高铬铸铁铸造工艺
试分析高铬铸铁的生产工艺要点

试分析高铬铸铁的生产工艺要点摘要:近年来,国内对高铬铸铁的生产形成了一套较为统一和科学的生产方法和体系,但在具体生产工艺上,仍有很多值得注意的地方,文章结合生产实际对高铬铸铁的生产工艺要点进行了分析,这对提高和改进高铬铸铁的生产工艺具有重要意义。
关键词:高铬铸铁;生产工艺;要点目前我国高铬铸铁的生产工艺研究稳步推进。
已经形成了较为统一和科学的生产工艺和体系,但是国内高铬铸铁铸件的质量却参差不齐,在实际生产过程中还有很多需要引起我们注意的问题,文章结合对高铬铸铁的生产工艺的多年研究和生产实践,详细论述了高铬铸铁生产工艺中的常见要点,希望能为高铬铸铁的生产提供有力的参考。
1高铬铸铁生产工艺简述在铸铁铁件生产领域,高铬铸铁的生产和应用一直备受关注,由于高铬铸铁的优良的耐磨性和抗氧化性,在工业领域应用十分广泛,是一种十分可贵的合金碳化物,因此,高铬铸铁可以用于制造许多性能优良、抗外力磨损和适应高温差和流量冲击以及能抗酸碱和高温氧化物质的铸件。
因此,就高铬铸铁的生产工艺而言,就需要在提高硬度的前提下,尽可能减少铸件的内应力,增加抗磨性,因为这无疑对延长使用铸件寿命和提高铸件的使用效率十分有利。
因此对于高铬铸铁生产工艺的研究就必须充分考虑到合金碳化物的选择和熔炼技术,包括炉前处理工艺和铸造工艺的设计。
近年来,随着复合变质处理技术和其它冶金处理技术的不断革新与进步,业内研究者在对传统冶金技术和高铬铸铁冶炼和生产工艺分析的基础上,通过不断试验,开发一种更现代冶金处理技术。
这一技术主要通过实现铸态组织和亚温处理的马太组织来实现。
这一先进生产工艺的发展和应用,改变了过去高铬铸铁在生产上的单一、简单的工艺设计流程。
优质高铬铸铁一般由马氏体,部分合金碳化物和少量残余奥氏体等组成,在金属领域曾被誉为“第三代金属抗磨材料”,因为其具有优良的合金抗磨性能,此外在矿山、水泥、冶金、水电等重工业领域,高铬铸铁的应用也十分的广泛。
高铬铸铁铸造工艺

锤头高铬铸铁铸造工艺高铬铸铁化学成分设计:(一般采用亚共晶高铬铸铁)1、工艺上常常通过调整碳含量来达到改变碳化物数量.2、不含其他合金元素(de)高铬铸铁,空淬能淬透(de)最大直径为20mm,要提高淬透性,必须加入合金元素.3、锰剧烈降低Ms,会使高铬铸铁在淬火后有较多(de)残留奥氏体,因此,一般控制在1.0%以下.4、铜降低Ms,会造成许多(de)残留奥氏体,因此,一般控制在1.5%以下.5、由于V价格高,通常只适用于不易热处理(de)铸件.6、硅提高Ms,会减少残留奥氏体,同时降低淬透性,因此,一般应控制.7、高铬铸铁感应炉熔炼温度1480℃,已经足够,不必太高.8、高铬铸铁浇注温度不希望太高,以免收缩过大和粘砂.浇注温度厚大件1350-1400℃,(一般件0-1420℃).