热障涂层的制备及其失效的研究现状
热障涂层的研究进展

热障涂层的研究进展随着现代工业的发展,高温材料的应用越来越广泛,如航空发动机、燃气涡轮等。
然而,高温环境下的材料容易发生氧化、腐蚀等问题,降低了材料的使用寿命和可靠性。
为了解决这一问题,人们引入了热障涂层技术,使其在高温工作环境中具有更优异的性能。
热障涂层是一种在金属表面涂覆陶瓷材料的技术,通过降低热通量的方式实现保护材料的目的。
它的特性包括良好的隔热性、抗氧化性、抗腐蚀性、抗磨损性等,使其广泛应用于航空航天、石油、化工、冶金等行业。
近年来,研究人员对热障涂层的性能进行了深入的研究和探讨,取得了不俗的成果。
热障涂层材料的研究热障涂层材料的性能主要取决于表面涂层的结构和材料的选择。
目前,常见的热障涂层材料包括氧化铝、氧化锆、氧化镁、二氧化硅等,其中以氧化铝涂层应用最为广泛。
研究人员通过对涂层材料的组织结构、化学成分等方面的研究,不断优化和提升热障涂层的性能。
例如,一些研究人员通过改变涂层中氧化铝和氧化锆的组成比例,制备了一种新型热障涂层材料。
实验结果表明,该涂层具有更好的耐热性能和耐磨性能,可以有效地提升高温材料的使用寿命。
另外,一些研究人员通过改变热障涂层中陶瓷颗粒的尺寸、形状等参数,探讨了不同参数对涂层性能的影响。
研究结果发现,涂层颗粒尺寸越大,涂层的热阻值越大;而颗粒形状则会对涂层磨损、断裂等性能产生影响。
热障涂层加工技术的研究由于热障涂层是一种高技术含量的涂层技术,其加工过程也十分关键。
研究人员对热障涂层加工技术进行了系统研究,探讨不同加工方法对涂层性能的影响,并提出了相应的改进方案。
例如,一些研究人员对热障涂层的喷涂工艺进行了优化,采用了高速火焰喷涂技术,实现了高效、节能的喷涂过程,同时提高了涂层质量和性能。
另外,研究人员还在热障涂层加工过程中引入了纳米材料,提高了涂层的性能和稳定性。
纳米材料具有较高的比表面积和活性,可以增加涂层的强度、硬度和耐磨性。
热障涂层应用领域的研究热障涂层技术的应用领域越来越广泛,涉及到航空、航天、汽车、船舶、石油、化工、冶金等多个领域。
热障涂层的研究现状与发展方向

从正方相向单斜相转变 ,伴随 3 %~5 %的体积膨胀 ,导致涂层 破坏 ,为延长涂层的使用寿命 , ZrO2 中需加入稳定剂 。20 世纪 60 年代用 MgO 和 CaO 作为稳定剂 ,后来发现以这两种氧化物 作为稳定剂的涂层组织稳定性不好 ,燃气的硫化作用使 MgO 和 CaO 从涂层中析出 ,降低了对 ZrO2 相的稳定作用 ,使涂层的 热循 环 寿 命 降 低 , 目 前 这 两 种 稳 定 剂 已 基 本 被 Y2 O3 所 替 代[6 ,7] 。Stecura 等对不同 Y2 O3 含量稳定的 ZrO2 陶瓷涂层的 热物性能进行了分析 ,结果表明在 Y2 O3 含量为 6 %~8 %时[8] , 陶瓷涂层抗热循环性能最好 ,寿命最长 。
