垫圈冲压工艺及模具设计
垫圈-冲压模具课程设计说明书
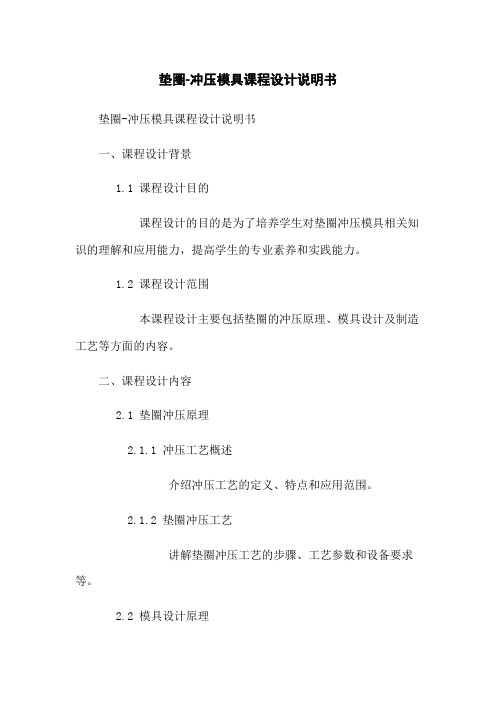
垫圈-冲压模具课程设计说明书垫圈-冲压模具课程设计说明书一、课程设计背景1.1 课程设计目的课程设计的目的是为了培养学生对垫圈冲压模具相关知识的理解和应用能力,提高学生的专业素养和实践能力。
1.2 课程设计范围本课程设计主要包括垫圈的冲压原理、模具设计及制造工艺等方面的内容。
二、课程设计内容2.1 垫圈冲压原理2.1.1 冲压工艺概述介绍冲压工艺的定义、特点和应用范围。
2.1.2 垫圈冲压工艺讲解垫圈冲压工艺的步骤、工艺参数和设备要求等。
2.2 模具设计原理2.2.1 模具设计概述概述模具设计的定义、分类和基本原理等。
2.2.2 垫圈冲压模具设计详细说明垫圈冲压模具的结构、功能和设计要点。
2.3 模具制造工艺2.3.1 模具制造工艺概述介绍模具制造工艺的基本流程和要求。
2.3.2 垫圈冲压模具制造工艺详细说明垫圈冲压模具制造的步骤、工艺和注意事项。
三、课程设计实施3.1 教学方法结合理论和实践,采用讲授、实验、案例分析等多种教学方法。
3.2 教材选用推荐教材:《冲压技术与模具设计》3.3 实践任务安排学生参与垫圈冲压模具制造过程的实际操作,提高实践能力。
四、课程设计评价4.1 评价指标根据学生的实际表现,评价其对垫圈冲压模具知识理解和应用能力的程度。
4.2 评价方法采用考试、实验报告、实践操作和互动讨论等方式进行评价。
五、附件本文档中涉及以下附件,请参阅:2.垫圈冲压模具设计图纸3.相关案例分析资料六、法律名词及注释1.冲压工艺:指将板材或带材通过冲压模具的冲压动作,加工成所需形状的工艺。
2.模具设计:指根据工件要求,设计模具的结构和尺寸,以实现对工件的加工。
3.模具制造工艺:模具制造过程中的工艺流程,包括铣削、钳工、研磨、电火花等工艺环节。
垫圈冲压成形工艺及模具设计—冲孔--课程设计
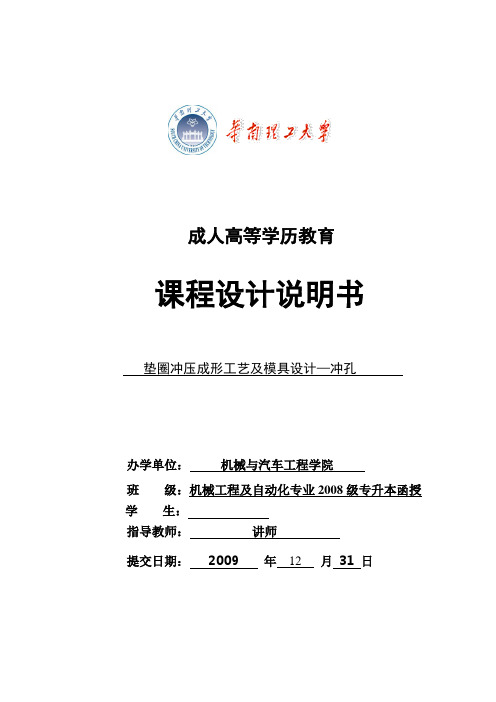
成人高等学历教育课程设计说明书垫圈冲压成形工艺及模具设计—冲孔办学单位: 机械与汽车工程学院班 级:机械工程及自动化专业2008级专升本函授学 生:指导教师: 讲师提交日期: 2009 年 12 月 31 日课程设计任务书兹发给机械工程及自动化专业2008级专升本函授班学生魏媚媚课程设计任务书,内容如下:1. 课程设计题目:垫圈冲压成形工艺及模具设计-冲孔2. 课程设计内容:(1)图示零件冲压工艺性的分析;(2) 分析比较后,确定零件的冲压工艺方案;(3)零件的冲压工艺计算;(4)选择和确定模具类型及结构形式;(5) 设计冲孔工序的模具(绘制总装图及凸、凹模图);(6)编写上述内容的设计计算说明书。
3。
主要参考资料:(1) 王孝培主编. 冲压设计资料。
北京:机械工业出版社,1983. (2)夏琴香,袁宁编著. 模具设计及计算机应用. 广州:华南理工大学出版社,2008;(3)李天佑主编。
冲模图册。
北京:机械工业出版社,1990;(4)吴诗惇主编。
冲压工艺及模具设计。
西安:西北工业大学出版社,2002。
4。
本设计任务书于2009年10 月11 日发出,应于2009 年12 月31 日前完成,然后进行答辩。
专业教研室、研究所负责人夏琴香审核2009 年10 月10 日指导教师袁宁签发2009 年10 月11 日摘要冲压加工可以很高效率对板材实施塑性成形加工.此外,与其他加工方法相比较,具有生产效率高,材料利用率高、零件互换性好及成形零件机械性能好的特点。
由于冲压加工方法具有独特的技术优势,在制造领域中的利用越来越广泛,在航天航空、兵器、船舶、汽车、电气、仪表等生产中,冲压加工技术以及成为不可缺少的重要加工方法之一。
