IntroductionofQS9000-TS169495keytools-MSASPC
QS9000 介绍(doc 11)

QS9000 介绍(doc 11)部门: xxx时间: xxx整理范文,仅供参考,可下载自行编辑QS9000 Introduction美国三大汽车公司(福特、克莱斯勒、通用)根据汽车行业的特点,编制了QS 9000标准,该标准已在欧美国家普遍采用。
在我国,1995年由中国汽车技术研究中心组织翻译了这套标准,并获得美国方面的认可。
随着时间的推移,QS 9000标准逐步引起我国政府有关部门、认证机构和汽车行业的广泛关注。
据报道,我国已有四个认证机构得到授权开展 QS 9000认证工作,已有近十个组织获得了国内认证机构颁发的QS 9000证书。
现在,新闻媒介对 QS 9000认证的宣传越来越多,国外采购商对我国汽车零部件组织提出QS 9000认证要求的也越来越多,而我国许多汽车零部件组织对QS 9000标准,可以说一知半解,有的甚至一无所知,对QS 9000 认证也缺乏了解。
那么,QS 9000是个什么样的标准?它与ISO 9000有何区别?QS 9000认证对哪些组织适用?以及已经获得ISO 9000认证的组织是否还需要申请QS 9000认证?笔者谈点粗浅认识。
一、QS9000标准的由来QS 9000标准的编制,最早可追溯到1988年。
在此之前,美国三大汽车公司各自有一套对供应商质量控制的办法,它们根据各自的情况对供应商所提出有特殊要求,因此,这些要求在内容、术语、文件形式等方面存在差异。
而有些供应商可能是三大公司或其中两大公司共同的供应商,所以,这些供应商感到对不同公司的不同要求难以同时满足,也造成了不必要的浪费。
如为了满足某公司的特殊要求,供应商不得不增加投入一些额外的资源。
供应商们纷纷要求三大公司能够有一个统一的说法。
此外,ISO 9000系列标准的颁布与实施,也给美国三大汽车公司以重要的启迪。
基于这些原因,美国三大汽车公司于1988年正式开始着手编制QS 9000标准。
可以说,这套标准主要是以ISO 9001标准为基础的,在基本保留了ISO 9001标准的全部内容的基础上,增加了美国三大汽车公司对供应商的特殊要求;这些特殊要求是系统地总结了美国三大汽车公司质量管理经验的结果。
QS9000与TS16949(W003

SPC管理
质量成本管理
持续改善活动管理 客户满意度管理
优质企业
国际标准ISO 9000 顾客要求 QS 9000
生产件批准程序 公司特殊要求
手册
程序 作业指导书
其他文件
QS 9000的架构
顾客参考手册 APQP FMEA MSA SPC
半导体补充要求
零件
商品 分部 — 特殊 公司 — 特殊
基础
QS 9000规定了签署本文 件公司的基本质量体系要求, 在QS 9000的基础上可以增 加公司、分部、商品和/或零 件的特殊要求。
质量手册建立 程序书建立 作业指导书、检验指导书、保养指导书等建立 表单设计 APQP项的选定、以及质量策划的展开 零缺陷抽样计划培训
基础培训期 系统建立期 试运行期 正式执行期 认证期
APQP 运作 PPAP 运作 MSA分析运作 全尺寸功能运作 分承包方建立及供应链管理 SPC,Ppk,Cpk效果评估 预防保养动作 全部的各项QS 9000要求的检查
QSA:(Quality System Assessement) 质量体系审核
APQP:Advanced Product Quality Plห้องสมุดไป่ตู้nning先期产品品质规划
QS 9000的构成家族
FMEA:Failure Mode & Effect analysis 失效模式与效应分析
MSA:Measurement System Analysis 测量系统分析
1
2
3
确定范围 计划和定义 产品设计 过程设计 和开发 和开发
0
DFMEA PFMEA
1
2
3
APQP
45
QS9000(ISOTS 16949)五大工具概要说明
