转 炉 长 寿 复 吹 冶 炼 工 艺 技 术
《钢冶金学》_第6章 氧气底吹转炉和顶底复合吹炼转炉炼钢

钢冶金学重庆科技学院王宏丹◆氧气底吹转炉炼钢氧气底吹转炉炼钢OBM法和LWS法吹炼高磷铁水时的成分变化Q-BOP法吹炼过程中钢水和炉渣成分的变化Q-BOP法吹炼过程炉渣成分的变化吹炼终点[C]和[O]的关系图终点[C]和[Mn]的关系Q-BOP和LD炉内渣中(FeO)6.2.1 顶底复吹转炉炼钢工艺类型6.2 顶底复合吹炼转炉的冶金特点6.2.2 顶底复吹转炉的底吹供气和供气元件6.2.3 顶底复吹转炉内的冶金反应6.2.4 冶金效果氧气顶底复吹转炉炼钢在复吹转炉中,了解和掌握底吹气体的性质、冶金行为、合理地确定底吹气体比例,选择和控制底吹供气强度,是复吹转炉获得良好的技术经济指标的重要因素。
底吹气体的冶金行为主要表现在三个方面: 强化熔池搅拌,使钢水成分,温度均匀;加速炉内反应,使渣钢反应界面增大,元素间化学反应和传质过程更加趋于平衡;冷却保护供气元件,使供气元件使用寿命延长。
底吹气体底吹O:需用冷却介质来保护供气元件,会与熔2池中碳发生反应,产生较大的搅拌力。
:可不用冷却剂,会与熔池中碳发生反 底吹CO2应搅拌力较强的气体;会使熔池CO分压增加,不利于超低碳钢冶炼。
、Ar和CO:属中性或惰性气体,供入铁 底吹N2水中不参与熔池内的反应,只起搅拌作用。
底吹气体比例在复吹转炉中,底吹气体量的多少决定熔池内搅拌的强弱程度。
,其底吹 在冶炼超低碳钢种时,即使用底吹O2供气量也要达20%左右;对一些具有特殊功能的复吹工艺(如喷石灰粉、煤粉等),其底吹供气量可达40%。
就一般复吹转炉而言,为了保证脱硫、脱气和渣-钢间反应趋于平衡,在吹炼结束前,也要采用较大的底吹供气来搅拌熔池。
底吹供气强度获得最佳搅拌强度,使熔池混合最均匀。
大量实验研究表明,熔池的混匀程度与搅拌强度有关,而搅拌强度受供气量和底吹元件布置影响。
根据吹炼过程调节供气强度。
复吹转炉的特点是能有效地把熔池搅拌与炉渣氧化性有机统一起来,而实现手段就是控制底吹供气强度。
不锈钢冶炼三步法的特点

不锈钢冶炼三步法的特点一步法:即电炉一步冶炼不锈钢。
由于一步法对原料要求苛刻(需返回不锈钢废钢、低碳铬铁和金属铬),生产中原材料、能源介质消耗高,成本高,冶炼周期长,生产率低,产品品种少,质量差,炉衬寿命短,耐火材料消耗高,因此目前很少采用此法生产不锈钢。
二步法1965年和1968年,VOD和AOD精炼装置相继产生,它们对不锈钢生产工艺的变革起了决定性作用。
前者是真空吹氧脱碳,后者是用氩气和氮气稀释气体来脱碳。
将这两种精炼设施的任何一种与电炉相配合,这就形成了不锈钢的二步法生产工艺。
三步法:即电炉+复吹转炉+VOD三步冶炼不锈钢。
其特点是电炉作为熔化设备,只负责向转炉提供含Cr、Ni的半成品钢水,复吹转炉主要任务是吹氧快速脱碳,以达到最大回收Cr的目的。
VOD真空吹氧负责进一步脱碳、脱气和成分微调。
三步法比较适合氩气供应比较短缺的地区,并采用含碳量较高的铁水作原料,且生产低C、低N不锈钢比例较大的专业厂采用。
电炉+复吹转炉+VOD三步。
其特点是电炉作为熔化设备,只负责向转炉提供含Cr、Ni 的半成品钢水,复吹转炉主要任务是吹氧快速脱碳,以达到最大回收Cr的目的。
