应力腐蚀及环境氢脆测试方法
应力腐蚀和氢脆

二、应力腐蚀产生的条件
▪ (1)只有在拉伸应力作用下才能引起应力腐蚀开 裂(近年来,也发现在不锈钢中可以有压应力引起)。 这种拉应力可以是外加载荷造成的应力,但 主要是各种残余应力,如焊接残余应力、热处理 残余应力和装配应力等。 据统计,在应力腐蚀开裂事故中,由残余应 力所引起的占80%以上,而由工作应力引起的则 不足20%。
▪ 控制温度,使材料工作在该体系的临界温度以下, 以抑制SCC的发生。
▪ 采用外加电流阴极保护法也可以防止SCC的发生, 而且在裂纹形成后还可使其停止发展。
采用电化学保护
▪ 一般采用阴极保护法,但高强度钢或其它 氢脆敏感的材料不宜采用。
F/A-18舰载机
SCC像晶间腐蚀一样,能导致飞机结构的临界载荷破裂失效。 在飞机制造时,安装和装配应力也应该消除。材料选择和过程 也能预防SCC,选择较小SCC倾向的铝合金是关键。必须采用 经过长时间时效处理、延展的和消除了应力的铝合金。同样, 利用开发的用于减少应力腐蚀开裂的恰当的铝回火热处理也很 重要。
▪ 应力腐蚀的主裂纹扩展时常有分枝。但不要形成绝对化 的概念,应力腐蚀裂纹并不总是分枝的。
▪ 应力腐蚀破坏的断口,其颜色灰暗,表面常有腐蚀产物 (泥状花样),或腐蚀坑。而疲劳断口的表面,如果是 新鲜断口常常较光滑,有光泽。
▪ 应力腐蚀引起的断裂可以是穿晶断裂,也可以是沿晶断 裂。如果是穿晶断裂,其断口是解理或准解理的,其裂 纹有似人字形或羽毛状的标记。
枯枝状
泥状花状
奥氏体不锈钢应力腐 蚀断口
1Cr18Ni9Ti钢应力腐蚀的解理断口(SEM)
a) 解理断口Βιβλιοθήκη b) 扇形状或羽毛状的痕迹
应力腐蚀及环境氢脆测试方法

KISCC可以实测得到,也可以通过计算方法求 得。一般,通过理论方法求得KISCC十分麻烦,工 程上多通过实测得到。
7、裂纹扩展速率da/dt及裂纹扩展速度v
d、恒位移中心预裂试样
4、恒K1试样
a、锥梯形试样
b、与(w-a)无关的锥梯形试样
c、与(w-a)有关的锥梯形试样
5、KISCC及da/dt的测试步骤
a、试样的准备 应力腐蚀破裂试样的截取,要考虑
到母材的轧制方向,不同取向的试样, 试验结果不一样。
b、平面应变的条件是 B,a,(W-a)2.5(KISCC/s)2
b、三点弯曲试样
恒应变三点弯曲 试样及试验装置
恒载荷三点弯曲试验
1-棒;2-试样; 3-荷重
C、四点弯曲试样
恒应变四点弯曲试样及试样架
恒应变四点弯曲试样及试样架
1-棒;2-试样;3-荷重源自d、双弯梁3、U形弯曲试样
U形试样 弯曲过程
常用的U形试样
1-焊接或缚紧;2-焊接;3-夹紧前;4-受力试样
• 应力腐蚀试验的试样是浸在腐蚀介质中的,因此对 于裂纹扩展情况的观察和测量都受到限制。
• 应力腐蚀试验的微区电化学过程的测试,还存在技 术上的困难,如微区的电极电位,微区的极化曲线 等等的测量,目前还相当困难。
• 应力腐蚀试验的影响因素很多,往往试验结果数据 很分散,而且重现性较差,因此处理很困难。
