高铬铸铁耐磨衬板的热处理工艺改进
高铬热处理工艺

高铬铸热处理工艺化学成分:C2.05,Si1.40,Mn0.78,Cr26.03,Ni0.81,Mo0.351、常用的高铬铸铁的热处理工艺是加热到950~1000℃,经保温空冷淬火后再进行200~260℃的低温回火。
2、高温团球化处理1140~1180℃保温16h空冷却,可以明显提高冲击韧度和耐磨性能。
高温团球化处理可使碳化物全部呈团球状,可消除或减少大块状和连续网状碳化物对基体的隔裂作用,经团球化的碳化物受到更加均匀的基体支撑,特别受到一定数量的奥氏体的支撑。
如果适当减少保温时间,对薄截面零件也可以取得效果。
该工艺的不足是工艺消耗热能较多。
加热到1050℃,经保温空淬火后再进行550℃的回火,效果会怎么样?要控制加热速度,最好在650 750 850 时保温一定时间。
我以前做过,正火就可以了。
硬度能做到61----65HRC成熟工艺是:铸造后软化退火,便于加工,加工后空冷淬火加低温去应力回火。
使用硬度一般要求为HRC58-62,多用于比如渣浆泵零部件等耐磨易损件。
我们这里是高铬生产基地,一般提供Cr24,Cr26,Cr28,Cr15Mo3等,价格是不便宜的。
价格要包括中间的软化退火和精加后的淬火及回火。
楼主的材料应该叫Cr26做高铬磨球的,Cr%=10.2~10.5%,C%=2.2~2.7%,Si、S双零以下,要求硬度HRC>58我们现在用的是淬火液淬火,淬火工艺参数是:650度保温2小时,升温到960度保温3.5小时淬火;回火温度380~400,保温4~6小时。
磨球规格φ40-φ80。
工艺是1050淬火+250~350回火金属耐磨材料在水泥企业的研究和应用[摘要] 本文从金属耐磨材料的概述、水泥企业常用的耐磨材料以及根据磨损原理具体的选用金属耐磨材料,对金属耐磨材料进行了研究、分析,对其他选用金属耐磨材料给予一定的参考和借鉴。
[关键词] 金属耐磨材料水泥企业研究应用一、金属耐磨材料的概述材料的耐磨性不仅决定于材料的硬度Hm,而且更主要的是决定于材料硬度Hm和磨料硬度Ha的比值。
高铬铸铁耐磨衬板的热处理工艺改进

高铬铸铁耐磨衬板的热处理工艺改进我公司生产的2号和6号衬板是一种高铬合金铸铁,因其耐热耐磨性能好,广泛用于各大钢铁公司的高炉设备。
但由于其脆性大,无论在铸造还是在热处理过程中、极易断裂。
据我们过去统计,在热处理时,尺寸约在1000毫米×500毫米×25毫米以下的中小型衬板废品率一般在10~15%,尺寸在此以上的大衬板最高时甚至达到50%左右。
由于规格繁多,几何形状多样,生产难度较大,每年的平均废品率一般都在16%左右。
走访过一些单位,大家都认为衬板开裂的原因很多,与其铸造内在质量、外观质量、尺寸大小、几何形状、化学成分等多种因素有关。
但我们认为主要是热处理加热和冷却条件。
这种衬板在加热和冷却过程中体积变化特别突出。
加热时其体积增大,而冷却时体积缩小。
对同一块衬板来说,加热速度过快,体积增大速度上下不一,造成较大应力,导致开裂。
衬板在砂箱中摆放过挤,受热后体积增大受到限制,也会迫使它以开裂方式释放体积变化受阻产生的应力。
开裂最多是在出炉后,衬板在砂箱中以空气风冷时,边缘冷却快,体积大幅度收缩,而中部不易冷却,其红热部分收缩量滞后,中部阻止外部收缩,这时中部承受边缘施加的压应力,而边缘收缩受阻承受很大的拉应力,而衬板的韧性又较低,当拉应力达到一定极限后,外部边缘以开裂形式来释放应力。