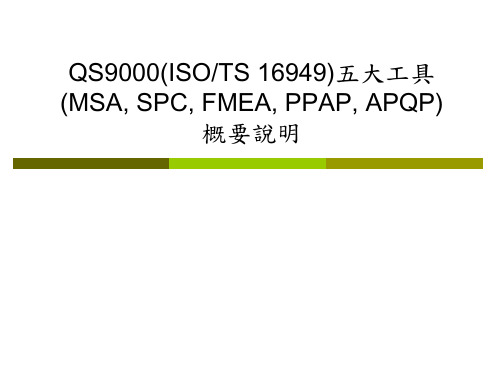
UNTL
0.00135
x 3ˆ
六、製程能力分析(續)
1. 製程能力分析可定義為估計製程能力的一種工作研究, 通常是量測產品品質特性進而瞭解現有生產條件(材料 、方法、環境)對該特性之管制能力。
2. 製程能力的估計可用機率分配的型態、 位置 (平均數) 及分散(標準差) 來表示。
3. 製程能力的評估必須要在製程穩定後才實施。亦即管制 圖上之點子連續若干點判讀為正常,無非機遇原因,或 直方圖顯示,特性數據呈現趨近於常態分配。
定功能。 2.在規定條件下,產品參數值不能維持在規定的上
下限之間。 3.產品在工作範圍內,導致零組件的破裂、斷裂、
卡死等損壞現象。
三、FMEA過程順序
系統有那功能,特徵,需要條件?
會有那些錯誤?
發生錯誤會有多慘?
那些錯誤是什麼造成的?
發生之頻率? 有那些預防和檢測?
檢測方法能多好程度?
我們能做什麼? -設計變更 -過程變更 -特殊控制 -改變標準程序或指南
變更和發展更進一步的設計。
九、設計FMEA作業流程
組成DFMEA小組 資料蒐集
釐訂DFMEA計畫 建立功能方塊圖
產品結構樹 設計可靠度展開(DQFD)
決定分析之項目功能 進行DFMEA分析 選擇關鍵失效模式
選擇關鍵失效模式
矯正預防
填寫矯正後風險優先數
N
所有RPN小
於規定值?
Y
FTA分析
DFMEA報告 N
2.不同之使用法產生之失效,以FMEA克服
五、FMEA之演變
1.FMECA之前身為FMEA,係在1950由格魯曼 飛機提出,用在飛機主控系統的失效分析。 2.波音與馬丁公司在1957年正式編訂FMEA的作 業程序,列在其工程手冊中。 3.60年代初期,美太空總署將FMECA成功的應用 於太控計畫。美軍同時也開始應用FMECA技術,並 於1974年出版MIC-STD-1629 FMECA作業程序。 4.1980修改為MIC-STD-1629A,延用至今。 5.1985由國際電工委員會 (IEC)出版之 FMECA國際標準 (IEC812),即參考MIC-STD-1629A 加以部份修改而成。
qs9000中英文版(DOC 46)

目錄(Contents):管理責任品質政策組織責任與授權Resourc資源管理代表組織聯系界面通知管理階層管理審查- 4管理審查經營計劃Analysis公司層級資料的分析和應用- 4.1.5.顧客滿意Certification Body/Re通知認証團體品質系統概述品質系統程序品質規劃先期產品品質規劃管制特性可行性審查產品平安性Process Failure Mode and Effect 制程的失效模式與效應分析錯誤防止The Control Plan - 4.2.管制計劃量產零組件核准程序概述分包商的要求工程變更的確認- 4.持續改善概述Quality an品質和生產力的改進持續改善的技術F設施與工模具管理設施、設備及制程規劃和效益工模具管理合約審查General - 4.概述審查Amendment to a Contract - 4.3.合約變更記錄設計管制概述設計資料的運用設計與開發規劃所需技能組織與技術的介面設計輸入設計輸入- 補充Design O設計輸出設計輸出- 補充設計審查設計驗証設計確認設計確認- 補充設計變更Design Chan 設計變更- 補充設計變更的影響Customer Prototype Suppor顧客原型樣品的配合保密性文件與資料管制概述文件與資料之核准與發行工程規格文件及資料變更採購概述量產中的核准物料政府,平安與環境法規Evaluation of Sub-contractor分包商之評估分包商的開發分包商交貨日程規劃採購資料採購產品的驗証供應商在分包商處的驗証Customer Verification of Subcontracted Product - ISO6.顧客以分包商產品的驗証顧客提供產品之管制Customer Owned Tooling - 4.