第七章 烧结过程成矿机理
烧结矿的固结机理
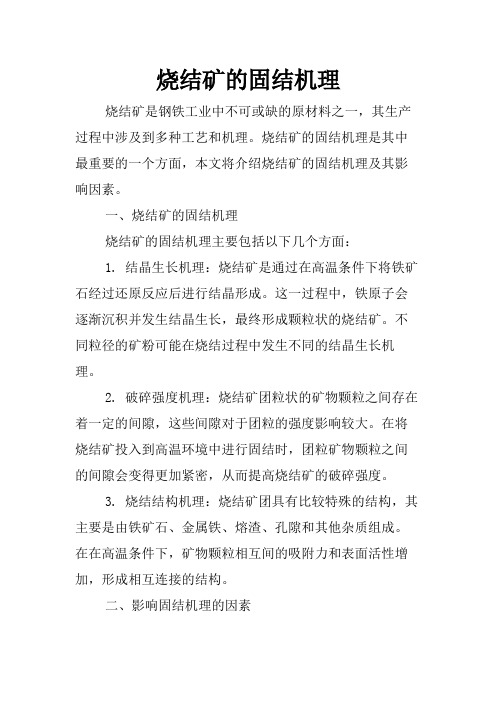
烧结矿的固结机理烧结矿是钢铁工业中不可或缺的原材料之一,其生产过程中涉及到多种工艺和机理。
烧结矿的固结机理是其中最重要的一个方面,本文将介绍烧结矿的固结机理及其影响因素。
一、烧结矿的固结机理烧结矿的固结机理主要包括以下几个方面:1. 结晶生长机理:烧结矿是通过在高温条件下将铁矿石经过还原反应后进行结晶形成。
这一过程中,铁原子会逐渐沉积并发生结晶生长,最终形成颗粒状的烧结矿。
不同粒径的矿粉可能在烧结过程中发生不同的结晶生长机理。
2. 破碎强度机理:烧结矿团粒状的矿物颗粒之间存在着一定的间隙,这些间隙对于团粒的强度影响较大。
在将烧结矿投入到高温环境中进行固结时,团粒矿物颗粒之间的间隙会变得更加紧密,从而提高烧结矿的破碎强度。
3. 烧结结构机理:烧结矿团具有比较特殊的结构,其主要是由铁矿石、金属铁、熔渣、孔隙和其他杂质组成。
在在高温条件下,矿物颗粒相互间的吸附力和表面活性增加,形成相互连接的结构。
二、影响固结机理的因素烧结矿固结机理受到多种因素的影响,主要包括以下几个方面:1. 矿石成分:矿石的成分会显著影响烧结矿的固结机理。
在不同的还原反应条件下,矿石的不同成分在烧结过程中发挥着不同的作用。
2. 烧结温度:烧结温度是烧结矿固结机理中最为重要的因素之一。
不同的矿粉在不同的烧结温度下会发生不同的固结反应,形成不同的团粒结构。
3. 气氛控制:在固结过程中,气氛的控制也是十分重要的。
氧气、水蒸气、二氧化碳等气体的含量都有可能对烧结团粒的形成产生影响。
4. 压力控制:固结过程中的压力控制也十分关键。
烧结矿的压力会影响其团粒结构的形成和稳定性。
5. 冷却方式:在固结后的冷却过程中,冷却速率和方式都有可能对烧结团粒的微观结构和力学性能产生影响。
三、结论烧结矿固结机理是复杂的,受到多种因素的影响。
在烧结矿的生产过程中,需要综合考虑多方面因素的影响,并采取相应的措施来进行优化和调控。
通过研究烧结矿的固结机理,可以更好地掌握其生产过程和性能特征,对于提高钢铁生产的效率和质量都具有重要意义。
烧结制备过程的原理

烧结制备过程的原理
烧结是一种通过粉末材料在高温下进行加热压制以形成坚固体的工艺。
烧结过程的原理可以归纳为以下几个方面:
1. 粒子扩散:在烧结过程中,由于高温下原子和分子的热振动,粉末颗粒之间的原子或分子会发生扩散,逐渐形成颗粒间的结合。
这种扩散是烧结中最关键的阶段。
2. 颗粒聚结:当粉末颗粒接触时,由于表面能的存在,两个接触颗粒会发生一定程度的结合。
在烧结过程中,随着温度的升高,这些颗粒间的结合会不断强化,最终形成坚固的结构。
3. 烧结颈部形成:在烧结过程中,颗粒间的结合会产生烧结颗粒之间的颈部。
随着烧结过程的进行,烧结颈部逐渐增长,并最终连接在一起,形成一个连续的块体。
4. 表面张力的作用:在烧结过程中,颗粒间的结合也受到表面张力的影响。
表面张力会使形成的结合处有一定的凹陷,这种凹陷可以促进烧结颈部的形成,从而增强颗粒间的结合。