这时如注意观察会发现,裂纹通常起源于衬板冷得最快的长边中段某处,因为这里的应力聚集最大,开口裂得较宽,裂口端部可达3~4毫米,当中部随时间延长逐渐降温收缩后,边缘与中部的收缩量接近一致,裂口便闭合在一起,然而,很长的裂纹已经产生,甚至断开。
所以我们认为冷却和加热过程中,在同一块衬板上的温度一致性,是保证衬板不裂的决定性因素。
裂因明确后,在加热过程中,我们采取逐步升温、均温的方法,这与老方法基本相同,目的使同一块衬板均匀受热,各部分膨胀系数基本一样,但必须注意要将大衬板摆放在宽松的工装或砂箱内,让其可以有足够的空间膨胀。
高铬铸铁的热处理

高铬铸铁的热处理1. 退火由于高铬制品其铸态硬度较高,为改善工件的机械加工性能,所有毛坯必须进行必要的软化退火处理。
具体工艺( 以壁厚不超过100mm且外形较复杂铸件为例) 如下。
首先将需处理工件在室温下装入热处理炉,然后随炉缓慢升温至400 ℃左右进行保温1 ~2h,随后将炉温升至600 ℃再进行保温1 ~2h,之后以不超过150 ℃/ h的温升速度,将炉温快速升至950 ℃后进行2 ~3h 的保温,而后停止加热,待炉温自然降至820 ℃左右,此后可控制电炉以10 ~15 ℃/ h 的温降速度将炉温降至700 ~720 ℃,并在此温度保温4 ~6h ( 工件越厚其保温时间应越长) 后停炉,工件可视情况随炉冷却或出炉置于静止的空气中冷却至室温( 以获得珠光体基体,满足性能要求,便于切削加工) 。
具体生产中,若所处理工件形状较为简单,也可采用较快速的退火工艺,即在温升至950 ℃并保温3h 后停炉,之后可随炉冷却至400 ℃左右,然后打开炉门,继续冷却至300 ℃以下,工件即可出炉空冷。
工件退火后可进行机械加工,由于高铬白口铸铁在淬火过程中尺寸变化比铸钢和灰铸铁小的多,一般无须矫正尺寸,对于按工艺要求需磨削加工的工件所留磨削量也可很小。
2. 淬火将机械加工后的工件室温装炉,以小于80 ℃/ h 的温升速度将炉温升至600 ℃( 若工件较厚或形状较复杂,可在温升至300 ℃、400 ℃、500 ℃、600 ℃时分别给予0. 5h 的保温) ,之后以不超过150 ℃/ h 的温升速度将炉温升至淬火温度950 ~980 ℃后进行保温,保温时间为2~4h ( 视工件厚薄不同保温时间有所差别,越厚保温时间越长) ,而后将工件快速出炉进行空冷,若遇环境气温较高,淬火时应辅以强风和水雾喷洒,以强化冷却,淬火工艺曲线如图2 所示。
3. 回火为降低铸件残余应力和脆性,并保持其淬火得到的高硬度和耐磨性,同时也使马氏体得以回火,以及残余奥氏体有所减少,应对淬火后的工件再进行230 ~260 ℃的回火处理。
热处理工艺对金属材料的耐磨性和耐蚀性的改善

热处理工艺对金属材料的耐磨性和耐蚀性的改善热处理工艺是一种通过控制金属材料的温度和时间,从而改变其组织结构和性能的方法。
在金属材料的应用中,耐磨性和耐蚀性是两个重要的性能指标。
热处理工艺可以有效地改善金属材料的耐磨性和耐蚀性,提高其在各种工作环境下的使用寿命和性能。
首先,耐磨性是指金属材料在摩擦和磨损条件下不易受到表面破坏的能力。
金属材料的耐磨性取决于其组织结构和硬度等因素。
