不锈钢器皿的深拉伸工艺与模具设计
不锈钢拉伸模设计要点

不锈钢拉伸模设计要点学习不锈钢拉伸模设计这么久,今天来说说关键要点。
首先我理解,不锈钢这种材料有自己独特的性质,强度高韧性好。
这就决定了在拉伸模设计的时候,模具的材料得够硬。
我之前老是想不明白为什么有的模具用一段时间就不行了,后来才总结出就是因为一开始没选对模具材料。
就像你拿个很单薄的塑料铲子想去挖硬土一样,肯定没几下就坏了。
所以啊,像铬钼合金钢这种硬度比较高的材料就比较适合用来做不锈钢拉伸模的材料。
模具的间隙也超级重要。
这个间隙的大小可是很有讲究的。
我之前记错了这个参数,结果做出的拉伸件不是拉破了就是起皱了。
不锈钢的延展性虽然还可以,但是没调好间隙,它也没法完美的成型。
我总结这个间隙啊,得根据不锈钢的厚度来,一般来说是不锈钢板厚度的10%到20%之间。
打个比方,就像我们穿鞋子,鞋子太大就容易不跟脚(就好比拉伸件起皱),鞋子太小又会挤脚(类似拉伸件拉破)。
对了还有个要点,拉伸模的圆角半径。
这个圆角如果设计不好,很容易让不锈钢在拉伸过程中应力集中,从而出现破裂等问题。
我理解这个圆角半径应该是要根据每个拉伸件的具体形状和拉伸的深度等因素综合设计的。
我就碰到过一个比较大深度的拉伸件的设计,一开始不管怎么调试模具,拉伸件底部老是破裂,后来我就着重调整了圆角半径,才解决这个问题。
还有脱模的设计也不能疏忽。
不锈钢相比一些软质材料,摩擦力比较大,如果脱模设计的不好,拉伸件就很难顺利从模具里取出来。
我之前就想当然地按照设计普通材料模具的脱模方式来做不锈钢拉伸模的脱模设计,结果就耽误了不少时间。
现在我总结就是要考虑加一些脱模斜度或者脱模剂等辅助脱模的设计。
学习资料的话,我觉得《冲压模具设计手册》就很不错,里面有很多关于拉伸模具的通用知识,也有一些不锈钢拉伸模具设计的相关要点。
还有一些行业的论坛也很有用,像“模具之家”论坛,能跟一些有经验的老师傅交流他们在实际设计不锈钢拉伸模中的心得,那可真的是能让自己少走很多弯路啊!我自己还一直在学习,感觉很多知识都是要不断在实践中才能掌握得更好的。
不锈钢拉伸工艺

不锈钢拉伸工艺一、引言不锈钢是一种具有优异耐腐蚀性能的金属材料,广泛应用于航空航天、汽车制造、建筑等领域。
而不锈钢拉伸工艺是将不锈钢材料通过拉伸加工,使其形成所需的形状和尺寸。
本文将从不锈钢的特性、拉伸工艺的原理和具体步骤等方面进行阐述。
二、不锈钢的特性不锈钢具有良好的耐腐蚀性、高强度和韧性,是一种理想的结构材料。
其主要成分为铁、铬、镍和少量的其他元素。
其中,铬的加入可以形成一层致密的氧化膜,防止氧气侵蚀金属内部,从而起到防腐蚀的作用。
不锈钢的高强度和韧性使其具有较好的可塑性,适合进行拉伸加工。
三、拉伸工艺的原理拉伸工艺是通过施加力使不锈钢材料发生塑性变形,从而改变其形状和尺寸。
拉伸过程中,外力作用下,材料内部的晶界滑移和形变使其逐渐延长。
不锈钢的高韧性使其具有较高的延伸率,能够承受较大的拉伸应力。
拉伸过程中,不锈钢材料会发生颈缩现象,即在某一局部出现断裂,但整体仍能保持一定的强度。
四、拉伸工艺的步骤1. 材料准备:选择合适的不锈钢材料,并进行切割或加工成所需形状和尺寸。
2. 加热处理:不锈钢材料在拉伸前需要进行加热处理,以提高其塑性和可塑性。
常用的加热方式有电阻加热、感应加热等。
