加工钢化玻璃中玻璃常见缺陷及解决办法
钢化玻璃常见的缺陷,产生原因

4
炸口
1半成品磨边质量差
2玻璃出炉温度底
3变弧速度慢或快
4变弧滞后时间长
1增加炉温或加热时间
2清理风栅处辊子
3降低变弧速度
4校正变弧装置
常在玻璃表面出现和弯形制品
5
玻璃中央灰白线或光学变形
1硅辊温度过高
2Hale Waihona Puke 平衡吹风压力太底3无SO2气体或用得少
1降低炉底温度或增加上部温度
2调整热平衡压力
1加热厚玻璃时温度过高
2加热时间长
3陶瓷辊表面温度高
1适当降低炉温
2适量减少加热时间
3打开加热平衡阀或降低下部温度
常在10mm以上的玻璃出现
序号
缺陷名称
产生原因
处理方法
备注
3
裂纹
1玻璃出炉温度底
2风栅处有硬质物接触玻璃表面
3变弧速度快
4变弧步同步
1增加炉温或加热时间
2清整风栅出辊子
3降低变弧速度快
4校正变弧装置
钢化厚玻璃及钻孔、切槽、开口的玻璃容易发生
3钻孔,切槽,开口不符合标准
4钢化厚玻璃时炉温太高
5重复钢化
1采购优质原片,存在裂纹,暗伤,结石,较大气泡时禁止钢化
2提高磨边质量,使玻璃边部平整光滑,无微裂纹
3按照标准进行钻孔,切槽和开口.
4钢化厚玻璃时(15-19mm)炉温应相应降低.
5禁止二次钢化
钢化厚玻璃及钻孔,切槽,开口得玻璃时容易发生
11
玻璃钢化时烂(钢化吹风烂)
1玻璃材料有缺陷
如:砂粒、微裂纹等
2玻璃温度不均匀,加热时间短
3切角、钻孔、开槽时,边部质量较差,倒角不良
【金晶玻璃●技术交流】钢化玻璃常见质量问题的分析与解决

【金晶玻璃●技术交流】钢化玻璃常见质量问题的分析与解决钢化玻璃的外观质量问题有许多表现形式,我们按照其出现在生产过程中阶段的不同,将其分为两大类:①由原片质量缺陷造成的钢化玻璃外观质量问题,如:点状缺陷(气泡、夹杂物)、划伤、光学变形等;②由钢化加工过程造成的外观质量问题,如:钢化玻璃的平整度问题(波浪纹、吻合度、板面变形)、光学方面的问题(中部灰色、应力斑过重、虹彩现象)、白道、划伤、麻点等。
一由原片缺陷造成的外观质量问题及原因分析最常见的有:点状缺陷(气泡、夹杂物)、划伤、光学变形等。
气泡、夹杂物和光学变形是原板固有的缺陷,划伤是在原片玻璃生产和搬运过程中形成的。
如果原片达不到相应的标准要求,不仅会使钢化后的玻璃在外观质量方面达不到《钢化玻璃》国家标准要求,同时也会大大增加钢化玻璃的炸炉、应力分布不均匀、自爆、机械强度降低、热稳定性以及各种安全性能变差等的风险,导致钢化炉的停产、清炉,使得产品的成品率和生产效率下降,生产成本的上升,造成没必要的浪费。
钢化玻璃生产企业即使通过调整钢化炉的工艺参数也无法避免这类质量问题的发生,而企业只能通过严格控制生产管理制度,对员工加强培训,使操作人员熟练掌握检验标准的内容和相应的检验方法,对原片玻璃进行严格的筛选,避免有问题的原片玻璃流入再加工阶段。