据报道 ,目前美国几乎所有的陆用和船用燃气轮机都采用 了 TBCs ,每年约有 300t 氧化锆材料用在 TBCs 上 ,在未来 10 年中 TBCs 将达到 12 %的年增长率 ,其中在发动机部件中的年 增长率将达到 25 %[2] ,具有广阔的应用开发前景 。近年来 ,随 着航空燃气涡轮机向高流量比 、高推重比 、高进口温度方向发 展 ,燃烧室中的燃气温度和压力也不断提高 。目前 ,燃气温度已 接近 2000 K ,因此航空发动机涡轮叶片的合金材料上需喷涂热 障涂层以承受 1600 ℃以上的涡轮进口温度[4] 。实际应用的热 障涂层大多采用由陶瓷隔热表层和金属粘结底层组成的双层结 构 ,6 %~8 %氧化钇稳定的氧化锆 ( YSZ) 是目前使用最广泛的 陶瓷隔热表层材料 ,金属粘结底层主要为 MCrAl Y 合金 ,其中 M 代表 Ni 、Co 或 NiCo [5] 。由于 YSZ 热障涂层的长期使用温度 为 1200 ℃,超过 1200 ℃,相变加剧 ,易烧结 ,氧传导率高 ,过渡金 属易被氧化 ,导致涂层失效 ,已难以满足涡轮进口温度进一步提 高的需要 。
热障涂层的研究现状与发展方向
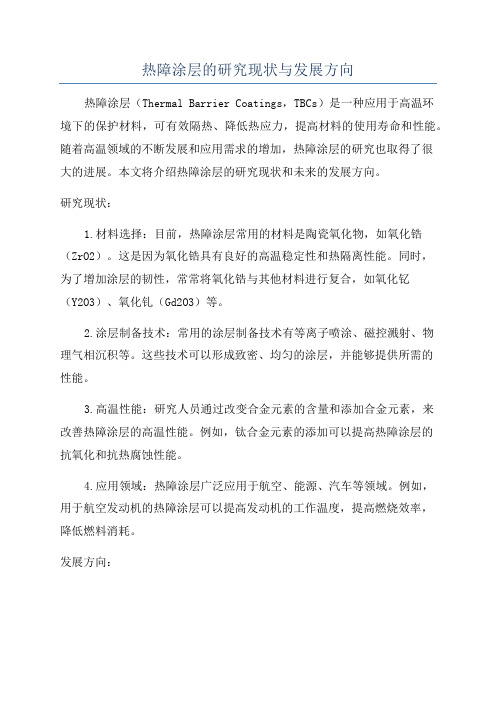
热障涂层的研究现状与发展方向热障涂层(Thermal Barrier Coatings,TBCs)是一种应用于高温环境下的保护材料,可有效隔热、降低热应力,提高材料的使用寿命和性能。
随着高温领域的不断发展和应用需求的增加,热障涂层的研究也取得了很大的进展。
本文将介绍热障涂层的研究现状和未来的发展方向。
研究现状:1.材料选择:目前,热障涂层常用的材料是陶瓷氧化物,如氧化锆(ZrO2)。
这是因为氧化锆具有良好的高温稳定性和热隔离性能。
同时,为了增加涂层的韧性,常常将氧化锆与其他材料进行复合,如氧化钇(Y2O3)、氧化钆(Gd2O3)等。
2.涂层制备技术:常用的涂层制备技术有等离子喷涂、磁控溅射、物理气相沉积等。
这些技术可以形成致密、均匀的涂层,并能够提供所需的性能。
3.高温性能:研究人员通过改变合金元素的含量和添加合金元素,来改善热障涂层的高温性能。
例如,钛合金元素的添加可以提高热障涂层的抗氧化和抗热腐蚀性能。
4.应用领域:热障涂层广泛应用于航空、能源、汽车等领域。
例如,用于航空发动机的热障涂层可以提高发动机的工作温度,提高燃烧效率,降低燃料消耗。
发展方向:1.纳米材料研究:纳米材料具有较高的比表面积和界面效应,可以提高热障涂层的热导率和热膨胀系数匹配性。
因此,研究者们正在探索利用纳米材料制备热障涂层,并研究其热性能。
2.多层涂层研究:多层热障涂层可以提供更好的隔热性能和更高的耐热性。
目前,研究人员正在研究不同层次和组分的多层涂层结构,以提高涂层的性能。
3.高温腐蚀性能研究:热障涂层在高温腐蚀环境中容易受损。
因此,研究者们正在研究改善热障涂层的高温腐蚀性能,以提高其使用寿命。
4.综合性能优化:除了热性能,热障涂层的机械性能、热膨胀系数匹配性、附着强度等都是重要的指标。
因此,未来的研究将更加注重综合性能的优化,以提高热障涂层的整体性能和可靠性。
总结:热障涂层作为一种重要的保护材料,在高温环境下担负着隔热和降低热应力的任务。
热障涂层的研究现状与进展

均 由结 合底 层材 料 和 陶 瓷 表层 材 料 组成 , 且各 层 中
这 2种 材料 的组 成 比呈 梯度 变 化 , 种 梯 度 变化 的 这 涂 层 结构 可使金 属基 体 到陶瓷 工作 层 的热膨胀 系数 逐 渐 变化 。受热 时基 体 与工作 层 间的温 度梯度将 减 小 , 而提 高 了涂层 的抗 热震性 能 。许 多研究 表 明 : 从 采 用梯 度 T B 设计 , 有效提 高涂 层 抗热 震性 能 , C s 能
