煤矸石自动分选机简介
煤矸石智能分选设备原理

煤矸石智能分选设备原理
煤矸石智能分选设备是一种新型的煤矸石分选设备,它采用先进的智能技术,可以有效地实现煤矸石的分选。
它的原理是:首先,将煤矸石放入设备中,然后,设备会根据煤矸石的形状、大小、重量等特征,运用智能算法,将煤矸石分类,最后,将分类后的煤矸石放入不同的容器中。
煤矸石智能分选设备的优势在于,它可以有效地提高煤矸石的分选效率,减少人工分选的时间和劳动强度,提高分选的准确性,减少分选过程中的污染,从而节省大量的人力物力。
此外,煤矸石智能分选设备还可以根据客户的需求,自动调整分选参数,从而更好地满足客户的需求。
煤矸石智能分选设备的应用非常广泛,它可以用于煤矸石的分选,也可以用于其他物料的分选,如矿石、砂石、煤粉等。
它的应用不仅可以提高分选效率,而且还可以提高分选质量,从而节省大量的人力物力。
煤矸石智能分选设备的出现,为煤矸石分选提供了一种新的选择,它不仅可以提高分选效率,而且还可以提高分选质量,减少分选过程中的污染,从而节省大量的人力物力。
它的出现,为煤矸石分选带来了极大的便利,也为煤矸石行业的发展带来了新的机遇。
TBS简介
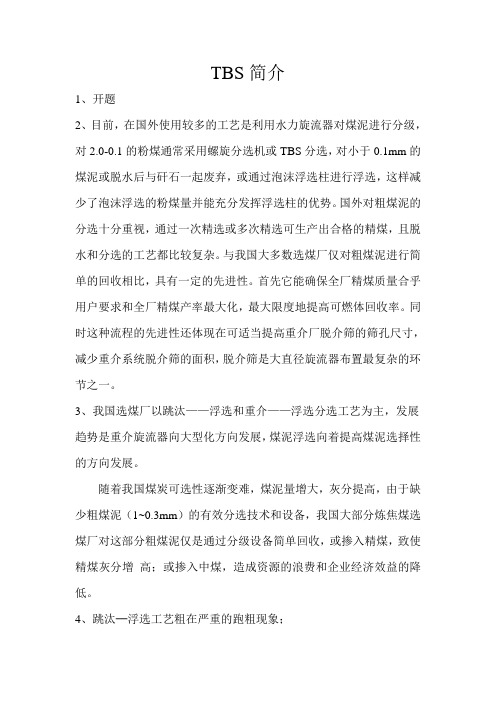
TBS简介1、开题2、目前,在国外使用较多的工艺是利用水力旋流器对煤泥进行分级,对2.0-0.1的粉煤通常采用螺旋分选机或TBS分选,对小于0.1mm的煤泥或脱水后与矸石一起废弃,或通过泡沫浮选柱进行浮选,这样减少了泡沫浮选的粉煤量并能充分发挥浮选柱的优势。
国外对粗煤泥的分选十分重视,通过一次精选或多次精选可生产出合格的精煤,且脱水和分选的工艺都比较复杂。
与我国大多数选煤厂仅对粗煤泥进行简单的回收相比,具有一定的先进性。
首先它能确保全厂精煤质量合乎用户要求和全厂精煤产率最大化,最大限度地提高可燃体回收率。
同时这种流程的先进性还体现在可适当提高重介厂脱介筛的筛孔尺寸,减少重介系统脱介筛的面积,脱介筛是大直径旋流器布置最复杂的环节之一。
3、我国选煤厂以跳汰——浮选和重介——浮选分选工艺为主,发展趋势是重介旋流器向大型化方向发展,煤泥浮选向着提高煤泥选择性的方向发展。
随着我国煤炭可选性逐渐变难,煤泥量增大,灰分提高,由于缺少粗煤泥(1~0.3mm)的有效分选技术和设备,我国大部分炼焦煤选煤厂对这部分粗煤泥仅是通过分级设备简单回收,或掺入精煤,致使精煤灰分增高;或掺入中煤,造成资源的浪费和企业经济效益的降低。
4、跳汰─浮选工艺粗在严重的跑粗现象;对于细粒度含量大的原煤,跳汰分选由于其机理限制,不可避免的存在吸啜作用,细粒原煤将被吸入跳汰机筛下进入中煤或矸石,造成中煤矸石大量带煤,影响精煤产率,降低分选精度。
5、采用预先脱泥的重介—浮选工艺的选煤厂,由于磨损,脱泥筛筛缝变大,跑粗现象仍然存在,浪费了大量的资源。
