圆形堆取料机施工组织方案
堆取料机施工方案

堆取料机施工方案一、工程概况目前,随着工业化的发展,自动化设备在各行各业都得到了广泛应用。
堆取料机作为一种自动化设备,在物料搬运、仓储等领域具有广泛的用途。
本文将介绍堆取料机的施工方案,包括施工拆除、施工现场安全措施、施工过程安排等内容,确保施工过程的顺利进行。
二、施工拆除1.准备工作在进行堆取料机的施工拆除工作前,需要做好充分的准备工作,包括制定拆除方案、调集所需人员和设备、准备必要的材料等。
2.拆除过程a.施工现场划定首先,需要将施工现场划定出来,确保施工过程中的安全。
b.拆除顺序安排按照拆除方案,合理安排拆除的顺序,避免对其他设备和设施造成影响。
c.拆除流程根据设备的具体结构和安装方式,有序进行拆除工作。
要注意遵守相关安全规定,做好防护工作。
三、施工现场安全措施1.工地防护在施工现场周边设置围挡,防止施工过程中的材料飞溅、设备坠落等情况对周围人员和设施造成伤害。
2.现场标识在施工现场进行标识,明确安全通道、危险区域等,提醒施工人员注意安全。
3.安全防护装备施工人员必须配备个人防护装备,包括安全帽、手套、防护眼镜等,确保个人安全。
四、施工过程安排1.施工人员培训在开始施工之前,对参与施工的人员进行相关培训,使其了解施工方案和操作规程,掌握相关安全知识。
2.施工流程控制根据施工方案,制定详细的施工流程,并合理安排施工时间,确保施工过程的高效进行。
3.施工质量控制引入质量控制人员,确保施工质量符合相关标准和要求。
五、施工材料和设备1.施工材料根据具体的施工方案,准备所需的施工材料,包括金属构件、电气元器件等。
2.施工设备根据施工方案,调集合适的施工设备,包括吊车、起重机等,确保施工过程的顺利进行。
六、施工方案评估和改进1.施工方案评估在施工过程中,进行施工方案的评估,及时发现和解决问题,确保施工进度和施工质量。
2.改进措施对施工中出现的问题,制定相应的改进措施,以提高施工效率和质量。
七、施工安全考虑在整个施工过程中,安全是最重要的考虑因素。
圆形预均化堆取料机施工方案
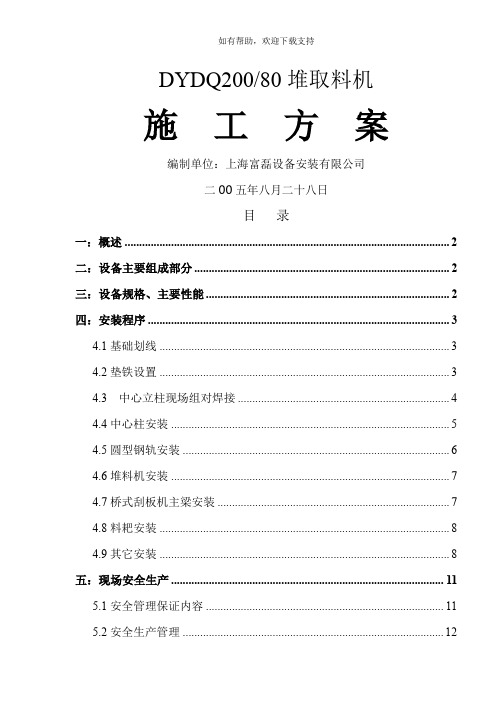
DYDQ200/80堆取料机施工方案编制单位:上海富磊设备安装有限公司二00五年八月二十八日目录一:概述 (2)二:设备主要组成部分 (2)三:设备规格、主要性能 (2)四:安装程序 (3)4.1基础划线 (3)4.2垫铁设置 (3)4.3 中心立柱现场组对焊接 (4)4.4中心柱安装 (5)4.5圆型钢轨安装 (6)4.6堆料机安装 (7)4.7桥式刮板机主梁安装 (7)4.8料耙安装 (8)4.9其它安装 (8)五:现场安全生产 (11)5.1安全管理保证内容 (11)5.2安全生产管理 (12)5.3安全施工措施 (12)一:概述该堆取料机生产厂家为上海建设路桥机械设备有限公司。
用于工业盐堆取料,堆料方式为:定点回转堆料;取料方式为:侧式刮板取料。
二:设备主要组成部分DYDQ200/80堆取料机主要由中心柱、圆形轨道、堆料机、桥式刮板取料机、行走平台等组成。
堆料机沿弧形作扇形和上下运动进行播料;取料机沿一周行走使物料沿径向中心柱移动取料。
物料进出均采用皮带输送机。
三:设备规格、主要性能型号:DYDQ200/80均化比:3.5有效储存量:51000(t)堆料机能力:1500t/h取料机能力:100t/h堆取料形式:顶堆侧取四:安装程序4.1基础划线在土建施工完成后,拆除所用的中心柱脚手架,经厂方验收中心柱基础与圆型轨道基础符合施工设计要求后才能进行施工。