件 可显 著提 高使 用温度 , 延长使 用寿命 , 高发 动 机 的效 率 。综述 了热 障涂层 的涂 层设 计 方 法 , 别 比较 提 分 了等 离子 喷涂 、 激光 重熔 、 电子 束物 理 气相 沉 积 、 自蔓 延 高温 合 成 等 方法 制备 热 障涂 层 的特 点 , 分析 了涂
TB s的基 本 构 想 是 利 用 陶 瓷 材 料 具 有 高 熔 C 点 、 导热率 的特性 , 此类 材料 以不 同的方 式涂 覆 低 将 于基体 金属 或其 它材 料 的 表 面 上 , 可形 成 一 个 热 就
的屏 障层 。 目前 , C TB s根 据 不 同要 求 可设 计 成 双
维普资讯
热 障 涂层 的研 究现 状 与进展
刘 海 浪 , 宝健 , 永 丹 , 丰 王 刘 闫
( 西 理 工 大 学 材 料 与化 学工 程 学 院 , 西 赣 州 3 1 0 ) 江 江 4 0 0
摘 要 : 热障涂层 一般 由金 属黏 结层 和具 有 低 热 导率 的 陶 瓷顶 层 组 成 , 用 于 涡轮 发 动机 的热 端 部 应
隔热性好 的 陶瓷热保 护 功能层 组成 的“ 合 型” 属 层 金 陶瓷复合 涂层 系统_ 。 主要 用来 降低 基体 的工 作 温 2 ] 度, 免受 高温 氧化 、 蚀 、 腐 磨损 。
热障涂层的研究现状与发展趋势
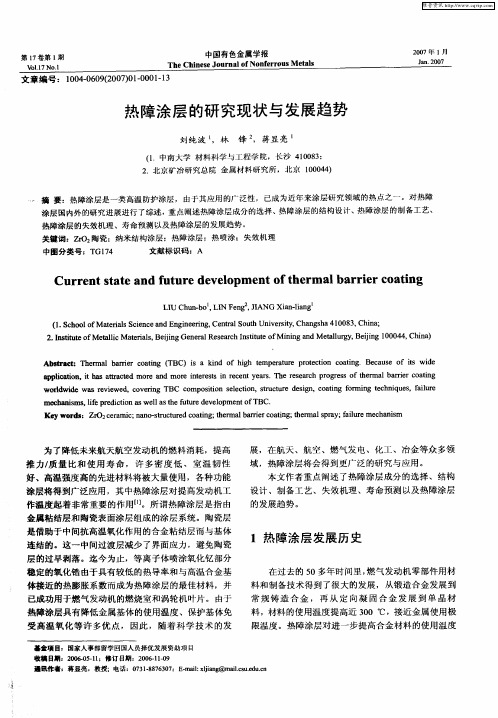
2 Is tt o Me lc t asB in e eaR sac s tt o MiigadMe l ry B in o 0 4 C ia . tue f t l e l e igG n rl eerhI tue f nn t l g , e igl0 4 , hn) ni a i Ma r , j i ni n au j
( . c o l f tr l S in ea dEn ie rn , nrl o t ie s y Ch n s a41 0 3 Chn ; 1 S h o e as ce c n gn e g Ce ta uhUnv ri , a g h 8 , ia o Ma i i S t 0
me h n s , i r d c i n a l a h t r e e o me t f C. cai ms l e p e it s f o we l s e f u ed v lp n TB t u o Ke r  ̄ Zr e a c n o sI c L l o t g t e a a re o t g t e a p a ; a lr c a im y wo d : 02 r mi ; a -t t r d c a i ; r l rirc a i ; r l r y f i eme h s c n u l e n h m b n h m s u n
wo l wi e Wa e iwe ,c v r g TBC o o i o e e t n tu t r e in o t g f r ig tc n q e ,f i r rd d S r v e d o e i n c mp s i n s l ci ,sr c u e d sg ,c ai o t o n m n eh iu s al e u
热障涂层材料Mg2SiO4的制备与性能研究
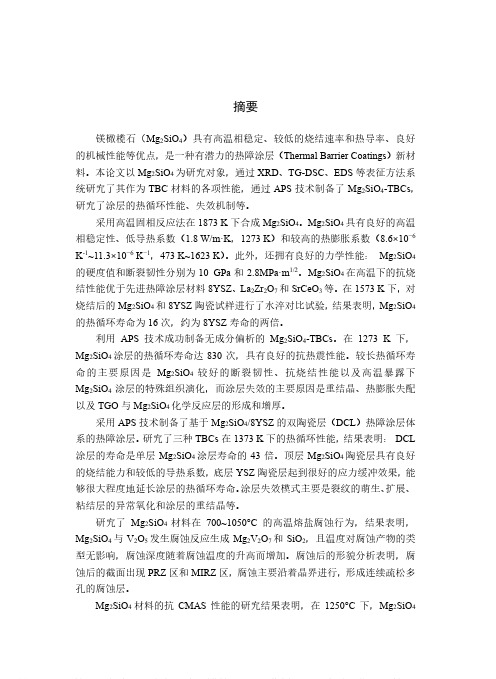
