柳钢转炉厂方坯连铸机全自动出坯功能的实现
方坯连铸机工程基础自动化系统操作说明书(精)

海鑫七流海鑫七流方坯方坯方坯连铸机连铸机连铸机电气自动化说明书电气自动化说明书中冶连铸技术工程股份有限公司中冶连铸技术工程股份有限公司20020099·6目录一、电气操作说明1.概述1.1控制说明1.2电气控制柜、操作台2.公用系统2.1 大包回转台2.2 钢包加盖2. 3 滑动水口2.4 中间罐车2.5 二冷室排汽风机2.6 主机液压站系统2.7 出坯液压站系统2.8 油气润滑站系统2.9出坯辊道2.10移坯车2.11翻转冷床3.铸流系统3. 1 结晶器控制系统3.2 拉矫机控制系统3.3 拉坯辊、脱坯辊3.4火切机系统3.5 切前辊道3.6 输送辊道3.7 翻钢机3. 8 升降档板4.仪表配水系统4.1 二冷水喷淋系统二、二冷水自动配水操作说明1.概述1.1.操作说明1.2.自动配水操作简要说明1.3.自动配水的具体操作三、变频器参数表一、电气自动化操作说明1.概述1.1.控制说明根据设计要求,本电气设备设计主要包括MCC马达控制系统和自动控制PLC 系统。
根据工艺要求,MCC设备设计包括大包回转台、中间罐车、排汽风机、拉矫机、切前辊道、输送辊道及存放装置、火切机系统、出坯辊道和主机液压站等设备。
具体请见MCC设备设计图纸R255C3301。
自动化控制系统采用了八台德国西门子SIEMENS S7 300 系列PLC控制系统,其中每铸流一台,共7台;公用一台。
铸流CPU及公用CPU与工作站、工作站与工作站以及工作站与服务器之间的通讯是通过以太网连接的;铸流、公用的CPU与远程站、变频器之间的连接是通过PROFIBUS网连接的;具体请见PLC 设备设计图纸R255C3302 和仪表设备设计图纸R255C3401。
1.2.电气控制柜、操作台箱本连铸机设:1.MCC控制柜(包括变频器柜28台:其中LZ0-P1~LZ0-P14为公用铸流部分控制柜;LZ1-P1~LZ1-P2~ LZ7-P1~LZ7-P2为铸流部分控制柜。
板坯连铸机自动控制

民 蕾科技 爪 需
板 坯连铸 机 自动控 制
夏永刚 ’ 李宏声 2
科论 技坛
(、 1一重集团大连 国际科技 贸易有限公 司, 宁 大连 1 60 2 一重集团大连设计研究院 新品技 术研 究室, 宁 大连 160 ) 辽 160 、 辽 16 0
摘 要: 主要介绍 了板坯连铸机Байду номын сангаас的 自动化控制和生产工序 。自动化控制的总体设计采 用了集成的 自动化平台, 包括 SE N IME S公 司的监控 、 编程
前言
作者简介 : 永刚 , 夏 一重集 团大连国际科技 贸易有限公司 , 师。李宏声 , 工程 一重集 团大连设计研 究院新品技术研 究室, 高级工程师。
软件及硬件 的设计使用 ,- 2 . ̄f太网及 Pobs Y r u 现场总线的应 用, i f 远程通讯控制的使 用, 使整套连铸机的 自动化控制 系统具有可靠、 稳定、 安全、 易操