损坏情况:运转2月后发现泄漏,运转3个月检修时发现70多根 管子 破裂。破裂多发生在高温侧管板缝隙附近。 分析检验:裂纹从管外壁产生,向内壁扩展,属穿晶型应力 腐蚀裂纹特征。断口扫描电镜发现,破裂是典型的脆性解 理断裂,是由氯化物应力腐蚀造成的。
Q345R(R-HIC)中HIC氢致开裂分类(氢脆和氢腐蚀)

Q345R(R・HIC)中HIC 试验1、氢致开裂(HIC)试验简介氢致开裂(HIC)英文全称是:Hydrogen induced crackingo硫化氢是石油和天然气中最具腐蚀作用的有害介质之一,在天然气输送过程中,硫化氢对输送管线的应力腐蚀占很大比重。
在湿硫化氢环境中使用时,能导致碳钢内部出现氢鼓泡(HB)、氢致开裂(HIC)和应力导向的氢致开裂(SOHIC)。
管材在含硫化氢等酸性环境中,因腐蚀产生的氢侵入钢内而产生的裂纹称为氢致开裂(HIC)国标GB/T8650-2006《管线钢和压力容器钢抗氢致开裂评定方法》,规定了管线钢和压力容器钢板在含有硫化物水溶液的腐蚀环境中,由于腐蚀吸氢引起的HIC的评定方法。
美标NACE TM 0284管道、压力容器抗氢致开裂钢性能评价的试验方法,规定了HIC氢致开裂的评定方法。
2、氢致开裂分类(氢脆和氢腐蚀)1)氢脆:各种情况下产生的氢原子直接渗透到钢内部后,使钢晶粒间原子结合力降低,造成钢材的延伸性、端面收缩率降低,强度也发生变化。
在裂纹尖端有与阳极反应相应的阴极反应发生。
所生成的氢或加工氢进入钢中引起氢致开裂。
2)氢腐蚀:氢与钢中的碳化物发生反应产生甲烷,甲烷气体不能从钢中扩散出去,聚集在晶粒间形成局部高压,造成应力集中,进而使钢材产生微裂纹或鼓泡。
3、破坏类型在石油天然气行业和石化行业中,如果在湿H2S环境下选用碳钢或低合金钢,那么钢板会发生很严重的脆化。
这种脆化的机理是:H2s与钢材表面发生腐蚀反应产生氢,而后氢又被钢材吸收导致氢脆。
对于低合金钢来说,这种破坏可分为以下几种类型:1)氢诱导开裂(HIC)。
HIC不需要应力就可以在钢材内部产生并传播。
2)硫化物应力开裂(SSC) ° SSC主要出现在硬度高的区域,如焊缝区。
3)应力方向氢诱导开裂(SOHIC)o事实上,SOHIC可被看作是HIC和SSC共同作用的结果。
4)氢致延迟裂纹:容器在焊接过程中,焊接材料中水分或油污在电弧高温作用下分解产生氢,这些氢一部分进入熔融的焊缝金属中,当焊缝冷却时来不急扩散出去形成局部高压而导致焊缝出现微裂纹的现象。
氢脆试验判定标准

氢脆试验判定标准氢脆是一种由于内应力能量集中或过大而导致的金属材料的脆性断裂现象。
这种现象在工业生产中具有重要的意义,因为它可能导致材料的失效和事故发生。
为了准确判定氢脆现象的出现,制定一份科学严谨的氢脆试验判定标准是十分必要的。
一、试验材料的选择进行氢脆试验时,首先需要选择合适的试验材料。
一般来说,常用的试验材料包括钢、铁、铜等金属材料。
选择试验材料时,需要考虑其应力应变特性、化学成分和微观组织等因素,以确保试验结果具有代表性。
二、试验方法的选择确定试验方法是进行氢脆试验的重要步骤之一。
庆丰氢脆试验方法是目前应用最广泛的一种方法之一。
该方法通过对材料进行腐蚀处理,使其表面产生氢气,并通过施加应力来观察材料是否发生氢脆断裂。
