层状撕裂
浅谈焊接层状撕裂裂纹的成因和防治办法

浅谈焊接层状撕裂裂纹的成因和防治办法摘要:随着钢铁、石油化工、造船、轨道交通和电力等工业的发展,在焊接结构方面都趋向大型化、大容量和高参数的方向发展,有的还在低温、深冷、腐蚀介质等环境下工作。
因此,各种低合金高强钢,中、高合金钢、超强钢,以及各种合金材料的应用日益广泛。
但是随着这些钢种和合金的应用,在焊接生产上带来许多新的问题,其中较为普遍而又十份严重的就是焊接裂纹。
焊接过程中所产生的裂纹有多种多样,就目前的研究,按产生裂纹的本质来分,大体上可分为以下五大类:热裂纹、再热裂纹、冷裂纹、层状撕裂、应力腐蚀裂纹等,其中层状撕裂裂纹的危害性更为严重,由于层状撕裂在外观上没有任何迹象,无损检测手段又较难发现,即使能判断结构中又层状撕裂也很难修复,造成巨大经济损失,特别严重的是层状撕裂引起的事故往往是灾难性的。
如何防止层状撕裂的发生,是焊接应用中的一项重要课题。
关键词:焊接裂纹层状撕裂层状撕裂是一种内部的低温开裂。
仅限于厚板的母材金属或焊缝热影响区,多发生于“L”、“T”、“+”型接头中。
其定义为轧制的厚钢板沿厚度方向塑性不足以承受该方向上的焊接收缩应变而发生于母材的一种阶梯状冷裂纹。
一般是由于厚钢板在轧制过程中,把钢内的一些非金属夹杂物轧成平行于轧制方向的带状夹杂物,这些夹杂物引起了钢板在力学性能上的各向导性。
防治层状撕裂在选材上可以选用精练钢,即选用z向性能高的钢板,也可以改善接头设计形式,避免单侧焊缝、或在承受z向应力的一侧开出坡口。
1、层状撕裂的特点层状撕裂与冷裂不同,它的产生与钢种强度级别无关,主要与钢中的夹杂量和分布形态有关。
一般轧制的厚钢板,如低碳钢、低合金高强钢,甚至铝合金的板材中也会出现层状撕裂。
根据层状撕裂产生的位置大体可以分为三类:第一类是在焊接热影响区焊趾或焊根冷裂纹诱发而形成的层状撕裂。
第二类是焊接热影响区沿夹杂开裂,是工程上最常见的层状撕裂。
第三类远离热影响区母材中沿夹杂开裂,一般多出现在有较多MnS的片状夹杂的厚板结构中。
层状撕裂的防止

层状撕裂的防止一概述厚度较大的钢板在轧制过程中存在各向异性。
经过轧制之后,钢板内部由硫、磷偏析产生的杂质和其它非金属夹杂物被压成薄片,出现分层(夹层)现象。
分层使钢板厚度方向受拉的性能恶化,并有可能在焊缝收缩或在拉力作用下出现层间撕裂。
层状撕裂主要发生在T形、十字形和角部接头中,这些部件约束程度大,使母材在厚度方向引起应变,由于延性有限无法调节,当钢板存在分层缺陷时,容易发生层间撕裂。
结构复杂,焊缝集中的节点,约束大,如刚接框架节点域中柱的翼缘板也可能产生层状撕裂。
二层状撕裂的起因由前述可知,层状撕裂主要由两个原因共同促成,即:①钢板存在分层缺陷;②在钢板分层处表面焊接和(或)其厚度方向有外拉力作用。
三防止层关撕裂的措施我国《建筑抗震设计规范》GB50011-2001和《高层民用钢结构技术规范》JBJ99-88等均有对焊接连接的节点,当钢板厚度大于50(或40)mm,并承受沿厚度方向的拉力作用时,应采用厚度方向性能钢板(抗层间撕裂的Z向钢板)的条款。
但是,Z向钢板目前产量较小,价格也比普通钢板高很多,而且采用质量好的钢板并不能消除焊缝收缩,也不一定能防止高约束节点处的层状撕裂,仅能减少层状撕裂的危险性。