顧客所有之工模具產品之識別與追溯性制程管制生產工場的清潔緊急應變計劃.2管制特性的指定預防保養制程監測和作業指導書制程控制的維持制程管制要求的變更作業設定的驗証制程變更外觀項目檢驗與測試概述計數值允收準則收料檢驗與測試進料產品的品質- 4.10.制程中之檢驗與測試最終檢驗與測試全盤尺寸檢驗與機能測試最終產品稽核檢驗及測試記錄供應商的實驗室要求實驗室品質系統實驗室人員Labora實驗室被測產品的識別與測試實驗室流程管制實驗室測試與校正的方法實驗室統計方法驗証的實驗室檢驗、量測與試驗設備的管制概述管制程序Calibration Services - 4.校正服務檢驗,量測及與試驗設備之記錄Measuring System量測系統分析檢驗與測試狀況額外驗証不合格品之管制概述可疑材料或產品視覺識別不合格產品之檢討與處理不合格品優先減量計劃重工產品之管制工程認可產品的授權矯正與預防措施概述解決問題的方法錯誤防止Corrective Act矯正措施退回產品的測試/分析Corrective Action Impact - 4.14.矯正行動的影響預防措施Handling, Storage, Packaging, Preservation and Delivery-Elemen 搬運、儲存、包裝、保存與交貨概述搬運儲存庫存量包裝顧客包裝標準標識防護交貨Supplier Delivery Performance Moni 供應商交貨績效監測生產排程電子通訊交貨通知系統品質記錄的管制內部品質稽核Interna稽核計劃排程訓練訓練的有效性服務服務資訊的回饋統計技術需求的確定程序統計工具的選擇Knowledge of Basic Statistical Concep 根本統計概念的知識管理責任品質政策The Supplier's management with executive responsibility shall define and document its policy for quality, including objectives for quality and its commitment to quality. The quality policy shall be relevant to the supplier's organizational goals and the expectations and needs of its customers. The supplier shall ensure that this policy is understood, implemented and maintained at all levels of the organization.供應商負經管責任之管理階層應界定並明文記載其對品質所持之政策,包含品質目標與對品質之承諾。
QS9000汽车行业质量管理体系介绍
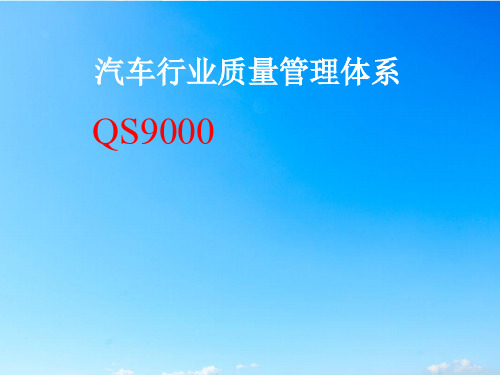
顾客参考手册 APQP
第二层次 确定谁、 做什么、 何时做
第三层次 回答如何做
FMEA MSA SPC
第四层次 信息的即时记录
汽车行业QMS的发展
ISO 9000
VDA 6.1: 1998
AVSQ
QS-9000: 1998
EAQF: 1995
现实中的困难
VDA 6.1
ADEFQSV 9016 AVSQ
产品质量先期策划和控制计划参考手册 (APQP) -第一版 : 06/1994
標準手冊
半导体补充件
- 第一版 : 04/1995
AEC-A100: QSA 半导体部分
- 第一版 : 04/1995
工装和设备补充件 (TE)
- 第一版 : 07/1996
机器与设备制造的可靠性和可维修性导则
1963 1965 1969 1971 1973 1975 1975 1979 1979 1981 1983 1987 1987 1994
QS-9000 渊源
