剪板机的结构设计
剪板机的设计
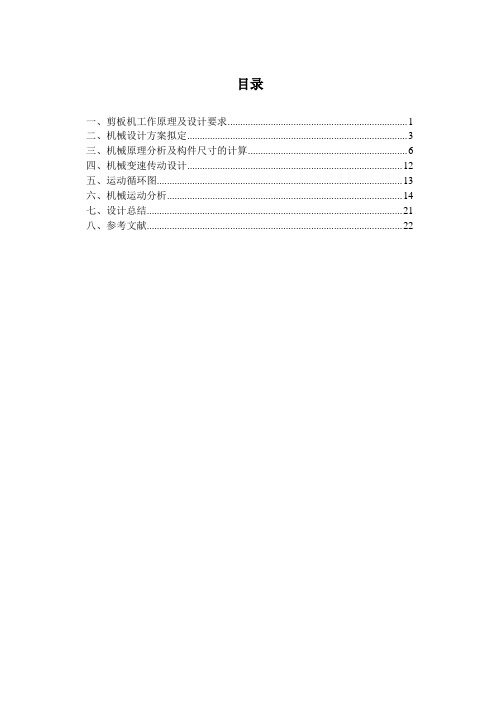
目录一、剪板机工作原理及设计要求 (1)二、机械设计方案拟定 (3)三、机械原理分析及构件尺寸的计算 (6)四、机械变速传动设计 (12)五、运动循环图 (13)六、机械运动分析 (14)七、设计总结 (21)八、参考文献 (22)一、剪板机工作原理及设计要求1.工作原理及工艺过程本剪板机是将卷料展开并剪成一定长度铁板的机器,即将板料作定长度的间歇送进,在板料短暂的停歇时间内,剪刀在一定位置上将铁板剪断,其工艺过程由输送原材料和剪板两个过程来完成。
2.原始数据及设计要求原材料为成卷的板料。
每次输送铁板长度L=1900或2000或2200mm (设计时任选一种)。
(1)每次输送铁板到达规定长度后,铁板稍停,以待剪板机构将其剪断。
剪断工艺所需时间约为铁板输送周期的十五分之一。
建议铁板停歇时间不超过剪断工艺时间的1.5倍,以保证有较高的生产率。
(2)输送机构运转应平稳,振动和冲击应尽量小(即要求输送机构从动件的加速度曲线连续无突变)。
3.机械系统功能分析剪板机要实现将卷料展开并剪成一定长度铁板,采用两个相互配合的间歇机构来实现停歇与剪板。
利用附加曲柄摇杆机构实现连续转动。
利用两个滚轮将铁板压紧,依靠滚轮和铁板间的摩擦力将铁板从卷料上拉出并推向前进的输送方式。
原理分析如下:在主动曲柄AB(齿轮1)等速转动,系杆H变速运动的一周内,齿轮4在某一时间内总能使其角速度为零。
在主动曲柄AB(齿轮1)等速转动一周的时间内,从动齿轮4按下述规律运动:当曲柄开始转过某一角度时间内时,齿轮4停歇不动,以等待剪切机构将铁板剪断;在主动曲柄转过一周中其余角度时,输出构件4转过另一角度,这时刚好将铁板输送到所要求的长度L。
原理图如下:二、机械设计方案拟定1.输送机构方案的比较和拟定方案一:不完全齿轮机构利用不完全齿轮实现间歇输送板料在主动轮上作出一部分的轮齿,根据运动时间与停歇时间的要求,在从动轮上做出与主动轮相齿和的轮齿,当主动轮做连续回转运动时从动轮做间歇回转运动。
机械式剪板机设计

机械式剪板机设计机械式剪板机是一种常用于金属板材切割的机械设备,它通过剪切动作将板材切成所需的尺寸和形状。
机械式剪板机通常由机架、上刀座、刀座传动机构、下刀座、剪切刀、刀冲床、后挡料槽、后挡料刀、液压传动系统等组成。
机架是整个剪板机的支撑结构,要具有足够的刚性和稳定性,以保证剪切过程中的安全和准确性。
上刀座和下刀座分别安装在机架的上部和下部,通过传动机构连接,实现剪刀的开合运动。
传动机构可以采用液压、机械或电动等方式,具体选用哪种传动方式,需要根据切割材料的性质和切割要求来确定。
剪切刀是机械式剪板机的核心部件,它通常由多片刀片组成,刀片之间安装在刀冲床上,通过剪刀的开合运动将切割材料剪断。
在设计上,刀片的选材和硬度应根据所需切割材料的硬度和厚度来决定,以保证切割质量和刀片的寿命。