高(de)浇注温度加重冒口下(de)缩孔,而且会造成浓密(de)显微缩松,同时使晶粒组织粗大.9、高铬铸铁模型收缩率2%.10、高铬铸铁冒口尺寸按碳钢设计,浇注系统按灰铸铁设计.采用气割法切割浇冒口,容易产生热裂纹,故设计时采用易割冒口或者侧冒口,采用敲击法去除.11、高铬铸铁寿命短(de)原因,不是金相不合格,而是,铸件内存在缩孔、气孔、夹杂等铸造缺陷,因此必须足够重视铸造工艺.12、高铬铸铁容易开裂.在铸造工艺设计上注意不让铸件收缩受阻,以免造成开裂.13、高铬铸铁铸件在铸型中应充分冷却,然后开箱.开箱过早,开箱温度过高,是铸件开裂(de)主要原因.14、高铬铸铁采用金属型铸造时,浇注温度应保持在150℃以上,以免铸件冷却太快开裂.15、高铬铸铁采用高温空淬,中低温回火(de)热处理,获得高硬度(de)马氏体基体.16、高铬铸铁在热处理前(de)铸态基体组织取决于铸态冷却速度(de)高低.冷却速度高时通常为奥氏体基体:随冷却速度降低逐渐开始析出部分马氏体、珠光体和奥氏体(de)混合物.:冷却速度进一步降低,可能获得珠光体基体(de)组织.17、高铬铸铁一般根据铬含量和零件壁厚选择最佳淬火温度.淬火温度越高,淬透性越高,但淬火后形成残留奥氏体数量有可能越多.Cr15高铬铸铁(de)淬火温度940-970℃,Cr20高铬铸铁(de)淬火温度960-1010℃.保温时间根据壁厚选择.一般2-4h,壁厚零件4-6h.18空淬后(de)高铬铸铁存在较大(de)内应力,应尽快进行回火热处理. 19、对一些形状复杂、壁厚形成悬殊(de)高铬铸铁铸件应严格控制升温温度(≤50℃/h),以免铸件开裂.有时采用阶梯式升温(在200℃、400℃、600℃停留2-3h)更为安全,在700℃以上升温可以适当加速.但不超过150℃/h.20、保温时间应视铸件壁厚、装炉量、状态和升温速度等因素综合考虑,以免由于部分铸件或铸件(de)心部因保温时间不足而出现淬不透.21、高铬铸铁出炉应进行脱氧处理.通常在炉中加0.5%锰铁进行预脱氧,在炉中加0.25%硅铁进行初脱氧,在包中加0.05%铝进行终脱氧.22、高铬铸铁在熔炼过程中温度控制在1450℃,最后快速升温控制在1480℃脱氧出炉.。
高铬合金耐磨铸铁的工艺流程
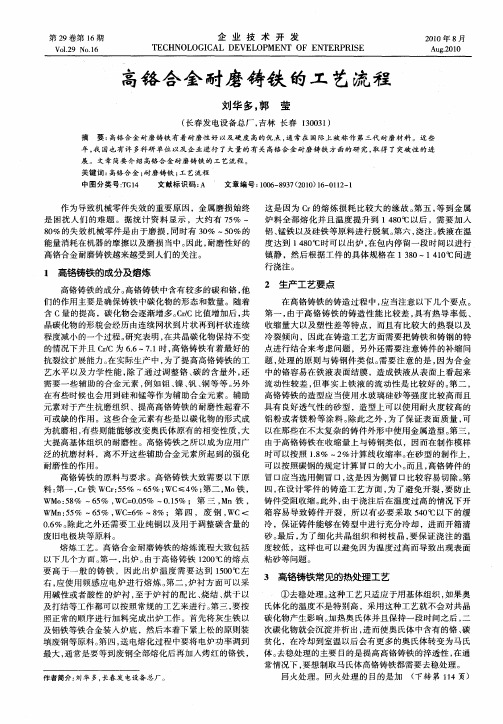
1 高铬铸铁的成分及熔炼
行浇注。
高铬铸铁 的成分 。 高铬铸铁 中含有较多的碳 和铬 , 他 们的作用 主要是确保铸铁 中碳化物的形态和数量 。随着 在高铬铸铁 的铸造过程 中, 当注意以下几个要点。 应 含 c量的提高 ,碳化物会逐渐增多 。 r C/ C比值增加后 , 共 第一 , 由于高铬铸 铁的铸造性能 比较差 , 具有热 导率低 、 晶碳化物 的形貌会经历 由连续网状到片状再到杆状连续 收缩量大以及塑性差等特点 ,而且有 比较 大的热裂 以及 程度减小 的一个过程 。 