VOD真空吹氧负责进一步脱碳、脱气和成分微调。
三步法比较适合氩气供应比较短缺的地区,并采用含碳量较高的铁水作原料,且生产低C、低N不锈钢冲压弯头比例较大的专业厂采用。
目前世界上88%不锈钢冲压弯头采用二步法生产,其中76%是通过AOD炉生产。
因此它比较适合大型不锈钢冲压弯头专业厂使用。
二步法1965年和1968年,VOD和AOD精炼装置相继产生,它们对不锈钢生产工艺的变革起了决定性作用。
前者是真空吹氧脱碳,后者是用氩气和氮气稀释气体来脱碳。
将这两种精炼设施的任何一种与电炉相配合,这就形成了不锈钢的二步法生产工艺。
采用电炉与VOD二步法炼钢工艺比较适合小规模多品种的兼容厂的不锈钢生产。
采用电炉与AOD的二步法炼钢工艺生产不锈钢具有如下优点:1、AOD生产工艺对原材料要求较低,电炉出钢含C可达2%左右,因此可以采用廉价的高碳FeCr和20%的不锈钢废钢作为原料,降低了操作成本。
转炉炼钢技术

转炉炼钢技术09冶金(3)班吴丰一、摘要转炉炼钢(converter steelmaking)是以铁水、废钢、铁合金为主要原料,不借助外加能源,靠铁液本身的物理热和铁液组分间化学反应产生热量而在转炉中完成炼钢过程。
转炉按耐火材料分为酸性和碱性,按气体吹入炉内的部位有顶吹、底吹和侧吹;按气体种类为分空气转炉和氧气转炉。
碱性气顶吹和顶底复吹转炉由于其生产速度快、产量大,单炉产量高、成本低、投资少,为目前使用最普遍的炼钢设备。
转氧炉主要用于生产碳钢、合金钢及铜和镍的冶炼。
本文系统阐述了转炉炼钢技术的原理以及介绍了整个的工艺流程;总结了转炉炼钢技术的发展历程和世界转炉炼钢趋势。
二、引言早在1856 年德国人贝赛麦就发明了底吹酸性转炉炼钢法,这种方法是近代炼钢法的开端,它为人类生产了大量廉价钢,促进了欧洲的工业革命。
但由于此法不能去除硫和磷,因而其发展受到了限制。
1879 年出现了托马斯底吹碱性转炉炼钢法,它使用带有碱性炉衬的转炉来处理高磷生铁。
虽然转炉法可以大量生产钢,但它对生铁成分有着较严格的要求,而且一般不能多用废钢。
随着工业的进一步发展,废钢越来越多。
在酸性转炉炼钢法发明不到十年,法国人马丁利用蓄热原理,在1864 年创立了平炉炼钢法,1888 年出现了碱性平炉。
平炉炼钢法对原料的要求不那么严格,容量大,生产的品种多,所以不到20 年它就成为世界上主要的炼钢方法,直到20 世纪50 年代,在世界钢产量中,约85%是平炉炼出来的。
1952 年在奥地利出现纯氧顶吹转炉,它解决了钢中氮和其他有害杂质的含量问题,使质量接近平炉钢,同时减少了随废气(当用普通空气吹炼时,空气含79 % 无用的氮)损失的热量,可以吹炼温度较低的平炉生铁,因而节省了高炉的焦炭耗量,且能使用更多的废钢。
由于转炉炼钢速度快(炼一炉钢约10min,而平炉则需7h),负能炼钢,节约能源,故转炉炼钢成为当代炼钢的主流。
转炉炼钢(图2) 其实130 年以前贝斯麦发明底吹空气炼钢法时,就提出了用氧气炼钢的设想,但受当时条件的限制没能实现。
复吹转炉工艺技术在太钢的应用及优化

池搅拌较顶吹强 。 碳氧浓度积更接近平衡值. 复吹效
果更加 明显 。
