4300宽厚板车间工艺设计11
4300mm宽厚板热处理线工艺及主要设备介绍

4300mm宽厚板热处理线工艺及主要设备介绍张训江 熊 伟 王明亮(宽厚板厂)摘 要 本文简要介绍了鄂钢4300mm宽厚板热处理线的工艺流程,并对其中的辐射管加热无氧化辊底式热处理炉和辊式淬火机的主要工艺设备特点、选择原则进行了重点介绍。
关键词 热处理线 辐射管 辊式淬火机 工艺特点1 前言热处理是将固态金属或合金采用适当的方式进行加热、保温和冷却,以获得预期组织结构与性能的工艺,通过热处理可以改变钢的组织形态,细化晶粒,从而提高材料的韧性及强度,改善材料的机械性能和工艺性能,提高材料的可靠性及使用寿命。
是充分挖掘材料性能和节约合金元素的重要手段之一。
热处理对提高产品附加值,增加企业核心竟争力具有举足轻重的作用。
为了优化鄂钢公司的产品结构,提高其市场竞争力,在4300mm宽厚板轧线后建设两条热处理线,包括一条淬火线和一条正火线。
其中,淬火线包括一座淬火炉(辐射管加热无氧化辊底式热处理炉)及辊式淬火机,用于钢板奥氏体化、正火及回火;正火线(明火炉),用于钢板的正火及回火。
2 热处理线热处理能力热处理的产品品种有造船板、锅炉板、压力容器板、模具用钢板、海洋平台板及低合金高强度钢板。
两条线年热处理成品总量为20,8 104t/a,年热处理总量为30 6 104t/a,两座炉热处理量分配见表1。
表1热处理炉年处理量 (t)淬火炉正火炉合计正火处理量24,000104,000128,000正火后回火量--18,00018,000淬火处理量80,000--80,000淬火后回火量30,00050,00080,000合计134,000172,000300,6003 工艺流程钢板在进入淬火炉前需要进行抛丸处理,目的是去除钢板表面的氧化铁皮,消除氧化铁皮对钢板热传导性能的影响以及划伤钢板表面而影响钢板表面质量,使钢板在加热过程中温度更加均匀,淬火过程中能够淬透,避免淬火软点。
抛丸后一些微小的氧化铁皮粒子将被磁化而吸附在钢板表面,如果随钢板带入炉内,将会引起炉底辊结瘤,所以抛丸后的钢板需用物理方法清除微小的氧化铁皮离子。
莱钢4300宽厚板提高成材率采用的轧制新技术
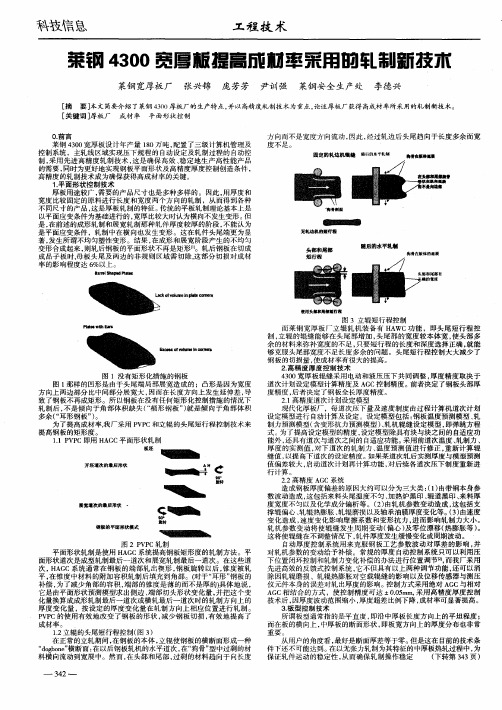
余 的 材料 来 弥补 宽 度 的不 足 , 只要 短 行 程 的 长度 和 深度 选 择 正 确 , 能 就 够克服头尾 部宽度不足长度多余 的问题 。头 尾短行 程控制大大减少 了 钢板的切损量, 使成材率有很大的提高。 2高 精 度 厚 度 控 制 技 术 .