后挡料槽和后挡料刀用于固定和定位切割材料,以保证切割精度和重复定位精度。
后挡料槽通常由一块细密钢板制成,与下刀座配合使用,后挡料刀则由多片刀片组成,固定在机架的底部,通过调节刀片的位置来实现切割宽度的调整。
在机械式剪板机的设计和制造过程中,还需要考虑一些其他因素,如切割速度、切割厚度范围、切割精度等。
切割速度应根据切割材料的性质和厚度来确定,过高的切割速度可能导致刀具磨损加剧,切割精度下降;切割厚度范围应根据用户需求来确定,过大的切割厚度范围可能导致刀具负荷过大,降低切割质量;切割精度则需要通过适当的调节和控制来实现,可采用自动化控制系统来提高精度。
机械式剪板机设计的目标是实现高效、安全、稳定和可靠的切割过程,提高生产效率和产品质量。
设计者需要综合考虑材料的性质、切割要求、机械精度、设备成本等因素,选取合适的材料、传动方式、液压系统等,以满足用户的需求。
同时,还需要对设备进行结构强度和稳定性的验证,以确保设备在长期运行中的可靠性和安全性。
综上所述,机械式剪板机设计需要综合考虑材料的性质、切割要求和设备成本等因素,选择适合的机械结构、动力传动方式和液压系统,以实现高效、安全、稳定和可靠的切割过程。
小型剪板机设计范文
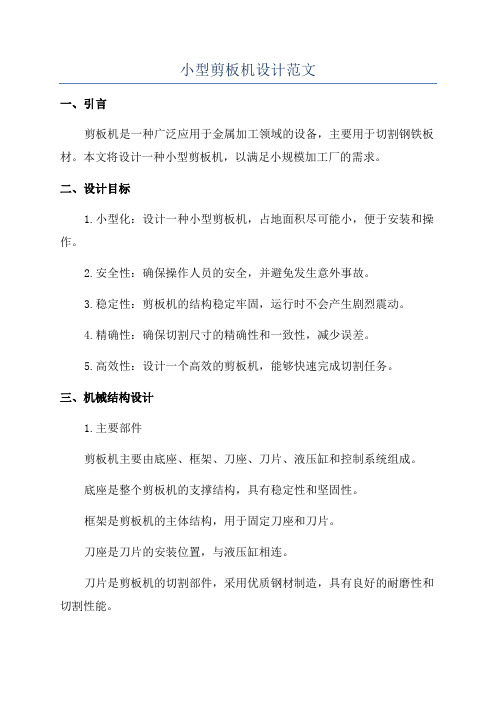
小型剪板机设计范文一、引言剪板机是一种广泛应用于金属加工领域的设备,主要用于切割钢铁板材。
本文将设计一种小型剪板机,以满足小规模加工厂的需求。
二、设计目标1.小型化:设计一种小型剪板机,占地面积尽可能小,便于安装和操作。
2.安全性:确保操作人员的安全,并避免发生意外事故。
3.稳定性:剪板机的结构稳定牢固,运行时不会产生剧烈震动。
4.精确性:确保切割尺寸的精确性和一致性,减少误差。
5.高效性:设计一个高效的剪板机,能够快速完成切割任务。
三、机械结构设计1.主要部件剪板机主要由底座、框架、刀座、刀片、液压缸和控制系统组成。
底座是整个剪板机的支撑结构,具有稳定性和坚固性。
框架是剪板机的主体结构,用于固定刀座和刀片。
刀座是刀片的安装位置,与液压缸相连。
刀片是剪板机的切割部件,采用优质钢材制造,具有良好的耐磨性和切割性能。
控制系统用于控制剪板机的运行,包括启动、运行、停止等指令。
2.工作原理剪板机的工作原理是通过液压缸施加一定的压力使刀片来回运动,切割金属板材。
操作人员根据需要调整刀片的位置和切割力度,通过控制系统启动液压缸使刀片运动,完成切割任务。
四、性能要求1. 最大切割厚度:设计剪板机的最大切割厚度为6mm。
2. 最大切割宽度:设计剪板机的最大切割宽度为1500mm。
3. 切割精度:设计剪板机的切割精度为±0.5mm。
4.刀片材质:采用优质高速钢材制造刀片,具有良好的耐磨性和切割性能。
5.液压系统:选择性能稳定可靠的液压系统,确保提供足够的切割力。
五、安全措施1.剪板机采用完全封闭的结构,防止刀片和其他零部件对操作人员造成伤害。