摘要镁橄榄石(Mg2SiO4)具有高温相稳定、较低的烧结速率和热导率、良好的机械性能等优点,是一种有潜力的热障涂层(Thermal Barrier Coatings)新材料。
本论文以Mg2SiO4为研究对象,通过XRD、TG-DSC、EDS等表征方法系统研究了其作为TBC材料的各项性能,通过APS技术制备了Mg2SiO4-TBCs,研究了涂层的热循环性能、失效机制等。
采用高温固相反应法在1873 K下合成Mg2SiO4。
Mg2SiO4具有良好的高温相稳定性、低导热系数(1.8 W/m·K,1273 K)和较高的热膨胀系数(8.6×10−6 K-1~11.3×10−6 K−1,473 K~1623 K)。
此外,还拥有良好的力学性能:Mg2SiO4的硬度值和断裂韧性分别为10 GPa和2.8MPa·m1/2。
Mg2SiO4在高温下的抗烧结性能优于先进热障涂层材料8YSZ、La2Zr2O7和SrCeO3等。
在1573 K下,对烧结后的Mg2SiO4和8YSZ陶瓷试样进行了水淬对比试验,结果表明,Mg2SiO4的热循环寿命为16次,约为8YSZ寿命的两倍。
利用APS技术成功制备无成分偏析的Mg2SiO4-TBCs。
在1273 K下,Mg2SiO4涂层的热循环寿命达830次,具有良好的抗热震性能。
较长热循环寿命的主要原因是Mg2SiO4较好的断裂韧性、抗烧结性能以及高温暴露下Mg2SiO4涂层的特殊组织演化,而涂层失效的主要原因是重结晶、热膨胀失配以及TGO与Mg2SiO4化学反应层的形成和增厚。
采用APS技术制备了基于Mg2SiO4/8YSZ的双陶瓷层(DCL)热障涂层体系的热障涂层。
研究了三种TBCs在1373 K下的热循环性能,结果表明:DCL 涂层的寿命是单层Mg2SiO4涂层寿命的43倍。
顶层Mg2SiO4陶瓷层具有良好的烧结能力和较低的导热系数,底层YSZ陶瓷层起到很好的应力缓冲效果,能够很大程度地延长涂层的热循环寿命。
热障涂层性能检测技术发展现状
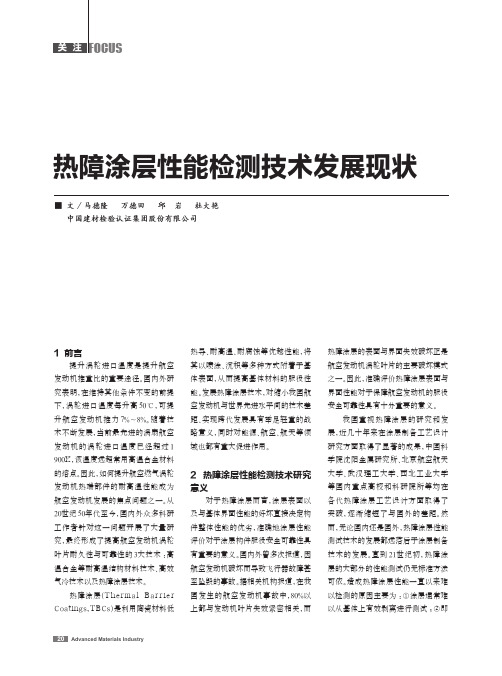
热障涂层性能检测技术发展现状■ 文/马德隆 万德田 邱 岩 杜大艳 中国建材检验认证集团股份有限公司1 前言提升涡轮进口温度是提升航空发动机推重比的重要途径。
国内外研究表明,在维持其他条件不变的前提下,涡轮进口温度每升高50℃,可提升航空发动机推力7%~8%。
随着技术不断发展,当前最先进的涡扇航空发动机的涡轮进口温度已经超过1 900K,该温度远超常用高温合金材料的熔点。
因此,如何提升航空燃气涡轮发动机热端部件的耐高温性能成为航空发动机发展的焦点问题之一。
从20世纪50年代至今,国内外众多科研工作者针对这一问题开展了大量研究,最终形成了提高航空发动机涡轮叶片耐久性与可靠性的3大技术:高温合金等耐高温结构材料技术、高效气冷技术以及热障涂层技术。
热障涂层(T h e r m a l B a r r i e r Coatings,TBCs)是利用陶瓷材料低热导、耐高温、耐腐蚀等优越性能,将其以喷涂、沉积等多种方式附着于基体表面,从而提高基体材料的服役性能。
发展热障涂层技术,对缩小我国航空发动机与世界先进水平间的技术差距、实现跨代发展具有举足轻重的战略意义,同时对能源、航空、航天等领域也都有重大促进作用。
2 热障涂层性能检测技术研究意义对于热障涂层而言,涂层表面以及与基体界面性能的好坏直接决定构件整体性能的优劣,准确地涂层性能评价对于涂层构件服役安全可靠性具有重要的意义。