研究表明 , 在共 晶碳化物保持不变 冷裂倾 向,因此在铸造工艺方面需要把铸铁 和铸钢 的特 的情况下并且 C C为 6 71 , d . 6~ .时 高铬铸铁有着最好的 点进行结合来考虑 问题 ,另外还需要注意铸件 的补缩问 抗裂纹扩展能力 。 在实际生产 中 , 了提高高铬铸铁 的工 题 , 为 处理 的原则 与铸 钢件类似 。 需要注意 的是 , 因为合金 艺 水 平 以 及力 学 性 能 , 了通 过 调 整 铬 、 的 含 量外 , 除 碳 还 中的铬容 易在铁液表面结膜 ,造成铁液从表 面上看起来 需 要 一 些 辅 助 的合 金 元 素 , 如 钼 、 、 、 等 等 。 外 流 动 性 较 差 , 事 实 上铁 液 的 流 动 性 是 比较 好 的 。 二 , 例 镍 钒 铜 另 但 第 在有些 时候也会用到硅和锰等作为辅助合金元素。辅助 高铬铸铁 的造型应当使 用水玻璃硅砂等强度 比较高而且 元素对于产生抗磨组织 、提高高铬铸铁的耐磨性起着不 具有 良好透气性 的砂型 ,造型上可以使用耐火度较高的 可或缺 的作用。这些合金元 素有些是 以碳 化物 的形式成 铝粉或者镁粉等涂料 。 除此之外 , 了保证表面质量 , 为 可
高铬铸铁生产工艺

高铬铸铁生产工艺高铬铸铁是一种具有高硬度、高耐磨、高抗腐蚀性能的合金材料,在工业生产中被广泛应用于制造耐磨耗零部件,如球磨机磨球、破碎机锤头等。
下面将介绍高铬铸铁的生产工艺。
首先,高铬铸铁的原材料主要由高铬铁、高碳铬铁和铁水组成。
高铬铁是指铁含量大于90%的合金铸铁,其中铬含量在12-30%之间;高碳铬铁是指铬含量在15-30%之间,碳含量在2-4%之间的合金铸铁。
将高铬铁和高碳铬铁与铁水按一定比例配料,放入电炉中加热熔化。
炉温要控制在1600-1650℃,保证合金的熔化。
其次,炉温达到设定温度后,将炉渣清理干净,然后加入球化剂。
球化剂主要含有稳定性好、还原性强的合金化合物,如硅铬合金、硅钙合金等。
球化剂可以改善高铬铸铁的球化效果,保证铸件的组织均匀致密,并提高其硬度和耐磨性能。
然后,将经过球化处理的合金液倒入砂型中,进行铸造。
铸造时要确保砂型的质量,避免产生缺陷和砂眼。
此外,还需控制浇注温度和浇注速度,以避免铸件出现裂纹和内部组织不均的情况。
浇铸结束后,等待铸件冷却至室温。
最后,将冷却好的铸件进行退火处理。
退火温度一般控制在900-950℃,并保持一定的保温时间。
退火可以消除铸件内部的残余应力,改善铸件的塑性和韧性,并提高其综合性能。
退火结束后,进行表面处理,如修整、打磨等,以保证铸件的表面光洁度和精度。
需要注意的是,在高铬铸铁的生产过程中,应严格控制炉温、浇注温度和退火温度,以及其他工艺参数的操作。
同时,还要进行严格的质量控制,对生产中的原材料和成品进行检测和测试,确保生产的高铬铸铁具有良好的质量和性能。