因此,防止层状撕裂问题,必须从设计、制造工艺和检查等方面综合考虑。
要做到与焊接材料协调,可能产生层状撕裂的节点,设计时应考虑使其节点结构具有最大的柔性,避免高约束,使焊缝收缩应力最小。
具体措施如下:1.设计a. 在设计中不任意加大焊缝,在满足强度要求时应尽可能采用最小焊脚尺寸,在满足焊透深度要求时,应采用较小的焊接坡口角度和间隙;b. 避免焊接节点沿厚度方向受拉力作用;c. 相关节点采用高强度螺栓连接;d. 钢板厚度较大的角接接头焊缝,采用收缩时不易产生层状撕裂的构造(下图);T形接头采用对称(K形)坡口焊缝;e. 相关位置采用Z向钢板。
对受动力作用和大气环境恶劣的结构,如海上采油平台,其重要构件的钢板沿厚度方向所受拉力较大时,相应区域可采用Z向钢板;高层建筑钢结构刚性框架节点域由于焊缝集中,且约束程度大,梁端弯矩很大时可采用Z向钢;2 制造工艺a. 采用低氢型焊条,在满足设计强度要求时,选用屈服强度较低的焊条;b. 严格规定焊接顺序和焊接工艺,防止在约束状态下施焊,尽可能减小垂直于板面方向的约束;c. 适当提高预热温度施焊和进行必要的后热处理;d. 带有角部和T形接头的小组件在构件装配前全部焊好,构件最后装配只作对接焊接;e. 在容易发生层状撕裂的母材表面先用低氢型焊条堆置焊层;f. 采用“锤击”或其它特殊的工艺方法,减小母材厚度方向的应变。
钢结构层状撕裂的防止措施

钢结构层状撕裂的防止措施钢板的层状撕裂一般在板厚方向有较大拉应力时发生.在焊接节点中,焊缝冷却时,会产生收缩变形。
如果很薄或没有对变形的约束,钢板会发生变形从而释放了应力。
但如果钢板很厚或有加劲肋,相邻板件的约束,钢板受到约束不能自由变形,会在垂直于板面方向上产生很大的应力。
在约束很强的区域,由于焊缝收缩引起的局部应力可能数倍于材料的屈服极限,致使钢板产生层状撕裂.。
层状撕裂只可能发生在基材内,而且当它出现在接近焊缝的焊脚位置时,往往正好位于热影响区边缘,并且不会延伸至钢板表面.层状撕裂表面往往时纤维状的,发生在热影响区外并且具有阶梯行当纵向断面,纵向的尺寸往往数倍于横向尺寸。
这些特征可以容易将它与发生在热影响区内的由于氢引起的断裂区分开。
当有可能层状撕裂发生时,为防止钢板的层状撕裂,可采取一下措施:(1)改进节点的连接形式改进节点连接形式以减小局部区域内由于焊缝收缩而引起的应力集中,或避免使钢板在板垂直方向受拉。
(2)采用合理的焊缝形式及小焊脚焊缝焊缝的形式对基材变形有很大影响。
坡口焊缝的坡口越大,焊缝表面积也越大,将增加收缩应力。
单坡坡口焊缝会在整个连接厚度方向上产生不对称收缩应变而双坡焊缝会减少和平衡部分收缩变形,当板材厚度不大于19mm时,用双坡口代替单坡口并不能显著降低焊缝收缩变形。
随意用全熔透坡口焊代替角焊缝或在不需要熔透焊的连接中也要求采用全熔透焊,并不妥当,它会增加局部应力,容易导致层状撕裂。
(3)分段拼装在可行的情况下,应将一个大节点分成几个部分分别焊好后再拼装,并对各部分中焊缝的焊接次序进行仔细安排.此外,应尽可能减少定位焊点的尺寸及数量。
这些都将有利于节点焊缝去的收缩变形。
(4)谨慎布置加劲肋加劲肋会对焊缝变形产生约束.应按计算的要求设计加劲肋及其焊缝。
