工业过程控制系统
PLC、DCS、FCS三大工业控制系统的区别

PLC›DCS、FCS三大工业控制系统的区别随着工业技术的快速发展,相继出现了集散控制系统和现场总线控制系统,一些行业当中有的人认为FCS是由PLC发展而来的;另一些行业的人认为FCS又是由DCS发展而来的。
FCS与PLC及DCS之间既有密不可分的关联,又存在着本质的区别。
在工业过程控制中的三大控制系统,分别是PLC、DCS、FCSoPLC控制器是一种数字运算操作的电子系统,专为工业环境下的应用而设计。
它采用一类可编程的存储器,用于其内部存储程序、执行逻辑运算、顺序控制、定时、计数与算术操作等面向用户的指令,并通过数字式或模拟式输入或输出,控制各种类型的机械或生产过程。
DCS集散控制系统,又叫计算机分布式控制系统,它是20世纪70年代中期迅速发展起来的,它把控制技术、计算机技术、图像显示技术以及通信技术结合起来,也称作4C技术,实现了对生产过程的监视、控制和管理。
它既打破了常规控制仪表功能的局限性,又较好的解决了早期计算机系统对于信息、管理和控制作用过于集中带来的危险性。
FCS现场总线控制系统的核心是总线协议,基础是数字智能现场设备,本质是信息处理现场化。
1、大型PLC构成的过程控制系统的基本特点⑴从上到下的结构,PLC既可以作为独立的DCS,也可以作为DCS的子系统。
(2)PID放在控制站中,可实现连续PID控制等各种功能。
⑶可用一台PC为主站,多台同类型PLC为从站;也可用一台PLC为主站,多台同类型PLC为从站,构成PLC网络。
⑷主要用于工控中的顺序控制,新型PLC也兼有闭环控制功能。
2、DCS控制系统的基本特点⑴从上到下的树状系统,其中通信是关键。
(2)PID在控制器中,连接计算机与现场仪器仪表。
⑶是树状拓扑和并行连续的链路结构,有大量电缆从中继站并行到现场仪器仪表。
⑷信号系统包括开关量信号和模拟信号。
(5)DCS一般是由现场仪表层、控制装置单元层、工厂(车间)层、和企业管理层构成。
传统DCS-现场级设备与控制器之间连接采用一对一I/O连线方式3、FCS控制系统的基本特点(I)FCS是3C技术的融合。
工业生产过程中的自动化控制系统
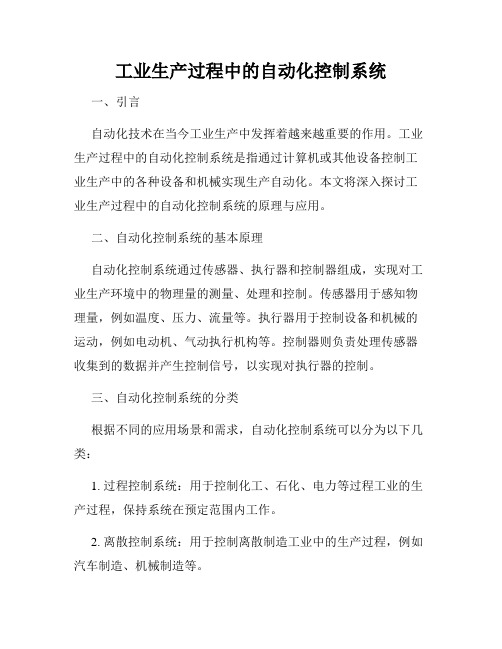
工业生产过程中的自动化控制系统一、引言自动化技术在当今工业生产中发挥着越来越重要的作用。
工业生产过程中的自动化控制系统是指通过计算机或其他设备控制工业生产中的各种设备和机械实现生产自动化。
本文将深入探讨工业生产过程中的自动化控制系统的原理与应用。
二、自动化控制系统的基本原理自动化控制系统通过传感器、执行器和控制器组成,实现对工业生产环境中的物理量的测量、处理和控制。
传感器用于感知物理量,例如温度、压力、流量等。
执行器用于控制设备和机械的运动,例如电动机、气动执行机构等。
控制器则负责处理传感器收集到的数据并产生控制信号,以实现对执行器的控制。
三、自动化控制系统的分类根据不同的应用场景和需求,自动化控制系统可以分为以下几类:1. 过程控制系统:用于控制化工、石化、电力等过程工业的生产过程,保持系统在预定范围内工作。
2. 离散控制系统:用于控制离散制造工业中的生产过程,例如汽车制造、机械制造等。
