编码器标定过程
abz编码器的零位调整 -回复

abz编码器的零位调整-回复ABZ编码器是一种电子设备,常用于测量和控制系统中。
在使用ABZ编码器时,零位调整是非常重要的一个步骤,它确保编码器测量的数据准确性和可靠性。
本文将详细介绍ABZ编码器的零位调整过程,包括准备工作、零位调整方法和注意事项等内容。
第一步:准备工作在开始零位调整之前,我们需要准备一些工具和设备,以确保调整过程的顺利进行。
首先,我们需要准备一个适用于ABZ编码器的电压表,在调整过程中用来测量输出信号的电压。
另外,我们还需要一根杠杆或尺子,用于手动旋转ABZ编码器的轴,以调整其零位。
最后,我们还需要电源供应器和连接ABZ编码器的电缆。
第二步:零位调整方法1. 将ABZ编码器连接到电源供应器,并确保其正常工作。
使用电压表测量ABZ编码器的输出信号电压,记录下初始值。
2. 手动旋转ABZ编码器的轴,将其调整到所需的零位位置。
这个位置应该是一个已知的基准位置,例如机械安装参考点或系统的初始状态。
3. 继续测量ABZ编码器的输出信号电压,记录下调整后的数值。
4. 使用电压表的测量结果,计算出零位调整的误差值。
根据ABZ编码器的规格和要求,确定这个误差值是否在可接受的范围内。
5. 如果误差值超过了可接受范围,需要进行进一步的调整。
根据ABZ编码器的型号和说明书,查找调整零位的方法。
通常,调整ABZ编码器的零位可以通过调整编码器轴上的磁性环或光栅板的位置来实现。
6. 按照ABZ编码器的说明书,使用适当的工具和方法,进行零位的微调。
在调整过程中,使用电压表测量ABZ编码器的输出信号电压,并记录下调整后的数值。
7. 重复步骤4和步骤6,直到所测量的误差值达到可接受的范围为止。
在这个过程中,需要耐心和细心,确保每一次微调都是准确的。
第三步:注意事项在进行ABZ编码器的零位调整时,有一些注意事项需要注意。
1. 调整过程中要小心谨慎,避免过度调整或不当操作,以免损坏ABZ编码器。
2. 在调整之前,确保ABZ编码器的安装位置稳定,并且没有外部扰动。
欧姆龙绝对值编码器原点标定

欧姆龙绝对值编码器原点标定
伺服系统零点校对的绝对值编码器调零方法,涉及工业自动化和智能机器人领域。
方法,在通用交流伺服驱动器不变的基础上,采用对电机电角度零位校对补偿的方法,弥补了伺服电机与编码器初始安装过程中的电角度零位偏差,由于电角度计算的准确度影响控制策略的控制效果,因此该角度定位精度的提升,使得该伺服驱动器的整机控制性能提升,提高了行业应用的价值。
如果编码器的值没有丢失,MCP里有显示第二原点,把机器人的第一原点移动到跟第二原点。
时硕的电控柜开门背后有六个编码器的初始值,初始值就是机器人的出厂绝对零点,输进去就可以。
绝对值旋转单圈绝对值编码器:以转动中测量光电码盘各道刻线,以获取唯一的编码,当转动超过360度时,编码又回到原点,这样的编码只能用于旋转范围360度以内的测量。
多圈绝对值编码器:测量旋转超过360度范围时使用,用到编码器生产运用钟表齿轮机械原理,当中心码盘旋转时,通过齿轮传动另一组码盘(或多组齿轮,多组码盘)。
在单圈编码的基础上再增加圈数的编码,以扩大编码器的测量
范围,它同样是由机械位置确定编码,每个位置编码唯一不重复,而无需记忆。
焊机编码器标定

焊机编码器(位移传感器)标定讲课人:王伟焊机有几个编码器,包括夹紧台,大车移动,导向辊,如遇数值不准导致无法到位时,或者更换后都需要对编码器进行标定,现场有油漆标示,用以检验编码器数值是否准确。
标定工作可在焊机画面上完成。
1 夹紧台(clamping table)位移传感器标定1)打开夹紧台标定画面点adjust on/off 按钮变成on为解锁2)把limit shear pos os&ds 都设为-100,点保存3)完全移动entry/exit table 到两边,不能移动时点击offset 置0.4)把limit weld pos os&ds 都设为27,点保存5)将entry/exit table 向中间移动到27,点offset.6)将limit weld pos 改为72,limit shear pos 改为-12,点保存。