美国軍方: MIL - Q - 9858A 通用: 通用质量標準 (GQS) 北約: AQAP 防衛標準 美國ANSI: N45 - 2 英國防部: DEF STANS 加拿大: CSA Z299 澳洲: AS 1821 / 22 /23 英國: BS 5750 美國: ANSI / ASQC / Z1.15 福特: Q101 克莱斯勒: Quality Assurance 通用: Target for Excellence ISO 9000 : 1987 標 準 系 列 ISO 9000 : 1994 標 準 系 列
- 第一版 : 1993
ISO 9000 vs QS-9000
TS16949 QS9000标准简介
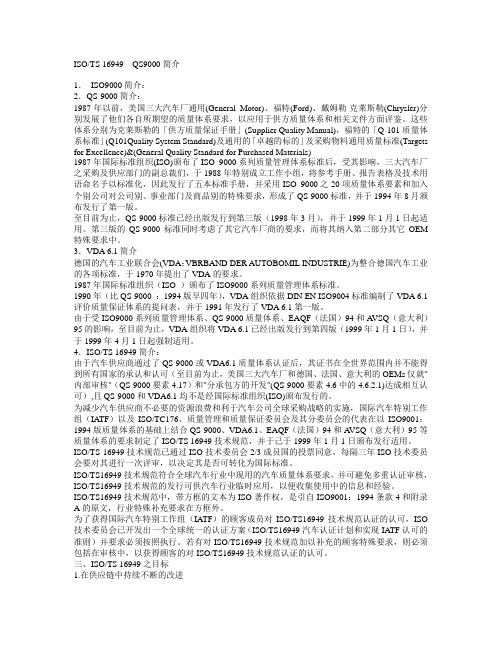
ISO/TS 16949 QS9000简介1.ISO9000简介:2.QS-9000简介:1987年以前,美国三大汽车厂通用(General Motor)、福特(Ford)、戴姆勒-克莱斯勒(Chrysler)分别发展了他们各自所期望的质量体系要求,以应用于供方质量体系和相关文件方面评鉴。
这些体系分别为克莱斯勒的「供方质量保证手册」(Supplier Quality Manual),福特的「Q-101质量体系标准」(Q101Quality System Standard)及通用的「卓越的标的」及采购物料通用质量标准(Targets for Excellence)&(General Quality Standard for Purchased Materials)1987年国际标准组织(ISO)颁布了ISO 9000系列质量管理体系标准后,受其影响,三大汽车厂之采购及供应部门的副总裁们,于1988年特别成立工作小组,将参考手册、报告表格及技术用语命名予以标准化,因此发行了五本标准手册,并采用ISO 9000之20项质量体系要素和加入个别公司对公司别、事业部门及商品别的特殊要求,形成了QS-9000标准,并于1994年8月颁布发行了第一版。
至目前为止,QS-9000标准已经出版发行到第三版(1998年3月),并于1999年1月1日起适用。
第三版的QS-9000标准同时考虑了其它汽车厂商的要求,而将其纳入第二部分其它OEM 特殊要求中。
3.VDA 6.1简介德国的汽车工业联合会(VDA:VBRBAND DER AUTOBOMIL INDUSTRIE)为整合德国汽车工业的各项标准,于1970年提出了VDA的要求。
1987年国际标准组织(ISO )颁布了ISO9000系列质量管理体系标准。
1990年(比QS-9000 :1994版早四年),VDA组织依据DIN EN ISO9004标准编制了VDA 6.1评价质量保证体系的提问表,并于1991年发行了VDA 6.1第一版。
IntroductionofQS9000-TS169495keytools-MSASPC
4、SPC:《统计过程控制》手册英文Statistical Process Control首字母缩写。用于识别过程变差,并提前采 取预防措施。
5、FMEA:《潜在失效模式及后果分析》手册英文 Potential Failure Mode and Effects Analysis的首字母 缩写,它包含设计和过程FMEA两个阶段,分别用DFMEA/PFMEA表示。用于提前识别设计缺陷而寻找预防性的改 进方案。
五大工具的关系 :APQP是树干,其余为树枝
DFMEA PFMEA
SPC APQP
MSA
PPAP
3
QS-9000 简介
QS9000是美国三大汽车公司通用、福特、克莱斯勒及一些货车制造公司所 制定的供应商基本质量体系要求。
QS9000是美国克莱斯勒汽车公司 供方质量保证手册、福特汽车公司 Q101质量体系标准 和通用汽车公司 北美创优目标 及货车制造公司基本要求 的协调产物。
--第二版 1995年2月
统计过程控制参考手册(SPC) --第一版 1992年