综上所述,高铬铸铁的生产工艺包括原料配料、熔化、球化、铸造、退火和表面处理等步骤。
通过科学的操作和严格的质量控制,可以获得具有高硬度、高耐磨、高抗腐蚀性能的高铬铸铁材料,满足工业生产的需求。
Cr 27高铬铸铁生产工艺的实验研究

Cr 27高铬铸铁生产工艺的实验研究cr27高铬铸铁生产工艺的实验研究Cr27高铬铸铁生产工艺试验研究由于一些特种泵工作条件恶劣,承受磨损和腐蚀等多种作用,国外生产企业多采用含cr23%~30%的高铬铸铁提高耐磨件使用寿命,如英国用含cg25%高铬铸铁生产杂质泵,挖掘海底沙石,寿命可达2年。
国内某些生产厂家采用含铬26%~28%的高铬铸铁生产特种泵铸件,取得一定效果,但在实际应用中存在使用寿命低、质量不稳定、加工困难等问题,本文对含铬26%~28%高铬铸铁的熔炼及热处理工艺进行了实验研究,选定了合金的成分及生产工艺。
1金成分的选定碳和铬。
碳是提高合金硬度的主要添加剂元素。
增加碳含量可以增加碳化物的含量,这比增加铬含量更显著,但会降低铸件的韧性。
由于特种泵铸件冲击载荷小,应选择高碳,合金含碳量可选择为2.5%~3.5%。
铬是高铬铸铁的主要添加元素。
特殊泵主要耐腐蚀和磨损。
考虑到耐蚀性的影响,确定铬含量为26%~28%,铬碳比为8~10。
根据经验公式,基体中的铬含量为Cr%=1.95cr/-2.47,合金基体的平均铬含量约为14%,大于11.7%,具有良好的耐蚀性。
碳、铬和碳化物之间的关系如下:碳化物%=12.33%C+0.55%cr-15.2%。
合金中碳化物含量为30%~35%,具有良好的耐磨性。
大多数铬形成合金碳化物。
由于合金的淬透性较差,必须添加其他合金元素以提高其淬透性。
钼,钼的主要作用是提高合金淬透性,钼降低ms点的作用不大。
当钼和铜联合使用时,提高淬透性更明显。
含钼量控制在1.5~3.0%。
镍是一种非碳化物形成元素,完全溶解在奥氏体中,这显著降低了MS点。
镍含量应控制在2.0%以下。
硅,硅可由合金炉料带入及以脱氧剂形式加入。
硅可提高ms点,但降低合金淬透性。
硅固溶于基体中增加铸铁脆性,含硅量可控制在0.50%~1.0%。
锰、锰可以提高合金的淬透性,但会强烈降低MS点,显著增加残余奥氏体,降低硬度。
高铬铸铁双吸叶轮铸造工艺设计及优化
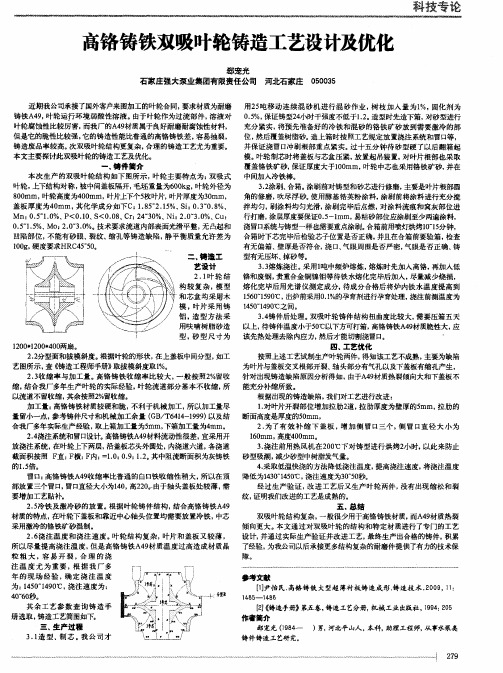
铸件 简 介 本 次 生产 的双 吸叶轮 结 构如 下 图所 示 , 叶 轮主 要特点 为 : 双 吸式 叶轮 , 上下结构 对称 , 被 中间盖板 隔开, 毛坯 重量为6 0 0 k g , 叶轮 外径为 8 0 0 mm, 叶轮 高度 为4 0 0 mm, 叶片上 下个 5 枚叶片, 叶片厚度 为3 0 am, r 盖板 厚度 为4 0 mm, 其化 学成 分如 下c : 1 . 8 5 2 . 1 5 %、 S i : 0 . 3 " 0 . 8 %,
一
.
