上胶量的确定及测量
凝胶使用及用量计算公式

凝胶使用及用量计算公式凝胶是一种常见的药物剂型,它具有质地柔软、易于涂抹和吸收的特点,广泛应用于外用药物制剂中。
在使用凝胶时,正确的用量计算是非常重要的,因为用量不当可能会影响药物疗效,甚至产生不良反应。
本文将介绍凝胶的使用方法和用量计算公式。
一、凝胶的使用方法。
1. 清洁皮肤,在使用凝胶之前,首先要清洁皮肤,以确保皮肤表面干净。
可以用温水和肥皂轻轻清洁皮肤,然后用干净的毛巾擦干。
2. 取适量凝胶,根据医生或药师的建议,取适量凝胶涂抹在患处。
一般来说,取一颗豆大小的凝胶就可以覆盖一个手掌大小的区域。
3. 涂抹均匀,用手指将凝胶均匀涂抹在患处,轻轻按摩以帮助凝胶更好地被皮肤吸收。
4. 洗手,使用完凝胶后,要及时洗手,以防止药物残留在手上。
二、凝胶用量计算公式。
在使用凝胶时,正确的用量计算是非常重要的。
凝胶的用量计算通常根据患处面积和药物浓度来确定。
以下是常见的凝胶用量计算公式:1. 患处面积计算公式,患处面积(cm²)= 长(cm)×宽(cm)。
2. 药物用量计算公式,药物用量(g)= 患处面积(cm²)×药物浓度(g/cm ²)。
其中,药物浓度是指每单位面积所含药物的量,通常以克/平方厘米(g/cm²)为单位。
举例说明:假设患者患有面积为10平方厘米的湿疹,医生开具了一种药物浓度为0.1g/cm ²的凝胶,那么根据上述公式,可以计算出药物的用量为:药物用量(g)= 10(cm²)× 0.1(g/cm²)= 1g。
因此,患者在使用该凝胶时,应该取1g的凝胶涂抹在患处。
三、凝胶用量计算注意事项。
1. 注意药物浓度,在计算凝胶用量时,要注意药物的浓度,不同药物的浓度可能会有所不同,需要根据实际情况进行调整。
2. 遵医嘱使用,在使用凝胶时,应该遵循医生或药师的建议,按照医嘱使用适量的凝胶,不要随意增减用量。
高速注胶机胶量及同步调整(1)

高速注胶机胶量调整第一步-胶枪设置新设备使用或盖径变化时,需调整胶枪的高低、进出位置。
阀针闭合高度初始设定0.8mm 左右(经验值)。
①② ③④⑤第二步-注胶时间设定由于各工作头上的执行器电磁力与机械摩擦的差异,导致各工作头的单圈注胶时间也略有差异,在设定时间时根据实际情况来判定。
设定步骤:1. 设定操作参数(触摸屏)首先设定托盘转数(202盖型经验值2200),根据托盘转数换算托盘单圈所需时间(理论值),按理论时间设定单圈注胶时间。
2. 开机试注胶,根据实际注胶重叠情况对各工作头时间进行调整,直到实际注胶圈数达到2.1左右。
实际操作可能碰到的问题:1.肉眼无法明显分辨注胶重叠量。
1.1 通过切边距来判断(重叠部分的切边距相对不重叠部分要小)1.2 通过改变注胶圈数来判断,首先设定注胶时间为单圈的注胶时间(理论时间),此时在盖子上的胶圈重叠与否很容易判断,根据实际情况对各工作头的单圈注胶时间进行修正,然后再修改为实际2.1圈的注胶时间。
2.开机试车时无法准确判定出口的罐盖与工作头的对应关系。
