丰田生产方式
丰田生产方式
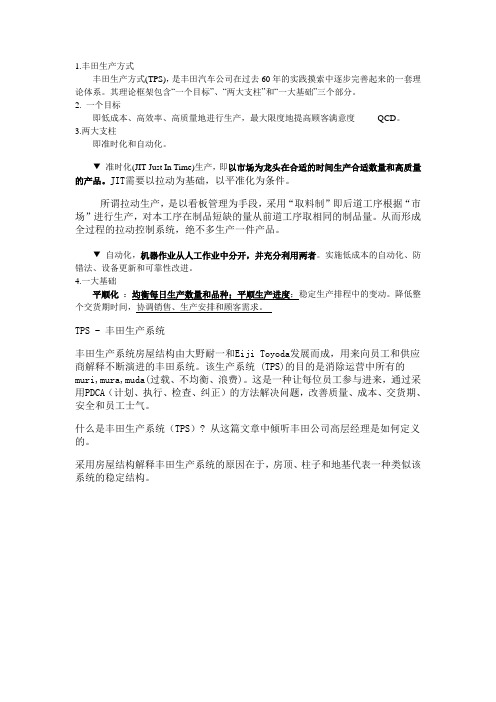
1.丰田生产方式丰田生产方式(TPS),是丰田汽车公司在过去60年的实践摸索中逐步完善起来的一套理论体系。
其理论框架包含“一个目标”、“两大支柱”和“一大基础”三个部分。
2. 一个目标即低成本、高效率、高质量地进行生产,最大限度地提高顾客满意度------- QCD。
3.两大支柱即准时化和自动化。
▼准时化(JIT-Just In Time)生产,即以市场为龙头在合适的时间生产合适数量和高质量的产品。
JIT需要以拉动为基础,以平准化为条件。
所谓拉动生产,是以看板管理为手段,采用“取料制”即后道工序根据“市场”进行生产,对本工序在制品短缺的量从前道工序取相同的制品量。
从而形成全过程的拉动控制系统,绝不多生产一件产品。
▼自动化,机器作业从人工作业中分开,并充分利用两者。
实施低成本的自动化、防错法、设备更新和可靠性改进。
4.一大基础平顺化:均衡每日生产数量和品种;平顺生产进度;稳定生产排程中的变动。
降低整个交货期时间,协调销售、生产安排和顾客需求。
TPS - 丰田生产系统丰田生产系统房屋结构由大野耐一和Eiji Toyoda发展而成,用来向员工和供应商解释不断演进的丰田系统。
该生产系统 (TPS)的目的是消除运营中所有的muri,mura,muda(过载、不均衡、浪费)。
这是一种让每位员工参与进来,通过采用PDCA(计划、执行、检查、纠正)的方法解决问题,改善质量、成本、交货期、安全和员工士气。
什么是丰田生产系统(TPS)? 从这篇文章中倾听丰田公司高层经理是如何定义的。
采用房屋结构解释丰田生产系统的原因在于,房顶、柱子和地基代表一种类似该系统的稳定结构。
今天,丰田生产系统还在不断的发展。
丰田人开始称丰田生产系统为“员工思考的系统”来代替原有名称。
丰田系统总是不断的改进。
丰田生产系统(TPS)是精益企业的运营蓝图大多数成功实施精益的组织都采用丰田生产系统作为他们的运营蓝图。
他们学习并理解该系统,重新命名使其结合自身情况为其所用,同时尽可能采用纯粹的丰田方式。
丰田生产方式
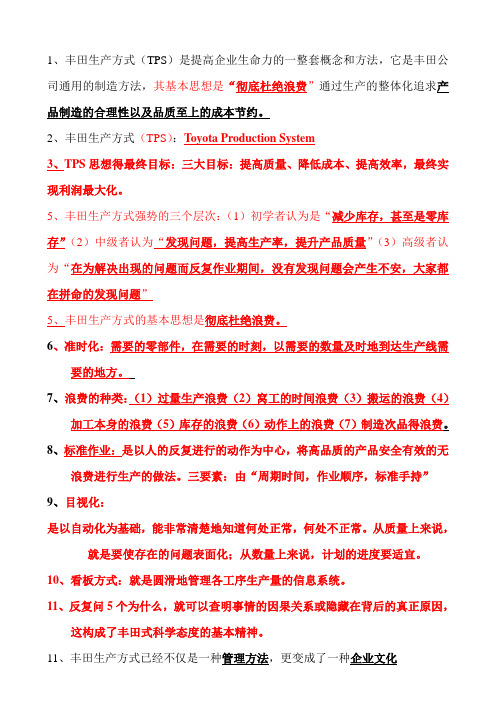
1、丰田生产方式(TPS)是提高企业生命力的一整套概念和方法,它是丰田公司通用的制造方法,其基本思想是“彻底杜绝浪费”通过生产的整体化追求产品制造的合理性以及品质至上的成本节约。
2、丰田生产方式(TPS):Toyota Production System3、TPS思想得最终目标:三大目标:提高质量、降低成本、提高效率,最终实现利润最大化。
5、丰田生产方式强势的三个层次:(1)初学者认为是“减少库存,甚至是零库存”(2)中级者认为“发现问题,提高生产率,提升产品质量”(3)高级者认为“在为解决出现的问题而反复作业期间,没有发现问题会产生不安,大家都在拼命的发现问题”5、丰田生产方式的基本思想是彻底杜绝浪费。
6、准时化:需要的零部件,在需要的时刻,以需要的数量及时地到达生产线需要的地方。
7、浪费的种类:(1)过量生产浪费(2)窝工的时间浪费(3)搬运的浪费(4)加工本身的浪费(5)库存的浪费(6)动作上的浪费(7)制造次品得浪费。
8、标准作业:是以人的反复进行的动作为中心,将高品质的产品安全有效的无浪费进行生产的做法。
三要素:由“周期时间,作业顺序,标准手持”9、目视化:是以自动化为基础,能非常清楚地知道何处正常,何处不正常。
从质量上来说,就是要使存在的问题表面化;从数量上来说,计划的进度要适宜。
10、看板方式:就是圆滑地管理各工序生产量的信息系统。
11、反复问5个为什么,就可以查明事情的因果关系或隐藏在背后的真正原因,这构成了丰田式科学态度的基本精神。
11、丰田生产方式已经不仅是一种管理方法,更变成了一种企业文化12、为提升自主创新力而学习丰田生产方式6、实践证明,丰田生产方式是企业在激烈市场竞争中取胜的法宝7、丰田生产方式代表了一种崇尚创新的企业文化和企业精神。
