方坯连铸机高效改造工作总结
连铸工程工作总结

厚板坯连铸工程14年度总结宝钢厚板坯连铸工程自2012年开工以来,在总包项目部的领导下,通过项目部全体成员的共同努力,在原有的基础上克服整个项目工期紧、施工技术要求高、场地狭小施工作业面少、交通不利、施工组织难度大等诸多困难,确保了工程顺利进行,在保证质量的同时于14年12月12日提前工期18天投入生产,得到了总包和业主的赞誉。
新建连铸厂房长262m,宽199m,是一个不规侧的厂房。
主厂房建筑面积近29177 m2。
厂房由高54 .5 m左右的浇注跨分三层向纬三路逐渐降至22 m高的精整跨 (见连铸厂房剖面图) 。
最长的屋面瓦约80 m,一般瓦长在60 m左右。
在此区间内有二条冲沟分别在-6 m 以下穿越板坯辊道,在Ea列14线处-10 m穿越主厂区。
另有二条电缆沟,二条液压管廊分别穿越和围绕连铸浇注机基础。
连铸机基础挖土深度为-7.5 m,基础顶部标高14.20 m。
在-4.5m处有2条蒸气管廊在Ba列9线与之连接,连铸机的辊道长度约260 m,分布在厂房的东、北侧。
在厂房Ea列外是连铸水处理系统,它是有三个直经分别为φ16 m、φ23 m×2的圆池组成。
连铸外围工程有空压站、宏观试验室和辊子堆焊间三部分工程组成。
空压站土建工程为单层框架结构,基础均为独立柱基础,建筑面积为975m2。
其中空压站主厂房为全钢结构,墙皮、屋面均采用压型金属板作为围护;电气室为钢砼结构。
宏观试验室土建工程为单层框架结构,基础均为独立柱基础,建筑面积为975m2。
宝钢厚板坯连铸工程辊子堆焊间设备基础位于原生产车间厂房内。
连铸工程自进入2014年后主体工程大部分都已进入收尾阶段,主要任务是主厂房建筑施工及配合专业组织施工、实物交接和软件资料交工。
连铸工程的特点是厂房面积大单位工程多,面积达3万多平米,分布着10个单位工程,并且还有一系列的外围工程,但是项目部克服诸多困难,精心组织收尾的施工队伍,详细细化收尾节点,认真落实每一项安排,按时或提前完成节点。
年度总结钢厂连铸的(3篇)
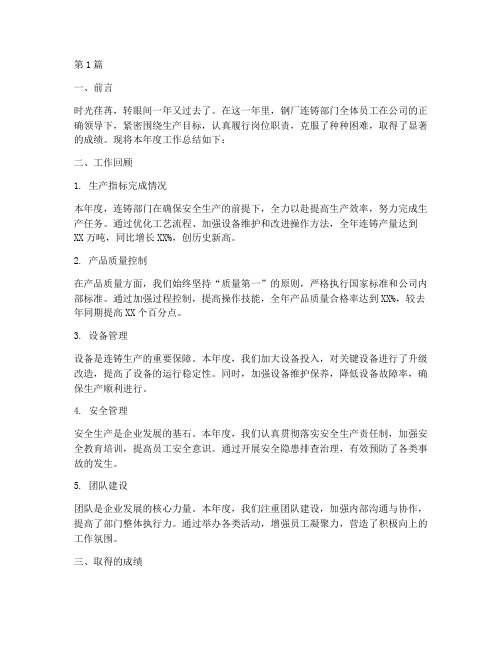
第1篇一、前言时光荏苒,转眼间一年又过去了。
在这一年里,钢厂连铸部门全体员工在公司的正确领导下,紧密围绕生产目标,认真履行岗位职责,克服了种种困难,取得了显著的成绩。
现将本年度工作总结如下:二、工作回顾1. 生产指标完成情况本年度,连铸部门在确保安全生产的前提下,全力以赴提高生产效率,努力完成生产任务。
通过优化工艺流程、加强设备维护和改进操作方法,全年连铸产量达到XX万吨,同比增长XX%,创历史新高。
2. 产品质量控制在产品质量方面,我们始终坚持“质量第一”的原则,严格执行国家标准和公司内部标准。
