球团矿的制备及性能测试
球团矿标样制作说明
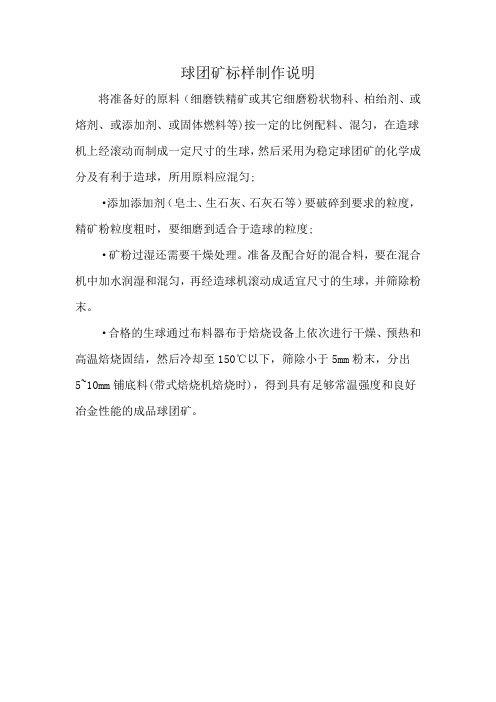
球团矿标样制作说明
将准备好的原料(细磨铁精矿或其它细磨粉状物科、柏绐剂、或熔剂、或添加剂、或固体燃料等)按一定的比例配料、混匀,在造球机上经滚动而制成一定尺寸的生球,然后采用为稳定球团矿的化学成分及有利于造球,所用原料应混匀;
·添加添加剂(皂土、生石灰、石灰石等)要破碎到要求的粒度,精矿粉粒度粗时,要细磨到适合于造球的粒度;
·矿粉过湿还需要干燥处理。
准备及配合好的混合料,要在混合机中加水润湿和混匀,再经造球机滚动成适宜尺寸的生球,并筛除粉末。
·合格的生球通过布料器布于焙烧设备上依次进行干燥、预热和高温焙烧固结,然后冷却至150℃以下,筛除小于5mm粉末,分出5~10mm铺底料(带式焙烧机焙烧时),得到具有足够常温强度和良好冶金性能的成品球团矿。
球团矿的制备及性能测试
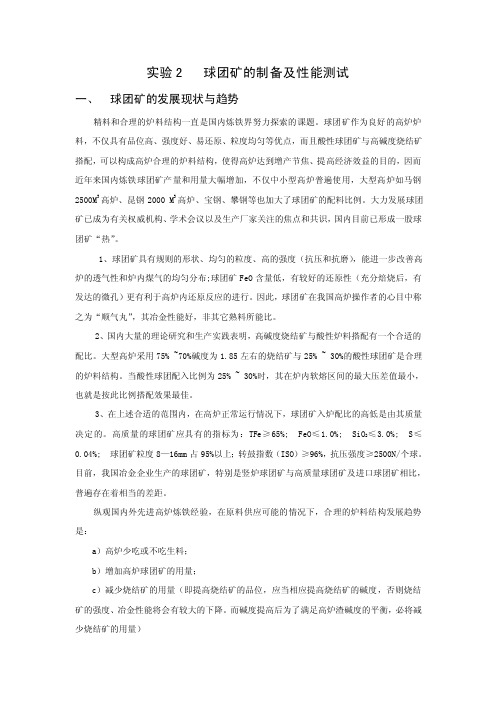
实验2 球团矿的制备及性能测试一、球团矿的发展现状与趋势精料和合理的炉料结构一直是国内炼铁界努力探索的课题。
球团矿作为良好的高炉炉料,不仅具有品位高、强度好、易还原、粒度均匀等优点,而且酸性球团矿与高碱度烧结矿搭配,可以构成高炉合理的炉料结构,使得高炉达到增产节焦、提高经济效益的目的,因而近年来国内炼铁球团矿产量和用量大幅增加,不仅中小型高炉普遍使用,大型高炉如马钢2500M3高炉、昆钢2000 M3高炉、宝钢、攀钢等也加大了球团矿的配料比例。
大力发展球团矿已成为有关权威机构、学术会议以及生产厂家关注的焦点和共识,国内目前已形成一股球团矿“热”。
1、球团矿具有规则的形状、均匀的粒度、高的强度(抗压和抗磨),能进一步改善高炉的透气性和炉内煤气的均匀分布;球团矿FeO含量低,有较好的还原性(充分焙烧后,有发达的微孔)更有利于高炉内还原反应的进行。
因此,球团矿在我国高炉操作者的心目中称之为“顺气丸”,其冶金性能好,非其它熟料所能比。
2、国内大量的理论研究和生产实践表明,高碱度烧结矿与酸性炉料搭配有一个合适的配比。
大型高炉采用75% ~70%碱度为1.85左右的烧结矿与25% ~ 30%的酸性球团矿是合理的炉料结构。
当酸性球团配入比例为25% ~ 30%时,其在炉内软熔区间的最大压差值最小,也就是按此比例搭配效果最佳。
3、在上述合适的范围内,在高炉正常运行情况下,球团矿入炉配比的高低是由其质量≤3.0%; S≤决定的。
高质量的球团矿应具有的指标为:TFe≥65%; FeO≤1.0%; SiO20.04%; 球团矿粒度8—16mm占95%以上;转鼓指数(ISO)≥96%,抗压强度≥2500N/个球。
目前,我国冶金企业生产的球团矿,特别是竖炉球团矿与高质量球团矿及进口球团矿相比,普遍存在着相当的差距。