8、汽车是改造世界的工具,丰田生产方式改变了汽车界9、丰田生产方式是一场意识革命。
10、我国已经公开提出:走中国特色自主创新道路,为建设创新型国家而奋斗得目标10、麻省理工学院的研究人员,把丰田生产方式总结为“精益生产理念”说他“是一种不做无用功的精干型生产系统”11、丰田生产方式吸纳了美国通用汽车公司的“多品种少批量”的理念,还采纳了福特公司“彻底的合理化和成本降低”的思想12、当代世界经济发展的主流已从“知识经济”转向“创新力经济”13、“从顾客的需求出发”“彻底杜绝浪费”是丰田生产方式的基本思想14、丰田生产方式是以多品种少批量的方法制造出便宜的产品;准时化和自动化是贯穿其中的两大支柱;丰田生产方式是一种生产方法,而看板则是一种管理方式。
精益生产之丰田生产方式
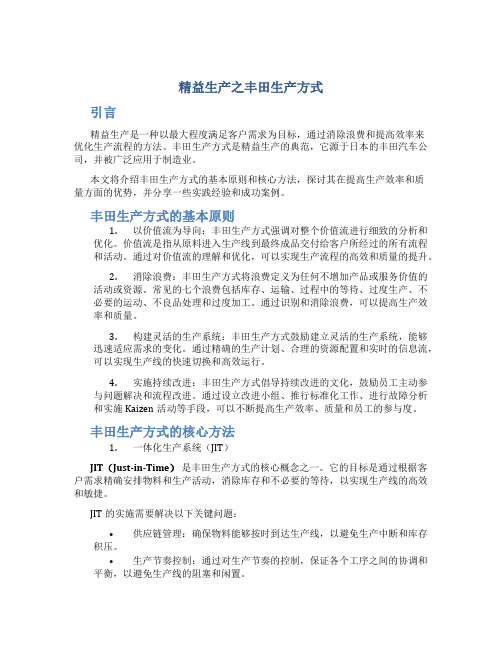
精益生产之丰田生产方式引言精益生产是一种以最大程度满足客户需求为目标,通过消除浪费和提高效率来优化生产流程的方法。
丰田生产方式是精益生产的典范,它源于日本的丰田汽车公司,并被广泛应用于制造业。
本文将介绍丰田生产方式的基本原则和核心方法,探讨其在提高生产效率和质量方面的优势,并分享一些实践经验和成功案例。
丰田生产方式的基本原则1.以价值流为导向:丰田生产方式强调对整个价值流进行细致的分析和优化。
价值流是指从原料进入生产线到最终成品交付给客户所经过的所有流程和活动。
通过对价值流的理解和优化,可以实现生产流程的高效和质量的提升。
2.消除浪费:丰田生产方式将浪费定义为任何不增加产品或服务价值的活动或资源。
常见的七个浪费包括库存、运输、过程中的等待、过度生产、不必要的运动、不良品处理和过度加工。
通过识别和消除浪费,可以提高生产效率和质量。
3.构建灵活的生产系统:丰田生产方式鼓励建立灵活的生产系统,能够迅速适应需求的变化。
通过精确的生产计划、合理的资源配置和实时的信息流,可以实现生产线的快速切换和高效运行。
4.实施持续改进:丰田生产方式倡导持续改进的文化,鼓励员工主动参与问题解决和流程改进。
通过设立改进小组、推行标准化工作、进行故障分析和实施Kaizen活动等手段,可以不断提高生产效率、质量和员工的参与度。
丰田生产方式的核心方法1.一体化生产系统(JIT)JIT(Just-in-Time)是丰田生产方式的核心概念之一。
它的目标是通过根据客户需求精确安排物料和生产活动,消除库存和不必要的等待,以实现生产线的高效和敏捷。
JIT的实施需要解决以下关键问题:•供应链管理:确保物料能够按时到达生产线,以避免生产中断和库存积压。
•生产节奏控制:通过对生产节奏的控制,保证各个工序之间的协调和平衡,以避免生产线的阻塞和闲置。
•节约资源:减少库存、运输和不必要的加工,以优化资源的利用率和降低生产成本。
2.精益流程改善(Kaizen)Kaizen是丰田生产方式中的另一个核心概念,意为持续改进。
丰田生产方式(ToyotaProductionSysterm,TPS)又称精益生产方式

丰田生产方式(ToyotaProductionSysterm,TPS)又称精益生产方式1 绪论1.1 课题背景许多年来,美国和一些主要工业化国家也抱怨自己的制造业衰落了,而且经常因此而指责中国制造业的发展。
但是,近年Robert McGuckin 博士的最新的研究披露,现在不能证实各国的制造业存在着这种缓慢下滑趋势。
例如在美国,无论他们认为制造业发展是好还是“下滑”的时候,其制造业都至少每年为本国创造了1600万个就业岗位,它占全美就业的14%,而包括德国、法国与日本等发达国家也存在相似的状况。
世界很多大型企业都在学习丰田管理模式的基础上,建立了各自的管理系统,以试图实现标杆超越,像通用电气公司、福特公司、克莱斯勒公司等世界著名企业都加入了这一行列。