2.在刀片和液压缸周围设置安全护栏,防止操作人员误碰。
3.设定严格的运行规程,操作人员必须经过专门培训,并佩戴安全防护设备。
4.在程序控制系统中设置断电自锁装置,一旦出现故障,剪板机会自动停止工作。
5.定期对剪板机进行维护和检查,确保各部件的正常运行。
六、总结本文设计了一种小型剪板机,以满足小规模加工厂的需求。
自动剪板机毕业设计

自动剪板机毕业设计
**一、前言**
自动剪板机是一种用于金属板材裁剪的自动化设备,广泛应用于钢铁、汽车、机械制造等行业。
本次毕业设计旨在设计一种高效、精确、安全的自动剪板机,以满足现代工业生产的需求。
**二、设计要求**
1. 板材厚度范围:1-10mm。
2. 板材裁剪长度:500-3000mm。
3. 裁剪精度:±0.2mm。
4. 生产效率:每分钟裁剪 10 次以上。
5. 安全性能:具备防护装置,保证操作人员安全。
**三、设计方案**
1. 机械结构设计:采用龙门式结构,由机身、工作台、剪刀机构、压料装置、输送装置等组成。
2. 控制系统设计:采用 PLC 作为控制核心,实现板材的自动送料、裁剪、计数等功能。
3. 传动系统设计:采用液压传动系统,实现剪刀的上下运动和压料装置的压紧松开。
4. 安全防护设计:设置防护栏、光电传感器等安全装置,确保操作人员的安全。
**四、关键部件设计**
1. 剪刀机构:采用液压驱动,剪刀刀片选用优质合金钢,保证裁剪精度和使用寿命。
2. 压料装置:采用液压驱动,压紧力可调节,确保板材在裁剪过程中不移动。
3. 输送装置:采用链条输送,输送速度可调节,保证板材的平稳输送。
**五、总结**
本设计方案充分考虑了自动剪板机的功能需求和安全性,采用了先进的控制和传动技术,具有结构紧凑、操作方便、效率高等优点。
通过本次毕业设计,我对机械设计和自动化控制有了更深入的了解,为今后的工作和学习打下了坚实的基础。
钢板剪板机的原理与设计
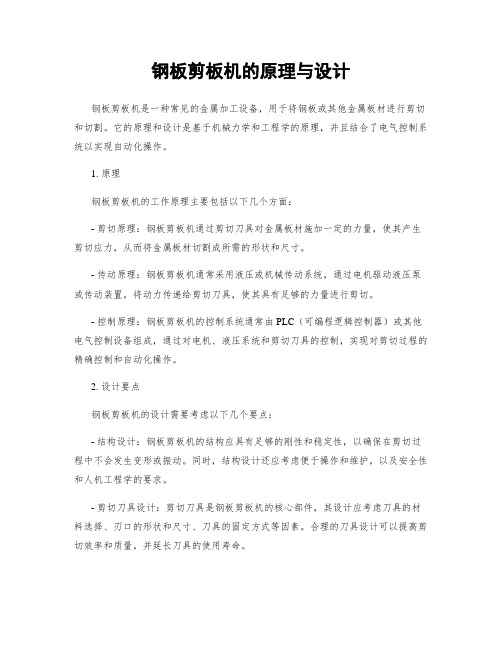
钢板剪板机的原理与设计钢板剪板机是一种常见的金属加工设备,用于将钢板或其他金属板材进行剪切和切割。
它的原理和设计是基于机械力学和工程学的原理,并且结合了电气控制系统以实现自动化操作。
1. 原理钢板剪板机的工作原理主要包括以下几个方面:- 剪切原理:钢板剪板机通过剪切刀具对金属板材施加一定的力量,使其产生剪切应力,从而将金属板材切割成所需的形状和尺寸。
- 传动原理:钢板剪板机通常采用液压或机械传动系统,通过电机驱动液压泵或传动装置,将动力传递给剪切刀具,使其具有足够的力量进行剪切。
- 控制原理:钢板剪板机的控制系统通常由PLC(可编程逻辑控制器)或其他电气控制设备组成,通过对电机、液压系统和剪切刀具的控制,实现对剪切过程的精确控制和自动化操作。
2. 设计要点钢板剪板机的设计需要考虑以下几个要点:- 结构设计:钢板剪板机的结构应具有足够的刚性和稳定性,以确保在剪切过程中不会发生变形或振动。