二由钢化加工过程造成的外观质量问题最常见的有:钢化玻璃的平整度问题(波浪纹、吻合度、板面变形)、光学方面的问题(中部灰色、风斑过重、虹彩现象)、白道、划伤、麻点等。
1 钢化玻璃平整度不好的问题钢化玻璃平整度不好的问题可以分为2类:第1类,弯型钢化玻璃平整度不好的问题。
对这类问题通常考虑其吻合度指标,当弯型钢化玻璃成品出现吻合度达不到设计要求时,主要会出现以下3种现象:1)成品玻璃与设计要求出现扭曲偏差。
这说明需要进行弯钢化的玻璃在辊道上的位置没有放置正确,玻璃弯曲的中心线与辊道不平行,如果出现这种情况,操作人员需要重新调整玻璃在上片台上的位置,使玻璃弯曲的中心线与辊道处于平行状态。
钢化玻璃出现问题及解决方案

总结词
光学畸变是由于玻璃的透光性能不均匀造成的,需要进 行改善。
详细描述
可以使用物理或化学方法改善光学畸变。物理方法是通 过改变加热和冷却制度,使玻璃在热处理过程中受热和 冷却更加均匀,从而改善透光性能。化学方法则是使用 相应的化学药剂对玻璃表面进行腐蚀或抛光处理,使透 光性能更加均匀。
04
预防措施
安装问题
总结词
安装问题通常是由于安装过程中对玻 璃的扭曲、切割不当或安装后固定不 牢固等原因引起的。
详细描述
在安装钢化玻璃时,如果操作不当, 如扭曲、切割不当或固定不牢固,可 能会导致玻璃受力不均,从而在使用 过程中出现开裂、变形等问题。
使用环境影响
总结词
使用环境影响主要包括温度变化、紫 外线照射和化学物质侵蚀等因素,这 些因素可能加速钢化玻璃的老化,导 致其性能下降。
ቤተ መጻሕፍቲ ባይዱ
运输与存储不当
总结词
运输与存储不当可能导致钢化玻璃在运输或存储过程中受到撞击、挤压或振动等外力作用,从而引发 开裂、破损等问题。
详细描述
在运输或存储钢化玻璃时,如果操作不当,使其受到撞击、挤压或振动等外力作用,可能会导致玻璃 内部产生应力,从而在使用过程中出现开裂、破损等问题。
03
解决方案
破裂问题解决方案
要点二
详细描述
可以使用高温处理、化学处理等方法消除气泡。高温处理 是将玻璃加热到高温,使气体在玻璃中充分溶解,然后进 行缓慢冷却,使气体在冷却过程中从玻璃中析出,最后进 行抛光处理。化学处理则是使用相应的化学药剂对玻璃进 行浸泡或涂覆,使气体在玻璃中溶解度降低,从而达到消 除气泡的效果。
光学畸变问题解决方案
钢化玻璃出现问题及 解决方案
钢化玻璃常见的缺陷产生原因
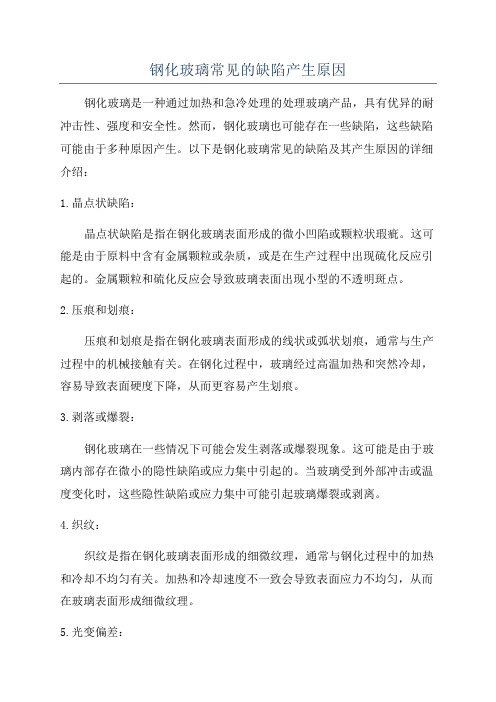
钢化玻璃常见的缺陷产生原因
钢化玻璃是一种通过加热和急冷处理的处理玻璃产品,具有优异的耐冲击性、强度和安全性。