元件由 3 层不锈钢无缝钢管组成.最外层直径为 ̄2 2
m 每炉座 为 4 m。 个底吹供气元件 。 每个底吹供气元件
的气量可 以通过计算机单独检测与控制 。底 吹供气元
皿l Ⅲ {
缸
件 布置在炉底 以 0 5 D为炉底 直径 ) . D( 4 为半径 的同心 圆上 , 与耳轴连线成 3 。 并 0 夹角 , 与耳 轴连线成对称 布
t 。为充分利用顶底复合 吹炼转炉工艺 的冶 金特性 . 更
T 1L4 等钢 种进行 了终 点碳 同溶解 氧 的关 系及 50 、5号 终点 碳 同碳氧 积 的关 系测 定 ,结果 表 明 :当炉 龄为 30 炉 时 , 00 在终 点碳 含量 为 009 温度 为 1 7 . %, 7 8℃ 6 的条件下 . 碳氧浓 度积 为 0 0 6 当炉龄 为 850炉 . 27 : 0 0
时 ,在终点碳 含量 为 0 6 %,温度为 1 6 %的条件 .3 0 4 6 下 , 氧浓 度积为 00 27 。测定 结果表 明 : 碳 . 8 0 随着炉 龄
咖 啪 鲫 伽 瑚 。
好地发挥特钢 的优势 ,提高转炉钢的质量 ,04 1 20 年 1 月太钢将第二炼钢 厂 的 2、 吹氧气改 造为顶底 复 3顶 合 吹炼 转炉。通过近 2年 的生产 实践 , 3复吹改造 2、
宝
皿1 圜
抽
0.0 0
0.5 0
01 .0
0.5 1
0.0 2
0_ 5 2
图 1 底 吹 供 气元 件 的布 置 方式
终点碳
闰 3 终 点 碳 与 氧 含 量 关 系 ( 龄 : 0 炉 85 0炉 )
转炉炼钢工艺流程
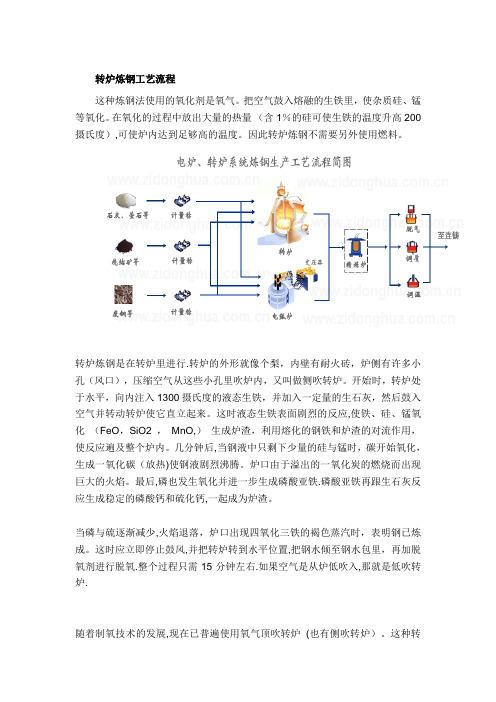
转炉炼钢工艺流程这种炼钢法使用的氧化剂是氧气。
把空气鼓入熔融的生铁里,使杂质硅、锰等氧化。
在氧化的过程中放出大量的热量(含1%的硅可使生铁的温度升高200摄氏度),可使炉内达到足够高的温度。
因此转炉炼钢不需要另外使用燃料。
转炉炼钢是在转炉里进行.转炉的外形就像个梨,内壁有耐火砖,炉侧有许多小孔(风口),压缩空气从这些小孔里吹炉内,又叫做侧吹转炉。
开始时,转炉处于水平,向内注入1300摄氏度的液态生铁,并加入一定量的生石灰,然后鼓入空气并转动转炉使它直立起来。
这时液态生铁表面剧烈的反应,使铁、硅、锰氧化(FeO,SiO2 ,MnO,)生成炉渣,利用熔化的钢铁和炉渣的对流作用,使反应遍及整个炉内。
几分钟后,当钢液中只剩下少量的硅与锰时,碳开始氧化,生成一氧化碳(放热)使钢液剧烈沸腾。
炉口由于溢出的一氧化炭的燃烧而出现巨大的火焰。
最后,磷也发生氧化并进一步生成磷酸亚铁.磷酸亚铁再跟生石灰反应生成稳定的磷酸钙和硫化钙,一起成为炉渣。
当磷与硫逐渐减少,火焰退落,炉口出现四氧化三铁的褐色蒸汽时,表明钢已炼成。
这时应立即停止鼓风,并把转炉转到水平位置,把钢水倾至钢水包里,再加脱氧剂进行脱氧.整个过程只需15分钟左右.如果空气是从炉低吹入,那就是低吹转炉.随着制氧技术的发展,现在已普遍使用氧气顶吹转炉(也有侧吹转炉)。
这种转炉吹如的是高压工业纯氧,反应更为剧烈,能进一步提高生产效率和钢的质量。
转炉一炉钢的基本冶炼过程。