同时,结构设计还应考虑便于操作和维护,以及安全性和人机工程学的要求。
- 剪切刀具设计:剪切刀具是钢板剪板机的核心部件,其设计应考虑刀具的材料选择、刃口的形状和尺寸、刀具的固定方式等因素。
合理的刀具设计可以提高剪切效率和质量,并延长刀具的使用寿命。
- 传动系统设计:传动系统的设计应考虑传动效率、传动比例和传动精度等因素。
液压传动系统通常具有较大的输出力和可调节性,适用于对大尺寸和高强度钢板进行剪切。
机械传动系统则通常适用于对小尺寸和低强度钢板进行剪切。
- 控制系统设计:控制系统的设计应考虑操作的便捷性、控制的精确性和可靠性。
PLC控制系统通常具有较高的控制精度和可编程性,可以实现对剪切过程的自动化控制和监测。
3. 实际应用钢板剪板机广泛应用于钢铁、船舶、汽车、机械制造和建筑等行业,用于对各种金属板材进行剪切和切割。
具体应用包括但不限于以下几个方面:- 制造业:钢板剪板机用于制造各种金属制品,如汽车零部件、机械零件、建筑结构等。
剪板机机构地设计3

机械原理课程设计说明书设计题目:学院:班级:组名:组员:指导老师:2016年月目录一、机构简介 (2)二、执行机构的选择与比较 (3)1、方案设计提示 (3)2、设计任务 (4)3、机构设计方案的设计 (5)三、方案筛选与总结 (13)四、机构运动分析 (14)1. 送料装置: (14)2. 剪断机构 (15)五、执行机构的选择与比较 (17)六、对结果的分析与体会(每个人不同) (18)七、参考文献 (18)一、机构简介剪板机(英文名称:plate shears;guillotine shear)是用一个刀片相对另一刀片作往复直线运动剪切板材的机器。
是借于运动的上刀片和固定的下刀片,采用合理的刀片间隙,对各种厚度的金属板材施加剪切力,使板材按所需要的尺寸断裂分离。
剪板机属于锻压机械中的一种,主要作用就是金属加工行业。
产品广泛适用于航空、轻工、冶金、化工、建筑、船舶、汽车、电力、电器、装潢等行业提供所需的专用机械和成套设备。
工作原理剪板机剪切后应能保证被剪板料剪切面的直线度和平行度要求,并尽量减少板材扭曲,以获得高质量的工件。
剪板机的上刀片固定在刀架上,下刀片固定在工作台上。
工作台上安装有托料球,以便于板料的在上面滑动时不被划伤。
后挡料用于板料定位,位置由电机进行调节。
压料缸用于压紧板料,以防止板料在剪切时移动。
护栏是安全装置,以防止发生工伤事故。
回程一般靠氮气,速度快,冲击小。
3、原始数据及设计要求(1) 原材料为成卷的板料。
每次输送铁板长度为L=1900或2000或2200 mm(设计时任选一种)。
(2) 每次输送铁板到达规定长度后,铁板稍停,以待剪板机构将其剪断。
剪断工艺所需时间约为铁板输送周期的十五分之一。
建议铁板停歇时间不超过剪断工艺时间的1.5倍,以保证有较高的生产率。
