第五版 FMEA 新版FMEA【第五版】
新版本第五版FMEA
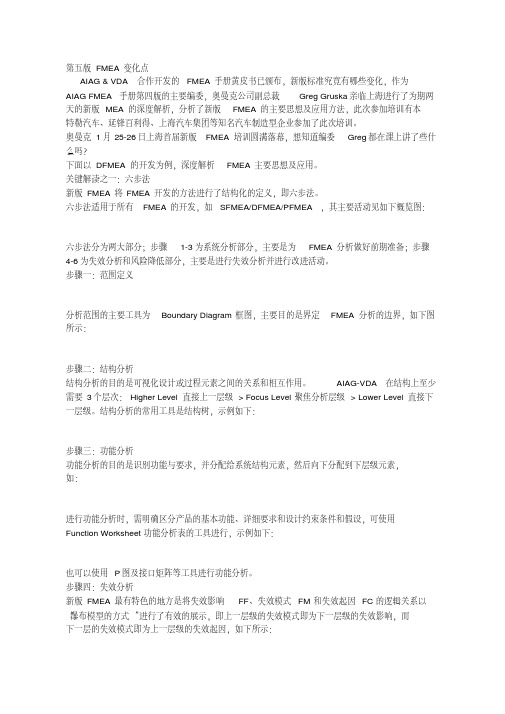
第五版FMEA变化点AIAG & VDA合作开发的FMEA手册黄皮书已颁布,新版标准究竟有哪些变化,作为AIAG FMEA手册第四版的主要编委,奥曼克公司副总裁Greg Gruska 亲临上海进行了为期两天的新版MEA的深度解析,分析了新版FMEA的主要思想及应用方法,此次参加培训有本特勒汽车、延锋百利得、上海汽车集团等知名汽车制造型企业参加了此次培训。
奥曼克1月25-26日上海首届新版FMEA培训圆满落幕,想知道编委Greg都在课上讲了些什么吗?下面以DFMEA的开发为例,深度解析FMEA主要思想及应用。
关键解读之一:六步法新版FMEA将FMEA开发的方法进行了结构化的定义,即六步法。
六步法适用于所有FMEA的开发,如SFMEA/DFMEA/PFMEA,其主要活动见如下概览图:六步法分为两大部分;步骤1-3为系统分析部分,主要是为FMEA分析做好前期准备;步骤4-6为失效分析和风险降低部分,主要是进行失效分析并进行改进活动。
步骤一:范围定义分析范围的主要工具为Boundary Diagram框图,主要目的是界定FMEA分析的边界,如下图所示:步骤二:结构分析结构分析的目的是可视化设计或过程元素之间的关系和相互作用。
AIAG-VDA在结构上至少需要3个层次:Higher Level 直接上一层级> Focus Level 聚焦分析层级> Lower Level直接下一层级。
结构分析的常用工具是结构树,示例如下:步骤三:功能分析功能分析的目的是识别功能与要求,并分配给系统结构元素,然后向下分配到下层级元素,如:进行功能分析时,需明确区分产品的基本功能、详细要求和设计约束条件和假设,可使用Function Worksheet功能分析表的工具进行,示例如下:也可以使用P图及接口矩阵等工具进行功能分析。
步骤四:失效分析新版FMEA最有特色的地方是将失效影响FF、失效模式FM和失效起因FC的逻辑关系以“瀑布模型的方式”进行了有效的展示,即上一层级的失效模式即为下一层级的失效影响,而下一层的失效模式即为上一层级的失效起因,如下所示:在进行失效分析时,需同时进行三个层级的分析,并在FMEA表中体现出三者的逻辑性,如下图所示:步骤五:风险分析该步骤的主要目的是对严重度、频度及探测度进行打分以量化风险,并确定改进行动的优先级(AP)。
FMEA-第五版全

课程总目标
AIAG&VDA FMEA的 基本概念以及FMEA 有效实施的基本方法 论
AIAG&VDA P FMEA有 效实施的基本方法(七 步法)
结合实际项目的 AIAG&VDA P FMEA的 实施以及后应用和动态 管理
FMEA的目的和范围
➢FMEA是一套面向团队的系统的、定性分析方法,目的: 评估产品/过程中失效的潜在技术风险 分析失效的起因和影响 记录预防和探测措施 针对降低风险的措施提出建议 FMEA仅用于分析计划风险,从而减少失效、提高产品和过程的安全性。
项目确定
分析范围可视 化
产品和过程的 功能可视化
建立失效链
为失效定制现有和/或计划 的控制措施和评级
项目规划、 目的、时间 安排、团队 、任务和工 具
FMEA分析中 包括什么, 不包括什么
DFEMA结构树或 等效的方法、 框图、边界图 、数字建模实 体部件;PFMEA 结构树或等效 的方法、过程 流程图;