7)点adjust on/off 按钮变成off 锁定。
2 大车(welding carriage)编码器标定1)打开大车标定画面点adjust on/off 按钮变成on为解锁2)把大车开到操作侧直到安全销可以锁紧的位置,锁紧安全销,点offset.3)点adjust on/off 按钮变成off 锁定。
3 导向辊(pilot roll)位移传感器标定1)打开导向辊标定画面点adjust on/off 按钮变成on为解锁2)把大车开到中间,使导向辊在夹紧台下面,在夹紧台中间放一完全水平的装置。
3)把手动把导向辊entry/exit开到与夹紧台下表面平行的位置(正好碰到水平装置),点Offset 置0.4)点adjust on/off 按钮变成off 锁定。
CB编码器标定(强制)

关于编码器标定规定:◆在更换了编码器本体(非DP接口),或处理过编码器接手的情况下,编码器的值发生了变化,有可能需要标定。
在确需标定后,标定步骤如下:1、通知操作人员,要求相应设备打到停止位置。
2、确认当前位置值,一般情况下要在转臂的2个基位信号到的位置标定(对于冷床应该在低位信号到)。
3、打开“SIMATIC MANAGER”,点开冷床程序的“BLOCKS”。
4、找到变量表“encode1”,双击打开。
5、找到相应的编码器变量,例如LOAD1 SM(PID72),然后在第2格(QW74)后的“modify value”栏输入标定值(通常转臂是4度,1#冷床低位是13度,1#冷床低位是17度)。
6、然后在第3格(Q72.7)后的“modify value”栏输入1,点击工具栏的双箭头符号或到菜单栏选“variable”下的“Activate Modify Values”,立即进行下一步:7、又在第3格(Q72.7)后的“modify value”栏输入0,点击工具栏的双箭头符号或到菜单栏选“variable”下的“Activate Modify Values”。
注意:一定要完成这一步骤。
8、关闭变量表“encode1”,如果提示是否保存(Do you want to save the variable table?)选择No。
9、通知操作人员试车,监视标定后值是否正常变化。
一定要确认无问题,方可结束工作。
关于修改变量:对于一些M点、Q点、DB点,如果程序中未置位信号,则可以通过修改变量的方式来改变值(类似强制),优点是:有置位语句这样的操作不会起作用,比较安全。
而强制是无条件的,必须确认清楚。
操作如下:1、打开相应的程序。
2、打开或建立一个变量表。
3、输入你要修改值的变量地址。
4、在变量地址后的“modify value”栏输入想修改的值。
点击工具栏的双箭头符号或到菜单栏选“variable”下的“Activate Modify Values”。
Z编码器校准

12.安装Encoder先将Microe Mercury 2000Encoder 装在EncoderBracket 上面,A 与B 点要无间隙(No Gap)Encoder Bracket 与ARMUnit 要有0.5mm 的间隙。
检查Microe InterpolatorSS200的接头共15pin ,有无与外壳短路。
1. Setup Interpolator:将Interpolator 与EncoderAlignment(与计算机的接口)连接。
1.确认Interpolator 的讯号(Signal)是否正常先将Transducer 往上移到顶,再慢慢往下移,此时讯号灯会Off-On 两次,第一次是Index1的位置,第二次是Index2的位置。
2.设定实际的精密度(Resolution)1.设定Interpolator 频率1.8MHz 。