另外,按0.25mm 脱泥,脱泥效率存在问题,相当一部分的-0.25mm的物料进入重介系统,影响重介旋流器的高效运行。
不脱泥重介—浮选工艺由于大直径旋流器有效分选下限的提高和微泡浮选柱等浮选方式入料粒度上限的降低,伴随着设备的跑粗现象,最终导致介于重介旋流器有效分选下限和浮选柱分选上限之间的粗煤泥(1~0.25mm)得不到有效分选。
井下矸石智能分选系统方案设计

井下矸石智能分选系统方案设计摘要:随着煤矿绿色开的推广,国内已有多个井工煤矿实现了井下矸石分选及不可利用矸石返井充填开采。
本文结合矿井实际,针对生产矿井原煤开采情况,在矿井原有生产系统基础上,经过分析、比选,设计出煤矸分选方案。
设计提出的智能分选系统具有布置简单、灵活、宜复制的特点,可在同类矿井中推广应用。
系统选出的矸石进入充填运输系统,用于井下各地点充填使用。
本文对充填部分不作论述,仅提出智能分选系统设备、硐室布置等设计内容。
关键词:绿色开采井下智能选矸煤矸分选分选硐室1 矿井现状及井下分选的必要性1.1基本情况该矿生产能力为2.40Mt/a,矿井采用主斜、副立的开拓方式。
全矿井设置主辅两个水平,在10号煤层布置主水平,在5号煤层布置辅助水平,两水平的主运输大巷直接与主斜井相连,且分别布置一个10号煤层、5号煤层回采工作面。
矿井井下主运输方式采用带式输送机运输,井下辅助运输方式采用无极绳连续牵引车运输为主,部分斜巷采用绞车提升矿车及架空乘人装置等运输方式。
井下煤炭运输路径为:工作面落煤通过刮板输送机、转载机、顺槽带式输送机→南翼集中皮带大巷→主斜井→地面,进入地面生产系统及选煤厂。
掘进工作面出煤(矸)经带式输送机汇入主煤流运输系统。
1.2井下分选的必要性该矿10号煤层为厚煤层,开采的原煤中含矸量较少;5号煤层为薄煤层,开采的原煤中含矸量大。
回采时,实际割顶、破底的情况较多,一般割顶板和破底板各约200mm。
经估算仅5煤层回采工作面顶底板割落矸石量约40-56万t/a。
此外,5号煤层中的巷道均为半煤岩巷,其掘进出料含矸石量比例更高,经估算该部分掘进矸石量约10-13万t/a。
这些矸石均汇入原煤运输系统,如果不在井下分选出来则全部升井,不但造成环境污染,而且增加堆存土地占用。
同时,增加无效提升,增加能耗,降低矿井的经济效益。
基于环境保护和绿色开采的理念,将原煤中的矸石在升井之前进行分选,将其作为井下充填材料。
煤矿井下智能选矸技术(干选)装置及工艺
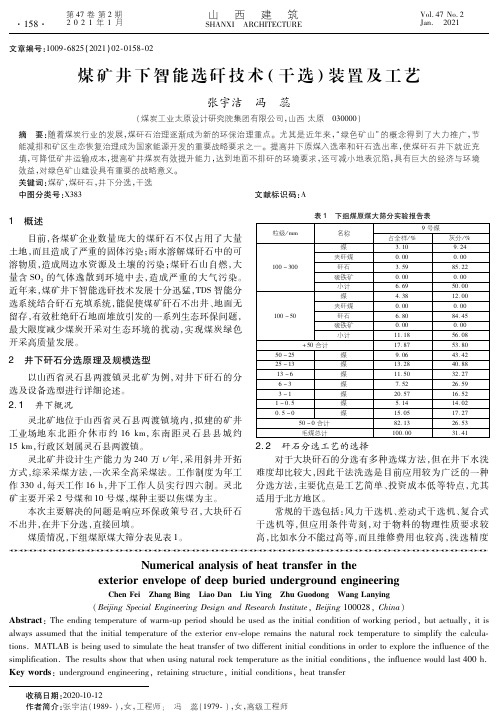
文章编号:1009 6825(2021)02 0158 02煤矿井下智能选矸技术(干选)装置及工艺收稿日期:2020 10 12 作者简介:张宇洁(1989 ),女,工程师; 冯 蕊(1979 ),女,高级工程师张宇洁 冯 蕊(煤炭工业太原设计研究院集团有限公司,山西太原 030000)摘 要:随着煤炭行业的发展,煤矸石治理逐渐成为新的环保治理重点。
