焊接坡口加工要求
常见坡口形式及加工技术要求'

常见坡口形式及加工技术要求'
一、常见坡口形式:
1.V型坡口:即将两个零件的边缘切削成V字形,常见的有全V型坡
口和半V型坡口。
这种坡口形式适用于边缘焊接。
2.U型坡口:将两个零件的边缘切削成U字形,常见的有全U型坡口
和半U型坡口。
这种坡口形式适用于角焊接。
3.J型坡口:将两个零件的边缘切削成J字形,常见的有全J型坡口
和半J型坡口。
这种坡口形式适用于角间隙较大的焊接。
4.X型坡口:将两个零件的边缘切削成X字形,可用于非常厚的板材
的焊接。
5.Y型坡口:将两个零件的边缘切削成Y字形,常见的有全Y型坡口
和半Y型坡口。
适用于非常厚的板件的角焊缝。
二、加工技术要求:
1.坡口的尺寸要符合焊接工艺规程的要求,必须保证焊接接头的强度
和可靠性。
2.坡口的形状和倾斜角要严格控制,以确保焊接时更好的熔深和焊缝
的合理形态。
3.坡口的加工精度要高,尤其是板材的面度和平整度要做到符合要求,以便保证焊接质量。
4.加工坡口的工艺要求要合理,包括采用合适的切割工具、切割参数
和切割方法,并保证坡口的光洁度和表面质量。
5.加工过程中要注意安全,避免事故的发生,同时还要注意保护环境,合理处理废料和废气。
6.在坡口加工过程中要时刻掌握加工的进度和质量,及时调整加工参数,确保坡口的加工质量。
总之,常见坡口形式及其加工技术要求对于焊接工艺的控制和焊缝的
质量有着重要的影响。
加工人员需要严格按照相应的标准和规范进行坡口
的加工,并认真进行质量检查和控制,以确保焊接接头的质量和可靠性。
管道焊接坡口打磨要求
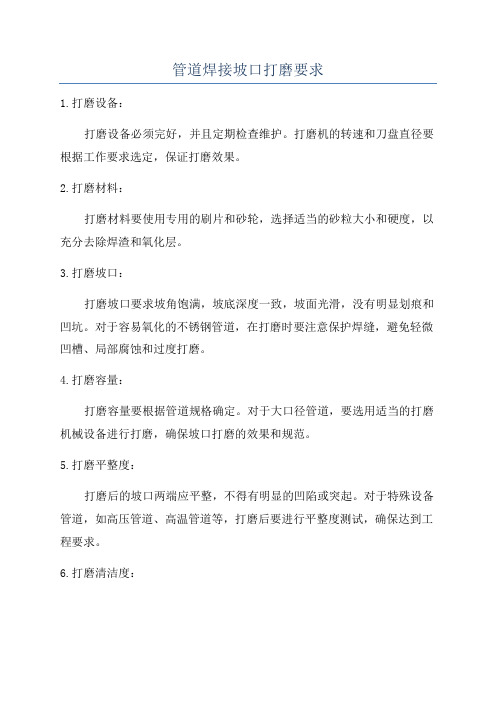
管道焊接坡口打磨要求1.打磨设备:打磨设备必须完好,并且定期检查维护。
打磨机的转速和刀盘直径要根据工作要求选定,保证打磨效果。
2.打磨材料:打磨材料要使用专用的刷片和砂轮,选择适当的砂粒大小和硬度,以充分去除焊渣和氧化层。
3.打磨坡口:打磨坡口要求坡角饱满,坡底深度一致,坡面光滑,没有明显划痕和凹坑。
对于容易氧化的不锈钢管道,在打磨时要注意保护焊缝,避免轻微凹槽、局部腐蚀和过度打磨。
4.打磨容量:打磨容量要根据管道规格确定。
对于大口径管道,要选用适当的打磨机械设备进行打磨,确保坡口打磨的效果和规范。
5.打磨平整度:打磨后的坡口两端应平整,不得有明显的凹陷或突起。
对于特殊设备管道,如高压管道、高温管道等,打磨后要进行平整度测试,确保达到工程要求。
6.打磨清洁度:打磨完毕后,要对焊缝进行清洁处理,确保没有杂质和焊渣。
可以用空气枪吹净焊缝,或者用棉纱蘸酒精进行清洁。
特别是对于不锈钢管道,要避免铁屑等杂质粘附在焊缝上,以免引起锈蚀。
7.打磨光洁度:打磨后的焊缝表面应平整光滑,没有明显的划痕和磨痕。
可以通过目测和手触检查光洁度,也可以使用光洁度仪进行精确的测试。
8.打磨结束标记:打磨结束后,要对每个焊缝进行标记,包括焊接坡口的编号、打磨人员的签字和日期等信息,以便质检人员进行复查。
在管道焊接坡口打磨过程中,要注意操作安全,戴好防护眼镜、面具和手套,避免操作中的意外伤害。
另外,操作人员要熟悉打磨设备和工艺要求,保证打磨质量符合相关标准和规范。