通过加强过程控制,提高操作技能,全年产品质量合格率达到XX%,较去年同期提高XX个百分点。
3. 设备管理设备是连铸生产的重要保障。
本年度,我们加大设备投入,对关键设备进行了升级改造,提高了设备的运行稳定性。
同时,加强设备维护保养,降低设备故障率,确保生产顺利进行。
4. 安全管理安全生产是企业发展的基石。
本年度,我们认真贯彻落实安全生产责任制,加强安全教育培训,提高员工安全意识。
通过开展安全隐患排查治理,有效预防了各类事故的发生。
5. 团队建设团队是企业发展的核心力量。
本年度,我们注重团队建设,加强内部沟通与协作,提高了部门整体执行力。
通过举办各类活动,增强员工凝聚力,营造了积极向上的工作氛围。
三、取得的成绩1. 连铸产量创历史新高,为公司创造了良好的经济效益。
2. 产品质量得到有效提升,客户满意度不断提高。
3. 设备管理水平得到加强,设备故障率明显降低。
4. 安全生产形势稳定,未发生重大安全事故。
5. 团队凝聚力增强,员工素质得到提高。
四、不足与改进1. 生产效率仍有提升空间,需进一步优化工艺流程。
2. 部分员工操作技能有待提高,需加强培训。
3. 设备维护保养工作需加强,降低设备故障率。
4. 安全生产意识需进一步加强,提高全员安全意识。
五、展望展望未来,我们将继续坚持以安全生产为基础,以提高生产效率、提升产品质量为目标,加强团队建设,努力实现以下目标:1. 优化工艺流程,提高生产效率。
连铸改造完成情况汇报

连铸改造完成情况汇报尊敬的领导:我向您汇报连铸改造完成情况如下:一、项目背景。
公司连铸设备已运行多年,存在一定的老化和磨损,为提高生产效率和产品质量,公司决定进行连铸改造项目。
二、改造内容。
1. 设备更新,更换老化设备,引进先进的连铸设备,提高生产效率和产品质量。
2. 工艺优化,优化连铸工艺,提高产品成形率,减少废品率。
3. 自动化控制,引入自动化控制系统,提高生产线的智能化水平,减少人为操作对产品质量的影响。
三、改造进展。
1. 设备更新,目前已完成设备更新的采购工作,新设备已陆续到货并开始安装调试。
2. 工艺优化,优化工艺方案已经制定完成,正在进行试验验证,初步效果良好。
3. 自动化控制,自动化控制系统已经完成采购和安装,正在进行联调测试,预计很快可以投入使用。
四、改造效果。
1. 设备更新,新设备的安装调试工作进展顺利,预计可以在规定时间内完成,提高了生产线的稳定性和可靠性。
2. 工艺优化,优化后的工艺方案有效提高了产品成形率,减少了废品率,产品质量得到了明显提升。
3. 自动化控制,自动化控制系统的引入大大减少了人为操作,提高了生产线的智能化水平,降低了人力成本,提高了生产效率。
五、下一步工作。
1. 完成设备更新的安装调试工作,确保新设备的正常运行。