质量体系评定(QSA) --第二版 1998年3月
QS-9000 质量体系要求—半导体补充 要求
--第一版 1995年4月 质量体系评定(AEC-A100)—半导体 版
--第一版 1995年4月 QS-9000 质量体系要求—工具和设备 补充要求
--第一版 1996年7月 质量体系评审(QSA-TE)—工具和设 备版
--第一版 1996年7月
6
QS-9000 质量体系文件
国际标准 ISO 9000
品质管理质量认证TS16949五大核心工具学习交流
此处是大标题样稿字样十五字以内目 录一、TS 16949 五大核心工具介绍二、APQP、PPAP、FMEA应用实例三、学习交流课题TS 16949 五大核心工具包括:APQP、PPAP、FMEA、SPC、MSAAdvanced Product Quality Planning and Control PlanAPQP&CP(简称APQP):产品质量先期策划和控制计划用来确定和制定确保某产品使顾客满意所需步骤的一种结构化的方法。
是QS9000/TS16949质量管理体系的一部分。
前身是美国福特汽车公司的AQP( Advanced Quality Planning )。
Production Part Approval ProcessPPAP:生产件批准程序是指供方按照顾客要求提交生产件并获得顾客批准认可的过程,它是实施APQP、实现顾客要求的关键过程。
Failure Mode and Effects AnalysisFMEA:失效模式及后果分析是产品可靠性分析的一种重要定性方法,是一项用于确定、识别、预防或消除产品在系统、设计、过程、和服务中已知的和潜在的失效、问题、错误的工程技术。
TS 16949 标准要求:FMEAD FMEA 设计失效模式及后果分析 (技术中心主导)P FMEA 过程失效模式及后果分析 (工艺部主导)输出:特殊特性进行特别控制1、影响装配、质量的重要尺寸;2、容易出现故障的尺寸拓展思维:影响一个车型销量目标达成的因素有哪些?1、影响严重2、经常发生PPAP:生产件批准程序ppm:百万分率。
如果一个车型年目标销量为300台,3 -4月为销售旺季, 3-4月月均销量为25台,全年目标能达成吗?1、如何进行APQP(产品质量先期策划和控制计划)?目前存在的问题:未能形成CFT小组协同开展工作①、 产品前期调研及产品定义、品质目标制定,CV品质保证部参与度低,造成产品定义、品质目标制定存在不合理的现象;②、 CV品质保证部制定质量保证计划与产品定义、品质目标冲突;③、 CV技术中心试验任务书的判定条件与质量保证计划、产品定义、品质目标冲突;④、 试验结果符合国家标准要求,但不符合产品定义、品质目标及质量保证计划要求,被判定合格。
汽车行业质量管理体系TS16949五大工具介绍及应用
明确国际质量管理体系要求 国际汽车质量管理体系要求
顾客支持的参考手册 : APQP&CP FMEA MSA SPC PPAP
注: 一旦记录,第四层的项目就可以成为 质量记录
顾客特殊要求
顾客相关质量管理体系要求
质量手册
第一层 确定途径和职责 包括顾客要求的保证
程序
第二层 确定谁,做什么,何时做
作业指导书 其它文件
第三层 回答如何做
第四层 及时记录的信息 如表格,标记,标签
10/30
五大工具介绍及应用
质量管理体系的五大技术手册概况
五大 技术 手册
产品质量先期策划 (APQP)
潜在失效模式和后果分析 (FMEA)
测量系统分析 (MSA)
统计过程控制 (SPC)
生产件批准程序 (PPAP)
第一版 1994年6月 第三版 2001年7月 第三版 2002年3月 第二版 2005年7月 第四版 2006年3月
子系 统
潜在 潜在 严 级 潜在 频 现行控 失效 失效 重 别 失效 度 制
探 R建 测 P议
模式 后果 度
功能
S
要求
起因 O /机 理
预 防
探 测
度 D
N
措 施
功能、特 性或要求 是什么?