总之,管道焊接坡口打磨对于管道焊接质量的保证至关重要,要严格按照规范要求进行操作,确保焊接接头的质量和可靠性。
管道焊接坡口规范
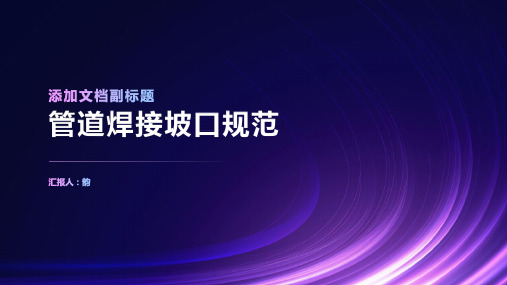
施工安全措施
焊接前应检查管道坡口是否符合规范要求,确保无裂纹、夹渣等缺陷。 焊接时应采取措施防止飞溅和弧光伤人,如使用防护面罩、手套等。 焊接时应保持工作场所整洁,避免易燃易爆物品,并配备灭火器等消防器材。 焊接完成后应进行质量检查,确保无焊接缺陷,并进行必要的防腐处理。
施工质量控制
焊接前检查坡口角度、间隙和钝边是否符合要求 控制焊接电流和电压,保持稳定的焊接参数 焊接过程中注意焊缝的层间温度,避免过热 焊后进行外观检查和无损检测,确保质量合格
火焰加工法:使 用火焰对管道坡 口进行加热,利 用热胀冷缩的原 理进行加工。
激光加工法:利 用激光的高能量 对管道坡口进行 加工,具有精度 高、速度快的特 点。
等离子加工法: 利用等离子弧的 高温对管道坡口 进行切割和加工。
V型坡口
定义:V型坡口是 一种常见的管道 焊接坡口形式, 其形状类似于英 文字母“V”,具 有较大的坡口角 度。
施工记录与报告
记录施工过程:包 括焊接设备、材料、 工艺参数等
报告问题与处理:如 发现焊接缺陷、设备 故障等,应及时报告 并记录处理过程
验收报告:焊接完成 后,应提交验收报告, 包括焊接质量、外观 检测等内容
存档管理:施工记 录与报告应妥善保 存,以便后期查阅 和追溯
感谢您的观看
适用范围:适用于各种类型的管道系统,尤其适用于需要同时传输液体和气体的管道系统
注意事项:在选择和使用复合型坡口时,需要考虑管道系统的压力、温度、介质等参数,以及 管道的安装和维护要求
手工加工坡口
定义:使用手工工 具对管道进行坡口 加工的方法
适用范围:适用于 小批量、小直径管 道的坡口制备
加工工具:砂轮机 、角磨机、坡口机 等
管道焊接坡口规范
焊接坡口加工工艺指南坡口要这样开

焊接坡口加工工艺指南坡口要这样开一、坡口开口要求1.开口形状:坡口的形状应该符合工艺要求,一般为V型、U型、X 型、J型等。
2.开口尺寸:坡口开口尺寸应根据焊接材料的厚度、焊接方法和要求来确定。
一般情况下,坡口的开口尺寸为焊接材料厚度的1.5倍至2倍。
开口宽度决定了焊接强度的增加,但过大的开口宽度会导致焊接变形和材料的浪费,过小则会影响焊接质量。
3.开口角度:坡口的开口角度也是需要注意的,一般情况下,焊接坡口的开口角度应为40°至60°之间,开口角度过小会导致焊料填充不足,开口角度过大会增加焊接难度。
4.坡口的净宽和倒角:坡口的净宽应符合相关标准要求,倒角后的内壁应光滑、无毛刺、无裂纹,以确保焊接的良好质量。
二、坡口开口方式1.机械方式:机械开口是指使用机械设备如磨床、切割机等对工件进行开口加工。
这种方式开口速度快、精度高,适用于规格较大、质量要求较高的工件。
2.火焰切割方式:火焰切割是指使用高温火焰对工件进行切割。
这种方式适用于钢板、钢管等材料的开口加工,开口较大,但精度较低。
3.氧气割方式:氧气割是指利用金属与氧气在高温下反应的原理进行切割,适用于切割较厚的金属材料,适用性较广。