尤其是近年来,“绿色矿山”的概念得到了大力推广,节能减排和矿区生态恢复治理成为国家能源开发的重要战略要求之一。
提高井下原煤入选率和矸石选出率,使煤矸石井下就近充填,可降低矿井运输成本,提高矿井煤炭有效提升能力,达到地面不排矸的环境要求,还可减小地表沉陷,具有巨大的经济与环境效益,对绿色矿山建设具有重要的战略意义。
关键词:煤矿,煤矸石,井下分选,干选中图分类号:X383文献标识码:A1 概述目前,各煤矿企业数量庞大的煤矸石不仅占用了大量土地,而且造成了严重的固体污染;雨水溶解煤矸石中的可溶物质,造成周边水资源及土壤的污染;煤矸石山自燃,大量含SO2的气体逸散到环境中去,造成严重的大气污染。
近年来,煤矿井下智能选矸技术发展十分迅猛,TDS智能分选系统结合矸石充填系统,能促使煤矿矸石不出井、地面无留存,有效杜绝矸石地面堆放引发的一系列生态环保问题,最大限度减少煤炭开采对生态环境的扰动,实现煤炭绿色开采高质量发展。
2 井下矸石分选原理及规模选型以山西省灵石县两渡镇灵北矿为例,对井下矸石的分选及设备选型进行详细论述。
2.1 井下概况灵北矿地位于山西省灵石县两渡镇境内,拟建的矿井工业场地东北距介休市约16km,东南距灵石县县城约15km,行政区划属灵石县两渡镇。
灵北矿井设计生产能力为240万t/年,采用斜井开拓方式,综采采煤方法,一次采全高采煤法。
工作制度为年工作330d,每天工作16h,井下工作人员实行四六制。
灵北矿主要开采2号煤和10号煤,煤种主要以焦煤为主。
煤矿井下排矸系统

煤矿井下排矸系统简介煤矿井下排矸系统是一种用于处理煤矿井下废弃物的设备。
在采煤过程中,产生了大量的矸石、岩屑和煤屑等废弃物,如果不及时处理,会对煤矿环境和采煤工人的安全造成严重影响。
煤矿井下排矸系统的主要作用就是将这些废弃物经过筛选和分离处理,使之达到无害化、减少占地等作用。
原理煤矿井下排矸系统的主要原理是基于重力和水力的分离。
废弃物通常含有的重物质与煤相比重,因此可以通过重力分离的方式将其和煤分离开来。
在分离过程中,需要使用水流将废弃物带到处理设备进行分离,通常使用的是斜板和可调节水流量的喷嘴,使废弃物沿斜板流向废物泵池,同时让煤沿着斜板流入煤收集槽中。
经过这样的处理,可以有效地将废弃物和煤分离开来。
设备煤矿井下排矸系统通常由以下几个部分组成:斜板斜板是煤矿井下排矸系统的主体部分,也是用于分离废弃物和煤的主要设备。
斜板是一块呈一定角度倾斜的板材,其上有喷嘴和排污槽。
废弃物经过喷嘴加工后会沿着斜板流动到排污槽中,而煤则会沿着斜板流入煤收集槽中。
废物泵池废物泵池是用于收集废弃物的设备,其位于斜板下方。
废弃物通过斜板经过处理后,会落入废物泵池中,然后通过泵进行处理。
煤收集槽煤收集槽是用于收集煤的设备,其位于斜板上方。
通过斜板分离处理后的煤会落入煤收集槽中,方便后续的处理和运输。
分选机分选机是用于对煤进行进一步分选的设备。