2. 进一步优化工艺方案,提高产品质量和生产效率。
3. 完成自动化控制系统的联调测试,确保系统稳定可靠,投入正常生产使用。
六、结语。
连铸改造项目是公司生产线升级的重要举措,经过各部门的通力合作,项目进展顺利,效果显著。
我们将继续努力,确保项目顺利完成,为公司的发展贡献力量。
谢谢!。
连铸工作中的改进方案和总结
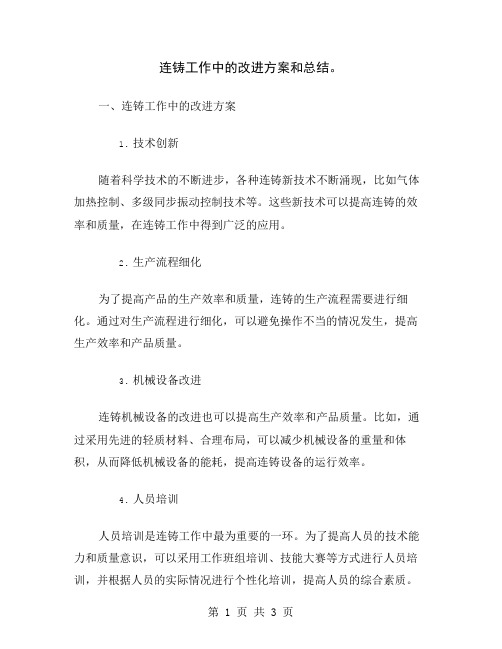
连铸工作中的改进方案和总结。
一、连铸工作中的改进方案1.技术创新随着科学技术的不断进步,各种连铸新技术不断涌现,比如气体加热控制、多级同步振动控制技术等。
这些新技术可以提高连铸的效率和质量,在连铸工作中得到广泛的应用。
2.生产流程细化为了提高产品的生产效率和质量,连铸的生产流程需要进行细化。
通过对生产流程进行细化,可以避免操作不当的情况发生,提高生产效率和产品质量。
3.机械设备改进连铸机械设备的改进也可以提高生产效率和产品质量。
比如,通过采用先进的轻质材料、合理布局,可以减少机械设备的重量和体积,从而降低机械设备的能耗,提高连铸设备的运行效率。
4.人员培训人员培训是连铸工作中最为重要的一环。
为了提高人员的技术能力和质量意识,可以采用工作班组培训、技能大赛等方式进行人员培训,并根据人员的实际情况进行个性化培训,提高人员的综合素质。
二、连铸工作中的总结1.高品质的原材料在连铸工作中,高品质的原材料是保证产品质量的基础。
因此,在原材料采购时,一定要选择质量好、纯度高的原材料。
2.加强管理和监控为了确保连铸工作的正常进行,必须要加强对生产过程的管理和监控。
通过实时监测,可以及时发现和解决生产过程中的问题,避免问题扩大并影响生产效率和产品质量。
3.用先进技术提升质量为了确保连铸生产的高效率和高质量,必须使用先进技术。
只有掌握了先进技术,才能不断提升连铸生产的效率和质量。
4.确保生产安全安全是连铸工作中最为重要的一环。
为了确保生产过程的安全,必须严格遵守生产规程,在工作过程中注意安全,提高员工的安全意识,加强设备的安全保障。
连铸工作中的改进方案和总结可以提高生产效率和产品质量,以适应市场需求的不断增长。
通过不断探索和发展,连铸技术和生产工艺将会得到更加广泛的应用,为实现精准制造和高质量发展做出贡献。
小方坯连铸机结晶器高效化改造与实践

(铸 机 曲率半 径 : 5 m; 1 ) 520m
4 原结晶器工艺结构及参数分析
41 铜管支撑和固定方式 . 原结晶器总称为卡板式结构 , 因设计时间较早 , 随着二炼钢对连铸的要求愈来愈高, 逐渐显示 出其
(铸坯断面:2 m× 2 l ; 2 ) 10m 10nn / (设计拉速 :. 32m mn 3 ) 28— . / i;
影响铸坯质量和结晶器铜管使用寿命。
4 2 水 套形式 .