4.1.1以中心柱基础中心为圆心。
(参考建筑中心)4.1.2为便于尺量,在中心柱基础上平面设中心支架。
4.1.3以中心架中心为圆心挂线坠,使与基础中心相重合,埋设中标板。
4.1.4确定中心后划出基础十字线,检查地脚孔位置是否与设备图纸相符。
4.1.5根据设计图纸测出中心柱,基座标高与园型轨道标高。
4.1.6以中心柱中心为圆心,用15kg弹簧称和固定钢盘尺划出钢轨中心辅助线,划线误差 1mm。
4.2垫铁设置根据划线所得的标高:4.2.1中心柱基座设垫铁4组,由525#高强度水泥配比而成的砂堆,钢垫铁设备在砂堆上面其规格为20*400*250。
堆取料机施工方案.

批准:审核:编制:目录1.简介2-31.1基本参数说明 2-31.2工况说明 31.3车间施工平面布置图 32.施工方案编制依据43.质量保证体系44.安装说明 5-134.1主要部件重量表54.2安装顺序流程54.3安装思路54.4安装说明及技术要求64.4.1基础验收64.4.2基础划线64.3.3轨道垫板安装 64.3.4轨道安装6-74.3.5中心落料灰斗安装 7 4.3.6中柱底座安装74.3.7中柱安装7-84.3.8端梁安装8-94.3.9主梁组对及安装94.3.10刮板取料机安装9-104.3.11料耙装置安装114.3.12集电器安装11-12堆取料机安装施工方案第14.3.13堆料装置安装124.3.14液压管路以及润滑系统装配124.3.15控制室安装125.安全文明施工措施 13堆取料机安装施工方案第21.概述:盘固华阳水泥厂页岩预均化堆场采用了沈阳矿山机械厂生产的圆形料场堆取料机。
料场直径为80米,料场存储量为38100吨(页岩)。
圆形料场堆取料机具备环堆侧取的功能,能够有效的利用堆场的空间;另外由于实现了连续合成。
堆料以及全断面取料可以使物料进行预均化,本厂采用的堆取料机可以使物料的均化比达到10:1(理论计算值)。
堆取料机是集结构、机械、液压装置、自动控制为一体的大型设备,其主要部件包括:回转中柱、堆料装置、堆料臂仰俯液压系统、取料机、主梁、端梁、料耙、料耙液压驱动装置、轨道系统等,其基本结构可见图(1)所示。
堆料过程在物料进行连续输送的同时,PLC程序控制堆料机回转在120度的范围内往复回转、同时程序控制器也控制液压仰俯系统的比例流量阀使堆料臂架作仰俯运动;堆料过程实际是中柱回转、堆料臂仰俯、物料输送三个运动的合成。
取料过程是PLC程序控制器的控制端梁行走变频电机驱动主梁及端梁围绕中柱回转、料耙在液压推杆的带动下往复运动不停的将物料从料堆上耙下、刮板取料机取料等多个功能体的运动合成。
堆取料机施工方案

批准:审核:编制:目录1.简介2—31。
1基本参数说明 2-31.2工况说明 31.3车间施工平面布置图 32。
施工方案编制依据 43.质量保证体系 44。
安装说明 5—134.1主要部件重量表 54。
2安装顺序流程 54。
3安装思路 54.4安装说明及技术要求 64。
4。
1基础验收 64.4.2基础划线 64。
3。
3轨道垫板安装 64.3.4轨道安装6-74。
3.5中心落料灰斗安装 7 4.3。
6中柱底座安装74.3.7中柱安装7-84。
3.8端梁安装8—94.3。
9主梁组对及安装94.3。
10刮板取料机安装9—104.3.11料耙装置安装114。
3。
12集电器安装11—124.3。
13堆料装置安装124。