其主要原理是根据煤的密度大小和特性进行分辨和分选,将煤从杂质中进一步分离出来。
优点煤矿井下排矸系统具有以下优点:环保煤矿井下排矸系统在处理废弃物时,能够将其中可回收或可利用的物质进行再利用,减少了对自然环境的污染。
减少占地采煤过程中产生的废弃物通常需要占用大量场地进行存放和处理。
使用煤矿井下排矸系统可以将废弃物进行有效处理,从而减少对场地资源的占用。
节约成本在采煤生产过程中,废弃物通常需要进行收集和处理,这需要消耗大量的人力和物力成本。
使用煤矿井下排矸系统可以将处理成本有效降低。
煤矿井下排矸系统的使用可以有效地处理采煤过程中产生的废弃物,从而减少了对自然环境和人员安全的危害,具有环保、减少占地、节约成本等优点。
煤矸石智能分选系统
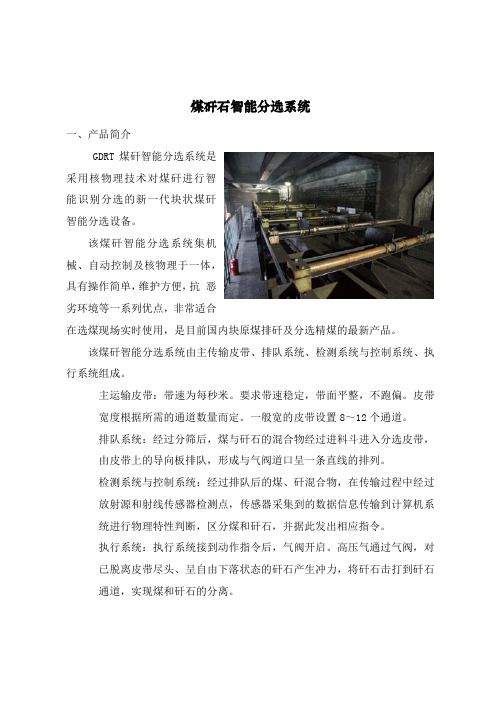
煤矸石智能分选系统一、产品简介GDRT煤矸智能分选系统是采用核物理技术对煤矸进行智能识别分选的新一代块状煤矸智能分选设备。
该煤矸智能分选系统集机械、自动控制及核物理于一体,具有操作简单,维护方便,抗恶劣环境等一系列优点,非常适合在选煤现场实时使用,是目前国内块原煤排矸及分选精煤的最新产品。
该煤矸智能分选系统由主传输皮带、排队系统、检测系统与控制系统、执行系统组成。
主运输皮带:带速为每秒米。
要求带速稳定,带面平整,不跑偏。
皮带宽度根据所需的通道数量而定。
一般宽的皮带设置8~12个通道。
排队系统:经过分筛后,煤与矸石的混合物经过进料斗进入分选皮带,由皮带上的导向板排队,形成与气阀道口呈一条直线的排列。
检测系统与控制系统:经过排队后的煤、矸混合物,在传输过程中经过放射源和射线传感器检测点,传感器采集到的数据信息传输到计算机系统进行物理特性判断,区分煤和矸石,并据此发出相应指令。
执行系统:执行系统接到动作指令后,气阀开启。
高压气通过气阀,对已脱离皮带尽头、呈自由下落状态的矸石产生冲力,将矸石击打到矸石通道,实现煤和矸石的分离。
排队系统检测系统控制系统执行系统该煤矸智能分选系统每通道的处理能力约为每小时15吨左右(根据不同的煤质、含矸量、粒度而不同),可依据具体需求在系统中设计配置相应的通道数量。
二、设备特点三、产品系列本公司根据客户要求分选物料粒级研发有如下四个产品系列:产品型号适用分选物料粒度单通道处理量(吨/小时)实际处理量跟该粒级大小物料的各自比重相关GDRT40-9040mm-190mm4 GDRT90-20090mm-200mm20 GDRT200-300200mm-300mm50四、经济及社会效益分析(一)经济效益1、经过分选,提高煤炭质量某矿选煤车间测试记录测试时间煤种测试数量矸石总量(kg)含矸量(%)发热量(Kcal/kg)早班5#混煤20吨945500445441350572、减少人工,节约费用每套系统每班仅需要系统操作人员一名,辅助人员2名。
了解光电智能分选设备,助力矿石分选应用!