目前,冲压加工及其模具技术的发展主要集中早金属塑性成形理论与工艺研究,冲压加工过程中的计算机辅助分析,开发研制成形新工艺及新型模具,以及生成自动化和柔性化等方面.本次设计了一套冲孔、落料的模具。
方形垫圈冲压复合模具设计

方形垫圈冲压复合模具设计
设计一个方形垫圈冲压复合模具需要考虑以下几个方面:模具结构设计、材料选择、工艺流程和模具加工。
1.模具结构设计:
上模由切割机构、冲头和定位销组成。
切割机构用于切割板材成为合
适的尺寸,冲头用于将板材冲击成为方形形状,定位销用于确保上模位于
恰当的位置。
下模由定位销、导向柱和冲头组成。
定位销用于将下模固定在机床上,导向柱用于保证上模和下模的准确对位,冲头用于将板材冲击成为带有孔
的方形形状。
背模由切割机构、冲头和导向柱组成。
切割机构用于将垫圈从板材中
切割出来,冲头用于将垫圈从板材上弹出,导向柱用于保持背模和上下模
的准确对位。
2.材料选择:
考虑到垫圈需要具有一定的弹性和耐用性,一般选择具有良好塑性和
高强度的金属材料,如不锈钢、铜等。
3.工艺流程:
在制造方形垫圈的过程中,首先需要将适当尺寸的板材切割成相应的
形状,然后使用上模和下模将板材冲压成为带有孔的方形形状。
最后,使
用背模将垫圈从板材上切割出来。
4.模具加工:
根据设计需求和材料选择,可以采用车削、铣削、线切割、磨削等工艺进行模具的加工。
同时,需要考虑加工精度和模具的寿命,以确保模具的可靠性和稳定性。
在设计方形垫圈冲压复合模具时,还需要考虑到其使用环境和应用要求,例如垫圈的尺寸、材料厚度、产量要求等。
通过综合考虑以上因素,可以设计出适合生产方形垫圈的冲压复合模具。
垫圈冲压工艺及模具设计
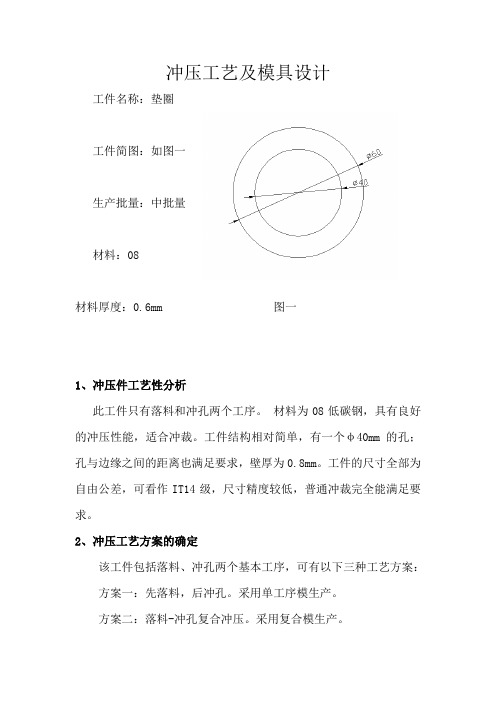
冲压工艺及模具设计工件名称:垫圈工件简图:如图一生产批量:中批量材料:08材料厚度:0.6mm 图一1、冲压件工艺性分析此工件只有落料和冲孔两个工序。
材料为08低碳钢,具有良好的冲压性能,适合冲裁。
工件结构相对简单,有一个φ40mm的孔;孔与边缘之间的距离也满足要求,壁厚为0.8mm。
工件的尺寸全部为自由公差,可看作IT14级,尺寸精度较低,普通冲裁完全能满足要求。
2、冲压工艺方案的确定该工件包括落料、冲孔两个基本工序,可有以下三种工艺方案:方案一:先落料,后冲孔。
采用单工序模生产。
方案二:落料-冲孔复合冲压。
采用复合模生产。
方案三:冲孔—落料级进冲压。
采用级进模生产。
方案一模具结构简单,但需两道工序两副模具,成本高而生产效率低,难以满足大批量生产要求。
方案二只需一副模具,工件的精度及生产效率都较高,且工件最小壁厚20mm远大于凸凹模许用最小壁厚1.8mm,模具强度较好,制造难度小,落料圆和冲孔圆同轴度满足要求。
方案三也只需一副模具,生产效率高,操作方便,但工件同轴度不意满足要求。
通过对上述三种方案的分析比较,该件的冲压生产采用方案二为佳。
3、主要设计计算(1)排样方式的确定及其计算设计复合模,首先要设计条料排样图。
垫圈的形状为圆,直排时材料利用率低,应采用多排,如图二垫圈排样图所示的排样方法,可显著地减少废料。
搭边值查表可得1mm和1.2mm。
冲裁件面积 A=πr²=3.14×30²=2826 mm²条料宽度 B=60×2﹢1.2×2+61×1.7/2=174.2 mm由于冲压常用钢板规格宜选710mm×1420mm的钢板,取B=177.5 mm步距 S=60+1=61 mm一个步距的材料利用率η=nA/BS×100%=3×2826/﹙177.5×61﹚×100%=78.3%故条料宽度为177.5mm,步距离为61 mm,一个步距的材料利用率为78.3%。
垫圈冲压工艺与模具毕业设计