(3) 输送机构运转应平稳,振动和冲击应尽量小(即要求输送机构从动件的加速度曲线连续无突变)。
二、执行机构的选择与比较1、方案设计提示将铁板作间歇送进的机构方案设计,可从下述两个方面考虑机构的选择:(1) 如何夹持和输送铁板,并使停歇时保持铁板的待剪位置;(2) 如何实现间歇送进,并能使铁板停歇时运送铁板的构件的速度和加速度曲线仍然连续,这样,送进机构的运转就比较平稳。
剪板机结构及工作原理

剪板机结构及工作原理嘿,朋友们!今天咱来聊聊剪板机这玩意儿。
你说它像不像一个大力士,能把那些厚厚的板材给乖乖驯服呢!剪板机啊,它主要由机架、刀片、传动系统这些部分组成。
这机架就像是大力士的身体,得足够结实才能撑得住各种折腾呀。
刀片呢,那可是它的厉害武器,锋利无比,咔嚓一下就能把板材剪开。
传动系统就像是大力士的力量源泉,让整个机器能顺畅地工作起来。
那它是怎么工作的呢?就好比你剪纸一样,只不过剪板机要剪的可不是纸,而是那些硬邦邦的板材。
板材被放在剪板机的工作台上,就像等待被修剪的小树苗。
然后呢,传动系统发力,带动刀片快速地落下来,就像一把大剪刀咔嚓一下,板材就被剪成我们想要的形状啦。
你想想看,要是没有剪板机,我们要把那些板材剪成合适的形状得多费劲啊!说不定得用锤子敲、用锯子锯,那得多累人啊!可剪板机就不一样了,它轻轻松松就能搞定,这可真是帮了我们大忙了。
而且啊,不同的剪板机还有不同的本领呢!有的能剪很薄的板材,就像能给头发做精细修剪的理发师;有的则能对付那些超厚的板材,简直就是大力士中的大力神。
在很多工厂里,剪板机可都是不可或缺的宝贝呢!它就像一个默默无闻的英雄,一直在那里为我们的生产加工贡献着力量。
它能让我们快速地得到我们需要的板材形状,提高生产效率,让一切都变得更加高效快捷。
你说它厉不厉害?它虽然不会说话,不会像人一样表达自己的情感,但它却一直在那里努力工作着,为我们创造着价值。
这不就跟我们很多勤劳的工人师傅一样嘛,虽然平凡,但却无比重要。
所以啊,我们可不能小瞧了剪板机哦!它虽然看起来不起眼,但在工业生产中可是有着举足轻重的地位呢!我们要好好爱护它,让它能一直为我们服务下去。
你说是不是呀?。
剪板机构造

3.液压一机械联合传动剪板机亡剪刀装在滑块上,下剪刀装在工作 这种剪板机是采用机械机构达到刀架平行移 动的液压传动剪板机,它既有液压传动的优点,又不要复杂的油路。
(1)刚性离合器又有滑销式、爪齿式等等,其优点是体积小、结构简单、成本低;其缺点是只有单次和连续两种 规范,接合时冲击振动大。
(2)摩擦离合器有单片式、多片式及圆锥形等多种形式。摩擦离合器的结构复杂,一般只用在中厚板料的剪板机上 。优点是除有单次行程和连续行程外,还可以进行寸动操作。
(3)和刚性离合器配合使用的制动器是带式制动器,装有摩擦离合器的剪板机是采用和离合器形式一样的制动器。
(2)机动挡料架:机动的后挡料架可以减轻劳动强度和缩短操作时间,在现在的剪板机中已广泛应用。
(六)平衡器 机械传动的剪板机由于曲柄连杆.