项目确定
分析范围可视 化
产品和过程的 功能可视化
建立失效链
为失效定制现有 和/或计划的控制
措施和评级
识别降低风险 的必要措施
对降低风险的 措施进行固化
AIAG&VDA FMEA开发七步法
第1步 策划准备
第2步 结构分析
第3步 功能分析
第4步 失效分析
第5步 风险分析
第6步
改进优 化
第7步
结果文件化
AIAG&VDA FMEA概述
FMEA的定义
FMEA:潜在失效模式及后果分析 (Potential Failure Mode and Effects Analysis) FMEA是一种系统化的过程活动; 1.针对产品(系统、子系统、零件)或制造过程; 2.分析潜在失效原因、失效模式及失效后果; 3.识别现行的控制措施; 4.风险评价; 5.按行动优先级,制定改进措施并完成验证。
新版FMEA控制程序,第五版FMEA
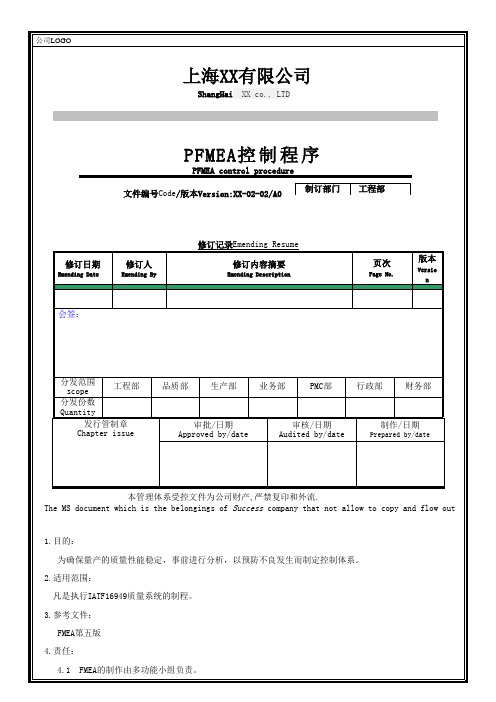
影响
对您的工厂的影响
对发运至工厂的影响(在已知情况下)
对最终用户的影响(在已知情况下
10
高
失效可能会导致从事生产或组装作业的工人面临更严重的健康和或安全风险
失效可能会导致从事生产或组装作业的工人面临严重的健康和或安全风险
影响到车辆和或其他车辆的操作安全,驾驶员、乘客、交通参与者或行人的健康状况
9
13
分类
对需要附加过程控制的零部件、子系统或系统的一些特殊过程特性分类
14
潜在失效起因/机理
指失效是怎么发生的?并依据可以被纠正或被控制的原则来描述
15
发生度
指具体的失效起因/机理发生的可能性的评价等级
16
现行过程控制
是对尽可能阻止失效模式或失效原因/机理的发生,或者探测将发生的失效模式或失效原因/机理的控制的描述
5.10.2只有修改设计及/或制程变更才能减少严重度等级。
5.11表格之填写:
项次
项 目
填 写 说 明
1
公司名称:
本公司名称
2
制造地址:
本产品生产的地点及楼层
3
顾客名称:
直接发运的客户
4
年型/平台:
产品版本
5
项目:
产品名称及规格型号
6
PFMEA开始日期:
PFMEA定稿的时间
7
PFMEA修订日期:
当工程变更,品质异常,管理评审后对PFMEA的修改。
2.适用范围:
凡是执行IATF16949质量系统的制程。
3.参考文件:
FMEA第五版
4.责任:
4.1FMEA的制作由多功能小组负责。
4.2工程部负责FMEA的整理。
五大工具第五版FMEA手册六步法与AP优先级表

一.五大工具之AIAG-VDA FMEA手册(很多场合被称第五版FMEA)六步法新版FMEA开发的方法进行了结构化的定义,即六步法。
六步法适用于所有FMEA的开发,如SFMEA/DFMEA/PFMEA,分为两大部分:步骤1-3为系统分析部分,主要是为FMEA分析做好前期准备;步骤4-6为失效分析和风险降低部分,主要是进行失效分析并进行改进活动。
步骤一:范围定义分析范围的主要工具为Boundary Diagram框图,主要目的是界定FMEA分析的边界,定义在 FMEA 中包含和排除的内容。
步骤二:结构分析结构分析的目的是可视化设计或过程元素之间的关系和相互作用。
AIAG-VDA在结构上至少需要3个层次:Higher Level 直接上一层级> Focus Level 聚焦分析层级> Lower Level直接下一层级。
结构分析的常用工具是结构树。
