统计过程控制(SPC)
统计过程控制(SPC)
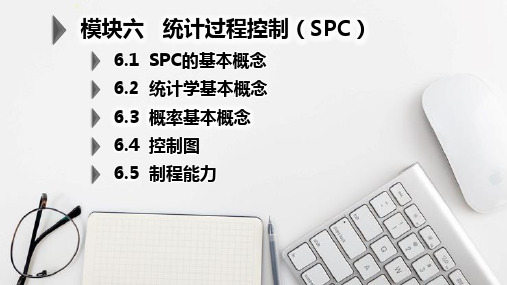
足公司管理需求作用。
6.2 统计学基本概念
6.2.1 统计学基础
母体指某家特定工厂所生
产的商品。
母体的子集代替研究母体
的每一笔资料,称做样本。
以某种经验设计实验所搜
集的样本叫做资料。
图6-4 统计学原理
利用推论统计学方法,将资料中的数据建模,计算它的机率并且做出对于母
常常是不经济的。
如果目前的产品不能满足顾客的要求,则有必要将所有的产品进行分类,
报废不合格品或返工。这种状态将持续到对过程采取必要的校正措施并验证,或
持续到产品更改为止。
在统计质量控制(SQC-Statistical Quality Control)过程中,引起质量波
动的原因主要来自六个方面(5M1E):
体的推论。
这个推论可能以对/错问题的答案所呈现(假设检定),对数字特征量的估
计,对未来观察的预测,对关联性的预测(相关性),或是将关系模型化。
在统计学中,其基本要素包括:
1. 母体与样本的关系
母体和样本的概念不是固定不便的,随着研究的不同,母体和样本也会有所
不同。
2. 指标与标志的区别
指标是说明总体特征;而标志是说明总体单位特征的。标志可以分为不能用
以下几个阶段:
第一阶段:
SPC--统计过程控制,可判断过程的异常,及时告警;不能告知此异常是什
么因素引起的。
第二阶段:
SPCD--统计过程控制与诊断,SPCD既有告警功能,又有诊断功能。
第三阶段:
SPCDA--统计过程控制、诊断与调整,它能控制产品质量、发现异常并诊
断导致异常的原因、自动进行调整。
统计过程控制(SPC)
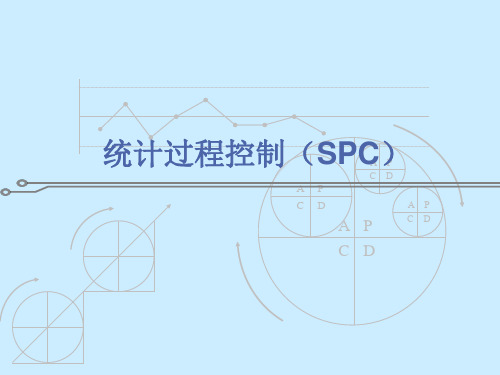
CD
AP
CD
AP
AP
CD
CD
统计过程控制(SPC)
SPC的基本概念 控制图原理 常规(休哈特)控制图 控制图的判断准则 常用控制图的计算 通用控制图 过程能力与过程能力指数
统计过程控制(SPC)
SPC的基本概念
• SPC的涵义 SPC是英文Statistical Process Control(统计过程控制)
C B A
准则:连续9点落在中心线同一側。
LCL
准则:连续6点递增或递减。
准则:连续14点中相邻点上下交替。
准则:连续3点中有2点落在中心线同一側的B区之外。
准则:连续5点中有4点落在中心线同一側的C区之外。
准则:连续15点在C区的中心线上下。
准则:连续8点在中心线两側,但无一在C区中。
统计过程控制(SPC)
统计过程控制(SPC)
• 控制图的作用 控制图的作用是:及时告警。体现SPC与SPD的贯彻
预防原则。 控制图是SPC与SPD的重要工具,用以直接控制与诊断 过程,故为质量管理七个工具的核心。
质量管理七个工具:因果图(Cause-effect diagram), 排列图(Pareto diagram),直方图(Histogram),散 步图(Scatter diagram),控制图(Control chart),分 层法(Stratification),检查表(Check list)。 贯彻预防原则的“20字方针”:
u控制图的控制线为:
UCL = u + 3 u / n CL = u
LCL = u - 3 u / n
式 否中则:控u制=线 呈ci /凹凸ni 状,。ci为样本的不合格数。样本容量n最好恒定,
统计过程控制(SPC)

(三) x R 控制图的操作步骤
1. 确定控制对象(统计量) 2. 收集k组预备数据(一般K=25;每组数
据个数n ≥ 2;遵循合理子组原则) 3. 计算每一个样本的均值 X i 与极差 Ri 。 4. 计算 X与R 5. 计算R图控制限并作图 6. 用各样本点绘在图中,判断状态。