推荐阅读:
2.液压传动剪板机 液压传动剪板机在剪板机中的比重不断增加,液压传动在厚板料剪板机上的应用越来越广泛 ,其优点是:
(1)工作安全,可以防止因超载而引起的设备故障。
(2)结构简单、容易制造、生产周期短、成本低。
(3)操作方便,可以实现单次行程、连续行程、点动行程、行程中途停车和返程等动作。
(4)振动小、工作平稳、噪音小和刀具寿命长。
(三)滑块[刀架) 滑块是剪板机的一个重要的部件,它需要有足够的强度和刚度才能保证剪切的板料有高的剪切精 度和好的断口质量。
(四)压料机构 板料在剪切过程中应该始终被压紧在工作台面上,否则板料会在剪切过程中发生位移现象,造成被 剪板料的尺寸偏差增大,因此剪板机需要有压料机构。 压料机构有机械压料机构和液压压料机构两种形式。
- 1、下载文档前请自行甄别文档内容的完整性,平台不提供额外的编辑、内容补充、找答案等附加服务。
- 2、"仅部分预览"的文档,不可在线预览部分如存在完整性等问题,可反馈申请退款(可完整预览的文档不适用该条件!)。
- 3、如文档侵犯您的权益,请联系客服反馈,我们会尽快为您处理(人工客服工作时间:9:00-18:30)。
第1章绪论1.1课题研究现状,选题的目的和意义我国目前高档数控机床和成套成线设备的开发、生产能力,在品种、质量和数量上还不能适应市场需要。
拿汽车工业、航空航天工业来说,目前急需的高档数控机床设备有:高速加工中心、多轴联动加工中心、双主轴车削中心和车铣中心、精密磨床和复合磨床、精密电加工机床、精密大型龙头镗铣床和精密落地镗铣床、高效数控专机等,而这些设备国内企业还不能很好满足,产业化水平尚待提高。
随着我国制造业的发展,告诉简板机床的发展越来越成为机械制造行业中的中流砥柱,通用型高性能简板机,广泛适用于航空、汽车、农机、电机、电器、仪器仪表、医疗器械、家电、五金等行业。
通过对算选课题的全面研究及所给参数的分析确定告诉剪板机的整体方案,并进行主轴组件的设计计算和主轴箱的整体结构安排,最终完成高速剪板机的设计从而全面培养学生综合运用所学的基础理论,分析解决实际问题的能力;为以后更好的走向工作岗位打下坚实的基础。
我国机床产量居世界第四,但高档数控机床仍主要靠进口。
专家指出,要使我国机床水平得到整体提升,就要加大数控机床的研发力度。
近年来,我国数控机床一直保持两位数增长。
去年产值达260亿元,产。
但与发达国家相比,我国机床数控化率还不高,目前生产产值数控化率还不到30%;消费值数控化率还不到50%,而发达国家大多在70%左右。
拿金切机床来说,我国去年产量为23万台,其中数控机床只有2.4万台,仅为产量的1/10强。
高档次的数控机床及配套部件只能靠进口。
信息产业是我国增长最快的先导产业,必将为我国机床业发展提供有力支持。
以新材料、新能源、自动化等为特征的高新技术产业也将成为我国经济发展的新亮点,其发展需要大量高精、复合、智能、多轴控制、自动化高档机床。
国家许多重点项目引发的机床需求也颇为可观。
传统产业技术改造的步伐加快,制造装备水平和数控化程度的要求越来越高。
专家指出,以我国目前高档数控机床和成套成线设备的开发、生产能力,在品种、质量和数量上还不能适应市场需要。
拿汽车工业、航空航天工业来说,目前急需的高档数控机床设备有:高速加工中心、多轴联动加工中心、双主轴车削中心和车铣中心、精密磨床和复合磨床、精密电加工机床、精密- 1 -大型龙头镗铣床和精密落地镗铣床、高效数控专机等,而这些设备国内企业还不能很好满足,产业化水平尚待提高。
所以从整体上提高我国机床水平刻不容缓。
当前需要特别注意的是,必须快速提高数控机床产品的自主开发、制造能力。
为此,要建立有效的数控技术开发中心,加强对重点工艺的研究、试验,形成成套开发能力;同时,通过国际合作生产、合资经营,实现主流产品生产的高起点、成量、专业化。
提升机床质量,必须建立新型的机床企业发展模式。