总的来说,烧结制备过程的原理是靠粒子的扩散、颗粒的聚结以及烧结颈部的形成和表面张力的作用,使得粉末材料在高温下能够形成坚固的物体。
烧结工艺具
有高效、经济、环保等优势,在陶瓷、金属、塑料等领域被广泛应用。
烧结过程的理论基础
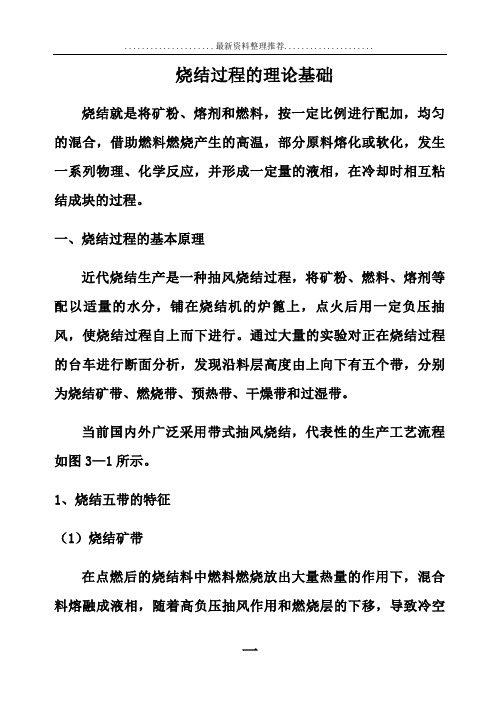
烧结过程的理论基础烧结就是将矿粉、熔剂和燃料,按一定比例进行配加,均匀的混合,借助燃料燃烧产生的高温,部分原料熔化或软化,发生一系列物理、化学反应,并形成一定量的液相,在冷却时相互粘结成块的过程。
一、烧结过程的基本原理近代烧结生产是一种抽风烧结过程,将矿粉、燃料、熔剂等配以适量的水分,铺在烧结机的炉篦上,点火后用一定负压抽风,使烧结过程自上而下进行。
通过大量的实验对正在烧结过程的台车进行断面分析,发现沿料层高度由上向下有五个带,分别为烧结矿带、燃烧带、预热带、干燥带和过湿带。
当前国内外广泛采用带式抽风烧结,代表性的生产工艺流程如图3—1所示。
1、烧结五带的特征(1)烧结矿带在点燃后的烧结料中燃料燃烧放出大量热量的作用下,混合料熔融成液相,随着高负压抽风作用和燃烧层的下移,导致冷空气从烧结矿带通过,物料温度逐渐降低,熔融的液相被冷却凝固成网孔状的固体,这就是烧结矿带。
此带主要反应是液相凝结、矿物析晶、预热空气,此带表层强度较差,一般是返矿的主要来源。
(2)燃烧带该带温度可达1350~1600度,此处混合料软化、熔融及液相生成,发生异常复杂的物理化学变化。
该层厚度为15~50mm 。
此高炉灰轧钢皮碎焦无烟煤 石灰石白云石 精矿富矿粉水空气烟道灰返矿排出废气(热烧结矿) 冷烧结矿图3—1 烧结生产一般工艺流程图带对烧结产量及质量影响很大。
该带过宽会影响料层透气性,导致产量低。
该带过窄,烧结温度低,液相量不足,烧结矿粘结不好,导致烧结矿强度低。
燃烧带宽窄主要受物料特性、燃料粒度及抽风量的影响。
(3)预热带该带主要使下部料层加热到燃料的着火温度。
一般温度为400~800度。
该带主要反应是烧结料中的结晶水及部分碳酸盐、硫酸盐分解,磁铁矿进行还原以及组分间的固相反应等。
(4)干燥带烧结料的热废气从预热带进入下层,迅速将烧结料加热到100℃以上,因此该带主要是水分的激烈蒸发。
(5)过湿带从烧结料点火开始,物料中的水分就开始转移到气流中去。
烧结过程及机理

气氛
气氛对烧结过程的 影响
气氛是烧结过程中的一个重要 因素。气氛中的气体成分可以 与材料发生化学反应,从而影 响烧结过程和材料的性能。
气氛对材料相变的 影响
在烧结过程中,气氛中的气体 成分可以与材料发生化学反应 ,导致材料发生相变。这种相 变可以改变材料的物理和化学 性质,因此控制气氛可以实现 对材料相变和性能的调控。
压力
压力对烧结过程的影响
压力是烧结过程中的另一个重要参数。在适宜的压力范围内,随着压力的增加,烧结速率 加快,材料的致密度和强度增加。
压力对材料结构的影响
在烧结过程中,压力可以改变材料的结构。例如,在高温高压条件下,某些材料会发生晶 体结构的改变或相变,从而改变材料的性能。
压力对扩散的影响