鱼lmI f 鞘哺● Pa ¨ l ̄ t
‘ 粕量甜鬻
…
 ̄ ̄Tt s m i岫 et en
健埘头挪 聃 籍杼程
一
图 3 立 辊 短 行程 控 制
而莱钢 宽厚 板厂立辊 轧机装备有 H WC功能 ,即头尾 短行程控 A 制, 立辊 的辊 缝能够在头尾部增 加 , 头尾部 的宽度 较本体宽 , 使头部 多
... — —
40 30宽厚 板辊缝 采用电动和液压压下共 同调 整 , 厚度精度取决 于 道 次计划设定模型计算精度及 A C控制精度。前者决定了钢板头部厚 G 度精 度 , 后者决定 了钢板全长厚度精度。 2 高精度道次计划设定模型 . 1 现代化厚板厂 ,每道次压下量及速度制度 由过程计算机道次计划 设定模 型进行 自动计算及设定 。设定模型包括 : 钢板温度预测模 型、 轧 制力 预测模 型( 含变形抗力预测模型 )轧机辊缝设定模型 , 、 即弹跳方程 式。 为了提高设定模型的精度 , 设定模 型除具有块与块之间的 自 适应功 能外 , 还具有道次与道次之间的 自适应功能。 采用前道次温度 、 轧制力 、 厚度 的实测值 , 对下道次 的轧制 力 、 温度预测值进 行修正 , 重新计算辊 缝值 , 以提 高下道次的设定精度。如果某道次轧后实测厚度与模 型预测 值偏差较大 , 启动道次计划再计算功能 , 对后续各道次压下制度重新进 行计算 。 22高精度 A . GC系统 造成钢板厚度偏差 的原 因大约可 以分为三 大类 :1 由带 钢本身参 () 数波动造成 , 这包括来料头尾温度不匀 、 加热炉黑 印 、 辊道黑 印 、 来料厚 度宽度不匀 以及化学成分偏析等 。( ) 2 由轧机参数变动造成 , 这包括支 撑辊偏心 、 轧辊热膨胀 、 轧辊磨损以及轴承油膜厚度变化等。 3 由速度 () 变 化造成 , 速度 变化影响摩擦 系数 和变形抗力 , 而影响轧制力大小 。 进 轧机参数变动将 使辊缝发生周期变 动( 偏心 ) 及零 位漂移( 热膨胀等 ) 。 这将使辊缝 在不调整情况下 , 轧件厚度发生缓慢变化 或周期波动。 自动厚度控制 系统用 来克服钢板工 艺参数波动对厚差 的影响 , 并 对 轧机参数 的变动给予补偿 。常规 的厚度 自 动控制 系统 只可 以利用压 下位 置闭环控制 和轧制力变化补偿 的办法进行位置调节目, 而我厂采用 先进 高效 的反馈式控制系统 , 它不但具有 以上两种 调节功 能, 还可 以消 除因轧辊磨损 、轧辊热膨胀对空载辊缝 的影 响以及位 移传感 器与测 压 仪元件本 身的误差对轧 出厚度的影响。控制方式采用绝对 A C与相对 G A C相结合的方式 ,使控制精度可达 ± . r , G 0 5 m 采用高精度厚度控 制 0a 技术后 , 因厚度波动范 围缩小 , 厚度超差 比例下 降, 成材率可显著提高。
4300工艺流程

生产工艺操作主要工序简介板坯库及钢锭库内工艺流程厚板连铸车间运送来的厚板坯通过汽车运送到No.1、No.2或No.3板坯库内,由主厂房起重机吊运下坯。
然后通过板坯库内的电动平车可分别送至其他板坯库内堆跺,组坯准备上料进入加热炉。
按计划准备上料的板坯首先由主厂房起重机吊至上料辊道上,然后由No.1板坯横移小车将板坯横移至上料辊道上,在No.2板坯称重装置上称重。
准备进入No.1加热炉(推钢炉)进行加热的板坯,再通过No.2板坯横移装置,横移至No.1加热炉上料辊道上按照计划准备入炉;准备进入No.2加热炉的板坯则可直接通过No.2炉前辊道,直接运送至No.2入炉辊道上,按照计划等待入炉。
从厂外运送来的钢锭,通过汽车运至钢锭跨,由主厂房的钢锭夹钳吊运下料堆放。
按照要求,运至钢锭库内的钢锭为切除帽口的合格钢锭,对于表面存在缺陷及留有残渣和飞边的钢锭,则通过火焰切割枪对钢锭进一步进行处理。