通过热处理工艺加工,可以改变金属材料的晶粒结构,提高其硬度和强度,从而提高耐磨性。
例如,通过淬火热处理,金属材料的组织结构可以变得均匀细小,晶界清晰,从而提高其硬度和抗磨损能力。
此外,通过淬火时的快速冷却和回火处理,可以在金属材料中形成均匀的残余应力和强化相,提高其抗疲劳和抗裂纹扩展能力,进一步增加耐磨性。
其次,耐蚀性是指金属材料在各种腐蚀介质下能够保持其表面和性能的能力。
金属材料的耐蚀性主要取决于其化学成分和表面保护膜等因素。
通过热处理工艺可以改变金属材料的化学成分和表面状态,从而提高其耐蚀性。
例如,通过淬火热处理,可以增加金属材料中的合金元素含量和析出相的形成,增加材料的耐蚀能力。
同时,通过热处理过程中的气体保护,可以减少金属材料与氧气的接触,减少氧化反应,从而提高耐蚀性。
此外,通过表面覆盖涂层或浸渍处理,可以形成一层保护膜,提高金属材料的抗腐蚀能力。
总之,热处理工艺可以通过改变金属材料的组织结构和化学成分,提高其耐磨性和耐蚀性。
对于提高金属材料的耐磨性,可以通过控制热处理工艺参数,使其组织结构细化和均匀化,提高硬度和抗磨损能力。
对于提高金属材料的耐蚀性,可以通过调整热处理工艺条件和采用表面保护措施,形成保护膜和增加合金元素含量,提高其耐蚀能力。
热处理工艺的改善对金属材料的耐磨性和耐蚀性提供了有效的方法,有利于金属材料在各种工作环境下的应用和延长使用寿命。
热处理工艺对金属材料的耐磨性和耐蚀性的改善是通过改变材料的组织结构和化学成分来实现的。
高强度高铬铸铁衬板的热处理.
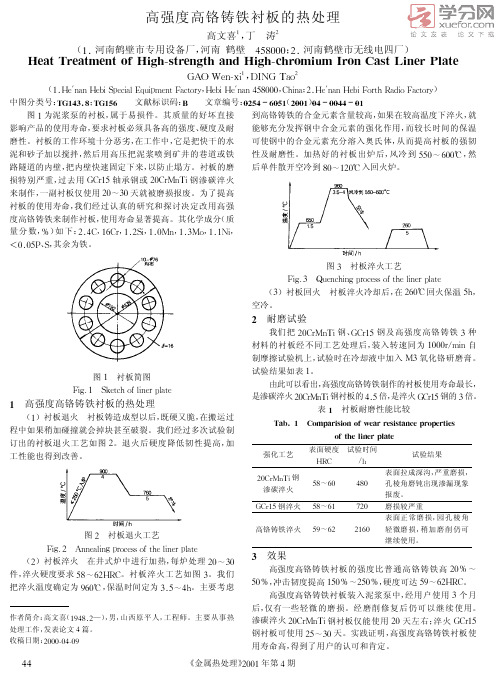
度高铬铸铁来制作衬板,使用寿命显著提高。其化学成分(质
量分 数,% )如 下:2. 4C,16Cr ,1. 2Si ,1. 0 Mn ,1. 3 Mo ,1. 1 Ni , !0. 05P 、S,其余为铁。
图1 衬板简图 Fi g .1 Sketch of li ner plate
l 高强度高铬铸铁衬板的热处理
(1. ~e/ nan ~ebi Special ECui p ment Factory ,~ebi ~e/ nan 458000 ,Chi na ;2. ~e/ nan ~ebi Fort h Radi o Factory ) 中图分类号:Tgl43 .8 ;Tgl56 文献标识码:B 文章编号:0254 -605l(200l )04 -0044 -0l
高强度高铬铸铁衬板的热处理
高文喜1 ,丁 涛2
(1. 河南鹤壁市专用设备厂,河南 鹤壁 458000 ;2. 河南鹤壁市无线电四厂)
heat Treat ment of hi gh-strengt h and hi gh-chro mi u m iron cast Li ner pl ate
GA0 Wen- xi 1 ,DI NG Tao2
(1 )衬板退火 衬板铸造成型以后,既硬又脆,在搬运过 程中如果稍加碰撞就会掉块甚至破裂。我们经过多次试验制 订出的衬板退火工艺如图2 。退火后硬度降低韧性提高,加 工性能也得到改善。
图2 衬板退火工艺 Fi g .2 Anneali ng process of t he li ner plate (2 )衬板淬火 在井式炉中进行加热,每炉处理20 !30 件,淬火硬度要求58 !62 ~RC。衬板淬火工艺如图3 。我们 把淬火温度确定为960 C ,保温时间定为3. 5 !4h 。主要考虑