了解光电智能分选设备,助力矿石分选应用!随着我国经济社会发展对矿产资源需求日益增长,我国矿产资源的开发规模也达到较高程度。
不过随着矿产资源的开发,高品易选矿石储量越来越少,低品难选矿增多,导致采选成本越来越高。
据不完全统计,当前我国尾矿和废石累积堆存量已达700多亿吨。
除了铁、铜开采产生尾矿占比较高外,非金属类矿石尾矿占比也在逐渐增加,如此开展多路径的矿山开采废石和尾矿的资源综合利用,通过废石和尾矿用来生产再生砂石骨料、混凝土细骨料、水泥的基本原料、水泥的混合材料,以及用于生产各类砖等多种用途,成为选矿工艺技术革新的主要研究方向。
目前,光电选矿技术在矿石预分选方面逐渐得到广泛应用,尤其随着AI算法、大数据、人工智能等技术的发展与普及,在光电选矿领域得到充分应用。
已成为AI智能光电选矿技术的主要解决方案。
光电选矿设备大致可分选可见光、红外、紫外、X射线几种分选方式,其主要构成大致可分为:供料系统、光电系统、控制系统、分选系统四大板块。
(1)供料系统:由进料斗、震动给料机、履带组成,待分选物料在供料系统中通过震动和导向自动形成连续的线状排列,以恒定的速度进入光电系统探测区,保障分选效果稳定。
(2)光电系统:光源、背景板、传感器或X射线源及采传板组成,可以通过矿石表面综合特征或密度差异对矿石进行高清成像,并通过传感器转化成电信号传达给电控系统。
(3)控制系统:负责将光电系统传达过来的电信号进行识别和分析,通主要是对矿石的颜色、纹理、光泽、质感、形状、密度等不同特征信息,进行模型训练、学习,并智能识别、比对好坏矿,通过非海量矿石数据的识别分选。
(4)分选系统:主要由次品槽、成品槽、喷阀和空气压缩机等组成,在接收到电控系统指令之后,喷阀会将瑕疵品吹入次品槽中,从而达到分选目的。
针对不同的矿石选用不同的设备不同的矿石根据其特征情况选用对应的设备,如具体表面特征性差异的矿石,可选用人工智能分选机,主要是通过颜色、纹理、光泽、质感、形状等,如滑石、硅灰石、硅渣、钨尾矿、碳酸钙、硅石、磷矿、煤系高岭岩等,通过其表面多重特征进行识别分选。
煤矸石智能分选系统

煤矸石智能分选系统一、产品简介GDRT煤矸智能分选系统是采用核物理技术对煤矸进行智能识别分选的新一代块状煤矸智能分选设备。
该煤矸智能分选系统集机械、自动控制及核物理于一体,具有操作简单,维护方便,抗恶劣环境等一系列优点,非常适合在选煤现场实时使用,是目前国内块原煤排矸及分选精煤的最新产品。
该煤矸智能分选系统由主传输皮带、排队系统、检测系统与控制系统、执行系统组成。
●主运输皮带:带速为每秒0.8--1米。
要求带速稳定,带面平整,不跑偏。
皮带宽度根据所需的通道数量而定。
一般1.4M宽的皮带设置8~12个通道。
●排队系统:经过分筛后,煤与矸石的混合物经过进料斗进入分选皮带,由皮带上的导向板排队,形成与气阀道口呈一条直线的排列。
●检测系统与控制系统:经过排队后的煤、矸混合物,在传输过程中经过放射源和射线传感器检测点,传感器采集到的数据信息传输到计算机系统进行物理特性判断,区分煤和矸石,并据此发出相应指令。
●执行系统:执行系统接到动作指令后,气阀开启。
高压气通过气阀,对已脱离皮带尽头、呈自由下落状态的矸石产生冲力,将矸石击打到矸石通道,实现煤和矸石的分离。
排队系统检测系统控制系统执行系统该煤矸智能分选系统每通道的处理能力约为每小时15吨左右(根据不同的煤质、含矸量、粒度而不同),可依据具体需求在系统中设计配置相应的通道数量。