但是,令人惊异的是,尽管丰田管理模式已为全球所认同和接受,真正成功的企业却并不多,如今位于日本的丰田公司每天都要接受数以万计的企业高级管理者参观,这些参观者将他们看到的管理方式带到本国后,并没有得到意想的效果,为此,很多人认为丰田管理模式的成功根源于其独特的文化因素。
但事实并非如此,例如同是日本公司的尼桑和本田却并没有达到丰田的标准,而丰田本身却将其独特的管理模式带到了全世界,这其中的代表就是位于美国肯塔基州的丰田乔治城汽车生产厂,该厂自1988年7月开始在1300英亩的厂址上进行批量生产,年生产能力为200000辆Camry轿车,相当于以往美国从日本进口同类型轿车的总量,1991年秋天丰田美国公司引入了全新的Camry轿车,1992年该类型车的供应量为40000辆,销售额将增加20%。
新的Camry轿车属于中等家庭车系列,占有美国所有轿车市场l/3的市场份额,价格平均为$18500,税前平均利润为17%,显然,其经营绩效是十分瞩目的。
各国长期经济发展的经验证明,制造业对于提高国家生产率和国民的生活水平有至关重要的决定性作用。
由于制造业在国家经济发展中的这些重要作用使美国、英国、德国、墨西哥与比利时等国过半数的制造公司在2004年都优先支持满足顾客需求的制造技术革新与改进,他们都在为计算机、数据采集装置和B9C等顶层自动化进行投资(TPS 咨询公司,2004)。
丰田生产方式的24个基本概念

1.丰田生产方式对丰田生产方式加以剖析,首先是“丰田式制造方法”。
首要的是在生产现场建立流水作业线。
它不像过去那样,把车床和车床、铣床和铣床,都集中在一起,而是按照工艺工序,把车床、铣床和钻床等一台一台地布置起来。
按照这种排列,从过去一人管一台机器过渡到一人管多台机器。
准确地说是一人管数道工序,以提高生产效率。
其次就是“看板”方式。
它是为了实现“丰田式制造方法”的非常及时生产而采取的一种手段。
为了在需要的时间只得到需要的数量和需要的物品,“看板”作为取件指令和搬运指令以及在生产时的作业信息而有效地发挥作用。
2.准时化如果能做到在需要的时间、按需要的数量取得需要的物品,就能够消除生产现场中的无效劳动和浪费,以及改善生产不均衡化的状态和管理不到位的现象,从而提高效率。
准时化是丰田汽车工业公司的创业人丰田喜一郎先生创造的。
他的继承者们发展了这种思想,总结为生产体系。
不仅要适时,而且要适量,这是关键的关键。
“准时化”和“自働化”思想构成了丰田生产方式的两大支柱。
3.自働化在丰田生产方式中,始终强调必须是带人字旁的“自働化”。
所谓“自働化”,是将人的智慧赋予机器的意思。
“自働化”这种思想的发端是从丰田公司的开山鼻祖-丰田佐吉先生的自动纺织机开始的。
丰田式自动纺织机在经纱断了或纬纱没有了的时候,机器立即停车,这是通过装有使机器能判断工作状态好坏的装置实现的。
丰田公司不仅把这种想法用于机器,而且也扩大到流水线上的操作者。
这就是说,如果发生异常,操作者可以把整个流水线停车。
“自働化”的优点是,能够防止生产次品,制止过量制造。
此外,还能自动控制生产现场发生的异常现象。
4.目视化管理在“自働化”的含义中,包含有这样一种意思,即如果发生异常现象,生产线和机床就立即停车。
这种考虑的基础来源于非常清楚地知道何处正常,何处不正常。
从质量上来说,就是要使存在问题表面化;从数量上来说,计划的进度要适宜。
这一切都应当做到用眼睛一看就立即明了的程度。
TPS丰田生产方式的主要构成要素

TPS丰田生产方式的主要构成要素丰田生产方式(Toyota Production System,TPS)是一种以精益生产和质量管理为基础的生产方式,具有极高的效率和质量控制能力。
其主要构成要素包括以下几个方面:1. 丰田生产方式的核心思想是精益生产(Lean Production),即通过消除浪费来提高生产效率和产品质量。
TPS强调通过减少人力、物料、时间和能源的浪费,以实现更高的生产能力和客户满意度。