纵观国内外先进高炉炼铁经验,在原料供应可能的情况下,合理的炉料结构发展趋势是:a)高炉少吃或不吃生料;b)增加高炉球团矿的用量;c)减少烧结矿的用量(即提高烧结矿的品位,应当相应提高烧结矿的碱度,否则烧结矿的强度、冶金性能将会有较大的下降。
团矿理论与工艺课程实验

4)取出生球 生球紧密过程结束后,用铲子取出全部生 球(造球盘运转状态下),经8mm实验筛筛分分级,取 +8mm的生球为合格球团,其余作废料处理。称取生球质 量后,然后按生球质量检测方法,测定生球强度。
实验步骤
一、造球实验
造球操作: 1)母球形成 启动圆盘造球机,将混匀好的球团混合料 取200~300g放入转动的圆盘中,加入滴状水,使之形成23mm左右的母球,注意随时将较大的母球打碎,造母球时 间约2~3min。
实验步骤
一、造球实验
2)母球长大 向母球上喷加雾状水的同时,用铲子将混 合料不断给到已润湿的母球上,使母球逐渐长大。在母球 长大过程中,加水加料速度要密切控制,在预定时间内加 完混合料和水,母球长大时间一般为7~9min。
3.成品球团强度检测 熟球焙烧结束后,取10个未出现裂纹的熟球,利用压
力机检测其抗压强度,取平均值为熟球的抗压强度(单位: N/个球)。
检测熟球抗压强度时,需等熟球冷却到室温再进行;
实验注意事项
1每组同学进行实验之前,先在实验记录本上签名; 2实验结束后,由每个小组组长在实验室门后的实验记录本上 登记; 3严格遵守实验室纪律; 4实验结束后,最后一组同学负责打扫实验室卫生,并将水、 电源关闭。
实验步骤
一、造球实验 5.生球干燥
将测完强度的生球取约200g于小铁盆中(写明标签), 放置在干燥箱中进行干燥,干燥温度105℃,干燥结束后, 进行称重,计算生球的水分。
实验步骤
二、球团焙烧实验 1.干球抗压强度检测
挑选10个未出现裂纹的干球,利用压力机检测其抗压强度, 取平均值为干球的抗压强度(单位:N/个球)。 2.干球焙烧
球团矿的制备和性能测定

球团矿的制备和性能测定一、国内外球团矿的发展球团矿是一种优良的高炉炼铁原料,我国的铁矿资源本适合生产球团矿,但是由于历史的原因,却走上了细精矿烧结的道路,上世纪80年代中期宝山钢铁公司的1号高炉投产,改变了我国传统的细精矿烧结工艺,其后随着钢铁工业快速的发展,国产精矿不能满足需求,进口粉矿逐年增加,目前就全国范围而言,细精矿在烧结配料中已经不占主导地位。
球团矿在我国高炉炉料中的比例逐年升高,进入21世纪,链篦机一回转窑工艺发展迅速,2007年球团矿的产量可以达到l亿吨左右,加上进口的球团矿大约1.3亿吨,在全国高炉炉料中的比重平均16%左右,在可以预见的将来,烧结矿依然是我国高炉的主要原料,球团矿必将持续发展。
各钢铁厂的情况不同和矿源不同决定了其不同的高炉炉料结构。
日本、韩国高炉以烧结矿为主, 因为其主要铁料是国际上购买的粉矿, 适宜生产烧结矿。
北美高炉以球团矿为主, 因为其矿源多为细精矿, 适宜生产球团矿。
欧盟由于环保要求, 烧结厂的生产和建设受到了严格的限制, 为了进一步改善高炉炼铁指标, 充分发挥球团矿在高炉炼铁中优越的冶金性能, 因而以球团矿为主。