作和可扩展等性能和特点。 关键词 : 板坯连铸机 ; 自动化 ; 监控 ; 编程 ; 工业 以太网 ; 场总线 现 此时可在悬挂操作箱上 按下 “ 浇铸启动 ”按钮 ,浇铸 过程就 自动 近几年 电子技术 日新月异蓬 勃发 展 ,电气控制技术 的发展 相 当成 进 行 。 熟 。我 院在 20 07年设计 了一套 板坯连铸 机生 产线 ,设 计 生产 10 x 0 1 设备故 障可在监控画面上反映。 10 m板坯 ,年 产连铸坯 10 万吨 ,二冷水采用气雾冷却方 式。工 8m 5约 尾坯控制 : 艺都是我们 自行编制的 ,三电控制为三电合一的 自 化平 台控制。 动 “ 拉尾坯模式”只是在 “ 铸造模式”的状态下才有效 ,它是在浇铸 1 系 统 配置 将要结束时 ,由操作人员在悬 挂操 作箱上按 “ 浇铸结束 ”按钮 , 时 这 连铸 电气控 制系统配置了 四台工控 机 ,一台放置在主 电室 ,一台 将 自动进人 “ 拉尾坯模 式”的工作状态。 放置在二操室 ,另两台放置在主控室 。火焰 切割机 自动化控制 系统成 4 连 铸 电气 控 制 系统 主 要 软 件 设计 套供 货。其它设 备采用 S M N 公司 的 s _ o L I ES E 7 4 o P C产 品进 行控制 。 41 冷却水系统设计 . 应用 了 Po b sD rf u— P现场总线技术 ,P C通 过 S E 7 5 i L T P . 4软件编程 ,监 二冷 水动态控制 :根据二 冷区铸 坯的实际情况来及时改变二冷水 控系统采用基于在 WI D WS N O 操作 系统下 的 SM TC Wi c . 组态监 量 的控制方法叫动态控 制。一般有三种控制方法: I A I n 6 c 0 控软件。 1 比例控制 :即二冷水 的水量与拉速成一定 的比例。 ) 2 系统 组 态 通常表示为 :Q a+ = vb 板坯连铸机 由 SE N I ME S的 ¥ - 0 7 4 0三套及 远程 I / O和四台 H 监 MI 式中 Q 二冷水 的总量 ,Lri;V 拉速 ,m m n 、b 常数。 一 /n 一 a / i ;a - 控站进行控制( 切割机 自动化控制通过采用编码器信号及摄 像定 尺进行 2 )参数控制:建立符合 Q a + v c = C b+ 的数学模 型,将 a 、C 、b 参数 控制 ,是一套独立 的系统) 。主要功能 :实现在主控 室、浇铸平 台、配 存人计算机 ,浇铸 时选取对应钢种 的参数 ,根据拉速 自动配置各 回路 。 水 室 、二 操 室 、液 压 室 、大包 平 台 进行 操 作 控 制 。远 程 I / O使用 水 量 。 E 20 T 0 ,采用 Pob s D rf u— P现场总线 和 P C进行通讯 、数据交换 ,P C i L L 3 目标表面温度控制 :考虑了钢种、拉速及 浇铸状态建立数学模 ) 通过工业 以太 网与监控站传输数据。采用 SMA I n d . I T C Wic i 0制做人机 型 ,根据建立 的数学模 型计算 出目标温度 ,实测铸 坯表面温度 ,根据 对话界面 , 实现在线修改和监控 的功能 。 二者 的差值 ,自动调整二冷水的水量。 42 电控系统设计 . 3 控制对象及生产控 制流程 连铸机 为一机 两流 ( 10 10 m) 10 x 8 m 。控制对 象包括 大包 回转台 、 1 )液压站控制设计 。 中间罐 车、煤气烘烤 站 、结 晶器 、拉矫机 、脱锭机 、切 割机 、辊道 、 液压部分包括 :高压泵 、油箱及 附属 的油位 、温度计及加热器和 移钢机、蒸气排 出风机、液压站 、配水站等 。 冷却器、过滤器 、循环泵 、各种电磁阀及 蓄势器等。 生产控制流程 : 在液压站有三 台高 压泵 ,在正常情况下 两台工作 ,一台备用 。