3. 机器人控制系统:用于控制工业机器人的运动和操作,广泛应用于汽车制造、电子组装等行业。
4. 智能化控制系统:利用人工智能、机器学习等技术实现对工业生产过程的智能化管理和控制。
四、自动化控制系统的关键技术1. 传感技术:传感器是自动化控制系统的重要组成部分,能够将物理量转化为电信号。
目前常用的传感技术包括压力传感技术、温度传感技术、流量传感技术等。
2. 控制算法:控制算法是自动化控制系统中的核心部分,能够根据传感器数据生成控制信号,如PID控制算法、模糊控制算法等。
3. 通信技术:自动化控制系统需要实现设备和机械之间的通信,常用的通信技术包括以太网、无线通信等。
4. 可靠性技术:工业生产过程需要保证系统的可靠性和安全性,因此可靠性技术十分重要,如备份系统、故障诊断技术等。
五、自动化控制系统在工业生产中的应用1. 提高生产效率:自动化控制系统可以减少人工操作,提高生产效率和产量,减少人为操作误差。
2. 降低生产成本:自动化控制系统可以减少人工成本,提高生产效益,降低生产成本。
过程控制系统 (2)
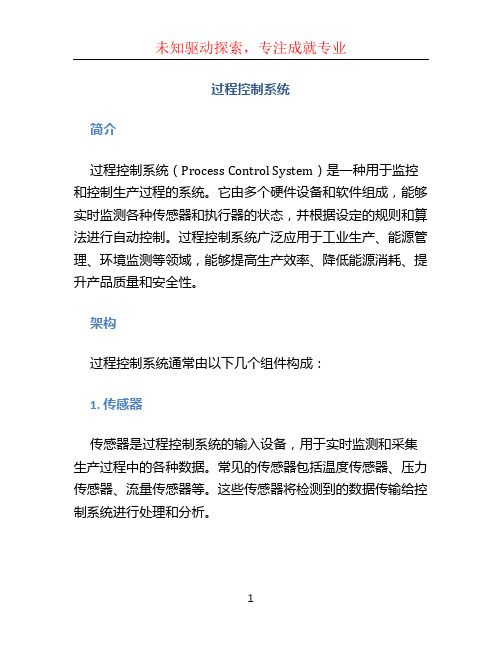
过程控制系统简介过程控制系统(Process Control System)是一种用于监控和控制生产过程的系统。
它由多个硬件设备和软件组成,能够实时监测各种传感器和执行器的状态,并根据设定的规则和算法进行自动控制。
过程控制系统广泛应用于工业生产、能源管理、环境监测等领域,能够提高生产效率、降低能源消耗、提升产品质量和安全性。
架构过程控制系统通常由以下几个组件构成:1. 传感器传感器是过程控制系统的输入设备,用于实时监测和采集生产过程中的各种数据。
常见的传感器包括温度传感器、压力传感器、流量传感器等。
这些传感器将检测到的数据传输给控制系统进行处理和分析。
2. 执行器执行器是过程控制系统的输出设备,用于根据系统的控制策略执行操作。
例如,根据温度传感器的数据,过程控制系统可以控制执行器来调节加热或冷却设备的操作,以维持所需的温度。
3. 控制器控制器是过程控制系统的核心组件,负责接收传感器数据、计算控制策略,并通过执行器来实现控制。
控制器可以是硬件控制器,如可编程逻辑控制器(PLC),也可以是软件控制器,如基于计算机的控制系统。
4. 监视界面监视界面是过程控制系统的用户界面,用于显示实时数据、报警信息和操作状态,方便操作人员进行监控和操作。
监视界面通常具有图形化界面,方便用户进行数据浏览、参数调整和报表生成等操作。
5. 数据存储与分析过程控制系统还需要具备数据存储和分析功能,以便后续的监测和分析。
数据存储可以使用数据库或云存储等方式,分析可以使用数据挖掘、统计学等方法,以提供对生产过程的优化建议。
工作原理过程控制系统的工作原理可分为以下几个步骤:1.传感器实时采集生产过程中的数据,如温度、压力、流量等。
2.数据被传输到控制器,控制器将采集到的数据与设定的控制规则进行比较,并计算出相应的控制量。
3.控制器通过执行器来实现控制操作,例如调节温度、打开或关闭阀门等。
4.控制器还会将数据传输到监视界面,以便操作人员实时监测生产过程,并及时处理异常情况。
基于智能算法的工业过程控制系统优化设计

基于智能算法的工业过程控制系统优化设计智能算法在工业过程控制系统优化设计中起着重要作用。