内水 套 为直 角 四板 对 焊结 构 , 于 1小方 坯 而 对
现用 结 晶器 冷却 水压 较低 , 量偏 小 , 能满足 水 不
言, 随着拉坯速度 的提高 ( . 4 0m mn , 3 8— . / i) 热交 换也随之加快 , 就要求 内水套 内的水速 、 水量能满足 铸坯在结晶器 内的过热、 热、 潜 显热 与水 的交换平
现用水缝宽度和水速均不 能满 足生产工艺要 求, 在同等条件下, 水缝宽 ( 4m ) 流速慢 ( 2 > m , <1 m s )进 出水温差大 ( 7o ) 有 可能使铜管冷 /e , e > c , 面温度超过 10℃ , 0 出现水 的核沸腾现象 , 造成铜管
永久 性变形 。
-) 机流 数 : (铸 4 四机 四流 。
2021年连铸工作总结

2021年连铸工作总结
2021年,是连铸工作的关键一年。
在全球疫情的影响下,连铸行业面临着前所未有的挑战和机遇。
在这一年里,我们经历了各种困难和挑战,但也取得了一定的成绩和进步。
首先,我们在技术创新方面取得了一定的突破。
通过不断的研发和改进,我们
成功地开发了一系列新型连铸设备,并在生产中进行了应用。
这些设备不仅提高了生产效率,还大大降低了能耗和原材料的浪费,为企业节约了大量成本,提高了竞争力。
其次,我们在质量控制方面取得了显著的进步。
通过引进先进的质量管理体系
和技术手段,我们成功地提高了产品的质量稳定性和一致性,为客户提供了更加可靠的产品和服务。
同时,我们还加强了质量监督和检测力度,确保了产品符合国家标准和客户需求。
另外,我们在环保方面也取得了一定的成绩。
通过引进先进的环保设备和技术,我们成功地降低了排放物的含量和排放量,减少了对环境的污染,为可持续发展做出了积极的贡献。
当然,我们也面临着一些问题和挑战。
比如,原材料价格的上涨、人工成本的
增加、市场竞争的加剧等,都给企业的发展带来了一定的压力。
但我们相信,在各级领导的正确领导下,我们一定能够克服这些困难,迎接更大的挑战。
总的来说,2021年是连铸工作的一年,我们在技术创新、质量控制、环保等方面都取得了一定的成绩和进步。
同时,我们也清醒地认识到了自身存在的问题和不足,将会在未来的工作中加以改进和完善。
相信在全体员工的共同努力下,我们一定能够取得更大的成绩,迎接更大的挑战。
连铸工作总结

连铸工作总结连铸工作总结一、工作目标和任务作为连铸工作的负责人,我的主要工作目标和任务是确保生产过程中的连铸设备的正常运转,并且保证生产出的铸坯质量达到要求。
在工作初期,我与我的团队一起仔细研究了生产计划,制定了合理的生产安排和工作流程,并制定了规范的工作指导书。
二、工作进展和完成情况在工作过程中,我们认真监控了整个生产过程,确保设备运转正常并按时完成生产任务。
我们采取了多种措施,如定期维护设备、清洗焊缝、检查电缆和设备接头,对设备进行全面的保养和维护。
在生产过程中,我们也遇到了一些困难和问题。
由于生产计划的不确定性,我们需要根据具体情况进行调整,维护设备的工作也需要安排得当。
同时,在产品质量方面,我们也需要注意每个细节,确保低碳铸坯的超薄宽度一致性,同时尽可能降低残余应力,确保铸坯的良好成形。
在生产任务完成后,我们进行了全面的验收,并通过实际检验,我们的生产效率的确提高了许多。
我们成功地将连铸工作的工作质量和效率推向了一个新的高峰。
三、工作难点及问题在连铸工作的过程中,我们遇到的最大的问题在于生产计划的不确定性。