在 站 内操作箱上有工作方式 选择开关 ,选择几号泵为 备用 ,当液压系统 工作时 ,工作泵启动运行 。当工作泵 出现故 障时 ,自动或人工停止工 作泵再启 动备用泵 。 2 )引锭杆跟踪系统。 工作方式及控制内容 : 手动方式 : 引锭杆跟踪系统 由引锭杆、安装在 3 6号和 5 8号辊上 的脉 冲发生 L 随时可将 工作方式转为手动 。当转为手动时 ,断开 自动控制和有 器及 P C的高速计数模块等组成 。 关设备 之间的联锁 ,这时设备运行状 态不发生任何 中断或 改变 ,直到 跟踪 系统分为三部分 : 操作者 给出新 的控制指令 为止。 a . 送引锭杆阶段 ; b浇铸初期阶段 ; . 自动方式 : 连铸机 工作主要是在 自动方式 下进行 。在 自动状 态下 ,仅需要操 c . 拉尾坯阶段。 3 )拉矫和振动的电控设计。 作有关 的几 只按钮 ,其余各设备 的运 行是 由引锭杆跟 踪系统和联锁关 系控制 的。当在 “ 浇铸 ”时,把选择开关转为 “ 手动” ,各设备间的联 拉矫和振动电气控制 系统采用了 S ME S系列的交流变频装 置 , I N E 锁就 被解除 ,跟踪系统将 继续工作 ,其所送 出的信号不 起控制作 用 , 其具有高稳 态精度和优 良的动态 响应 ,可通过 内部的 软件进行调试 , 仅作 为参考 。当把选择开关从 “ 手动”转为 “ 动 ”时 ,自动顺序控 操作简单 。同时该装置具 有高效的故障诊 断功能 ,通过网络接 口进行 自 信息交换 ,拉矫机速度给定通过 P C L 实时控 制 ,以求拉速和二冷水符 制将按照跟踪系统继续进行 。 下列设备 完全与 “ 自动” “ 手动”工作方式选择 无关 :大包 回转 合工艺设计要求 。振动电机的振动频率也是和拉速同步调节 。 台;l 、2号 中间罐 车;引锭杆存放装置 ;辊 道设备 ;火焰 切割机 ;液 4 )切 割 系统 。 切割 系统为成套供货设备 , 铸坯切割分为 自 动和半 自动两种方式 。 压设备 。 自动方式的切割信号为摄 像定尺发 出达到定 尺信 号 自动发 出切割信号 送引锭控制 : 半 动方式为达到定尺长度时,人为发 出切割信号 。 当送引锭杆准备好后 ,将开关打到 “ 插入模式” ,在主操作台及悬 来完成 ; 自 结束语 挂操作箱上 “ 插入模式 ”灯亮 。 连铸 机对 自动化水平及 可靠性的要求很 高,本连铸 机从调试到投 如果未准备好 而选择 “ 插入模式” ,此时 “ 插入模式”灯闪烁 ,直 到 “ 准备模式 ”好后为平光 。但这不影响各设备在送引锭前的准备。 产 ,一直正常运行 。实践证 明 ,该系统设计合理 ,安全 可靠 ,操作方 便 ,大大减 轻了工人的劳动强 度 ,提高工作效率 。所有信 号都 是通过 浇铸控 制 : 如果浇铸条件具 备 ,则各操作 台上 相应 灯亮 ;如果浇铸 条件 不具 工业 以太 网及 Pobs 场总线来完 成的 ,大 大降低了成本 和施 工难 r u现 i f 度 ,为用户增加了可观的经济效益 。 备 , 灯闪烁 , 则 直到进行有关操作后 , 灯光 变为平光 。
板坯连铸机电气自动化的优化

板坯连铸机电气自动化的优化随着钢铁工业的发展与进步,板坯连铸技术越来越成为制造优质钢材的重要方法之一。
板坯连铸机的电气自动化是保证连铸质量、提升生产效率、降低成本的关键。