三、试验条件的确定在进行氢脆试验之前,还需要确定试验的环境条件和试验参数。
环境条件包括气体氛围、温度和湿度等因素。
常用的气体氛围包括干燥氢气、氮气等。
温度一般选择在室温到高温之间,具体根据试验要求和试验材料来确定。
湿度则需要根据试验要求来调整。
四、试验过程的要求在进行氢脆试验时,需要严格控制试验过程中的环境条件和试验参数。
还要采取有效的措施,防止试验过程中的干扰因素对试验结果的影响。
为了保证试验结果的准确性和可重复性,还要对试验仪器设备进行校准和验证,确保其工作状态良好。
五、试验结果的判定根据氢脆试验的结果,对材料的氢脆程度进行判定。
一般来说,氢脆程度可以通过断裂面的形貌和试验后材料的性能损失程度来评估。
氢脆断裂面呈现出很脆的特征,且材料性能出现明显下降,即可判定材料发生了氢脆现象。
六、试验结果的记录和分析对于氢脆试验的结果,需要进行详细的记录和分析。
记录试验过程中的环境条件、试验参数和试验结果等信息,并绘制曲线或表格进行分析。
还需要对试验结果进行比对和统计,以获取更全面的试验结论。
七、试验结果的应用根据氢脆试验的结果,对材料的使用和应用进行合理安排。
如果试验结果表明材料具有较高的抗氢脆能力,那么可以继续使用。
应力腐蚀和氢脆

分子态
化合态
▪ 在一般情况下,氢以间隙原子状态固溶在金属中, 对于大多数工业合金,氢的溶解度随温度降低而 降低。
▪ 氢在金属中也可通过扩散聚集在较大的缺陷(如空 洞、气泡、裂纹等)处以氢分子状态存在。
▪ 氢还可能和一些过渡族、稀土或碱土金属元素作 用生成氢化物,或与金属中的第二相作用生成气 体产物,如钢中的氢可以和渗碳体中的碳原子作 用形成甲烷等。
▪ 解放初期黄铜子弹壳开裂现象:原因是润滑用肥皂水中 含微量铵离子。
二、应力腐蚀产生的条件
▪ (1)只有在拉伸应力作用下才能引起应力腐蚀开 裂(近年来,也发现在不锈钢中可以有压应力引起)。 这种拉应力可以是外加载荷造成的应力,但 主要是各种残余应力,如焊接残余应力、热处理 残余应力和装配应力等。 据统计,在应力腐蚀开裂事故中,由残余应 力所引起的占80%以上,而由工作应力引起的则 不足20%。
▪ 当KⅠ值降低到某一临界值(图中为38MPa.m1/2) 时,应力腐蚀开裂实际上就不发生了。这一KⅠ 值称之为应力腐蚀临界场强度因子,也称应力
腐蚀门槛值,以 KⅠSCC表示(SCC表示应力腐蚀 断裂)。
应力腐蚀临界应力场强度因子KISCC
✓试样在特定化学介质中不发生应力腐蚀断裂的 最大应力场强度因子,也称为应力腐蚀门槛值。 ✓表示含有宏观裂纹的材料在应力腐蚀条件下的 断裂韧度。 ✓一定的材料与介质,KISCC值恒定。是金属材料 的一个力学性能指标。
▪ 钛合金(Ti-8Al-1Mo-1V)的预制裂纹试祥在恒载荷作用下,于 3.5%Nacl水溶液中进行应力腐蚀试验的结果。
Ti-8Al-1Mo-1V预制裂纹试祥的KⅠ-tf曲线
▪ 该合金的KⅠc=100MPa.m1/2,在3.5%盐水中, 当初始KⅠ值仅为40 MPa.m1/2时,仅几分钟试样 就破坏了。如果将KⅠ值稍微降低,则破坏时间 可大大推迟。