垫圈冲压工艺与模具毕业设计摘要随着工业的发展,冲压技术在各个领域中得到广泛应用,垫圈冲压作为其中的一种重要工艺,具有操作简单、效率高等优点。
本毕业设计以垫圈冲压工艺为研究对象,通过对冲压工艺参数的优化设计,提高了垫圈冲压工艺的质量和效率。
通过对垫圈冲压工艺中一些常见问题的分析,并对模具结构进行优化设计,增加了模具的使用寿命和冲压件的质量。
通过实际工艺测试,验证了优化设计的有效性。
关键词:垫圈冲压;工艺参数;模具结构;优化设计1.引言冲压工艺作为一种常见的金属加工工艺,其应用领域非常广泛。
垫圈冲压作为冲压工艺的一种重要形式,因其形状简单、操作方便等优点,在汽车、机械制造等行业中得到广泛应用。
本毕业设计以垫圈冲压工艺为研究对象,通过对冲压工艺参数的优化设计,提高了垫圈冲压工艺的质量和效率。
2.垫圈冲压工艺参数的优化设计冲压工艺参数的合理选择对于提高冲压件的质量和效率至关重要。
本设计通过对垫圈冲压过程中的几个关键参数进行优化设计,提高了垫圈冲压的质量和效率。
2.1材料选用垫圈通常使用冷轧板材或冷拔优质钢丝作为原材料。
本设计中选择了冷轧板材作为垫圈的原材料,因其成本较低、易于加工等优点。
2.2模具设计垫圈的模具设计是冲压工艺中非常重要的一环。
本设计通过对模具的结构进行优化设计,提高了模具的使用寿命和冲压件的质量。
模具采用硬质合金材料制作,保证了模具的硬度和耐磨性。
同时,对模具的几何形状进行了优化设计,减少了冲压过程中的歪斜和裂纹等缺陷。
2.3工艺参数的优化选择在垫圈冲压工艺中,工艺参数的选择对于冲压件的质量和效率有着重要影响。
本设计通过实验和理论分析,选择了合适的冲压速度、冲裁力和冲压次数等参数,使得冲压件的质量和效率达到最优。
3.结果与分析通过对垫圈冲压工艺中一些常见问题的分析,本设计提出了解决方案,并进行了实际工艺测试。
结果表明,通过优化设计的冲压工艺参数和模具结构,有效地提高了垫圈冲压工艺的质量和效率。
垫圈冲压成型工艺及模具设计机械加工工艺过程卡
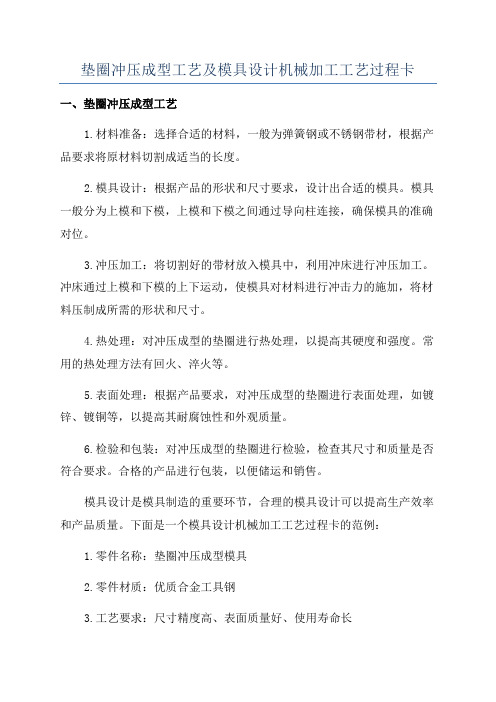
垫圈冲压成型工艺及模具设计机械加工工艺过程卡一、垫圈冲压成型工艺1.材料准备:选择合适的材料,一般为弹簧钢或不锈钢带材,根据产品要求将原材料切割成适当的长度。
2.模具设计:根据产品的形状和尺寸要求,设计出合适的模具。
模具一般分为上模和下模,上模和下模之间通过导向柱连接,确保模具的准确对位。
3.冲压加工:将切割好的带材放入模具中,利用冲床进行冲压加工。
冲床通过上模和下模的上下运动,使模具对材料进行冲击力的施加,将材料压制成所需的形状和尺寸。
4.热处理:对冲压成型的垫圈进行热处理,以提高其硬度和强度。
常用的热处理方法有回火、淬火等。
5.表面处理:根据产品要求,对冲压成型的垫圈进行表面处理,如镀锌、镀铜等,以提高其耐腐蚀性和外观质量。
6.检验和包装:对冲压成型的垫圈进行检验,检查其尺寸和质量是否符合要求。
合格的产品进行包装,以便储运和销售。
模具设计是模具制造的重要环节,合理的模具设计可以提高生产效率和产品质量。
下面是一个模具设计机械加工工艺过程卡的范例:1.零件名称:垫圈冲压成型模具2.零件材质:优质合金工具钢3.工艺要求:尺寸精度高、表面质量好、使用寿命长4.工艺步骤:4.1设计模具结构:根据垫圈的形状和尺寸要求,设计模具的上模、下模、导向柱和定位装置等部件。
4.2绘制模具图纸:根据模具结构设计,绘制模具图纸,包括三视图、剖视图、局部放大图等。
4.3材料准备:选择合适的优质合金工具钢作为模具材料,根据模具图纸将材料切割成适当的尺寸。
4.4粗加工:对材料进行粗加工,包括铣削、车削、钻孔等工艺。
通过粗加工,将材料修整成接近最终形状的毛坯。
4.5精加工:对粗加工后的毛坯进行精加工,包括镗削、磨削、线切割等工艺。