二、设备特点三、产品系列本公司根据客户要求分选物料粒级研发有如下四个产品系列:产品型号适用分选物料粒度单通道处理量(吨/小时)实际处理量跟该粒级大小物料的各自比重相关GDRT40-90 40mm -190mm 4 GDRT90-200 90mm -200mm 20 GDRT200-300200mm -300mm50四、经济及社会效益分析(一)经济效益1、经过分选,提高煤炭质量 某矿选煤车间测试记录测试时间 煤种测试数量矸石总量(kg)含矸量(%)发热量(Kcal/kg )6.18早班 5#混煤 20吨 9455004454.72.52.244135057 2、减少人工,节约费用每套系统每班仅需要系统操作人员一名,辅助人员2名。
- 1、下载文档前请自行甄别文档内容的完整性,平台不提供额外的编辑、内容补充、找答案等附加服务。
- 2、"仅部分预览"的文档,不可在线预览部分如存在完整性等问题,可反馈申请退款(可完整预览的文档不适用该条件!)。
- 3、如文档侵犯您的权益,请联系客服反馈,我们会尽快为您处理(人工客服工作时间:9:00-18:30)。
煤矸石自动分选机
简介
德沃中能电气(北京)有限公司
DEWO ZHONGNENG ELECTRIC(BEIJING) Co., LTD
2009年9月16日
1.煤矸石自动分选机意义及简介
煤中矸石的自动剔选是现代化煤炭生产加工过程中的重要环节之一。
先进的分选方式与方法研究已逐渐引起煤炭生产和应用部门的重视,煤矸石自动分选机是对块状原煤里的矸石在传输过程中实现其物理分选的专用设备。
它的出现主要基于对以下几方面的考虑。
1)我国大部分煤炭开采生产仍延续着人工选矸的落后方式,劳动强度大,生产效率低下,矸石拣选率也直接受人员素质、管理水平等人为因素影响。
2)传统的重介分离等排矸方法产生大量难以处理的煤泥污染物,对人和农作物赖以生存的水源和耕地破坏严重,尤其是在我国主要产煤地区出现的开采煤炭资源与环境污染以及原本就十分匮乏的水资源间的矛盾日显突出。
目前,已有不少煤炭生产加工企业不同程度地受到我国环境保护法的制约,造成设备闲置,产量下降,经济损失严重。
3)煤是一种资源,它作为特殊能源和产品原料,在诸多行业生产中起着越来越重要的作用。
在国际国内市场上,块煤交易形势一直较好,但由于我国煤炭初加工能力较弱,块煤含矸率偏高,价格损失较大,市场竞争力不强。
4)干式分选方法是当今煤炭分选技术的重要发展趋势之一。
煤炭的洗选主要是跳汰选煤和风选,此外还有其它选煤方式,如浮选工艺法、复合式干法选煤等洗煤方法。
但这几种方法都是基于跳汰选煤工艺或风选原理的基础上改进而成。
均存在设备整体结构复杂,占地面积大,造价昂贵,使用成本较高,维护困难等问题,尤为严重的是环境污染问题。
目前在国际上尚未见有煤矸石自动分选机实用产品或类似设备的出现。
因此,煤矸石自动分选设备对我国干式分选技术的进步与发展也将起到积极的推动作用。
填补了此项的空白。
我们经过十几年的研究、探索,采用“放射性同位素射源”,根据煤和矸石对射线吸收量的不同来识别煤和矸石,用高频电磁气阀作为执行机构 ,生产并投入使用目前国内外第一台自动化程度较高的自动选矸设备,其中多项核心技术已获国家专利。
该设备集机械、自动控制及核物理于一体,具有操作简单,维护方便,抗恶劣环境等一系列优点,非常适合在选煤现场实时使用,有效解决了现有选煤设备存在的问题。
设备于2005年5月在河南许昌新龙公司梁北煤矿(现改名为神火集团梁北煤矿)正式投入使用,设备安装在梁北煤矿原手工选矸的传送皮带上,完全替代了人工手选,并且保证选出的矸石中不含煤块。
设备运行以来,在矿上没有配备任何维护人员的情况下,运行稳定,受到煤矿领导及生产人员的高度评价。
该系统在技术上主要解决了以下几个关键问题:
1.运用新型双能γ射线衍射方式,实现了在较大粒度范围的煤与矸石的在线识别;
2.采用集散控制方式,确保了识别仪表系统在恶劣工矿下的长期可靠运行;
3.机械排队机构更加简便有效,满足了对物料进行准确识别的要求;
4.气动执行机构简单可靠。
