外圆磨削中常见缺陷的产生原因及消除方法
外圆切削的常见问题及解决方法

削瘤 , 善零件表面 光洁度的主要 方法 。 改
砂 轮 气 孔 的 铝 及 铝 合 金 等 工 件 , 细 车 的 精 优 点 更 为 明 显 。 加 工 大 型 精 密外 圆表 面 在
2 车 削时圆度难控制
车 削 过 程 中 零 件 外 圆 椭 圆 度 大 , 度 圆 紧 ; 刀磨 损 , 头不 利 , 车 刀 崩刀 , 口有 缺 口; 刃
精 细 车 的 特 点 是 背 吃 刀量 和 进 给 量 取 情 况 就 更 为 明 显 。 当然 , 面 出现 切 削 瘤 的 表 值极 小 , 削 速 度 高达 1 0 0 0 /ri 。 切 5 ~2 0 m a n
精 细 车 一 般 采 用立 方 氨化 硼 ( N)金 刚 石 CB 、
卡 盘 有 明显 松 动 时 , 打 开 床 头 箱 , 空 则 挂 挡 , 整 主 轴 前 轴 承 的 松 紧度 , 百 分 表检 调 用
样 对 车 削 后 零 件 的 形 位 尺 寸 , 面 光 洁 度 查 , 制 主 轴 的 径 向 间隙 , 表 控 同时 检 查 主 轴后 产 生 影 响 。 刀 刃磨 不 合 理 、 刀损 坏 或 磨 轴 承 的 松 紧 度 , 整 控 制 后 轴 承 的 并 帽 螺 车 车 调 钝 都 很 容 易 产 生 切 削 瘤 。 果 刀 具 选 择 不 母 , 手 旋 转 卡 盘 , 主 轴 转 动 合 理 , 如 用 让 百分 合 理 , 容 易 崩 刀 , 削 过 程 中 有 无 切 削 表检 查 , 制 主 轴 的 轴 向 间隙 , 样 就 可 以 则 车 控 这 液 , 种 切 削 液 , 度 是 否 合 适 , 削 后 的 解 决 因 为 主轴 松 动 引 起 车 削 过 程 中 发 生 的 何 浓 车 避 零 件 表 面 光 洁 度 就 会 不 一 样 , 车 时 这 种 异 常 震 动 , 免 工 件 径 向 和 轴 向 窜 动 所 产 精 生 的震 纹 。 果 床 头 箱 内 的 齿 轮 严 重 磨 损 , 如 啮 合 间 隙无 法 调 整 , 需 要 更 换 齿 轮 , 则 使得 主 要 原 因 是 因 为车 刀不 锋利 , 刀尖 损 坏 , 车
磨削缺陷分析与解决

磨削缺陷分析与解决1.产生原因及影响因素零件的磨削精度指零件在磨削加工后,其形状、尺寸及表面相互位置三方面与理想零件的符合程度。
一般说来,形状精度高于尺寸精度,而位置精度也应高于尺寸精度。
磨削加工中的误差主要来源与两方面。
一是磨床-夹具-砂轮组成的工艺系统本身误差;二是磨削过程中出现的载荷和各种干扰:包括力变形、热变形、振动、磨损等引起的误差。
而在磨削过程中,使砂轮与工件位置改变以降低磨削精度的主要原因有:⑴.由磨削力引起的磨床和工件弹性变形;⑵.磨床和工件的热变形;⑶.磨床和工件的振动;⑷.砂轮磨损后其形状、尺寸变化;⑸.工装、夹具的损坏或变形;⑹.导轨、轴承和轴等部件的非弹性变形。
其中磨削过程中的弹性变形是主要的影响因素,它会使砂轮的实际切入深度与输入切入深度不一致,这一变化是由“砂轮架—砂轮轴承-砂轮轴-工件-工件支承”的弹性系统刚性决定。
一般为消除这种原因带来的误差常在行程进给磨削后,停止相互间的进给,仅依靠弹性回复力维持磨削,即光磨阶段(又叫清火花磨削),从而消除残留余量。
当然造成磨削误差的其它因素液很多如:工件磨削形状误差,工件热变形,磨粒切刃引起的塑性变形,砂轮的磨损等。