顶吹转炉冶炼一炉钢的操作过程主要由以下六步组成:(1)上炉出钢、倒渣,检查炉衬和倾动设备等并进行必要的修补和修理;(2)倾炉,加废钢、兑铁水,摇正炉体(至垂直位置);(3)降枪开吹,同时加入第一批渣料(起初炉内噪声较大,从炉口冒出赤色烟雾,随后喷出暗红的火焰;3~5min后硅锰氧接近结束,碳氧反应逐渐激烈,炉口的火焰变大,亮度随之提高;同时渣料熔化,噪声减弱);(4)3~5min后加入第二批渣料继续吹炼(随吹炼进行钢中碳逐渐降低,约12min 后火焰微弱,停吹);(5)倒炉,测温、取样,并确定补吹时间或出钢;(6)出钢,同时(将计算好的合金加入钢包中)进行脱氧合金化.上炉钢出完钢后,倒净炉渣,堵出钢口,兑铁水和加废钢,降枪供氧,开始吹炼。
转炉炼钢工艺

转炉炼钢工艺转炉炼钢工艺绪论1、转炉炼钢法的分类转炉是以铁水为主要原料的现代炼钢方法。
该种炼钢炉由圆台型炉帽、圆柱型炉身和球缺型炉底组成。
炉身设有可绕之旋转的耳轴,以满足装料和出钢、倒渣操作,故而得名。
酸性空气底吹转炉——贝塞麦炉〔英国1856年〕空气转炉{ 碱性空气底吹转炉——托马斯炉〔德国1878年〕碱性空气侧吹转炉〔中国1952年〕转炉{ 氧气顶吹转炉——LD〔奥地利1952年〕氧气转炉{ 氧气底吹转炉——OBM〔德国1967年〕顶底复吹转炉〔法国1975年〕2、氧气顶吹转炉炼钢法简介(1) 诞生的布景及简称现代炼钢出产首先是一个氧化精炼过程,最初的贝氏炉和托马斯炉之所以采用空气吹炼正是操纵此中的氧。
二次世界大战以后,工业制氧机在美国问世,使操纵纯氧炼钢成为可能,但本来的底吹方式炉底及喷枪极易烧坏。
美国联合碳化物公司于1947年在尝试室进行氧气顶吹转炉的尝试并获成功,定名为BOF。
奥地利闻之即派有关专家前往参不雅学习,回来后于1949年在2吨的转炉长进行半工业性尝试并获成功,1952年、1953年30吨氧气顶吹转炉别离在Linz和Donawitz建成投产,故常简称LD。
1967年12月德国与加拿大合作缔造了氧气底吹转炉,使用双层套管喷嘴并通以气态碳氢化合物进行冷却。
1975年法国研发了顶底复吹转炉,综合了LD和OBM的长处,77年在世界年会上颁发。
(2) 氧气顶吹转炉的特点1〕长处氧气顶吹转炉一经问世就显示出了极大的优越性,世界各国竟相开展,目前成为最主要的炼钢法。
其长处主要暗示在:〔1〕熔炼速度快,出产率高〔一炉钢只需20分钟〕;〔2〕热效率高,冶炼中不需外来热源,且可配用10%~30%的废钢;〔3〕钢的品种多,质量好〔上下碳钢都能炼,S、P、H、N、O及夹杂含量低〕;〔4〕便于开展综合操纵和实现出产过程计算机控制。
2〕错误谬误当然,LD尚存在一些问题,如吹损较高〔10%,〕、所炼钢种仍受必然限制〔冶炼含大量难熔元素和易氧化元素的高合金钢有必然的困难〕等。
顶吹转炉吹炼工艺

顶吹转炉吹炼工艺1、装入制度包括哪些内容?装入制度是确定转炉合理的装入量,合适的铁水废钢比。
转炉的装入量是指主原料即铁水和废钢的装入数量。
2、什么是转炉的炉容比,影响转炉炉容比的因素有哪些?新转炉砌砖完成后的容积称为转炉的工作容积,也称有效容积,以“V”表示,公称吨位用“T”表示,两者之比值“V/T”称之为炉容比,单位为(m33、确定装入量的原则是什么?在确定合理的装入量时,除了考虑转炉要有一个合适的炉容比外,还应保持合适的熔池深度。