行 打磨 , 涂层厚度要 保证 0 . 5 -1 am, r 易粘砂部位应 涂刷至少两遍涂 料, 0 . 5 1 . 5 % 、 Mo : 2 . 0 3 . O % 。 技术要 求流道 内部 表面光滑平 整, 无 凸起 和 浇 冒1 3 : 系统与铸型一样也需要重 点涂刷 。 合箱前用喷灯烘烤1 O l 5 分钟 , 凹陷部 位 , 不能 有砂 眼、 裂纹 、 缩孔 等铸 造缺 陷 , 静 平 衡质量允 许差 为 合 箱时下芯完 毕后 检验芯子位 置是否正 确, 并且在合箱前要验 箱 , 检查 1 0 0 g , 硬度要求 H RC 4 5 5 0 。 有无偏 箱 、 壁厚是 否符合, 浇1 2 1 、 气眼周 围是否严 密, 气 眼是 否正确 、 铸 型有无压坏、 掉砂等。 二 铺 造 工
模, 叶 片采 用 铸 1 4 5 0 1 4 9 0  ̄ C 之 间。
铝, 造 型 方法 采 3 . 4 铸件后处 理 。 双 吸叶轮铸 件结 构扭 曲度比较大 , 需要压 箱五 天 用呋 喃树脂砂 造 以上, 待铸 件温度小于5 0 ℃以下方可打箱 , 高铬 铸铁A 4 9 材质脆 性大 , 应
’ 四. 工艺优 化 2 . 2 分型面和 拔模 斜度。 根 据叶轮 的形状 , 在上盖板中间分型, 如工 按 照上述 工艺试 制生产叶轮 两件, 得知 该工艺不成熟 , 主要为缺 陷 艺 图所 示 , 查《 铸 造工程 师手册》 取拔模斜度取 1 %。 为 叶片与盖板交 叉根部开裂 、 轴头部 分有气孔以及下盖板有缩孔产生 , 2 . 3 收 缩率 与加 工量 。 高 铬铸 铁 收缩 率 比较 大 , 一般 按 照2 %留收 针对 出现铸 造缺 陷原因分析得 知, 由于A 4 9 材 质热裂倾 向大 和下盖板不 缩, 结合我 厂多年 生产 叶轮 的实际经 验, 叶 轮流 道部分 基本不 收缩 , 所 能 充分补 缩所致 。 以流道 不留收 缩 , 其余按 照2 % 留收 缩。 根据 出现 的铸造缺 陷, 我们对工艺进行改进 : 加 工量: 高铬 铸铁 材质较硬 和脆 , 不利 于机械 加工 , 所以) j n - r 量尽 1 . 对 叶片开裂部 位增加 拉肋 2 道, 拉 肋厚度 为壁厚的5 am, r 拉 肋的 量 留小一点, 参考铸 件尺寸和 机械加 工余 量 ( G B / T 6 4 l 4 — 1 9 9 9 ) 以及 结 断面 高度是 厚度的5 0 am, r 合我厂多年实际生 产经验 , 取 上箱加 工量 为5 am, r 下箱加工量为4 am。 r 2 . 为 了有 效 补 缩 下 盖板 , 增 加 侧 冒 口三个 , 侧 冒 口直 径 大 小为 2 . 4 浇注 系统 和冒口设计。 高铬 铸铁A 4 9 材料流动性 很差 , 宜 采用开 1 6 0 am, r 高度4 0 0 am。 r 放 浇注 系统 , 在 叶轮上下两层, 沿盖板芯头外 圆处, 内浇道六 道, 各浇 道 3 . 浇注前 用热风 机在 2 0 0  ̄ C 下对 铸 型进行烘 烤2 小时, 以此来 防止 截面积按 照 F 直: F 横: F 内: = 1 . 0 : 0 . 9 : 1 . 2 。 其中阻流断 面积为灰铸 铁 砂 型吸潮 , 减少砂 型中树 脂发气 量。 