2.对工件的影响:降低工件使用寿命;降低工件抗疲劳强度;特殊特性的尺寸精度误差易影响工件使用,如轴承孔尺寸的控制,尺寸过小,安装不到轴上;过大,易引起振动,影响轴承使用寿命等。
3.解决方法:增加系统刚性;减少上工序加工留量,以减小磨削厚度,从而减小磨削力降低残留应力;增加光磨时间;及时修整砂轮,及时检查工装、夹具、轴承完好性及电主轴的振动性等;精细的选择砂轮,如挑选细粒度,硬度较大,组织稍紧密的砂轮;选用导热性好的砂轮(如CBN 砂轮);采用冷却性能优良的磨削液以减少因热变形引起的误差。
二、工件表面粗糙度1.产生原因及影响因素表面粗糙度指加工表面具有较小间距和峰谷所组成微观几何形状特征。
它是大量磨粒在工件表面进行切削后留下的微观痕迹的集合。
外圆磨削质量缺陷原因分析与排除措施

外圆磨削质量缺陷原因分析与排除措施摘要:在外圆磨削加工过程中,在工件表面经常会产生各种各样的表面缺陷,常见的如表面存在波纹、表面划伤、烧伤、鱼鳞状痕迹等。
为了保证磨削的质量,不仅要保证磨床有较高的加工精度,还要保证砂轮有较好的磨削性能。
我们从检查的角度对外圆磨削这些质量缺陷,进行分析并给出相应的解决措施。
关键词:外圆磨削质量缺陷原因分析1.表面波纹缺陷在磨削加工的过程中,工件表面或多或少的都会留下一些加工波纹,表面的波纹是磨削加工过程中最常见的缺陷,形成表面波纹的原因是由于磨削过程中,磨床存在机械的振动,使砂轮在磨削工件时,与工件表面的接触力不能保证时刻一致,从而在工件的表面会留下不同的加工痕迹,由于振动的随机性,因此会产生不同的波纹。
常见的有直线的条纹、多边形波纹、鱼鳞斑纹和斜纹、螺纹线等。
(1)直线条纹产生原因及排除措施直线条纹的产生主要原因是由于磨削系统中存在的各种振动:①、由于砂轮的不平衡,在转动过程中产生的振动。
排除的方法:主要是在使用的过程中,保证砂轮的平衡质量,砂轮使用一段时间后,要对砂轮重新进行平衡性调整。
②、由于砂轮自身的硬度不均匀,在磨削的过程中引起振动。
排除方法:检查砂轮表面的硬度是否满足工艺的要求,如果硬度过高要更换硬度较软些的砂轮。
③、砂轮的修整量过大,或者是修整量不够。
排除的方法:对砂轮要进行合理的修整,修整量过大或不足同样会对工件的表面产生影响,根据要加工的工件进行合理的修整。
④、电机的振动引起的加工过程中砂轮的振动。
排除方法:电机要固定平衡,或者采用相应的隔振装置,如通过弹性零件吸收振动,消除电机的振动对磨削加工的影响。
⑤、砂轮的主轴与轴承这间的间隙过大,使砂轮在旋转时产生径向的跳动。
排除的方法:检查砂轮主轴与轴承间的间隙,按要求正确调整间隙。
(2)多边形波纹产生的原因及排除措施①、由于工件细长,在磨削过程中,工件由于刚性不足,产生振动。
排除的方法:在工件中间增加支撑架,提高支承的刚性,同时稍微降低进给量和进给速度。
磨削加工中的磨削误差分析
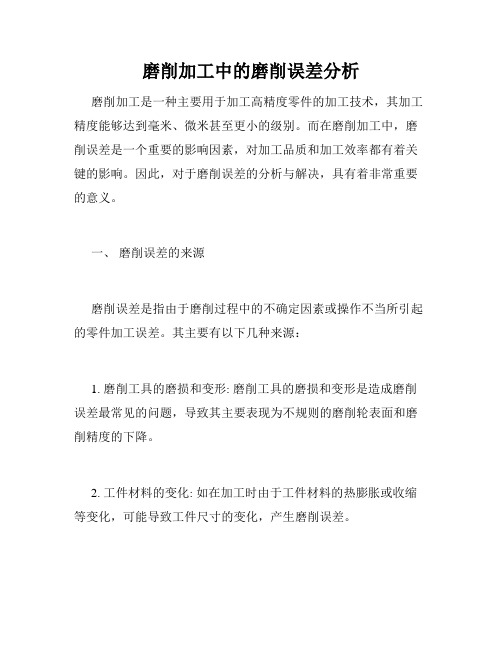
磨削加工中的磨削误差分析磨削加工是一种主要用于加工高精度零件的加工技术,其加工精度能够达到毫米、微米甚至更小的级别。
而在磨削加工中,磨削误差是一个重要的影响因素,对加工品质和加工效率都有着关键的影响。
因此,对于磨削误差的分析与解决,具有着非常重要的意义。
一、磨削误差的来源磨削误差是指由于磨削过程中的不确定因素或操作不当所引起的零件加工误差。