以保证炉底不受氧气射流的冲声,熔池深度必须超过氧流对熔池的最大穿透深度。
对于模铸工艺,装入量还应与锭型相配合。
装入量减去吹损及浇注必要损失后的钢水量,应是各种锭型的整数倍,尽量减少注余。
对连铸车间,转炉装入量可根据实际情况在一定范围内波动。
此外,确定装入量时,既要考虑发挥现有设备潜力,又要防止片面不顾实际的盲目超装,以免造成事故和浪费。
4、生产中应用的装入制度有哪几种类型,各有什么特点?氧气顶吹转炉的装入制度有:定量装入制度、分阶段定量装入制度和定深装入制度。
其中定深装入制度是每炉装入量均使熔池深度保持不变,由于生产组织的制约,实际上难以实现。
(1)定量装入制度。
在整个炉役期间,每炉的装入量保持不变。
这种装入制度的优点是:发挥了设备的最大潜力,生产组织、操作稳定,有利于实现过于音速,在出口处达到超音速。
由于氧气是可压缩流体,当高压低速氧气流经拉瓦尔管收缩段时,氧流速度提高,在到达音速时若继续缩小管径,氧流速度并不再增高,只会造成氧气密度增大;此时要继续提高氧流速度,只能设法增大管径,使其产生绝热膨胀过程,氧压降低,密度减小、体积膨胀。
当氧压与外界气压相等时,就可以获得超音速的氧射流,压力能转变为动能。
扩大管径。
拉瓦尔型喷头能够把压力能(势能)最大限度地转换成速度能(动能),并能获得比较稳定的超音速射流,在相同射流穿透深度的情况下,它的枪位可以高些,这就有利于改善氧枪的工作条件和炼钢的技术经济指标,因此拉瓦尔型喷头被广泛应用。
iData_炼铜转炉吹炼技术的发展_李晓霞
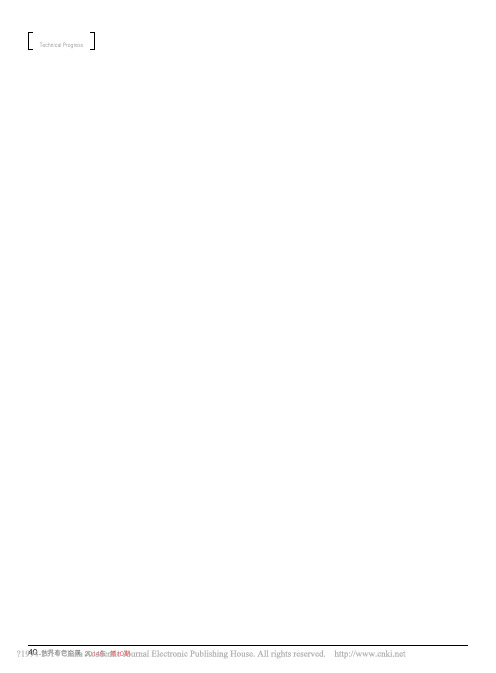
40 世界有色金属 2014年 第10期
技术进步
Technical ogress
图 1 转炉结构示意图
图 2 Hoboken 转炉结构示意图
2 转炉炉型及配套设备改进 2.1 结构改进(如霍伯肯转炉 ) [7、8]
转炉的结构是炉身上只开一个大口, 兼具出烟口和进出料口的功能。炉口不能 完全密封,而且转炉操作为正压操作,在 加 料 时,难 免 会 有 烟 气 逸 出,污 染 环 境。 转炉的结构示意图如图 1。
套筒烧嘴优点是 :操作简单,在鼓风 期间或转炉操作周期内不需要进行任何 特殊维护,也不需要捅风眼 ;在炉寿方面, 套筒烧嘴使用30% ~ 40%的富氧浓度,比传 统风嘴使用21% ~ 23%富氧浓度时要好,或 等同于该情况。
3 转炉吹炼环保方面改进 转炉吹炼低空污染问题始终是一个
难题,也开发了密封烟罩和旋转烟罩,且 它们结构也在不断完善和改进。
(2)送 风 系 统 采 用 法 国 液 空 公 司 高 氧套筒喷射技术,内层通富氧空气,外层 通 氮 气,压 力 分 别 为 0.6 ~ 0.8MPa 和 0.8 ~ 1.0MPa,送 风 压 力 高,有 利 于 熔 体的搅动,提高了氧气的利用率 ;氮气冷 却作用允许风管超出耐火砖约 200mm, 屏蔽了风眼区的强氧化反应,延长了风眼 区耐火砖的寿命,并且风眼末端不产生炉 结,取消了捅风眼机。
[5] 尹 长 春 . 高 品 位 冰 铜 吹 炼 操 作 技 术 问 题 探 讨 [C]. 重冶学委会 2000 年学术年会论文集 .