压力可以影响材料内部原子或分子的扩散速度。在烧结过程中,扩散速度决定了材料的致 密化程度和显微结构,因此控制压力可以实现对材料结构和性能的调控。
烧结的重要性
烧结是材料制备过程中的重要环节,通过 烧结可以获得高性能的材料,广泛应用于 航空航天、汽车、电子、能源等领域。
通过优化烧结工艺参数和添加合金元 素等方法,可以进一步改善材料的性 能,提高其综合性能和应用价值。
烧结过程可以改变材料的物理和化学性质 ,如密度、硬度、电导率、热导率等,从 而满足不同领域对材料性能的需求。
陶瓷材料的烧结机理主要包括扩散传质和流动传质,扩散 传质是材料内部质点通过热运动进行迁移的过程,流动传 质则是气体在压力作用下通过材料孔隙的流动过程。
金属材料
金属材料的烧结过程是在一定的温度和压力下,通过原子或分子的扩散和流动,使松散的金属粉末颗 粒紧密结合在一起,形成致密的金属块体。金属材料具有高强度、高导电性、高导热性等优点,广泛 应用于机械、电子、航空航天等领域。
铁矿粉烧结过程基础理论
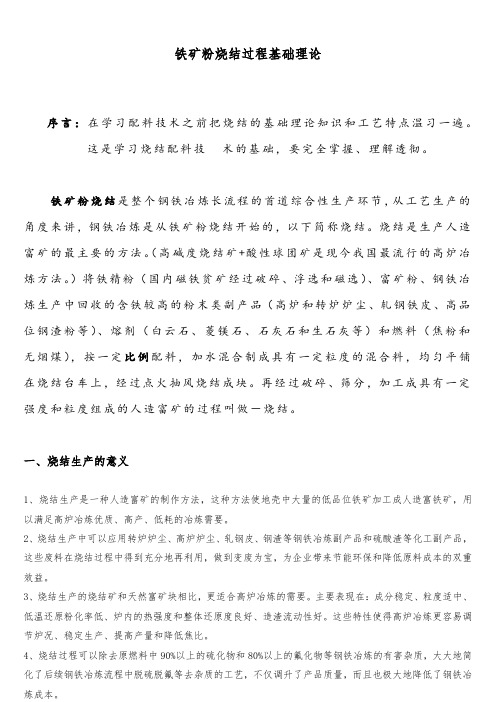
铁矿粉烧结过程基础理论序言:在学习配料技术之前把烧结的基础理论知识和工艺特点温习一遍。
这是学习烧结配料技术的基础,要完全掌握、理解透彻。
铁矿粉烧结是整个钢铁冶炼长流程的首道综合性生产环节,从工艺生产的角度来讲,钢铁冶炼是从铁矿粉烧结开始的,以下简称烧结。
烧结是生产人造富矿的最主要的方法。
(高碱度烧结矿+酸性球团矿是现今我国最流行的高炉冶炼方法。
)将铁精粉(国内磁铁贫矿经过破碎、浮选和磁选)、富矿粉、钢铁冶炼生产中回收的含铁较高的粉末类副产品(高炉和转炉炉尘、轧钢铁皮、高品位钢渣粉等)、熔剂(白云石、菱镁石、石灰石和生石灰等)和燃料(焦粉和无烟煤),按一定比例配料,加水混合制成具有一定粒度的混合料,均匀平铺在烧结台车上,经过点火抽风烧结成块。
再经过破碎、筛分,加工成具有一定强度和粒度组成的人造富矿的过程叫做-烧结。
一、烧结生产的意义1、烧结生产是一种人造富矿的制作方法,这种方法使地壳中大量的低品位铁矿加工成人造富铁矿,用以满足高炉冶炼优质、高产、低耗的冶炼需要。
2、烧结生产中可以应用转炉炉尘、高炉炉尘、轧钢皮、钢渣等钢铁冶炼副产品和硫酸渣等化工副产品,这些废料在烧结过程中得到充分地再利用,做到变废为宝,为企业带来节能环保和降低原料成本的双重效益。
3、烧结生产的烧结矿和天然富矿块相比,更适合高炉冶炼的需要。
主要表现在:成分稳定、粒度适中、低温还原粉化率低、炉内的热强度和整体还原度良好、造渣流动性好。
这些特性使得高炉冶炼更容易调节炉况、稳定生产、提高产量和降低焦比。
4、烧结过程可以除去原燃料中90%以上的硫化物和80%以上的氟化物等钢铁冶炼的有害杂质,大大地简化了后续钢铁冶炼流程中脱硫脱氟等去杂质的工艺,不仅调升了产品质量,而且也极大地降低了钢铁冶炼成本。
二、烧结生产过程1、烧结工艺流程大多数人开始学习烧结工艺的时候,首先学习的就是工艺流程图,我们去某个地方参观或者学习时,也必先熟悉那里的工艺流程图。
粉末冶金原理第七章

7.2
烧结过程的热力学基础
7.2.1 烧结的基本过程 7.2.2 烧结的热力学问题 7.2.3 烧结驱动力的计算