其主要有以下几种来源:1. 磨削工具的磨损和变形: 磨削工具的磨损和变形是造成磨削误差最常见的问题,导致其主要表现为不规则的磨削轮表面和磨削精度的下降。
2. 工件材料的变化: 如在加工时由于工件材料的热膨胀或收缩等变化,可能导致工件尺寸的变化,产生磨削误差。
3. 加工参数的不确定性: 如磨削参数的选择不合适、未能够准确把握加工过程的变化,就可能造成加工精度的不稳定。
4. 制造中的人员和设备因素: 如由于人员工艺水平的不同或设备自身的问题所导致的制造误差等,都可能成为磨削误差的来源。
二、磨削误差的分类磨削误差有以下几种分类方式:1. 几何度量的分类: 如直线度、平面度、圆度、同轴度等。
2. 粗糙度的分类: 如表面粗糙度、压痕深度等。
3. 特殊误差的分类: 如振动引起的误差、加工过程中的热变形等。
4. 组合误差的分类: 如由于几种误差的组合所构成的误差。
三、磨削误差的控制技术为了有效地控制磨削误差,需要采用一些专门的控制技术。
其中,常见的技术有以下几种:1. 磨削参数控制: 如通过合理的磨削参数,来控制磨削加工中的误差,包括磨削轮的选取、磨削轮的转速、磨削轮进给速度、工件进给速度等。
2. 磨削工具的优化设计: 如采用特殊的磨削工具,通过设计和制造优良的磨削工具,来减少磨削误差的源头。
3. 清洁和维护: 如加强磨削设备的清洁和润滑,以确保磨削设备和工具能够保持良好的状态,减少误差的产生。
4. 加工设备的质量控制: 如对于加工设备的选型、评估和维护,采用更加精密的加工设备,并要对其进行定期的检测和调整,以确保加工质量的稳定性和精度。
轴承表面磨削出现缺陷的原因和分析

轴承表面磨削出现缺陷的原因和分析轴承在磨加工过程中,其工作表面是通过高速旋转的砂轮进行磨削的,因此在磨削时如果不按作业指导书进行操作和调整设备,就会在轴承工作表面出现种种缺陷,以致影响轴承的整体质量。
轴承在精密磨削时,由于粗糙要求很高,工作表面出现的磨削痕迹往往能用肉眼观察到其表面磨削痕迹主要有以下几种。
表现出现交叉螺旋线痕迹出现这种痕迹的原因主要是由于砂轮的母线平直性差,存在凹凸现象,在磨削时,砂轮与工件仅是部分接触,当工件或砂轮数次往返运动后,在工件表现就会再现交叉螺旋线且肉眼可以观察到。
这些螺旋线的螺距与工件台速度、工件转速大小有关,同时也与砂轮轴心线和工作台导轨不平行有关。
(一)螺旋线形成的主要原因1.砂轮修整不良,边角未倒角,未使用冷却液进行修整;2.工作台导轨导润滑油过多,致使工作台漂浮;3.机床精度不好;4.磨削压力过大等。
(二)螺旋线形成的具有原因1.V形导轨刚性不好,当磨削时砂轮产生偏移,只是砂轮边缘与工作表面接触;2.修整吵轮时工作台换向速度不稳定,精度不高,使砂轮某一边缘修整略少;3.工件本身刚性差;4.砂轮上有破碎太剥落的砂粒和工件磨削下的铁屑积附在砂轮表面上,为此应将修整好的砂轮用冷却水冲洗或刷洗干净;5.砂轮修整不好,有局部凸起等。
表面出现鱼鳞状表面再现鱼鳞状痕迹的主要原因是由于砂轮的切削刃不够锋利,在磨削时发生“啃住”现象,此时振动较大。
造成工件表面出现鱼鳞状痕迹的具体原因是:1.砂轮表面有垃圾和油污物;2.砂轮未修整圆;3.砂轮变钝。
修整不够锋利;4.金刚石紧固架不牢固,金刚石摇动或金刚石质量不好不尖锐;5.砂轮硬度不均匀等。
工作面拉毛表面再现拉毛痕迹的主要原因是由于粗粒度磨粒脱落后,磨粒夹在工件与砂轮之间而造成。