(5)选择屈服强度低的焊条只要能满足受力要求,应尽可能选择屈服强度低的焊条。
美国焊接学会的<<结构焊接规范>>和美国钢结构协会的<<建筑结构设计、制作、安装规程>>均指出:焊条、焊丝和焊剂应于基材"匹配"。
常见焊接裂纹的解析
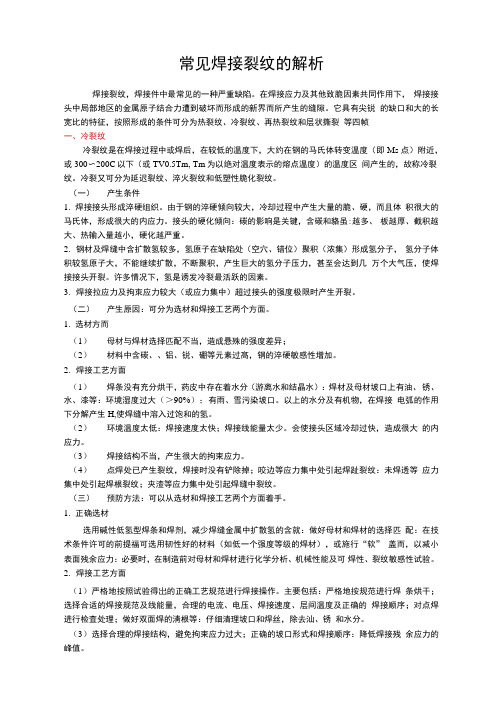
常见焊接裂纹的解析焊接裂纹,焊接件中最常见的一种严重缺陷。
在焊接应力及其他致脆因素共同作用下,焊接接头中局部地区的金属原子结合力遭到破坏而形成的新界而所产生的缝隙。
它具有尖锐的缺口和大的长宽比的特征,按照形成的条件可分为热裂纹、冷裂纹、再热裂纹和层状撕裂等四帧一、冷裂纹冷裂纹是在焊接过程中或焊后,在较低的温度下,大约在钢的马氏体转变温度(即Ms 点)附近,或300〜200C以下(或TV0.5Tm, Tm为以绝对温度表示的熔点温度)的温度区间产生的,故称冷裂纹。
冷裂又可分为延迟裂纹、淬火裂纹和低塑性脆化裂纹。
(一)产生条件1.焊接接头形成淬硬组织。
由于钢的淬硬倾向较大,冷却过程中产生大量的脆、硬,而且体积很大的马氏体,形成很大的内应力。
接头的硬化倾向:碳的影响是关键,含碳和貉虽:越多、板越厚、截积越大、热输入量越小,硬化越严重。
2.钢材及焊缝中含扩散氢较多,氢原子在缺陷处(空穴、错位)聚积(浓集)形成氢分子,氢分子体积较氢原子大,不能继续扩散,不断聚积,产生巨大的氢分子压力,甚至会达到几万个大气压,使焊接接头开裂。
许多情况下,氢是诱发冷裂最活跃的因素。
3.焊接拉应力及拘朿应力较大(或应力集中)超过接头的强度极限时产生开裂。
(二)产生原因:可分为选材和焊接工艺两个方面。
1.选材方而(1)母材与焊材选择匹配不当,造成悬殊的强度差异;(2)材料中含碳、、铝、锐、硼等元素过髙,钢的淬硬敏感性增加。
2.焊接工艺方面(1)焊条没有充分烘干,药皮中存在着水分(游离水和结晶水):焊材及母材坡口上有油、锈、水、漆等:环境湿度过大(>90%);有雨、雪污染坡口。
以上的水分及有机物,在焊接电弧的作用下分解产生H,使焊缝中溶入过饱和的氢。
(2)环境温度太低:焊接速度太快;焊接线能量太少。
会使接头区域冷却过快,造成很大的内应力。
(3)焊接结构不当,产生很大的拘束应力。
(4)点焊处已产生裂纹,焊接时没有铲除掉;咬边等应力集中处引起焊趾裂纹:未焊透等应力集中处引起焊根裂纹;夹渣等应力集中处引起焊缝中裂纹。
防止层状撕裂的措施
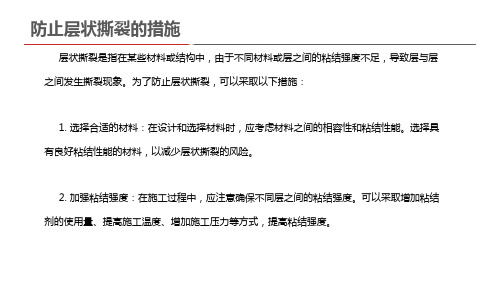
4. 控制施工条件:在施工过程中,要注意控制温度、湿度和施工速度等条件。避免温度过 高或过低、湿度过大或过小,以及施工速度过快或过慢等情况,影响粘结剂的固化和粘结效 果。
防止层状撕裂的措施
层状撕裂是指在某些材料或结构中,由于不同材料或层之间的粘结强度不足,导致层与层 之间发生撕裂现象。为了防止层状撕裂,可以采取以下措施:
1. 选择合适的材料:在设计和选择材料时,应考虑材料之间的相容性和粘结性能。选择具 有良好粘结性能的材料,以减少层状撕裂的风险。
2. 加强粘结强度:在施工过程中,应注意确保不同层之间的粘结强度。可以采取增加粘结 剂的使用量、提高施工温度、增加施工压力等方式,提高粘结强度。