然而,钢化玻璃也可能存在一些缺陷,这些缺陷可能由于多种原因产生。
以下是钢化玻璃常见的缺陷及其产生原因的详细介绍:
1.晶点状缺陷:
晶点状缺陷是指在钢化玻璃表面形成的微小凹陷或颗粒状瑕疵。
这可能是由于原料中含有金属颗粒或杂质,或是在生产过程中出现硫化反应引起的。
金属颗粒和硫化反应会导致玻璃表面出现小型的不透明斑点。
2.压痕和划痕:
压痕和划痕是指在钢化玻璃表面形成的线状或弧状划痕,通常与生产过程中的机械接触有关。
在钢化过程中,玻璃经过高温加热和突然冷却,容易导致表面硬度下降,从而更容易产生划痕。
3.剥落或爆裂:
钢化玻璃在一些情况下可能会发生剥落或爆裂现象。
这可能是由于玻璃内部存在微小的隐性缺陷或应力集中引起的。
当玻璃受到外部冲击或温度变化时,这些隐性缺陷或应力集中可能引起玻璃爆裂或剥离。
4.织纹:
织纹是指在钢化玻璃表面形成的细微纹理,通常与钢化过程中的加热和冷却不均匀有关。
加热和冷却速度不一致会导致表面应力不均匀,从而在玻璃表面形成细微纹理。
5.光变偏差:
光变偏差是指钢化玻璃在一些情况下可能会导致光线透射的颜色和变形。
这可能是由于原料中的金属杂质或生产过程中的一些物质残留导致的。
玻璃中常见缺陷种类及主要来源和控制方法
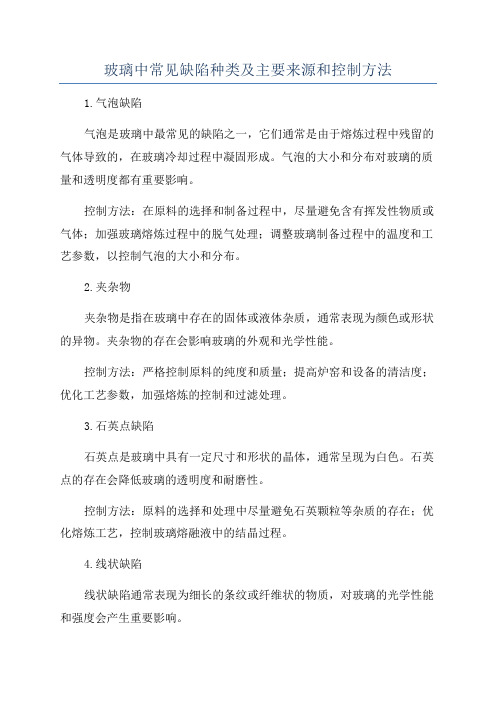
玻璃中常见缺陷种类及主要来源和控制方法
1.气泡缺陷
气泡是玻璃中最常见的缺陷之一,它们通常是由于熔炼过程中残留的气体导致的,在玻璃冷却过程中凝固形成。
气泡的大小和分布对玻璃的质量和透明度都有重要影响。
控制方法:在原料的选择和制备过程中,尽量避免含有挥发性物质或气体;加强玻璃熔炼过程中的脱气处理;调整玻璃制备过程中的温度和工艺参数,以控制气泡的大小和分布。
2.夹杂物
夹杂物是指在玻璃中存在的固体或液体杂质,通常表现为颜色或形状的异物。
夹杂物的存在会影响玻璃的外观和光学性能。
控制方法:严格控制原料的纯度和质量;提高炉窑和设备的清洁度;优化工艺参数,加强熔炼的控制和过滤处理。
3.石英点缺陷
石英点是玻璃中具有一定尺寸和形状的晶体,通常呈现为白色。
石英点的存在会降低玻璃的透明度和耐磨性。
控制方法:原料的选择和处理中尽量避免石英颗粒等杂质的存在;优化熔炼工艺,控制玻璃熔融液中的结晶过程。
4.线状缺陷
线状缺陷通常表现为细长的条纹或纤维状的物质,对玻璃的光学性能和强度会产生重要影响。
控制方法:优化原料的处理和质量控制,降低不溶物的含量;定期维护和更换工艺设备,减少颗粒的产生;加强熔炼过程中的温度和熔融液流动控制。
玻璃在钢化过程中经常遇到的问题及解决办法

玻璃在钢化过程中经常遇到的问题及解决办法加工钢化玻璃过程中,各种参数不合理,可能造成钢化玻璃弯曲及其他外观质量,在此总结了一些经常遇到的弯曲原因及如何解决钢化玻璃质量的问题。