这也是我们遇到的最大的困难。
在确定生产计划方面,我们需要仔细分析生产过程中的各个环节,找到关键节点,同时确保设备和工艺的连续性。
在生产过程中,我们还会遇到一些意外情况,比如设备故障和维修费用,我们需要有备无患,备好足够的维修资金,并且对设备进行定期的保养维护,以减少不必要的损失。
四、工作质量和压力在保证设备和工艺的连续性的同时,我们还需要随时关注生产过程中的各个环节,并确保超薄宽度铸坯的成形和质量。
随着产品标准的不断提高,我们面临的压力也越来越大。
我们的工作质量和压力是紧密相关的,必须在时间紧迫和高质量的压力下工作。
五、工作经验和教训在连铸工作的过程中,我们积累了许多经验和教训。
我们意识到了在生产计划和设备维修方面的重要性,这也使我们对其他公司的连铸工作更加优秀。
另外,我们也意识到了必须不断提高自己的能力和独立解决问题的能力。
连铸半年工作总结
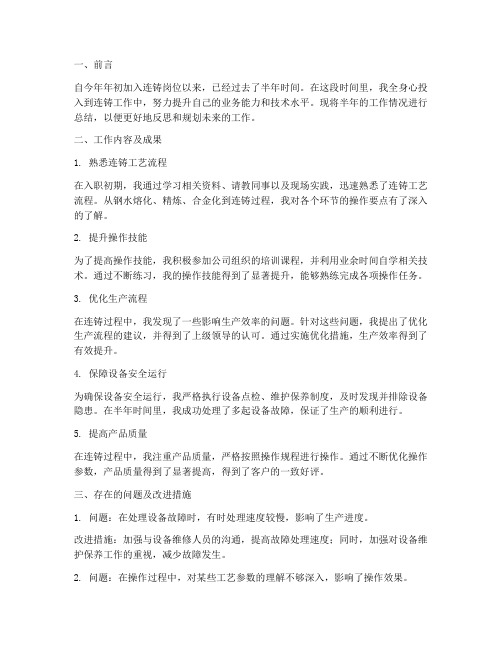
一、前言自今年年初加入连铸岗位以来,已经过去了半年时间。
在这段时间里,我全身心投入到连铸工作中,努力提升自己的业务能力和技术水平。
现将半年的工作情况进行总结,以便更好地反思和规划未来的工作。
二、工作内容及成果1. 熟悉连铸工艺流程在入职初期,我通过学习相关资料、请教同事以及现场实践,迅速熟悉了连铸工艺流程。
从钢水熔化、精炼、合金化到连铸过程,我对各个环节的操作要点有了深入的了解。
2. 提升操作技能为了提高操作技能,我积极参加公司组织的培训课程,并利用业余时间自学相关技术。
通过不断练习,我的操作技能得到了显著提升,能够熟练完成各项操作任务。
3. 优化生产流程在连铸过程中,我发现了一些影响生产效率的问题。
针对这些问题,我提出了优化生产流程的建议,并得到了上级领导的认可。
通过实施优化措施,生产效率得到了有效提升。
4. 保障设备安全运行为确保设备安全运行,我严格执行设备点检、维护保养制度,及时发现并排除设备隐患。
在半年时间里,我成功处理了多起设备故障,保证了生产的顺利进行。
5. 提高产品质量在连铸过程中,我注重产品质量,严格按照操作规程进行操作。
通过不断优化操作参数,产品质量得到了显著提高,得到了客户的一致好评。
三、存在的问题及改进措施1. 问题:在处理设备故障时,有时处理速度较慢,影响了生产进度。
改进措施:加强与设备维修人员的沟通,提高故障处理速度;同时,加强对设备维护保养工作的重视,减少故障发生。
2. 问题:在操作过程中,对某些工艺参数的理解不够深入,影响了操作效果。
改进措施:继续深入学习相关理论知识,提高对工艺参数的理解;在实际操作中,多向有经验的同事请教,不断积累实践经验。
3. 问题:与同事之间的沟通协作不够顺畅。
改进措施:加强团队协作意识,主动与同事沟通交流,共同提高工作效率。
四、总结回顾过去半年,我在连铸岗位上取得了一定的成绩,但也存在一些不足。
在今后的工作中,我将继续努力,不断提高自己的业务能力和技术水平,为公司的发展贡献自己的力量。
- 1、下载文档前请自行甄别文档内容的完整性,平台不提供额外的编辑、内容补充、找答案等附加服务。
- 2、"仅部分预览"的文档,不可在线预览部分如存在完整性等问题,可反馈申请退款(可完整预览的文档不适用该条件!)。
- 3、如文档侵犯您的权益,请联系客服反馈,我们会尽快为您处理(人工客服工作时间:9:00-18:30)。