7.2
烧结过程的热力学基础
图7-1
烧结球之间形成烧结颈的扫描 电子显微照片
7.2.1 烧结的基本过程
(1)黏结阶段 烧结初期,颗粒间的原始接触点或面转变成 晶体结合,即通过成核、结晶长大等原子过程形成烧结颈。 (2)烧结颈长大阶段 原子向颗粒结合面大量迁移,使烧结 颈扩大,颗粒间的距离缩小,形成连续的孔隙网络;同时由 于晶粒长大,晶界越过孔隙移动,而被晶界扫过的地方,孔 隙大量消失。 (3)闭孔隙球化和缩小阶段 当烧结体密度达到90%以后, 多数孔隙被完全分隔,闭孔数量增加,孔隙形状趋近球形并 不断缩小。
7.2.1 烧结的基本过程
图7-2 球形颗粒的烧结模型 a)烧结前颗粒的原始接触 b)烧结早期的烧结颈长大 c)、d)烧结后期的孔隙球 化
7.2.2 烧结的热力学问题
1)由于颗粒结合面(烧结颈)的增大和颗粒表面的平直化,粉 末体的总比表面积和总表面自由能减小。 2)烧结体内孔隙总体积和总表面积减小。 3)粉末颗粒内晶格畸变逐渐消除。
7.2.3 烧结驱动力的计算
图7-3
烧结颈模型
7.2.3 烧结驱动力的计算
图7-4
两球模型
7.2.3 烧结驱动力的计算
图7-6 颈部直径为X的两球形 颗粒的烧结剖视图
7.2.3 烧结驱动力的计算
图7-7
不同温度下烧结时间对烧结颈大小、表面积减小率、 收缩率和致密化的影响
7.3
烧结理论与物质迁移
图7-38 烧结过程接触面和孔隙形状、尺寸的变化模型
7.3.5 烧结末期
图7-26 烧结时间与孔隙率、孔径、晶粒之间的关系。
烧结基本原理

、烧结(1)、烧结基本原理烧结是粉末冶金生产过程中最基本的工序之一。
烧结对最终产品的性能起着决定性作用,因为由烧结造成的废品是无法通过以后的工序挽救的;相反,烧结前的工序中的某些缺陷,在一定的范围内可以通过烧结工艺的调整,例如适当改变温度,调节升降温时间与速度等而加以纠正。
烧结是粉末或粉末压坯,加热到低于其中基本成分的熔点温度,然后以一定的方法和速度冷却到室温的过程。
烧结的结果是粉末颗粒之间发生粘结,烧结体的强度增加。
在烧结过程中发生一系列物理和化学的变化,把粉末颗粒的聚集体变成为晶粒的聚结体,从而获得具有所需物理,机械性能的制品或材料。
烧结时,除了粉末颗粒联结外,还可能发生致密化,合金化,热处理,联接等作用。
人们一般还把金属粉末烧结过程分类为:1、单相粉末(纯金属、古熔体或金属化合物)烧结;2、多相粉末(金属—金属或金属—非金属)固相烧结;3、多相粉末液相烧结;4、熔浸。
通常在目前PORITE微小轴承所接触的和需要了解的为前三类烧结。
通常在烧结过程中粉末颗粒常发生有以下几个阶段的变化:1、颗粒间开始联结;2、颗粒间粘结颈长大;3、孔隙通道的封闭;4、孔隙球化;5、孔隙收缩;6、孔隙粗化。
上述烧结过程中的种种变化都与物质的运动和迁移密切相关。
理论上机理为:1、蒸发凝聚;2、体积扩散;3、表面扩散;4、晶间扩散;5、粘性流动;6、塑性流动。
(2)、烧结工艺2-1、烧结的过程粉末冶金的烧结过程大致可以分成四个温度阶段:低温预烧阶段,在此阶段主要发生金属的回复及吸附气体和水分的挥 发,压坯内成形剂的分解和排除等。