2.1在触摸屏上会显示每次开机第一个开始的工作头编号,启动运行前先复位,此时显示编号为0,在按“启动运行”。
当然,在出口位置必须要有集盖装置(可以在进烘箱的磁轮集盖处取出试机的样盖)。
2.2在设备上的其中一个工作头上设置记号装置,这样会在经过此工作头的盖子上留下标记,以此为参考依据来判定盖子与工作头的对应关系。
注:此装置的使用会在盖子的中心处留下点状压痕!关于注胶延时:一般情况下本公司调试人员在调试时已有设定,用户无需在去改变。
它的意义有二方面,一是为了盖子到达上死点后有一定的稳定时间。
二是为了控制压头的注胶前旋转时间与注胶后旋转时间的相对比例(对有些用户很重要)。
第三步-胶量设定影响胶量的几个方面:1.胶枪内阀针的拔起高度。
阀针的拔起高度在一定范围内对胶量的影响成线性关系,所以设定合适的高度很重要。
一般不大于1.2mm比较合适。
上胶量的确定及测量解读
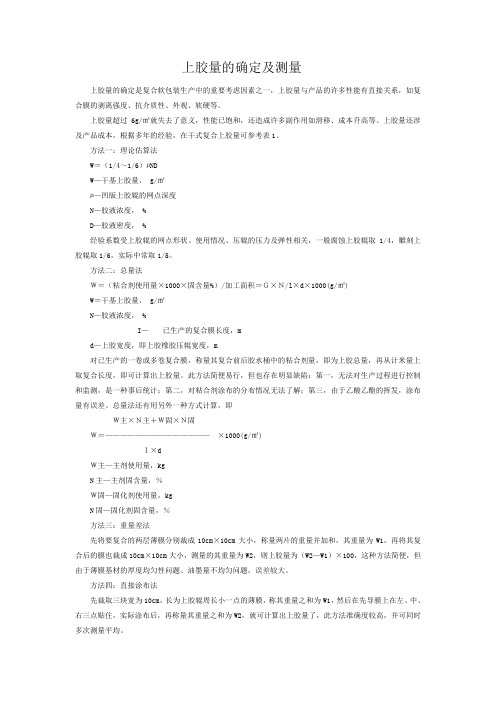
上胶量的确定及测量上胶量的确定是复合软包装生产中的重要考虑因素之一,上胶量与产品的许多性能有直接关系,如复合膜的剥离强度、抗介质性、外观、软硬等。
上胶量超过6g/㎡就失去了意义,性能已饱和,还造成许多副作用如滑移、成本升高等。
上胶量还涉及产品成本,根据多年的经验,在干式复合上胶量可参考表1。
方法一:理论估算法W=(1/4~1/6)µNDW—干基上胶量, g/㎡µ—凹版上胶辊的网点深度N—胶液浓度, %D—胶液密度, %经验系数受上胶辊的网点形状、使用情况、压辊的压力及弹性相关,一般腐蚀上胶辊取1/4,雕刻上胶辊取1/6,实际中常取1/5。
方法二:总量法W=(粘合剂使用量×1000×固含量%)/加工面积=G×N/l×d×1000(g/㎡)W=干基上胶量, g/㎡N—胶液浓度, %I—已生产的复合膜长度,md—上胶宽度,即上胶橡胶压辊宽度,m对已生产的一卷或多卷复合膜,称量其复合前后胶水桶中的粘合剂量,即为上胶总量,再从计米量上取复合长度,即可计算出上胶量。
此方法简便易行,但也存在明显缺陷:第一,无法对生产过程进行控制和监测,是一种事后统计;第二,对粘合剂涂布的分布情况无法了解;第三,由于乙酸乙酯的挥发,涂布量有误差。
总量法还有用另外一种方式计算,即W主×N主+W固×N固W=——————————————×1000(g/㎡)I×dW主—主剂使用量,kgN主—主剂固含量,%W固—固化剂使用量,kgN固—固化剂固含量,%方法三:重量差法先将要复合的两层薄膜分别裁成10cm×10cm大小,称量两片的重量并加和,其重量为W1,再将其复合后的膜也裁成10cm×10cm大小,测量的其重量为W2,则上胶量为(W2—W1)×100,这种方法简便,但由于薄膜基材的厚度均匀性问题、油墨量不均匀问题,误差较大。
学习情景五 干式复合上胶量的控制资料

涂胶辊压的选用
压力辊的目的是将印膜与涂布辊压实,使其涂布 均匀,不产生气泡。
涂胶辊压的选用