表面处理完毕的钢锭,按照计划等待入均热炉。
均热炉也考虑了厚板坯加热的工艺要求。
对于采用均热炉加热的厚板坯,通过板坯库内的过跨电动平车,直接运进钢锭库内,按照计划由钢锭夹钳吊运至均热炉的炉坑内。
装炉、加热及出炉加热炉区共设3座加热炉和12座均热炉。
其中一期建设1座推钢式加热炉、1座步进式加热炉和1座均热炉。
二期增建另外1座步进式加热炉。
加热炉区完成上料后的板坯根据入炉计划分别送至各个加热炉的装炉辊道上,由推钢机或装钢机送入加热炉内进行加热。
在已给定的坯料条件下,No.1~2加热炉均采用双排装料。
加热的工艺操作包括对加热温度、加热速度、加热时间等工艺参数的控制以及对炉温制度、炉内气氛和炉压等的控制。
坯料一般加热到1,100℃~1,200℃。
对于中高碳钢、合金结构钢和高铬高镍类合金钢,加热温度偏靠下限。
对控制轧制所采用的微合金化钢,出于缩短轧制过程中的待温时间和细化奥氏体晶粒的双重要求,一般需采用低温加热。
加热温度可进一步降至1,050℃左右。
济钢210t-4300宽厚板线工艺装备和产品介绍
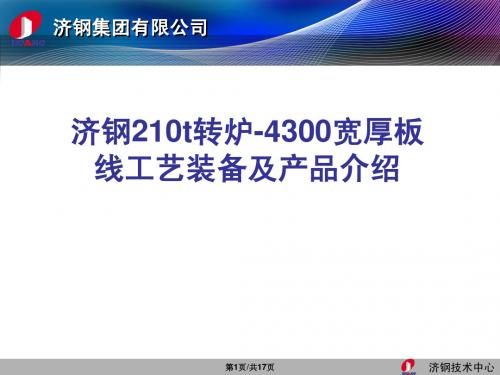
济钢技术中心
备,达到国际一流先进水平。
该产线目标聚集“高、精、尖、新、特、优”,积极推进差异化 战略,做精品宽厚钢板,努力打造我国宽厚钢板、特厚钢板领域的创 新与产业化基地。 该产线始终把客户价值摆在首位,加快产品、工艺技术开发步伐, 加大热机械轧制技术、控轧控冷技术的应用,加强高效产品的自主创 新能力,培育宽厚板领域内领先核心技术,形成一批拥有自主知识产 权的拳头产品。
济钢技术中心济钢集团有限公司济钢集团有限公司210t4300济钢技术中心济钢集团有限公司济钢集团有限公司产线定位济钢技术中心济钢集团有限公司济钢集团有限公司济钢宽厚板生产线是我公司十一五规划的重点工程配备210吨转炉4300mm宽厚板轧机等大型化自动化现代化的先进工艺装备达到国际一流先进水平
济钢集团有限公司
济钢集团有限公司
MUPIC 冷却:配置了当
今最先进的多功能冷却 设备,具备 ACC/DQ/AQ+A CC 等冷却功能,能够满 足各种 TMCP 和在线淬火
工艺要求。
MUPIC冷却系统
第10页/共17页
济钢技术中心
济钢集团有限公司
板型控制 在 MULPIC 系统之前配备了预矫 直机,提高了钢板的板形控制水平 和冷却均匀性。 精整线配备了强力的热矫直机、 冷矫直机等设备,能最大限度地消
第3页/共17页
济钢技术中心
济钢集团有限公司
2、装备保障能力
炼钢 KR 铁水预处理 1 座,脱硫后
铁水硫含量在20ppm以下。
210t 转炉炼钢系统采用顶底 复吹工艺,采用副枪技术、两 级自动化控制系统及德国鲁奇
LT干法除尘等国际先进技术,
在冶炼经济和环保方面达到国 内先进水平。
第4页/共17页
4300mm宽厚板轧机轧制8mm厚钢板生产实践

在轧制8mm 厚 钢 板 前,将 工 作 辊 辊 身 中 部 冷却水开启量 调 整 为 80%,两 侧 调 整 为 50%,使 轧辊中部冷却收 缩 率 增 加,减 小 轧 辊 中 部 的 热 凸 度,同 时 配 合 弯 辊 力 的 调 整,板 形 控 制 效 果 良 好。 实际生产过程中可根据季节与环境温度的不同调 整冷却水量,冷却 水 量 过 小 会 使 辊 身 温 度 过 高 从 而造成辊面出现 疲 劳 裂 纹;冷 却 水 量 过 大 会 增 大
钢 板 在 轧 制 过 程 中 的 温 降 ,增 加 轧 制 难 度 ,不 利 于 板形控制 。 [4] 3.4 轧 制 规 程