分析过程若失控或异常,找出原因, 进行纠正,防止再发生。
7. 计算 X 图控制限并作图,判断状态。 8. 计算过程能力指数验证是否符合要求 9. 延长控制限,作控制用控制图,进行日
常管理
四、 X S 图(掌握) 五、X-Rs图(了解)
六、Me-R图(了解)
七、P控制图
(一)P控制图的控制状态
P 常数
n
n
ˆp p di / ni
i1 i1
(二)P控制图的统计基础为二项分布,其
内容 (1)利用控制图分析过程的稳定性,对
过程存在的异常原因进行预警;
(2)计算过程能力指数分析稳定的过程 能力满足技术要求的程度,对过程质量进行 评价。
三、统计过程控制的特点 是一种预防性的方法 贯彻预防原则是现代质量管理的核心 强调全员参与
SPC的涵义
为了贯彻预防原则,应用统计技术对 过程各阶段评估和监控,建立并保持过程 处于可接受的并且稳定的水平从而保证产 品与服务符合规定的要求的一种质量管理 技术。
过程能力指数 过程性能指数
CP
TU TL 6ˆ ST
PP
TU TL 6ˆ LT
其中 ˆ St —— 短期波动的标准差估计,在稳态
下计算
ˆ St
R d2
或
S C4
ˆ Lt —— 长期波动的标准差估计,在实
际情况下计算 ˆ Lt S
统计过程控制SPC

0.256
1.744
3.258
0.283
1.717
3.336
0.307
1.693
3.407
0.328
1.672
3.472
0.347
1.653
3.532
0.363
1.637
3.588
0.378
1.622
3.640
0.391
1.608
3.689
0.403
1.597
3.735
SPC统计过程控制

SPC统计过程控制SPC(Statistical Process Control,统计过程控制)是一种基于统计原理和数据分析方法的质量管理工具,用于监控和控制生产过程中的变异性,以确保产品或服务的质量。
SPC是由质量概念的先驱沃尔特·A·谢温(Walter A. Shewhart)在20世纪20年代初首次引入的。
它的目的是通过使用统计技术来分析生产过程中的数据,从而减少产品或服务的变异性,提高整体质量水平。
SPC的基本原理是通过统计分析来了解生产过程中的变异性,以便及时采取措施来纠正和调整生产过程。
它主要包括以下步骤:1.确定控制指标:选择适当的指标来监控生产过程的变异性。
常用的指标包括尺寸、重量、硬度等。
2.收集数据:根据预定的采样计划和频率,定期收集生产过程中的数据。
数据可以通过各种手段收集,如直接测量、抽样检验等。
3.绘制控制图:使用统计方法将收集到的数据绘制成控制图。
控制图是一种图表,它显示了一个或多个过程指标的变化情况,以及上下限范围。
通过观察控制图,人们可以判断生产过程是否处于控制状态,是否存在异常情况。
4.分析控制图:根据控制图上的变化趋势和模式,进行统计分析,以确定生产过程的绩效。
常用的统计分析方法包括均值、标准差、极差等。
5.制定改进措施:根据分析的结果,确定需要改进的方面,并制定相应的措施。
改进措施可以包括修改生产过程参数、调整设备、培训员工等。
6.监控和调整:持续监控生产过程,并根据需要进行调整,以确保控制图保持在预定的限制范围内。
SPC的优势在于它能够提供实时和持续的监控生产过程的能力。
通过采集数据和绘制控制图,生产者可以及时发现生产过程中的变异,并采取措施进行纠正。
这样可以防止不良品的产生,并提高产品或服务的一致性和质量。
此外,SPC还具有以下几点优势:1.提高生产效率:通过控制和减少生产过程中的变异性,SPC可以提高生产效率。
它能够帮助生产者发现并消除生产过程中的浪费和不必要的变动,从而提高生产效率和资源利用率。
统计过程控制