3. 拉伸装置:将加热后的不锈钢材料固定在拉伸装置上,根据需要施加适当的拉伸力。
4. 拉伸过程:通过拉伸装置施加外力,使不锈钢材料发生塑性变形,逐渐延长。
5. 检测与调整:在拉伸过程中,需要不断检测拉伸力和变形情况,根据需要进行调整,以确保拉伸效果。
6. 冷却处理:拉伸完成后,对不锈钢材料进行冷却处理,使其恢复到室温状态。
五、工艺参数的选择在不锈钢拉伸工艺中,工艺参数的选择对于成品的质量和性能具有重要影响。
常见的工艺参数包括拉伸速度、拉伸力、加热温度和冷却速度等。
拉伸速度的选择应根据不锈钢材料的性能和尺寸来确定,过快的拉伸速度可能导致材料脆性增加,而过慢则会增加拉伸时间。
拉伸力的选择应根据材料的强度和韧性来确定,过大的拉伸力可能导致断裂,而过小则会影响拉伸效果。
不锈钢器皿的深拉伸工艺与模具设计

不锈钢器皿的深拉伸工艺与模具设计摘要:不锈钢器皿在我国日常生活中有着诸多应用,特别是随着我国机械制造业不断发展,不锈钢器皿依靠其诸多优势在我国市场上站稳脚跟。
可以说,不锈钢器皿是劳动智慧与科学工艺发展共同结合的结果,在实际应用的过程中有着诸多优势。
在进行不锈钢器皿生产的过程中,需要经历诸多生产阶段,其中最为常见的生产工艺就是深拉伸工艺。
不锈钢在形成器皿的过程中,需要通过科学的模具辅助深拉伸工艺的实施与应用,进而实现不锈钢器皿的生产。
在长期的生产与加工中,不锈钢器皿由于其富有个性、节能环保等应用备受群众的喜爱。
因此,如果进一步优化不锈钢器皿的深拉伸工艺就成为诸多不锈钢器皿制造企业当前工作的主要目标。
所以,本文主要针对不锈钢器皿深拉伸工艺展开研究,并对模具的设计进行分析。
关键词:机械制造;模具设计;冲压形成不锈钢器皿是其他材质器皿的主要替代品,由于其较高的安全性及群众消费理念的变化,不锈钢器皿在当前市场上所占有的份额比重较大,在一定程度上取代了很多其他材质的器皿。
不论是在国内还是在国外,不锈钢器皿市场潜力巨大,很多企业均在通过优化工艺展开市场份额的抢占工作。
其中,深拉伸工艺就是不锈钢器皿在生产过程中需要应用到工艺技术之一,在目前的器皿生产中占有较大的比重。
1拉伸工艺的具体设计1.1毛坯尺寸计算在本次研究中,主要以不锈钢材质的琴音叫盖水壶作为研究对象。
不锈钢琴音叫盖水壶的主要材质是SUS304 2B钢材,是目前市场上较为常见的可食用级钢材之一。
琴音叫盖水壶在日常生活中的应用较多,在水烧开后,由于水蒸气的压力作用,就会使壶盖发出琴音,提醒使用者水已经烧开。
在实际生产的过程中,叫盖水壶的壁厚厚度为0.7mm在进行生产的过程中需要涉及到两次深拉伸,深拉伸的计算公式为d= d2f-4dh+1.72dR+0.65R2-1.72dr-0.56r2(1)。
其中,df=172.5mm,d=152.5mm,h=203mm,R=r=4.5mm。
不锈钢深拉伸工艺
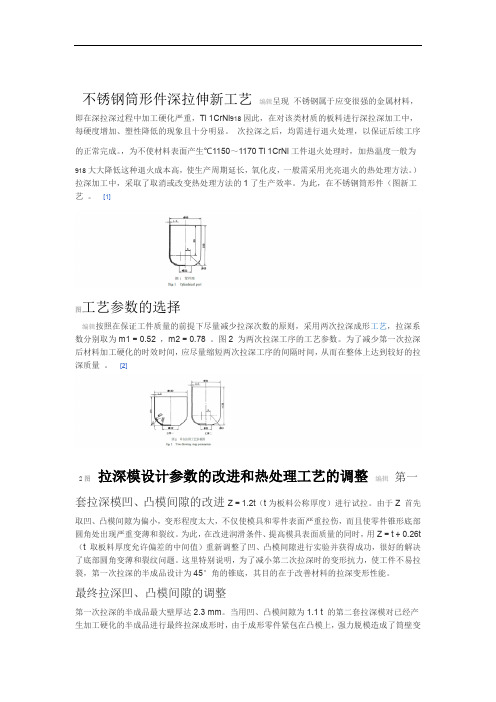
不锈钢筒形件深拉伸新工艺编辑呈现不锈钢属于应变很强的金属材料,即在深拉深过程中加工硬化严重,Ti 1CrNi918因此,在对该类材质的板料进行深拉深加工中,每硬度增加、塑性降低的现象且十分明显。
次拉深之后,均需进行退火处理,以保证后续工序的正常完成。
,为不使材料表面产生℃1150~1170 Ti 1CrNi工件退火处理时,加热温度一般为918大大降低这种退火成本高,使生产周期延长,氧化皮,一般需采用光亮退火的热处理方法。