这包括通过流程改进、提高绩效指标、优化布局和提高员工参与度等措施来实现。
2.人员流动(人力灵活性)是TPS的重要特征之一、在丰田生产方式中,员工被要求具有多种技能,可以灵活地在不同的岗位间流动,以适应生产需求的变化。
这种人力灵活性使得丰田能够在生产过程中进行更好的资源调配和需求适应。
3. 在丰田生产方式中,质量管理是一个非常重要的要素。
TPS通过建立和遵循严格的品质标准,强调质量的一致性和持续改进。
TPS采用了各种质量管理工具和技术,如统计过程控制(SPC)、质量圈(QC)和持续改进(Kaizen)等,以确保产品及其生产过程的高质量。
4.丰田生产方式还强调对供应链的管理。
在TPS中,供应商被视为合作伙伴,与丰田共同推动整个供应链的效率和质量。
通过与供应商密切合作,丰田能够确保及时供货、降低库存和实现更高的生产效率。
5.标准化是丰田生产方式不可或缺的一部分。
TPS鼓励制定和遵循标准工作流程和操作规程,以确保产品质量和生产效率的稳定性。
标准化使得每个环节的工作都能够按照规范进行,减少了错误和浪费。
6.持续改进是丰田生产方式的核心原则之一、TPS鼓励所有员工积极参与到持续改进的过程中,通过发现问题、制定解决方案、执行改进计划并反馈结果的循环来不断改进生产过程和产品质量。
7.丰田生产方式还强调通过尊重员工和提高员工参与度来推动生产效率和质量的提高。
TPS注重培养员工的技能和能力,通过培训、激励和自主决策的机会来提高员工的责任感和投入度。
精选丰田生产方式简介及JIT准时生产制
该报告的结论性意见是:
全球性的竞争使得市场变化太快,单个企业依靠自己的资源进行自我调整的速度赶不上市场变化的速度。为了解决这个影响企业生存和发展的世界性问题,报告提出了以虚拟企业(Virtual Enterprise)或动态联盟为基础的敏捷制造模式。敏捷制造是一次战略高度的变革。敏捷制造面对的是全球化激烈竞争的买方市场,采用可以快速重构的生产单元构成的扁平组织结构,以充分自治的、分布式的协同工作代替金字塔式的多层管理结构。注重发挥人的创造性,变企业之间你死我活的竞争关系为既有竞争又有合作的“共赢”(Win-win)关系。敏捷制造强调基于互联网的信息开放、共享和集成。
10.2 JIT的实质-2
JIT的实质:在需要的时候,按需要的量,生产所需要的产品(零件)。JIT的是一种理想的生产方式
10.3 看板控制系统
(1)看板的含义 所谓看板,也有人把它称为卡片,但实际上看板的形式并不局限于记载有各种信息的某种卡片形式。看板的本质是在需要的时间、按需要的量对所需零部件发出生产指令的一种信息媒介体,而实现这一功能的形式是可以多种多样的。例如在丰田的工厂中,小圆球、圆轮、台车等均被利用来作为看板。近年来随着计算机的普及程度提高,已经越来越多地引入了在各工序设置计算机终端,在计算机屏幕上显示看板信息的做法。
敏捷制造企业的特征
3)根据用户反应建立组织机构。类似于精细生产中“牵引”(Pull)方式,完全按下游的需要来组织上游的生产活动。从对用户需求及市场竞争做出迅速反应出发,“牵引”出对新的企业组织各方面的要求,根据需求促进新的组织机构的变化。4)多方动态合作。从竞争走向合作,共同抓市场机遇,将是未来制造业的一个重要特征。这种合作关系可以发生在不同层次上,有不同的紧密程度。因为低层的工作人员也都已被授权,在他本人权力范围内通过各种标准过程进入各种合作,只要这样做对满足顾客需求有利就行。
丰田生产方式简介及JIT准时生产制
丰田生产方式简介及JIT准时生产制1. 丰田生产方式简介丰田生产方式是由日本汽车制造商丰田汽车公司开发的一种生产方式,旨在提高生产效率、减少浪费,增加生产灵活性,以期提供高质量汽车以满足客户需求。
该生产方式被广泛认为是世界上最有效率和最成功的生产方式之一。
1.1 核心原则丰田生产方式的核心原则包括以下几个方面:•精益生产(Lean Production):通过减少浪费、提高生产效率、缩短生产周期等手段来实现精益生产。