随着科技的不断发展和进步,智能算法被广泛应用于各个领域,工业过程控制系统亦不例外。
本文将介绍智能算法在工业过程控制系统优化设计中的应用,并详细阐述其原理和优势。
一、智能算法在工业过程控制系统中的应用工业过程控制系统是指通过对生产过程中的各个环节进行监测和控制,实现产品质量的稳定和生产效率的提高的系统。
智能算法在工业过程控制系统中的应用,主要体现在以下几个方面:1.1 过程建模与预测:智能算法可以利用历史数据和实时数据对工业过程进行建模和预测。
通过分析数据的规律和变化趋势,可以预测未来的设备状态和生产趋势,从而为生产调度和优化决策提供依据。
1.2 变量优化与控制:智能算法可以优化控制系统中的各个变量,例如温度、压力、流量等。
通过调整这些变量的数值,可以实现产品质量的稳定和生产效率的提高。
1.3 故障诊断与预警:智能算法可以通过监测设备状态和数据异常,实现故障的诊断和预警。
当系统出现异常情况时,智能算法可以及时发出警报并提供相应的解决方案,避免故障的扩大和损失的加剧。
1.4 能耗优化与节能减排:智能算法可以对工业过程中的能耗进行优化和节能减排。
通过分析设备的工作状态和能源的消耗情况,智能算法可以制定合理的能源管理策略,从而实现能源的高效利用和减少对环境的影响。
二、智能算法在工业过程控制系统优化设计中的原理2.1 神经网络算法:神经网络算法是一种模拟人类大脑神经元功能的计算模型。
它通过学习和训练,建立模型的输入和输出之间的映射关系,从而实现对工业过程的优化设计。
2.2 遗传算法:遗传算法模拟了自然界中的遗传和进化机制。
它通过选择、交叉和变异等操作,将优良个体遗传给下一代,逐步寻找最优解。
在工业过程控制系统中,遗传算法可以用于参数优化和控制策略的设计。
2.3 模糊逻辑算法:模糊逻辑算法是一种对于不完全信息和不确定性进行建模和处理的方法。
过程控制系统概述

过程控制系统概述杨峰电信学院06自动化3班学号:40604010321所谓过程控制(Process Control)是指根据工业生产过程的特点,采用测量仪表、执行机构和计算机等自动化工具,应用控制理论,设计工业生产过程控制系统,实现工业生产过程自动化。
一﹑过程控制的特点随着生产过程的连续化﹑大型化和不断强化, 随着对过程内在规律的进一步了解,以及仪表﹑计算机技术的不断发展, 生产过程控制技术近年来发展异常迅速.所谓生产过程自动化, 一般指工业生产中(如石油﹑化工﹑冶金﹑炼焦﹑造纸﹑建材﹑陶瓷及热力发电等)连续的或按一定程序周期进行的生产过程的自动控制.凡是采用模拟或数字控制方式对生产过程的某一或某些物理参数(如温度﹑压力﹑流量等)进行的自动控制统称为过程控制.生产过程的自动控制, 一般要求保持过程进行中的有关参数为一定值或按一定规律变化. 由于被控参数不但受内﹑外界各种条件的影响, 而且各参数之间也会相互影响, 这就给对某些参数进行自动控制增加了复杂性和困难性. 除此之外, 过程控制尚有如下一些特点:1. 被控对象的多样性.对生产过程进行有效的控制, 首先得认识被控对象的行为特征, 并用数学模型给以表征, 这叫对象特性的辨识. 由于被控对象多样性这一特点, 就给辨识对象特性带来一定的困难.2. 被控对象存在滞后.由于生产过程大多在比较庞大的设备内进行, 对象的储存能力大, 惯性也大. 