)拉深加工中,采取了取消或改变热处理方法的1了生产效率。
为此,在不锈钢筒形件(图新工艺。
[1]图工艺参数的选择编辑按照在保证工件质量的前提下尽量减少拉深次数的原则,采用两次拉深成形工艺,拉深系数分别取为m1 = 0.52 ,m2 = 0.78 。
图2 为两次拉深工序的工艺参数。
为了减少第一次拉深后材料加工硬化的时效时间,应尽量缩短两次拉深工序的间隔时间,从而在整体上达到较好的拉深质量。
[2]2图拉深模设计参数的改进和热处理工艺的调整编辑第一套拉深模凹、凸模间隙的改进Z = 1.2t(t为板料公称厚度)进行试拉。
由于Z 首先取凹、凸模间隙为偏小,变形程度太大,不仅使模具和零件表面严重拉伤,而且使零件锥形底部圆角处出现严重变薄和裂纹。
为此,在改进润滑条件、提高模具表面质量的同时,用Z = t + 0.26t (t 取板料厚度允许偏差的中间值)重新调整了凹、凸模间隙进行实验并获得成功,很好的解决了底部圆角变薄和裂纹问题。
这里特别说明,为了减小第二次拉深时的变形抗力,使工件不易拉裂,第一次拉深的半成品设计为45°角的锥底,其目的在于改善材料的拉深变形性能。
最终拉深凹、凸模间隙的调整第一次拉深的半成品最大壁厚达2.3 mm。
当用凹、凸模间隙为1.1 t 的第二套拉深模对已经产生加工硬化的半成品进行最终拉深成形时,由于成形零件紧包在凸模上,强力脱模造成了筒壁变形,使之产生了凸肚(图3)。
不锈钢深拉伸工艺
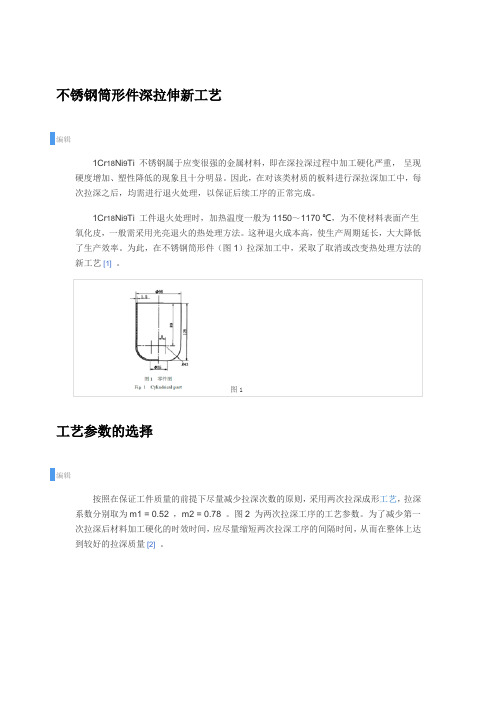
不锈钢筒形件深拉伸新工艺编辑1Cr18Ni9Ti 不锈钢属于应变很强的金属材料,即在深拉深过程中加工硬化严重,呈现硬度增加、塑性降低的现象且十分明显。
因此,在对该类材质的板料进行深拉深加工中,每次拉深之后,均需进行退火处理,以保证后续工序的正常完成。
1Cr18Ni9Ti 工件退火处理时,加热温度一般为1150~1170 ℃,为不使材料表面产生氧化皮,一般需采用光亮退火的热处理方法。
这种退火成本高,使生产周期延长,大大降低了生产效率。
为此,在不锈钢筒形件(图1)拉深加工中,采取了取消或改变热处理方法的新工艺 [1]。
图1工艺参数的选择编辑按照在保证工件质量的前提下尽量减少拉深次数的原则,采用两次拉深成形工艺,拉深系数分别取为m1 = 0.52 ,m2 = 0.78 。
图2 为两次拉深工序的工艺参数。
为了减少第一次拉深后材料加工硬化的时效时间,应尽量缩短两次拉深工序的间隔时间,从而在整体上达到较好的拉深质量 [2]。
图2拉深模设计参数的改进和热处理工艺的调整编辑第一套拉深模凹、凸模间隙的改进首先取凹、凸模间隙为Z = 1.2t(t为板料公称厚度)进行试拉。
由于Z 偏小,变形程度太大,不仅使模具和零件表面严重拉伤,而且使零件锥形底部圆角处出现严重变薄和裂纹。
为此,在改进润滑条件、提高模具表面质量的同时,用Z = t + 0.26t(t 取板料厚度允许偏差的中间值)重新调整了凹、凸模间隙进行实验并获得成功,很好的解决了底部圆角变薄和裂纹问题。
这里特别说明,为了减小第二次拉深时的变形抗力,使工件不易拉裂,第一次拉深的半成品设计为45°角的锥底,其目的在于改善材料的拉深变形性能。
最终拉深凹、凸模间隙的调整第一次拉深的半成品最大壁厚达2.3 mm。