后果是 什么?
有多 糟糕 ?
起因是 什么?
会是什么问题? -无功能 -部分功能/功能 过强/功能降级 -功能间歇 -非预期功能
发生的频 率如何?
怎样能得到 预防和探测? 该方法在
探测时 有多好?
责任及 目标完 成日期
措施结果
采取 的措 施
S ODR P N
能做些什么? -设计更改 -过程更改 -特殊控制 -标准、程序或 指南的更改
QS9000 基础知识介绍
APQP
• 各阶段要求输入输出流程图,上阶段的输出为下阶段的输入:
输入
计划和 确定项目
产品设计和 开发验证
过程设计和 开发验证
产品与过 程确认
反馈、评定 和纠正措施
输出
我们所关注的!
9
February 15, 2019
产品设计和开发验证
-与产品质量策划相关的输出
• 新设备、工装和设施要求
产品质量策划小组应产品设计时应评审新设备和设施需求的可能性以保证新的设备和工装有能力 并及时供货,并要监测设施进度情况,以确保能在计划的试产前完工。
•
6
February 15, 2019
APQP
•
APQP(先期产品质量策划)是Advanced Product Quality Plan 的缩写,它是一种结构化的方法,用来确定和制定确保某产品使用 顾客满意所需的步骤与要求。 APQP反映的是一个产品从概念开发到量产整个过程的质量保证体 系,它包括计划和确定项目、产品设计和开发验证、过程设计和开 发验证、产品与过程确认和反馈,评定及纠正措施五个方面的要求 通过APQP的实施将引导资源,满意顾客、促进对所需更改的早期 识别、避免晚期更改和以最低的成本准时提供优质的产品
QS9000 标准最初由美国三大汽车公司Chrysler, Ford, GM 所创建, 旨在于向这三家汽车厂商及其OEM厂商提供量產及服務性材料與零件的 供應商所需建立的品質系统要求。 取得ISO9001标准证书的公司不意味着符合QS9000要求。 QS-9000適用於下列所有直接交貨給採用本文件OEM顧客的內部外部供應 商其場所: a) 量產材料, b) 量產或服務零件, c) 熱處理, 噴漆, 電 鍍或其他表面處理。 半导体业的厂商需满足Chrysler, Ford及Delco Electronics所發行的 半導體補充要求; 工模具与设备业的厂商需满足Chrysler, Ford及GM所 發行的工模具及設備(TE)補充要求。
- 1、下载文档前请自行甄别文档内容的完整性,平台不提供额外的编辑、内容补充、找答案等附加服务。
- 2、"仅部分预览"的文档,不可在线预览部分如存在完整性等问题,可反馈申请退款(可完整预览的文档不适用该条件!)。
- 3、如文档侵犯您的权益,请联系客服反馈,我们会尽快为您处理(人工客服工作时间:9:00-18:30)。
➢ 环境内部:温度、湿度、振动、亮度、清洁度的短期起伏变化。 ➢ 违背假定:稳定、正确操作 ➢ 仪器设计或方法缺乏稳健性,一致性不好 ➢ 应用错误的量具 ➢ 量具或零件变形,硬度不足 ➢ 应用:零件尺寸、位置、操作者技能、疲劳、观察误差(易读性、
视差)
13
再现性(Reproducibility)
由不同操作人员,采用相同的测量仪器,测量同一 零件的同一特性时测量平均值的变差(三同一异)
--第一版 1996年7月 质量体系评审(QSA-TE)—工具和设 备版
--第一版 1996年7月
6
QS-9000 质量体系文件
国际标准 ISO 9000
规定国际要求
顾客要求
QS-9000 生产件批准程序
公司特殊要求
规定顾客要求
手册 程序 作业指导书 其它文件
第一层次 确定途径及职责
第二层次 确定谁、做什么、 何时做