国内外曾多次报道,因航空发动机破坏而导致飞行器故障甚至坠毁的事故。
据相关机构报道,在我国发生的航空发动机事故中,80%以上都与发动机叶片失效紧密相关,而热障涂层的表面与界面失效破坏正是航空发动机涡轮叶片的主要破坏模式之一。
因此,准确评价热障涂层表面与界面性能对于保障航空发动机的服役安全可靠性具有十分重要的意义。
我国重视热障涂层的研究和发展,近几十年来在涂层制备工艺设计研究方面取得了显著的成果,中国科学院沈阳金属研究所、北京航空航天大学、武汉理工大学、西北工业大学等国内重点高校和科研院所等均在各代热障涂层工艺设计方面取得了突破,逐渐缩短了与国外的差距。
航空发动机涡轮叶片热障涂层研究现状

航空发动机涡轮叶片热障涂层研究现状一、引言航空发动机是现代航空器的重要组成部分,其性能直接影响到飞机的安全和经济性。
涡轮叶片作为航空发动机的重要组件之一,承受着高温和高速气流的冲击,对其表面进行热障涂层的研究成为了发展的热点之一。
本文将综述航空发动机涡轮叶片热障涂层的研究现状,并对未来的研究方向进行展望。
二、背景在航空发动机中,高温气流是涡轮叶片面临的主要问题之一。
高温气流的冲击会导致涡轮叶片的热膨胀、氧化和烧蚀等问题,进而降低了发动机的性能和寿命。
为了解决这一问题,研究人员提出了热障涂层的概念。
三、热障涂层的种类热障涂层可以分为传统热障涂层和新型热障涂层两大类。
1. 传统热障涂层传统热障涂层主要包括YSZ (Yttria Stabilized Zirconia) 和 GCO (Gadolinium Cerium Oxide) 等。
YSZ涂层被广泛应用于航空发动机中,具有优异的热障效果和氧化屏障性能。
GCO涂层相比于YSZ涂层,具有更好的机械和热损伤修复能力,但研究相对较少。
2. 新型热障涂层新型热障涂层主要包括二氧化铝涂层、钨合金涂层等。
经过改良的二氧化铝涂层具有更好的耐腐蚀性能和较低的热导率,但是其热障效果相对较差。
钨合金涂层则具有更好的高温性能和耐烧蚀能力,但是涂层的结构和制备工艺仍面临挑战。
四、热障涂层的制备工艺热障涂层的制备工艺对涂层性能的影响至关重要。
目前,常见的热障涂层制备工艺包括物理气相沉积(Physical Vapor Deposition,PVD)、化学气相沉积(Chemical Vapor Deposition,CVD)和高速火焰喷涂(High VelocityOxygen/Fuel,HVOF)等。
1. PVDPVD技术通过物理手段将材料从固态直接转变为气态,然后沉积到基底上。
PVD制备的热障涂层具有致密的结构、低孔隙率和较高的结合强度,但是制备成本较高。
2. CVDCVD技术是利用化学反应将气态前驱体沉积在基底上,形成热障涂层。
- 1、下载文档前请自行甄别文档内容的完整性,平台不提供额外的编辑、内容补充、找答案等附加服务。
- 2、"仅部分预览"的文档,不可在线预览部分如存在完整性等问题,可反馈申请退款(可完整预览的文档不适用该条件!)。
- 3、如文档侵犯您的权益,请联系客服反馈,我们会尽快为您处理(人工客服工作时间:9:00-18:30)。