在PORITE 微小铜、铁系轴承中,用R 、B 、 O(Rapid Burning Off)来代替低温预烧阶段,且铜、铁系产品经过R 、B 、O 后会氧化,但在本体中可以被还原,同时还可以促进烧结。
2、中温升温烧结阶段,在此阶段开始出现再结晶,首先在颗粒内,变形 的晶粒得以恢复,改组为新晶粒,同时颗粒表面氧化物被完全还原,颗粒界 面形成烧结颈。
烧结过程的理论基础

烧结过程的理论基础烧结就是将矿粉、熔剂和燃料,按一定比例进行配加,均匀的混合,借助燃料燃烧产生的高温,部分原料熔化或软化,发生一系列物理、化学反应,并形成一定量的液相,在冷却时相互粘结成块的过程。
一、烧结过程的基本原理近代烧结生产是一种抽风烧结过程,将矿粉、燃料、熔剂等配以适量的水分,铺在烧结机的炉篦上,点火后用一定负压抽风,使烧结过程自上而下进行。
通过大量的实验对正在烧结过程的台车进行断面分析,发现沿料层高度由上向下有五个带,分别为烧结矿带、燃烧带、预热带、干燥带和过湿带。
当前国内外广泛采用带式抽风烧结,代表性的生产工艺流程如图3—1所示。
1、烧结五带的特征(1)烧结矿带在点燃后的烧结料中燃料燃烧放出大量热量的作用下,混合料熔融成液相,随着高负压抽风作用和燃烧层的下移,导致冷空气从烧结矿带通过,物料温度逐渐降低,熔融的液相被冷却凝固成网孔状的固体,这就是烧结矿带。
此带主要反应是液相凝结、矿物析晶、预热空气,此带表层强度较差,一般是返矿的主要来源。
(2)燃烧带该带温度可达1350~1600度,此处混合料软化、熔融及液相生成,发生异常复杂的物理化学变化。
该层厚度为15~50mm 。
此高炉灰轧钢皮 (10~0mm ) 碎焦无烟煤 (25~0mm ) 石灰石白云石 (80~0mm ) 精矿富矿粉 (10~0mm )空气排出废气(热烧结矿)冷烧结矿图3—1 烧结生产一般工艺流程图带对烧结产量及质量影响很大。
该带过宽会影响料层透气性,导致产量低。
该带过窄,烧结温度低,液相量不足,烧结矿粘结不好,导致烧结矿强度低。
燃烧带宽窄主要受物料特性、燃料粒度及抽风量的影响。
(3)预热带该带主要使下部料层加热到燃料的着火温度。
一般温度为400~800度。
该带主要反应是烧结料中的结晶水及部分碳酸盐、硫酸盐分解,磁铁矿进行还原以及组分间的固相反应等。
(4)干燥带烧结料的热废气从预热带进入下层,迅速将烧结料加热到100℃以上,因此该带主要是水分的激烈蒸发。
- 1、下载文档前请自行甄别文档内容的完整性,平台不提供额外的编辑、内容补充、找答案等附加服务。
- 2、"仅部分预览"的文档,不可在线预览部分如存在完整性等问题,可反馈申请退款(可完整预览的文档不适用该条件!)。
- 3、如文档侵犯您的权益,请联系客服反馈,我们会尽快为您处理(人工客服工作时间:9:00-18:30)。
烧结理论与工艺
(三)液相形成在烧结过程中的主要作用
(4)液相能润湿未熔的矿粒表面,产生一定的表面张力 液相能润湿未熔的矿粒表面, 将矿粒拉紧,使其冷凝后具有强度; 将矿粒拉紧,使其冷凝后具有强度; 从液相中形成并析出烧结料中所没有的新生矿物, (5)从液相中形成并析出烧结料中所没有的新生矿物, 这种新生矿物有利于改善烧结矿的强度和还原性。 这种新生矿物有利于改善烧结矿的强度和还原性。