通过精加工,使模具达到精度要求。
4.6热处理:对加工完成的模具进行热处理,以提高其硬度和耐磨性。
常用的热处理方法有淬火、回火等。
4.7组装调试:将经过热处理的零部件进行组装,确保模具的准确配合和正常工作。
垫圈的冲压工艺及模具设计
垫圈的冲压工艺及模具设计垫圈是广泛应用于机械、建筑、电器、汽车等领域的一种紧固件。
它通常由金属或橡胶材料制成,具有防水、防尘、减震、缓冲等作用。
垫圈的冲压工艺和模具设计是制造垫圈的重要环节,对产品的质量和生产效率有着直接的影响。
下面将详细介绍垫圈的冲压工艺及模具设计。
首先是垫圈的冲压工艺。
在进行切割时,需要根据垫圈的尺寸和形状来决定切割的方式。
常用的切割方式有剪切、剪板和冲击等。
剪切是将板材剪断成所需形状的方法,剪板是指将板材在一个刀模上进行剪切,冲击则是通过模具上的冲头将材料冲出所需形状。
送料是将板材送入冲床模具的过程。
优化的送料方式可以提高工作效率和产品质量。
常见的送料方式有机械送料和气动送料等。
成形是将材料按照模具的形状进行加工的过程。
这一步骤需要根据垫圈的尺寸和形状来确定合适的冲床模具。
冲压过程中,需要注意调整冲头的压力和冲程,以确保垫圈的成型质量。
取出是将已经成型的垫圈从模具中取出的过程。
垫圈的取出方式可以采用手工取出或自动取出。
手工取出适用于较小规模的生产,自动取出适用于大规模生产。
接下来是垫圈的模具设计。
模具是进行垫圈冲压加工的工具。
合理的模具设计可以提高工作效率和产品质量。
垫圈的模具设计主要包括模具结构设计和模具零件设计。
模具结构设计是模具整体结构形式的设计。
在设计时,需要考虑到材料的特性、冲压工艺的要求、模具的可靠性和易于维护的方便性等因素。
模具结构设计通常包括上模板、下模板、导向柱、导向套、顶针和顶板等模具零件的安排和组合。
模具零件设计是模具的具体零件形状和尺寸的设计。
模具零件设计包括模具的内外形状设计、冲头和冲座的设计、导向柱和导向套的设计等。
在模具零件设计中,需要考虑到材料的硬度、耐磨性和耐腐蚀性等性能要求,以及模具的使用寿命和生产效率等因素。
在垫圈的模具设计中,还需要注意一些特殊要求。
例如,在对垫圈进行冲剪时,需要考虑到切割刃的尺寸和角度,以确保切割的准确性和平整度;在对垫圈进行成形时,需要注意冲头和冲座的尺寸和形状,以确保垫圈的形状和尺寸的一致性。
垫圈冲压课程设计
课程设计冲压工艺与模具设计第一章制件工艺性分析及计算1.1课程设计题目垫圈冲压成型工艺及模具设计,零件图如图1:零件名称:垫圈技术要求:1材料:08F2厚度:1mm3生产批量:大批图1 零件图1.2冲压件工艺分析①材料:该冲裁件的材料08F是超低碳素钢,具有较好的可冲压性能。
②零件结构:该冲裁件结构简单,比较适合冲裁。
③尺寸精度:零件图上所有未注公差的尺寸,属自由尺寸,可按IT14级确定工件尺寸的公差.查公差表可得各尺寸公差为:零件外形: 100-0.36mm 4300.62-mm 零件内形: 100.360+ mm 250.520+mm孔中心距:600.740.74+-mm 结论:适合冲裁1.3方案及模具结构类型该零件包括落料、冲孔两个基本工序,可以采用以下三种工艺方案:方案①先落料,再冲孔,采用单工序模生产。
方案②落料一冲孔复合冲压,采用复合模生产。
方案③中孔一落料连续冲压,采用级进模生产。
方案①模具结构简单,但需要两道工序、两套模具才能完成零件的加工,生产效率较低,难以满足零件大批量生产的需求。
由于零件结构简单,为提高生产效率,主要应采用复合冲裁或级进冲裁方式。
方案②只需要一套模具,冲压件的形位精度和尺寸易于保证,且生产效率也高。
尽管模具结构较方案一复杂,但由于零件的几何形状简单对称,模具制造并不困难。
方案③也只需要一套模具,生产效率也很高,但零件的冲压精度较复合模的低。