3。
14液压管路以及润滑系统装配124。
3。
15控制室安装125。
安全文明施工措施 131。
概述:盘固华阳水泥厂页岩预均化堆场采用了沈阳矿山机械厂生产的圆形料场堆取料机。
料场直径为80米,料场存储量为38100吨(页岩)。
圆形料场堆取料机具备环堆侧取的功能,能够有效的利用堆场的空间;另外由于实现了连续合成.堆料以及全断面取料可以使物料进行预均化,本厂采用的堆取料机可以使物料的均化比达到10:1(理论计算值).堆取料机是集结构、机械、液压装置、自动控制为一体的大型设备,其主要部件包括:回转中柱、堆料装置、堆料臂仰俯液压系统、取料机、主梁、端梁、料耙、料耙液压驱动装置、轨道系统等,其基本结构可见图(1)所示。
堆料过程在物料进行连续输送的同时,PLC程序控制堆料机回转在120度的范围内往复回转、同时程序控制器也控制液压仰俯系统的比例流量阀使堆料臂架作仰俯运动;堆料过程实际是中柱回转、堆料臂仰俯、物料输送三个运动的合成.取料过程是PLC程序控制器的控制端梁行走变频电机驱动主梁及端梁围绕中柱回转、料耙在液压推杆的带动下往复运动不停的将物料从料堆上耙下、刮板取料机取料等多个功能体的运动合成.1.回转中柱;2。
YG250堆取料机工程施工组织设计方案

YG250/80混匀堆取料机安装方案一.概述:1.YG250/80混匀堆取料机是江门海螺水泥φ80m圆形煤堆场的专用设备,总重量294吨。
计划于2006年3月初开工,工期为35天。
现土建正在施工中。
2.设备简介:YG250/80混匀堆取料机主要由中心柱、堆料机部分、取料机部分三部分组成。
堆料机和取料机可以绕中心柱回转。
中心柱由3个支腿及中心柱体组成,上部支撑堆料机和来料栈桥,下部支撑取料机。
中心落料斗布置在地脚底部并穿过支腿,取料机刮取原煤由中心落料斗落到胶带机上运出。
堆料机部分主要由上部回转平台、中部回转平台、堆料臂架、配重箱、胶带机等组成,在中部和上部回转平台分别设置一套回转支撑。
取料机部分主要由刮板臂、刮板链装置、刮板驱动装置、配重箱、回转平台、回转驱动等组成,在回转平台位置设置有回转支撑。
3.工程特点:3.1本工程所涉及的专业和工种围广,高空作业、交叉作业多,施工难度大,工期紧,因此安全工作尤为重要。
3.2各部件体积大、质量重,技术要求高,在施工过程中要注意各专业间的配合、协调,服从统一安排。
二.主要技术参数:3.1 物料及料场参数3.2 堆料机部分性能参数3.3 取料机部分性能参数3.4电气性能参数三.施工准备:1.技术资料设备的施工图、工艺图、产品说明书以及土建方面相关图纸;有关配套件(如润滑、减速机、回转支撑等)安装使用说明书;国家规定的施工规及标准。
2.主要工器具2.1安装器具:汽车、吊车、电焊机及其他安装用工具;2.2检测工具:经纬仪、光学水准仪、水平仪、百分表、塞尺、重锤、钢卷尺、钢板尺等。
3.设备及基础验收3.1按照施工图纸、技术资料及装箱清单对设备进行外观检查,核对其零、部件、附件的名称、型号、规格、数量;3.2设备验收应在建设单位、监理、施工单位等各方代表参加下进行,验收完毕后由参加的各方代表在整理好的验收记录上签字;3.3对基础进行外观检查,不得有裂纹、蜂窝、空洞、露筋等缺陷;3.4按有关土建基础施工图及安装技术资料,对基础尺寸及位置进行复测检查:尺寸φ9640mm误差不得大于±10mm,标高+0.600m误差不得大于±5mm。
圆形堆取料机施工方案
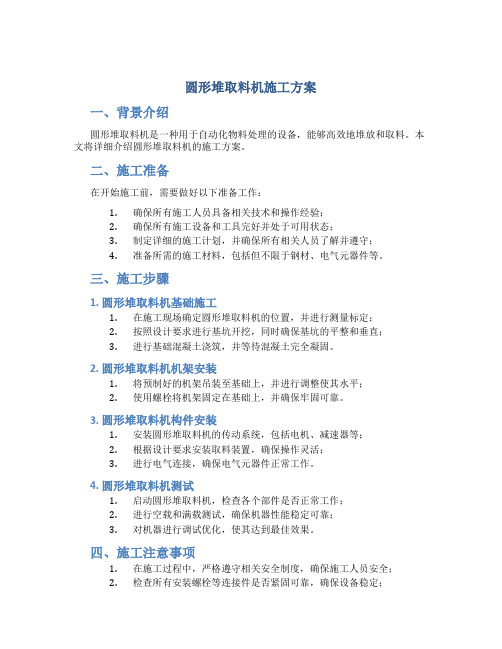