在热工生产过程中, 内部介质的流动和热量转移都存在一定的阻力, 因此对象一般均存在滞后性. 由自动控制理论可知, 如系统中某一环节具有较大的滞后特性, 将对系统的稳定性和动态质量指标带来不利的影响, 增加控制的难度.3. 被控对象一般具有非线性特点.当被控对象具有的非线性特性较明显而不能忽略不计时, 系统为非线性系统, 必需用非线性理论来设计控制系统, 设计的难度较高. 如将具有明显的非线性特性的被控对象经线性化处理后近似成线性对象, 用线性理论来设计控制系统, 由于被控对象的动态特性有明显的差别, 难以达到理想的控制目的.4. 控制系统比较复杂.控制系统的复杂性表现之一是其运行现场具有较多的干扰因素. 基于生产安全上的考虑, 应使控制系统具有很高的可靠性.由于以上特点, 要完全通过理论计算进行系统设计与控制器的参数整定至今乃存在相当的困难, 一般是通过理论计算与现场调整的方法, 达到过程控制的目的.二﹑过程控制系统的组成过程控制系统的组成, 一般可用如下框图表示被控参数(变量)y(t ) ;控制(操纵)参数(变量)q(t) ;扰动量f(t) ;给定值r(t) ;当前值z(t); 偏差e(t) ;控制作用u(t)三、过程控制系统的分类按系统的结构特点来分反馈控制系统,前馈控制系统,复合控制系统(前馈-反馈控制系统)按给定值信号的特点来分定值控制系统,随动控制系统1.反馈控制系统偏差值是控制的依据,最后达到减小或消除偏差的目的。
过程控制系统与优化
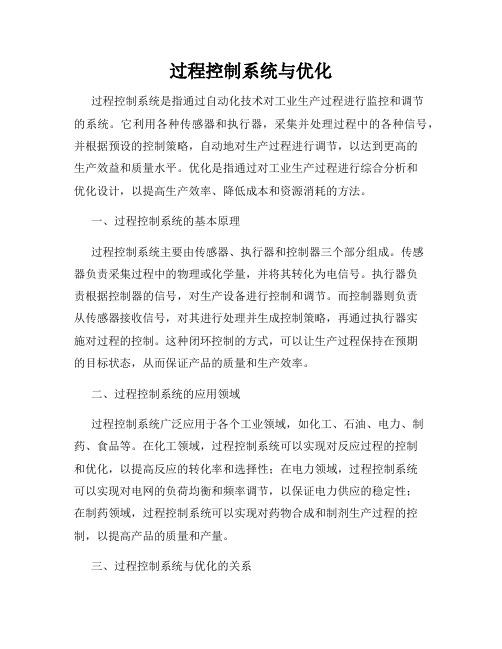
过程控制系统与优化过程控制系统是指通过自动化技术对工业生产过程进行监控和调节的系统。
它利用各种传感器和执行器,采集并处理过程中的各种信号,并根据预设的控制策略,自动地对生产过程进行调节,以达到更高的生产效益和质量水平。
优化是指通过对工业生产过程进行综合分析和优化设计,以提高生产效率、降低成本和资源消耗的方法。
一、过程控制系统的基本原理过程控制系统主要由传感器、执行器和控制器三个部分组成。
传感器负责采集过程中的物理或化学量,并将其转化为电信号。
执行器负责根据控制器的信号,对生产设备进行控制和调节。
而控制器则负责从传感器接收信号,对其进行处理并生成控制策略,再通过执行器实施对过程的控制。
这种闭环控制的方式,可以让生产过程保持在预期的目标状态,从而保证产品的质量和生产效率。
二、过程控制系统的应用领域过程控制系统广泛应用于各个工业领域,如化工、石油、电力、制药、食品等。
在化工领域,过程控制系统可以实现对反应过程的控制和优化,以提高反应的转化率和选择性;在电力领域,过程控制系统可以实现对电网的负荷均衡和频率调节,以保证电力供应的稳定性;在制药领域,过程控制系统可以实现对药物合成和制剂生产过程的控制,以提高产品的质量和产量。
三、过程控制系统与优化的关系过程控制系统与优化是密切相关的。
通过过程控制系统,可以实时监控生产过程中的各种参数和变量,并根据预设的控制策略对过程进行调节。
通过优化方法,可以对生产过程进行全面的分析和综合设计,以找到最佳的生产参数和操作策略,从而提高生产过程的效率和质量。
过程控制系统和优化方法相互结合,可以实现生产过程的动态优化,进一步提高生产效益和质量水平。