欲保证冲压件的形位精度,通过以上三种方案的分析比较,对该件冲压生产以采用方案②为佳。
1.4排样设计查《冷冲压工艺与模具设计》【1】表2-10,确定搭边值 两工件间的搭边:a=1.5mm工件边缘搭边:a 1=1.8mm 步距为:63m条料宽度B=(L+2a)0∆-=46.60∆-mm 取480∆-mm确定后排样图如图2所示:图2 排样图一个步距内的材料利用率η为冲裁单件材料的利用率按式计算,即100%AS Bη=⨯∙=2600÷(63×46.6)×100%=88.56% 式中 S —在送料方向,排样图中相邻两个制件对应点的距离(mm )B — 条料宽度A —一个进距之间的实用面积1.5压力中心模具压力中心是指冲压时各个冲压力合力的作用点位置。
垫圈冲压成型工艺及模具设计垫圈冲压成型工艺及模具设计
1 绪论模具工业是国民经济的基础工业,是工业生产的重要工艺装备。
先进国家的模具工业已摆脱从属地位,发展为独立的行业。
日本工业界认为:“模具工业是其它工业的先行工业,是创造富裕社会的动力”。
美国工业界认为:“模具工业是美国工业的基石”。
在德国模具被冠以“金属加工业中的帝王”之称。
1.1 国内模具的现状和发展趋势在我国,1998年3月在《国务院关于当前产业政策要点的决定》模具被列为机械工业技术改造序列的第一位,生产和基本建设序列第二位,把发展模具工业摆在发展国民经济的重要位置。
目前,我国冲压模具在产值占模具总产值的40%以上,处于主导地位。
冲压是一种先进的少无切削加工方法,具有节能省材,效率高,产品质量好,重量轻,加工成本低等一系列优点,在汽车,航空航天,仪器仪表,家电,电子,通讯,军工,日用品等产品的生产中得到了广泛的应用。
据统计,薄板成型后,制造了相当于原材料的12倍的附加值,在国民经济生产总值中,与其相关的产品占四分之一,在现代汽车工业中,冲压件的产值占总产值的59%。
但大型多工位级进模、精密冲压模具、大型多型腔精密注塑模、大型汽车覆盖件模具等虽已能生产,但总体技术水平不高,与国外先进国家相比,仍有很大差距。
改革开放以来,随着国民经济的高速发展,市场对模具的需求量不断增长。
近年来,模具工业一直以15%左右的增长速度快速发展,模具工业企业的所有制成分也发生了巨大变化,除了国有专业模具厂外,集体、合资、独资和私营也得到了快速发展。
到目前,中国约有模具生产厂家2万多家,从业人员有50多万人,全年模具产值高达450亿元人民币以上。
中国模具工业的发展在地域分布上存在不平衡性,东南沿海地区发展快于中西部地区,南方的发展快于北方。
模具生产最集中的地区在珠江三角和长江三角地区,其模具产值约占全国产值的三分之二以上。
而在模具制造领域中占有重要地位的冲压模具生产技术与工业发达国家相比还相当落后,主要原因是我国在冲压基础理论及成形工艺、模具标准化、模具设计、模具制造工艺及设备方面与工业发达国家尚有相当大的差距,导致我国模具在寿命、效率、加工精度、生产周期等方面与工业发达国家的模具相比差距相当大。
垫圈的冲裁模设计
垫圈的冲裁模设计垫圈冲裁模具设计垫圈是一种常用的密封元件,在机械、汽车和建筑行业中广泛应用。
垫圈的冲裁模具设计是实现垫圈生产的重要步骤之一、本文将对垫圈的冲裁模具进行详细设计,以确保垫圈的质量和生产效率。
1.垫圈冲裁模具的构造垫圈冲裁模具通常由上下模板、冲头、导柱、导套和底座等组成。
冲头是用来将材料冲下的部件,它需要与上下模板以及底座等部件相连接。
导柱和导套则用来保证冲头与模板之间的相对位置,以确保冲裁的准确性。
2.垫圈冲裁模具的材料选择垫圈冲裁模具所选用的材料需要具备耐磨、耐冲击和耐腐蚀等特点。
常用的模具材料有合金工具钢、高速钢和硬质合金等。
具体选择材料时需考虑垫圈的形状、尺寸和生产数量等因素。