检测氢脆的方法
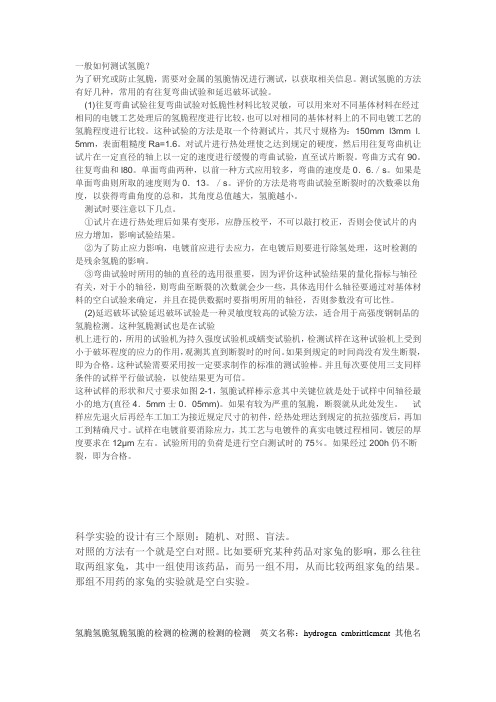
一般如何测试氢脆?为了研究或防止氢脆,需要对金属的氢脆情况进行测试,以获取相关信息。
测试氢脆的方法有好几种,常用的有往复弯曲试验和延迟破坏试验。
(1)往复弯曲试验往复弯曲试验对低脆性材料比较灵敏,可以用来对不同基体材料在经过相同的电镀工艺处理后的氢脆程度进行比较,也可以对相同的基体材料上的不同电镀工艺的氢脆程度进行比较。
这种试验的方法是取一个待测试片,其尺寸规格为:150mm×l3mm×l. 5mm,表面粗糙度Ra=1.6。
对试片进行热处理使之达到规定的硬度,然后用往复弯曲机让试片在一定直径的轴上以一定的速度进行缓慢的弯曲试验,直至试片断裂。
弯曲方式有90。
往复弯曲和l80。
单面弯曲两种,以前一种方式应用较多,弯曲的速度是0.6./s。
如果是单面弯曲则所取的速度则为0.13。
/s。
评价的方法是将弯曲试验至断裂时的次数乘以角度,以获得弯曲角度的总和,其角度总值越大,氢脆越小。
测试时要注意以下几点。
①试片在进行热处理后如果有变形,应静压校平,不可以敲打校正,否则会使试片的内应力增加,影响试验结果。
②为了防止应力影响,电镀前应进行去应力,在电镀后则要进行除氢处理,这时检测的是残余氢脆的影响。
③弯曲试验时所用的轴的直径的选用很重要,因为评价这种试验结果的量化指标与轴径有关,对于小的轴径,则弯曲至断裂的次数就会少一些,具体选用什么轴径要通过对基体材料的空白试验来确定,并且在提供数据时要指明所用的轴径,否则参数没有可比性。
(2)延迟破坏试验延迟破坏试验是一种灵敏度较高的试验方法,适合用于高强度钢制品的氢脆检测。
这种氢脆测试也是在试验机上进行的,所用的试验机为持久强度试验机或蠕变试验机,检测试样在这种试验机上受到小于破坏程度的应力的作用,观测其直到断裂时的时间。
如果到规定的时间尚没有发生断裂,即为合格。
这种试验需要采用按一定要求制作的标准的测试验棒。
并且每次要使用三支同样条件的试样平行做试验,以使结果更为可信。
应力腐蚀及环境氢脆测试方法

大量事故分析表明,不论是胀-焊还是仅胀未焊连接,不锈钢管束应力腐蚀裂纹多位于胀与未胀过渡区。
02
这与滚胀连接时,局部变形,受有较大的纵向残余拉应力有关。实测表明,此处纵向应力一般高达相当于屈服强度的数值。
03
不锈钢管与管板胀接部位的横向裂纹
0Cr15Ni75Fe耐蚀合金管材与管板胀接后, 滚胀区内表面残余应力分布
d、恒位移中心预裂试样
4、恒K1试样 a、锥梯形试样
b、与(w-a)无关的锥梯形试样
c、与(w-a)有关的锥梯形试样
KISCC及da/dt的测试步骤
a、试样的准备 应力腐蚀破裂试样的截取,要考虑到母材的轧制方向,不同取向的试样,试验结果不一样。
1
b、平面应变的条件是
2
B,a,(W-a)2.5(KISCC/s)2
试样破裂百分比 用应力腐蚀试样在特定条件下发生破裂和未发生破裂的百分数来表示敏感性。
5、应力腐蚀破裂敏感系数 在特定条件下,把应力腐蚀破裂时间的倒数,称为破裂敏感系数。当破裂敏感系数越大时,材料的应力腐蚀敏感性也越大。