1.上翘原因:玻璃在出炉时,玻璃上表面温度高于下表面温度,玻璃上表面温度过高流失快,下表面温度低流失慢,在风栅处,上部风压低于下部风压。
解决方法:使炉底温度升高、适当降低上部温度,若炉温稳定,可调整风栅压力,在风嘴高度不变时使上部压力大于下部压力。
2.下弯原因:玻璃在出炉时,玻璃下表面温度高于上表面温度,玻璃下表面温度过高流失快,上表面温度低流失慢,在风栅处,下部风压低于上部风压。
解决方法:使上部温度升高、适当降低下部温度,若炉温稳定,可调整风栅压力,在风嘴高度不变时使下部压力大于上部压力。
3.波筋原因:玻璃在炉内加热时间过长,炉内温度过高,玻璃在出炉时陶瓷辊道转动速度过慢。
解决方法:缩短加热时间、降低炉温、加快玻璃出炉速度。
4.球面原因:玻璃中部温度低于边缘温度。
解决方法:改变加热温度控制模式,提高中部温度;降低整体炉温,延长加热时间。
5.斑麻点原因:炉底温度过高,陶瓷轨道表面太脏,玻璃在炉内加热时间过长。
解决方法:降低加热时间,清洗陶瓷轨道,降低炉底温度。
6.玻璃中心发乌(发灰)和光学缺陷原因:玻璃在进炉后边缘上翘而弯曲,造成玻璃下表面对陶瓷轨道的压力过大从而引起这种缺陷,或者,陶瓷辊道表面温度过高与玻璃表面接触导致的,或玻璃进炉后陶瓷辊道摆动速度 过快。
解决方法:提高空炉时间热平衡时间,提高玻璃上表面温度,减少空炉时间,保证玻璃连续进炉,降低玻璃进炉后陶瓷辊道摆动速度。
7.钢化玻璃的表面上有裂纹原因:玻璃在炉内加热时间过短或炉温过低。
解决方法:提高炉温,延长加热时间。
8.在炉内破碎原因:有以下几种情况:A.玻璃内有裂纹(钢化玻璃内在必须无裂纹),在裂纹的末稍,积累的应力释放而破裂。
B.磨边不好,留下细微的裂纹。
C.钢化厚玻璃时,炉温太高,表面和中心的温差太大。
加工钢化玻璃中玻璃常见缺陷及解决办法

调整上下风栅。
炉内炸裂
炉内温度设置不合理。
调整炉内温区上下温度设置。
某组风栅通风不畅或漏风。
解决漏风和不通风的问题。
原片玻璃退火不良,残余应力过大或不匀(断面有生茬),有结石、裂子等缺陷。
严格检验挑选原片。
风栅内炸裂
切割、磨边粗糙,造成微裂纹扩展。
改进切割、磨边工艺,避免缺陷。
提高风压或降低风栅高度。
输送速度过低,玻璃后端入风栅太迟,降温多。
提高输送速度,减少温降。
碎片颗粒过大或不均匀
加热温度低,时间短或炉内温差大。
适当提高炉温和加长时间,开热平衡均匀炉温。
玻璃厚度比规定的小。
使用标准厚度的玻璃。
冷却强度不够,或不均匀。
增加风压或降低风栅高度。
风栅内某一位置玻璃有上弯,某一位置玻璃有下弯,某一位置玻璃不弯。
以上原因分析和解决方案是综合不少优秀操作工的经验整合成文档在此公开,希望给众多玻璃深加工操作人员帮助!