圆形堆取料机施工方案一、背景介绍圆形堆取料机是一种用于自动化物料处理的设备,能够高效地堆放和取料。
本文将详细介绍圆形堆取料机的施工方案。
二、施工准备在开始施工前,需要做好以下准备工作:1.确保所有施工人员具备相关技术和操作经验;2.确保所有施工设备和工具完好并处于可用状态;3.制定详细的施工计划,并确保所有相关人员了解并遵守;4.准备所需的施工材料,包括但不限于钢材、电气元器件等。
三、施工步骤1. 圆形堆取料机基础施工1.在施工现场确定圆形堆取料机的位置,并进行测量标定;2.按照设计要求进行基坑开挖,同时确保基坑的平整和垂直;3.进行基础混凝土浇筑,并等待混凝土完全凝固。
2. 圆形堆取料机机架安装1.将预制好的机架吊装至基础上,并进行调整使其水平;2.使用螺栓将机架固定在基础上,并确保牢固可靠。
3. 圆形堆取料机构件安装1.安装圆形堆取料机的传动系统,包括电机、减速器等;2.根据设计要求安装取料装置,确保操作灵活;3.进行电气连接,确保电气元器件正常工作。
4. 圆形堆取料机测试1.启动圆形堆取料机,检查各个部件是否正常工作;2.进行空载和满载测试,确保机器性能稳定可靠;3.对机器进行调试优化,使其达到最佳效果。
四、施工注意事项1.在施工过程中,严格遵守相关安全制度,确保施工人员安全;2.检查所有安装螺栓等连接件是否紧固可靠,确保设备稳定;3.在机器测试阶段,密切关注机器工作环境和状态,及时发现并解决问题。
五、施工总结通过以上施工步骤和注意事项,我们可以顺利完成圆形堆取料机的施工工作。
在未来的运行过程中,需要定期检查和维护设备,确保设备长期稳定运行。
记住:安全第一,质量为上!以上为圆形堆取料机施工方案的详细介绍,希望对您有所帮助。
石灰石圆形堆取料机施工方案
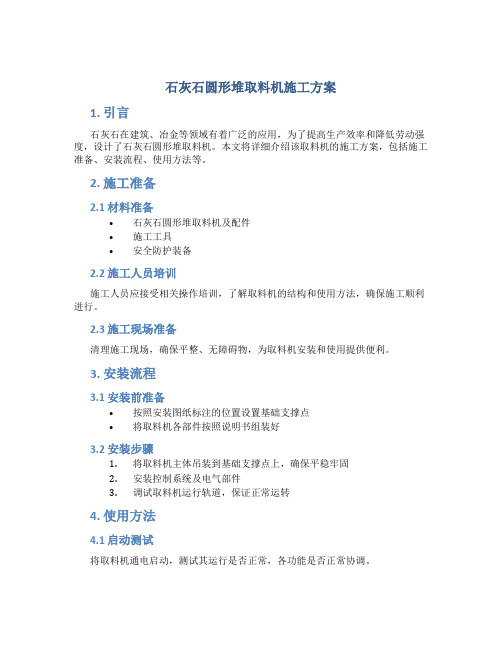
石灰石圆形堆取料机施工方案
1. 引言
石灰石在建筑、冶金等领域有着广泛的应用,为了提高生产效率和降低劳动强度,设计了石灰石圆形堆取料机。
本文将详细介绍该取料机的施工方案,包括施工准备、安装流程、使用方法等。
2. 施工准备
2.1 材料准备
•石灰石圆形堆取料机及配件
•施工工具
•安全防护装备
2.2 施工人员培训
施工人员应接受相关操作培训,了解取料机的结构和使用方法,确保施工顺利进行。
2.3 施工现场准备
清理施工现场,确保平整、无障碍物,为取料机安装和使用提供便利。
3. 安装流程
3.1 安装前准备
•按照安装图纸标注的位置设置基础支撑点
•将取料机各部件按照说明书组装好
3.2 安装步骤
1.将取料机主体吊装到基础支撑点上,确保平稳牢固
2.安装控制系统及电气部件
3.调试取料机运行轨道,保证正常运转
4. 使用方法
4.1 启动测试
将取料机通电启动,测试其运行是否正常,各功能是否正常协调。
4.2 操作流程
1.转动操作手柄,控制取料机在石灰石堆中取料
2.调整取料机高度和倾角,使取料更加准确高效
4.3 安全注意事项
•操作人员应穿戴好安全防护装备
•操作过程中不得随意触碰机器部件
•运行过程中严禁站在取料机下方
5. 维护保养
定期检查取料机各部件是否有松动、磨损等现象,及时进行维修保养,延长取料机的使用寿命。
6. 结语
石灰石圆形堆取料机的施工方案是保证取料机正常运行的重要保障。
通过严格按照施工步骤和要求进行施工和使用,可提高工作效率,降低安全风险,确保设备长期稳定运行。
堆取料机施工方案