1. 对于 DFMEA,项目被扩展为系统、系统组件和零部件2. 对于 PFMEA,项目被扩展为过程、过程步骤和过程元素3. 添加过程工作元素标签4. 人、机器、间接材料、环境步骤三:功能分析功能分析的目的是识别功能与要求,并分配给系统结构元素,然后向下分配到下层级元素,进行功能分析时,需明确区分产品的基本功能、详细要求和设计约束条件和假设,可使用Function Worksheet功能分析表的工具进行,也可以使用P图及接口矩阵等工具进行功能分析。
1. 对于 DFMEA,功能/要求是系统功能的扩展功能,系统组件的要求或预期功能,以及组件元素的性能和功能,以及要求的预期输出或特性;2. 对于 PFMEA,功能/要求是焦点组件、功能过程步骤和工作功能的扩展功能。
步骤四:失效分析新版FMEA最有特色的地方是将失效影响FF、失效模式FM和失效起因FC的逻辑关系以“瀑布模型的方式”进行了有效的展示,即上一层级的失效模式即为下一层级的失效影响,而下一层的失效模式即为上一层级的失效起因,在进行失效分析时,需同时进行三个层级的分析,并在FMEA表中体现出三者的逻辑性。
第五版__FMEA培训教材_新版
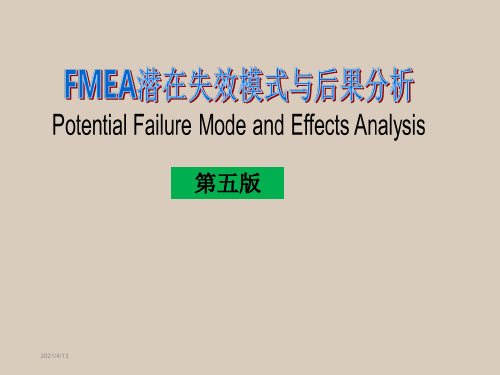
4
2021/4/13
0. 生活的现象--默菲定 律 • 默菲定律:所有可能出错的地方都将会出错!
那么,在产品制造之前我们都担心一些什么呢?
• FMEA:将问题扼杀在摇篮之中
2021/4/13 2021/4/13
对于可能存在的风险,“差不多“先生觉得可以一笔带过 ,而“零缺陷“先生觉得要不断分析其中的根本原因,然 后找到解决对策。
的一种量化的定性分析计算方法,并根据风险的大小,采取有针
对性的改进,从而了解产品(和/或制造过程)设计能力,达成一种
2021/4/13
12
事先 2021/4/13 预防并实施改进措施进行改进的方法工具。
二、FMEA基础知识
1. FMEA起源与发展
2. 何谓FMEA
3. 面对问题时FMEA应发挥的作 用
第五版
2021/4/13
产品质量策划进度图表
概念提出 项目
/批准
批准
样件
试生产
生产
策划 产品设计和开发 过程设计和开发 产品与过程确认
反馈、评定和纠正措施
策划 生产
计划和确 产品设计和 过程设计和 定项目 开发验证 开发验证
产品与过 程确认
反馈、评定 和纠正措
一 引言
二 FMEA基础知识
三 FMEA通用指南
四 DFMEA应用与实施
五 PFMEA应用与实施
➢ 总结测试
2021/4/13 2021/4/13
穿插游戏 和练习
3
一 、引言
0. 生活的现象 1. 关于潜在的理解 2. 何谓失效 3. 后果应关注的内容 4. 风险是否存在 5. 对FMEA理解
2021/4/13
10
(完整版)新版FMEA控制程序,第五版FMEA

D
探测能力
探测方法成熟度
探测机会
10
非常低
尚未建立或有已知的测试或检验方法。
不能或无法探测到失效模式
9
测试或检验方法不可能探测到失效模式。
通过任意或不定时的审核很难探测到失效模式
8
得分
影响
对您的工厂的影响
对发运至工厂的影响(在已知情况下)
对最终用户的影响(在已知情况下
10
高
失效可能会导致从事生产或组装作业的工人面临更严重的健康和或安全风险
失效可能会导致从事生产或组装作业的工人面临严重的健康和或安全风险