第二炼钢厂方坯连铸机高效化改造工作总结安钢第二炼钢厂2006年5月8日第二炼钢厂方坯连铸机高效化改造工作总结第二炼钢厂现有3座公称容量20吨的氧气顶吹转炉,一台R6m 半径120×120mm2小方坯连铸机,两台R5.25m半径120×120mm2的小方坯连铸机,一台基本半径R5.7m1050×150 mm2超低头板坯连铸机和一台半径R6m两流180×260 mm2的矩形坯连铸机。
2004年二炼钢产钢210万吨,分别为第一轧钢厂,第二轧钢厂、第三轧钢厂、第四轧钢厂提供坯料。
1、方坯高效改造的必要性1.1 二炼产能平衡的需要二炼钢的年产钢量210万吨,三台方坯约年产钢165万吨左右,随着公司“三步走”战略第二步的完成,三轧、无缝的关停,5#矩形坯连铸机必然被停产;随着二炼轧的投产和一炼轧产能的发挥,板坯坯料过剩的供求矛盾日益显现,二炼4#板坯连铸机生产小规格连铸坯的调剂作用不大,不需批量组织生产,年产量很少;公司对二炼的坯料需求几乎全转向了小方坯生产,为此必须提高目前三台方坯的生产能力,实现炉机匹配,将现有的13.7万吨/流的产量提高到16万吨/流以上,确保二炼钢的经济效益和产品质量实现新跨越,保证公司的“三步走”战略顺利实施。
1.2 二炼钢进一步降本增效和优化各项指标需要。
转炉与连铸生产工艺不匹配,制约了低成本生产目标的实现,为保证连铸浇注温度,在无炉外钢水加热设施的条件下,只能采用提高转炉出钢温度的方式来弥补浇钢过程盛钢桶的热损失,此种工艺保证了生产顺行,但却降低了转炉、盛钢桶、中间包使用寿命及金属收得率和连铸技术经济指标,造成了连铸生产的低效率、高消耗;而且转炉、盛钢桶、中间包被浸蚀掉的大量耐火材料严重污染了钢水,使铸坯质量恶化,因而必须通过方坯高效化改造,三炉对三台方坯炉机匹配,进一步降低生产成本、优化各项指标。
根据国内有关报道(见表1)其高效后其综合效益为30-87元/吨钢。
表1 高效连铸综合经济效益(冶金丛刊,2002.3)1.3 生产顺行的需要。
目前我厂生产模式为三炉对四机,由于炉机的不匹配,造成生产调度复杂性高,工艺制度的执行无法保证,连铸生产事故较高,有时铸机的漏钢率达0.97%。
实现炉机匹配后,生产模式简单化,钢水温度、衔接时间都可以得到保证,漏钢率降低至0.4%(济钢120×120mm2,0.32%;南昌钢厂120×120mm2,150×150mm2,0.301%)以下,从而确保了生产的顺行。
1.4 提高铸坯质量的需要高效连铸机的实现是依靠整个炼钢系统的系统优化,其是建立在钢水的较低过热度和良好的可浇注性、操作的标准化、优化和完善的铸机设备、严格的工艺纪律、稳定的生产调度组织基础上的,从而有利于铸坯质量的控制,大幅度提高铸坯的表面和内部质量。
因而必须对现有的3台120mm×120mm的方坯连铸机进行高效化的设备改造和工艺优化,使其具备炉机匹配的生产条件,最终实现二炼钢全厂炉机匹配的最佳生产组织模式,从而实现生产组织的最优化、消耗和成本的最低化、技术经济指标的最佳化、经济效益的最大化,为公司的经济效益增长发挥积极作用。
2、第二炼钢厂三台方坯连铸机主要工艺参数第二炼钢厂三台方坯连铸机主要工艺参数见表2。
生产的主要钢种:普碳钢Q215系列、Q235系列、船角A、45#等;低合金钢HRB335、HRB400、Q345、Q295系列、27MnSi、船角B等;低碳钢包括:Q195系列、C7D等。