3.垫圈冲裁模具的设计原则垫圈冲裁模具的设计应遵循以下原则:(1)合理确定冲裁模具的结构和外形尺寸,以适应垫圈的形状和尺寸要求。
(2)采用合理的冲头形状和尺寸,以确保冲裁的准确性和一致性。
(3)冲裁模具的冲裁力要足够大,以确保材料能够完全冲下,并且冲裁过程中不产生过大的变形。
(4)冲裁模具的导柱和导套要设计合理,以确保冲头在冲裁过程中的定位准确。
(5)考虑垫圈的生产数量和使用寿命等因素,设计模具的强度和耐用性。
4.垫圈冲裁模具的制造工艺垫圈冲裁模具的制造过程一般包括以下几个步骤:(1)根据设计图纸,制作上下模板、冲头和底座等模具部件。
(2)加工导柱和导套等配件,保证模具的准确定位。
(3)对模具部件进行硬化处理,以增加其硬度和耐磨性。
(4)将模具部件进行装配,并进行必要的调试,确保各部件之间的配合准确。
(5)进行模具的试产和调整,以确保冲裁的准确性和生产效率。
5.垫圈冲裁模具的维护与保养为了确保垫圈冲裁模具的正常使用和延长其寿命,需要进行定期的维护与保养工作。
主要包括:(1)对模具进行清洁,去除灰尘和油污等杂质。
(2)定期对模具进行润滑,以减小摩擦和磨损。
(3)及时修复或更换损坏的模具部件,以保证模具的正常工作。
- 1、下载文档前请自行甄别文档内容的完整性,平台不提供额外的编辑、内容补充、找答案等附加服务。
- 2、"仅部分预览"的文档,不可在线预览部分如存在完整性等问题,可反馈申请退款(可完整预览的文档不适用该条件!)。
- 3、如文档侵犯您的权益,请联系客服反馈,我们会尽快为您处理(人工客服工作时间:9:00-18:30)。
冲压工艺及模具设计工件名称:垫圈工件简图:如图一生产批量:中批量材料:08材料厚度:0.6mm 图一1、冲压件工艺性分析此工件只有落料和冲孔两个工序。
材料为08低碳钢,具有良好的冲压性能,适合冲裁。
工件结构相对简单,有一个φ40mm的孔;孔与边缘之间的距离也满足要求,壁厚为0.8mm。
工件的尺寸全部为自由公差,可看作IT14级,尺寸精度较低,普通冲裁完全能满足要求。
2、冲压工艺方案的确定该工件包括落料、冲孔两个基本工序,可有以下三种工艺方案:方案一:先落料,后冲孔。
采用单工序模生产。
方案二:落料-冲孔复合冲压。
采用复合模生产。
方案三:冲孔—落料级进冲压。
采用级进模生产。
方案一模具结构简单,但需两道工序两副模具,成本高而生产效率低,难以满足大批量生产要求。
方案二只需一副模具,工件的精度及生产效率都较高,且工件最小壁厚20mm远大于凸凹模许用最小壁厚1.8mm,模具强度较好,制造难度小,落料圆和冲孔圆同轴度满足要求。
方案三也只需一副模具,生产效率高,操作方便,但工件同轴度不意满足要求。
通过对上述三种方案的分析比较,该件的冲压生产采用方案二为佳。
3、主要设计计算(1)排样方式的确定及其计算设计复合模,首先要设计条料排样图。
垫圈的形状为圆,直排时材料利用率低,应采用多排,如图二垫圈排样图所示的排样方法,可显著地减少废料。
搭边值查表可得1mm和1.2mm。
冲裁件面积 A=πr²=3.14×30²=2826 mm²条料宽度 B=60×2﹢1.2×2+61×1.7/2=174.2 mm由于冲压常用钢板规格宜选710mm×1420mm的钢板,取B=177.5 mm步距 S=60+1=61 mm一个步距的材料利用率η=nA/BS×100%=3×2826/﹙177.5×61﹚×100%=78.3%故条料宽度为177.5mm,步距离为61 mm,一个步距的材料利用率为78.3%。
查板材标准,宜选710mm×1420mm的钢板,每张钢板可剪裁为4张条料(177.5mm×1420mm),每张条料可冲68个工件,故每张钢板的材料利用率为76.2%。