因此,对板坯连铸机电气自动化的优化已成为钢铁企业不可避免的问题。
板坯连铸机电气自动化的特点在于需要实现多参数的自动控制,包括液压、气动、水系、机械传动等方面的控制,同时要与上位系统实现数据采集、状态监测、通信联络等功能。
在对板坯连铸机电气自动化的优化过程中,需要解决的问题主要有以下几个方面:1.连铸机的自动化程度板坯连铸机的自动化程度越高,掌握材料质量、冷却控制、结晶器工作方式等关键技术就会越来越容易。
通过连铸机自动化掌握以上各项技术,可以保证钢坯的质量与稳定性,同时也可以提高生产效率与降低成本。
2.连铸机控制系统的可靠性板坯连铸机的控制系统需要具有高精度、高灵敏、高可靠的特点。
在连铸过程中,一旦控制系统出现故障导致连铸过程无法正常进行,不仅会影响钢材的质量,也会浪费大量时间与资源。
因此,控制系统的可靠性是连铸机电气自动化优化过程中的重要考虑因素。
随着智能化技术的发展,板坯连铸机的控制系统也应逐步实现智能化。
通过智能化技术的应用,可以实现设备在故障条件下自动切换、自动保护等功能,避免了人为干预控制系统带来的误操作与事故隐患。
在实际生产中,钢铁企业通过多种方式开展板坯连铸机电气自动化的优化。
具体优化策略如下:1. 现场实时监测与控制通过在生产现场使用现代集成式控制、自动化技术,可以实现在线监测与控制,保证了钢坯制造工艺的稳定性、一致性和连铸坯尺寸的准确性。
同时,实现自动化技术的应用,也可以有效掌握操作人员所不能掌握的大量的有关生产过程的数据和信息,以便决策部门对钢坯制造工艺做出更具有科学性和合理性的调整,得到更好的经济效益。
2. 智能化控制系统的应用智能化控制系统是按照钢铁行业的特点,对控制系统进行研究和开发的产品,具备高可靠性、高稳定性、高可控性、高安全性等特点。
柳钢35t转炉方坯连铸机系统优化措施
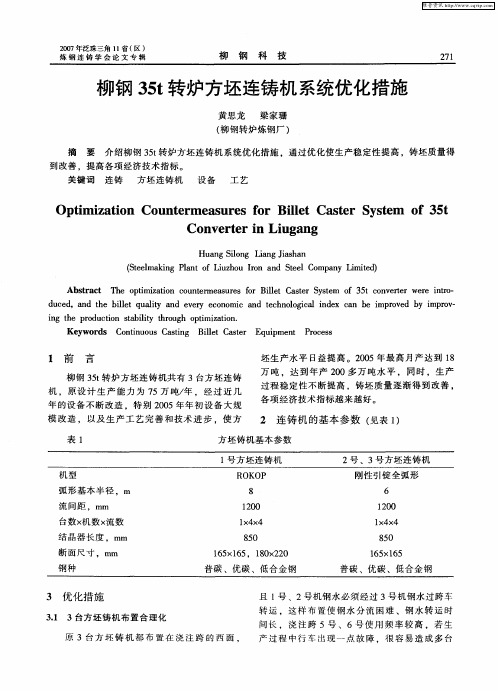
Ke wo d C n i u u a t g B l t Ca t r E u p n P o e s y rs o t o s C si i e se q i me t r c s n n l
维普资讯
炼 连 霉 钢 铸 霎 妻辑 学论 专 会文
柳钢科技 p 致
2 7 1
柳钢 3 t 5 转炉方坯连铸机 系统优化措施
黄思龙 梁家 珊 ( 钢转 炉炼 钢厂 ) 柳
摘 要
关键词
介 绍柳 钢 3 t 5 转炉方 坯连 铸机 系统 优化 措施 ,通过 优化使 生 产稳定 性提 高 ,铸坯 质量得
Ab t a t T e o t z t n c u tr a u e o i e a tr S se o 5 o v r r we e i t — s r c h p i a i o n e me s r s f r B l t C se y t m f 3 t c n e t r n r mi o l e o d c d n h i e u l y a d e e y e o o c a d tc n lg c n e a e i r v d b mp o — u e ,a d t e b l t q a i n v r c n mi n e h o o i a i d x c n b mp o e y i r v l t l
故 明显减 少 .过程稳 定 性 大大提 高 。
34 方坯 自动配 水技 术应 用 .