四、现代过程控制系统的发展趋势随着科技的不断进步和应用需求的不断增加,现代过程控制系统正朝着以下几个方向进行发展:1.智能化:过程控制系统越来越多地采用智能化的技术,如人工智能、模糊控制和神经网络等,以提高系统对复杂过程的识别和控制能力。
工业控制系统
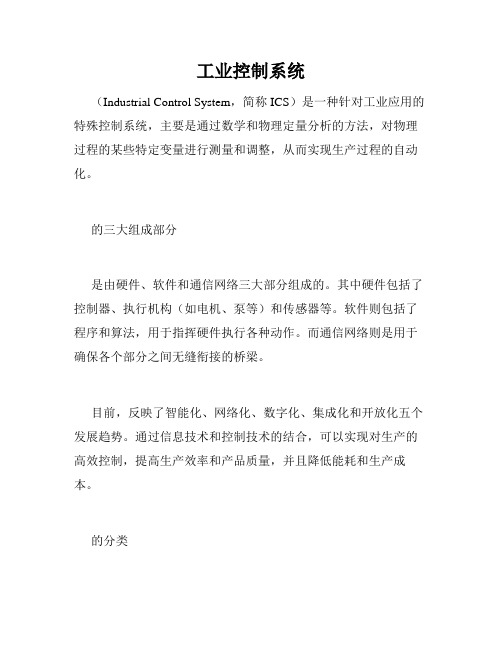
工业控制系统(Industrial Control System,简称ICS)是一种针对工业应用的特殊控制系统,主要是通过数学和物理定量分析的方法,对物理过程的某些特定变量进行测量和调整,从而实现生产过程的自动化。
的三大组成部分是由硬件、软件和通信网络三大部分组成的。
其中硬件包括了控制器、执行机构(如电机、泵等)和传感器等。
软件则包括了程序和算法,用于指挥硬件执行各种动作。
而通信网络则是用于确保各个部分之间无缝衔接的桥梁。
目前,反映了智能化、网络化、数字化、集成化和开放化五个发展趋势。
通过信息技术和控制技术的结合,可以实现对生产的高效控制,提高生产效率和产品质量,并且降低能耗和生产成本。
的分类根据控制对象的不同,可以分为过程控制系统和机器控制系统两种。
过程控制系统主要应用于化工、石油、电力、冶金、水泥、钢铁等行业,其控制对象通常是工业的物理过程,如温度、压力、流量、含量等。
过程控制系统主要分为单参数控制和多参数控制两大类。
单参数控制一般适用于控制单个物理量,如温度、压力等;而多参数控制则是将多个物理量联系在一起进行调控,如化工过程中的反应速度、温度、流量等因素的综合控制。
机器控制系统也称为离散控制系统,主要应用于机械加工、自动化装配、机器人控制等领域。
其控制对象是机器设备本身,如运动轨迹、速度、位置等。
机器控制系统一般采用开环控制或者闭环控制方式,通过感知设备发送的信号,来控制设备的运动轨迹和位置等参数。
的安全问题由于在生产领域中的重要性日益提高,因此对于其安全问题也越来越引起关注。
一旦遭到攻击或者出现故障,不仅会影响生产过程,还有可能对生产系统造成严重的损害。
针对的安全问题,现有的解决方案主要包括以下几点:1、防御攻击。
加密、访问控制和安全检测技术都是有效的安全防御措施。
其中加密技术可以对敏感信息进行加密,不让管道中的任何人来访问和窃取数据。
此外,访问控制和安全检测技术则可以限制未经授权的访问和检测任何异常活动。
工业过程控制系统设计与实现

工业过程控制系统设计与实现工业过程控制系统在现代工业生产中扮演着重要的角色,它是一种实现现代化自动化生产的关键技术之一。
随着科学技术的发展,工业过程控制系统逐渐成为工业企业中不可缺少的技术手段之一。
然而,工业过程控制系统设计与实现需要掌握一定的技术和知识,本文将就此进行探讨。
一、工业过程控制系统的概念工业过程控制系统是指将计算机技术与自动控制技术相结合,利用传感器、执行器、控制器等技术手段,对工业生产过程进行全面控制和管理的一种系统。
目的是提高企业生产效率、降低成本以及保证产品质量等。
二、工业过程控制系统的组成工业过程控制系统主要由以下几个部分组成:1、传感器:负责将实际物理量转换为电信号,并将其送至控制器。
2、控制器:负责根据对被控制对象的监测数据来进行计算和判断,并发出相应的控制信号,予以实现对被控对象的控制。
3、执行器:负责将控制信号转换为能够引起被控对象状态的控制动作,如通过振动、压力等方式对被控对象进行控制。