图二排样方式图(2)冲压力的计算该模具采用复合模,考虑操作安全,采用典型的倒装结构。
拟选择刚性推件装置推出垫圈。
冲压力的相关计算如下。
落料力的计算: F=KLtτ式中 F——落料力(N);K——系数,模具间隙值的波动、刃口的磨损、板料力学性能和厚度波动等因素的影响而给出的修正系数,一般取K=1.3。
L——落料周边长度(mm);t——材料厚度(mm);τ——材料抗剪强度 (MPa)。
L=πd=3.14×60=188.4 mm查表可知τ为325 MPa。
F=KLtτ=1.3×188.4×0.6×325= 47759.4 N同理冲孔力 F冲孔= 1.3×3.14×40×0.6×325=31839.6 N查表知:卸料力 F₁=K₁×F=0.05×47759.4=2387.97 N推件力 F₂=nK推F冲孔=3×0.05×31839.6 =4775.94 NF₄= F+F冲孔+F₁+F₂=86762.91 N根据计算结果,冲压设备拟选100KN冲床。
(3)压力中心的确定及相关计算该工件为规则外形形状,压力中心位于几何中心即圆心上故,不需计算。
(4)工作零件刃口尺寸计算在确定工作零件刃口尺寸计算方法之前,首先要考虑工作零件的加工方法及模具装配方法。
结合该模具的特点,工作零件的形状相对较简单,适宜采用线切割机床分别加工落料凸模、凹模、凸模固定板以及卸料板,这种加工方法可以保证这些零件各个孔的同轴度,使装配工作简化。
因此工作零件刃口尺寸计算就按分开加工的方法来计算,具体计算如下所示。
所有未注公差的尺寸,属自由尺寸,可按IT l4级确定工件尺寸的公差。
零件外形尺寸为:60零件内形尺寸为:40查公差表可得各尺寸公差为:零件外形: 零件内形: 以凹模为基准:零件内形: 以冲孔凸模为基准计算4、模具总体设计(1)弹簧的选择选择依据:最大压缩量时不超过弹簧极限,而最大压缩量=预压量h1+卸料工作行程h2+修模量h3。
考虑到卸料的可靠 性,取弹簧在预压量为h1时就应有的压力Fx 。
由卸料力和模具安装弹簧的空间大小,初选弹簧的数量为二,则每个弹簧应有的预压力N 4.6592/8.1318/Q11==≥n F F 。
初选弹簧为工作极限负荷Fj=1390N>659.4N ,钢丝直径d=6mm ,弹簧中径D=32mm ,自由高度74.060-67.0040+074.060-)4(0)(∆=+∆-=p x B B d δ474.00)74.05.060(+⨯-=d B 185.0065.59+=67.0040+0)(p x A A p δ-∆+=017.00467.034.40)67.05.040(--=⨯+=L0=65mm ,极限负荷下的变形量hj=19.3mm 。
当弹簧在预压量h1时,卸压力达659.4N ,由压缩量和力的线形关系得:预压量15.93.1913904.65911=⨯==j j h F F h 又因卸料板的工作行程h 2=0.6+1=1.6mm ;修磨量h 3=5mm ;所以最大压缩量)3.19(65.155.615.9j h h <=+=总 即能满足要求。
弹簧装配高度h=L 0-h 1=65-9.15=55.85mm 。
(2)卸料板的选择: 根据凸凹模及弹簧、卸料螺钉等的布置,取卸料板的平面尺寸为125mm ×125mm ,厚度为15mm 。
(3)选择上、下模座:采用GB2855.5、6—1990后侧带导柱形式模板。
根据最大轮廓尺寸125mm ×125mm 选相近规格标准模座.L ×B 为125mm ×125mm ,上模座厚35mm ,下模板座35mm 。
(4)导柱导套:按GB2861.1、6选d=38mm ,模具闭合高度225.5mm ,选导柱110mm,d=22mm 。
(5)模柄:查表知100kN 压力机模柄孔尺寸为Φ30×50。
所以选尺寸为Φ30×Φ70的带凸缘形式的模柄。