涂胶压辊的硬度与粘合剂的涂布
硬胶辊
软胶辊
硬度控制在80邵氏左右。
涂胶辊压的选用
涂胶压辊的压力与涂布状态
涂胶压辊
网纹辊
上 胶 量
压胶辊的选用
橡胶压辊的表面是否有损伤,有缺陷。
胶辊使用时间长了之后,表面缺乏弹性,有“硬化
上胶量的控制
练习2: 上胶量的操作演示。
涂胶装置
网线辊
网线辊涂胶原理: 网纹辊浸入胶盘,胶液注满网孔,离开胶液,表
面平滑处的胶液由刮刀刮去,网纹辊与涂胶基膜接触时,
在橡胶辊加压下,胶液转移到了基膜,利用胶液的流动 性,自动铺开流平,由网点变成均匀、连续。
网线辊参数
网线辊的深度与粘合剂的上胶量
d
d
H1
H2
浅网孔
深网孔
网线辊的深度越深,上胶量越多。
短时,胶黏剂的转移率也相应提高。
刮刀的调节
刮刀角度、刮刀距离可以通过调节刮刀架的升降
手轮及两个前后调节手轮来完成。
刮刀压力通过面板上的压力阀来调节。
练习1
1)刮刀角度变大
2)刮刀角度不变,距离变短 3)网纹辊的直径变大,刮刀的角度和距离不变
抹平辊
抹平辊的转速、压力、
抹平辊
胶辊
表面清洁度均关系到胶 黏剂的流平效果,抹平 辊的转动方向应与复合
”现象,出现此现象后,上胶时就容易有胶液往外溢出
,就容易产生粘边。 解决的办法将上胶辊置于50℃左右的熟化室内熟化1 ~2小时,使其表面恢复弹性,或者换新的胶辊。
压胶辊的选用
橡胶压辊宽度一般比薄膜宽度窄5-10mm。
胶质层指数测定方法

烟煤胶质层指数测定方法鹤壁冶金仪器公司—朱鸿雁烟煤胶质层指数测定包括最大胶质层厚度Y ,最终收缩度X 和体积变化曲线及焦块技术特征等指标,在我国现行的以炼焦煤为主的煤分类方案中,Y 值为分类指标之一。
一、仪器设备(应安装在专用通风柜中,前面设有上下开关式推拉门)1 、复式胶质层测定仪:有带平衡蛇和不带平衡馆的两种类型,HMS4 型为后一种类型.( l )煤杯其规格为:外径70mm;杯底内径59mm;从距杯底50mm处至杯口的内径为60mm:从杯底到杯口的高底110mm,煤杯用45 号钢制作。
煤杯内杯壁应当光滑,无条痕和缺凹,应定期检查平均直径相差不大于0.5mm。
杯底与杯体之间隙也不应大于0.5mm,杯底和压力盘,析气孔的布置详见GB479-2000 。
( 2 )胶质层层面探针(简称探针):探针直径为lmm ,下端为钝头。
刻度单位为lmm 。
精度0.1-0.2mm,对装好煤样尚未试验的煤杯,用探针测量其纸管部位置时,指针应指在刻度尺的零点上.( 3 )加热炉:由下、上部砖垛和电热元件组成电热元件采用硅碳棒.保证按规定的“在最初30min 内以8 ℃/分的升温度到250 ℃以后以3 ℃汾的速度升至730 ℃终止"。
( 4 )硅碳棒的规格要求(L270 或300mm代替)电压110V ,电流8 -20A;使用部分长度150mm,直径8mm:冷端长度60mm,直径16mm:灼热部分温度极限1200 -1400 ℃。
两电阻值相近的硅碳棒串联使用.( 5 )程控仪:附有时间显示,温度显示同时控制两煤样试验,操作方便,曲线重复性好。