三、常见坡口类型1.V型坡口:V型坡口是指将工件两侧倒角后形成的坡口,适用于焊接钢板、钢管等较大厚度的材料。
2.U型坡口:U型坡口是指将工件坡肩倒角后形成的坡口,适用于焊接较厚的工件,具有较高的焊缝强度。
3.J型坡口:J型坡口是指将工件一边倒角后形成的坡口,适用于焊接厚度较小的工件。
4.X型坡口:X型坡口是指将工件两侧倒角后形成的倒角坡口,适用于焊接对焊时间较紧的工件。
四、坡口选择原则1.根据焊接材料的厚度选择合适的坡口类型。
2.根据焊接方法选择合适的坡口类型。
3.根据焊接强度要求选择合适的坡口类型。
4.根据坡口的开口尺寸选择合适的坡口类型。
总结起来,焊接坡口加工是一项重要的工艺,在焊接过程中起到了连接材料、提高焊接强度和质量的重要作用。
焊接坡口加工要求
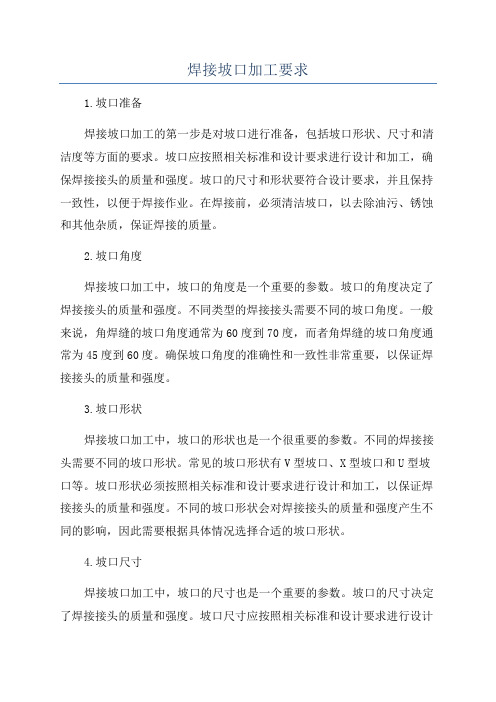
焊接坡口加工要求1.坡口准备焊接坡口加工的第一步是对坡口进行准备,包括坡口形状、尺寸和清洁度等方面的要求。
坡口应按照相关标准和设计要求进行设计和加工,确保焊接接头的质量和强度。
坡口的尺寸和形状要符合设计要求,并且保持一致性,以便于焊接作业。
在焊接前,必须清洁坡口,以去除油污、锈蚀和其他杂质,保证焊接的质量。
2.坡口角度焊接坡口加工中,坡口的角度是一个重要的参数。
坡口的角度决定了焊接接头的质量和强度。
不同类型的焊接接头需要不同的坡口角度。
一般来说,角焊缝的坡口角度通常为60度到70度,而者角焊缝的坡口角度通常为45度到60度。
确保坡口角度的准确性和一致性非常重要,以保证焊接接头的质量和强度。
3.坡口形状焊接坡口加工中,坡口的形状也是一个很重要的参数。
不同的焊接接头需要不同的坡口形状。
常见的坡口形状有V型坡口、X型坡口和U型坡口等。
坡口形状必须按照相关标准和设计要求进行设计和加工,以保证焊接接头的质量和强度。
不同的坡口形状会对焊接接头的质量和强度产生不同的影响,因此需要根据具体情况选择合适的坡口形状。
4.坡口尺寸焊接坡口加工中,坡口的尺寸也是一个重要的参数。
坡口的尺寸决定了焊接接头的质量和强度。
坡口尺寸应按照相关标准和设计要求进行设计和加工,以保证焊接接头的质量和强度。
坡口尺寸的准确性和一致性对于焊接接头的质量和强度非常重要。
在焊接坡口加工前,必须使用适当的测量工具进行测量,以确保坡口尺寸的准确性。
5.坡口清洁度焊接坡口加工中,坡口的清洁度也是一个重要的要求。
坡口必须保持清洁,以去除油污、锈蚀和其他杂质,确保焊接的质量。
在焊接坡口加工前,必须使用适当的清洁工具清洁坡口,以确保焊接接头的质量和强度。
只有保持良好的坡口清洁度,才能保证焊接接头的质量和强度。
总之,焊接坡口加工要求非常严格,包括坡口准备、坡口角度、坡口形状、坡口尺寸和坡口清洁度等方面的要求。
这些要求的严苛程度直接关系到焊接接头的质量和强度。
焊接坡口加工要求
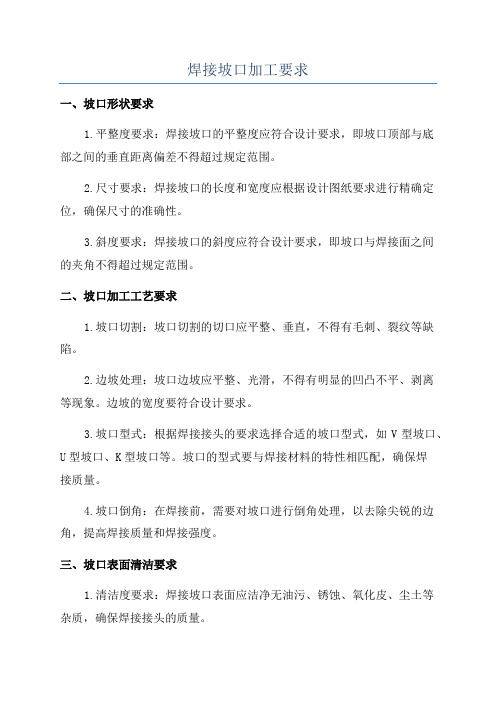
焊接坡口加工要求一、坡口形状要求1.平整度要求:焊接坡口的平整度应符合设计要求,即坡口顶部与底部之间的垂直距离偏差不得超过规定范围。