•持续改善:不断寻求改进和创新,使生产过程更加高效、灵活。
•尊重人:重视员工意见,鼓励员工参与生产决策,培养团队合作意识。
1.2 生产方式特点丰田生产方式的主要特点包括:•Just In Time(JIT)生产:实现生产的准时、准量投放,避免库存积压和浪费。
•自动化:采用先进的自动化设备和技术,提高生产效率。
•柔性生产:能够根据客户需求灵活调整生产线,迅速适应市场变化。
2. JIT准时生产制JIT准时生产制是丰田生产方式的一个重要组成部分,其核心思想是在生产过程中准确计算生产所需原材料和零部件的需求量,并在需要的时候进行供应,以避免库存堆积和浪费。
以下是JIT准时生产制的主要特点和优势:2.1 特点•准时制度:所有生产活动都按照严格的时间表进行,以确保生产线的顺畅运转。
•零库存:尽可能减少原材料和半成品的库存,避免过多的资金囤积。
•高效供应链:与供应商建立紧密的合作关系,确保及时供应所需物料。
2.2 优势•降低成本:减少库存和浪费,提高生产效率,降低生产成本。
•提高供应链效率:建立稳定而高效的供应链,确保生产所需物料的及时供应。
•增加生产灵活性:能够根据客户需求快速调整生产计划,灵活应对市场变化。
结语总的来说,丰田生产方式及其重要组成部分JIT准时生产制是一种高效、灵活的生产方式,能够有效降低生产成本、提高生产效率,同时满足客户需求,是值得其他企业借鉴和学习的生产管理经验。
希望随着技术的不断发展,各行各业都能实践类似的生产方式,提升企业的竞争力,为社会经济发展做出更大的贡献。
02-丰田生产方式概述
丰田生产方式概述丰田的黑匣子就是丰田生产方式。
丰田生产方式(TOYOTA P roduction System),简称TPS。
丰田生产方式强调的是严格依据能销售的速度准时生产(Just in time 简称JIT ),也就是“在必需的时候、仅按必须的数量、生产所必需的产品”。
所以又称:准时生产方式美国麻省理工学院经过5年的汽车产业调查,指出,丰田生产方式是一种不做无用功的精干型生产系统,并命名为“精益生产方式”。
利润是企业持续经营和发展的前提条件,或者说是企业的经营目标。
那么,企业的利润从何而来呢?丰田汽车公司认为,工业企业的利润应该来自制造现场。
有两个简单的公司可以说明:公式一:售价=成本+利润,它是一种基于成本的定价方式,称之为成本主义,是指制造产品时花了一定的成本,所以售价应是成本加适当的利润。
在今天激烈竞争的时代,成本主义是行不通的。
公式二:利润=售价-成本,它的经济意义是:价格是有市场决定的,企业要想获得利润就必须学会降低成本。
丰田汽车公司采用后一公式,即汽车的售价有市场行情确定,为了获得利润,就要尽量降低成本,彻底消除一切浪费。
这就是产生企业利润的源泉。
也就是说,只能从企业的内部挖掘降低成本的办法。
这里所说的成本概念是非常广泛的。
从本质上讲,为了实现利润应从销售额中扣除的过去、现在、将来的现金支出。
那么,什么是“丰田生产方式”呢?是我们平时说的“看板方式”,或是“JIT—准时生产”。
“看板方式”是实现TPS的手段,“准时生产”和“自働化”是TPS的两大支柱。
他们是“TPS”的重要组成部分,但不能代表“TPS”。
丰田生产方式,其目的是彻底杜绝企业内部的各种浪费、提高生产效率、减低成本、生产高质量的产品;其实质就是逐步减少库存,最终实现零库存,并通过准时化生产方式彻底追求生产过程的合理性、高效性和灵活性,以满足消费者对质量和快速交货的要求。
丰田生产方式追求的最终目标:1-生产“零库存”。
丰田生产方式及其在企业推进的建议
丰田生产方式及其在企业推进的建议摘要:丰田生产方式是一种有效的企业管理模式,其包括精益生产、零库存、质量管理等核心原则,旨在提高生产效率和降低成本。
本文将探讨丰田生产方式的特点和优势,并提出推广丰田生产方式的建议,包括加强员工培训、优化流程、实施供应链管理等。