收稿日期:2009206201; 修订日期:2009206225作者简介:邢亚哲(19762 ),陕西岐山人,讲师,博士.研究方向:材料表面强化及器件制造.Email:x ingyazhe@gm 热障涂层的制备及其失效的研究现状邢亚哲,郝建民(长安大学材料科学与工程学院,陕西西安710064)摘要:热障涂层作为航空发动机和燃气轮机高温部件的保护涂层,其抗高温失效能力直接决定了部件的工作效率和寿命。
回顾热障涂层的发展历史及研究现状,着重介绍了热障涂层的主要制备方法及其相应涂层的结构特征,综述了各类热障涂层失效的影响因素和失效机理。
关键词:热障涂层;电子束物理气相沉积;等离子喷涂;失效机理中图分类号:TG174.44 文献标识码:A 文章编号:100028365(2009)0720922204Re se a rc h Stat us in Fa bric at ion and Fa ilure of The rmal Barrie r Co atingsXING Ya 2zhe,HAO Jian 2min(School of Mater ials Science and Engineering,Chang p an University,Xi p an 710064,China)Abst ract:Thermal barrier coatings are widely used to protect the components in aircraft and industrial gas 2turbine engines against high temperature damage.The e ne rgy efficiency and lifetime of these components are mainly dominated by the failure resistance of thermal barrier coatings in the high te mperature atmosphere.In this paper,the development and research status of thermal barrie r coatings are reviewe d.Especially,the main fabricating methods and the microstructure fe ature of the coatings,as well as the factors re sulting in the failure of thermal barrier coatings and its failure mechanisms,are summarized in detail.K e y words:Thermal barrier coatings;Electron beam physical vapor deposition;Plasma Spraying;Fa ilure mechanism随着现代工业的发展,数以百计种类型的涂层被用在各种结构材料表面,以使这些材料表面免受腐蚀、磨损、侵蚀和高温氧化等危害。
热障涂层(T BCs:Thermal Barrier Coatings)就是其中的一种,其具有最复杂的结构且工作在高温环境下,常作为航空发动机和燃气轮机受高温零件的保护涂层,以提高设备的工作温度和效能,同时减少温室气体的排放量。