Ni对18%Cr钢和合金的 SCC倾向影响示意图 1-穿晶破裂 2-晶间破裂
应力腐蚀破裂临界应力强度因子KISCC
01
KISCC系指在应力腐蚀破裂条件下的临界应力强度因子。KISCC的实用价值在于它可以预示材料在特定环境中抗应力腐蚀破裂的能力和使用寿命以及是否处于安全使用状态。 KISCC可以实测得到,也可以通过计算方法求得。一般,通过理论方法求得KISCC十分麻烦,工程上多通过实测得到。
单击添加标题
K1-tF曲线
01
五、慢应变率法试验
SERT型慢应变应力腐蚀试验机
慢应变率法,又称恒应变率法,它是将拉伸试样放在特定的介质中,然后在慢应变率试验机上,用一定的、缓慢的应变速度进行拉伸试验,直到拉断。
应力腐蚀和氢脆
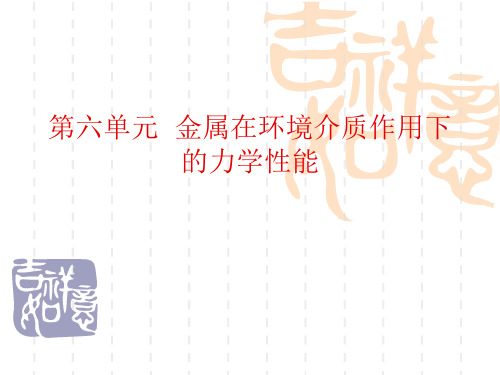
在纵向断面上,裂纹呈现近似圆形或椭圆形的银白色斑点, 故称白点;在横断面宏观磨片上,腐蚀后则呈现为毛细裂 纹,故又称发裂。
10CrNiMoV钢锻材调质后纵断面上的白点形貌
如炼油过程中的一些加氢反应装置;石油化工生产
过程中的甲醇合成塔等。
二、氢的来源
按照氢的来源可将氢脆分为内部氢脆和环境氢脆。
⑴内部氢脆:材料在使用前内部已含有足够的氢
并导致了脆性,它可以是材料在冶炼、热加工、 热处理、焊接、电镀、酸洗等制造过程中产生。
严格控制电镀工艺,镀后还要通过 对电镀件长时间的烘烤,使游离状 的氢得以释放,减轻对镀件产品的 影响。
M——裂纹截面上的弯矩, M=F·。 L B——试样厚度。 W—— 试样宽度。 a—— 裂纹长度。
1/ 2
4.12M KI 3/ 2 BW
1 3 a a3
能力知识点3 提高应力腐蚀抗力的措施
降低和消除应力
在加工(如热处理、焊接、电镀等)和装配过程中, 应尽量避免产生残余拉应力,或者在加工中采取 必要的消除应力措施。 制备和装配时尽量使结构具有最小的应力集中系 数,并使其与介质接触部分具有最小的残余拉应 力。
三、氢脆的类型和特点
氢可通过不同的机制使金属脆化,因氢脆的种类 很多,现将常见的几种氢脆现象从其特征简介如 下。
1.氢蚀
这是由于氢与金属中的第二相作用生成高压气体,使基体 金属晶界结合力减弱而导致金属脆化。 如在石油高压加氢及液化石油气的设备中,在300~ 500℃时,由于氢与钢中的碳化物作用生成高压的CH4气 泡,当气泡在晶界上达到一定密度后,金属的塑性将大幅 度降低。 这种氢脆现象的断裂源产生在工件与高温、高压氢气相接 触的部位。 宏观断口形貌:呈氧化色,颗粒状;微观:晶界明显加宽, 呈沿晶断裂。
- 1、下载文档前请自行甄别文档内容的完整性,平台不提供额外的编辑、内容补充、找答案等附加服务。
- 2、"仅部分预览"的文档,不可在线预览部分如存在完整性等问题,可反馈申请退款(可完整预览的文档不适用该条件!)。
- 3、如文档侵犯您的权益,请联系客服反馈,我们会尽快为您处理(人工客服工作时间:9:00-18:30)。
K1-tF曲线
五、慢应变率法试验
慢应变率法,又称恒 应变率法,它是将拉伸试 样放在特定的介质中,然 后在慢应变率试验机上, 用一定的、缓慢的应变速 度进行拉伸试验,直到拉 断。