高铬铸铁衬板铸造工艺的优化设计

根据试 制 时 出现 的铸 造缺 陷 ,改 进时 主要 针对 缩 孔 、 孔 的缺 陷采取 了措施 。 气 ( ) 后 衬板 的外 缘开 设 6个 内浇 道 , 1在 在直 浇道 对
面开设 o 0 的溢流 槽 ,在 中间位 置设 置 o 0 的 4 mm 5 mm
Po u t nT c nq e rd ci e h iu s生 产技 o
高铬铸铁衬板铸造工艺的优化设计
刘 金旺 ( 家庄 强 大泵业 集 团有 限责任 公 司 , 家庄 石 石 00 3 5 0 5)
摘要: 通过改进 内浇道 、 直浇道 、 出气孔 的设计 , 保温冒口的使用 , 以及严格控制生产过程 的各个环节, 品的 产
缩孔 、 气孔废 品大大减 少 , 毛坯 的废 品率 降至 2 %以下。
关键词: 高铬铸铁 ; 衬板; 铸造工艺
中 图分 类号 : G 5 2: T 2 l. 文献 标 识码 : ; B 文章编 号 : 0 6 9 5 ( 0 1 0 — 1 0 — 6 8 2 l )4 2 2 1 我公 司接 到一 个 生 产 高 铬 铸 铁 后 衬 板 备 0 0年 件 的项 目, 衬 板毛 坯 三维 图如 图 1 后 所示 。 该衬 板最 大 直径 o44 14 mm, 7 mm, 孑 直 径 o 6 m 单 面 加 高 6 内 L 94 m,
工余量 8 m, m 铸件重 1Ok 。 lO g 材质为高铬铸铁 , 产品技 术要求十分严格 , 加工面不允许有任何铸造缺陷。
出气孔,并在上砂型上扎出气孔 ,在上平面放置一个 o 6 m 的保 温 冒 口 , 20m 如图 3 。
图 1 后衬 板 毛 坯 三 维 图
1 原铸 造 工艺
高铬铸铁件的热处理

高铬铸铁件的热处理
高铬铸铁件作为一种抗磨材料,除了具有必要的强韧性以外,其硬度是最重要的质量指标,有些高铬铸铁件可以在铸态下获得所需要硬度,但是绝大多数是要通过热处理来达到硬度要求的。
热处理几乎是每一个高铬铸铁件必须经过的工序,合理淬火可使铸件获得最佳的抗磨料磨损的能力;退火可改变铸件的切削性能,使之能够机械加工,还有一些热处理工艺措施可以提高铸件的强韧性和改善各种使用性能,应该说,热处理是发挥高铬铸铁将性能潜力的重要手段。
高铬铸铁件与合金钢件在淬火工艺规范有一定的差别,主要表现在以下几方面:
1、高铬铸铁组织中存在大量共晶碳化物,这些碳化物与基体金属的热胀缩和热传导方面存
在一定的差别。
热处理过程中急剧的温度变化会使碳化物周围产生较高的热应力,极易在碳化物附近产生热裂纹。
2、高铬铸铁的奥氏体中溶有大量碳和铬,以及其他合金元素,淬火后基体组织中还保留大
量奥氏体。
这些残余体不但影响淬火硬度,而且还会导致铸件在淬火后或使用中开裂或变形。
3、高铬铸铁件淬火时,必须经过脱稳处理过程,脱稳处理的加热混入保温过程取决于材料
的碳含量和铬碳比。
保温及深冷处理对改善高铬铸铁性能的研究
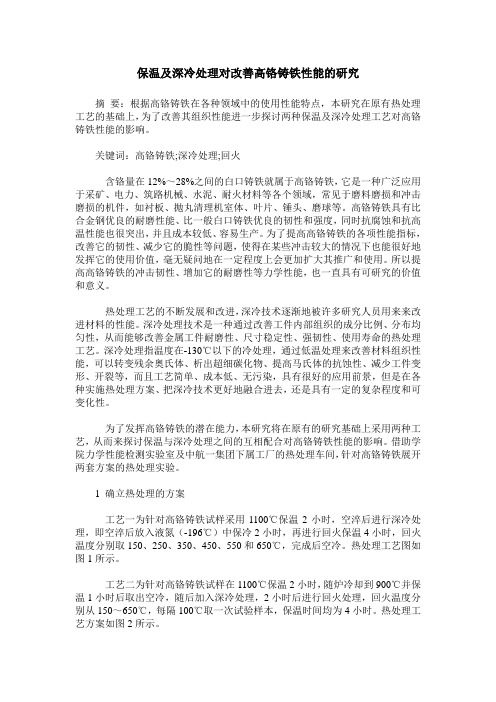
保温及深冷处理对改善高铬铸铁性能的研究摘要:根据高铬铸铁在各种领域中的使用性能特点,本研究在原有热处理工艺的基础上,为了改善其组织性能进一步探讨两种保温及深冷处理工艺对高铬铸铁性能的影响。