5. 加强质量检验:在施工过程中,要进行质量检验和控制。对粘结剂、材料和施工工艺等 进行检测,确保其符合规定标准和要求。
防止层状撕裂的措施
6. 加强施工监督:加强对施工过程的监督和管理。确保施工人员按照规定的施工工艺和要 求进行施工,避免施工不当导致层状撕裂的发生。
综上所述,通过选择合适的材料、加强粘结强度、表面处理、控制施工条件、加强质量检 验和施工监督等措施,可以有效预防层状撕裂的发生,提高结构的稳定性和安全性。
铝合金焊接层状撕裂的原因

铝合金焊接层状撕裂的原因
铝合金焊接时出现层状撕裂可能是由于凝固时发生了低熔点相的液态融化和再凝固引起的。
以下是导致铝合金焊接层状撕裂的主要原因:
1.成分不均匀:
铝合金中的合金元素分布不均匀,特别是低熔点元素(如铝-硅合金)。
焊材和母材的成分差异较大,导致在焊接区域出现合金元素不均匀的情况。
2.低熔点相的液态融化:
在焊接过程中,合金元素可能由于高温而液化,形成低熔点相的液态。
这些液态相在凝固过程中可能会引起凝固线附近的脆性裂纹。
3.冷却速率过快:
过快的冷却速率可能促使液态相在凝固时无法充分扩散和混合。
过快的冷却还可能导致组织过于脆性,容易发生撕裂。
4.焊接热输入过高:
过高的焊接热输入会导致焊缝区域温度升高,促使低熔点相液态化。
这种情况下,即使冷却速率适中,仍可能出现层状撕裂。
5.合金固溶度范围宽:
部分铝合金的固溶度范围较宽,使得在焊接过程中容易形成液态相。
如果焊缝区域的合金处于固溶度范围内,就容易发生层状撕裂。
热裂纹、再热裂纹、冷裂纹、层状撕裂,这些你都了解吗?
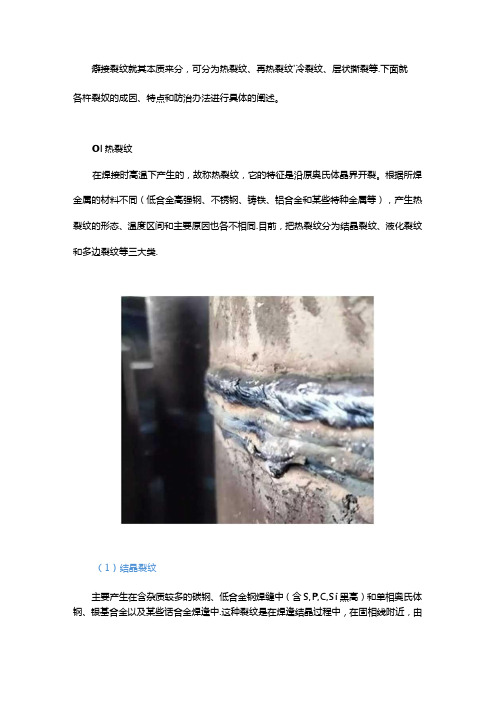
癖接裂纹就其本质来分,可分为热裂纹、再热裂纹'冷裂纹、层状撕裂等.下面就各杵裂奴的成因、特点和防治办法进行具体的阐述。
Ol热裂纹在焊接时高温下产生的,故称热裂纹,它的特征是沿原奥氏体晶界开裂。
根据所焊金属的材料不同(低合金高强钢、不锈钢、铸铁、铝合金和某些特种金属等),产生热裂纹的形态、温度区间和主要原因也各不相同.目前,把热裂纹分为结晶裂纹、液化裂纹和多边裂纹等三大类.(1)结晶裂纹主要产生在含杂质较多的碳钢、低合金钢焊缝中(含S,P,C,Si黑高)和单相奥氏体钢、银基合金以及某些话合金焊逢中.这种裂纹是在焊逢结晶过程中,在固相线附近,由于凝固金属的收缩,残余液体金属不足,不能及时添充,在应力作用下发生沿晶开裂.防治措施为:在冶金因素方面,适当调整焊逢金属成分,缩短照性温度区的范围控制焊逢中硫、磷、碳等有害杂质的含量;细化焊逢金属一次晶粒,即适当加入M。
、V、Ti.Nb等元素;在工艺方面,可以通过焊前预热、控制线能量、减小接头拘束度等方面来防治。
(2)近缱区液化裂纹是一种沿奥氏体晶界开裂的微裂纹,它的尺寸很小,发生于HAZ近缝区或层间。
它的成因一般是由于焊接时近缝区金属或焊缝层间金属,在高温下使这些区域的奥氏体晶界上的低熔共晶组成物被重新熔化,在拉应力的作用下沿奥氏体晶间开裂而形成液化裂纹。