提高加热温度或延长加热时间,使玻璃加热至可塑状态。
自爆
玻璃只是表面达到可塑温度,内层未烧透,冷却后期才炸裂,玻璃块度小,类似钢化玻璃。
调整加热温度或时间,使玻璃热透。
玻璃加热、淬冷不匀或不对称,造成应力不均匀或偏移。
调节炉温或冷却强度,使之均匀而对称。
厚玻璃冷却时风压过大,张应力过大,炸后颗粒过细。
钻孔、开槽较多或钢化再加热。
精细加工,加热时勤开炉门检查,发现炸裂及时排出。
加热厚玻璃时炉温过高,内外层温差大,内层张力过大。
适当降低炉温,延长加热时间。
玻璃钻孔边部未处理好或玻璃钻孔直径小于玻璃厚度。
处理好钻孔的边缘,加大钻孔直径。
玻璃钢制品常见缺陷及处理办法

1、玻璃纤维折叠的折纹
2、辊子滚压不充分
1、不要用力折叠纤维
2、仔细认真地滚压
变形(翘曲)
树脂收缩
1、减慢固化速度(M水、钴水加入量要适中)
使固化完全后再脱模
3、防止局部因放热过多而引起局部翘曲
4、脱模后正确放置产品,以防后固化时变形
5、使用低收缩的树脂
1、配大料时确认是否加入钴水
2、使用时一定要加入规定量的M水
3、加入M水时要搅拌均匀
伤痕及裂纹
1、擦伤
2、脱模方式不对或勉强脱模
3、模具形状不合理或局部难脱模
1、小心操作及搬运
2、采取正确的脱模方式,并且不可用力过猛
3、模具设计及加工时应考虑可脱模性
二、结构层的缺陷
缺陷
原因分析
改进措施
空洞(气泡)
1、操作时滚压不够
3、胶衣问题
1、仔细进行模具的保养
2、打蜡仔细
3、检查胶衣树脂及颜料
鼓泡
1、胶衣层与铺层间有空洞和气泡
2、涂刷胶衣层后时间过长才涂铺树脂纤维
3、涂刷胶衣层后,表面粘有水份或杂质
1、操作时一丝不苟地进行脱泡
2、应在适当的时候(凭手感粘性)铺涂树脂纤维(20分钟左右)
3、表面不能有水滴或杂质
颜色不均
1、胶衣混入水份
玻璃钢制品常见缺陷及处理办法
一、胶衣面中的缺陷
缺陷
原因分析
改进措施
起皱
1、胶衣层膜厚不足或厚度不均
2、作业场地湿度太高
3、固化剂M水太少或搅拌不足
1、均匀涂刷胶衣,并达到规定的厚度
2、除湿,极端情况下停止作业
3、固化剂加入量不能过少,要充分搅拌均匀
光泽不良
- 1、下载文档前请自行甄别文档内容的完整性,平台不提供额外的编辑、内容补充、找答案等附加服务。
- 2、"仅部分预览"的文档,不可在线预览部分如存在完整性等问题,可反馈申请退款(可完整预览的文档不适用该条件!)。
- 3、如文档侵犯您的权益,请联系客服反馈,我们会尽快为您处理(人工客服工作时间:9:00-18:30)。
缺陷名称
产生原因分析
解决办法
玻璃划伤
玻璃重叠拿、放。
单片拿、放。
输送辊道辊面不干净。
清理辊道。
辊道面不平或不同步。
调整辊道使之水平或同步。
辊痕与麻点
辊子上有粘附物。
轻微时通SO2,严重时停炉清辊。
玻璃加热时间过长。
缩短加热时间。
玻璃边部温度过高,边部缺陷集中。
缩小片间隙,交错装片,使各炉装载率相近。
以上原因分析和解决方案是综合不少优秀操作工的经验整合成文档在此公开,希望给众多玻璃深加工操作人员帮助!