4、人机界面:通过人机交互界面,生产过程控制人员可以对整个过程进行实时监控和管理,以及根据生产需要进行各种数据分析、生产调度等操作。
三、工业过程控制系统的设计流程1、需求分析:在进行工业过程控制系统的设计之前,首先需要对所要控制的对象进行需求分析。
需要明确被控物体的控制需求及控制对象所需要完成的工作。
2、系统设计:在了解被控对象的需求后,需要进行系统设计,根据需求场景根据被控对象的运行状态、数据通信、数据处理、人机界面等方面进行设计。
3、硬件选型:根据需求分析、系统设计的要求,为系统选择合适的硬件设备,包括传感器、控制器、执行器、数据采集卡等。
4、系统实现:根据硬件选型,开始对系统进行实现,包括软硬件的编程、算法的设计等。
5、调试测试:对设计实现的系统进行进行调试和测试,检测系统是否能够达到控制要求,是否能够正常运行。
6、系统维护:当系统正式推广到生产中时,需要进行后期的维护和更新。
- 1、下载文档前请自行甄别文档内容的完整性,平台不提供额外的编辑、内容补充、找答案等附加服务。
- 2、"仅部分预览"的文档,不可在线预览部分如存在完整性等问题,可反馈申请退款(可完整预览的文档不适用该条件!)。
- 3、如文档侵犯您的权益,请联系客服反馈,我们会尽快为您处理(人工客服工作时间:9:00-18:30)。
IN 2
OUT 2
可设置限值
PLC
DGT1在系统中的应用示例
标准软件功能
• 通过称重显示器的键盘或PC端的Dini- • 快速准确的重量读取,速度可达3200Hz。
tools软件,可以进行数字标定或理论 标定,并可将仪表的配置进行备份, 便于技术支持或在其他仪表上重复设 置(OEM)。
• 标配支持Modbus RTU协议。 • Dini Argeo协议,可在电脑端的控制软
多功能软件使您可以将重量转换为其 它单位(牛顿、升、件等)、测量峰 值重量、进行连续累计并传输总重。
软硬件的设计由专业的工程师在意大 利完成。所有产品均可以根据EN4550 1、OIML R67用于贸易结算。
通过外部即插即用的转换装置,您还 可以通过以太网、WIFI、PROFIBUS和 无线电进行通讯。 该系列称重显示器可方便地安装在DI N导轨或标准尺寸面板开孔中。
18
单物料加料(至多4个称量斗)
19
单物料卸料(至多4个称量斗)
20
多物料逐次配料
21
多物料同时配料
22
皮带秤
23
失重秤
24
28
Dinitools, Weimonitor
30
单剪切梁传感器
32
轮辐式传感器
34
双剪切梁传感器
36
波纹管传感器
38
铝制平行梁传感器
40
不锈钢平行梁传感器
42
S型传感器
44
应用指南
4
过程称重解决方案
轮重和轴重秤
模拟或无线称重片,适用于在任何平地上建立移动式车辆称量站,节省时间和 成本。
工业秤
多功能、灵活精确的工业桌秤和地磅,以及高度灵活的称重模块,适用于工业、 商业和实验室使用。
“Scale House”系列工业秤、实验室设备和商业秤
“Scale House”系列是面向欧洲市场的具有较高性价比的精选系列产品。
170
75
170
67
160
170
106
160 160
5
8
过程称重解决方案
72
115
5
PROCESS CONTROL
FILLING