2.尺寸要求:焊接坡口的长度和宽度应根据设计图纸要求进行精确定位,确保尺寸的准确性。
3.斜度要求:焊接坡口的斜度应符合设计要求,即坡口与焊接面之间的夹角不得超过规定范围。
二、坡口加工工艺要求1.坡口切割:坡口切割的切口应平整、垂直,不得有毛刺、裂纹等缺陷。
2.边坡处理:坡口边坡应平整、光滑,不得有明显的凹凸不平、剥离等现象。
边坡的宽度要符合设计要求。
3.坡口型式:根据焊接接头的要求选择合适的坡口型式,如V型坡口、U型坡口、K型坡口等。
坡口的型式要与焊接材料的特性相匹配,确保焊接质量。
4.坡口倒角:在焊接前,需要对坡口进行倒角处理,以去除尖锐的边角,提高焊接质量和焊接强度。
三、坡口表面清洁要求1.清洁度要求:焊接坡口表面应洁净无油污、锈蚀、氧化皮、尘土等杂质,确保焊接接头的质量。
2.清洗方法:清洗方法可以采用机械清洗、化学清洗或喷砂等方法,具体根据焊接材料和坡口的特性来选择合适的方法进行清洗。
四、焊缝预留量要求1.焊缝预留量:在焊接坡口加工中,需要根据焊接材料和焊接方式,预先确定好焊缝的预留量,以确保焊接过程中的材料收缩和变形。
2.预留量计算:预留量的计算需要根据材料的热胀冷缩系数、变形系数、焊接方法和焊缝长度等参数进行计算,具体根据设计要求进行不同的计算。
总结起来,焊接坡口加工要求包括坡口形状要求、坡口加工工艺要求、坡口表面清洁要求和焊缝预留量要求等方面。
只有合理满足这些要求,才能保证焊接接头的质量和连接强度。
钢板焊接坡口尺寸标准
钢板焊接坡口尺寸标准
一、坡口类型与尺寸
1.根据焊接工艺要求和钢板材质,选择合适的坡口类型,如V型、U型、X型
等。
2.坡口尺寸应满足焊接要求,包括坡口宽度、深度、长度等。
二、坡口角度与间隙
1.坡口角度根据钢板厚度和焊接工艺要求确定,一般采用60°~75°的角度。
2.间隙应符合焊接工艺要求,一般控制在2~3mm之间。
三、钝边尺寸与间隙
1.钝边尺寸根据钢板厚度和焊接工艺要求确定,一般采用1~2mm的钝边。
2.间隙应控制在1~2mm之间,以保证焊接质量。
四、坡口表面质量与处理
1.坡口表面应无毛刺、飞边、油污等杂质。
2.坡口表面应进行清理和打磨,去除氧化膜、锈迹等杂质,保证焊接质量。
五、坡口装配与焊接顺序
1.按照焊接工艺要求进行坡口装配,保证对口质量。
2.焊接顺序应按照先焊立焊,再焊平焊,最后焊仰焊的顺序进行。
六、焊缝检验与质量控制
1.对焊缝进行外观检查,应无气孔、夹渣、裂纹等缺陷。
2.对焊缝进行无损检测,如射线探伤、超声波探伤等,以保证焊接质量。
七、坡口加工精度与公差要求
1.坡口加工精度应符合焊接工艺要求,一般控制在±0.5mm以内。
2.公差要求根据焊接工艺要求确定,一般控制在±1mm以内。
八、坡口安全要求与环境保护
1.操作人员应佩戴防护用品,如防护眼镜、手套等。
2.焊接时应注意防止火灾、烫伤等事故的发生。
3.焊接后应及时清理现场,防止对环境造成污染。
管道坡口打磨标准
管道坡口打磨标准
管道坡口打磨是确保管道焊接质量的关键步骤,其标准包括:
1. 坡口型式与尺寸:根据管道的材质、壁厚和焊接要求,选择相应的坡口型式(如V型、U型)和尺寸。
通常3mm-10mm的管壁选用V型坡口,而10mm以上的则选用U型坡口。