批准:审核:编制:目录1.简介2-3 1.1基本参数说明2-3 1.2工况说明31.3车间施工平面布置图32.施工方案编制依据43.质量保证体系44.安装说明5-13 4.1主要部件重量表5 4.2安装顺序流程5 4.3安装思路5 4.4安装说明及技术要求6 4.4.1基础验收6 4.4.2基础划线6 4.3.3轨道垫板安装 6 4.3.4轨道安装6-7 4.3.5中心落料灰斗安装74.3.6中柱底座安装7 4.3.7中柱安装7-8 4.3.8端梁安装8-9 4.3.9主梁组对及安装9 4.3.10刮板取料机安装9-10 4.3.11料耙装置安装11 4.3.12集电器安装11-12 4.3.13堆料装置安装124.3.14液压管路以及润滑系统装配124.3.15控制室安装125.安全文明施工措施131.概述:盘固华阳水泥厂页岩预均化堆场采用了沈阳矿山机械厂生产的圆形料场堆取料机。
料场直径为80米,料场存储量为38100吨(页岩)。
圆形料场堆取料机具备环堆侧取的功能,能够有效的利用堆场的空间;另外由于实现了连续合成。
堆料以及全断面取料可以使物料进行预均化,本厂采用的堆取料机可以使物料的均化比达到10:1(理论计算值)。
堆取料机是集结构、机械、液压装置、自动控制为一体的大型设备,其主要部件包括:回转中柱、堆料装置、堆料臂仰俯液压系统、取料机、主梁、端梁、料耙、料耙液压驱动装置、轨道系统等,其基本结构可见图(1)所示。
堆料过程在物料进行连续输送的同时,PLC程序控制堆料机回转在120度的范围内往复回转、同时程序控制器也控制液压仰俯系统的比例流量阀使堆料臂架作仰俯运动;堆料过程实际是中柱回转、堆料臂仰俯、物料输送三个运动的合成。
取料过程是PLC程序控制器的控制端梁行走变频电机驱动主梁及端梁围绕中柱回转、料耙在液压推杆的带动下往复运动不停的将物料从料堆上耙下、刮板取料机取料等多个功能体的运动合成。
物料种类:页岩物料容重: 1.6t/m3物料粒度80% ≤80mm物料休止角400轨道直径:轨道型号料场总储量 14000t堆料方式:堆料层数堆料能力300t/h堆料半径堆料胶带机带宽:变幅角度:回转速度:取料方式:取料能力:250t/h端梁工作运行速度:0.002—0.02m/min 调车运行速度:刮板尺寸(长X 宽)900 mm * 200 mm 刮板间距:刮板链速:刮板驱动电机功率:45KW料耙驱动方式:料耙倾角:料耙运行速度:料耙驱动电机功率:30KW动力电压:控制电压:控制方式:总装机功率:125KW2.安装方案编制依据:2.1 沈阳矿山机械厂的投标书;2.2 沈阳矿山机械厂提供的安装维修说明书; 2.3 《水泥工业用堆取料机技术条件》;2.4 CBMI质量控制文件CBMI.QS.03.13;2.5 CBMI质量控制文件CBMI.QS.03.21;2.6 40吨汽车起重机性能手册;2.7 20吨汽车起重机性能手册;2.8 《水泥机械设备安装工程施工及验收规范》; 3.堆取料机安装质量保证体系:4.堆取料机安装说明书4.1堆取料机的主要部件重量表:两台堆取料机的部件基本一致,此表中仅列出页岩堆取料机的部件重量。
- 1、下载文档前请自行甄别文档内容的完整性,平台不提供额外的编辑、内容补充、找答案等附加服务。
- 2、"仅部分预览"的文档,不可在线预览部分如存在完整性等问题,可反馈申请退款(可完整预览的文档不适用该条件!)。
- 3、如文档侵犯您的权益,请联系客服反馈,我们会尽快为您处理(人工客服工作时间:9:00-18:30)。