关键词:高铬铸铁;深冷处理;回火含铬量在12%~28%之间的白口铸铁就属于高铬铸铁,它是一种广泛应用于采矿、电力、筑路机械、水泥、耐火材料等各个领域,常见于磨料磨损和冲击磨损的机件,如衬板、抛丸清理机室体、叶片、锤头、磨球等。
高铬铸铁具有比合金钢优良的耐磨性能、比一般白口铸铁优良的韧性和强度,同时抗腐蚀和抗高温性能也很突出,并且成本较低、容易生产。
为了提高高铬铸铁的各项性能指标,改善它的韧性、减少它的脆性等问题,使得在某些冲击较大的情况下也能很好地发挥它的使用价值,毫无疑问地在一定程度上会更加扩大其推广和使用。
所以提高高铬铸铁的冲击韧性、增加它的耐磨性等力学性能,也一直具有可研究的价值和意义。
热处理工艺的不断发展和改进,深冷技术逐渐地被许多研究人员用来来改进材料的性能。
深冷处理技术是一种通过改善工件内部组织的成分比例、分布均匀性,从而能够改善金属工件耐磨性、尺寸稳定性、强韧性、使用寿命的热处理工艺。
深冷处理指温度在-130℃以下的冷处理,通过低温处理来改善材料组织性能,可以转变残余奥氏体、析出超细碳化物、提高马氏体的抗蚀性、减少工件变形、开裂等,而且工艺简单、成本低、无污染,具有很好的应用前景,但是在各种实施热处理方案、把深冷技术更好地融合进去,还是具有一定的复杂程度和可变化性。
为了发挥高铬铸铁的潜在能力,本研究将在原有的研究基础上采用两种工艺,从而来探讨保温与深冷处理之间的互相配合对高铬铸铁性能的影响。
借助学院力学性能检测实验室及中航一集团下属工厂的热处理车间,针对高铬铸铁展开两套方案的热处理实验。
1 确立热处理的方案工艺一为针对高铬铸铁试样采用1100℃保温2小时,空淬后进行深冷处理,即空淬后放入液氮(-196℃)中保冷2小时,再进行回火保温4小时,回火温度分别取150、250、350、450、550和650℃,完成后空冷。
- 1、下载文档前请自行甄别文档内容的完整性,平台不提供额外的编辑、内容补充、找答案等附加服务。
- 2、"仅部分预览"的文档,不可在线预览部分如存在完整性等问题,可反馈申请退款(可完整预览的文档不适用该条件!)。
- 3、如文档侵犯您的权益,请联系客服反馈,我们会尽快为您处理(人工客服工作时间:9:00-18:30)。
高铬铸铁耐磨衬板的热处理工艺改进
我公司生产的2号和6号衬板是一种高铬合金铸铁,因其耐热耐磨性能好,广泛用于各大钢铁公司的高炉设备。
但由于其脆性大,无论在铸造还是在热处理过程中、极易断裂。
据我们过去统计,在热处理时,尺寸约在1000毫米×500毫米×25毫米以下的中小型衬板废品率一般在10~15%,尺寸在此以上的大衬板最高时甚至达到50%左右。
由于规格繁多,几何形状多样,生产难度较大,每年的平均废品率一般都在16%左右。
走访过一些单位,大家都认为衬板开裂的原因很多,与其铸造内在质量、外观质量、尺寸大小、几何形状、化学成分等多种因素有关。
但我们认为主要是热处理加热和冷却条件。
这种衬板在加热和冷却过程中体积变化特别突出。
加热时其体积增大,而冷却时体积缩小。
对同一块衬板来说,加热速度过快,体积增大速度上下不一,造成较大应力,导致开裂。
衬板在砂箱中摆放过挤,受热后体积增大受到限制,也会迫使它以开裂方式释放体积变化受阻产生的应力。