2.先设定Interpolator 的值为129。
3.将Capillary 放在Height Gauge 上后Reset Count 值。
4.将Capillary 放到S/F Gauge 的9.1mm 位置看Count 值为多少。
5.实际精密度为9.1mm ÷Count 值,若不是在0.3982~0.4013um ,则设定Interpolator 的值为130,在从第3项开始,再做一次。
3.设定Index1和Index2的中心值。
1.将Transducer 往下移至底。
2.按Cal 则讯号(Signal)灯Off 。
3.将Transducer 由下往上移至顶,则讯号(Signal)灯On ,设定完成。
多圈绝对值编码器调零对位方法
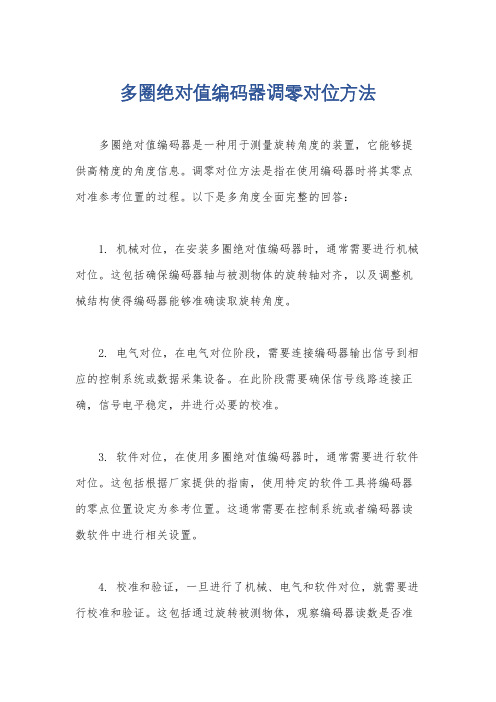
多圈绝对值编码器调零对位方法
多圈绝对值编码器是一种用于测量旋转角度的装置,它能够提供高精度的角度信息。
调零对位方法是指在使用编码器时将其零点对准参考位置的过程。
以下是多角度全面完整的回答:
1. 机械对位,在安装多圈绝对值编码器时,通常需要进行机械对位。
这包括确保编码器轴与被测物体的旋转轴对齐,以及调整机械结构使得编码器能够准确读取旋转角度。
2. 电气对位,在电气对位阶段,需要连接编码器输出信号到相应的控制系统或数据采集设备。
在此阶段需要确保信号线路连接正确,信号电平稳定,并进行必要的校准。
3. 软件对位,在使用多圈绝对值编码器时,通常需要进行软件对位。
这包括根据厂家提供的指南,使用特定的软件工具将编码器的零点位置设定为参考位置。
这通常需要在控制系统或者编码器读数软件中进行相关设置。
4. 校准和验证,一旦进行了机械、电气和软件对位,就需要进行校准和验证。
这包括通过旋转被测物体,观察编码器读数是否准
确,并进行必要的校准调整,以确保编码器能够准确反映被测物体
的旋转角度。
5. 定期维护,为了保持多圈绝对值编码器的准确性,需要定期
进行维护和校准。
这包括清洁编码器表面,检查连接线路是否良好,以及校准和验证编码器的零点位置是否保持准确。
总之,多圈绝对值编码器的调零对位涉及到机械、电气、软件
和校准等多个方面,需要全面考虑并严格执行相关步骤,以确保编
码器能够准确地提供角度信息。
编码器标定过程

编码器标定过程标定现场编码器因为现场编码器所使用地点不同,标定方法不尽相同,但原理相同。
此处以轧机入口侧导板编码器为例讲解。
所谓标定是指对图1中红线框中的数值进行设定使得现场的位移变化量与程序中的位移变化量相同(误差允许范围内)。
标定后的值记为β,标定前的经验值记为α。
图11.程序中设定现在程序中对所标定参数进行设定(经验值)。
设定位置如图2红线框所示图2设定值与图2中的蓝线框中的数值有关,如果是蓝线框是100则红线框为两位数,如果蓝线框是1000则红线框为三位数,设定方法为双击,在对话框中Device栏中进行输入数值。
此处经验值为140记为α。
2.现场测量在现场设备上确定一个测量的基准点(用胶带贴在设备上,在上划线作为每次测量的基准)移动现场设备,先进行一次点动,移动量不用很大确保以后的移动方向与此次点动方向相同(减小误差)移动现场设备,测量移动距离,记录为L1(473mm)在程序中查看程序中的移动量,查看位置如图红线框所示(有多处与此处数值相同)。
记录为S1(565.7mm)。
再次移动现场设备(与上次方向相同)测量移动距离记录为L2(599mm)。
再此查看程序相同位置记录数据为S2(726.8mm)。
3.计算①ΔL=|L2‐L1|=126mm ②ΔS=|S2‐S1|=161.1mm ③β=ΔL÷ΔS×α=109.49经过计算β值为109.49,现场实际测量不免有误差,多测几组(测量计算方法相同)进行比较,得出最后结果此处给出结果β值为110。