SERT型慢应变应力腐蚀试验机
六、应力腐蚀案例
不锈钢管与管板胀接部位的横向裂纹
管与管板连接方式很多,在应 力腐蚀工程事故分析中,多遇到胀 -焊连接,仅胀未焊连接还仅焊未 胀连接三种。部分胀-焊连接方式 见图。 大量事故分析表明,不论是胀 -焊还是仅胀未焊连接,不锈钢管 束应力腐蚀裂纹多位于胀与未胀过 渡区。 这与滚胀连接时,局部变形, 受有较大的纵向残余拉应力有关。 实测表明,此处纵向应力一般高达 相当于屈服强度的数值。
典型的da/dt-K曲线(K为应力强度因子)
8、破裂电位范围和临界破裂电位
大量的例子表明,对于某一特定体系应力腐蚀 破裂只发生于一定的电位以上,低于这个电位则不 会发生,这个电位值称为应力腐蚀破裂临界电位。
在沸腾的42%MgCl2 溶液中,18-8Ti 不锈钢的电位-断裂 时间关系
二、试样及测试方法的类型
b、三点弯曲试样
恒应变三点弯曲 试样及试验装置
恒载荷三点弯曲试验
1-棒;2-试样; 3-荷重
C、四点弯曲试样
恒应变四点弯曲试样及试样架
恒应变四点弯曲试样及试样架
1-棒;2-试样;3-荷重
d、双弯梁
3、U形弯曲试样
U形试样 弯曲过程
常用的U形试样
1-焊接或缚紧;2-焊接;3-夹紧前;4-受力试样
水中Cl-浓度对 0Cr18Ni10钢SCC 敏感性的影响
5、应力腐蚀破裂敏感系数
在特定条件下,把应力腐蚀破裂时间的倒 数,称为破裂敏感系数。当破裂敏感系数越大时, 材料的应力腐蚀敏感性也越大。
Ni对18%Cr钢和合金的 SCC倾向影响示意图 1-穿晶破裂 2-晶间破裂
6、应力腐蚀破裂临界应力强度因子KISCC
67管与管板连接 及管上应力腐蚀裂纹示意图
管板缝隙处破裂的管子
案例二、化肥厂冷却器管的破损
材质:00Cr18Ni10 尺寸: ø 19× 2
工作环境:管内-高温CO2 ;管外-冷却水 损坏情况:运转不到半年,发生多处破损事故。 分析检验:裂纹以横裂为主。裂纹由外壁产生,向内壁扩展,属典 型的穿晶型应力腐蚀裂纹。
应力腐蚀裂纹扩展速率da/dt,是评定金属材料 应力腐蚀破裂敏感性的重要指标。一般来说, da/dt越大,材料的应力腐蚀敏感性也越大。已经 产生应力腐蚀裂纹的典型的da/dt-K曲线如下图。
从图中看出,它分为三个阶段:(1)K值超过KISCC 达到某一门坎值KTH,裂纹随K值的增加迅速扩展, da/dt 与K基本呈线性关系;(2)当K增加到某一数值时,这时的 裂纹扩展速度达到某一稳定值,裂纹扩展速率基本是一个 常数, da/dt与K几乎无关;(3)当K继续增加到某一数值 时,随着K增加, da/dt迅速增加,当K增加到KIC,材料发 生机械失稳断裂。
2、恒负载KI增加试样
a、单缺口恒拉伸预制试样(SEL试样)
b、恒负载三点弯曲试样(3PB试样)
c、恒负载四点弯曲试样(4BP试样)
d、恒负载悬臂弯曲试样(CB试样)
e、恒负载中心预制裂纹试样(CC试样)
f、恒负载表面预制裂纹
g、双缺口预裂纹拉伸试样
h、圆棒形预裂纹拉伸试样
i、紧凑拉伸试样(CT)
三、应力腐蚀及环境氢脆敏感性常用 测试方法简介
1、拉伸试验
a、恒载荷拉伸试样
拉伸试验加载机构示意图