开裂最多是在出炉后,衬板在砂箱中以空气风冷时,边缘冷却快,体积大幅度收缩,而中部不易冷却,其红热部分收缩量滞后,中部阻止外部收缩,这时中部承受边缘施加的压应力,而边缘收缩受阻承受很大的拉应力,而衬板的韧性又较低,当拉应力达到一定极限后,外部边缘以开裂形式来释放应力。
这时如注意观察会发现,裂纹通常起源于衬板冷得最快的长边中段某处,因为这里的应力聚集最大,开口裂得较宽,裂口端部可达3~4毫米,当中部随时间延长逐渐降温收缩后,边缘与中部的收缩量接近一致,裂口便闭合在一起,然而,很长的裂纹已经产生,甚至断开。
所以我们认为冷却和加热过程中,在同一块衬板上的温度一致性,是保证衬板不裂的决定性因素。
裂因明确后,在加热过程中,我们采取逐步升温、均温的方法,这与老方法基本相同,目的使同一块衬板均匀受热,各部分膨胀系数基本一样,但必须注意要将大衬板摆放在宽松的工装或砂箱内,让其可以有足够的空间膨胀。
这样通常可以保证衬板在炉中不裂。
衬板出炉时是最关键的步骤。
冷却速度的快慢决定着硬度的高低,而同一块衬板上如何均温冷却,决定着裂与不裂。
为此,我们做了大量的工作,用风吹、向中部喷水雾,但都不具备良好的可操作性,尤其是喷水雾,尽管可以使硬度提高、开裂率下降,但对操作者的要求太严,不能有任何粗心大意,在生产实际中很难实施,只能停留在实验中。
最后,我们采取分批单件散开,即在台车炉加热衬板出炉时,迅速将其中的一砂箱吊离炉底板,并立刻一块一块散开空冷。
为防止台车上的衬板出炉后,边缘与其中部随时间延长造成较大温差,一定要及时将台车开进炉内均温,均温时不送电、炉门可以不全关。
目的是防止衬板边沿变暗或使已稍变暗的边沿回温,以保证其均温效果。
第一批散开后,再出第二批砂箱,如此直到全炉衬板出完。
最后一批出炉的衬板,温度一般控制在仪表显示760℃以上,其硬度值不受影响。
这样便解决了衬板均温快速冷却的问题。
这一方法效果非常明显,不仅不易出现开裂,而且衬板中部与边缘基本同时冷却,冷却过程中各处的体积收缩速度趋于一致,产生的热应力也很小。
更大的优点是衬板硬度各处一致,避免了在砂箱中冷却时,衬板的硬度边缘只能勉强合格、中部则往往严重偏低的问题。
由于散开后冷却速度加快,其硬度值也得以显著提高,2号衬板一般达到58~64HRC, 6号衬板达到54~60HRC,均达到技术要求。
特别要提的是我们通过科学分析、实验验证后认为:均温冷却过程中残留应力很小,传统的低温回火又对这种高铬铸铁的机械性能几乎不产生作用,所以在新工艺方法中,将通常认为“必不可少的回火工艺”省去。
这样在衬板热处理质量不受影响的同时,还使工艺周期大大
缩短,生产效率得到提高。
附1:高铬铸铁衬板热处理新工艺
采用(2×5m²)650kw台车式电阻炉加热衬板:200℃以下装炉,阶梯升温,200℃保温1小时;350℃保温1.5小时;500℃保温1小时;650℃保温1.5小时;960℃保温2~2.5小时;停炉;分批
出炉空冷,迅速全部散开。
注释:
1、硬度值与960℃保温时间有关,不宜过短。
2、季节对本工艺有一定的影响。
出炉时,气温越低,散开衬板的速度应当越快。
冬季出炉前,可先停电降温至900~920℃左右,然后出炉,这样可以让衬板在炉内有个缓慢适应降温的过程,并减轻炉内温度与环境温度差别过大的影响,减少因散开不够及时造成的开裂。