业内人士认为,机床企业要“收缩阵线”,精化主业,掌握关键件、关键工序的核心技术。
一般的零件加工可以充分实施国际化采购。
同时,要加强企业发展战略联盟,为了更快得到最新技术,企业可直接与国内外科研院所“联姻”。
相对数控机床主机来说,我国功能部件生产企业的发展更显滞后。
但功能部件不仅决定着机床的整机性能,还占到整机成本的60%左右,其发展状况直接关系到机床的竞争力水平。
目前,我国的功能部件生产企业规模普遍较小,布局分散,有些还依附于主机厂或研究所。
理顺功能部件生产企业的体制,做大做强一批功能部件生产企业,已迫在眉睫。
在很大程度上取决于数控系统的性能和水平,而数控系统的发展及其技术基础离不开微电子技术和计算机技术。
随着计算机及其软硬件技术的飞速发展,数控系统的硬件平台趋于一致化,而控制系统软件的竞争日益加剧。
我国的数控系统经过“六五”期间的引进,“七五”期间的数控系统开发,“八五”期间的数控应用技术研究以及“九五”期间的主数控系统软件开发应用,已逐步形成了以航天数控、蓝天数控、华中数控和中华数控为主的数控系统产业。
1.2 国内外在该方向的研究现状及分析随着渗透和交叉融合,推动了先进冲压成形技术的形成和发展。
近十多年来,随着对发展先进制造技术的重要性获得前所未有的共识,冲压成型技术无论在深度和广度上都取得了前所未有的进展,其特征是与高新技术结合,在方法和体系上发生很大变化。
计算机技术、信息技术、现代测控技术。
在汽车、航空航天、电子和家用电器领域,需要大量的金属板壳零件,特别是随着电子业的发展,小型电子零件的需求日趋高涨,促进了高精度、高效率的高速剪板机的发展。
目前日本已成为高速剪板机技术的领军,在100KN压力、8mm冲程下,滑块速度可达4000次/min。
我国金丰、江苏扬锻、高将精机、江苏扬力、徐锻和西安通力等公司都有高速剪板机产品。
2004年已开发出了速度达1200次/min的SH-25开式高速精密剪板机。
其他还有VH形- 2 -式、JF75G闭式系列高速剪板机。
这些剪板机广泛应用于电子和微电子行业,全面提高了行业技术装备水平,替代了大量的进口机床。
近年来,我国数控机床的产量持续增长,数控化率也显著提高。
另一方面我国数控产品的技术水平和质量也不断提高。
目前我国一部分普及型数控机床的生产已经形成一定规模,产品技术性能指标较为成熟,价格合理,在国际市场上具有一定的竞争力。
我国数控机床行业所掌握的五轴联动数控技术较成熟,并已有成熟商品走向市场。
我国数控机床行业近年来大力推广应用CAD等信息技术,很多企业已开始和计划实施应用ERP、MRPⅡ和电子商务。
如,济南第二机床集团有限公司的CAD普及率达100%,是国家级“CAD示范企业”,企业的MRPⅡ系统应用也非常成功,现代化管理水平较高。
但是和发达国家相比,我国数控机床行业在信息化技术应用上仍然存在很多不足。
一、信息化技术基础薄弱,对国外技术依存度高。
我国数控机床行业总体的技术开发能力和技术基础薄弱,信息化技术应用程度不高。
行业现有的信息化技术来源主要依靠引进国外技术,对国外技术的依存度较高,对引进技术的消化仍停留在掌握已有技术和提高国产化率上,没有上升到形成产品自主开发能力和技术创新能力的高度。
具有高精、高速、高效、复合功能、多轴联动等特点的高性能数控机床基本上还得依赖进口。
二、产品成熟度较低,可行性不高。
国外数控系统平均无故障时间在10000小时以上,国内自主开发的数控系统仅3000-5000小时;整机平均无故障工作时间国外达800小时以上,国内最好只有300小时。
三、创新能力低,市场竞争力不强。
我国生产数控机床的企业虽达百余家,但大多数未能形成规模生产,信息化技术利用不足,创新能力低,制造成本高,产品市场竞争能力不强。
高速度、高精度化。
速度和精度是数控机床的两个重要指标,它直接关系到加工效率和产品质量。
目前,我国生产的第六代数控机床系统均采用位数、频率更高的处理器,以提高系统的基本运算速度,使得高速运算、模块化及多轴成组控制系统成为可能。