坡口的角度一般在45度到60度之间,具体角度和间隙尺寸应符合设计或工艺要求。
2. 坡口表面处理:采用机械方法(如管道坡口机)或热加工方法(如等离子弧、氧-乙炔焰)进行加工后,必须清除坡口表面的氧化皮、熔渣及影响接头质量的表面层。
凹凸不平处需打磨平整,确保坡口表明平整且无裂纹、重皮、毛刺等缺陷存在。
3. 坡口检验标准:坡口表面光洁无毛刺、坑洼、氧化皮、锈蚀等杂质;坡口尺寸和形状要符合设计图纸和技术标准的要求;坡口粗糙度应满足工艺要求,以保证管道高效输送和连接的紧密性。
需要注意的是,在实施坡口加工时,还需要考虑到材料的浪费问题,以及切割和打磨的精确性和效率,以优化工作流程并降低成本。
焊接坡口标准
焊接坡口标准焊接坡口是焊接工艺中的重要环节,其质量直接影响着焊接接头的牢固程度和密封性能。
因此,对于焊接坡口的标准化要求非常严格。
下面将就焊接坡口标准进行详细介绍。
首先,焊接坡口的几何形状应符合相关标准要求。
一般来说,焊接坡口的几何形状包括坡口角、坡口深度、坡口宽度等。
其中,坡口角是指两坡口面的夹角,其大小通常由具体的焊接工艺和焊接材料决定。
坡口深度是指坡口的开口到坡口底部的距离,其大小也需要根据具体的焊接要求来确定。
坡口宽度则是指坡口开口的宽度,同样需要根据具体情况来进行设计。
其次,焊接坡口的加工质量需符合相关标准要求。
焊接坡口的加工质量直接关系到焊接接头的质量。
在加工过程中,需要注意坡口表面的光洁度和平整度,以及坡口的角度和尺寸是否符合要求。
此外,还需要注意坡口的边缘是否存在裂纹、氧化、锈蚀等缺陷,这些缺陷都会对焊接接头的质量造成影响。
再次,焊接坡口的材料选择也是十分重要的。
在选择坡口材料时,需要考虑到坡口材料与焊接材料的相容性、热膨胀系数的匹配性等因素。
只有选择合适的坡口材料,才能确保焊接接头的牢固性和密封性。
最后,对于焊接坡口的焊接工艺也有一定的要求。
在进行焊接时,需要根据具体情况选择合适的焊接方法和焊接参数,以保证焊接接头的质量。
同时,还需要注意焊接过程中的预热、焊接速度、焊接层间温度控制等细节,以确保焊接接头的质量。
综上所述,焊接坡口标准对于焊接工艺具有重要的指导意义。
只有严格按照标准要求进行设计、加工和焊接,才能确保焊接接头的质量和可靠性。
因此,在实际生产中,需要严格遵守相关标准,不断提高焊接坡口的加工质量和焊接工艺水平,以满足不同工程项目的需求。
焊接坡口加工工艺指南坡口要这样开
焊接坡口加工工艺指南坡口要这样开一、坡口的定义和分类坡口是将要焊接的工件边缘加工成特定形状以满足焊接需要的加工方式。
坡口可以分为直角坡口、V型坡口、X型坡口、U型坡口、J型坡口等多种形式,根据不同的焊接要求和工件材料,选择合适的坡口加工方法是保证焊接质量的关键。
二、确定坡口类型和加工参数1.确定焊接方式:根据焊接工件的形状和工艺要求,确定适用的焊接方式,如手工焊接、自动焊接、半自动焊接等。
2.确定焊接材料:根据工件的材料和焊接要求,选择合适的焊接材料,如焊丝、焊条等。
3.确定坡口类型:根据工件的形状和焊接要求,选择合适的坡口类型,如V型坡口适用于对接焊,U型坡口适用于搭接焊等。
4.确定坡口尺寸:根据焊接要求,确定坡口的尺寸,包括坡口宽度、坡口深度等。