统计过程控制统计过程控制(SPC)是一种基于数据分析的质量管理方法,旨在通过对过程的监测与控制,实现生产过程中的连续改进。
这种方法可以帮助提高产品质量,降低生产成本,提高客户满意度。
以下是SPC的简介、使用方法、益处以及实现过程中可能存在的问题。
简介SPC的理念是“控制过程而不是修理产品”,它的核心是把质量管理的重点从检查和纠正缺陷转移到控制过程。
SPC主要应用于制造业,但也适用于服务业和医疗行业等其他领域。
通过数据收集、分析和监控,SPC可以帮助企业了解其生产过程并制定相应的改进计划,从而实现生产效率和产品质量的提高。
使用方法SPC主要包括数据的收集和分析两个阶段。
数据的收集通常是由受训人员通过抽样等方式获取,然后数据会被汇总到一个控制图表中。
控制图表是SPC最基本的工具,它可以反映生产过程中数据的变化情况,通过样本数据的变化来判断是否存在特殊因素,以及是否需要采取相应的措施来防止这些因素的再次出现。
在数据分析阶段,SPC通常使用各种统计方法来分析数据的规律性和变动性,从而确定过程的性能是否符合要求。
如果发现过程出现特殊的变化,就需要针对这些问题采取相应的措施。
然后,通过监控过程的稳定性和性能,来确保所采取的措施有效。
益处SPC的主要益处是提高质量和降低成本。
由于SPC持续地跟踪和分析数据,可以及时发现问题,并采取相应的措施。
这减少了产品缺陷率和因此而导致的重新工作或返工数量。
此外,SPC还可以提高生产效率,因为它可以减少生产中的浪费和停机时间,并优化制造工艺。
此外,SPC还可以增加生产过程的可持续性,使过程更加稳定,从而提高客户满意度。
实现过程中可能存在的问题尽管SPC被广泛运用于生产领域,但在实施过程中仍然存在一些问题。
例如,如果质量数据不正确或不完整,则无法有效地检测和纠正问题。
确保收集到正确和完整的数据非常重要。
另一个问题是寻找和培养高素质的SPC人才。
虽然有许多SPC工具和软件可以帮助质量控制人员更好地应用SPC,但必须确保员工已经得到了适当的培训,以确保他们理解SPC的基本概念和运用方法。
统计过程控制(SPC)
21
22
1447
1720
1278
1472
2272
2190
1480
1859
1619.25
1810.25
994
718
903
903
2060.6
2060.6
0
0
23
24 25
829
429 1479
1613
312 1529
719
1408 1217
1758
1236 1729
1229.75
846.25 1488.5
SPC(统计过程控制)
根据上海思科统计质量咨询服务有限公司 俞钟行老师讲课整理
内容:
1.SPC(统计过程控制)概述 2.Xbar-R控制图和Xbar-s控制图 3.XmR(即X-RS)控制图 4.分析用控制图和控制用控制图 5.过程能力指数Cp、Cpk 6.过程性能指数Pp、Ppk 7.p控制图(含标准化的应用) 8.控制图判异准则 9.应用和滥用SPC(统计过程控制) 10.测试设备校正(美国“质量”杂志SPC案例2001年) 11.短流程的加工(美国“质量”杂志SPC案例2000年)
n
A3
2 2.659 0 3.267
3 1.954 0 2.568
B3
B4
计算结果(1)
Number 1 2 3 4 5 S 412.8 142.5 494.9 550.9 291.5 Sbar 405.3 405.3 405.3 405.3 405.3 B4Sbar 918.4 918.4 918.4 918.4 918.4 B3Sbar 0 0 0 0 0 Xbarbar 1400.96 1400.96 1400.96 1400.96 1400.96 Xbar+a3Sbar 2060.796172 2060.796172 2060.796172 2060.796172 2060.796172 Xbar-a3Sbar 741.1238285 741.1238285 741.1238285 741.1238285 741.1238285 Xbar 1182.5 1125.5 1435.5 1050.25 1062.25