当用凹、凸模间隙为1.1 t 的第二套拉深模对已经产生加工硬化的半成品进行最终拉深成形时,由于成形零件紧包在凸模上,强力脱模造成了筒壁变形,使之产生了凸肚(图3)。
不锈钢薄板深拉伸成型工艺及模具设计

不锈钢薄板深拉伸成型工艺及模具设计伴随我国工业领域的快速发展,许多行业如汽车、电子、化工、石油等对不锈钢的应用性能提出更高的要求。
如不锈钢薄板,其作为部分产品关键零件,加工难度较大,需引入有效的加工工艺与设计方法,在加工效率提高的同时保证产品质量。
本次研究将对不锈钢薄板深拉伸成型工艺、模具设计思路以及不锈钢薄板深拉伸成型工艺与模具设计其他注意事项进行分析。
标签:不锈钢薄板;深拉伸成型工艺;模具设计前言:作为当前工业领域中常用的材料,不锈钢材料本身在工艺性能、使用性能上都有一定的优势。
本次研究中主要选择由不锈钢薄板构成的套筒为对象,不锈钢材料为06Cr19Ni10奥氏体型不锈钢,有低温韧性、可塑性、耐腐蚀性等优势,但值得注意的是做套筒加工中,若直接以传统数控加工方式为主,将面临加工难度大、费时费力等问题,此时便可考虑引入拉伸模模具成型方法,可使加工质量得以保证。
因此,本文对不锈钢薄板深拉伸成型工艺与模具设计研究,具有十分重要的意义。
1不锈钢薄板深拉伸成型工艺1.1研究对象本次研究中所选取对象为薄壁厚度为0.3mm的深型腔结构,其深度、内径比控制为2:3。
因壁厚过薄不适合采用精铸或直接数控加工,可能会导致型腔变形,且不利于大批量生产。
1.2工艺方案选择深拉伸工艺应用下,要求圆筒形件在拉伸系数、毛坯尺寸上合理控制,且保工序尺寸满足拉伸模设计要求。
以圆筒形件拉伸规律为依据,且选择拉伸面积相等为条件,进行套筒拉伸毛坯尺寸的确定,可为Φ54mm。
同时对压边圈下圆筒形拉伸件拉伸系数确定,具体确定中一般需借助相关的公式,如毛坯尺寸、工件直径、总拉伸系数分别以D、d、m表示,第1次与第n次拉伸时拉伸件直径分别以d1、dn表示,第1次与第n次拉伸系数分别以m1、mn表示,则有m=d/D=15.3/54=0.283;m1=d1/D;m2=d2/d1;mn=dn/dn-1。
由于本次研究所选取加工件需经过四次拉伸,所以需做四次拉伸系数计算,确保拉伸系数滿足加工要求。
拉伸工艺及拉伸模具设计

拉伸工艺及拉伸模具设计1. 引言拉伸工艺及拉伸模具设计是金属加工中重要的工艺之一。
通过拉伸工艺,可以使金属材料在不改变其截面积的情况下,有效地改变其形状和尺寸。
而拉伸模具设计则是为了实现拉伸工艺的顺利进行,确保拉伸过程中材料的变形满足预期要求。
本文将介绍拉伸工艺的基本原理和步骤,以及拉伸模具设计的关键考虑因素和设计要点。
2. 拉伸工艺的基本原理和步骤拉伸工艺是通过对金属材料施加拉力,使其发生塑性变形的过程。
其基本原理是利用材料的延伸性,使其在一定条件下引入应力并改变形状。
拉伸工艺的基本步骤如下:2.1 材料准备在进行拉伸工艺之前,需要对材料进行准备。
首先是材料的选择,根据工件的要求选择适合的金属材料。
其次是材料的加工准备,包括切割和清洁等步骤,以确保材料表面的平整和无杂质。
2.2 模具设计拉伸工艺需要使用专门设计的模具,以便在施加拉力时能够确保材料的形状和尺寸得到准确控制。
模具设计需要考虑多个因素,包括工件的形状和尺寸、材料的性质以及拉伸过程中的应力情况等。
2.3 拉伸过程拉伸过程中,首先将材料放置于模具中,并施加拉力。