C1 33.50 3B3.05 32.808 32.80 3332.4.700 33.00 32.95 32.80 33.05 33.85
C2 33.55 3B3.00 32.809 32.80 3332.5.905 33.05 32.95 32.80 33.05 33.80
B
10
33.85
C
1
33.50
VS
Accurate and precise
precise but not accurate
Accurate but not precise
Not accurate or precise
10
测量系统的统计特性
Bias偏倚(Bias) Repeatability重复性(precision) Reproducibility再现性 Linearity线性 Stability稳定性
Master Value
Inspector A Inspector B Inspector C Inspector B Inspector A Inspector C
再现性
3.再现性不好的可能潜在原因
➢ 零件(样品)之间:使用同样的仪器、同样的操作者和方 法时,当测量零件的类型为A,B,C时的均值差。
3、MSA:《测量系统分析》手册英文 Measurement System Analysis首字母缩写。用于识别测量系统误差并提 前采取预防措施。
4、SPC:《统计过程控制》手册英文Statistical Process Control首字母缩写。用于识别过程变差,并提前采 取预防措施。
5、FMEA:《潜在失效模式及后果分析》手册英文 Potential Failure Mode and Effects Analysis的首字母 缩写,它包含设计和过程FMEA两个阶段,分别用DFMEA/PFMEA表示。用于提前识别设计缺陷而寻找预防性的改 进方案。
➢ 仪器之间:同样的零件、操作者、和环境,使用仪器 A,B,C等的均值差
➢ 标准之间:测量过程中不同的设定标准的平均影响 ➢ 方法之间:改变点密度,手动与自动系统相比,零点调
整、夹持或夹紧方法等导致的均值差
➢ 评价人(操作者)之间:评价人A,B,C等的训练、技术、技能和经 验不同导致的均值差。对于产品及过程资格以及一台手动测 量仪器,推蕮进行此研究。
五大工具的关系 :APQP是树干,其余为树枝
DFMEA PFMEA
SPC APQP
MSA
PPAP
3
QS-9000 简介
QS9000是美国三大汽车公司通用、福特、克莱斯勒及一些货车制造公司所 制定的供应商基本质量体系要求。
QS9000是美国克莱斯勒汽车公司 供方质量保证手册、福特汽车公司 Q101质量体系标准 和通用汽车公司 北美创优目标 及货车制造公司基本要求 的协调产物。
A2 33.60 3B3.00 32.805 32.95 3333.4.450 33.00 32.95 32.80 33.00 33.70
B1
33.55 3B3.05 32.806 32.80 3333.4.005 33.00 32.95 32.75 33.00 33.55
B2
33.55 3B2.95 32.757 32.75 3332.4.900 33.05 32.90 32.70 32.95 33.50
第三层次 回答如何做
顾客参考手册
产品质量先期策划和控制计划 失效模式和后果分析 测量系统分析 基础统计过程控制
第四层次 信息的即时记录诸如表格、名签、标签等, 一旦记录下来就可能成为质量记录
7
MSA
测量系统分析 Measurement System Analysis
8
测量系统变异性的影响
我们所观测制程的变异里包含了实际制程变异和测量系统的变异.假如测量 系统的变异比较大时会发生什么样的问题?