[6] 周安梁 . 贵溪冶炼厂吹炼技术的发展 [J]. 有色 冶金(冶炼部分), 2001,1(2).
[7] 周安梁 .Hoboken 转炉作业简述 [J]. 铜业工程, 2005(3).
- 1、下载文档前请自行甄别文档内容的完整性,平台不提供额外的编辑、内容补充、找答案等附加服务。
- 2、"仅部分预览"的文档,不可在线预览部分如存在完整性等问题,可反馈申请退款(可完整预览的文档不适用该条件!)。
- 3、如文档侵犯您的权益,请联系客服反馈,我们会尽快为您处理(人工客服工作时间:9:00-18:30)。
转炉长寿复吹冶炼工艺技术转炉长寿复吹冶炼工艺技术钢铁研究总院工艺所是我国最早开发、推广复吹转炉炼钢工艺技术的企业。
在70-80年代,钢铁研究总院工艺所就率先在国内首钢、唐钢等钢厂推广了复吹转炉炼钢工艺技术。
上世纪末90年代,转炉溅渣护炉技术在我国大面积推广应用,转炉炉龄大幅度提高。
在我国出现了复吹转炉底吹供气元件寿命低,不能与转炉炉龄同步、复吹效益不能得到充分发挥的问题。
钢铁研究总院工艺所针对这一问题,作了大量开发研究工作。
目前已成功地开发出“长寿复吹转炉冶炼工艺技术”,形成了多项专利技术。
现已在包钢、本钢、首钢、莱钢、武钢二炼钢和济钢等数十家大、中、小型钢铁企业得到应用,并取得了显著的效果。
采用“长寿复吹转炉冶炼技术”后,底吹供气元件寿命做到了与转炉高炉龄基本同步,使复吹的冶金效果在全炉役得到发挥。
“长寿复吹转炉冶炼技术”的开发成功,使我国复吹转炉炼钢工艺技术一举走在了世界的前列。
该项技术现已在国内多次获得了国家、行业的科学技术进步奖。
1 复吹转吹炼工艺技术基本原理复吹转炉炼钢工艺技术是氧气转炉诞生五十年来,所出现的两次重大的技术进步之一,基本原理是在顶吹氧气炼钢同时底吹辅助性搅拌气体:l 钢水终点氧含量降低:0.01-0.03%l 低碳钢水终点氧含量降低:100PPm;l 吨钢效益为2-6元/t;l 金属收得率提高:0.5~1.5%;l 石灰消耗降低:3~10kg/t;l 复吹工艺具有成渣速度快和吹炼平稳的双重优点;l 复吹工艺具有降低消耗,具有广泛的钢种冶炼适应性;l 氧气消耗减少:4~6Nm3/t;l 是否采用复吹炼钢工艺,已成为现代转炉的标志之一。
2 转炉长寿复吹的技术发展复吹转炉采用溅渣技术后,炉龄大幅度提高(超过万炉)。
炉龄提高后,底吹供气元件一次性寿命不能同步提高,造成复吹比大幅度降低。
如何提高底吹供气元件寿命,已成为炼钢工业国际性难题。
3 转炉长寿复吹的技术发展转炉采用溅渣技术后,随着炉龄提高到一定水平时,转炉底吹供气元件被蚀损掉或出现堵塞,导致丧失底吹供气功能,而成为顶吹转炉炼钢。
国际炼钢界对此问题,采取了以下不同的技术措施。
4 长寿复吹转炉的技术发展复吹转炉炼钢工艺核心技术是底吹供气与供气元件。
二十余年来冶金工作者为保持底吹供气元件寿命与炉衬同步,进行了不懈的努力:•改变底吹供气元件结构:弥散式—狭缝式—毛细管式—环缝管式•生长蘑菇头保护技术:利用高速气体的冷却作用,液体金属在供气元件表面生长出蘑菇头,以此来保护供气元件。
•改进生产工艺:如降低出钢温度,采用渣补或火焰喷补技术。
溅渣护炉技术在复吹转炉上应用以后,钢铁研究总院工艺所与武钢等企业合作,经过技术攻关与理论实践,形成了多项专利技术,终于解决了底吹供气元件一次性寿命与炉龄不能同步的问题。
提高了底吹供气元件一次性寿命,我国冶金者攻克了冶金界一个世界性难题。