3、以上工艺的改进,关键在出炉方式,尤其对较宽大的衬板,单件散开速度必须快,否则中部
冷却滞后于边沿,极易开裂。
附2:新、老工艺生产的废品率统计分析对比
表1 2003年耐磨高铬铸铁衬板废品率统计分析
Table 1 Statistics & analysis on the rate of waste product for wear-resistance &
High-chromium Iron Cast Liner Plate in 2003
月份热处理工艺
产量
(吨)
废品量
(吨)废品率
(%)
废品主要原
因分析
备注
1 老工艺:将衬板阶梯升温至960℃х2h出炉,在砂箱或工装架上空冷或风冷约1小时后,280~300℃回火5小时。
57.540 8.200 14.25 空冷过程中,
同一块衬板上冷热
不均。
中部冷却慢,
导致硬度偏低,边沿
冷却相对快,导致开
裂。
低温回火对防裂
和硬度无明显影响。
对老
工艺进行
观察分析
阶段,找出
了开裂产
生的原因。
2 91.700 9.260 10.10
3 76.380 13.480 17.65
4 老工艺:960℃
出炉后,空冷的同时对砂箱中部红热部分采取喷水雾促使均匀降温。
97.910 8.690 8.88
喷水雾可以
提高硬度,控制得
好、开裂率能够下
降,但操作要求严、
不宜掌握,难以实
施。
试验
喷水雾阶
段。
5
114.53
4
5.466 4.77
较好
地控制喷
雾,能够达
到废品率
≤5%的目
标。
6 本月中旬试行
散开空冷新工艺。
82.433 3.829 4.64
仍以喷水雾
措施为主。
7 7月起正式执行新工艺,与老工艺相比,新工艺适当缩短了升温加热总时间,960℃出炉后,衬板全部散开空冷,82.660 0.406 0.49 严格按新工
艺执行后,废品率明
显降低,可以非常有
把握地控制在公司
要求的5%以下。
但
10月内,由于天气
新工
艺带来的
效果,令人
十分满意。
8 82.433 0.807 0.98
9 55.203 0.451 0.82
1 0 69.33
2 3.364 4.85
工装
吊具不配
使同一块衬板能够快速均匀降温,保证
了硬度值稳定提高,由于大大减轻了冷热不均产生的热应力,故而省去了回火工艺,且产品质量和生产效率同时大幅度提高。
变冷、重视不够,加之大衬板(每块300kg 以上)较多、
工装吊具不配套、散开不够及时等原因,曾出现一炉开裂6块大衬板的现象。
重视后,11月内,改变大衬板工装吊具,并适当降温后出炉,废品率得以控制。
套、散开不够及时。
11
59.612
0.847
1.42
恢复
到满意状
态。
12
68.167
0.358
0.53
7~12月执行新工艺的产量、质量统计结果。
417.40
7
6.233
1.49
结论:执行新工艺半年,
总废品率为1.49% 。
远低于公司要求的5%指标。
从2003年全年生产情况看,自7月份开始采用新工艺后,废品率大幅度降低。
通过近几年的生产实践,截止目前,尚未发现省去回火工艺对质量有任何影响,广大用户对我公司的产品使用寿命非常满意。
实践证明:使用本工艺进行衬板热处理,硬度质量可达100%合格、开裂废品率可以非常
有把握地控制在1. 5%以下,从而解决了衬板热处理开裂量大的难题。