拉力的大小和方向将影响材料的延展性和变形形式。
通过对拉力的控制,可以控制材料的形状和尺寸变化。
2.4 热处理在拉伸过程完成后,有时需要对材料进行热处理,以消除拉伸过程中产生的应力和改善材料的性能。
常见的热处理方法包括退火、淬火和回火等。
3. 拉伸模具设计的关键考虑因素拉伸模具设计的关键考虑因素包括以下几点:3.1 工件形状和尺寸拉伸模具的设计应根据工件的形状和尺寸,确保拉伸过程中工件的形变满足要求。
对于复杂形状的工件,可能需要设计多级模具,以实现更精确的形变控制。
3.2 材料的特性不同材料的特性会对拉伸模具的设计产生影响。
例如,材料的延展性和硬度将决定模具设计中的一些参数,如模具的角度和半径。
了解材料的特性是设计拉伸模具的重要基础。
3.3 拉力和应力分布拉力和应力分布对模具的设计也有重要影响。
毕业设计(论文)-不锈钢水杯落料拉深复合模设计与参数化建模

摘要论文主要介绍了一套落料拉深复合模具的设计方法。
经过查阅资料,首先要对零件进行工艺分析,经过工艺分析和对比,采用落料拉深复合、二次拉深工序,通过冲裁力、顶件力、卸料力等的计算,确定压力机的型号。
再分析对冲压件加工的模具适用的类型选择所需设计的模具。
得到将设计的模具类型后将模具的各工作零部件设计过程表达出来。
在设计中第一部分,主要叙述了冲压模具的发展状况,说明冲压模具的重要性与本次设计的意义。
第二部分对冲压件的工艺分析,完成了工艺方案的确定,接着是零件冲压工艺计算。
接着是对冲压模具的设计和结构的确定。
本次设计阐述了落料拉深复合模的结构设计。
本模具性能可靠,运行平稳,提高了产品质量和生产效率,降低生产成本。
关键词:落料拉深复合模模具结构冲压AbstractThis paper mainly describes the design method of a composite die. Through access to information, we must first process the parts analysis, technology analysis and comparison by using the composite blanking drawing, second drawing process, by blanking force, the top pieces of force, discharge force of the calculations to determine the Press models. Further analysis of the stamping dies for the type of processing to select the desired design of the mold. Obtained after the design of the mold type of mold design process of the working parts express.In the first part of the design, mainly described the development of stamping die, stamping die shows the importance and significance of this design. The