统计过程控制(SPC)
9.94 9.81 9.85 10.11 10.24 10.17 9.83 10.33 10.39 9.64
10.42 10.13 9.61 10.03 10.60 10.00 9.55 10.15 10.16 9.88
10.30 10.21 10.03 10.15 9.58 10.09 9.87 9.91 9.73 10.02
Mo=1
2 12.67
3.56
练习
数列:12,11,12,13,18,30,24,9 请计算下列统计量:
R
X
Md
Mo
2
数据的收集与整理
群体
行 动
结论
抽样 分析
样本 测 试
数据
每件产品的尺寸与别的都不同
范围
范围
范围
范围
但它们形成一个模型,若稳定,可以描述为一个分布
量具精确度是指测量观察平均值与真实值(基准值) 的差异。 真实值由更精确的测量设备所确定
测量系统变差
量具重复性
量具重复性是由一个操作者采用一种测量 仪器,多次测量同一零件的同一特性时获得的 测量值变差。
测量系统变差
量具再现性
量具再现性是由不同的操作者,采用相同 的测量仪器,测量同一零件的同一特性时测量 平均值的变差。
Statistical Process Control
(统计过程控制)
统计过程控制(SPC)
1、SPC的发展史 2、基本统计概念 3、过程变差 4、控制图 5、过程控制和过程能力
SPC的发展
20世纪20年代,美国休哈特提出; 二战后期,美国将休哈特方法在军工部门推行; 1950~1980,逐渐从美国工业中消失 ;休哈
统计过程控制(SPC)
1.分析过程阶段 通过PFMEA、小组会议、与主管专家、操作人员 的商讨,对控制图的分析,变差特殊原因与 普通原因的识别等技术,达到对过程现有状况的 了解。并回答下列问题: 本过程应做什么? 会出现什么问题? 本过程正在做什么?是否在生产废品和需返工产品? 本过程是否处于统计控制状态? 本过程是否有能力?是否可靠?
4.两种过程能力研究:长期研究和短期研究 短期过程能力研究是从一个操作循环中获取的测量 为基础,在判定该过程没有发现特殊原因,可以计 算短期能力指数。其用途: ①验证首批产品; ②机器能力研究; ③验证一个新的或经修改的过程的实际性能是否符 合工程参数。 长期过程能力研究是通过长时间进行测量所收 集的数据为基础,其用途是用来描述过程在很长时 间内的变差原因出现后能否满足顾客要求的能力。
八、控制图的益处
1.便于操作者在现场使用; 2.有助于过程在质量上和成本上持续地、可预测地 保持; 3.当过程处于统计控制状态,可以通过减少普通原 因和调整过程中心线,提高质量和降低成本; 4.提供有关过程特性能信息交流的共同语言。 5.通过区分变差的普通原因和特殊原因,为确定采 取局部措施还是系统措施提供依据。减少问题的混 淆、时间和资源的浪费。
二、收集数据
1.选择子组容量、频率、子组数
①在X—R控制图中,子组的容量是恒定的。
②每隔一定的周期(如15min或每班两次)抽取子组。 ③足够的子组数可以确保发现变差的主要原因。一般情 况下,至少应满足:25个子组,100个数据。
统计过程控制(SPC)
解:
于是,过程能力指数为:
过程能力不够充分,从图2发现分布中心μ=0.1968与规范中心M=(TU+TL)/2=0.1720有偏离,应进行调整。调整后,Cp值会有所提高。
单侧规范情况的过程能力指数
01
只有上限要求,而对下限没有要求: 只适用于的范围:
02
只有下限要求,而对上限没有要求: 只适用于的范围:
4
3
6
5