发展可靠性最大化。
数控机床的可靠性一直是用户最关心的主要指标。
新一代的数控系统将采用更高集成度的电路芯片,利用大规模或超大规模的专用及混合式集成电路,减少元器件的数量,从而提高可靠性。
同时通过自动运行诊断、在线诊断、离线诊断等多种诊断程序,实现对系统内硬件、软件和各种外部设备进行故障诊断和报警。
- 3 -第2章剪板机的结构设计与校核计算2.1 总体技术参数的确定本机器用于剪切厚度为0.8-6mm,最大宽度为2000mm,最大长度为800mm 的钢板。
被剪钢板(Q235)强度以2/N为准,如需剪切其他强度的板料时,450mm可相应的改变被剪板料的厚度。
2.2 总体结构的确定本设计的剪板机正面看呈龙门式,侧面看呈C字形,主要如图2.1.01 构,为了节省材料横梁和侧板等支撑结构均采用空心钢板焊接结构。
图2-1-1 总体结构图2.2.1 主要技术要求1.有足够的强度,能长期承受最高工作压力及短期动态试验压力而不会产生永久变形。
2.有足够的刚度,能承受油缸的作用力,不至于产生弯曲。
3.焊接结构的焊接处不应产生裂纹或有过大的变形。
2.2.2 侧板的校核计算侧板是缸体的固定部分它承受着主要动力,是本设计的主要受力部分,它的计算是否满足要求至关重要,涉及到精度、材料力学的性能。
为了节省- 4 -- 5 -材料本设计的结构多数采用空心焊板结构具体如图2-1-2图2-1-2侧板受力主要为来自剪切时的剪切力,其主要计算公式为μττ≤=A F 公式(2-2-1) 式中 τ一一工作时最大剪切应力F 一一工作时最大工作压力 500KNA 一一受的剪切面积 (2mm )μτ一一剪切极限应力, 取μτ=300MPaMPa mN A F 6.1603.05000002===τ μττ≤ 满足要求由于最危险的截面在喉口,所以在喉口处加厚一肋板结构如图所示图2-1-3 肋板的固定- 6 -2.2.3 横梁的设计计算横梁主要是用于支撑油缸的耳环、支撑油箱和电机和泵等液压系统元件和连接侧板的,起主要计算涉及到剪切计算和挠度的计算。
剪切的计算在前面已经计算过在此不祥述了。
这里主要进行挠度的计算。
其挠度主要由两部分合成计算公式如下21ωωω+= 公式(2-2-2) EIGl 4831-=ω 公式(2-2-3) EIal 384542-=ω 公式(2-2-4) 式中ω:总挠度之和1ω:横梁内的元件重力产生的挠度2ω:横梁自重产生的挠度q :横梁重力产生的均布载荷E :弹性模量,去 E =210GPaG :横梁内的元件重力l :横梁的长度I :惯性矩,矩形的惯性矩为123hb I = 公式(2-2-5)式中h :矩形的高b :矩形的宽m EIGl 00013.04831==ω m EIql 00008.0384542=-=ω mm m 021.000021.021==+=ωωω挠度为0.021mm 对工作没有大的影响,满足挠度要求。
- 7 - 2.3 上刀架的设计计算上刀架是直接的受力体,所以对上刀架的要求很严格的,即要满足力学性能要求,还要满足受挠度的影响。
而且还和精度有很大的联系。
所以上刀架应满足下面的要求。
2.3.1 上刀架的主要技术要求1. 有足够的强度,能长期承受最高工作压力及短期动态试验压力而不会产生永久变形2. 有足够的挠度,能承受或缓解两个油缸的不均衡作用力,不至于产生弯曲甚至扭断上刀架。
3. 有足够的精度,上刀架是安装上刀片的装置,上刀的安装是确定精度的一个重要部件,所以上到因该有足够的精度才能满足要求。
2.3.2 上刀架的受力计算和校核上刀架的主要力源是来自液压缸和切削工件时带来的剪切力。
起计算公式为μττ≤=AF 公式(2-3-1) 式中τ一一工作时最大剪切应力F —— 工作时最大工作压力 500KNA —— 受的剪切面积 (2m )μτ一一剪切极限应力,取MPa 300=μτMPa AF 06.2==τ μττ≤力学强度满足要求。