(6)凹模:凹模采用整体凹模,各冲裁的凹模孔均采用线切割机床加工,安排凹模在模架上的位置时,要依据计算压力中心的数据,将压力中心与模柄中心重合。
凹模厚度 H=Kb=0.3×60 mm=18 mm (查表2.26得k=0.3) 凹模壁厚 C=(1.5~2)H=27~36 mm取凹模厚度H=20 mm ,凹模壁厚C=35 mm ,凹模宽度B=b+2C=(60+2×30)mm=120 mm凹模长度L 取125 mm (送料方向)凹模轮廓尺寸为125 mm ×125 mm ×30 mm 。
(7)凸模:1)凸模固定板:厚度:D H )5.1~1(=40)5.1~1(⨯=60~40=所以取其厚度为40mm 。
直径为130mm 。
2)凸模全长:结合工件外形并考虑加工,将落料凸模设计成直通式,采用线切割机床加工,2个M10螺钉固定在垫板上,与凸模固定板的配合按H6/m5。
其总长L=h ₁+h ₂+t +h :式中 L ——凸模长度(mm );h ₁——凸模固定板厚度(mm );h ₂——卸料板厚度(mm );t ——材料厚度(mm );h ——增加长度,它包括凸模的修磨量,凸模进入凹模的深度(0.5mm ~1mm ),凸模固定板与卸料板之间的安全距离等,一般取10mm~20mm。
L =20+14+0.6+27.4=62mm(8)凸凹模:采用直接固定方法,取其高度为20 mm,定凸缘高度为20mm.直径为76mm,为减小模具尺寸,在凸缘外铣去2个缺口以放置卸料弹簧。
(9)垫板:考虑推件装置在上模内挖窝,采用垫板加固。
取垫板厚度取l0mm,长宽为125×125mm(10)闭合高度:模具闭合高度为上模板、下模板、凸凹模、凹模、固定板、垫板等厚度的总和。
即H0=30+35+62+25+20+40-0.6=211.4mm其中减去的0.6为冲裁时上模进入下模的距离。
因公称压力为100KN的压力机的最大闭合高度为170mm小于211.4mm。
所以选择公称压力为250KN 的压力机。
即其Hmax=250mm,Hmin=(250-70)mm=180mm。
满足mmHHmmH105minmax+≥≥-。
此外模柄的尺寸也应该重选:查表1.7知250kN压力机模柄孔尺寸为Φ50×70。
所以选尺寸为Φ50×100的带凸缘形式的模柄.(11)卸料螺钉:根据模具的结构选择,并且应满足螺钉窝深h+螺钉杆长l +卸料板厚=0.6+下模板厚+凸凹模厚。
按GB2867、6-81选d=10mm的带肩卸料螺钉,螺柱长l=60mm。
螺钉头高度10mm.因螺钉窝深h +螺钉杆长+卸料板厚=0.5mm十凸凹模厚十下模板厚。
即h+60+12=0.5+41+35得卸料螺钉窝深h=24.5mm。
检验:卸料螺钉窝深h -螺钉头高度=24.5-10=14.5 mm 卸料板行程+修磨量+安全间隙=1.5+5+(2~6)=8.5~12.5mm。
所以所选的螺钉长度满足要求,并且定卸料螺钉窝深h=24.5mm。
(12)推杆的选择:按推件状态时推杆需高出滑块模柄孔一定距离c≈5~10,即推杆长度L ≥安全距离c+模柄孔深+模柄法兰厚+修模量=c(5~10)+50+16+5=76~81。
所以推杆可按GB28671-81选择,其尺寸为:d=12mm,L=100mm,c=7mm。
3.冲压设备选择:选择公称压力为250KN的开式压力机,其具体数值如下:公称压力250KN,最大封闭高度250mm,封闭高度调节量70mm,工作台尺寸(左右×前后)560mm×360mm,模柄孔尺寸:φ50×70。
垫圈冲压工艺卡片排样图草图工序工序说明加工草图设备0 剪床下料公称压力为250KN的开式压力机1 落料2 冲孔3 检验材料名称牌号 08号钢每张条数 4 形状尺寸 1420x750 每条件数 68。