关键词:丰田生产方式、精益生产、零库存、质量管理、企业推进正文:一、丰田生产方式的特点和优势1.特点丰田生产方式是一种以客户需求为导向、以精益生产为核心,以流程化管理和全员参与为特点的生产模式。
其主要特点包括:(1)零库存:丰田实行的是“拉动式生产”,即生产自己需要的零部件,减少库存,尽量避免过程中的浪费。
(2)流程化管理:丰田实行的“精益生产”强调的是流程、时间、效率的优化,并且在实施过程中不断完善和改进。
(3)以人为本:丰田重视员工,鼓励员工的创新和参与,实行全员参与的生产方式,以创造更高的生产效率和质量。
2.优势丰田生产方式的优势主要体现在以下几个方面:(1)能够提高生产效率和质量,降低生产成本,提高企业竞争力。
(2)能够充分调动员工的积极性和创造力,增强员工的归属感,促进企业文化建设。
(3)能够为企业提供更加高效的供应链管理和物流管理,提高企业物流效率和节约企业资源。
二、推广丰田生产方式的建议1.加强员工培训丰田生产方式注重员工培训,培养员工的技能和创新意识。
企业在推广丰田生产方式时,应加强员工的技能培训,提高员工的理解和掌握程度,同时不断鼓励员工的创新意识和参与度。
2.优化流程企业在实施丰田生产方式时,应该注重流程的优化,关注方法的不断改进,不断适应市场和客户的需求变换。
3.实施供应链管理丰田生产方式不仅注重自身生产的流程、效率、质量等问题,同时重视和管理其供应链,通过供应链管理的方式来实现制造过程中所需材料和服务的高质量化、高效化、低成本化,从而进一步控制企业的成本。
企业在推广丰田生产方式时,应该注重实施供应链管理,逐步打造一个高效、高质供应链,达到共赢的局面。
- 1、下载文档前请自行甄别文档内容的完整性,平台不提供额外的编辑、内容补充、找答案等附加服务。
- 2、"仅部分预览"的文档,不可在线预览部分如存在完整性等问题,可反馈申请退款(可完整预览的文档不适用该条件!)。
- 3、如文档侵犯您的权益,请联系客服反馈,我们会尽快为您处理(人工客服工作时间:9:00-18:30)。
• “预备、瞄准、瞄准、瞄准、开火”
– 明确陈述问题,等于解决了问题的一半 – 陈述问题最好用简要说明再配上图表,用趋势图(时间不能太短, 最好6周、6个月以上) – 集中精力并有效利用资源,解决重要问题
• 反复问5个“为什么”
• 现场管理者必须将“动作”转变成“工作”,提 高投入与产出比。
– 工作是按工序向前进展,任务完成,浪费少,效率高, 是创造价值的活动。
八类浪费
①过量生产
②停工待料 ③搬运 ④加工 ⑤ 库存 ⑥ 重做 ⑦次品
⑧未被使用的员工创造力
彻底了解情况与定义问题
• ―现地现物”原则
– 不抱任何先入为主之见,亲自去仔细观察实际作业流程,才能启 动真正了解问题的流程。 – 站在圆圈里4~8个小时,仔细观察某个作业流程,直到找出其中的 浪费情形,以及导致这些浪费的原因。(马拉松式的训练)
• 原则13:不急于制定决策,以共识为基础,彻底 考虑所有可能的选择,并快速执行决策。
– – – – 以多选择同步考虑方法,广泛考虑各种可能的选择 通过根回以达成共识 以一页纸沟通并作出决策 在最前线充分地学习有助于决策
4、持续解决根本问题是学习刑组织的驱动力 • 原则14:通过不断地反省与持续改进,以 变成一个学习型的组织。
3、发展员工与事业伙伴,为组织创造价值
• 原则9:把彻底了解并拥护公司理念的员工培养为领导者, 使他们能教导其他员工。
– 从内部培养领导者,而不是自外部招揽 – 管理者的第一堂课:顾客至上
• 原则10:培养与发展信奉公司理念的杰出人才与团队。
– 发展卓越的个别工作,倡导有效的团队合作 – 工作团队是解决问题的焦点 – 驱动持续改进的是员工
任何作业流程仍然会充满浪费的情形
消除浪费必须经过持续改进的学习过程
只有那些在此流程中工作的人和管理此流 程的人才能不断地改进此流程
自动化
• 人性自动化
安灯