4.验证让设备移动较大距离(尽量减小误差),测得L1、S1、L2、S2,计算得出ΔL、ΔS比较俩数值是否相同(误差允许范围)因为现场测量工具粗糙,此处认为误差在0.1mm即为相同。
编码器检验方法及规范
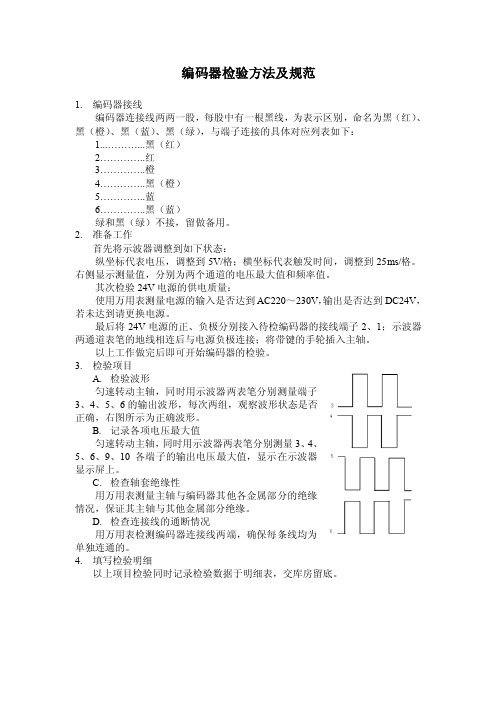
编码器检验方法及规范1.编码器接线编码器连接线两两一股,每股中有一根黑线,为表示区别,命名为黑(红)、黑(橙)、黑(蓝)、黑(绿),与端子连接的具体对应列表如下:1...………...黑(红)2…………..红3…………..橙4…………..黑(橙)5…………..蓝6…………..黑(蓝)绿和黑(绿)不接,留做备用。
2.准备工作首先将示波器调整到如下状态:纵坐标代表电压,调整到5V/格;横坐标代表触发时间,调整到25ms/格。
右侧显示测量值,分别为两个通道的电压最大值和频率值。
其次检验24V电源的供电质量:使用万用表测量电源的输入是否达到AC220~230V,输出是否达到DC24V,若未达到请更换电源。
最后将24V电源的正、负极分别接入待检编码器的接线端子2、1;示波器两通道表笔的地线相连后与电源负极连接;将带键的手轮插入主轴。
以上工作做完后即可开始编码器的检验。
3.检验项目A.检验波形匀速转动主轴,同时用示波器两表笔分别测量端子3、4、5、6的输出波形,每次两组,观察波形状态是否正确,右图所示为正确波形。
B.记录各项电压最大值匀速转动主轴,同时用示波器两表笔分别测量3、4、5、6、9、10各端子的输出电压最大值,显示在示波器显示屏上。
C.检查轴套绝缘性用万用表测量主轴与编码器其他各金属部分的绝缘情况,保证其主轴与其他金属部分绝缘。
D.检查连接线的通断情况用万用表检测编码器连接线两端,确保每条线均为单独连通的。
4.填写检验明细以上项目检验同时记录检验数据于明细表,交库房留底。
- 1、下载文档前请自行甄别文档内容的完整性,平台不提供额外的编辑、内容补充、找答案等附加服务。
- 2、"仅部分预览"的文档,不可在线预览部分如存在完整性等问题,可反馈申请退款(可完整预览的文档不适用该条件!)。
- 3、如文档侵犯您的权益,请联系客服反馈,我们会尽快为您处理(人工客服工作时间:9:00-18:30)。
标定现场编码器
因为现场编码器所使用地点不同,标定方法不尽相同,但原理相同。
此处以轧机入口侧导板
编码器为例讲解。
所谓标定是指对图1中红线框中的数值进行设定使得现场的位移变化量与
程序中的位移变化量相同(误差允许范围内)。
标定后的值记为β,标定前的经验值记为α。
图1
1.程序中设定
¾现在程序中对所标定参数进行设定(经验值)。
¾设定位置如图2红线框所示
图2
设定值与图2中的蓝线框中的数值有关,如果是蓝线框是100则红线框为两位数,
如果蓝线框是1000则红线框为三位数,设定方法为双击,在对话框中Device栏中
进行输入数值。
此处经验值为140记为α。
2.现场测量
¾在现场设备上确定一个测量的基准点(用胶带贴在设备上,在上划线作为每次测量的基准)
¾移动现场设备,先进行一次点动,移动量不用很大确保以后的移动方向与此次点动方向相同(减小误差)
¾移动现场设备,测量移动距离,记录为L1(473mm)
¾在程序中查看程序中的移动量,查看位置如图红线框所示(有多处与此处数值相同)。
记录为S1(565.7mm)。
¾再次移动现场设备(与上次方向相同)测量移动距离记录为L2(599mm)。
¾再此查看程序相同位置记录数据为S2(726.8mm)。
3.计算
①ΔL=|L2‐L1|=126mm ②ΔS=|S2‐S1|=161.1mm ③β=ΔL÷ΔS×α=109.49
经过计算β值为109.49,现场实际测量不免有误差,多测几组(测量计算方法相同)
进行比较,得出最后结果此处给出结果β值为110。
4.验证
让设备移动较大距离(尽量减小误差),测得L1、S1、L2、S2,计算得出ΔL、ΔS比较
俩数值是否相同(误差允许范围)因为现场测量工具粗糙,此处认为误差在0.1mm即
为相同。