影响到车辆和或其他车辆的操作安全,驾驶员、乘客、交通参与者或行人的健康状况
9
预防控制在防止失效起因出现的方面起到一定的作用
6
5
中
预防控制在防止失效起因出现的方面起到有效的作用
4
3
低
最佳实践:行为或技术控制
预防控制在防止失效起因出现的方面起到高度有效的作用
2
非常低
1
极低
技术控制
预防控制在预防失效起因设计(例如零件形状)或过程(如夹具或模具设计)而发生的失效起因方面极其有效。预防控制的目的,失效模式不会因失效起因而实际发生
外观、声音、振动、粗糙度或触感令人感觉非常不舒服。
3
低
部分产品可能需要在工位上返工后才能继续加工
缺陷产品会触发次要应对计划的启动;可能不会出现额外的缺陷产品;不需要分拣
外观、声音、振动、粗糙度或触感令人感觉一般性的不舒服。
2
会导致过程、操作或操作人员的不方便
缺陷产品不会触发应对计划的启动;可能不会出现额外的缺陷产品;不需要分拣;需要向供应商提供反馈
第五版-FMEA-新版FMEA【第五版】

1963年
美国太空总署 (NASA)“阿 波罗”探月项目
1993年
美国三大汽车公 司和美国汽车工 业行动集团 (AIAG)等组 织编制和出版了 《FMEA参考手 册》
1234
5.FMEA工作方法
建立多方参与团队DFMEA:
678
核心团队
DFMEA协调员 设计工程师 系统工程师 零部件工程师 测试工程师
C
3 潜在失效
准备 减少开发过程中的后期变更
保持无缺陷产品的发布
4 影响和起因 2024/8/12
在内外部顾客和供应商之间进行有针对性的沟通
在公以司最内低部建的立成知识本库及,即时将提获供得的优经良验教的训产形成品文
D
件
使组件、系统和车辆符合注册获批所需的法规
2024/8/12
持续 改进
预防
防错
团队 合作
2024/8/12
实施注意事项:
FMEA的有效实施及其结果执行汽车行
业产品设计者、制造商和或组装企业的
职品实施在责FM使之EA时一用,就寿。道遵循命在以下期进规范间行: 的分运析行时明确 条, 件必A ,须B特考虑别真实产是
安明确全: 技风术术险语明确和可预见的(但非故意)不当
使真实用: 失,效影这响真点实 很重要。
FMEA 是一种 “事前” 行为202,4/8/12 而不是
FMEA是一 种“事前”
FMEA是一 种“事前”
FMEA是 一种“事 前”行为, 而不是
12345
6.FMEA时间节点
78
FMEA是一种“事前”行为, 而不是“事后”行为; 基于VDA-MLA【新零件成熟度保障】, 识别FMEA关键节点;
• 管理层负责选择和分配资源, 并确保 在计划的项目时间实施有效的风险管 理负有最终责任
2024全新第五版fmea培训教材

2024全新第五版fmea培训教材一、教学内容1. 章节一:FMEA概述内容:介绍FMEA的定义、目的、历史和发展趋势。
2. 章节二:FMEA的步骤内容:详述FMEA的准备工作、执行过程、数据收集与分析、制定改进措施等步骤。
3. 章节三:FMEA的应用内容:举例说明FMEA在各种领域的应用,如制造业、医疗设备、航空航天等。
4. 章节四:FMEA与风险管理内容:探讨FMEA在风险管理中的作用、优势和局限性。
二、教学目标1. 学生能理解FMEA的基本概念和目的。
2. 学生能掌握FMEA的步骤和应用。
3. 学生能认识到FMEA在风险管理中的重要性。
三、教学难点与重点重点:FMEA的基本概念、步骤和应用。