判稳准则的分析 判稳准则的思路
打一个点未出界有两种可能性:
► 过程本来稳定 ► 漏报 (这里由于α小,所以β大),故打一个点子未出界不能立即判稳。
在点子随机排列的情况下,符合下列各点之一判稳:
01
► 连续25个点,界外点数d=0;
02
► 连续35个点,界外点数d<0;
03
► 连续100个点,界外点数d<2。
0.1821
0.1828
0.0086
18
0.1812
0.1585
0.1699
0.168
0.1694
0.0227
19
0.1700
0.1567
0.1694
0.1702
0.1666
0.0135
20
0.1698
0.1664
0.17
0.16
0.1666
0.01
图1
μ’
μ
图2-7 正态曲线随着标准差变化
σ=2.5
σ=1.0
σ=0.4
y
x
不论μ与σ取值为何,产品质量特性值落在[μ-3σ,μ+3σ]范围内的概率为99.73%。 图2-8 正态分布曲线下的面积
- 1、下载文档前请自行甄别文档内容的完整性,平台不提供额外的编辑、内容补充、找答案等附加服务。
- 2、"仅部分预览"的文档,不可在线预览部分如存在完整性等问题,可反馈申请退款(可完整预览的文档不适用该条件!)。
- 3、如文档侵犯您的权益,请联系客服反馈,我们会尽快为您处理(人工客服工作时间:9:00-18:30)。
11
控制图的选择
控制图的选定
计量值 数据性质
计数值
平均值
“n”=10~25 “n”是否较大
n≧1 样本大小 n≧2
Cl的性质
中位数 “n”=2~5
“n”=1
不良数
缺陷数
不良数或
缺陷数
不一定
一定
“n”是否一定
单位大小 是否一定 不一定 一定
X-s 图
X-R 图
X-R
X-Rm “p”
图
图图
“np” “c”
数据类别: 计数值数据:只以缺陷数和个数表示,不能连续取值的数据 计量值数据:以产品本身的特性来表示,可以连续取值的数据
2
两种变异
普通性(特定性)变异:不易避免的原因(普通 原因)造成的变异,如操作人员的熟练程度的 差异、设备精度与保养好坏的差异、同批原材 料本身的差异
特殊性(偶尔性)变异:可以避免也必须避免 的原因(特殊原因)造成的变异,如不同原材料 之间的差异、设备故障
“u”
图图
图
12
案例1(控制图的选择)
质量特性 长度 重量 乙醇比重 电灯亮/不亮 每一百平方米的 脏点
样本数 5 10 1
100 100平方米
选用什么图
13
答案1
质量特性 长度 重量 乙醇比重 电灯亮/不亮 每一百平方米的 脏点
样本数 5 10 1
100 100平方米
选用控制图 均值极差控制图
通常用来消除变差的普通原因 几乎总是要求管理措施,以便纠正 大约可纠正85%的过程问题
8
控制图的目的
控制图和一般的统计图不同,因其不仅能 将数值以曲线表示出来,以观其变异之趋 势,且能显示变异系属于机遇性或非机遇 性,以指示某种现象是否正常,而采取适 当之措施。
9
控制图的目的
及时发现工序过程中所出现的普通、特殊原因 引起的变异;
Xbar均值控制图
数据点(时间顺序排列)
控制上限 UCL 控制中心CL
控制下限LCL
21
管制界限和规格界限
规格界限:是用以说明品质特性之最大许 可值,来保证各个单位产品之正确性能。
管制界限:应用于一群单位产品集体之量 度,这种量度是从一群中各个单位产品所 得之观测值所计算出来者。
22
过程控制和过程能力
统计过程控制(SPC)
第一部分:SPC基础知识
统计过程控制的定义 统计过程控制是利用统计方法,分析工序质量特征,使工序处
于受控状态,系统地减小工序质量特征值的变异.它是英文 Statistical Process Control的缩写形式
数据-用作推理、讨论和计算基础的真实信息;被提供或承 认可作为结论基础的事实和真实情况.