堆取料机安装施工方案一、概述本方案根据圆形堆场用堆取料机编写,主要零部件包括:圆形轨道、中心立柱、主梁和悬臂梁、大车车轮、带式输送机、刮板机、料耙、液压系统、传动装置及液力偶合器,是预均化系统主要设备。
安装主要内容为中心立柱,主梁及悬臂梁等关键设备,体积大,零部件多,吨位重,吊装要求高,安装难度大,特别是交叉作业,现场条件差,使用机具及设备多,安装过程中应特别重视悬臂梁机构的安装。
安装中采用先进的施工方法和检测手段,严格控制每一道工序的施工质量,严格按照设计图纸及国家有关技术标准和规范进行安装施工。
二、施工准备:2.1组织施工人员熟悉图纸、安装说明书等技术资料,组织进行图纸自审及会审,作好技术交底。
2.2施工人员应了解设备到货及设备存放位置及现场情况。
2.3根据设备到货清单检查其规格、尺寸、数量及质量情况。
2.4根据现场情况及设备重量、体积,选择吊装方案及安装方法(施工时作详细施工方案)。
2.5基础验收及划线基础验收工作是设备安装工作一个重要工序,这项工作应在设备安装前会同土建、甲方和监理单位共同验收,并作好验收记录。
基础验收工作应符合施工图纸和施工及验收规范要求。
基础外形尺寸、中心线、标高、地脚螺栓相互位置尺寸。
其允许偏差见下表:2.6设备出库检查按照《水泥机械设备安装工程施工及验收规范》JCJ03-90及图纸技术要求和设备明细逐项检查,应符合合格要求,方可进行安装。
三、堆取料机的吊装堆取料机的安装采用一台120t履带式起重机为主要设备进行设备和构件吊装,一台25t液压汽车吊配合部件吊装。
3.1安装程序:基础验收及放线垫铁加工道轨的辅设找正主柱安装道轨找正灌浆与养生主柱找正灌浆与养生道轨二次找正、固定主柱二次找正、固定移动小车安装大梁安装、找正、焊接悬臂皮带机安装料耙安装操作室安装电缆盘安装电缆电器安装无负荷试车验联动试车3.2安装技术方法:3.2.1首先以中心立柱基础中心点为圆心敷设圆形轨道,其半径极限偏差为±3mm,轨道顶面相对理论高度的极限偏差在任意6m 范围内为±1mm,整圆轨道的极限偏差为±3mm。
3.2.2安装中心立柱底部(底座)及中心立柱,测量找正其垂直、水平度,达到标准后,固定安装。
中心立柱底座轴线对基础定位轴线偏移偏差不应大于1mm;中心立柱底座和顶部法兰的水平度公差为0.02mm/m。
3.2.3安装主梁、悬臂架时,应先把行走机构安装在轨道上垫平固定后,再将主梁、悬臂架用120吨吊车水平吊运到中心立柱用联接销轴与行走机构进行组装,在主梁、悬臂架下应搭设一套临时支架,做为临时支承,在主梁、悬臂架和行走机构组装完后符合技术要求后再撤出。
主梁回转半径应符合设备技术文件及GB10183—88中有关规定。
⑴、大梁找正要求错边量不应大于2mm;⑵、悬臂梁横向水平度公差为2mm。
3.2.4箱形梁焊接是大梁安装工作中一个主要施工工序,焊接质量好坏,直接影响大梁的正常运转和使用寿命。
为确保施工质量,一定要重视大梁焊接工作。
3.2.4.1焊接准备工作⑴、焊接材料和焊接方法的选择。
焊接材料选择将依据设备及工艺图纸要求进行选择,焊接方法拟采用手工焊成形焊接方式。
具体的焊接工艺将在设备图纸以及工艺图纸到现场进行确定。
⑵、电焊工在操作前进行考试,通过试样的透视检查、弯曲和抗拉强度的检验,全部合格后才能上岗。
⑶、焊前要对坡口两侧40mm范围内的油漆、铁锈、毛刺等杂物清除干净,露出母材光泽方可开始焊接。
焊条要烘干,比做好保温工作;⑷、全面检查坡口加工的角度、深度、间隙,对相对角度偏差较大。
