的安全性能。
正确的使用方法为避免设备故障,应在使用前按照制造厂家规定的操作程序正确地进行调试、使用和停机。
同时,在使用过程中,尽可能地减少或避免设备的过载和冲击,避免行车沿着铁轨窜行或行驶的时间过长,以维护设备的正常运行。
定期检查和维护记录在实施维护和保养过程中,应及时记录设备的故障、检查、维护和更换情况,制定设备维护和保养计划,并按期执行。
记录的内容应包括设备的故障情况、维护和保养的形式、内容、时间、费用以及技术人员的姓名、联系方式等信息。
刮板运输机安全技术操作规程(4篇)

刮板运输机安全技术操作规程刮板运输机是一种用于矿石、煤炭等物料的水平运输和堆放的重型机械设备,它具有工作效率高、运输距离远、操作简便等优点,但同时也存在一定的安全隐患。
为了确保刮板运输机的安全运行,保护作业人员和设备的安全,制定刮板运输机的安全技术操作规程是非常必要的。
一、刮板运输机的安全检查和准备工作1. 交接班时,班组长或操作员应认真查看刮板运输机的运转情况,包括润滑油温、传动部分是否异常等,并记录在检查记录册上。
2. 在刮板运输机启动前,操作员必须检查刮板运输机的各项安全装置是否完好,如传动部分的防护罩、紧急停车装置等。
3. 检查刮板运输机的工作环境是否安全,如空气流通是否良好,有没有易燃易爆物品等,确保没有安全隐患。
二、刮板运输机的操作流程1. 操作员在启动刮板运输机前,应对设备的操作流程进行逐步了解,并对操作顺序熟悉,确保能够正确操作。
2. 操作员在启动刮板运输机时,必须站在安全距离外,并确保无人在刮板运输机的作业区域内。
3. 操作员应根据物料的堆积情况和作业需求,调整刮板运输机的运行速度和倾角,确保物料能够顺利运输和堆放。
4. 操作员在刮板运输机运行过程中,需要时刻留意设备的运行情况,如传动部分是否正常、设备是否有异响等,如发现异常情况应立即停机排除故障。
5. 当刮板运输机运行结束后,操作员应立即停机,并关闭刮板运输机的电源,清理作业区域,确保设备彻底停止运转。
三、刮板运输机的维护和检修1. 操作员在使用刮板运输机的过程中,应定期对设备进行维护保养,如润滑部分的润滑油添加、防护罩的清理等,确保设备的正常运行。
2. 刮板运输机的关键部位和传动部分应定期进行检查和维修,如链条的松紧程度、轮箍的是否磨损等,及时更换和维修。
3. 在刮板运输机的检修过程中,操作员必须做好封锁措施,并采取安全防护措施,如戴好防护手套、眼镜等,以确保人员的安全。
四、刮板运输机的应急处理1. 在刮板运输机发生故障或异常情况时,操作员应立即停机,排除故障,不可随意进行修理。
刮板机构造

刮板机构造刮板机,作为一种广泛应用于各种工业领域的输送设备,其构造的复杂性和专业性都体现了现代机械设计的精妙之处。
本文将从刮板机的基本构造、工作原理、关键部件以及维护保养等方面进行详细阐述,以期为读者提供全面而深入的了解。
一、刮板机的基本构造刮板机主要由机架、刮板链条、驱动装置、张紧装置和刮板等部分组成。
机架是刮板机的支撑基础,通常采用钢材焊接而成,具有足够的强度和刚性。
刮板链条是刮板机的核心部件,负责承载和输送物料。
驱动装置为刮板链条提供动力,使其能够连续运转。
张紧装置则用于调整刮板链条的张紧度,保证其正常工作。
刮板则是直接与物料接触的部件,其形状和材质根据物料的性质和输送要求而定。
二、刮板机的工作原理刮板机的工作原理相对简单。
当驱动装置启动时,带动刮板链条在机架上循环运动。
刮板固定在链条上,随着链条的移动而移动。
当刮板经过物料堆积区时,会将物料刮起并带走,然后在输送路径上不断前行,最终将物料输送到指定位置。
在这个过程中,刮板链条的张紧度、刮板与机架的间隙以及驱动装置的速度等都会影响到刮板机的输送效率和稳定性。
三、刮板机的关键部件详解1. 刮板链条:刮板链条是刮板机的核心部件之一,它由链节、刮板和销轴等部分组成。
链节是链条的基本单元,通过销轴连接在一起。
刮板则固定在链节上,用于刮取和输送物料。