这一种裂纹的防治措施与结晶裂纹基本上是一致的.特别是在冶金方面,尽可能降低硫、磷、畦、硼等低熔共晶组成元素的含量是十分有效的;在工艺方面,可以减小线能量,减小熔池熔合线的凹度.(3)多边化裂纹是在形成多边化的过程中,由于高温时的芨性很低造成的.这种裂纹并不常见,其防治措施可以向焊缝中加入提高多边化激化能的元素如Mo、W、Ti等,02再热裂纹通常发生于某些含有沉淀强化元素的钢种和高温合金(包括低合金高强钢、珠光体耐热钢、沉淀强化高混合金,以及某些奥氏体不锈钢),他们焊后并未发现裂纹,而是在热处理过程中产生了裂纹。
层状撕裂 ppt课件

PPT课件
4
根据层状撕裂产生的位置大体可分三类:
(1)在焊接热影响区焊趾或焊根处由冷裂纹而诱发 现成的层状撕裂;
(2)在焊接热影响区沿夹杂开裂,是工程上最常见 的层状撕裂;
(3)远离热影响区母材中沿夹杂开裂,这种情况多 出现在有较多MS的片状夹杂的厚板结构中。
3.氢的影响
在焊接热影响区附近,由冷裂诱发成为层状撕裂中 氢是一个重要的影响因素。
PPT课件
7
常见形貌特征
•宏观形态
(A) ~ (D)比较 典型, 也常 见,(E)是产生 在自动焊对接 接头的一种撕 裂, 又称为热 撕裂或液化开 裂。
PPT课件
8
•显微断口
•右上图是一种由平台—直壁— 平台组成的阶梯状断裂面
层状撕裂
PPT课件
1
主要内容
概概念
常见 形貌 特征
产生 原因
预防 措施
PPT课件
2
概念
大型厚壁结构, 在焊接过程中会沿钢 板的厚度方面出现较 大的拉伸应力,如果 钢中有较多的夹杂, 那么沿钢板轧制方向 出现一种台阶状的裂 纹,一般称为层状撕 裂。
PPT课件
3
一、层状撕裂的特征及其危害性
• 层状撕裂是一种内部 沿轧向的应力开裂, 它的特征是呈阶梯状 ,这是其他裂纹所没 有的。
PPT课件
12
(2)在强度允许的情况下,尽量采用焊接量少的对 称角焊缝来代替焊接量大的全焊透焊缝,以避免产 生过大的应力。
(3)应在承受Z向应力的一侧开坡口。
(4)对于T形接头,可在横板上预先堆焊一层低强 的熔敷金属,以防止焊根出现裂纹,同时亦可缓和 横板的Z向应力。
- 1、下载文档前请自行甄别文档内容的完整性,平台不提供额外的编辑、内容补充、找答案等附加服务。
- 2、"仅部分预览"的文档,不可在线预览部分如存在完整性等问题,可反馈申请退款(可完整预览的文档不适用该条件!)。
- 3、如文档侵犯您的权益,请联系客服反馈,我们会尽快为您处理(人工客服工作时间:9:00-18:30)。
主要内容
概念 概念
常见 形貌 特征
产生 原因
预防 措施
概念
大型厚壁结构, 在焊接过程中会沿钢 板的厚度方面出现较 大的拉伸应力,如果 钢中有较多的夹杂, 那么沿钢板轧制方向 出现一种台阶状的裂 纹,一般称为层状撕 裂。
一、层状撕裂的特征及其危害性 • 层状撕裂是一种内部 沿轧向的应力开裂, 它的特征是呈阶梯状 ,这是其他裂纹所没 有的。 • 层状撕裂常出现在T 形接头、角接头和十 字接头中。
启裂源分类 第1类 以焊根裂纹。焊趾裂 纹为启裂源,沿HAZ发展
成因 焊趾裂纹为启裂源,沿HAZ发展由 冷裂而引起的(PCM、HD、RF偏 高)伸长的MnS夹杂物 角变形引起 有弯曲拘束应力或缺口引起的应变 集中
第2类 以轧层夹杂物为启裂 源。沿HAZ发展
第3类 完全由收缩应变而致 ,以轧层夹杂物为启裂源, 沿远离HAZ的母材板厚中央 发展 HAZ:热影响区域
常见形貌特征
•宏观形态