间隙过大(小)、深度不够的坡口都要进行修正,并做好记录。
采取相应的措施,确保焊接工艺质量;⑸、对大梁各个部位进行检查,消除各种影响大梁运转的因素;⑹、做好焊接外口的保护和安全工作。
3.2.4.2定位点焊正式焊接有着密切关系,所以对焊接工艺要求严格,焊接材料型号应与焊件材质相匹配,焊条焊接前必须经过350℃烘干1小时,定位点焊将每道焊口的每个边分三次焊接,两名焊工同时点焊每段长度为350-400mm,高度为6mm左右,且不大于6mm,点焊时必须保证熔透,位置应布置在焊道以外,并要求持合格证的焊工施焊.3.2.4.3根据大梁找正情况,编排好每道焊缝试焊程序;施焊工作应先焊接紧靠立柱处的那道焊缝,减少焊接变形对传动力矩的直接影响;⑴、焊接剖口:采用手工电弧焊焊接,务必焊透以及深度一致。
盖面焊时应控制好各焊接工艺参数;焊口焊接完毕后,应重新测定以上各处径向跳动,并与焊前作一比较,内部支撑清理完毕后,重复上面的工作;⑵、焊接结束后,应清理焊缝表面的熔渣及两侧的飞溅物,检查焊缝的外观质量,检查合格后在工艺规定的焊缝及部位打上焊工钢印;⑶、重测各点,保存各工序测量数据。
焊缝质量检验:焊缝表面应呈现平滑细鳞状,宽度均匀整齐,焊缝表面及热影响区不得有裂纹,弧坑、夹渣、气孔等缺陷,焊缝咬边深度不得大于0.5mm,焊缝最低点不得低于箱体表面,并应饱满;采用超声波探伤时,每条焊缝均应检查,探伤长度为该焊缝20%,要求达到JB1152的Ⅱ级,超声波探伤发现的疑点必须用射线探伤检查确定。
采用射线探伤时达GB3323中的Ⅲ级,焊缝交叉处必须重点检查。
3.2.5带式输送机应在悬臂架吊装前安装在悬臂架上,与其一起吊装就位。
输送机安装应符合设备技术文件及GB10595—89中有关规定。
3.2.6刮板输送机的安装和带式输送机同时进行。
⑴、刮板机中心线应与主梁中心线重合,其偏差不应大于2mm;⑵、主动链轮轴的轴线应垂直于刮板机中心线,其垂直度公差为其链轮轴轴承间距的1%;⑶、主、被动链轮轴的轴线水平度公差为0.5mm/m;⑷、同一轴上的两主(被)动链轮对刮板机纵向中心线的对称度公差为1mm;⑸、链轮导槽直线度公差为1mm/m,两条导槽安装位置对刮板机纵向中心线的对称度公差为 3 mm。
同一截面上的两条导槽的标高差不应大于2mm;⑹、刮板链条连接在一起时,应保证两条链条长度一致。
3.2.7料耙在刮板输送机安装合格后进行安装,料耙组装后,其平面度公差为5mm;行走车轮与导轨接触均匀;变幅卷绕机构应灵活,钢丝绳绳头应固定牢固,安全可靠。
3.2.8液压系统的安装应符合GB3766—83中有关规定;现场安装的管路必须进行酸洗处理,其油液清洁度不应低于奈氏10级;各种自动控制仪表、阀门,安装前应进行试验、调节、标定。
3.2.9传动装置各部件间的联接,同一轴线偏斜角不应大于所用联轴器允许的安装误差。
装配好的各传动装置应转动灵活,不得有异常现象。
制动器开闭灵活、制动时应平稳可靠,且闸块与制动盘工作面接触面积不应小于总面积的75%。
3.2.10液力偶合器安装时,其端面圆跳动和径向圆跳动公差为0.1mm。
四、试运转要求4.1空载试运转:4.1.1驱动装置运行平稳,无冲击和异常噪声,无渗油。
4.1.2行走机构运行平稳,车轮不卡轨。
4.1.3电动机和轴承温升不应高于30℃。
4.1.4液压系统油箱内油的温度不应高于65℃。
4.1.5内装式电动滚筒温升不应高于50℃,外装式电动滚筒温升不应高于30℃。
4.1.6液压系统运转正常,各种发讯装置灵敏可靠、管路、接头及密封件无漏油,压力表指示准确,各种阀门工作正常、平稳、无泄压。