刮板链条的材质通常为高强度合金钢,具有耐磨、耐腐蚀和良好的机械性能。
为了延长使用寿命和提高输送效率,刮板链条还需要进行定期的润滑和维护。
2. 驱动装置:驱动装置是刮板机的动力来源,通常由电机、减速器和联轴器等部分组成。
电机提供原始动力,通过减速器减速后传递给刮板链条。
联轴器则用于连接电机和减速器,传递扭矩。
驱动装置的性能直接影响到刮板机的运行速度和稳定性。
因此,在选择驱动装置时,需要根据刮板机的实际工作条件和输送要求来确定合适的型号和参数。
3. 张紧装置:张紧装置用于调整刮板链条的张紧度,保证其正常工作。
刮板输送机维护保养使用措施

刮板输送机使用维护保养措施一、概况在使用SGB620-40T刮板输送机期间,为了保证刮板机日常可靠运行,各部件良好运转,避免零部件过度损耗,减少事故的发生,特编制安全使用措施如下:二、刮板输送机使用操作要求。
(1)操作人员应按使用说明书要求进行操作1、开机前的准备工作:首先检查减速箱内润滑油的油位情况确保减速器内规定的注油量,确保液力耦合器的规定充液量,检查电机、联结召、液力耦合器、减速机、盲轴、机尾等各处螺栓是否有松动现象,如有松动,立刻紧固,检查刮板链的松紧情况,调整松紧适当,检查刮板链运转范围内是否有其它物体,应及时清除,一切准备就绪方可开机。
各密封处不得有渗漏现象。
2、开机应先空载运行几分钟,检查各密封处有无渗漏现象,刮板链有无刮卡现象,一切正常后,方可装煤运载,不得带载启动,以免造成电机及设备故障。
3、应先开机后装煤,不得带载启动。
4、运转过程中注意检查刮板链张紧程度,发现松弛应及时紧链。
刮板链在运转中若遇到刮卡,或其他异常情况,应立即停车故障,故障排除后方可继续工作。
三、刮板机日常维护保养(1)刮板机司机的日常维护刮板机一定要有经过培训持有合格证的固定或兼职司机,司机要经常注意和做好下列工作:1、要经常准备一些保险销子、销子套、链环和油脂;2、有传动链子的刮板机要经常注油;3、经常清扫机头或机尾由下链带出的碎矸石和煤粉,决不许传动链子埋在粉渣中;4、随时注意刮板链子的松紧,不合适的及时在运转中调整。
5、注意刮板机工作时始终保持平直;6、注意各个轴承的声音是否正常;温度不可超过65°~70℃;7、注意工作中的链环及刮板,有磨损时,及时更换。
(2)机修工的日常维护刮板输送机在使用一段时间时,必须进行一次检查,其内容如下:1、揭开减速机上的小盖,检查齿轮有无损坏;里面的齿轮油是否够,不够应添油;2、检查减速机、电动机和机头,机尾的轴承是否正常;3、检查机头、机尾的所有螺栓是否松动,松的要拧紧;4、检查各个部位和零部件如链条、刮板、传动链子、销子、上下槽、机尾的紧链装置,如果有磨损或变形的必须更换。
刮板输送机使用管理规定

刮板输送机使用管理规定一、总则为确保刮板输送机的安全运行,保障生产工艺的顺利进行,提高工作效率,减少事故的发生,根据相关法律法规和有关规定,制定本管理规定。
二、使用范围本管理规定适用于刮板输送机在矿山、煤矿、建筑材料厂等工业企业中的使用。
三、责任与义务1.企业应当明确刮板输送机的使用部门和人员,设立专门的维修保养岗位,并指定专人负责刮板输送机的日常管理。
2.生产部门要做好刮板输送机的使用计划,并根据生产需要和设备状况进行合理调控,确保刮板输送机的正常工作。
3.使用人员应当按照相关规定,正确操作刮板输送机,发现异常情况及时上报并停机处理。
四、设备维护1.刮板输送机的日常维护保养应由专人负责,包括定期检查设备磨损、润滑油漏失情况及时更换,并做好相应的保养记录。
2.刮板输送机的维护保养要按照设备操作说明书进行,不得擅自修改设备结构或进行非正常使用。
3.刮板输送机维修保养完成后要进行试运行,确保设备正常工作再投入使用。
五、操作规程1.操作人员必须经过正规培训,持有相应的刮板输送机操作证书方可上岗。
2.操作人员在操作刮板输送机时应集中注意力,严禁同时进行其他操作。