1、应力传感器;2、试样; 3、腐蚀锅;4、砝码
弹簧加载拉伸试验
1、弹簧;2、腐蚀锅; 3、试样
b、恒变形拉伸试样
2、弯曲试验
a、二支点弯曲试样
二支点弯曲试样及试样架
H可调试样架 (b)及应 变测量装置(a)
在125℃沸腾的MgCl2和CaCl2中,pH值 对0Cr18Ni10钢应力腐蚀破裂时间的影响
2、临界应力σSCE
金属材料在特定的腐蚀环境中,应力水平越 高,破裂时间越短;应力水平越低,破裂时间 越长。 原则上说,当应力水平低于某一数值时,不 会发生应力腐蚀破裂。该应力为临界应力,它 是评定应力腐蚀破裂敏感性的重要指标。
0Cr15Ni75Fe耐蚀 合金管材与管板 胀接后, 滚胀区 内表面残余应力 分布
案例:CO2高压热交换器管的破裂
材质:0Cr18Ni10 尺寸及结构:ø 19× 1.6,共232根,每根长 8.5米。管与管板采用胀焊连接。 工作环境: 管内:湿CO2 。进口温度:180℃ ; 出口温度40~50℃ ;压力:80~90kgf。 管外:冷却;出口温度:80 ℃ ; 压力:4 kgf。 损坏情况:运转2月后发现泄漏,运转3个月检修时发现70多根 管子 破裂。破裂多发生在高温侧管板缝隙附近。 分析检验:裂纹从管外壁产生,向内壁扩展,属穿晶型应力 腐蚀裂纹特征。断口扫描电镜发现,破裂是典型的脆性解 理断裂,是由氯化物应力腐蚀造成的。
KISCC系指在应力腐蚀破裂条件下的临界应力强 度因子。 KISCC 的实用价值在于它可以预示材料在 特定环境中抗应力腐蚀破裂的能力和使用寿命以 及是否处于安全使用状态。 KISCC 可以实测得到,也可以通过计算方法求 得。一般,通过理论方法求得 KISCC 十分麻烦,工 程上多通过实测得到。
7、裂纹扩展速率da/dt及裂纹扩展速度v
b、焊接圆盘试样
9、管状试验
内部压力下应力腐蚀试验的管 状试样和固定架
1-向管内加压应力及腐蚀剂 2-焊接
10、锅炉碱脆模拟试验装置
锅炉碱脆试验装置
1-锅炉水进;2-锅炉水出;3-通过锅炉水到试样;4-浓缩液; 5-蒸汽;6-试样;7-压紧板;8-垫片;9-夹紧螺母;10-调节螺钉
11、挂片试验
3、恒位移K1减小试样
a、紧凑拉伸型试样
孔的中心与试样中心偏差在1o以内 缺口中心与试样中心偏差在1.27mm以内
与(w-a)无关的单缺口恒位移紧凑拉伸试样
与(w-a)有关的单缺口恒位移紧凑拉伸试样
b、WOL-T试样
c、双悬臂梁试样(DCB试样)
1-疲劳裂纹;2-应力腐蚀破裂; 3-机械失稳破裂
各种工业用不锈钢在MgCl2 介质中对应力腐蚀破裂的敏感性
3.破裂深度hf
应力腐蚀破裂的敏感性,还可以用应力腐蚀裂 纹的深度,或平均裂纹深度,或是最大裂纹深度 来表示。 在一定条件下,应力腐蚀裂纹深度越大,应 力腐蚀破裂的敏感性也越大。
4、试样破裂百分比
用应力腐蚀试样在特定条件下发生破裂和未 发生破裂的百分数来表示敏感性。
应力腐蚀及环境氢脆测试方法
一、应力腐蚀及环境氢脆敏感性的判据
1、开裂时间tc及断裂时间Tf