second part of the stamping process analysis to determine the completion of the process plan, followed by stamping process calculation. Next is a stamping die design and structure determined.The design drawing blanking described the structure of compound die design. Reliable performance of the mold, smooth operation, improved product quality and production efficiency, reduce production costs.Keywords: Blanking die structure drawing ; compound die; stamping目录第1章绪论 (1)1.1冲压模具在制造业的地位 (1)1.2本课题研究的目的、意义 (1)1.3冲压模具的历史发展与现状 (2)1.4冲压设计的基本内容 (3)1.5冲压设计的一般工作程序 (3)第2章冲压成型工艺设计 (5)2.1产品冲压工艺分析: (5)2.1.1 制件介绍: (5)2.1.2产品尺寸: (5)2.2产品材料分析: (5)2.3冲压工艺方案的确定 (5)2.3.1工序性质和数量 (5)2.3.2冲压方案: (6)2.3.3各方案特点分析: (6)2.3.4工艺方案的确定 (6)2.4零件冲压工艺计算 (6)2.4.1零件毛坯尺寸计算 (6)2.4.2确定拉深次数 (7)2.4.3排样及相关计算 (8)第3章冲压模具设计 (10)3.1确定冲模类型机结构形式 (10)3.2计算工序压力,选择压力机 (10)3.2.1 落料与首次拉深 (10)3.2.2二次拉深 (11)3.3拉深模工作零件设计与计算 (12)3.3.1凸、凹模尺寸计算 (12)3.3.2落料拉深复合模其他工艺计算 (12)第4章模具结构的确定 (14)4.1模具的形式 (14)4.1.1正装式特点 (14)4.1.2倒装式特点 (14)4.2卸料装置 (14)4.2.1条料的卸除 (14)4.2.2工件的卸除 (14)4.2.3定位装置 (14)4.2.4导向零件 (14)4.2.5模架 (14)4.2.6模具的其他零件 (14)4.2.7模具材料的选用 (15)第5章落料拉深模具结构设计 (18)5.1落料、首次拉深复合模结构图 (18)5.2二次拉深模 (20)第6章工件冲压工艺规程 (21)6.1工艺规程设计的内容和步骤 (21)6.2分析冲压件的工艺性 (22)6.3不锈钢水杯冲压工艺规程 (22)第7章参数化建模 (23)7.1参数化建模概念及其优点 (23)7.1.1参数化建模 (23)7.1.2参数化建模优点 (23)7.2参数化建模方法与步骤 (23)7.2.1基本建模方法 (23)7.2.2零件的参数化建模步骤 (24)7.3参数化建模应用 (24)结论 (26)参考文献 (27)谢辞 (28)附录1 (29)附录2 (30)第1章绪论1.1冲压模具在制造业的地位冲压是使板料经分离或成形而得到制件的加工方法。