LOAD CELLS SOFTWARE ACCESSORIES BATCHING
主要规格参数
技术指标
DGT 1
DGT 4
DGTQ
DGTP
DGT20 DGTPK
供电
传感器允许连接最大个数
在爆炸性 环境中称重
我们的部分产品、方案、配件可以用于 EX 1&21、2&22爆炸性环境中。
请访问www.diniargeo.com 网站查看更 多防爆产品信息。
过程称重解决方案
7
88.6
96
67
72
PROCESS CONTROL
DGT 1 • 重量变送器,单通道,DIN导轨安装
53
58
90
53
58
106
58
90 90
ห้องสมุดไป่ตู้
DGT 4 • 重量变送器,4通道,DIN导轨安装
106
58
5
115
115
72
114335.5 135
170 170 160 160
120
120
67
120.5
9
96
6
90
88.6
80 96
9
90 170
80
FILLING
90
5
LOAD CELLS SOFTWARE ACCESSORIES BATCHING
这些标志给出了传感器的典型应用方式,表示:
1. 吊挂式料斗/槽罐
2. 各尺寸料筒
3. 水平槽罐(无论是否包含液体) 4. 4传感器秤台
5. 单传感器秤台
过程称重解决方案
5
PROCESS CONTROL
FILLING
过程控制
重量读取、传输及处理
该系列称重显示器是针对过程控制领 域设计的具有高性价比的解决方案, 可读取传感器的数据并将其通过RS23 2、RS485、继电器输出、模拟输出等 传输至外部设备(PC、PLC,微处理器 等)。
适用于零售行业的商业秤、收银机和自动化设备
Helmac设计和生产各类适用于商店、超市等的计价秤、台秤和吊秤,以及POS机 系统、收银机和适用于食品行业的自动计价打标系统。
砝码和标定服务
Cibe计量实验室可提供各类型砝码、砝码组、配件以及标定服务和自动及非自 动称重设备的法定周期性校验。
称重软件
Syntweb可提供与称重有关的各类软件方案,包括重量的读取、检验和记录;手 动自动配料;车辆IN/OUT称量;生产周期管理以及废弃物处理和追踪;计件;加 料过程检重等。
7722
11155
55
DGT Q • 称重显示器,面板安装,尺寸90x80mm
114433..55
112200..55
99
9966
6633
88.8.66
9966
6677 110066
113355 9900
8800
112200
99
117700
7755
DGT P 117700
• 称重显6677示器/重量变送器,面板安装。4通道,尺寸136x67mm
标识说明
INOX
INOX
AISI 304
具有此标志的产品可以用于根据ATEX条例规定具有爆炸性风险的环境(1 和21区或者2和22区)。
具有此标志的产品,材质为不锈钢,可用于对卫生有高要求的环境或需要 防腐蚀的环境。
IP等级说明了产品对固体(第一个数字)和液体(第二个数字)的防护等 级。Dini Argeo的许多产品都提供了对灰尘、潮湿和水溅的保护(IP65和 67)以及浸水密封保护(IP68)。