三、坡口的加工方法1.机械加工法:采用机械设备进行坡口加工,如铣床、刨床、钻床等。
适用于精密加工和批量生产。
2.手工加工法:采用手工工具进行坡口加工,如锉刀、锤子等。
适用于小型工件和少量生产。
3.火焰切割法:采用火焰切割设备进行坡口加工,如氧炔焊割设备。
适用于大型工件和特殊形状的坡口加工。
四、坡口加工的步骤1.准备工作:清理工件表面和坡口位置,确保无油污和杂质。
2.确定坡口位置:根据焊接要求,在工件上标记坡口位置,确保准确无误。
3.开启坡口:根据坡口类型和尺寸,选择适当的加工方法进行开口,保证坡口的平整度和一致性。
4.坡口整理:使用手工工具或机械设备对坡口进行整理和修整,确保坡口的光滑度和一致性。
5.清洁处理:清理坡口和焊接接头周围的污垢和杂质,确保焊接质量。
6.检查坡口质量:使用量具和目视检查等方式,检查坡口的尺寸和几何形状是否符合要求。
7.进行焊接:根据焊接工艺要求,进行焊接操作,保证焊接质量。
8.检查焊接质量:对焊接接头进行检测,如X射线检测、超声波检测等,确保焊缝的无缺陷和质量合格。
五、常见问题及解决方法1.坡口开口不均匀:检查开口刀具是否磨损,更换磨损刀具;调整加工参数,保证坡口的一致性。
- 1、下载文档前请自行甄别文档内容的完整性,平台不提供额外的编辑、内容补充、找答案等附加服务。
- 2、"仅部分预览"的文档,不可在线预览部分如存在完整性等问题,可反馈申请退款(可完整预览的文档不适用该条件!)。
- 3、如文档侵犯您的权益,请联系客服反馈,我们会尽快为您处理(人工客服工作时间:9:00-18:30)。
焊接坡口加工要求
1、大于16mm的钢板(不含16mm的钢板)可开双坡口,也可根据设计要求开坡口。
2、均采用半自动切割机切割坡口,严禁手工切割坡口。
坡口切割完毕后要检查板材的对角线误差值是否在规定的允许范围内。
如偏差过大,则要求进行修补。
3、坡口的允许偏差要求如下表:
4、坡口的加工方法可以采用磁力切割机沿管壁切割、采用半自动切割机在钢板上切割、采用坡口机切割钢板坡口。
卷管:
1、用CDW11HNC-50*2500型卷板机进行预弯和卷板。
2、根据实际情况进行多次往复卷制,采用靠模反复进行检验,以达到卷管的精度。
3、卷制成型后,进行点焊,点焊区域必须清除掉氧化铁等杂质,点焊高度不准超过坡口的2/3深度。
点焊长度应为80~100mm。
点焊的材料必须与正式焊接时用的焊接材料相一致。
4、卷板接口处的错边量必须小于板厚的10%,且不大于2mm。
如大于2mm,则要求进行再次卷制处理。
在卷制的过程中要严格控制错边量,以防止最后成型时出现错边量超差的现象。
5、上述过程结束后,方可从卷板机上卸下卷制成形的钢管。
焊接:
1、焊接材料必须按说明书中的要求进行烘干,焊条必须放置在焊条保温桶内,随用随取。
2、焊接时,焊工应遵守焊接工艺规程,不得自由施焊,不得在焊道外的母材上引弧。
3、焊接时,不得使用药皮脱落或焊芯生锈的焊条和受潮结块的焊剂及已熔烧过的渣壳。
4、焊丝在使用前应清除油污、铁锈。
5、焊条和焊剂,使用前应按产品说明书规定的烘焙时间和温度进行烘焙。
保护气体的纯度应符合焊接工艺评定的要求。