5 复吹技术在铁水预处理的应用长寿复吹技术在转炉领域得到了广泛的应用,在转炉脱磷冶炼工艺中,正是采用了两个复吹转炉联合作业,一座复吹转炉作为铁水预处理脱磷炉,另一座复吹转炉作为脱碳精炼炉。
经过预处理炉处理过的低磷、低硅半钢,兑入脱碳炉精炼成为优质钢水。
同时脱碳精炼炉的炉渣,可以处理后返回预处理脱磷炉中,作为化渣助熔剂使用.转炉双联炼钢工艺具有如下技术特点:(1)采用了两个复吹转炉联合作业,一座转炉作为铁水预处理脱磷炉,一座转炉作为脱碳精炼炉。
(2)在脱磷炉里完成了脱磷、部份脱硅及少量脱硫任务,实现了转炉铁水三脱预处理。
(3)精炼炉的任务可以大幅度减轻,将炼钢负荷简化为脱碳、升温,从而可以大幅度地提高供氧强度,实现高效转炉炼钢(包括自动化吹炼技术的采用)。
(4)大幅度地提高了转炉生产率,由于采用双联法,两个炉子联合作业后,冶炼周期大幅度地缩短,依然能达到两炉子2吹2的吹炼水平。
(5)由于实现了铁水全量预处理,可以在成本大幅度增加的情况,提高了钢水纯净度6 钢铁研究总院大力推广长寿复吹工艺钢铁研究总院工艺所经过二十余年的不解努力,长寿复吹转炉炼钢工艺技术推广工作获得了很大的成功:l 全国已有50个企业采用了我院的长寿复吹技术;l 从3-300吨200座转炉,包括全部炉型;l 现有4种基本型号500余支底吹供气元件在工作;l 转炉类型从铁合金熔炼转炉到普通转炉。
l 企业类型:国有大型企业(武钢等)、地方骨干企业(济钢)、股份制企业(津西钢厂)、民营企业(荣程钢厂)。
7 长寿复吹转炉技术基本特点•采用双环缝式底吹供气元件(钢铁研究总院专利产品),•底吹供气元件寿命与溅渣护炉后的转炉炉龄基本同步;•转炉底部布置根据炉容大小,布置多个底吹供气元件;•底吹供气支管路与供气元件数量相同,每路供气管路气量单独控制调节;•包括PLC基础级、上位机及其复吹供气模型软件的转炉复吹自动化系统;•建有采用工厂普通采用空气源的吹堵空气系统。
8 推广长寿复吹技术中产生的创新点•采用具有独立知识产权的环缝式底吹供气元件;•底吹供气强度可在较大范围内调整,以满足不同钢种的冶炼工艺需要;•底吹供气阀架设备的集成化、立体化、模块化;•完善的底吹控制自动化系统,形成了友好的人机控制画面;•支管旁通供应底吹基本气量技术,以保证供气系统的绝对安全;•远程控制吹堵技术在实践中应用。
9 长寿复吹转炉工艺成套技术钢铁研究总院工艺服务项目•向需求方提供工艺设计;•向需求方提供全部工程设计;•复吹工程全部设备供货;•全部工程施工指导服务;•提供厂内技术培训及操作规程;•提供全部控制软件编程;•复吹工程施工及开炉指导;•开炉后的复吹工艺技术服务。
10 冶金工艺所推广长寿复吹工艺技术业绩11 钢铁研究总院冶金工艺所推广长寿复吹工艺技术业绩l 授权实用新型专利2项;l 获得国家发明专利授权2项12长寿复吹转炉炼钢设备的特点底吹气源的供应:国内多数钢厂氮气和氩气气源供应量较紧张,压力不稳定。
为此在复吹转炉的底吹供气系统上设置了独立的增压站和储气罐,保证底吹气源的压力和流量的稳定。
实现在炼钢厂区内对复吹用气进行增压、调峰,保证复吹供气不受厂区总管网压力波动的影响。
底枪布置及底枪支数:我国早期复吹普遍采用单个或2个底吹供气元件,经常发生烧顶枪、喷溅及倒炉喷渣等问题。
为克服上述问题,开发多点供气技术:根据炉容及工艺的区别选择2-8支底吹底吹供气元件。
多路底吹供气系统均设有单独的流量、压力调节阀及检测系统。
可保证每支底吹供气元件供气均衡并保持稳定。
多路供气具有以下优点:(1)底吹能量分散,利于减少喷溅;(2)消除了倒炉时的经常发生的涌渣和炉口喷溅等现象,提高了安全性;(3)当个别底吹喷嘴堵塞时,其余底吹喷嘴自动提高供气量,保证工艺对底吹供气强度的要求;(4)多支底吹供气元件布置炉内圆周上,使炉内搅拌更加均匀。