∆G R K = A exp− RT
Q D = D0 exp− RT
气氛对固相反应也有重要影响。 气氛对固相反应也有重要影响。它可以通过改变固体吸附特性而影响表 面反应活性。气氛可直接影响晶体表面缺陷的浓度、 面反应活性。气氛可直接影响晶体表面缺陷的浓度、扩散机构和扩散速 度。
烧结理论与工艺
①物料化学组成与结构的影响
反应物化学组成与结构是影响固相反应的内因, 反应物化学组成与结构是影响固相反应的内因,是决定反 应方向和反应速率的重要因素。 应方向和反应速率的重要因素。 在一定温度、压力条件下, 从热力学角度 在一定温度、压力条件下,反应向自由能 减少( 的方向进行。 减少(<0)的方向进行。 反应物的结构状态、 从结构的观点 反应物的结构状态、质点间的化学键性质 以及各种缺陷浓度都将对反应速率产生影响。 以及各种缺陷浓度都将对反应速率产生影响。
SiO2-FeO Fe3O4-2FeO·SiO2 MnO-SiO2 MnO-Mn2O3-SiO2
2FeO·SiO2-2CaO·SiO2 钙铁橄榄石 钙铁橄榄石CaOx·FeO2-x·SiO2,X=0.19 2CaO·SiO2-FeO CaO·Fe2O3 Fe-Fe2O3-CaO Fe3O4-Fe2O3CaO·Fe2O3 Fe2O3-CaO·SiO2 烧结理论与工艺 2CaO·SiO2-FeO共晶混合物 共晶混合物 CaO·Fe2O3→液相 液相+2CaO·Fe2O3(异分熔化点) 异分熔化点) 液相 CaO·Fe2O3 -CaO·2Fe2O3(共晶混合物) 共晶混合物) (18%CaO+82%FeO)-2CaO·Fe2O3固熔体共晶混 % ) 合物 Fe3O4-{CaO·Fe2O3 2CaO·Fe2O3 2CaO·SiO2-CaO·Fe2O3-CaO·2Fe2O3共晶混合物
烧结理论与工艺
系 统
液 相 特 性 2FeO·SiO2 2FeO·SiO2-SiO2共晶混合物 2FeO·SiO2-FeO共晶混合物 共晶混合物 2FeO·SiO2-Fe3O4共晶混合物 2MnO·SiO2异分熔化点 MnO-Mn3O4、2MnO·SiO2共晶混合物
熔化温 度(℃) 1205 1178 1177 1142 1323 1303 1150 1280 1216 1200 1140 1180 1192
烧结理论与工艺
②反应物颗粒尺寸及分布的影响
在其它条件不变的情况下反应速率受到颗粒尺寸大小的强 烈影响。 烈影响。 反应速率常数值反比于颗粒半径平方。 反应速率常数值反比于颗粒半径平方。 另一方面, 另一方面,颗粒尺寸大小对反应速率的影响是通过改变反 应界面和扩散界面以及改变颗粒表面结构等效应来完成的, 应界面和扩散界面以及改变颗粒表面结构等效应来完成的, 颗粒尺寸越小,反应体系比表面积越大, 颗粒尺寸越小,反应体系比表面积越大,反应界面和扩散 界面也相应增加,因此反应速率增大。 界面也相应增加,因此反应速率增大。
烧结理论与工艺
7.2 烧结过程液相的形成与结晶