原 3台方 坯 机 采 用 人 工 配 水 控 制 ,拉 速 变 化 时 不 能 及 时精 确 调 整 配水 量 ,且 各 弧 面冷 却
转炉全自动出钢国内应用情况

转炉全自动出钢国内应用情况
转炉全自动出钢是一种先进的炼钢技术,它可以实现出钢过程的自动化和智能化控制,提高出钢效率和质量稳定性。
目前,该技术在国内已经得到广泛应用,主要体现在以下几个方面:
1. 大型钢铁企业的应用:国内一些大型钢铁企业已经开始采用全自动出钢技术,如宝钢、武钢、沙钢等。
这些企业通常拥有多座转炉,采用全自动出钢技术可以大幅度提高生产效率和产品质量,同时降低生产成本和环境污染。
2. 中小型钢铁企业的应用:除了大型钢铁企业,一些中小型钢铁企业也开始逐渐采用全自动出钢技术,以提高生产效率和产品质量。
这些企业通常规模较小,采用全自动出钢技术可以更好地适应市场需求,提高企业竞争力。
3. 技术升级和改造:一些传统的炼钢企业也开始对生产线进行技术升级和改造,采用全自动出钢技术来提高生产效率和产品质量。
这些企业通常面临着市场竞争和环保压力,采用先进技术可以更好地应对挑战。
总的来说,随着国内钢铁行业的不断发展和市场竞争的加剧,全自动
出钢技术在国内的应用范围将会进一步扩大。
柳钢转炉厂工艺技术的进展

进行 了多项整 改 , 到 2 0 — 6工 艺应用 趋成 熟 。 09 0
目前 ,铁 水 脱 硫 效 率 可 达 8% ,在脱 硫 效 率 、 0 脱硫成 本上都 达到 了设计 目标 。
2 R 精炼 技术应 用 . 3 H
共享 。 目前 ,转炉厂 的计算机信息管理系统 已
由电脑 自动控制 ,实现 了 “ 一键式”炼钢 ,不 倒炉出钢的 比例超 过 9 %。10 转炉 的 自 5 2t 动化
炼 钢模 型 由转 炉 厂工 程 技 术 人 员 自主研 发 ,有 效地 解 决 了转 炉 、精 炼 炉 标 准 化 作 业 执行 难 的 问题 ,真 正 实 现 了转 炉 、精 炼 炉标 准 自动 化 作
作 者:覃 强 ,大学学历 ,高级 工程 师 ,现任转炉炼
钢 厂 副厂 长 。
10 副枪炼 钢 、10 半 自动化炼钢技术 的 5t 2t
应 用 取 得 Biblioteka 破 。 10 转 炉 的副 枪 炼 钢 工 艺 日趋 5t 成 熟 ,具 备 了氧 枪 的 自动控 制 、 自动 称 料 、 自 动 加 料 、 自动 拉碳 等 功 能 ,整 个 吹 炼 过 程完 全
l l
方坯连铸机工艺技术操作规程

一、连铸机主要参数:二、连铸机工艺流程图转炉出钢→钢包回转台→中间罐→结晶器→二次冷却→拉矫机→火焰切割机→输送辊道→翻钢机、移坯机→出坯三、中间包的准备与烘烤1、定径水口技术要求:定径水口技术参数控制表2、中间包的检查:必须认真检查中间包水口座砖,发现座砖有问题,应及时更换。
绝热板包应认真检查中间包绝热板和绝热板之间的泥料,发现问题,及时处理;然后方可安装定径水口。
干式料中包应认真检查中包快换机构工作是否正常,是否存在滑块打不到位,滑块打不正等情况。
3、中间包的烘烤:3.1、绝热板包的烘烤:3.1.1、使用绝热板中间包,中包烘烤前必须清扫干净。
正常生产准备条件下,中间包在线烘烤时间为1-2小时,按以下步骤烘烤:小火烘烤不小于20分钟,中火烘烤不小于20分钟,大火烘烤不小于20分钟,大火烘烤时据煤气压力可考虑开风机。
3.1.2、非正常生产准备条件下,中间包在线烘烤时间不得低于40分钟,中火烘烤20分钟,大火烘烤20分钟。
3.1.3、定径水口安装后,应比内衬提前1小时以上进行烘烤,烘烤时间最长不得超过3小时。
3.2方坯干式料包的烘烤:3.2.1、使用干式料中间包,中包烘烤前必须清扫干净,包盖损坏要及时更换。