Master Value
重复性
2.重复性不好的可能原因
➢ 零件(样品)内部:形状、位置、表面加工、锥度、样品一 致性。
➢ 仪器内部:修理、磨损、设备或夹紧装置故障,质量差 或维护不当。
➢ 基准内部:质量、级别、磨损 ➢ 方法内部:在设置、技术、零位调整、夹持、夹紧、点密
度的变差
➢ 评价人内部:技术、职位、缺乏经验、操作技能或培训、 感觉、疲劳。
2.校准量具
B
5
33.40
3.测量,让三个测量人B对10个样6品的某项特33性.0进0 行测试,每个样品每人测量三次,将
数据填入表中。试B验时遵循以7 下原则:32.95
• 进盲行测随原机则的1:重对新BB1编0号个后样再品89测编,号避,免每主个3323观人..70偏测50 向完。第一轮后,由其他人对这10个样品
➢ 仪器设计或方法缺乏稳定性; ➢ 应用了错误的量具; ➢ 不同的测量方法—设置、安装、夹紧、
技术; ➢ 量具或零件随零件尺寸变化、变形; ➢ 环境影响—温度、湿度、震动、清洁度; ➢ 其它—零件尺寸、位置、操作者技能、
疲劳、读错。
15
稳定性(Stability)
稳定性
时间2
时间1
仪器需要校准,需要减少校准时间间隔 仪器、设备或夹紧装置的磨损 正常老化或退化 缺乏维护─通风、动力、液压、过滤器、腐 蚀、锈蚀、清洁
• 盲测原则2:三B个人之间1都0互相不知33道.5其5他人的测量结果。
4.计算:
B
1
33.55
零件
B
2
32.95
人員
1 B2
3 3 4 325.75 6
7
8
9
10
A1 33.65 3B3.00 32.854 32.85 3332.5.755 33.00 32.95 32.85 33.00 33.60
17
C
2
33.05
量具重复性和再现性数据表
作业者/量测次数
稳定性是测量系统在某持续时 间内测量同一基准或零件的单 一特性时获得的测量值总变差。
5.不稳定的可能原因
磨损或损坏的基准,基准出现误差 校准不当或调整基准的使用不当 仪器质量差─设计或一致性不好 仪器设计或方法缺乏稳健性 不同的测量方法─装置、安装、夹紧、技术 量具或零件变形 环境变化─温度、湿度、振动、清洁度 违背假定、在应用常量上出错 应用─零件尺寸、位置、操作者技能、疲劳、观察错误
➢ 不同的测量方法─设置、安装、夹紧、技术 ➢ 测量错误的特性 ➢ 量具或零件的变形 ➢ 环境─温度、湿度、振动、清洁的影响 ➢ 违背假定、在应用常量上出错 ➢ 应用─零件尺寸、位置、操作者技能、疲劳、观察错误
12
重复性(Repeatability)
指由同一个操作人员用同一种量具经多次测量同一 个零件的同一特性时获得的测量值变差(四同)
➢ 环境之间:在第1,2,3等时间段内测量,由环境循环引起的均 值差。这是对较高自动化系统在产品和过程资格中最常见的 研究。
➢ 违背研究中的假定 ➢ 仪器设计或方法缺乏稳健性 ➢ 操作者训练效果 ➢ 应用─零件尺寸、位置、观察误差(易读性、视差)
14
线性(Linearity)
較小的偏倚
基准值
在量具正常工作量程内的偏倚变化量
多个独立的偏倚误差在量具工作量程内的关 系是测量系统的系统误差构成
量測值
偏倚 無偏倚
量測平均值
線性(變化的線性偏倚)
(低量程)
4.线性误差的可能原因
基準值
➢ 仪器需要校准,需减少校准时间间隔; ➢ 仪器、设备或夹紧装置磨损; ➢ 缺乏维护—通风、动力、液压、腐蚀、清洁; ➢ 基准磨损或已损坏; ➢ 校准不当或调整基准使用不当; ➢ 仪器质量差;—设计或一致性不好;
5
QS-9000 内容
QS9000由11本手册组成:
QS-9000 质量体系要求 (QSR) --第三版 1998年3月
产品质量先期策划和控制计划 (APQP&CP)
--第一版 1994年6月 生产件批准程序(PPAP)
--第三版 2000年2月 潜在失效模式和后果分析参考手 册(FMEA)
--第二版 1995年2月 测量系统分析参考手册(MSA)
部分定义
1、APQP:《产品质量先期策划及控制计划》手册英文Advanced Product Quality Planning and Control Plan首字母的缩写。规定了产品开发的步骤。
2、PPAP:《生产件批准程序》手册英文Production Part Approval Process首字母的缩写。用来确保组织已经 完全理解并有能力长期满足顾客要求
16
A
8
32.80
量测系统分析AA法---均910值-极3333差..0700法
B
1
33.55
1.选择三个测量人(AB, B,C)和210个测量样33品.0。5