(一)液相的形成过程 在烧结过程中,由于烧结料的组成成分多, 在烧结过程中,由于烧结料的组成成分多,颗粒又互相紧 密接触,当加热到一定温度时, 密接触,当加热到一定温度时,各成分之间开始有了固相 反应,在生成新的化合物之间, 反应,在生成新的化合物之间,原烧结料各成分之间以及 新生化合物和原成分之间存在低共熔点物质, 新生化合物和原成分之间存在低共熔点物质,使得在较低 的温度下就生成液相,开始熔融。例如 的温度下就生成液相,开始熔融。例如Fe3O4的熔点为 1597℃,SiO2的熔点为 ℃ 的熔点为1713℃,而两固相接触界面的固 ℃ 相反应产物为2FeO·SiO2,其熔化温度 其熔化温度1205℃。当烧结温 相反应产物为 ℃ 度达到该化合物的熔点时,即开始形成液相。 度达到该化合物的熔点时,即开始形成液相。
烧结过程主要固相反应类型
赤铁矿非熔剂性烧结料中固相反应
烧结理论与工艺
烧结过程主要固相反应类型
赤铁矿熔剂性烧结料中固相反应
烧结理论与工艺
烧结过程主要固相反应类型
磁铁矿非熔剂性烧结料固相反应
烧结理论与工艺
烧结过程主要固相反应类型
磁铁矿熔剂性烧结料中固相反应
烧结理论与工艺
固相反应在烧结过程中的作用
烧结理论与工艺
(四)影响液相形成量的主要因素
(1)烧结温度。 )烧结温度。
烧结料液相量随着温度的提高而增加
(2)配料碱度(CaO/ SiO2)。 )配料碱度(
碱度是影响液相量和液相类型的主要因素, 碱度是影响液相量和液相类型的主要因素,烧结料的液相量随
烧结理论与工艺
④添加剂的影响
添加剂(矿化剂):在固相反应体系中加入少量非反应物物质或由 添加剂(矿化剂):在固相反应体系中加入少量非反应物物质或由 ): 于某些可能存在于原料中的杂质,常会对反应产生特殊的作用, 于某些可能存在于原料中的杂质,常会对反应产生特殊的作用,这 些物质在反应过程中不与反应物或反应产物起化学反应, 些物质在反应过程中不与反应物或反应产物起化学反应,但它们以 不同的方式和程度影响着反应的某些环节。 不同的方式和程度影响着反应的某些环节。 作用: 改变反应机构降低反应活化能 改变反应机构降低反应活化能; 影响晶核的生成速率 影响晶核的生成速率; 影响 作用:1)改变反应机构降低反应活化能;2)影响晶核的生成速率;3)影响 结晶速率及晶格结构; 降低体系共熔点 改善液相性质等。 降低体系共熔点, 结晶速率及晶格结构;4)降低体系共熔点,改善液相性质等。 例如烧结混合料中添加亚铁酸盐( 例如烧结混合料中添加亚铁酸盐(表7-3) )
①能促进原始烧结料所没有的易熔化的新物质的形成
②加速液相生成速度
固相反应产物不能决定烧结矿最终矿物成分
烧结理论与工艺
影响烧结固相反应的因素
固相反应过程涉及相界面的化学反应和相内部或外部的物 质扩散等若干环节,因此,除反应物的化学组成、 质扩散等若干环节,因此,除反应物的化学组成、特性和 结构状态以及温度、压力等因素外,其他可能的影响如: 结构状态以及温度、压力等因素外,其他可能的影响如: 晶格活化,相变等都会促进物质内外传输, 晶格活化,相变等都会促进物质内外传输,均会对反应起 影响作用。 影响作用。
(二)液相的形成过程