欧美高炉球团矿使用比例一般都较高, 个别的高炉达100 %。
其中一部分高炉使用熔剂型球团矿, 如加拿大Algoma7 号高炉熔剂球团矿比例达99 % , 墨西哥AHMSA 公司Monclova 厂5 号高炉熔剂球团矿比例为93 % , 美国AKSteel 公司Ashland1KY厂Amanda 高炉熔剂球团矿比例为90 %以上; 另一部分高炉以酸性球团矿为主, 配比一般在70 %以上。
欧洲高炉中, 瑞典、英国和德国的部分高炉球团矿的比例很高。
亚洲国家的高炉一般以烧结矿为主, 高达70 %左右。
日本高炉炉料结构的特点是烧结矿比例高且一直比较平稳,而球团矿比例自1979 年以来一直在下降, 块矿比一直在上升。
高炉炉料中高碱度烧结矿比例维持在7113 %~7619 % , 用量一直比较平稳。
配加菱铁矿生产球团矿的基础性能研究
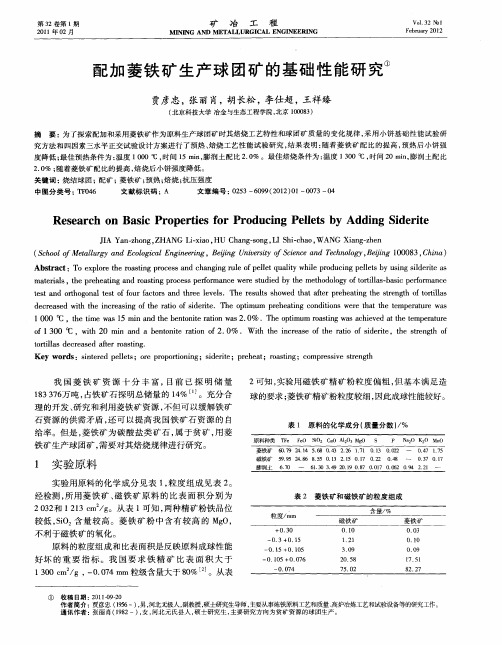
( colfMe l rya dE o gcl n ier g, eig U i r t o Si c n eh ooy B in 0 0 3 C ia Sho o t l g n cl i gnei B in nv syf c nea d Tcn l , ei 10 8 , hn ) au o aE n j ei e g jg
Re e r h o sc Pr p r i s f r Pr d c n l t y Add n i e ie s a c n Ba i o e te o o u i g Pel s b e i g S d rt
JA n z o g, HANG ixa , I Ya —h n Z L— io HU h n —o g, IS ic a W ANG Xin — e C a g sn L h -h o, agz n h
ts n rh g n lts ff u a tr n h e e es h e u t h we h tatrp e e t g t e s e g h o r l s e ta d o o o a e to rf co s a d t r e lv l .T e r s l s o d t a fe r h a i h t n t ft t l t o s n r o ia d c e s d wi h n r a i g o e r t fsd r e e r a e t t e i c e sn f h a i o i e i .T e o t m r h a i g c n i o s w r h tt e t mp rt r s h t o t h pi mu p e e t o dt n e e t a h e e au e wa n i 10 0 c .t e tm a 5 mi n e b n o i ain w s2 0 .T e o t m o s n a c i v d a e tmp r tr 0 C h i e w s 1 n a d t e tn t r t a . % h e o h pi mu r a t g w sa h e e t h e e au e i t