典型的TBCs 在结构上包含四个部分[1]:¹基体,即被保护的零件;º金属结合层(BC:Bond Coat),通常为高温合金MCrA lY(M 代表Ni 、Co 或NiCo 合金);»热生长氧化物层(T GO:Thermally Grown Oxide),TGO 是在高温条件下外部氧通过T C 层到达BC 层表面并使其氧化而形成的,通常为一致密的Al 2O 3薄膜,在随后的工作过程中能够阻止外部氧向BC 层内部和基体的扩散,起到保护基体(零件)的作用;¼陶瓷顶层(TC:Top Coat),一般为6%~8%Y 2O 32Zr O 2(YSZ),正是由于YSZ 低的热传导率和相对较高的热膨胀系数,使其具有优越的热障和耐热冲击性能。
目前,TBCs 研究的难点和重点主要为对其失效的控制[1~4]。
为此,对TBCs 微观结构的研究显得尤为重要。
而作为控制其微观结构的主要因素,即TBCs 的制备工艺就成了国内外学者们关注的热点。
1 基于制备工艺的T BCs 的发展历程早期在航空航天发动机中应用的TBCs(又称第一代T BCs),其BC 层和TC 层均采用大气等离子喷涂(APS:Atmospheric Plasma Spr aying)制备。
对于APS BC 层,涂层含氧量较高,特别是有一定量的氧化镍生成,而氧化镍的存在致使难以形成在高温下具有保护性能的致密TGO 氧化膜,BC 层使用过程中容易在其内部也发生显著氧化而使层内结合弱化,裂纹易在BC 层内扩展而造成涂层剥落失效,使得该类T BCs 寿命较低。
随着低压(又称真空)等离子喷涂(LPPS:Low Pressur e Plasma Spraying)技术的进步和发展,逐步采用VPS 制备BC 层,避免了喷涂过程中高温合金BC 层的氧化,并通过热扩散处理,从根本上强化了BC5铸造技术607/2009邢亚哲等:热障涂层的制备及其失效的研究现状层内结合,消除了BC层内的失效。
结合层的强化使涂层的失效从BC层内开裂转变到TGO与APS YSZ 涂层的界面附近的YSZ层内脱落。
这种失效机理的转变伴随着TBCs的使用性能与寿命的大幅度提高[5],这类T BCs称为第二代T BCs。
随着T BCs的不断发展,发现采用电子束物理气相沉积(EB2PVD:Electron Beam Physical Vapor Dep2 osition)技术制备YSZ TC层(又称第三代TBCs),涂层结构呈现从界面生长的连续柱状晶,如图1所示。
研究表明,这类TBCs涂层失效方式转变为由BC层表面高温下增厚的TGO引起,开裂发生在TGO与BC层界面、或T GO内、或YSZ与T GO界面[7~9]。
图1EB2P VD热障涂层的断面组织[6]Fig.1Micr ograph of the EB2PVD coating in cross2section[6]2T BCs的制备工艺2.1TC层制备工艺目前常用于制备TC层的主要工艺为等离子喷涂和电子束物理气相沉积[1],这也可以从前面TBCs的发展历程看出。
APS YSZ之所以广泛用于航空发动机、燃气轮机发动机的热障涂层,首先取决于等离子喷涂方法具有可以灵活地在任意形状表面制备陶瓷涂层的这一特点,其次,由于等离子喷涂陶瓷涂层的粒子层间结合有限且单个粒子中分布着网状微裂纹[10],致使陶瓷涂层的表观弹性模量低,呈现较好的缓和热应变的能力,加上YSZ具有相对较高的热膨胀系数,从而使等离子喷涂呈现良好的高抗热震性能,表现为在反复热循环工作条件下具有较长的使用寿命。
再次,构成涂层的扁平粒子之间大量的未结合界面,进一步降低了YSZ涂层的热传导率,显著提高隔热热障效果。