(采用调压控温很难达到要求)( 6 )热电偶高温计:用K 型恺装热电偶测温.并每季校验一次。
( 7 )推焦器1 个,1.0 -5.0mm左棉垫若干,卷烟纸,小铲等。
二、煤样要求:1 、胶质层测定用煤样应符合下列规定:a .煤样缩制方法,按GB474 进行。
b .煤样应达到空气干燥状态。
干式复合上胶量的控制与测算

02
改进阶段
随着工业技术的发展,出现了涂胶机等专用设备,实现了涂胶量的精确
控制和自动化生产。
03
创新阶段
近年来,随着环保意识的提高和新型粘合剂的研发,上胶技术不断创新,
出现了水基粘合剂和无溶剂粘合剂等环保型产品,为包装行业的发展提
供了新的动力。
02 干式复合上胶量的影响因 素
基材特性
基材厚度
01
05 干式复合上胶量控制与测 算的挑战与解决方案Βιβλιοθήκη 上胶不均匀问题总结词
上胶不均匀是干式复合工艺中常见的问题,会导致产品质 量下降。
详细描述
上胶不均匀通常是由于涂胶系统设计不合理、涂胶装置调 整不当或涂胶材料性质不均一所致。它会导致薄膜表面涂 胶量差异较大,影响产品的外观和性能。
解决方案
为了解决上胶不均匀问题,可以优化涂胶系统设计,调整 涂胶装置,确保涂胶材料性质均一。同时,定期检查和维 护涂胶系统,确保其正常工作。
降低了不良品率,并提高了生产效率。
案例二:某品牌产品上胶量稳定性提升
要点一
总结词
要点二
详细描述
通过严格控制原材料质量和工艺参数,提高上胶量稳定性
某品牌产品在干式复合过程中,对上胶量的稳定性要求极 高。为了达到这一要求,他们对原材料质量和工艺参数进 行了严格的控制,包括对上胶液的粘度、固含量、PH值等 参数进行精确测量和控制,同时对涂布轮转速、涂布压力 、烘干温度等工艺参数进行优化调整。通过这些措施,他 们成功地提高了上胶量的稳定性,保证了产品质量和客户 满意度。
06 实际应用案例分析
案例一:某公司上胶量控制优化
总结词
通过改进上胶工艺和设备,提高上胶量精度 和稳定性
详细描述
干式复合上胶量的确定及测量
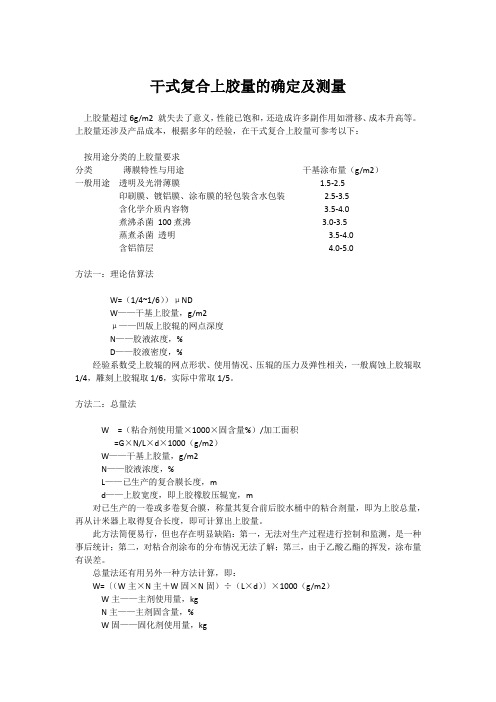
干式复合上胶量的确定及测量上胶量超过6g/m2 就失去了意义,性能已饱和,还造成许多副作用如滑移、成本升高等。
上胶量还涉及产品成本,根据多年的经验,在干式复合上胶量可参考以下:按用途分类的上胶量要求分类薄膜特性与用途干基涂布量(g/m2)一般用途透明及光滑薄膜 1.5-2.5印刷膜、镀铝膜、涂布膜的轻包装含水包装 2.5-3.5含化学介质内容物 3.5-4.0煮沸杀菌100煮沸 3.0-3.5蒸煮杀菌透明 3.5-4.0含铝箔层 4.0-5.0方法一:理论估算法W=(1/4~1/6))μNDW——干基上胶量,g/m2μ——凹版上胶辊的网点深度N——胶液浓度,%D——胶液密度,%经验系数受上胶辊的网点形状、使用情况、压辊的压力及弹性相关,一般腐蚀上胶辊取1/4,雕刻上胶辊取1/6,实际中常取1/5。