正常生产准备条件下,中间包烘烤时间2.5-3.5小时,按以下步骤烘烤:小火烘烤不小于50分钟,中火烘烤不小于50分钟,大火烘烤不小于50分钟,确保烘烤温度大于900℃,中包为红热状态。
3.2.2、非正常生产准备条件下,中间包在线烘烤时间不得低于2小时,中火烘烤60分钟,大火烘烤60分钟。
四、基本工艺参数控制:1、连铸钢水准备:1.1、常炼钢种:Q195-Q235、HRB400E等,其成分应符合相应的国家标准规定,并保证有良好的流动性,要求Mn/S必须大于15,Mn/Si不小于2.5。
1.2、钢水必须脱氧良好,钢中酸溶铝≤0.006%。
1.3、钢水必须进行吹N2处理,吹N2时间普碳钢不低于2分钟、低合金钢不低于3分钟,品种钢执行品种钢操作要点,氮气压力和流量以能达到钢包液渣面翻动而不裸露钢水为准。
方坯连铸机拉矫减速器的润滑改进

S e h n D r hb a uW n o g et S iio g
( eo i un c t l atr u n x S e C .Luhu5 5 0 ) Rvl n F raeSe c y,G a g i t l o /zo 4 0 2 vg eF o e
毡 矫t琏罩
图1 1 、2 方坯连铸机拉矫机的传动示意 图
构
铸机产 量快 速提升 ,拉矫 减速 器的 故 障随之 大增 。
对产生故障的减速器进行拆检发现,发生故障的 主要原因是蜗轮冠 的非正常磨损。
l ~
2一
,~
#
t ■#
1 故障分 析及 改 进办 法
1 1 故 障分析 .
摘要 :柳钢转 妒厂通过对 1 、2 方坯连诗 关键 设备拉矫战速器 的润滑改进 ,降低 了润 滑荆 消耗 ,延
长 了拉矫 残速 器的使 甩寿命 ,减 少 了运行 故障 ,节约 了维修 费 用,确保 了生产顺利进行。 关键词 :连铸机 ;拉矫机 ;环面双包络蜗 杆减速器 ;润滑
An I p o e e to brc to o te c r Le ei d c r m r v m n n Lu ia i n f r S r the v l ng Re u e o q r l t Co tn o s Ca tM a h n fS ua e Bi e n i u u s l cie
柳钢转炉厂 1、2方坯连铸机是 由武汉设计 院设计的 R m弧罗可普连铸机 ,拉矫 机的作用是 S 将引锭杆送入结晶器 ,并将铸坯从结 晶器内拉 出, 并能实现完全凝 固或带液相 的铸坯 的矫直 ,保证 矫直过程不影 响铸 坯质量。在 连铸生产过 程 中,
拉矫 机一 旦 出现故 障 即会 直接影 响 生产顺 利 进行 ,
- 1、下载文档前请自行甄别文档内容的完整性,平台不提供额外的编辑、内容补充、找答案等附加服务。
- 2、"仅部分预览"的文档,不可在线预览部分如存在完整性等问题,可反馈申请退款(可完整预览的文档不适用该条件!)。
- 3、如文档侵犯您的权益,请联系客服反馈,我们会尽快为您处理(人工客服工作时间:9:00-18:30)。
柳钢转炉厂方坯连铸机全自动出坯功能的实现
【摘要】本文介绍了柳钢转炉厂方坯连铸机全自动出坯功能的设计思路、控制流程以及生产应用效果。
【关键词】方坯连铸机;铸坯;全自动出坯
1 项目概况
柳钢转炉炼钢厂目前共有6台方坯连铸机,产能规模约500万吨钢,原方坯连铸机工艺控制流程包含:大回转台自动浇注钢包钢水到中间罐车;中间罐车的塞棒自动控制实现结晶器恒定液面浇注铸坯;结晶器的液面自动控制实现拉矫机自动恒拉速拉钢;红外定尺系统实现自动定尺切割铸坯;切割完好的铸坯经过运输辊道自动送坯到出坯冷床区域;在出坯冷床区域经过人工手动操作翻钢机翻转、移钢机移动铸坯来完成出坯。
实现方坯连铸出坯区域的全自动出坯功能是提升方坯连铸机全自动化装备水平的一个瓶颈问题。
根据转炉厂的发展需求:提升连铸机自动化装备水平,规范标准化操作。
实现方坯连铸出坯区域的全自动出坯功能势在必行!