低氢型焊条经烘焙后应放入保温筒内,随用随取。
6、焊前必须按施工图和工艺文件检查坡口尺寸、根部间隙,焊接前必须清除焊接区的有害物。
7、埋弧焊及用低氢焊条焊接的构件,焊接区及两侧必须清除铁锈、氧化皮等影响焊接质量的脏物。
清除定位焊的熔渣和飞溅;熔透焊缝背面必须清除影响焊透的焊瘤、熔渣,焊根。
8、焊缝出现裂纹时,焊工不得擅自处理,应查出原因,制定出修补工艺后方可处理。
9、焊缝同一部位的返修次数,不宜超过两次;当超过两次时,应按专门制定的返修工艺进行返修。
探伤检验:
1、单节钢管卷制、焊接完成后要进行探伤检验。
焊缝质量等级及缺陷分级应符合设计指导书中规定的《钢结构工程施工质量验收规范》的规定执行。
2、要求局部探伤的焊缝,有不允许的缺陷时,应在该缺陷两端的延伸部位增加探伤长度,增加的长度不应小于该焊缝长度的10%,且不应小于200mm;当仍有不允许
的缺陷时,应对该焊缝100%探伤检查。
矫圆:
1、由于焊接过程中可能会造成局部失圆,故焊接完毕后要进行圆度检验,不合格者要进行矫圆。
2、将需矫圆者放入卷板机内重新矫圆,或采用矫圆器进行矫圆。
矫圆器可以根据实际管径自制,采用丝杆顶弯。
组装和焊接环缝:
圆管加工工艺:
1、卷管前应根据工艺要求对零件和部件进行检查,合格后方可进行卷管。
卷管前将钢板上的毛刺、污垢、松动铁锈等杂物清除干净后方可卷管。
2、对于>30mm的钢板在零件下料时根据具体情况,在零件的相关方向增加引板。
其引板的长度一般为50~100mm。
3、卷管加工
1)一般卷管工艺流程图
2)卷管加工工艺流程说明
下料:
1、以管中径计算周长,下料时加2mm的横缝焊接收缩余量。
长度方向按每道环缝加2mm的焊接收缩余量。
2、采用半自动切割机切割,严禁手工切割。
3、切割的尺寸精度要求如下表:
开坡口:
1、一般情况下,16mm以下的钢板均采用单坡口的形式,外坡口和内坡口两种形式均可。
出于焊接方面的考虑,一般开外坡口,内部清根后焊接。
1、根据构件要求的长度进行组装,先将两节组装一大节,焊接环缝。
2、环缝采用焊接中心来进行,卷好的钢管必须放置在焊接滚轮架上进行,滚轮架采用无级变速,以适应不同的板厚、坡口、管径所需的焊接速度。
3、组装必须保证接口的错边量。
一般情况下,组装安排在滚轮架上进行曲,以调节接口的错边量。
4、接口的间隙控制在2~3mm,然后点焊。
5、环缝焊接时一般先焊接内坡口,在外部清根。
采用自动焊接时,在外部用一段曲率等同外径的槽钢来容纳焊剂,以便形成焊剂垫。
6、根据不同的板厚、运转速度来选择焊接参数。
单面焊双面成型最关键是在打底焊接上。
焊后从外部检验,如有个别成型不好或根部熔合不好,可采用碳弧气刨刨削,然后磨掉碳弧气刨形成的渗碳层,反面盖面焊接或埋弧焊(双坡口要进行外部埋弧焊)。
7、焊接完毕后进行探伤检验,要求同前。
清理、编号:
1、清理掉一切飞溅、杂物等。
对临时性的工装点焊接疤痕等要彻底清除。
2、在端部进行喷号,构件编号要清晰、位置要明确,以便进行成品管理。
3、构件上要用红色油漆标注X-X和Y-Y两个方向的中心线标记。
钢构件组装允许偏差应符合国家标准《钢结构工程施工质量验收规范》(GB50205—2001)的要求。