3.操作人员应按照设备操作规程,正确开机、停机,并且严格按照载荷、速度等参数进行操作,不得超负荷或超速运行。
4.刮板输送机的运行中应注意观察设备运行情况,一旦发现异常情况及时停机检查,并上报相关人员处理。
六、安全防护1.刮板输送机必须安装防护装置,确保操作人员和周围人员的安全。
2.使用人员必须穿戴好安全帽、工作服、防护眼镜等个人防护装备。
3.刮板输送机作业区域应设置明显的警示标志,禁止未经许可的人员靠近作业区域。
七、应急处理1.发生刮板输送机故障或事故时,操作人员应立即停机,并尽快上报相关人员进行处理。
2.生产单位应建立健全的应急预案,定期组织演练,提高应对突发情况的能力。
八、监督与检查1.企业要定期对刮板输送机进行检修,确保设备的正常运行。
2.监管部门有权对刮板输送机的使用情况进行监督检查,对违规操作和不合格设备要及时采取相应的措施。
刮板输送机使用维护

刮板输送机使用维护刮板输送机是一种常用的物料输送设备,主要用于水泥、煤矿等行业的物料输送和储存。
为了保证刮板输送机的正常工作和延长使用寿命,需要进行定期的维护和保养。
以下是刮板输送机使用维护的一般方法和注意事项。
1. 定期清洁:对刮板输送机进行定期清洁是维护的基本工作。
清洁时需注意断电,并清除输送机内外的杂物和积尘,特别是在输送机底部的链辊、刮板和侧边板等零部件,要保持清洁无杂质。
清洁时可以使用软刷子、吸尘器等工具。
2. 润滑维护:刮板输送机的链条、轴承、齿轮等部件需要定期润滑保养。
润滑油的添加和更换是重要的维护措施。
润滑油的选择应根据设备的运行环境和条件来确定,并按照设备使用说明书的要求添加和更换。
润滑油的使用量要控制在适当范围内,过多或过少都会影响设备的正常运行。
3. 检查链条张紧度:刮板输送机的链条张紧度对设备的正常工作非常重要。
链条过松会造成打滑和误动现象,链条过紧会增加设备的阻力和损坏链条。
定期检查链条张紧度,通过松紧螺栓或调整轴承座来调整链条的张紧度,保持在适当的范围内。
4. 检查刮板状态:刮板是刮板输送机送料的重要组成部分,需要定期检查其磨损情况。
如果刮板过度磨损或变形,需要及时更换。
刮板的更换要按照正确的安装方法进行,确保刮板与输送机的配合良好,不影响正常运行。
5. 检查电器设备:刮板输送机的电器设备要定期检查和保养。
检查电机的运行是否正常,是否存在过热、漏电等问题。
检查电缆是否有损伤,电器接线是否牢固。
对于有故障的电器设备,应及时修理或更换,确保设备的安全和正常运行。
6. 定期检查保护装置:刮板输送机的安全保护装置是保证设备安全运行的重要部分。
定期检查安全装置的可靠性,包括限位开关、急停开关、断电器等。
对于有故障的保护装置,要及时修理或更换,确保设备的安全运行。
7. 注意预防事故:在刮板输送机使用过程中,要注意预防事故的发生。
操作人员要熟悉设备的使用和维护方法,并服从操作规程。
刮板输送机管理制度(4篇)
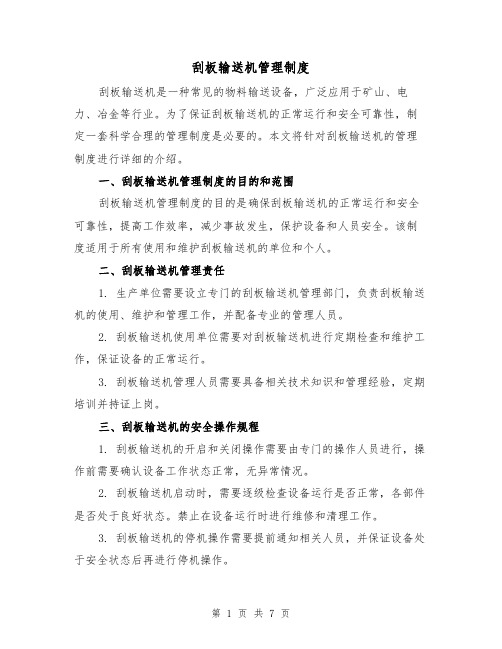
刮板输送机管理制度刮板输送机是一种常见的物料输送设备,广泛应用于矿山、电力、冶金等行业。
为了保证刮板输送机的正常运行和安全可靠性,制定一套科学合理的管理制度是必要的。
本文将针对刮板输送机的管理制度进行详细的介绍。
一、刮板输送机管理制度的目的和范围刮板输送机管理制度的目的是确保刮板输送机的正常运行和安全可靠性,提高工作效率,减少事故发生,保护设备和人员安全。
该制度适用于所有使用和维护刮板输送机的单位和个人。
二、刮板输送机管理责任1. 生产单位需要设立专门的刮板输送机管理部门,负责刮板输送机的使用、维护和管理工作,并配备专业的管理人员。
2. 刮板输送机使用单位需要对刮板输送机进行定期检查和维护工作,保证设备的正常运行。
3. 刮板输送机管理人员需要具备相关技术知识和管理经验,定期培训并持证上岗。
三、刮板输送机的安全操作规程1. 刮板输送机的开启和关闭操作需要由专门的操作人员进行,操作前需要确认设备工作状态正常,无异常情况。