– 赋予机器以人的智慧,带自动停止装置的机器, 机器正常运转不需要人,人只是在机器发生异 常情况、停止运转的时候去处理。 – 杜绝生产现场中过量制造的劳动,防止生产不 合格品。
• 原则7:运用目视管理,使问题无处隐藏。
– 视觉管理制度的目的是改进创造价值的流程 – A3格式报告:以一页报告呈现你必须知道的东西 – 以技术系统与人员制度促成视觉管理
• 原则8:使用可靠的、已经过充分测试的技术以支 持人员及生产流程。
– 新技术必须支持人员、流程与价值观 – 执行工作的是人,传送与沟通信息的是计算机 – 适当、正确地采用技术
TPS发展历程
• TPS (Toyota Production System )丰田生产方式
– 又称JIT (Just In Time准时制),或称LPS(Lean Production System精益生产方式); – 是丰田公司最赚钱的工业工程,是改变世界的机器; – 是一种从生产现场彻底杜绝了浪费、不合理和质量不 稳定现象的生产管理体系。
丰田汽车公司简介
• 成立于1933年,前身生产纺织机械 • 创始人:丰田喜一郎 • 全球十大汽车制造商,每年盈利数十亿或上百亿 美元,超过原世界三大汽车厂(通用、福特、克 莱斯勒)利润的总和,竞争力第一。 • 2004年利润超过1万亿日元,成为日本历史上最 赚钱的公司 • 2006年预计销售收入23万亿日元(1949亿美元), 营业利润2.2万亿日元(186亿美元),净利润 1.45万亿日元(122亿美元)
东京大学教授,日本研究丰田方式第一人
丰田生产方式体系框架
• 根本目的
彻底杜绝企业内部各种浪费,以提高生产效率。
• 一个基础
持续改善:局部到整体永远存在改进与提高的余地;消 除一切浪费;不断地完善。
• 两大支柱
准时化:合适时间,生产合适的数量和高品质的产品。 自动化:人员与机器设备的有机配合行为。 手段:看板管理
制造管理培训教材
丰田生产方式
Toyota Production System
中央制造部
培训目的
1、学习丰田(精益)生产方式的理念和方法; 2、运用精益生产的理念和方法,推进流程与 作业的简单化、标准化、可视化、准时化, 改善生产现场,降低浪费; 3、从点点滴滴的改善开始,经过学习、自省、 实践、提高的过程,逐步完善生产管理模 式,以提高竞争力。
• 原则3:实施“拉动式制度”以避免生产过剩。
– 顾客拉动,然后补货(超市的补货制度)
• 原则4:使工作负荷均衡化,像龟兔赛跑中的乌龟 一样。
– 按单生产,同时也使生产均衡化。 – 弹性地使用承包公司和供货商的人力来处理突然增加的 需求。
2、正确的流程方能产生优异成果
• 原则5:建立立即停止以解决问题,一开始就重视 品质管理的文化。
• 原则11:重视公司的事业伙伴与供应商网络,激励并帮助 它们改进。
– 寻找坚实伙伴,以长期互惠方式共同成长 – 和供货商形成伙伴关系方式
4、持续解决根本问题是学习型组织的驱动力
• 原则12:亲临现场察看以彻底了解情况。
– – – – 深入了解并报告你亲眼所见的情形 "大野圆圈"--观看与自行思考 根据亲自证实的资料来思考与陈述 领导者也必须奉行现地现物原则
• 丰田公司是为顾客、社会、社区及其同仁创造价值 的工具,丰田人致力于提升公司业绩并促使公司成 长,为社会作出长期贡献。
2、正确的流程方能产生优异成果
• 原则2:建立无间断的作业流程以使问题浮现。
– “无间断流程”是指尽力把任何工作计划中闲置或等候 他人工作的时间减少到零。 – 多数流程中,有90%是浪费 – "一个流"的心跳速度
不制造孤岛状态
• 如果作业人员站得很分散,便不可能互相帮助。 • 在工序安排上,研究能够互相帮助的作业分配, 可以减少人员“瓶颈”,达到“少人化”目的。 • 在生产现场建立灵活的流水线,便不会制造孤岛 状态。(如U型生产线) • “少人化” – 否定“定员制”,不管一个人、两个人还是几 个人,生产线和机器仍能开工。 – 从省力、省人、到少人。 – 产量少也要降低成本。