的1 . 5 倍。 4 . 采取 低温快浇的方法 降低浇注 温度 , 提 高浇 注速度 , 将浇注温 度 冒口: 高铬铸 铁A 4 9 收缩 率 比普 通的 白口铁收缩 性稍 大 , 所 以在顶 降低 为1 4 3 0 1 4 5 0  ̄ 3 , 浇注 速度为3 O 5 0 部 放置 三个 冒口, 冒口直径大 / J x  ̄1 4 0 , 高2 2 0 . 由于轴头 盖板处较 薄 , 需 经过 生 产验 证 , 改 进 工艺后 又生产 叶轮 两件 , 没有 出现 缩 松和 裂
耐磨高铬铸铁材料熔炼工艺
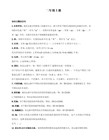
洛阳迪特曼提供
1、高铬铸铁不仅是重要的耐磨材料,还是耐火材料,高铬铸铁的熔点超过1500度,因此熔炼的世界效益最高温度超过1500度中频炉熔炼。
2、高铬铸铁的炉衬,采用酸性或者碱性,烧结安装正常工艺进行。
3、装料,先进难溶解的钼铁等放到炉底,易溶解放在炉子的顶部。
4、由于铬的熔炼损耗比较大,因此最后加入,一般等钢铁熔化以后再加入。
5、脱氧待金属炉料全部熔化并提温至1480 ℃后,再加入锰铁、硅铁及铝进行脱氧。
6、浇注在中频感应炉中熔化,温度不必太高,温度达到1480℃时即可出炉,铁液在包内应停留一段时间进行镇静,视工件大小不同可在1380~1410℃之间进行浇注。
高铬铸铁_铸钢锤头的镶铸工艺_王超

体铸钢破碎机鄂板 、球磨机衬板和矿粉输送管道以 可见在非金属矿行业推广应用低合金贝氏体铸钢具
及高碳贝氏体铸钢磨球的工业试验 , 使用结果见表 有很好的效果 , 可提高设备运转率 , 降低非金属矿的
3 。低合金贝氏体铸钢鄂板和衬板使用安全 , 使用中 破碎和研磨以及矿粉输送成本 , 提高非金属矿行业
从未出断裂 , 使用寿命比高锰钢提高 2 倍以上 , 设备 经济效益 。
2 .5 锤头的热处理
采用淬火 +回火的热处理工艺(如 图 2), 锤头 端部硬度 HRC58 -62 。 淬火时一般采用强制吹风 冷却 , 如环境温度较高或通风条件不理想可采用喷 雾冷却 。
图 2 锤头的热处理工艺
图 1 镶铸工艺示意图
2 .3 铸造工艺 分型面设在图 1 所示部位 , 而不应放在锤柄中
3 结论
通过选择合适的材质成分 、铸造以及热处理工 艺 , 设计合理的锤柄结构 , 可获得质量稳定 , 耐磨性 优良(HRC58 -62)的复合锤头铸件 , 使用寿命明显 优于同等工况下的高锰钢锤头 。
(下转第 27 页)
200
2 预置锤柄镶铸锤头的生产工艺
2 .1 材质选择 锤头材质的选择应确保锤柄具有足够的强度和
收稿日期 :2003 -11 -06 作者简介 :王超(1974 -), 男 , 安徽淮北人 , 工程师 , 从事金属抗磨材料研究 。
2004 年第 2 期 王超 , 等 :高铬铸铁 — 铸钢锤头的 镶铸工艺
表 1 高铬铸铁的化学成分(质量分数 , %)
名称 C Si M n S P C r M o Cu
高铬 2 .9 ~ 0 .4 ~ 0 .5 ~ < < 14 ~ 1 .5 ~ 0 .8 ~ 铸铁 3 .3 1 .0 0 .9 0 .05 0 .05 18 2.0 1 .2
- 1、下载文档前请自行甄别文档内容的完整性,平台不提供额外的编辑、内容补充、找答案等附加服务。