轧制薄规格钢板时轧制规程的制定主要考虑 5个方面:一是轧制道次应尽 可 能 少,加 快 轧 制 节 奏,减 少 轧 制 时 间;二 是 应 满 足 目 标 厚 度 要 求;三 是应充分考虑板 形 和 金 属 横 向 流 动 的 要 求,精 轧 后3个道次的轧制力与出口轧件厚度基本呈线性 关 系 ;四 是 应 满 足 设 备 安 全 要 求 ,不 能 超 过 极 限 负 荷;五是应满足轧制工艺的要求 。 [5]
Abstract:The heating process,initial roll shape design,roll body cooling,rolling schedule and rolling plan were studied,and the 8mm×3800mm thin gauge plate was successfully produced by 4300mm wide and heavy plate mill .Meanwhile,the volume stable production ability was formed. Key words:wide and heavy mill;thin gauge plate;shape of plate;process control
莱钢4300mm宽厚板生产线工艺技术特点
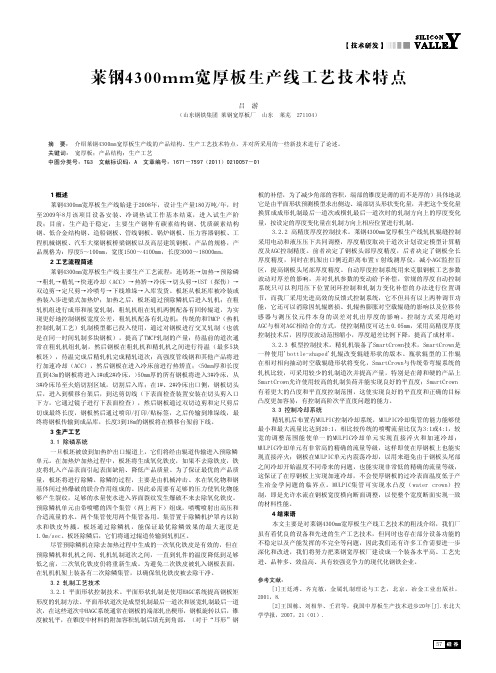
莱钢4300mm宽厚板生产线工艺技术特点吕游(山东钢铁集团 莱钢宽厚板厂山东莱芜 271104)摘 要:介绍莱钢4300mm宽厚板生产线的产品结构、生产工艺技术特点,并对所采用的一些新技术进行了论述。
关键词:宽厚板;产品结构;生产工艺中图分类号:TG3 文献标识码:A 文章编号:1671-7597(2011)0210057-011 概述板的补偿,为了减少角部的容积,端部的锥度是薄的而不是厚的)具体地说它是由平面形状预测模型求出侧边、端部切头形状变化量,并把这个变化量莱钢4300mm宽厚板生产线始建于2008年,设计生产量180万吨/年,时换算成成形轧制最后一道次或横轧最后一道次时的轧制方向上的厚度变化至2009年8月该项目设备安装、冷调热试工作基本结束,进入试生产阶量,按设定的厚度变化量在轧制方向上相应位置进行轧制。
段;目前,生产趋于稳定,主要生产钢种有碳素结构钢、优质碳素结构3.2.2 高精度厚度控制技术。
莱钢4300mm宽厚板生产线轧机辊缝控制钢、低合金结构钢、造船钢板、管线钢板、锅炉钢板、压力容器钢板、工采用电动和液压压下共同调整,厚度精度取决于道次计划设定模型计算精程机械钢板、汽车大梁钢板桥梁钢板以及高层建筑钢板,产品的规格,产度及AGC控制精度。
前者决定了钢板头部厚度精度,后者决定了钢板全长品规格为:厚度5~100mm,宽度1500~4100mm,长度3000~18000mm。
厚度精度,同时在机架出口侧近距离布置γ射线测厚仪,减小AGC监控盲2 工艺流程简述区,提高钢板头尾部厚度精度。
自动厚度控制系统用来克服钢板工艺参数莱钢4300mm宽厚板生产线主要生产工艺流程:连铸坯→加热→预除磷波动对厚差的影响,并对轧机参数的变动给予补偿,常规的厚度自动控制→粗轧→精轧→快速冷却(ACC)→热矫→冷床→切头剪→UST(探伤)→系统只可以利用压下位置闭环控制和轧制力变化补偿的办法进行位置调双边剪→定尺剪→冷喷号→下线堆垛→入库发货。
济钢4300mm宽厚板生产线工艺及设备特点
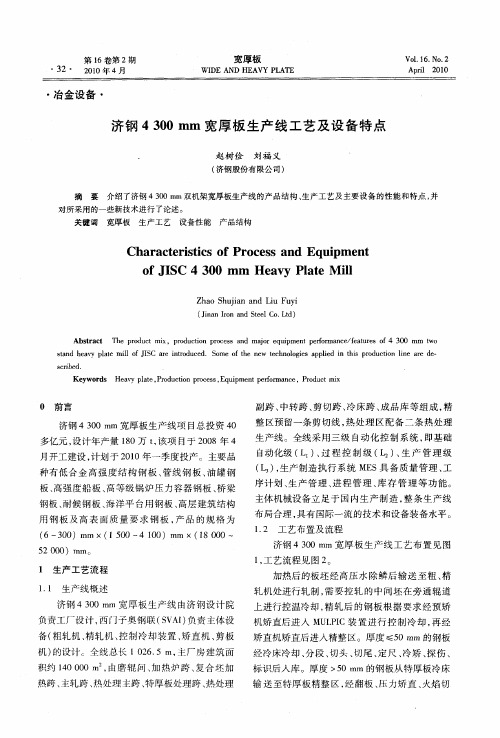
第 2期
赵树俭等 : 济钢430m m宽厚板生产线工艺及设备特点 0
。 3・ 3
1 步进式加热炉 ;2 台车式加热炉; 3 高压水除鳞系统 ; 4 四辊粗轧机 ;5 旁通辊道装置 ;-1 精轧机 ; 一 一 一 - - 6  ̄