与APS YSZ涂层相比,正是由于EB2PVD YSZ 层与界面垂直的连续柱状晶的结构特征(图1),不仅消除了APS YSZ涂层中粒子层间的弱结合,而且通过连续生长的柱状晶强化了YSZ涂层在与界面垂直方向上的断裂韧性,使得YSZ的抗开裂能力显著提高。
对于EB2PVD YSZ,YSZ涂层的柱状晶粒之间存在空隙、结合较弱,这种结构具有良好的热应变缓和能力,这也是提高EB2PVD热障涂层寿命的一个主要方面。
然而,EB2PVD涂层的热传导率高,隔热效果不如等离子喷涂层。
研究发现[11],可以通过调整基体方向获得低热导率的EB2PVD YSZ层。
另外,涂层寿命受表面形貌的影响显著[12,13],致使涂层寿命数据分散较大,甚至长短相差高达10倍[13]。
2.2BC层制备工艺目前常用于制备MCrAlY BC层的工艺有LPPS、EB2PVD和超音速火焰喷涂(H VOF:H igh Velocity Oxy2fuel)等。
由于孔洞、氧化物夹杂和裂纹都是氧的快速扩散通道,降低了涂层抗高温氧化和高温腐蚀性能。
因此,低孔隙率和低含氧量的MCrA lY BC层通常具有良好的抗高温氧化和热腐蚀性能。
当涂层中氧化物含量较高时,说明涂层中有限的Al在喷涂过程中就会被消耗掉一部分而可能造成MCrAlY涂层中贫Al,导致在高温氧化过程中形成多孔的含Cr和Co 的尖晶石氧化物、Y3Al5O12和Y2O3等氧化物[9,14],这些氧化物相的形成不利于T GO的完整性,并通过提供氧的快速通道而加速涂层的局部氧化。
LPPS工艺由于生产效率高、涂层厚度可调范围大、与基体的结合较好且致密,同时具有较低的孔隙率,现已成为MCrAlY涂层的主要制备方法。
但是,相对于其它涂层制备技术而言,LPPS制备涂层所需成本较高[2,9,15]。
相比热喷涂技术,EB2PVD的缺点是设备复杂,沉积速度低,不容易沉积大面积试样,涂层成分严重地受各元素蒸气压的影响而不易控制[15]。
对于H VOF制备的MCrA lY涂层,因H VOF具有粉末颗粒沉积速度高的优点,涂层密度,结合强度、硬度和耐磨性均优于PS MCrAlY涂层,然而喷涂过程是在高氧环境气氛中进行,由于Al和Y与氧具有较高的亲和性,因此在喷涂过程中不可避免地会产生氧化[16]。
研究表明[17],H VOF的工艺参数均影响涂层中氧化物含量,其中喷涂距离、氧燃比和送粉率的影响最为显著。
进一步研究表明[18],H VOF MCrAlY 涂层中的氧化物含量随着喷涂粉末粒径的减小而升高。
Tang等人[19]的研究发现氧化物的含量越低,越有利于A2A l2O3保护性氧化膜的生成,因其低的氧离子扩散率和强的附着能力[2],该成分的致密T GO膜才可以起到明显的抗氧化失效的作用。
3T BCs失效的影响因素及其失效机理服役中的T BCs系统的主要失效方式是涂层的剥落,失效过程是微裂纹的产生、扩展、联接和大裂纹增殖的过程,当大裂纹继续扩展联接后,将引起陶瓷涂层#923#出现边缘剥离(Edge Delamination)或鼓泡剥离(Buckle Delamination)[2,9],最终导致涂层失效。
热障涂层剥落的主要原因是其服役过程中产生的应力[9,23,24]:由温度梯度引起的热应力,热膨胀不匹配引起的热应力,T GO的热生长应力及相变应力。
温度梯度与热膨胀不匹配是热障涂层体系在其应用中必然存在的现象。