2. 刮板输送机启动时,需要逐级检查设备运行是否正常,各部件是否处于良好状态。
禁止在设备运行时进行维修和清理工作。
3. 刮板输送机的停机操作需要提前通知相关人员,并保证设备处于安全状态后再进行停机操作。
四、刮板输送机的维护与保养制度1. 刮板输送机的维护和保养工作需要由专门的维修人员进行,确保设备的良好运行状态。
2. 刮板输送机的各个部件需要定期检查和保养,发现问题及时处理。
3. 对于设备的关键部件,需要有相应的备件储备和更换计划,确保设备的连续运行。
五、刮板输送机的安全防护措施1. 刮板输送机的工作区域应设置明显的安全警示标识,禁止无关人员靠近。
2. 刮板输送机操作人员需要配戴安全防护帽、防护眼镜、防护口罩等相关防护用品。
3. 刮板输送机各个部位需要设置安全防护装置,防止工作人员伤害。
4. 刮板输送机使用单位需要定期组织安全培训和演练活动,加强员工的安全意识。
六、应急处理措施1. 刮板输送机发生故障或事故时,需要立即停止设备运行,并通知相关人员进行处理。
- 1、下载文档前请自行甄别文档内容的完整性,平台不提供额外的编辑、内容补充、找答案等附加服务。
- 2、"仅部分预览"的文档,不可在线预览部分如存在完整性等问题,可反馈申请退款(可完整预览的文档不适用该条件!)。
- 3、如文档侵犯您的权益,请联系客服反馈,我们会尽快为您处理(人工客服工作时间:9:00-18:30)。
刮板机日常保养及维护
刮板输送机是靠链传动运输物料的,在使用中,操作及检修人员除了注意轴承温度、按规定要求润滑外,还必须做好以下工作。
1、定期调紧刮板链的松紧程度,并使两链条松紧程度一致。
一般每半月检查一次,特别在使用的前半个月应每天栓查刮板链的松紧程度,以刮板链与链齿能正常啮合无跳动为准,并随时予以调整。
调整刮板链通过调整拉紧丝杆进行,如拉紧丝杆行程不够时,应更换刮板
链。
2、每班应逐一检查连接环与刮板的固定情况。
如出现连接螺栓松脱
力和刮板掉落时,立即停机处理。
3、当两侧的刮板链磨损不一致而造成刮板倾斜运行时,链环磨损超
过原直径的25%时,应更换。
4、经常检查头轮和尾轮的运行情况。
当头轮齿牙及尾轮链槽轨面磨
损超过原直径的1/4时,就予以更换。
凡已经变形弯曲的刮板,均应予以更换。
6、在使用中如发现中间槽铸石板松动或脱落应立即更换,以免卡住
链条。
7、滚动轴承的润滑,使用1号或2号钙钠基润滑脂,如三班连续生产,每三个月更换一次,使用时可根据情况适当延长或缩短周期。
8、拉紧螺杆不使用时,应涂以润滑脂,并用纸包住,以免落入灰尘。
9、拉紧螺杆锈蚀无法转动时,应予以更换。
四、减速机
1、滚动轴承的润滑见上述第(7)条。
2、应经常检查减速机内的油量。
3、应半年小修一次,两年大修一次。
小修包括更换润滑油,更换涧滑油时,不得更换涧滑油牌号;检查传动齿轮的状况及滚动轴承处的密封等。
大修除包括小修内容外,还需解体拆卸全部零件进行检查、修理或更换。
特别是传动齿轮出现下列情况之一者,应做报废处理:(a)出现裂纹。
(b)齿面点蚀达啮合面的30%且深度达齿厚的10%。
(c)第一级啮合齿轮磨损达原齿厚的10%,其他级齿轮磨损达原齿
厚的20%。
4、更换减速机或其中部分齿轮,其润滑油运转500h后,应再全部更
换新油。
5、对于长期连续工作的减速机,必须3个月换油一次;若使用中发
现温升超过60℃或油温超过85℃,须更换润滑油后再用。
6、带小油泵强制性润滑的减速机,应经常检查油管的上油情况,不
得随意拆除。
7、闸门
(1)轴承要定期加润滑油。
(2)由于平板闸门为开式齿轮传动,要经常清除齿轮、齿条表面的
污物。
(3)经常检查齿轮、齿条的正常啮合,如有卡阻现象应及时调整。
(4)每班应至少开启一次,以使闸门运转灵活,防止运动部分发生
锈死现象。
8、螺栓调节丝杠用的工具(圆钢直径24)用户自行解决。
如有侵权请联系告知删除,感谢你们的配合!。