(A) ~ (D)比较 典型, 也常 见,(E)是产生 在自动焊对接 接头的一种撕 裂, 又称为热 撕裂或液化开 裂。
•显微断口
•右上图是一种由平台—直壁— 平台组成的阶梯状断裂面
•裂缝平台区平坦, 边界清晰, 几乎看不到塑性变形, 是片状 夹杂物与基体在拉伸应力作用 下形成的一种解理面, 平台之 间被山脊状撕裂棱所间隔。因 此认为, 层状撕裂是低延性准 解理断裂, 见右下图。
ห้องสมุดไป่ตู้
产生原因
• 层状撕裂的产生与钢种强度级别无关,主要与 钢种夹杂物量和分布形态有关。 • 在轧制钢板中存在硫化物、氧化物和硅酸盐等 低熔点非金属夹杂物,其中尤以硫化物的作用 为主,在轧制过程中被延展成片状,分布在与 表面平行的各层中,在垂直于厚度方向的焊接 应力作用下,夹杂物首先开裂并扩展,以后这 种开裂在各层之间相继发生,连成一体,造成 层次撕裂的阶梯性。
(二)影响层状撕裂的因素 1.非金属夹杂物的种类、数量和分布形态它是产 生层状撕裂的基本原因,是造成钢的各向异性、力 学性能差异的内在因素。钢中夹杂物一般常见的有 硫化物、各种硅酸盐和铝酸盐等。 2.Z向拘束应力 厚壁结构在焊接过程中承受不同程度的Z向拘束应 力,同时还不焊后的残余应力及负载,它们是造成 层状撕裂的力学条件。 3.氢的影响 在焊接热影响区附近,由冷裂诱发成为层状撕裂中 氢是一个重要的影响因素。
(2)在强度允许的情况下,尽量采用焊接量少的对 称角焊缝来代替焊接量大的全焊透焊缝,以避免产 生过大的应力。 (3)应在承受Z向应力的一侧开坡口。 (4)对于T形接头,可在横板上预先堆焊一层低强 的熔敷金属,以防止焊根出现裂纹,同时亦可缓和 横板的Z向应力。 (5)为防止由冷裂引起的层状撕裂,应尽量采用一 些防止冷裂的措施,如降低氢量、适当提高预热、 控制层间温度等。
例如
• 作用于收缩方向上的焊缝厚度aD尽可能低
•焊缝连接基础应尽可能大
二、层状撕裂的形成机理及其影响因素
(一)层状撕裂的形成机理 厚板结构焊接时,特别是T形和角接接头,在 强制拘束的条件下,焊缝收缩时会在母材厚度方向 产生很大的拉伸应力和应变,当应变超过母材金属 的塑性变形能力时(沿板厚方向),夹杂物与金属 基体之间就会发生分离而产生微裂,在应力的继续 作用下,裂纹尖端沿着夹杂所在平面进行扩展,就 形成的所谓“平台”。
根据层状撕裂产生的位置大体可分三类: (1)在焊接热影响区焊趾或焊根处由冷裂纹而诱发 现成的层状撕裂; (2)在焊接热影响区沿夹杂开裂,是工程上最常见 的层状撕裂; (3)远离热影响区母材中沿夹杂开裂,这种情况多 出现在有较多MS的片状夹杂的厚板结构中。 层状撕裂主要发生在低合金高强钢的厚板焊接 结构中,多用于海洋采油平台、核反应堆压力容器 及潜艇外壳等重要结构。
伸长的MnS夹杂物及硅酸盐夹杂物 拘束度大,存在Z向拉伸拘束应力 氢脆
轧层中的长条MnS夹杂物及硅酸盐 夹杂物 拘束度大,弯曲拘束产生的 残余应力应变时效
预防措施
(一)选用具有抗层状撕裂的钢材,降低钢中夹杂 物的含量和控制夹杂物的形态,来提高钢板厚向的 塑性是有效的。 (二)设计和工艺上的措施 在设计和施工工艺上主要是避免Z向应力和应力集 中,具体措施如下: (1)应尽量避免单侧焊缝,改用双侧焊缝,这样可 以缓和焊缝根部的应力状态,并防止应力集中。