工件表面在磨削时被拉毛的具体原因是:1.粗磨时遗留下来的痕迹,精磨时未磨掉;2.冷却液中粗磨粒与微小磨粒过滤不干净;3.粗粒度砂轮刚修整好时磨粒容易脱落;4.材料韧性有效期或砂轮太软;5.磨粒韧性与工件材料韧性配合不当等。
外圆磨削加工的质量缺陷分析与控制

外圆磨削加工的质量缺陷分析与控制作者:张光普焦禹萃张艳兵来源:《科技资讯》 2014年第27期张光普焦禹萃张艳兵(郑州工业应用技术学院河南郑州 451100)摘要:目前,外圆磨削技术已广泛应用于各种零件的加工中,但在磨削过程中经常出现一些有质量缺陷的零件,如加工过的零件常常会出现表面烧伤、划伤等现象。
因此,为了保证磨削后的产品的质量,在加工时就要有足够高的加工精度的磨床。
该文将从外圆磨削加工的质量缺陷分析以及控制方法进行阐述。
关键词:磨削加工质量缺陷分析控制中图分类号:TG581 文献标识码:A 文章编号:1672-3791(2014)09(c)-0049-01Quality defects analysis and controlling of grindingZhang Guangpu Jiao Yucui Zhang Yanbing(The Industrial Applied Technology College of Zhengzhou,Zhengzhou Henan,451100 China)Abstract:at present, the external cylindrical grinding technology has been widely used in various kinds of parts processing, but often appear some quality defects in the process of grinding parts, such as processed parts often appear burns, scratches and other surface phenomenon. Therefore, in order to guarantee the quality of the products after grinding, during processing need to be high enough to machining precision grinding machine. This article will from external circular grinding quality defects analysis and elaborates the control approach.Key Words:Grinding;Analysis of Quality Defects;Control磨削是指用磨料、磨具等工具来加工比较精确零件的加工方法。
外圆磨床磨削圆跳动超差的原因分析及维修研究

外圆磨床磨削圆跳动超差的原因分析及维修研究摘要:数控外圆磨床是端面大轴类零件精密磨削加工中不可缺少的重要工具之一,其应用范围十分广泛,能够很好的确保零件的磨削效率及加工质量。
但是在长期运行使用后,却很容易出现磨削外圆表面跳动超差问题,这在一定程度上就会给零件加工带来较大困扰,进而无法保证最终的零件加工质量,因此,要想改善现状,就要寻找一条便捷有效的途径针对该故障问题进行解决和处理。
本文也会对外圆磨床磨削期间所产生的圆跳动超差故障进行着重研究,进而根据具体产生原因,提出科学合理的维修策略,以便相关人士参考借鉴。