2.产品特点
煤矸石自动分选机属于干选设备,煤和矸石经过该设备后即可自动分开,不同于目前国内外采用的水洗,湿洗和风选,它具有如下优点:
1.投资少,见效快;
2.分选效率高,不低于85%,保证选出的矸石中不含煤块,可靠性好;
3.系统操作简单,维护方便,运行成本低;
4.分选的煤种范围广,不受湿度的影响,环境适应性强;
5.处理粒度根据不同煤质可设定为30—50、50—150、150—250毫米;
6、不消耗水资源,能耗极低,不对环境造成破坏和污染。
3.前景与应用
煤矸石自动分选机的完善,推广应用,将对我国煤炭产品质量提升起到积极作用。
可广泛应用于物料分选等其他生产领域。
就煤炭生产而言,可用于:
1.现有煤矿生产系统的技术改造。
该设备可在煤流系统进行在线分选,不另需场地,
直接将原人工拣矸皮带改为自动分选,能够大大提高原煤分选率及生产自动化水
平。
2.完善干法选煤工艺。
现有空气重介质流化床干法选煤及FGX系列复合式干法选煤入
选原煤粒度均为0-50mm及0-80mm;而煤矸石自动分选机入选原煤最佳粒度为30
-300mm,弥补了上述两种干法选煤工艺的不足,为干法选煤工艺起到积极推动作
用。
3.矸石的综合应用。
由于煤矸石质量吸收系数K值可调,可对煤矸石进行准确分类(低热值劣质煤,碳质页岩),以分别应用于劣质煤发电,水泥生产等。
4.系统组成
煤矸石自动分选机分为机械传输系统、核检测系统、识别与控制系统和执行系统四部分
组成。
1、进料斗、传送皮带和排队机构构成设备的机械系统;
2、由放射源和射线传感器构成检测系统,放射源的辐射方向为正上方;
3、控制仪表构成系统的煤矸石识别及气阀的控制部分;
4、高压气和气阀构成系统的执行系统。
5.技术原理
煤矸石自动分选机主要由原料进料斗,煤和矸石出料斗,皮带传输机以及识别与分选控制系统几部分构成。
由于整个识别与分选工作过程是非接触,实时的,因此不会影响正常的物料传输。
皮带上设有若干个物料排队通道,每一通道独立的配置一套由双能γ射线源、射
线传感器、气动执行器和测控仪表组成的识别与分选系统,以提高整机的运行可靠性。
当一定粒度的物料落到传送皮带上以后,在排队机构的作用下顺序排列并穿过γ射线源和γ射线传感器,传感器将感应信号经过放大、整形后传送给控制仪表。
控制仪表中的微处理器将信号依据煤矸石识别数学模型进行运算,得出此时穿过γ射线的物料的密度加权值。
此加权值与事前设定的加权值相比较,高于设定值的判断为矸石,低于设定值的判断为煤。
当判断为矸石时,经过仪表设定的延时时间后,在矸石抛落过程中经过高频气阀时,控制仪表打开高频气阀,高压气流冲出气阀并击中抛落过程中的矸石,使其偏离原来的抛落轨迹,落入矸石料斗。
没有被击的煤块按原轨迹自然抛入煤斗。
6.核放射源技术参数和使用说明
CX104型双光子辐射输出器是中国原子能科学研究院同位素研究所设计的CX系列产品之一,采用贫化铀作为γ射线屏蔽材料。
该输出器设计安全,操作方便,性能稳定,准直孔定位准确。
输出器由罐体、转鼓、安装板和防尘板组成。
⑴.技术特征:
1.137Cs放射源最大装载量为1.11GBq(30mCi)
2.241Am放射源最大装载量为11.1GBq(300mCi)
3.准直孔直径Φ20mm,长度为100mm。
4. 罐体外型Φ138Х183mm。
5.罐体表面辐射剂量小于36uSv/h,离开罐体表面5cm处,辐射剂量小于1uSv/h,符合国家安全标准。
⑵.技术参数
1、铯-137活度: 0.74 GBq
2、镅-241活度: 11.1 GBq
3、表面5cm处最大剂量: < 25 uSv/h
4、表面0.5cm处最大剂量: < 2.5 uSv/h
5、工作状态时,准直方向1m处的输出剂量: ≈60 uSv/h。