13长寿复吹转炉炼钢设备的特点吹堵设备在长寿复吹技术中,采用厂内动力空气气源,可随时向复吹系统提供高压无油空气。
在底吹供气元件发生堵塞现象时用于吹堵,为底吹供气元件的维护提供辅助手段。
目前这一技术已获得了国家专利授权。
14 长寿复吹转炉炼钢设备的特点底部供气元件为解决喷嘴易堵塞问题,钢研总院研制开发了环缝管式底吹喷嘴并获得了国家专利授权。
环缝管式底吹喷嘴与传统集束管式供气元件相比,在使用中有如下优点:œ维护简单、不易堵塞,寿命长已做到大于15000炉,与炉龄同步;œ供气流量调节范围大,环缝管式底吹喷嘴在使用中气体流动阻力小,在较低压力下工作(0.3 MPa),不会堵塞;œ不易堵塞。
由于气流集中,动能大,对炉渣的穿透力强,不易发生堵塞;œ由于可在高压下工作,对钢种适应性强。
由于供气强度可在较大的范围内进行调整,从而保证了冶炼高碳钢到低碳钢等各类钢种对底部供气强度的要求。
15 底吹供气元件的维护效果16 底枪蘑菇头与底枪冷测通气量对比钢铁研究总院工艺所在试验室中,对用过的残枪进行了水模试验,将与新枪进行了对比,其性能基本一致,说明环缝式底吹元件的长寿性能良好。
17 停炉时拆下的底部供气元件水模试验18 长寿复吹工艺的技术路线1)“长寿复吹转炉冶炼工艺技术”将适应溅渣护炉的要求,底吹供气元件寿命与转炉高炉龄基本同步;(2)实现底吹供气元件的长寿,形成永久性蘑菇头保护底吹供气元件;(3)采取适当的维护措施,保证蘑菇头在全炉役内,具有良好的通气能力,能够控制与调节复吹的冶金效果。
(4)采用“长寿复吹转炉冶炼工艺技术”后,应能提高钢水的纯净度、缩短冶炼时间,获得一定的经济效益。
19 实用工艺方案举例120吨转炉长寿复吹工艺方案在吹炼前期采用氮气作为主搅拌气源,在终点倒炉前5分钟切换为氩气搅拌(或根据氧步实现这一功能)。
采用氩气搅拌钢水,为达到降低钢水终点氮含量的目的,吹氩气时间要求大于5分钟。
供气强度选择在0.03-0.10Nm3/t.min的范围内。
当底部供气强度超过0.10Nm3/t.min以后,提高底吹强度对熔池脱氮及均匀化已影响不大。
底部供气模式前期变化不大,后期需根据终点碳含量的变化改变供气强度。
终点碳越低,则底搅拌所需气量越大。
对高、中、低三种碳含量,一般设有C、B、A三种供气模式可供选择。
20 实用工艺方案举例工艺条件转炉公称炉容:120吨转炉最大装入量:130 吨转炉最大出钢量:120 吨21 底吹供气系统工程特点u 采用环缝式底吹供气元件(专利号:ZL01201717.5),底吹供气元件寿命与转炉炉龄基本同步;u 转炉底部布置底吹供气元件6个;u 底吹供气管路为6路供气,每路采用独立控制系统,每支底吹供气元件的流量可单独自动化控制调节;u 建有底枪空气吹堵模块,一旦发生底枪堵塞可用低压压缩空气复通;u 吹炼过程底吹供气采用模式控制方式,根据冶炼钢种要求选定控制模式后,由计算机全程闭环控制,无须人工干预;u 采用包括PLC基础级、上位机及复吹供气模型软件的转炉复吹自动化系统。
22 考核指标提供方提供“长寿复吹转炉工艺技术(LCB)”,应达到现今国内外先进水平。
采用“长寿复吹转炉冶炼工艺技术(LCB)”后,可达到如下技术经济指标:(1)复吹转炉底吹供气元件一次性寿命与炉龄同步;(2)冶炼低碳钢(终点碳含量在0.03-0.08%);[C]·[O]≤0.0030;(3)底吹气体在吹炼过程中快速切换并可调。