3、高效化改造前存在的问题3.1中间包中间包为矩形包,中间包型状较长、较窄容量偏小,在浇注过程中钢包钢水注流对中间包水口和包壁较近,对中间包注流产生扰动,同时对外壁的冲刷侵蚀严重,影响包龄寿命; 1#、3#包的高度低只有700mm,钢液在中间包内的停留时间短,夹杂物不容易上浮,也不利于钢水的衔接,特别是提高拉速后,造成中间包下渣,从而形成铸坯的加杂物缺陷,甚至造成夹杂漏钢。
3.2结晶器工艺参数不合理,见表3结晶器工艺参数不合理,结晶器铜管长度812.8mm,长度短,拉速只能控制在2.5~3.2m/min,限制铸机拉速的提高,使用寿命短,结晶器漏钢事故多,铸坯质量难以保证。
铜管壁薄,水套用四块钢板焊接而成,存在扭曲变形,制作和安装精度难以保证工艺要求,采用的定距螺栓为普通螺栓,容易生锈和捋丝,保证不了水缝的宽度均匀,造成铸坯菱变和角部裂纹,增加角裂漏钢的发生。
特别是漏钢一度成为制约方坯连铸机增产降耗的主要因素,直接导致拉速下降,注流断浇,延长备机时间,降低铸机作业率。
这就限制铸坯质量和产量的进一步提高,已成为方坯质量、产量上台阶一个瓶颈。
作为连铸机的“心脏”的结晶器的设计必须得到优化,从而与高质量产品、低操作成本和严格的生产周期相适应。
另外结晶器冷却水压力低,不能保证高拉速对结晶器冷却水量的要求。
3.3振动装置由于振动参数和振动运行不平稳造成生产操作难度大、生产事故多,具体来讲:1)振幅、拉速与振频关系不合理:2)振动偏摆量大:表3 改造前结晶器主要工艺技术参数项目原用主要工艺技术参数1#机2#机3#机铜管长度812.8mm 800mm 812.8mm铜管锥度 1.0%m 0.5~0.7%m 1.0%m内腔形状抛物线型抛物线型抛物线型铜管壁厚10mm 10mm 10mm铜管内圆角R6 R8 R6铜管材质磷脱氧铜磷脱氧铜磷脱氧铜冷却水量100~110 m³/h 8 0~90 m³/h 100~110 m³/h进水压力0.55~0.65Mpa 0.55~0.65Mpa 0.55~0.65Mpa水缝宽度4mm 4mm 4mm水缝流速8~10m/s 8~10m/s 8~10m/s水套结构钢板直角焊接钢板直角焊接钢板直角焊接固定方式上口侧端卡板上法兰压紧上口侧端卡板3.4二冷系统(1)三台方坯的二冷系统只有一个冷却段,二冷冷却段短,冷却长度1#方坯2.1m,2#方坯1.8 m,3#方坯2m。
二冷控制上部冷却强度大,下部没有冷却,铸坯回温严重,存在中间裂纹、中心裂纹、矫直裂纹。
内部质量见表4。
(2)喷嘴距铸坯的距离四面不等,铸坯冷却不均匀。
(3)二冷竖管上部供水,在换包总是引起下部变形,变形后必须进行更换,二冷竖管消耗高。
(4)浊水泵房设备老化,三台铸机同时生产,二冷水压仅有0.55~0.65Mpa,单流最大水量33t/h。
拉速大于3.2m/min后,水量偏小,造成铸坯缩孔严重,同时铸坯带液芯矫直,易于生成矫直裂纹。
(5)流量电磁控制阀故障多,特别是到夏季,因温度高,利用率更低,为避免影响正常生产,一般使用手动配水,铸坯质量难以保证。
4、高效改造的原则1)不能影响正常生产,改造以有序稳定、稳产、高效、低耗为目的,通过减少连铸的各类事故及故障,实现铸机拉速的提高,满足一炉配一机的生产组织模式。
2)结合我厂实际情况,以改造关键工艺技术为基础,对连铸机进行系统改造。
选用工艺先进,技术成熟的工艺设备,保证改造后设备故障少,提高铸机作业率和台时产量。
3)在保证改造后先进性、适用性前提下,尽量减少改造成本。
4)满足普碳钢、优质碳素结构钢、低合金钢等多钢种高拉速、高质量、高作业率、高连浇率的要求,同时降低备件与耐火材料消耗。