方法二:总量法W=(粘合剂使用量×1000×固含量%)/加工面积=G×N/L×d×1000(g/m2)W——干基上胶量,g/m2N——胶液浓度,%L——已生产的复合膜长度,md——上胶宽度,即上胶橡胶压辊宽,m对已生产的一卷或多卷复合膜,称量其复合前后胶水桶中的粘合剂量,即为上胶总量,再从计米器上取得复合长度,即可计算出上胶量。
此方法简便易行,但也存在明显缺陷:第一,无法对生产过程进行控制和监测,是一种事后统计;第二,对粘合剂涂布的分布情况无法了解;第三,由于乙酸乙酯的挥发,涂布量有误差。
总量法还有用另外一种方法计算,即:W=〔(W主×N主+W固×N固)÷(L×d)〕×1000(g/m2)W主——主剂使用量,kgN主——主剂固含量,%W固——固化剂使用量,kgN固——固化剂固含量,%方法三:重量差法先将要复合的两层薄膜分别裁成10cm×10cm大小,称量两片的重量并相加,其重量为W1,再将其复合后的膜也裁成10cm×10cm大小,测量的其重量为W2,则上胶量为(W2-W1)×100,这种方法简便,但由于薄膜基材的厚度均匀性问题、油墨量不均匀问题,误差较大。
浸渍纸检测和大板现场试验及养生

浸渍胶膜纸检测方法、标准和大板现场试验及养生一、浸渍纸检测方法及标准1检测方法1.1上胶量检测方法在浸渍纸宽度方向裁取左中右三小块浸渍纸(面积分别为100㎝2),编好号,置于电子称上称重。
然后根据以下公式计算出上胶量,并计算出平均上胶量。
公式:上胶量%=(浸渍纸重-浸渍纸定量重) ÷浸渍纸定量重╳100%1.2挥发份检测方法将测好上胶量的三小块浸渍纸置于160±2℃的烘箱中烘5min,取出放在干燥器内冷却5min,待冷却后马上拿出称重。
然后根据以下公式计算出挥发份,并计算出平均挥发份。
公式:挥发份%=(浸渍纸干前重-浸渍纸干后重) ÷浸渍纸干前重╳100%1.3预固化度检测方法在浸渍纸宽度方向裁取左中右各2组小块浸渍纸(100╳100mm),取一组将3个试件放入160±2℃的烘箱中烘10min, 取出放在干燥器内冷却5min,冷却后马上称重,计算出挥发份。
另一组置于40±1℃的恒温水浴中浸泡20 min,然后取出晾干5min,再放入160±2℃的烘箱中烘10min, 取出放在干燥器内冷却5min,待冷却后马上称重。
然后根据以下公式计算出挥发份,并计算出平均挥发份。
公式:预固化度%=(浸渍纸浸泡干后重-浸渍纸定量重) ÷(浸渍纸浸泡前重-浸渍纸浸泡前重╳挥发份-浸渍纸定量重)╳100%或预固化度%=(浸渍纸浸泡干后重-浸渍纸定量重) ÷(浸渍纸浸泡前干后重-浸渍纸定量重)╳100%2、浸渍纸技术指标要求见表1注:刮边宽度≤8mm。
2.1规格尺寸要求:2.1.1 宽度:1260mm 公差0mm、+10mm。
2.1.2长度:2470mm 公差:0mm、+10mm。
2.1.3 对角线差≤5mm。
2.1.4 装饰纸切割方式按要求MARK/长度切割。