2 全自动出坯功能的实现及其应用
2.1 设计方案
为了实现出坯辊道区域全自动出坯功能,根据现场环境、现有设备、控制流程、铸坯热装要求等等因素,确定设计方案:
(1)在连铸机出坯辊道区域实现对铸坯进入冷床、完成翻转信号的检测与判断。
(2)根据各个流次的铸坯到达冷床的先后顺序进行排列组合,使翻钢机按顺序依次进行周期性自动翻转铸坯。
(3)根据生产要求、铸坯热装工艺,设备承受状况等因素,移钢机按设定两个周期进行自动循环推动铸坯完成出坯任务。
2.2 铸坯进入冷床的检测
对每一流的铸坯进入冷床的情况进行检测通常我们采用的一些安装在现场的感应开关、光电开关等元器件来实现,但是由于现场环境温度高、水汽大等因素这些元器件寿命很短、引发故障率高。
通过几次元器件的改造换型后,我们采用了非接触式铸坯检测系统来判定每一流铸坯到位情况。
非接触式铸坯检测信号具有:准确率高、故障率低、使用寿命长等方面的优点。
2.3 翻钢机自动翻转铸坯
翻钢机的功能就是将辊道送来的铸坯翻转90度到距辊面上一层的平台支架上。
当非接触式铸坯检测系统检测到有铸坯进入冷床到位信号后,PLC控制程序根据检测信号按铸坯先到先翻转的原则对铸坯进行周期内排队组合,同时翻钢机进行翻坯动作(当某一流出现故障后,可以采用手动干预翻坯动作,手动翻坯动作具有优先级别)。
翻钢机翻坯动作分两个周期循环进行,第一个周期翻坯4支,第二个周期翻坯3支(周期内的翻坯支数可以在HMI上人工设定),当非接触式铸坯检测系统检测到支架上的翻坯支数等于我们所设定的数值时,判断翻钢完成了一个周期的动作任务等待进行下一个周期,以后依次循环。
2.4 移钢机自动循环推铸坯
移钢机的功能就是将翻钢机翻转到平台支架上的铸坯推送到冷床上实现热装热送。
当翻钢机完成一个周期的翻坯任务后,移钢机在满足自动运行连锁条件下开始从原点位置自动推坯,运转到终点位后经过10秒钟延时等待后自动返回到原点位位置完成一个周期的出坯任务,以后依次循环完成下一个周期的出坯任务(见图1)。
图1 全自动出坯功能流程图
2.5 安全互锁
由于7个流次的翻钢机和移钢机它们都是独立的设备,都是有着独立的PLC 系统控制,各PLC系统采用工业以太网进行通讯。
在以往生产操作过程中经常出现移钢机推动铸坯撞坏翻钢机的情况发生。
为了避免这一情况的发生,通过现场生产工序跟踪、分析,结合翻钢机、移钢钢机的工作特性,通过以太网交换各个PLC系统的数据信号,在自动控制模式下运转制定不同情况下的推钢机与翻钢机之间的动作限定一些有效可行的安全互锁条件,具体如下所示。
(1)7个流翻钢机都必须在回到原位。
否则移钢机禁止动作。
(2)移钢机未在原点位置,翻钢机禁止自动翻坯动作、移钢机无法自动启动运行。
(3)非接触式铸坯检测系统检测平台支架上的铸坯支数不等于设定的周期内数量时,移钢机禁止自动运行动作。
(4)在各流翻钢完毕、翻钢机回到原位后,方可将该流铸坯输送入冷床辊道。
3 结语
该功能自2013年11月从开发到投入使用以来,它的整个设备控制准确率、
设备运行完好率都达98%以上,满足实际工艺生产要求,并将该功能在全厂方坯连铸机上进行推广使用。
该功能的实现,进行一步提高了转炉厂连铸机自动化程度,优化操作水平,为转炉厂信息化工作创造良好条件。
同时满足了后期公司“方坯热送项目”的快速性、准确性的工艺要求。