难点:FMEA的数据收集与分析、制定改进措施。
四、教具与学具准备教具:PPT、投影仪、白板、马克笔。
学具:教材、笔记本、彩色笔。
五、教学过程1. 实践情景引入:以一次飞机事故为例,引导学生思考如何预防类似事故的发生。
2. 章节一:FMEA概述细节:介绍FMEA的定义、目的、历史和发展趋势,通过实例让学生了解FMEA的实际应用。
3. 章节二:FMEA的步骤细节:详述FMEA的准备工作、执行过程、数据收集与分析、制定改进措施等步骤,并以一个具体案例进行讲解。
4. 章节三:FMEA的应用细节:举例说明FMEA在各种领域的应用,如制造业、医疗设备、航空航天等,让学生了解FMEA的广泛应用。
5. 章节四:FMEA与风险管理细节:探讨FMEA在风险管理中的作用、优势和局限性,引导学生思考如何充分利用FMEA进行风险管理。
6. 随堂练习:让学生以小组为单位,选取一个感兴趣的领域,运用FMEA进行风险分析,并分享分析结果。
7. 例题讲解:针对教材中的典型例题,进行详细讲解,引导学生学会运用FMEA进行实际问题的分析。
六、板书设计板书内容:FMEA的基本概念、步骤、应用及其在风险管理中的重要性。
七、作业设计答案:由于作业需要根据具体产品或项目进行分析,故答案不固定。
- 1、下载文档前请自行甄别文档内容的完整性,平台不提供额外的编辑、内容补充、找答案等附加服务。
- 2、"仅部分预览"的文档,不可在线预览部分如存在完整性等问题,可反馈申请退款(可完整预览的文档不适用该条件!)。
- 3、如文档侵犯您的权益,请联系客服反馈,我们会尽快为您处理(人工客服工作时间:9:00-18:30)。
和严重程度,在本过程中包含要在生产中实施替代控制方法之前获得的内部批准; • 组织应在开始返工之前,利用风险分析(如FMEA)方法来评估返工过程中的风险。如顾客有的要求,
明确
A B 真实
完整
D C 合理
实施FMEA是质量管理水平提高的过程
FMEA开展过程
IDAA模型:FMEA开展是一个完整的过程,包括启动、开发、应用、动态管理四个阶段
FMEA 启动 Initiate
FMEA 开发 Development
FMEA 应用 Application
FMEA 动态管理
Active
问题、内部外部投诉 ❖ 危害分析和风险评估变更 ❖ 产品监视过程中发现问题 ❖ 经验教训
1
2
3
4.新版FMEA背景
5
6
7
8
1.IATF16949新版FMEA变化
• 最高管理者应证实其对质量管理体系的领导作用和承诺,通过5.1.1总则d)促进使用过程方法和基于风 险的思维;
• 增加了过程风险分析(如:FMEA、过程流程、控制计划和标准的工作指导书)的开发和评审要求; • 特殊特性增加了包括顾客确定的以及组织风险分析所确定的特殊特性; • 制造过程设计输出应包括产品和制造过程的特殊特性; • 组织应制定投产前控制计划和量产控制计划,显示设计风险分析(如果顾客提供了)、过程流程图和制
FMEA
1.什么是FMEA
2
3
4
5
6
7
8
F Failure 失效
M Mode 模式
E Effects 影响
A
Hale Waihona Puke Analysis 分析技术风险【FMEA】
是否对产品或过程 中的潜在失效进行 了分析?
在本手册范围中
财务风险 采取纠正措施后产 品是否有利可图?
不在本手册范围中
时间风险 改进措施是否能在 要求时间内完成?