5
普通原因与特殊原因
普通原因:是造成随着时间推移具有稳定的且可 重复的分布过程中的许多变差的原因,我们称之 为:“处于统计控制状态”、“受统计控制”, 或有时简称“受控”,普通原因表现为一个稳定 系统的偶然原因。只有变差的普通原因存在且不 改变时,过程的输出才可以预测。
特殊原因:指的是造成不是始终作用于过程的变 差的原因,即当它们出现时将造成(整个)过程的 分布改变。除非所有的特殊原因都被查找出来并 且采取了措施,否则它们将继续用不可预测的方 式来影响过程的输出。如果系统内存在变差的特 殊原因,随时间的推移,过程的输出将不稳定。
ACT
DO
STUDY
PLAN
2.控制过程 •监控过程性能 •查找变差的特殊原 因并采取措施
DO
ACT
STUDY
PLAN
DO
ACT
STUDY
3.改进过程 •改变过程从而更好 地理解普通原因变 差 •减少普通原因变差
27
第二部分:控制图的基本运用
控 制合图理的使益用处控制图能
供正在进行过程控制的操作者使用 有利于过程在质量上和成本上能持续地,可预测地保
k
k
1
•e(
x)2 2 2
2 •
e 2.718
μ+k σ
17
控制图原理
μ± kσ μ± 0.67σ
μ± 1σ μ± 1.96σ
μ± 2σ μ± 2.58σ
μ± 3σ
在内的概率 50.00% 68.26% 95.00% 95.45% 99.00% 99.73%
在外的概率 50.00% 31.74% 5.00% 4.55% 1.00% 0.27%
均值标准差控制图 单值移动极差控制图
不良数控制图 缺陷数控制图
14
控制图绘制流程
搜集数据 绘解析用控制图
是否稳定
寻找异常原因
绘直方图 是否满足规格
检讨机械、设备 提升制程能力
控制用控制图
15
计量值的分布表达
位置:中心值 形状:峰态 分布宽度
16
控制图原理说明
群体 平均值=μ 标准差=σ
抽樣
μ-k σ μ
确定工序质量水平得以改进的局部和系统措施; 使过程达到更高的质量、更低的单件成本和更
高的有效能力。
利用控制界限判断 是否为特殊性变异
10
控制图种类(以数制图 均值-标准差控制图 中位数-极差控制图
单值-移动极差控制 图
计数值控制图
不良率控制图 不良数控制图 缺陷数控制图 单位缺陷数控制图
18
正态分布概率
99.73% 95.45%
68.26% -3σ -2σ -1σ μ +1σ +2σ +3σ
19
控制图原理
x
3
x
x
3 x
3 x
x 3
x
上 控 制 限 UCL 中心線
下 控 制 限 LCL
个别值的正态分布 平均值的正态分布 控制图的正态分布
20
控制图的组成
*垂直轴----质量特征值 *水平轴----抽取的样本号 *中心线(CL) *上下控制限(UCL和LCL) *规格线Tu和Tl
满足要求 可接受
控制
不可接受
受控
1类 2类
不受控
3类 4类
简言之,首先应通过检查并消除变差的特殊原因使过程处于 受统计控制状态,那幺其性能是可预测的,就可评定满足顾 客期望的能力。
23
24
制程的组成以及其波动的原因
材料
機器
人
環境
測量
方法
波动原因
25
持续改进
26
过程改进循环
1、分析过程 •本过程应做什幺? •会出现什幺问题? PLAN •本过程正在做什幺? •达到统计控制状态 •确定能力
6
普通原因与特殊原因举例
合格原料的微小变化 机械的微小震动
气候、环境的微小变 化等等
使用不合格原料 设备调整不当
新手作业,违背操作 规程
刀具过量磨损等等
7
局部措施和对系统采取措施
局部措施
通常用来消除变差的特殊原因 通常由与过程直接相关的人员实施 大约可纠正15%的过程问题
对系统采取措施
持下去 使过程达到