4.1.7带式输送机运转正常、平稳、不跑偏。
4.1.8悬臂梁仰俯自如,回转正常、平稳。
4.1.9刮板机运行平稳,牵引件运转正常,无卡碰、跑偏、输送链张紧适中。
4.1.10料耙运行平稳,无拌动冲击现象。
4.1.11制动器开闭灵活,制动平稳。
4.1.12各安全保护装置动作灵敏准确,安全可靠。
4.1.13电控装置及程序运行准确可靠。
4.2负荷试运转:4.2.1应符合6.4.1中除6.4.1.3—6.4.1.5以外的要求。
4.2.2电动机和轴承温升不应高于40℃。
4.2.3液压系统油箱内油的温度不应高于70℃。
4.2.4内装式电动滚筒温升不应高于60℃,外装式电动滚筒温升不应高于40℃。
4.2.5输送带与托辊接触良好,张力适中,清扫器工作正常。
五、各项人员配置1、工段长: 1名2、质量负责人:1名3、钳工:4名1、焊工:4名2、铆工:2名3、力工:6名六、工器具配置1、25T吊车一台;2、焊机四台;3、手拉葫芦3T、四台;4、气割工具二套;5、常用小工具若干。
七、安全及文明施工措施1. 本工程工期紧,难度大,高空作业多,必须树立安全第一,预防为主的思想,严格执行安全操作规程,以保证工程的顺利进行。
2. 进入现场的施工人员,必须严格遵守安全规章制度。
配戴好安全防护用品,戴好安全帽,高空作业拴好安全带,电工、电焊工必须穿好绝缘鞋。
3. 高空作业施工设置好安全网,脚手架搭设应牢固、可靠,脚手架绑扎要按规范施工,跳板要封头,严格检查架杆、跳板,锈腐、裂纹、不合格禁止使用,以防塌落,高空作业禁止穿硬底鞋。
4. 高空作业工器具要放在安全地方,上下传递采用工具包,不得随意从高处向下扔或坠落任何物品。
5. 对使用电焊机把线必须完好无漏电破皮现象,氧气、乙炔瓶必须设专人管理,无漏气现象发生,如漏气立刻处理好以防火灾爆炸事故发生。
6. 对使用的电动工具,电源必须设触电保护器。
照明灯必须安全可靠,电工维护严格管理,不准他人移动,防触电伤人。
进入容器内照明灯要加装触电保护器。
7. 现场吊物要专人指挥,旗哨齐全,哨音清楚,闲人免进。
吊装时要先转杆到吊物放置位置,然后试吊,再起吊到相应高度转杆就位。
8. 对使用的吊装工器具、绳索必须严格检查,符合安全要求,不符合严禁使用。
9. 使用电焊,气焊割必须预防火灾发生,对有油垢的地方施工必须采取安全措施,如灭火器等。
氧乙炔气瓶定点放置,并保持安全距离。
10. 在施工中严格遵守安全生产规程,不可乱动运转设备。
11. 现场要设安全标语,“四口”要设防护栏及醒目标志等措施。
12. 参战人员必须听从指挥,遵章守纪,对违规违制者,按安全奖罚制度严格处罚。
13. 在施工过程中必须做到安全施工、文明施工。
严格按施工方案中的平面布置方案布置机具,随时清理废料及现场卫生,同时做好现场保卫工作。
八、质量保证措施本工程,工程量大,且施工周期短,构件品种多,几何尺寸大,单件吨位大。
因与设备吊装交叉问题,因此给吊装工作带来了不少困难。
针对以上所述问题,为了保证工程质量,达到施工进度要求,特别制定如下质量保证措施。
1、建立和健全质量保证体系2、认真贯彻执行我公司制定的质量方针和质量目标,落实合格质量检验管理人员及质量专检人员,确保施工全过程的质量管理。
3、制定和严格执行质量管理制度。
4、严格按公司依据ISO9001标准制定的工作程序工作。
5、对各阶段的主要工序和工艺质量制定控制计划。
6、认真作好各级施工人员的质量交底工作。