• • • •
1933~1972年,累计生产汽车1000万辆 1972~1976年,累计生产汽车1000万辆 20世纪60~70年代,完善了精益生产方式 20世纪80年代,全面走向国际化,实现了 500万辆的年产量 • 被普遍认为是继福特汽车公司的 “大规模 生产”之后,汽车制造业演进史上的新典 范。
– 找出问题的根本原因,并提出解决方案 – 找出根本原因:问5次"为什么" – 切实可行地解决问题 – 流程导向与结果导向
四、丰田管理方法与工具
丰田生产方式的强势有三个层次:初级者 认为是“减少库存,甚至是零库存”;中 级者理解为“发现问题、提高生产率、提 高产品质量”;而高级者认为“在为解决 出现的问题而反复作业期间,没有发现问 题会产生不安,大家都在拼命地发现问 题”。 藤本隆宏
– 暂停流程以建入品质(自动化) – 通过使用对策与防范错误来解决问题 – 使品质管理简单化,并使团队全体成员参与
• 原则6:标准化是持续改进与授权员工的基础。
– – – – 标准化是持续改进与品质的基础 强制性官僚制度与授权性官僚制度 推出新产品的标准化工作 以标准化作为授权的工具
2、正确的流程方能产生优异成果
二、精益生产方式简介
没有精益,戴尔不可能超越IBM, 没有精益,丰田不可能取代通用。
詹姆斯· 沃麦克
《改变世界的机器》作者
精益生产
• ―精益生产”是国际汽车计划组织(IMVP) 对日本丰田JIT生产模式的赞誉之称。 • “精”即少而精,不投入多余的生产要素, 只在适当的时候生产必要(后道工序)的 产品; • “益”即所有生产经营活动均要有效益, 具有经济性。 • 精益生产是现代IE(工业工程)发展的最好 应用。
三、丰田14大管理原则
丰田模式4P结构
Problem solving People & Partners 解决问题:不断解决根源问题以驱 动组织的学习,坚持现场第一,持 续改进与学习。 员工与事业伙伴:尊重他们,激励他们, 培养使他们成长。
Process
流程:流程是杜绝浪费、创造价值的精益 方法,致力于制定并坚持正确的流程。
目录
一、丰田公司简介 二、精益生产方式简介 三、丰田14大管理原则 四、丰田管理方法与工具 五、学习与自省
一、丰田公司简介
卓越思考,卓越产品
丰田能够只用别人20%到30%的人力,就 可以确保相同的产量。 如果亨利· 福特一世仍然在世的话,必定采 用类似于丰田生产方式的管理模式。
大野耐一
(丰田汽车公司前副社长,丰田模式的缔造者)
• 1953年,丰田开始推行均衡化生产,致力于机械 的人性自动化; • 1960年~1970,全面推行看板管理,形成完整的 生产体系; • 1975年,开始指导外包厂商推行丰田模式。
丰田文化
• • • • • •
核心要素: 识别并消除浪费 务实地解决问题 以标准化作为改进的重要基础 教导员工对顾客与质量的热情 倡导团队合作 充分认识人员的价值及对人员的重视
丰田的目标
学习型社群 人员
短期:有能力的员工 长期:不断学习以改进
学习型组织
短期:有能力的事业伙伴 长期:学习型企业
精益制度
企业
短期:有能力的流程 长期:改善价值的流程
创造价值的贡献者
短期: 具获利性 长期:成长及贡献社会
内部
外部
丰田的思考模式
顾客想要什么?
怎样的作业流程能够以最少的浪费为顾客 创造价值
准时化(Just In Time)
• 需要的零部件,在需要的时候,以需要的数量, 及时地到达生产线的需要位臵。关键是适时、适 量。 • 目标:消除生产现场的无效劳动和浪费、生产不 均衡化的状态以及管理不到位的现象,从而提高 效率。 • 准时化生产制度并非只是减少存货而已,还要使 问题浮现出来,使人员能立即解决问题。 • 准时化生产制度是很敏感的供应链制度,丰田把 此制度与它的基础理念延伸至供货商。供应商是 丰田组装线的延伸,从原材料到递送至顾客的整 个价值链上的任何浪费必须消除。