7 预矫机 ; 8轧后 控制冷却装置 ; 9 热矫直机 ; 1一 一 一 一 O 步进 式 冷 床 ; l一 头 剪 ; 1 一 边 剪 ;3 超 声 波 探 伤 装 置 1切 2双 1一 1 定 尺 剪 ; l 一冷 矫 机 ; 1 一 平 机 ; 1一自动 火 焰切 割 机 ; 1一 4一 5 6压 7 8 厚板 缓 冷坑 ; 1一 段 剪 2 一 刃 机 ; 9分 O抛 2 一 底 热 处 理 炉 ; 2 一自动 火 焰 切 割 机 ; 2 一 火 机 ; 2一 直 机 ; 2一 床 ; 2 一 样 剪 ; 2 一 库 1辊 2 3淬 4矫 5冷 6取 7板
矫 直机矫 直后进入 精整 区。厚度 ≤5 / 的钢板 0FT f/ /
经冷床 冷却 、 分段 、 切头 、 尾 、 尺 、 切 定 冷矫 、 伤 、 探
标 识后入 库 。厚度 > 0m 的钢板从 特厚板冷 床 5 m 输 送 至特厚 板精整 区 , 经翻板 、 力矫 直 、 压 火焰切
( 济钢股份有限公)
摘
要
介绍了济钢 430m 0 m双机架宽厚板生产线 的产 品结构 、 生产 工艺及主要设 备的性能和特点 , 并
生 产工 艺 设备 性 能 产 品结 构
对所 采 用 的 一些 新 技 术进 行 了论 述 。 关 键 词 宽厚 板
Ch r c e itc fPr c s n u p e t a a t rs is o o e s a d Eq i m n
宽厚板生产工艺设计

宽厚板生产工艺设计摘要本文对中厚板目前在我国的发展状况形式及中厚板轧制过程中的轧制规程、轧制方法及道次的确定进行阐述,并且对中厚板在轧制中的工艺、参数、设备,进行了进一步说明。
关键词:中厚板 ;轧钢工艺;轧钢设备Design of the production process of heavy plateAbstractIn this paper, plate current form of development in China and in the process of plate rolling schedule, rolling method and passes the determination to elaborate, and on the plate in the rolling process, parameters, equipment, further instructions.Key words: plate; steelrolling process; steelrolling equipment目录第1章绪论.......................................... 错误!未定义书签。
1.1国内中厚板生产简介................................... 错误!未定义书签。
1.2国外中厚板轧机的发展................................. 错误!未定义书签。
1.3中厚板生产的进步 (4)1.3.1生产技术方面的进步 (4)1.3.2装备方面的进步........................................................................... 错误!未定义书签。
1.4我国中厚板发展的不足................................. 错误!未定义书签。
- 1、下载文档前请自行甄别文档内容的完整性,平台不提供额外的编辑、内容补充、找答案等附加服务。
- 2、"仅部分预览"的文档,不可在线预览部分如存在完整性等问题,可反馈申请退款(可完整预览的文档不适用该条件!)。
- 3、如文档侵犯您的权益,请联系客服反馈,我们会尽快为您处理(人工客服工作时间:9:00-18:30)。
进入 21 世纪以来,大型造船业,海洋工程,桥梁、大口径石油、天然气输送管线、大型压力容器和贮罐、重型建筑结构(特别是高层、防火、耐侯、大跨度和非对称的空间结构用途、机械工程的技术进步和旺盛需求,极大地拉动了宽厚板的发展,低合金、高强度的宽厚板的生产技术进步。
宽厚板轧机生产的产品的厚度在 5- 100(200)mm,宽度在 3500- 4800(5300)mm。
高强度宽厚板钢材的屈服强度一般在 345MPa 以上,用于重大钢结构的则有Q345、Q390、Q420 和 Q460,例如 2008 年奥运会主体工程———国家体育场(鸟巢结构)就大量使用了舞阳钢厂生产的厚度为 110mm 的 Q460E- Z35 钢板。
为了提高安全性和整体性能,减轻自重,减少焊接量,造船和海洋平台则多用 D36 和 E36 以上的宽厚板,用于大口径石油和天然气输送管线多用 X70 级以上,甚至 X100和 X120 等级的抗硫化氢腐蚀的宽厚板。
这些用途的宽厚板往往还单独或综合要求具有良好的低温冲击性能,抗焊接热影响和裂纹敏感特性,或者试件断面收缩率Ψ达到 25%或 35%以上的抗层状撕裂的性能。
生产工艺简单。
中厚钢板大约有200年的生产历史,它是国家现代化不可或缺的一项钢材品种,被广泛应用于大直径输送管、压力容器、桥梁、锅炉、海洋平台、坦克装甲、各类战舰、车辆、机器结构、建筑构件等领域。
其种类繁多,使用温度要求广(-200—600℃),使用环境要求复杂(耐蚀性、耐候性等),使用强度要求高(强韧性、焊接性能好等)。
一个国家的中厚板轧机水平也是一个国家钢铁工业装备水平的标志之一,进而在一定程度上也是一个国家工业水平的反映。
随着我国工业的发展,对中厚板产品,无论是数量上还是品种质量上都提出了更高的要求。
控制轧制和控制冷却技术在国际上称为TMCP(Thermo-MechanicalControl Process),也有直译为热机械处理),它以冶金工艺(如再结晶、相变、沉淀)为基础,并充分利用强化机理(如固溶强化、沉淀强化、晶粒位错强化),特别是通过限制变形和温度条件使晶粒细化,将强度和韧性良好结合,使轧后状态下的钢板获得预定的最佳材质性能。
随着微合金细晶粒钢的进一步开发,它既有高强度,又由于碳含量的降低(≤0. 15% ),碳当量随之降低为0. 32%~0. 38%,从而进一步提高了钢板的韧性和焊接性能。
在控制轧制后再加速冷却,又进一步提高了钢板的综合性能。
因此TM-CP是当今厚板生产中最关键的工艺技术,可用来生产高屈服强度、高韧性和良好焊接性能的厚板表1 我国4000~5500mm宽厚板轧机简况序号企业简称轧机/mm 年产量/万t 投产/改造年·月说明1 宝钢5100 140 2005.5 引进德国SMS技术2 鞍钢4300 100 1993/2003 引进日本旧设备,引进技术改造3 舞钢4200 120 1979 国产4 宝钢浦钢4200+3500 143 1991 3500mm轧机、矫直机国产,5 沙钢5100 140 2006.11 引进奥钢联技术6 秦皇岛中板厂4300(二) 120 2006.10 引进德国SMS技术7 宝钢罗泾4200 160 2008 引进德国SMS技术8 鞍钢(营口) 5500 150 2006.8 引进德国SMS技术9 包钢4100 120 2007 引进德国SMS技术10 莱钢4300 180 2008 引进奥钢联技术11 鄂钢4300 120 2008.8 引进奥钢联技术控制轧制是相对常规轧制而言。
常规轧制时对终轧温度不甚讲究,相对较高,以致强度较低,对有些钢板则必须经热处理后才能达到性能要求。
控制轧制技术的关键之一要控制终轧温度,以往采用控温轧制TCR (Temperature Con-trolled Rolling),选择在稳定的奥氏体中的γ→α相变点略高、高于奥氏体再结晶温度时完成轧制。
根据板坯出炉温度和钢板厚度的不同,必须在轧制过程中待冷,以达到规定的终轧温度,使晶粒细化,经过再结晶和相变后, 可获得相当于正火后的铁素体—珠光体组织。
控制轧制TMR(Thermo-Mechanical Rolling)是在TCR基础上进一步发展起来的。
为获得更高的屈服强度和韧性,除需要更低的终轧温度外,还要控制最终的变形程度。
例如:屈服强度为450~500MPa的微合金的终轧温度在700~750℃,最终变形程度为2. 5~3. 5(相对压下率为60%~70% ),这就必须考虑轧机要有承受高荷载的可能。
为达到需要的终轧温度和最终变形程度,中间轧件开始进入终轧阶段的温度不能太高,而其厚度要适应最终变形程度的要求。
控制冷却是TMCP中又一重要工序,能进一步改善钢板性能。
对微合金高强度钢采用控制轧制,并紧接着加速强行冷却,使轧后组织转变为更细化的铁素体加贝氏体或单一的贝氏体,屈服强度更高,韧性和焊接性能也更好。
据国外资料报导,以海上平台用的含铌微合金钢为例,经从800℃强冷到550℃后(冷却速度为15℃/s),比一般控温轧制的钢板的屈服强度约可提高50MPa,与经正火处理的相比,约可提高150MPa。
为使控制冷却后的钢板达到预期的性能和平直度,对不同钢种、不同厚度、不同温度的钢板需采用不同的冷却速率。
冷却水流有水幕、单层流喷射、水/空气、水浸等多种型式。
钢板在水冷装置下的冷却方式有通过型(钢板边运行边冷却)、停止型(钢板不动整块同时冷却)、摇摆型(钢板在水冷装置下的辊道上来回摆动)。
轧机布置宽厚板轧机均采用四辊机架,单机架宽厚板轧机的产能为120- 180 万t/年,增加一架粗轧机后产能为150- 200 万t。
我国的宽厚板轧机至今都是分别由德国SMS- Demag 和奥地利SIEMENS- V AI 公司技术总负责建设的。
轧机本体均配备电动/液压压下,强力的液压弯辊和窜辊,具有很好的板厚公差液压和板形控制功能。
双机架配置的机组,其粗轧机架装有立辊,用于侧压定宽,具有液压自动调宽和短行程控制功能;机架的设计结构和参数与精轧是一样的,粗轧机架的开口度要高,特别是考虑用钢锭轧制的机组。
轧机的工作辊多用铸铁轧辊,采用滚动轴承;支承辊则采用合金铸钢或合金锻钢辊,采用油膜轴承产品大纲品种代表钢号钢板规格mm 执行标准产量万吨/年比例%碳素结构板Q195,Q275,Q215,Q23520~80×900~4000×3000~2500010 10.8低合金高强度板Q295,Q345,Q390,Q420 20~80×900~4000×300~2500011 11.9造船及海洋石油平台用板A,B,D,E,AH32,AH36,AH40,DH32,DH36,DH40,EH36,EH40,FH32,FH36,FH405~100×900~4000×300~25000GB712-2000 45 49工程机械用板09CuCrNi,16CuCr,StE460 5~100×900~4000×300~25000ASTMDIN1710210 10.8锅炉板20g,16Mng,15MnVg 5~100×900~4000×300~25000 GB713-1997 9 9.8SB410,SB450,SB480 JIS G3115(2005) A202,A299,A302,A516 ASTM压力容器板16MnR,15MnVR 5~100×900~4000×300~25000GB6654-1996 7 7.6 SPV355,SPV490 JSI G3115A622,A203,A517 ASTM合计92 100金属平衡表金属平衡是反映在某一定时期(通常是一年),产品金属材料的收支情况。