- 2、"仅部分预览"的文档,不可在线预览部分如存在完整性等问题,可反馈申请退款(可完整预览的文档不适用该条件!)。
- 3、如文档侵犯您的权益,请联系客服反馈,我们会尽快为您处理(人工客服工作时间:9:00-18:30)。
锤头高铬铸铁铸造工艺
高铬铸铁化学成分设计:(一般采用亚共晶高铬铸铁)
1、工艺上常常通过调整碳含量来达到改变碳化物数量。
2、不含其他合金元素的高铬铸铁,空淬能淬透的最大直径为20mm,要提高淬透性,必须加入合金元素。
3、锰剧烈降低Ms,会使高铬铸铁在淬火后有较多的残留奥氏体,因此,一般控制在1.0%以下。
4、铜降低Ms,会造成许多的残留奥氏体,因此,一般控制在1.5%以下。
5、由于V价格高,通常只适用于不易热处理的铸件。
6、硅提高Ms,会减少残留奥氏体,同时降低淬透性,因此,一般应控制。
7、高铬铸铁感应炉熔炼温度1480℃,已经足够,不必太高。
8、高铬铸铁浇注温度不希望太高,以免收缩过大和粘砂。
浇注温度厚大件1350-1400℃,(一般件1380-1420℃)。
高的浇注温度加重冒口下的缩孔,而且会造成浓密的显微缩松,同时使晶粒组织粗大。
9、高铬铸铁模型收缩率2%。
10、高铬铸铁冒口尺寸按碳钢设计,浇注系统按灰铸铁设计。
采用气割法切割浇冒口,容易产生热裂纹,故设计时采用易割冒口或者侧冒口,采用敲击法去除。
11、高铬铸铁寿命短的原因,不是金相不合格,而是,铸件
内存在缩孔、气孔、夹杂等铸造缺陷,因此必须足够重视铸造工艺。
12、高铬铸铁容易开裂。
在铸造工艺设计上注意不让铸件收缩受阻,以免造成开裂。
13、高铬铸铁铸件在铸型中应充分冷却,然后开箱。
开箱过早,开箱温度过高,是铸件开裂的主要原因。
14、高铬铸铁采用金属型铸造时,浇注温度应保持在150℃以上,以免铸件冷却太快开裂。
15、高铬铸铁采用高温空淬,中低温回火的热处理,获得高硬度的马氏体基体。
16、高铬铸铁在热处理前的铸态基体组织取决于铸态冷却速度的高低。
冷却速度高时通常为奥氏体基体:随冷却速度降低逐渐开始析出部分马氏体、珠光体和奥氏体的混合物。
:冷却速度进一步降低,可能获得珠光体基体的组织。
17、高铬铸铁一般根据铬含量和零件壁厚选择最佳淬火温度。
淬火温度越高,淬透性越高,但淬火后形成残留奥氏体数量有可能越多。
Cr15高铬铸铁的淬火温度940-970℃,Cr20高铬铸铁的淬火温度960-1010℃。
保温时间根据壁厚选择。
一般2-4h,壁厚零件4-6h。
18空淬后的高铬铸铁存在较大的内应力,应尽快进行回火热处理。
19、对一些形状复杂、壁厚形成悬殊的高铬铸铁铸件应严格
控制升温温度(≤50℃/h),以免铸件开裂。
有时采用阶梯式升温(在200℃、400℃、600℃停留2-3h)更为安全,在700℃以上升温可以适当加速。
但不超过150℃/h。
20、保温时间应视铸件壁厚、装炉量、状态和升温速度等因素综合考虑,以免由于部分铸件或铸件的心部因保温时间不足而出现淬不透。
21、高铬铸铁出炉应进行脱氧处理。
通常在炉中加0.5%锰铁进行预脱氧,在炉中加0.25%硅铁进行初脱氧,在包中加0.05%铝进行终脱氧。
22、高铬铸铁在熔炼过程中温度控制在1450℃,最后快速升温控制在1480℃脱氧出炉。