2.1.5 装饰纸浸渍膨胀量要求2.1.6长度要求0.4-0.7%2.1.7宽度要求2.2储存期:2.2.1 储存条件:温度≤25℃、相对湿度30%-70%。
- 1、下载文档前请自行甄别文档内容的完整性,平台不提供额外的编辑、内容补充、找答案等附加服务。
- 2、"仅部分预览"的文档,不可在线预览部分如存在完整性等问题,可反馈申请退款(可完整预览的文档不适用该条件!)。
- 3、如文档侵犯您的权益,请联系客服反馈,我们会尽快为您处理(人工客服工作时间:9:00-18:30)。
上胶量的确定及测量
上胶量的确定是复合软包装生产中的重要考虑因素之一,上胶量与产品的许多性能有直接关系,如复合膜的剥离强度、抗介质性、外观、软硬等。
上胶量超过6g/㎡就失去了意义,性能已饱和,还造成许多副作用如滑移、成本升高等。
上胶量还涉及产品成本,根据多年的经验,在干式复合上胶量可参考表1。
方法一:理论估算法
W=(1/4~1/6)µND
W—干基上胶量, g/㎡
µ—凹版上胶辊的网点深度
N—胶液浓度, %
D—胶液密度, %
经验系数受上胶辊的网点形状、使用情况、压辊的压力及弹性相关,一般腐蚀上胶辊取1/4,雕刻上胶辊取1/6,实际中常取1/5。
方法二:总量法
W=(粘合剂使用量×1000×固含量%)/加工面积=G×N/l×d×1000(g/㎡)
W=干基上胶量, g/㎡
N—胶液浓度, %
I—已生产的复合膜长度,m
d—上胶宽度,即上胶橡胶压辊宽度,m
对已生产的一卷或多卷复合膜,称量其复合前后胶水桶中的粘合剂量,即为上胶总量,再从计米量上取复合长度,即可计算出上胶量。
此方法简便易行,但也存在明显缺陷:第一,无法对生产过程进行控制和监测,是一种事后统计;第二,对粘合剂涂布的分布情况无法了解;第三,由于乙酸乙酯的挥发,涂布量有误差。
总量法还有用另外一种方式计算,即
W主×N主+W固×N固
W=——————————————×1000(g/㎡)
I×d
W主—主剂使用量,kg
N主—主剂固含量,%
W固—固化剂使用量,kg
N固—固化剂固含量,%
方法三:重量差法
先将要复合的两层薄膜分别裁成10cm×10cm大小,称量两片的重量并加和,其重量为W1,再将其复合后的膜也裁成10cm×10cm大小,测量的其重量为W2,则上胶量为(W2—W1)×100,这种方法简便,但由于薄膜基材的厚度均匀性问题、油墨量不均匀问题,误差较大。
方法四:直接涂布法
先裁取三块宽为10cm,长为上胶辊周长小一点的薄膜,称其重量之和为W1,然后在先导膜上在左、中、右三点贴住,实际涂布后,再称量其重量之和为W2,就可计算出上胶量了,此方法准确度较高,并可同时多次测量平均。
方法五:溶剂清除法:
将薄膜的未处理面与未处理复合在一块。
裁取此复合膜10cm×10cm,称重量为W1。
将复合膜剥开后,再用乙酸乙酯将膜上的粘合剂擦拭干净,并称两块膜的重量之和为W2则
涂布量=(W2—W1)×100
此方法须把粘合剂擦干净并等溶剂完全挥发后再测量重量。
此方法准确度较高,并可测量上胶分布的均匀度。