关键词:外圆磨床;磨削圆跳动超差故障;原因分析;维修策略现今,数控外圆磨床在汽车发动机及其它行业中有着很高的利用率,其虽然可以很好地确保零件磨削加工质量,但是在运行使用过程中仍存有一定的缺陷和不足,尤其是在磨削期间,很容易出现圆跳动超差问题,进而影响到零件加工质量,因此,要想避免这种故障问题的发生,就要通过全面的检测和维修,来挖掘出故障问题的诱发因素,并制定针对性的防控措施,这样才能最大化发挥外圆磨床的应用性能,满足端面大轴类零件磨削加工需求。
1.故障产生的具体原因分析1.1初步分析与判断在故障初步分析阶段,相关工作人员考虑主要是由以下原因所致:第一,由于磨床车轴顶尖孔加工精度不达标所致;第二,磨床拨盘结构为三拨叉结构,但在实际操作时,操作人员只采用双拨叉,这样就会导致磨床在磨削加工时因拨叉不均匀而出现旋转摆动情况,从而诱发圆跳动超差故障的发生;第三,由于磨床后轴承间隙过大,从而使得磨床运行期间出现不规律的径向跳动,进而诱发圆跳动超差故障的发生[1]。
针对这些故障原因,工作人员进行了相应的调整,得出以下结论:首先,重新修正车轴顶尖孔后,发现磨削圆跳动超差现象依然存在;其次,调整拨盘结构后,发现磨床磨削精度略有改善,可以初步判断拨叉分布的不均匀是导致该故障发生的原因之一,但不是主因;最后,对磨床头架主轴拨盘装置进行拆卸,并在夹持状态下对其头架主轴顶尖径向跳动情况进行全面检测,发现千分表指针顶尖锥端和锥尾最大跳动值分别为0. 014 mm、0. 011 mm,随后又将顶尖拆除,发现工件头架主轴的内外锥面径向跳动及前端面旋转轴向跳动分别为0. 011 mm、0. 007 mm、0. 006mm,均已超出设备最大精度允差,所以可以初步判定,头架主轴的跳动是导致故障发生的主要原因。
常见磨削缺陷的产生原因及消除方法
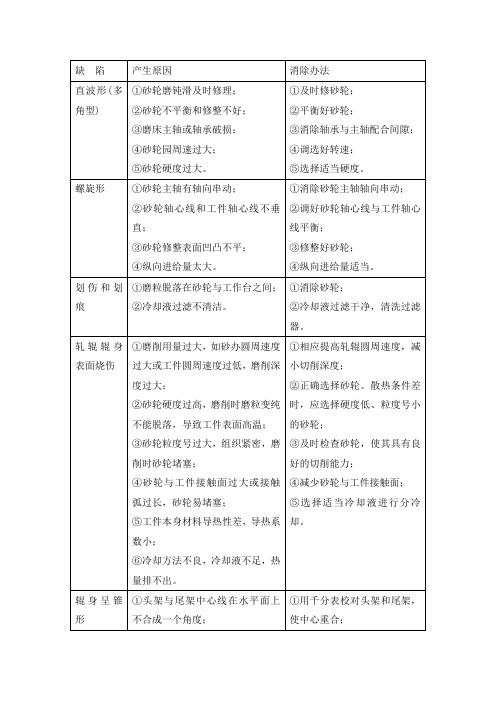
⑤选择适当冷却液进行分冷却。
辊身呈锥形
①头架与尾架中心线在水平面上不合成一个角度;
②轧辊轴线没有调整好,与砂轮轴线不垂直;
③砂轮太软,使砂轮由工件端走到另一端时产生磨耗。
①用千分表校对头架和尾架,使中心重合;
②调整好轧辊,使其轴线与顶针中心线重合;
③合理选择砂轮。
辊身呈细腰形
①头架尾架中心线在垂直平面内不重合成一个角度;
②轧辊轴线没调整好,在垂直平面内成一个角度。
①校正头架与尾架,使中心线重合;
②调整好轧辊,使其轴线与顶针中心重合。
外圆磨削中常见的缺陷及防止措施
缺陷
产生原因
消除办法
直波纹振痕
砂轮不平衡
砂轮进行精细平衡
砂轮磨钝,阻塞引起自振
及时修整砂轮
砂轮主轴或头架主轴跳动
缺陷
产生原因
消除办法
直波形(多角型)
①砂轮磨钝滑及时修理;
②砂轮不平衡和修整不好;
③磨床主轴或轴承破损;
④砂轮园周速过大;
⑤砂轮硬度过大。
①及时修砂轮;
②平衡好砂轮;
③消除轴承与主轴配合间隙;
④调选好转速;
⑤选择适当硬度。
螺旋形
①砂轮主轴有轴向串动;
②砂轮轴心线和工件轴心线不垂直;
③砂轮修整表面凹凸不平;
③砂轮粒度号过大,组织紧密,磨削时砂轮堵塞;
④砂轮与工件接触面过大或接触弧过长,砂轮易堵塞;
⑤工件本身材料导热性差,导热系数小;
⑥冷却方法不良,冷却液不足,热量排不出。
①相应提高轧辊圆周速度,减小切削深度;
②正确选择砂轮。散热条件差时,应选择硬度低、粒度号小的砂轮;
③及时检查砂轮,使其具有良好的切削能力;