实施注意事项:
FMEA的有效实施及其结果执行汽车行业产品设计者、制造商和或组装企业的职责之一。
在进行分析时,必须考虑产品在使用寿命期间的运行条件,特别是安全风险和可预见的(但非故 意)不当使用,这点很重要。
实施FMEA时,就道遵循以下规范: • 明确:技术术语明确 • 真实:失效影响真实 • 合理:失效起因合理【极端事件】 • 完整:失效项目完整
• 提高汽车产品的质量、可靠性、可制造性、可服务 性和安全性
• 确保获取各组件、系统和车辆之间的层次结构、连 接、接口、级联和要求符合性信息
• 降低保修和商誉成本 • 在市场的激烈竞争中提高顾客满意度 • 证明产品和过程风险分析,从而为承担法律责任做
好准备 • 减少开发过程中的后期变更 • 保持无缺陷产品的发布 • 在内外部顾客和供应商之间进行有针对性的沟通 • 在公司内部建立知识库,即将获得的经验教训形成
文件 • 使组件、系统和车辆符合注册获批所需的法规
4 影响和起因
D
以最低的成本及时提供优良的产品
持续 改进
预防
防错
团队 合作
减少 损失
减少 浪费
FMEA的局限性:
❖ 定性(主观的),非定量(可测量的)
❖ 单点失效分析,非多点失效分析
❖ 依赖团队的知识水平,可能预测、也可能无法预 测未来的性能
❖ 团队成员对他们讨论的内容和决定自行总结。因 此,FMEA报告的质量取决于团队的文字记录能 力,所做的记录可能全面,也可能不全面
1963年
美国太空总署 (NASA)“阿 波罗”探月项目
1993年
美国三大汽车公 司和美国汽车工 业行动集团 (AIAG)等组 织编制和出版了 《FMEA参考手 册》
决问题的方法 ❖ 为短期的财务结果而
行事 ❖ 缺乏顾客为关注焦点
12
3.何时FMEA
4
5
6
7
8
FMEA应用时机在三种基本情形下使用,每种情形都有
不同的范围或重点。
新设计、新技术 或新过程
包括 完整的设计、技术、 过程
现有设计或 过程的新应用
现有设计/过程 的工程变更
包含新环境、新场地、新 应用或使用概况(包括工 作周期、法规要求等)下 的现有设计或过程。FMEA 的范围应关注于新环境、 新场地或新应用对现有设 计或过程的影响
组织识应在开始产品返工之前获得顾客批准。 • 组织应验证产品质量先期策划(或等效策划)过程中包含了适当的统计工具,作为策划的一部分,并且
适当的统计工具还包含设计风险分析(如DFMEA)、过程风险分析(如PFMEA)和控制计划中。
2.ISO26262以及GB/T34590-2017道路车辆功能安全【第1到第10部份】
新技术开发、新要求、 产品召回和使用现场失 效可能会需要变更设计/ 过程。
12
3.何时FMEA
4
5
6
7
8
FMEA修订时机包含一系列关于设计或过程的知识,如果
至少有以下一点适用,则可在生产开始后进行修订:
❖ 设计或过程变更 ❖ 运行条件变更 ❖ 要求变更(法律、规范、顾客、或最新技术
变更) ❖ 质量问题,即工厂经验、零公里、使用现场
• 两个标准的变化对传统FMEA发起挑战 • 考虑如何实现?电子电器FMEA、软件FMEA、功能安全
1
2
3
FMEA的历史
4.新版FMEA背景
5
6
7
8
美国国防部制定 MIL-P-1629
1949年
福特汽车将FMEA 作为在对其零件 设计和生产制造 的评审项目中的 一部分
1977年
1944年
洛克希德的Kelly Johnson在P80战 机项目上首次采 用FMEA以缩短研 发周期(大约153 天)
活动时间投 入不够
FMEA“七宗罪”
缺乏顾客为 关注焦点
糟糕的内部 沟通
为短期的财 务结果而行
事
FMEA 七宗罪
缺乏真正的 员工授权
把FMEA当 作快速解决 问题的方法
缺少正式的 变革战略规
划
❖ 活动时间投入不够 ❖ 糟糕的内部沟通 ❖ 缺乏真正的员工授权 ❖ 缺少正式的变革战略
规划 ❖ 把FMEA当作快速解
不在本手册范围中
战略风险
改进措施是否能在 没有利润的情况下 导入?
不在本手册范围中
产品和过程改进的设计 降低风险后的产品和过程
1 2.FMEA目标及限制
3
4
5
6
7
8
FMEA的目标是识别产品的功能或过程步骤,以及相关的潜在失效模式、失
效起因和失效影响。
A
1产品功能
2 过程步骤
B
C
3 潜在失效
FMEA及其它活动的商业目标: