目视检测操作规程
目视检测操作规程

目视检测操作规程目视检测是一种常见的检测手段,用于观察和判断目标物体的形状、颜色、大小、数量等各种特征信息。
为了保证目视检测的准确性和可靠性,在进行目视检测时需要遵守一定的操作规程。
以下是一份目视检测的操作规程,供参考。
一、前期准备1.确保在适当的照明条件下进行目视检测。
如果需要,可使用辅助灯光或调整环境照明。
2.清理检测区域,保证目标物体的表面清洁,以免影响目视检测的观察结果。
3.针对目视检测的特殊要求,如检测目标的形状、颜色、大小等特征,做好必要的准备工作。
二、目视检测过程1.首先,确认检测目标的类型和要求。
了解目标的相关特征,以便进行正确的观察和评判。
2.将注意力集中在目标物体上,仔细观察其整体形状、颜色、大小等特征,并较为细致地观察其细节特征。
3.进行数量统计时,逐一仔细计数,确保不遗漏目标物体,并进行相应的记录。
4.在观察目标物体时,可以运用放大镜等工具进行辅助观察,以获得更详细、准确的信息。
5.如需要对目标物体进行测量,可以使用相应的测量工具进行测量操作,确保测量结果的准确性。
6.在目视检测过程中,如发现异常情况,比如物体损坏、缺损或其他异常状态,应及时记录并报告相关负责人或有关部门。
三、操作要求与注意事项1.进行目视检测时,需要保持充分的专注和耐心,细致观察。
尽量减少干扰和外界影响。
2.检测人员需具备良好的视觉能力和观察技巧,如有必要,可以进行相关培训和普查。
3.操作人员要熟悉所检测目标的特征和要求,遵循相关规程和标准进行操作。
4.在进行目视检测时,应按照规定要求完成记录,包括所检测物体的相关信息、结果和存在的问题等。
5.目视检测完成后,将记录整理并妥善保存,以备后续参考和查阅。
6.目视检测过程中,如需进行重复检测或配合其他检测方法,应按照要求进行操作。
7.如有必要,可利用科学仪器或技术手段对目标进行辅助检测,以提高检测准确度。
通过以上操作规程,可以提高目视检测的准确性和可靠性。
在实际操作中,应根据具体情况进行相应的调整和执行。
目视检查规范课件

05
目视检查的应用案例
Chapter
机械设备的目视检查
总结词
通过观察设备外观、结构、连接和运行状况,判断设备是否存在异常或潜在故障。
详细描述
目视检查是机械设备维护中常用的方法之一,通过观察设备的外观、结构、连接和运行状况,可以发现设备是否 存在异常或潜在故障。例如,检查机械零件是否有磨损、变形或断裂等现象,油路和气路是否畅通,以及设备运 行时的声音和振动是否正常等。
03
目视检查的方法
Chapter
直接目视检查
直接目视检查是指检查人员通过肉眼或简单工具直接观 察设备、产品或表面的状态,以发现异常或缺陷的过程 。 直接目视检查适用于观察表面状况、颜色、尺寸、结构 等,是目视检查中最基本的方法。
直接目视检查需要注意观察细节,并利用适当的光源和 角度来提高观察效果。
在初步观察的基础上,对被检查对象进行 详细检查,重点关注关键部位和可能存在 的问题点。
记录和拍照
交互与沟通
对检查过程中发现的问题进行记录,并拍 摄照片作为证据。同时,记录被检查对象 的整体情况,以便后续分析。
在检查过程中,与操作人员或其他相关人 员进行交流,了解被检查对象的运行状况 和使用情况,以便更好地理解问题所在。
操作熟练度,降低实际操作中的风险和误差。
THANKS
感谢观看
仪器辅助目视检查需要专业知识和技 能,并遵守相关安全操作规程。
常用的仪器辅助目视检查包括X射线 检测、超声检测、红外线检测等,可 以用于检测内部缺陷、材料性质等。
以上是关于目视检查方法的扩展内容 ,希望对您有所帮助。
04
目视检查的注意事项
Chapter
安全注意事项
01
金属探测仪的校准和操作规范
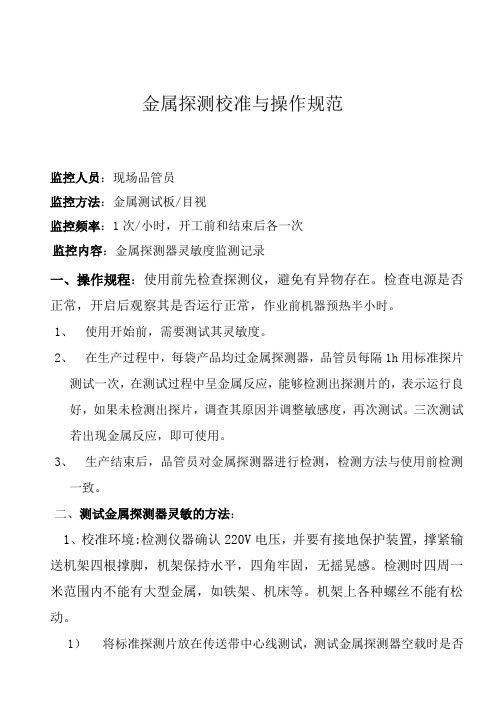
金属探测校准与操作规范监控人员:现场品管员监控方法:金属测试板/目视监控频率:1次/小时,开工前和结束后各一次监控内容:金属探测器灵敏度监测记录一、操作规程:使用前先检查探测仪,避免有异物存在。
检查电源是否正常,开启后观察其是否运行正常,作业前机器预热半小时。
1、使用开始前,需要测试其灵敏度。
2、在生产过程中,每袋产品均过金属探测器,品管员每隔1h用标准探片测试一次,在测试过程中呈金属反应,能够检测出探测片的,表示运行良好,如果未检测出探片,调查其原因并调整敏感度,再次测试。
三次测试若出现金属反应,即可使用。
3、生产结束后,品管员对金属探测器进行检测,检测方法与使用前检测一致。
二、测试金属探测器灵敏的方法:1、校准环境:检测仪器确认220V电压,并要有接地保护装置,撑紧输送机架四根撑脚,机架保持水平,四角牢固,无摇晃感。
检测时四周一米范围内不能有大型金属,如铁架、机床等。
机架上各种螺丝不能有松动。
1)将标准探测片放在传送带中心线测试,测试金属探测器空载时是否处于正常状态,若能够检测出探测片的,表示运行良好,如果未检测出探片,调查其原因并调整敏感度,再次测试。
测试若出现金属反应,即可使用;2)在生产过程中每隔1h用标准探片测试验证一次,在测试过程中呈金属反应,能够检测出探测片的,表示运行良好,如果未检测出探片的,调整其原因并调整敏感度,再次测试。
测试若出现金属反应即可使用。
3)模拟金属检测:分别将三个试块放在检测产品的上部、左补、右部,通过设备传送带的中间位置,金属检测仪应能报警并停止运行(每种试块3次)。
检测完成后,再检测一次产品是否正常通过金探机。
4)以上每次测试试块金属检测仪均可报警并停止运行,则说明设备的灵敏度合适。
若是任何一次检测出现不报警的情况,则说明灵敏度不稳定,这时应该在同一位置再连续检测3次,3次都能检岀方可证明灵敏度合格,若还是出现无报警的情况则需要停下进行调整和检查!2、对于大包装的冰鲜产品,(有些机型不适合于冰鲜品)如果生产中有金属探测器经检测失灵的情况,品管员应报告HACCP小组。
餐饮业食品原材料检验操作规程

餐饮业食品原材料检验操作规程一、引言餐饮业作为服务行业的一部分,其食品安全问题备受关注。
保证餐饮食品的安全和质量,对保障顾客的健康至关重要。
而食品原材料检验是餐饮业中不可或缺的一环。
本文就餐饮业食品原材料检验的操作规程进行详细介绍。
二、检验频率1.供应商审核:对食品原材料供应商进行定期审核,确保其具备合法的经营资质和出产能力。
审核要包括对供货商的生产设施、质检流程和员工培训情况等方面的考察。
2.进货前检验:在进货前对原材料进行检验。
重点检查原材料的包装完好情况、标签信息的准确性以及外观是否正常。
3.每日检验:对每天使用的原材料进行抽样检验。
主要关注原材料的卫生状况、新鲜度和质量指标等方面。
4.随机抽检:通过随机抽检的方式,对已入库的原材料进行检验。
目的是确保原材料的质量连续性和稳定性。
三、检验项目食品原材料检验项目应包括以下方面:1.外观:包括颜色、形状、大小以及表面是否有异物等。
外观正常的原材料才能被接受。
2.卫生状况:检验原材料是否含有有害微生物、农药残留、重金属等有害物质。
卫生状况不达标的原材料必须禁止使用。
3.新鲜度:对生鲜原材料,如蔬菜、水果等进行新鲜度检验。
主要检查原材料的气味、口感以及表面是否有腐烂、变质迹象。
4.质量指标:根据食品本身的特性和要求,检验原材料的相关指标如酸碱度、含水量、脂肪含量等。
五、检验方法1.目视检查:通过观察原料的外观、颜色、形状等来判断其是否达到要求。
2.感官评价:通过嗅觉、味觉等感官检测手段来判断原料的新鲜度和口感。
3.理化指标检测:通过使用专业设备,如PH计、电导率计等,对原料的理化指标进行检测。
4.微生物检测:通过对样品进行微生物培养和指标检测,判断原料是否达到卫生要求。
六、结果处理在对原材料进行检验后,需要根据检验结果采取相应的处理措施:1.合格原料:检验结果符合标准的原料可以入库或使用。
2.不合格原料:检验结果不符合标准的原料必须拒收,同时通知供应商,并与供应商协商解决方案。
目视检测操作规程

目视检测操作规程目视检测是指通过人眼进行观察和判断,以发现设备、产品或工作环境中的异常情况或问题。
它在工业生产、质量控制、安全监测等领域起着重要的作用。
为了确保目视检测的准确性和有效性,需要制定相应的操作规程。
以下是目视检测的操作规程,以确保检测工作的顺利进行。
一、操作前准备1.检查目视检测设备是否正常,并确保设备能够满足检测要求。
2.检查工作环境是否满足安全要求,如光照条件、电气设备的安全性等。
3.清理工作区域,确保没有杂物或安全隐患。
二、确定检测目标1.明确检测的对象,如产品、设备及相关部件等。
2.明确检测的要求和标准,包括尺寸、形状、颜色、表面质量等。
三、选择合适的检测位置和视角1.根据目标特点选择合适的检测位置,确保能够全面观察到目标。
2.根据目标特点选择合适的观察角度,避免产生视觉死角或遮挡。
四、进行目视检测操作1.始终保持专注和集中注意力,不受外界干扰。
2.仔细观察目标,注意细节和特征。
3.遵循事先设定的检测要求和标准进行判断和评估。
4.辅助使用一些工具,如放大镜、测量尺等,提高检测准确性和效率。
5.及时记录检测结果和发现的异常情况,确保后续分析和处理。
五、处理异常情况1.对于发现的异常情况,应及时报告相关人员,并按照规定的程序进行处理。
2.在处理过程中,应严格按照操作规程进行,确保处理结果符合要求。
六、定期维护和检修1.定期对目视检测设备进行维护和检修,确保设备状态良好。
2.根据实际需要进行设备校准,确保检测结果的准确性和可靠性。
七、记录和总结1.将检测结果和异常情况进行记录和归档,方便后续分析和改进。
2.定期对目视检测操作进行总结和评估,发现问题并进行改进和优化。
目视检测操作规程是确保检测工作的准确性和有效性的重要依据,它涵盖了操作前准备、确定检测目标、选择合适的检测位置和视角、进行目视检测操作、处理异常情况、定期维护和检修以及记录和总结等方面的内容。
通过遵循这些规程,可提高目视检测的准确性和效率,确保产品、设备和工作环境的安全和质量。
VT检测规程

目视检测规程一、依据及适用范围依据ISO10042:2005、ISO5817:2014、ISO6520-1:2007标准和本公司特性制定本操作规程,本规程规定了目视检验的方法及人员等技术管理要求。
本规程适用于碳钢、不锈钢及铝合金焊缝外观检查。
二、要求1.1岗操作。
1.21.31.422.12.22.32.433.13.211.11.21.3其它检测仪器如成型量具、镜子、照像机、内窥镜。
2焊缝的外观检测焊缝的外观检测的基本范围在所应用的标准中作出了规定:焊缝必须可见且便于检测,检测时间在表面处理之前。
焊缝的外观检测可分三个阶段:——焊前准备的外观检测——焊接过程中的外观检测——焊接后的外观检测2.1焊前准备的外观检测仅供个人学习参考仅供个人学习参考2.1.1坡口的形状、尺寸和均匀度必须符合相应标准的有关要求(与焊接工艺规程是否相符)。
坡口的尺寸不能过大。
2.1.2焊接坡口及界面必须按要求进行清理。
2.1.3按图纸要求进行装配和固定。
2.2焊接过程中的外观检测2.2.1多层焊时,在其进行下道焊道的施焊前,都要进行层间清理(特别是在焊缝金属和母材的过渡区)。
2.2.2如果一旦发现有裂纹、空穴或其它缺陷,应立即停止施焊,且采取措施加以消除。
2.2.3注意焊道的结构,以达到足够的熔合比,避免出现未熔合。
2.333.13.244.14.2。
4.3测量咬边深度时,使用焊缝检验尺的薄而尖的直边,以焊缝两侧的母材为基准面进行测量。
4.4对接焊缝的余高可用成型量具或焊缝尺等焊缝测量工具来测量。
如果焊缝两侧厚度不一样,可按下图来计算:。
4.5四、质量评定1焊接缺陷的种类21H +H =H焊接缺陷的种类很多,根据标准ISO6520把熔焊缺陷分为六类:第一类缺陷:裂纹第二类缺陷:孔穴第三类缺陷:固态夹渣物第四类缺陷:未熔合和未焊透第五类缺陷:外观缺陷第六类缺陷:其他缺陷。
具体缺陷编号及说明见标准ISO6520。
2观察及处理对缺陷件,须对缺陷的部位、大小、性质在检测报告上做出详细描述,并在工件上做出标识。
目视熔点仪安全操作规程

目视熔点仪安全操作规程1使用前的准备- 硅油的灌入:用注射器吸取硅油10mL从溢出口注入,重复6次,共需注入60mL硅油,然后在溢流口盖上溢油瓶。
- 油管的更换:如果需要更换浴管,请按以下方法更换:a)首先,取下溢油瓶,然后卸下侧板。
b)用手伸入仪器箱体内,一手拖住油浴管,一手拉下弹簧,然后垂直向下水平取出油浴管,取出油浴管时,须小心谨慎,以免玻璃破损。
c)把油浴管装入仪器内,按与上述方法相反的顺序进行。
2熔点的测定- 通过按键输入所需要的起始温度,设定的起始温度应低于待测物质的熔点;- 开启电源开关,开机显示:welcome!短时间显示后,出现以下屏幕,画面ST:画面,通过按键“←”“→”选择开始升温速率,预置温度的百位、十位、个位。
通过按键“+”“—”选择增量,减量。
选择完毕,按“预置”键,现在显示画面为:V:×× t:××× T:×××.×↑- 仪器已经静茹升温阶段,同时此次的设定速率、预设温度保存到系统存储器中,以备下次使用。
- 仪器预热20min,温度稳定后,将含有待测物质的毛细管从毛细管插入口的小孔放入浴管中,按“升温”键,现在仪器根据设定的升温速率进入匀速升温阶段。
- 测量者可根据目视样品的溶解情况,按下相应的键盘,此时,在相应位置显示并记录当前温度值(注意:初熔终熔点的键盘只能按一次)三根毛细管的初熔,终熔值都记录后,系统自动转F;(测量者如果想提前结束本次测量,按“预置”键,系统自动转F)。
- 一次测量结束后,测量人员小心地取出被测毛细管,测量者如果想进行再次测量,按“预置”键返回,跳动步骤ST。
3注意事项3.1一般测量低熔点物质,后测量高熔点物质。
3.2样品必须按要求烘干,在干燥和洁净的拈钵中碾碎,用自由落体轻敲毛细管,使样品充满牢固,填装高度应一致,具体要求应符合标准规定。
3.3括号取出毛细管,小心谨慎,避免断裂。
目视旋光仪标准操作规程

目的:明确WXG-4目视旋光仪的使用要求、基本操作步骤。
范围:WXG-4目视旋光仪的操作。
职责:质量管理部、QC.
内容:
1准备工作
1.1先把预测溶液配好,并加以稳定和沉淀;
1.2把预测溶液盛入试管待测。
但应注意试管两端螺旋不能旋得太紧(一般以随手旋紧不漏水为止),以免护玻片产生应力而引起视场亮度发生变化,影响测定准确度,并将两端残液揩拭干净;
1.3接通电源,约点燃10分钟,待完全发出钠黄光后,才可观察使用;
1.4检验度盘零度位置是否正确,如不正确,可旋松度盘盖四只连接螺钉、转动度盘壳进行校正(只能校正0.5°以下),或把误差值在测定过程中减之。
2测定工作
2.1打开镜盖,把试管放入镜筒中测定,并应把镜盖盖上和试管有圆泡一端朝上,以便把气泡存入,不致影响观察和测定;
2.2调节视度螺旋至视场中三分视界清晰时止;
2.3转动度盘手轮,至视场照度相一致(暗现场)时止;
2.4从放大镜中读出度盘所旋转的角度;
2.5利用下述公式,求出物质的比重、浓度、纯度与含量。
比旋度计算公式
[α]=100α/LC
式中α——测得的旋光度(度)
L——溶液的长度(dm)
C——为每100ml溶液中含有被测物质的重量(g)。
- 1、下载文档前请自行甄别文档内容的完整性,平台不提供额外的编辑、内容补充、找答案等附加服务。
- 2、"仅部分预览"的文档,不可在线预览部分如存在完整性等问题,可反馈申请退款(可完整预览的文档不适用该条件!)。
- 3、如文档侵犯您的权益,请联系客服反馈,我们会尽快为您处理(人工客服工作时间:9:00-18:30)。
目视检测操作规程
目录
1 范围 (2)
2 参考标准 (2)
3 检查条件和设备 (2)
4 人员 (3)
5 目测检查—总则 (3)
6. 目测检查接缝的准备 (3)
7 焊接时的目测检查 (4)
8 完成焊缝的目测检查 (4)
9 修理焊缝的目测检查 (5)
1 范围
本规范涉及对金属材料熔融焊缝的目测检查。
检查通常在同一焊接条件下的焊缝上进行,除非由比如应用规范所要求或经协议双方所同意,也可以在焊接过程的其它阶段进行。
2 参考标准
本规范结合了其它有日期的或无日期的出版物的规定。
在本文中以及出版物中在适当场合引用的这些参考标准将在后面列出。
对于有日期的参考标准,其后续修订或这些出版物的任何修订经结合后,也能适用于本欧洲标准。
对于无日期的参考规定,可以引用其出版的最新版本。
EN 288-2 金属材料焊接程序的技术规范和批准—第2部分:电弧焊
接的焊接程序技术规范
EN 473 无损检测人员的资格和证书—一般原则
prEN 12062 焊缝的无损检测—一般规则
EN 25817 钢材的弧焊焊缝—缺陷质量等级准则
EN 30042 铝和可焊合金的弧焊焊缝—缺陷质量等级准则(ISO 10042:1992)
ISO 3058:1974 无损试验—目视检测的辅助—低倍放大镜的选择
ISO 3058:1976 游标卡尺读数至0.1和0.05 mm
3 检查条件和设备
表面照度最小为350 lx;建议为500 lx。
进行直接检查时,眼睛最好位于距离检查表面600 mm处,观察角度不小于约30°(见图1)。
使用光纤检查镜作远距离检查时,光纤或摄像机属于附加要求,须由应用标准所指定或经协议双方所同意。
如果要求在全县和背景之间获得好的对比度和立体效果,则须使用附加光源。
在有疑问时,可以使用目测检查作为其它无损检测方法的补充对表面缺陷进行检查。
检查设备的举例在附录A 中给出。
4 人员
按照欧洲标准,进行检查的人员必须:
a)熟悉相关标准、规则和技术规范;
b)被告知所使用的有关焊接程序;
c)按照EN 473的要求必须具有好的视力,并且须在每过12个月后检查一
次。
5 目测检查—总则
检查范围必须由应用标准事先规定,或经协议双方同意。
检查员必须接近焊缝作必要的检查,并取得生产文件。
在可能实际接近的情况下,在同一焊接条件下检查焊缝,有时有必要在表面处理后再作检查。
范围
图1. 接近检查
6. 目测检查接缝的准备
在焊接之前需要进行目测检查时,必须检查:
a) 是否满足在焊接程序技术规范,即按照EN 288-2标准中指定要求所准备的焊缝形状和大小;
b) 熔融面和相邻面是否清洁;
c) 待焊接的零件是否按照图纸或说明已经相互固定。
7 焊接时的目测检查
需要的话,在焊接过程中可以进行以下检查:
a) 焊接金属的每道或每层在被另一焊道覆盖之前是否清洁,特别要注意焊接金属和熔融面之间的连接。
b) 不能有可见缺陷如裂缝或凹坑,如发现这些缺陷,必须汇报以便在进一步焊接之前采取救治行动。
c) 焊道之间以及焊缝和母材之间的过度在焊接下一焊道之前须有满意的熔融状态;
d) 凿槽的深度和形状必须符合焊接工艺规程(WPS)要求或与原先槽的形状相仿,以保证能按照规定完全清除焊接金属。
8 完成焊缝的目测检查
8.1 总则
检查完成焊缝以决定其能否满足经协商的接受标准,亦即EN 25817或EN 30042或参考的prEN 12062标准。
如果不能达到应用标准的范围或双方的协议要求,则需详细检查8.2自8.5章节的项目。
8.2清洁和熔修
检查焊缝的以下方面:
a)所有的焊渣是否经人工或机械方式去除,这可以防止缺陷被遮盖;
b)是否有工具印痕或打击痕迹;
c)当需要焊修时,使焊缝过热以避免研磨,同时可以避免研磨痕迹和不平整表面的产生;
d)对于需要熔修整平的角焊和对焊焊缝,接缝是否与母材合并光洁没有
凹陷。
8.3外形和尺寸
检查焊缝的以下方面:
a)焊接面的外形和任何加强焊缝的高度是否满足接受标准的要求(参见
8.1章节);
b)焊接表面是否规则、波纹标记的图案和间距是否均匀并满足目测外观要求,最后层和母材之间的距离或焊道位置是否按照焊接工艺规程(WPS)的要求进行测量;
c)焊缝宽度在整个焊缝上是否连续并满足焊接图纸或接受标准(参见8.1章节)的要求。
在对焊情况下,检查焊接准备工作是否已经完全做好。
8.4 焊缝根部和表面
检查目测可接近的焊缝部分,即单侧对焊的焊缝根部以及焊缝表面是否与接受标准存在偏差(参见8.1章节)。
检查焊缝的以下方面:
a) 对于单侧对焊的焊缝,检查渗透、根部焊缝凹度和任何烧穿或收缩凹槽在整个焊缝上是否在接受标准指定的极限范围内;
b) 任何咬边是否在接受标准范围内;
c) 在焊接表面或受热部位的任何缺陷如裂缝或检测到的孔洞,必要时采用光学辅助方法检查,是否符合适当的接受标准;
d) 任何临时焊接到目的物上以方便生产或组装,但会影响目的物的功能的附件必须清除使目的物不受损害。
检查固定附件的部位是否存在裂缝等。
8.5 焊接后热处理
在焊接后的热处理完成后,必须对焊缝做进一步的检查。
9 修理焊缝的目测检查
9.1 总则
如焊缝完全或部分未能满足接受标准并须进行修理后,则在修理过程中须对9.2至9.3章节所述事项进行详细检查。
9.2部分清除焊缝
检查铲除部分是否足够深和长以清除所有缺陷。
必须保证从切口底部至切口端部和侧面的金属焊缝表面有一个渐进的锥度。
切口的宽度和形状须留有合适的凹口用于重焊。
9.3全部清除焊缝
检查当彻底铲除有缺陷的焊缝时,不能严重伤及材料,或当清除有缺陷焊缝的材料段时,将插入新的材料段,准备焊接的形状和尺寸必须满足指定的要求。
9.4检查
按照原始焊缝在第8章所规定的同样要求来检查每个修理的焊缝。
编制:审核:批准:
(注:范文素材和资料部分来自网络,供参考。
只是收取少量整理收集费用,请预览后才下载,期待你的好评与关注)。