5、高效改造目标1)工作拉坯速度3.3~3.8m/min,最高拉速4.0m/min。
2)方坯铸机溢漏率<0.3%3)铸坯内部质量,中间裂纹:≤1.0级比例≥70%,≤2.0级比例≤30%中心裂纹:≤1.0级比例≥80%,≤2.0级比例≤20%缩孔≤2.0级比例≥80%3)铸坯合格率>95%。
6、高效改造的工艺方案(1)系统规划,分步实施。
(2)解决主要矛盾。
1)结晶器铜管采用850mm长,壁厚为12mm,圆角6mm,抛物线(或多锥度)形式。
水缝4mm,水套为整体冲压不锈钢圆角形式,水速12m/s。
2)振动装置采用半板簧振动,振幅4-6mm,振频0-240 次/min,振动参数优化。
3)二次冷却系统分为3段,比水量1.5-2.5,自动配水,采用原模型和比例控制形式,二冷参数优化。
4)辅助方坯二冷浊水泵房改造。
7、改造方案的实施及主要技术措施:7.1 中间包改造由长方形中间包改为深溶池梯形中间包,满足钢包合理浇注,减小了钢包注流对中间包流的冲击影响,保证了中间包注流的稳定浇注,提高中间包使用寿命。
钢水在中间包内停留时间12min左右,有利于促进钢中夹杂物上浮,同时有利于实现多炉连浇。
据统计中间包(干式包)平均寿命由2004年的平均115炉,提高到现在的154炉,最高包龄达到236炉,创造了单包浇注超过80小时的国际先进水平。
7.2温度制度的修改高效连铸与普通连铸相比对钢水的温度要求更加严格,低温浇注并严格控制钢水过热度是减少事故,实现高效连铸的前提。
为满足方坯高效连铸的需要,对第二炼钢厂的温度制度进行了多次适意性的修改,保证我厂方坯连铸机钢水过热度为10~20℃。
7.3结晶器高效改造要实现连铸的高效化,必须有相关的技术支撑,高效连铸的关键技术---高冷却强度的,导热均匀的长寿结晶器总成。
7.3.1结晶器特性参数优化高效改造后的结晶器主要工艺技术参数见表51)优化结晶器铜管长度,加长至850mm,有利于延长凝固壳在结晶器内的停留时间,增大出结晶器坯壳的厚度,减少漏钢。
2)优化铜管倒锥度,结晶器铜管的倒锥度0.7~0.8%/m,采用三锥度抛物线,使其内腔尺寸更趋符合高拉速下结晶器传热曲线。
3)优化铜管材质,铜管材质选用含磷Cu—Ag合金,具有良好的导热性、抗变形能力,较高的硬度及耐磨性,有效提高了铜管的使用寿命。
4)优化铜管厚度,铜管壁厚增至12mm和12.5mm,可有效提高铜管强度。
表5 高效改造后结晶器主要工艺技术参数项目原用主要工艺技术参数1#机2#机3#机铜管长度850mm 850mm 850mm铜管锥度0.7~0.8%m 0.7~0.8%m 0.7~0.8%m内腔形状抛物线型抛物线型抛物线型铜管壁厚12mm 12.5mm 12mm铜管内圆角R6 R6 R6铜管材质含磷银铜合金含磷银铜合金磷脱氧铜冷却水量110~120 m³/h 110~120 m³/h 110~120 m³/h进水压力0.75~0.85Mpa 0.75~0.85Mpa 0.75~0.85Mpa水缝宽度 3.5mm 3.5mm 3.5mm水缝流速12~15m/s 12~15m/s 12~15m/s水套结构整体冲压圆角不锈钢整体冲压圆角不锈钢整体冲压圆角不锈钢固定方式上法兰压紧铜管上翻边上口侧端卡板5) 优化铜管固定支撑方式1#机采用顶端密封,2#机采用上口翻边结晶器铜管,3#机采用特殊的密封结构,使结晶器的安装精度达到理想水平。