玻璃中部压强过大,中部缺陷较多。
减小上下温差,尽量减小入炉后玻璃边部上翘。
玻璃上弯(前、后端上翘)
出炉时玻璃上表面比下表面温度高,可塑状态冷却时热面收缩多。
降低炉内上部温度或提高下部温度。
淬冷时上表面比下表面冷却强度小,上面热收缩多。
增加上风栅冷却强度或减小下风栅冷却强度。
玻璃下弯(中部上鼓)
出炉时玻璃上表面比下表面温度低,可塑状态冷却时凉面收缩少。
提高加热温度或延长加热时间,使玻璃加热至可塑状态。
自爆
玻璃只是表面达到可塑温度,内层未烧透,冷却后期才炸裂,玻璃块度小,类似钢化玻璃。
调整加热温度或时间,使玻璃热透。
玻璃加热、淬冷不匀或不对称,造成应力不均匀或偏移。
调节炉温或冷却强度,使之均匀而对称。
厚玻璃冷却时风压过大,张应力过大,炸后颗粒过细。
浮法玻璃成型时,着锡面渗入SnO,钢化时被氧化成SnO2体积膨胀,玻璃表面受压出现微细皱褶,使光线产生干涉色。
选择优质原片,加热温度掌握下限,用细抛光粉进行抛光。
成品玻璃有较明显的风斑
风栅压的太低。
适当提高风栅高度。
钢化玻璃在加工过程中因为以上原因会造成钢化玻璃产品缺陷,成品不合格或者成品率低下,这就需要钢化炉的操作手根据不同的情况采取适当合理的措施让钢化玻璃产品达到最佳!
提高风压或降低风栅高度。
输送速度过低,玻璃后端入风栅太迟,降温多。
提高输送速度,减少温降。
碎片颗粒过大或不均匀
加热温度低,时间短或炉内温差大。
适当提高炉温和加长时间,开热平衡均匀炉温。
玻璃厚度比规定的小。
使用标准厚度的玻璃。
冷却强度不够,或不均匀。
增加风压或降低风栅高度。
风栅内某一位置玻璃有上弯,某一位置玻璃有下弯,某一位置玻璃不弯。
上下风栅调整不平与玻璃的距离远近不等。
调整上下风栅。
炉内炸裂
炉内温度设置不合理。
调整炉内温区上下温度设置。
某组风栅通风不畅或漏风。
解决漏风和不通风的问题。
原片玻璃退火不良,残余应力过大或不匀(断面有生茬),有结石、裂子等缺陷。
严格检验挑选原片。
风栅内炸裂
切割、磨边粗糙,造成微裂纹扩展。
改进切割、磨边工艺,避免缺陷。
适当降低冷却风压或调高凤栅高度。
玻璃在风栅内碰撞。
加大摆放距离。
原片有耐火材料结石等夹杂物
加强对原片的检验挑选。
钢化彩虹
玻璃中硫化镍(NiS)结晶在高温下α-NiS向低温的β-NiS转化漫长过程中晶体形状变化体积膨胀,造成应力平衡破坏。
设引爆炉在300度、1小时条件下进行热处理,使有可能自爆的玻璃在炉内爆裂。
提高炉内上部温度或降低下部温度。
淬冷时上表面比下表面冷却强度大,上面凉收缩少。
增加下风栅冷却强度或减小上风栅冷却强度。
蝶形变形
玻璃中间下凹,周边上翘,上表面周边温度高,收缩多,中部温度低,收缩少。
调节炉内上部温差,开热平衡均匀炉温。
玻璃中间上鼓,周边下弯,下表面周边温度高,收缩多,中部温度低,收缩少。
调节炉内下部温差,开热平衡均匀炉温。
波浪式变形
加热时间过长或温度过高。
缩短加热时间或降低炉温。
炉辊弯曲变形或辊径、辊高超标。
更换或调整辊子。
炉辊往复或传输速度过慢。
适当提高往复或传输速度。
抗冲击强度低
加热温度低或内外温差大,玻璃未烧透,应力不足。
适当提高炉温或延长加热时间。
淬冷时冷却强度小,温度梯度不够,应力小。
钻孔、开槽较多或钢化再加热。
精细加工,加热时勤开炉门检查,发现炸裂及时排出。
加热厚玻璃时炉温过高,内外层温差大,内层张力过大。
适当降低炉温,延长加热时间。
玻璃钻孔边部未处理好或玻璃钻孔直径小于玻璃厚度。
处理好钻孔的边缘,加大钻孔直径。
玻璃钻孔离玻璃边太近。
加大钻孔到玻璃边的距离。
玻璃未达到可塑温度,入风栅10~30秒即炸裂,炸后玻璃块度大,类似普通玻璃。