(1)初生液相。 初生液相。 (2)低熔点化合物加速形成。 低熔点化合物加速形成。 (3)液相扩展。 液相扩展。 (4)液相反应。 液相反应。 (5)液相同化。 液相同化。
烧结理论与工艺
(三)液相形成在烧结过程中的主要作用
(1)液相是烧结矿的粘结相,将未熔的固体颗粒粘结成块, 液相是烧结矿的粘结相,将未熔的固体颗粒粘结成块, 保证烧结矿具有一定的强度; 保证烧结矿具有一定的强度; 液相具有一定的流动性,可进行粘性或塑性流动传热, (2)液相具有一定的流动性,可进行粘性或塑性流动传热, 使高温熔融带的温度和成分均匀,液相反应后的烧结矿化学成 使高温熔融带的温度和成分均匀, 分均匀化。 分均匀化。 液相保证固体燃料充分燃烧, (3)液相保证固体燃料充分燃烧,大部分固体燃料是在液相 形成后燃烧完毕的,液相的数量和粘度应能保证燃料不断地显 形成后燃烧完毕的, 露到氧位较高的气流孔道附近,在较短的时期内燃烧完毕; 露到氧位较高的气流孔道附近,在较短的时期内燃烧完毕;
液相生成量是烧结料固结的基础
冷凝固结
烧结理论与工艺
7.1 烧结过程固相反应
(一)固相反应基础知识 (1)基本概念 固相反应是指物料在没的熔化之前, 固相反应是指物料在没的熔化之前,两 是指物料在没的熔化之前 种固体在它们的接触界面上发生的化学 反应,反应产物也是固体。 反应,反应产物也是固体。
B
烧结理论与工艺
③ 反应温度与气氛的影响
一般可以认为温度升高均有利于反应进行。这是因为温度升高, 一般可以认为温度升高均有利于反应进行。这是因为温度升高,固体 结构中质点热振动动能增大、 结构中质点热振动动能增大、反应能力和扩散能力均得到增强的原因 所致。 所致。
对于化学反应, 对于化学反应,其速率常数 对于扩散, 对于扩散,其扩散系数
冷却速度快 玻璃体析出
液相生成 熔化物的冷凝成为未熔物之间的粘结 剂,把烧结料粘结成多孔状的烧结体 FeO-SiO2 系液相 1175~1205℃ ~ ℃ 非自熔性烧结矿 的主要粘结相 CaO-SiO2-FeO 系液相 1073~1217℃ ~ ℃ 自熔性烧结矿 的主要粘结相 CaO-SiO2 系液相 1450~1540℃ ~ ℃ 高碱度烧结矿 的粘结相 CaO-Fe2O3 系液相 完成烧结过程 1205~1449℃ ~ ℃ 高碱度烧结矿 的主要粘结相
第7章 烧结过程成矿机理 章
7.1 烧结过程固相反应 7.2 烧结过程液相的形成与结晶 7.3 烧结成矿过程相图分析
烧结理论与工艺
固相反应 液相放出能量 生成低熔点物质 金属:(0.3-0.4)·T熔 盐类:0.57·T熔 硅酸盐:(0.8-0.9) ·T熔 为液相生成创造条件
冷却速度慢 结晶体析出
固相反应产物 Fe2O3 在SiO2中的固熔体 2FeO·SiO2 CaO·Fe2O3 MgO·Fe2O3 CaO·Fe2O3 2CaO·SiO2 2MgO·SiO2 镁富氏体 MgO·Al2O3
反应产物开始出现的温度 (℃) 575 990 500、600、610、650 、 、 、 600 590 500、610、600 、 、 680 700 920、1000 、