DINI ARGEO生产CE-M认证仪器或通过 CE-M认证的仪器(根据EN45501欧洲 条例-EEC90/384条例)。意大利中央 计量办公室(Italian Central Metric Office)颁发的CE-M认证说明了仪器 符合CE类型认证说明书,它规定了贸 易结算用仪器的相关规定。
46
接线盒
48
工业过程称重系统
Dini Argeo专业设计和生产各类称重 系统,并以其质量和可靠性闻名。
• 物流称重(托盘车秤、叉车秤及吊秤) • 车辆称重(汽车衡、静态或动态轮重
或轴重系统)
Dini Argeo公司为工业称重领域提供
完美的解决方案: • 读取、处理和传输重量数据 • 逐次或同步配料、包装加料或卸料、
116600
143.5
120.5
9
143.5 143.5
120.5 120.5
9 9
6767 67
7272 72 117700
111366500
116600
135 135
8080 80
120 121020
9
55
9
170 9
75
DGT 20 • 称重53 显示器58 /重量变送器,台式或1面70板安装。4通道67,尺寸160x106mm
皮带连续配料或失重秤 • 防爆区域称重 • 计件、标签系统
Dini Argeo产品的大量可选接口和通讯 协议使其可以方便地集成在各种自动化 和过程控制系统中,并可根据客户要求 建立OEM系统。
• 检重包装货物
生产 设计 质控
2
过程称重解决方案
DINI ARGEO: 质量体系和认证
DINI ARGEO根据UNI EN ISO 9001: 2008条例获取了质量管理体系认证。
件上读取重量、数字输入以及驱动继电 器输出。
• 最多8个线性化点(可设置)。 • 快速零点标定。 • 传感器过载/欠载控制。 • 键盘锁定功能和菜单访问权限设置功
• 事件日志。 • 可根据需要定制软件(OEM)。 • 通过以太网、PROFIBUS、WIFI、USB、
输入输出扩展板进行通讯。
能(密码设置)。
PROFI232:RS232>>PROFIBUS转换器 第28页
LOAD CELLS SOFTWARE ACCESSORIES BATCHING
RS232
清零 去皮 数据传输
RS485
V/A 模拟输出 0-5Vdc ; 0-10 Vdc ; 0 - 20mA ; 4 - 20 mA
IN 1
OUT 1
OIML
Dini Argeo公司生产的仪器符合国际
OIML标准: • OIML R60传感器认证 • OIML R76非自动化称重仪器认证 • OIML R134动态称重认证
Dini Argeo公司生产的仪器符合俄罗 斯联邦国际标准Gost-R认证。
Dini Argeo集团:360度全面服务
Dini Argeo可向客户提供方案定制、称重产品、PC端软件开发和网络通讯、标定服务、OEM系统认证等各方面服务。Dini Argeo已发展为一个具有国际知名度的集团,在欧洲、亚洲有数个分公司,并在全球超过70个国家有售后服务网络。 整个集团由Dini Argeo及其分公司组成,包括:
商业秤 www.helmac.it
软件和网络方案
计量实验室 www.cibelab.it
标定、安装、售后服务网络 www.servistar.it
硬件开发 www.selene-electronics.it
过程称重解决方案
3
最大显示分辨率 A/D转换器 转换速率/分辨率
24位 单通道
红色LED显示屏
8 mm