金属材料在不同的应力状态下和不同的介质 环境中的开裂或断裂时间;或者在一定应力状态 下和一定的介质环境中,可以用应力腐蚀及环境 氢脆断裂或开裂的时间来表示某种金属的应力腐 蚀及环境氢脆的敏感性。 一般来说,断裂或开裂时间越短,应力腐蚀 破裂及环境氢脆的敏感性越大。
海水挂片试验装置 1-气箱;2-试片架;3-试片;4-绳;5-键;6-水线
四、KISCC及da/dt测试方法
1、试样分类
KISCC的测试方法一般采用缺口预制裂纹试样。 根据开缺口及预制裂纹的情况可分为:单缺口预制 裂纹试样;双缺口预制裂纹试样;表面预制裂纹试 样;圆周预制裂纹试样等。
SCC预制 裂纹试样 分类
4、C形环试验
C形环试样 取样的方法 (a)-管材 (b)-棒材 (c)-板材
C形环试样受力方法
5、O形环试验
O形环试样及加力塞子
(a)O形环试样;(b)加载塞子
6、叉形试验
调音叉试样
7、薄板预变形试验
预变形薄板试样
8、焊接接头应力腐蚀试验
a、焊接弯梁试样
焊接弯梁试样组合件
1-焊接拉伸面;2-焊接压缩面;3-焊接根部
d、恒位移中心预裂试样
4、恒K1试样
a、锥梯形试样
b、与(w-a)无关的锥梯形试样
c、与(w-a)有关的锥梯形试样
5、KISCC及da/dt的测试步骤
a、试样的准备 应力腐蚀破裂试样的截取,要考虑 到母材的轧制方向,不同取向的试样, 试验结果不一样。
b、平面应变的条件是 B,a,(W-a)2.5(KISCC/σs)2 试样尺寸只有满足上述条件,测得的KISCC才 是有效的。
1、试样类型
• 光滑试样 • 缺口试样 • 缺口预制裂纹试样
2、测试方法分类
• 恒载荷法--试验过程中载荷不变; • 恒应变法--试验过程中加一恒定的应变; • KISCC及da/dt测定法; • 慢应变法; • 恒应力法,或称恒K1法。
3、应力腐蚀破裂试验中的困难
• 应力腐蚀试验的 试验周期一般较长 ,要保持试验介 质的浓度、温度等试验条件不变,是比较困难的, 而这些都将影响试验结果,同时如何缩短试验周期, 加速应力腐蚀破裂过程,也是需要解决的问题。 • 应力腐蚀试验的试样是浸在腐蚀介质中的,因此对 于裂纹扩展情况的观察和测量都受到限制。 • 应力腐蚀试验的 微区电化学过程的测试,还存在技 术上的困难, 如微区的电极电位,微区的极化曲线 等等的测量,目前还相当困难。 • 应力腐蚀试验的 影响因素很多 ,往往试验结果数据 很分散,而且重现性较差,因此处理很困难。
C、试样的加工
试样的加工,要求保证 尺寸公差和表面光洁度, 缺口的加工一般要求在线 切割机上进行,预制疲劳 裂纹在高频疲劳试验机上 进行,预制疲劳裂纹的走 向和试样中心的偏差一般 不超过10o。
d、试验步骤 ——以悬臂梁弯曲的试验步骤为例
• 将试样按要求装置在试验机上,首先在空气中逐渐加 大载荷,直至裂纹失稳扩展断裂,然后求KIC。 • 降低载荷,使试样的初始应力强度因子KIi低于KIx的 情况下,在特定腐蚀介质中试验,经过一段时间,试 样断裂;然后再降低KIi ,当KIi降低到某一极限值,试 样不再发生应力腐蚀断裂,这个极限值是KISCC。 • 用差动变压器或位移传感器测量加载点的位移δ ,求 出裂纹的长度a,绘制a-t曲线,根据a-t ,可以求出da/dt。