它是编制车间生产预算与制订计划的重要数据,同时对于设计车间的内部运输与外部运输以及平面布置,也是极为重要的依据。
因此,必须在确定产材率及金属损失率的基础上,编制出各种计算产品的金属平衡表。
表2.2 金属平衡表编号产品原料重量t 成品重量t烧损%切损%轧损%成材率%1 碳素结构板1.6 6.0 1.4 91.03 低合金高强度板1.3 6.0 1.8 90.94 造船及海洋石油平台用板1.4 6.2 1.7 90.76 工程机械用板1.9 5.8 1.5 90.87 锅炉板98901 90000 1.6 6.0 1.4 91.08 压力容器板76754 70000 1.7 6.1 1.0 91.2 2.3 典型产品40×2750×8000mm Q215B普碳钢板压下规程设计Q215B有一定的伸长率、强度,良好的韧性和铸造性,易于冲压和焊接,广泛用于一般机械零件的制造。
主要用于建筑、桥梁工程上质量要求较高的焊接结构件。
化学成分如下:表2.3化学元素 C Si Mn S P Cr Ni Cu≤Q215B 0.12~0.2 ≤0.30 0.25~0.55 0.05 0.045 0.3 0.3 0.3 注:屈服强度不小于215MPa生产方案宽厚板生产方法一般可分为双机架轧制、单机架轧制与连轧三种,其布置形式可以分为单机架布置、双机架布置与多机架连续式布置。
①单机架轧制。
在一架轧机上完成宽厚板的轧制是指单机架布置生产。
此方式,粗轧与精轧都在一架轧机上完成,因此产品质量较差,规格受限,产量较差,投资小,适合对产品和质量要求不高的钢板。
②双机架轧制。
将粗轧和精轧分到两个轧机上分别完成,这种方式,产品质量较好,产量也较高。
粗轧机可选用二辊可逆式或四辊可逆式,精轧机一律选用四辊可逆式轧机。
目前在轧机布置上,四辊双机架布置是主要形式。
③连轧。
这种方式,宽度一般不大,对于较厚的中板,轧制中用不着抢温保温,在一般单、双机架可逆式轧机上轧制就可以满足质量要求,因此也不必采用连轧机生产。
一、坯料选择根据成品尺寸选择不同规格的原料,坯料选择应考虑:连铸坯规格、单重(倍尺轧制)、加热炉宽、轧机辊身长、轧制方法、压缩比、辊道及冷床长宽尺寸等。
成品重量:6.908吨,考虑单倍尺,成品8m长,成材率可达92%,坯料尺寸单倍尺200*1550*30854.1加热温度制定未了保证成品钢的质量,在轧制前加热是一项非常重要的环节。
对于加热炉要求能把原料加热到轧制钢材所需要的温度,并且要求均匀,燃料消耗最低,最少的烧损氧化,原料表面不被划伤,满足轧制道次确定及压下量分配两道横轧,之后纵轧到底宽展E.Sibel 公式横轧第一道次压下量50mm=19.56横轧第二道次=18.66纵轧第三道== 9.51纵轧第四道==12.25纵轧第五道== 10.23纵轧第六道= B C ∆=B C ∆=B C ∆=B C ∆=B C ∆=B C ∆=B C ∆==2.5纵轧第7道= =7.8道次 轧制方法 机架类型轧件尺寸/mm压下量/mm 厚宽 长 0 除鳞 除鳞箱 200 3085 1550 — 1 横轧 四辊 150 **** **** 50 2横轧四辊1103123278340轧件转90°开始纵轧3 纵轧 四辊 90 2792 3804 20 4 纵轧 四辊 70 2804 4870 205 纵轧 四辊 55 2815 6174 156 纵轧 四辊 50 2817 6789 5B C∆=4.2轧制速度制定速度制度的确定由于轧件较长且为了操作方便,采用梯形速度制度图,依据经验取平均加速度a=40r/(min·s),平均角减速度b=60r/(min·s),咬入时速度高些更有利轴承油膜的形成故可采用稳定速度咬入咬入、抛出速度采取第1,2道次,n=20r/min第3,4,5,6,7道次n=40r/min3 工艺流程。