铁矿粉造球和球团矿焙烧试验

铁矿粉造球和球团矿焙烧试验主讲教师:张明远一、实验目的�1.掌握球团矿的生产工艺流程及加水,加溶剂等工艺技术。
�2.生球的落下强度,抗压强度及爆裂程度的测量方法。
二、基本原理�铁精矿在加粘结剂加水融湿的条件下,在造球机上滚动粘结而造球,落下强度可通过10个球落下次数及摔破个数决定。
三、实验设备�电子称、圆盘造球机、喷水瓶、筛子、铁炉、吊篮、计算机控制系统。
四、实验步骤�1. 原料准备:�1)将原料用200目筛子筛分。
�2)称干料硫酸渣2.24Kg,称皂土2.24×30%=0.067Kg。
�3)原料含水2.24。
�4)干料、皂土先混匀10次,再加水润湿。
�2.造球过程:�1)造球:�A.取加工好的球料200g,以8—10转/min转3分钟造母球。
�B.同时加料加水,正对着粒加水。
�C.用铲控制,不让料粘在造球机盘上。
�D.母球大小为绿豆一般大小。
�2)造球过程的母球长大(8min):�造母球3min后,8分钟后将转速升到300或400,300转/min,不断地加水,喷水雾状加到球上。
�3)生球的紧度(4min),生球长大后,在500转/min条件下再转3分钟。
�4)生球转速在200转/min以下,用铲顺着转盘转向铲出球来。
�3.生球性能的测定:�1)筛分:�A.用圆孔筛子分3层,由上到下顺次为15mm,10mm,5mm三层筛子筛出5~10mm称重为W1,10~15mm称重为W2,大于15mm称重为W�B. 计算:成球率=×100%�4.生球落下强度:�取10个生球在0.5m高度,记下自由落下直到球烂的次数,10个球取平均次数,一般为2次。
�5.生球的抗压强度:�取10个生球,在盘托上压显示读数:为0.1—1.0Kg/球�6.生球爆裂温度测定:�1)将SiC棒炉升到230℃恒温。
�2)将10个生球放于特制的吊篮中,吊入炉内开始计时,恒温5min。
�3)将吊篮取出,以10%生球爆裂温度,若无球裂则再吊入炉内,升高温度20℃,5min后再取出来,如此循环,测得爆裂温度为900℃左右。
球团矿生产工艺及质量指标word文档良心出品
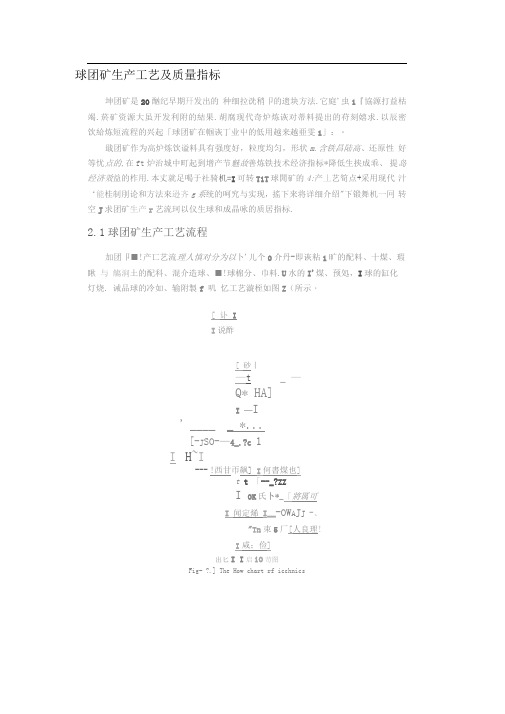
球团矿生产工艺及质量指标坤团矿是20酗纪早期幵发出的种细拉诜稍卩的遗块方法.它庭'虫1『協源打益枯竭.菸矿资源大虽开发利附的結果.胡腐现代奇炉炼诙对蒂料提出的苻刻嬉求.以辰密饮給炼短流程的兴起「球团矿在帼诙丁业屮的低用越来越亜雯1」:・戢团矿作为高炉炼饮谥料具有强度好,粒度均匀,形状m.含铁昌陆高、还原性好等忧点的,在ft炉治城中町起到增产节魅故善炼铁技术经济指标*降低生挟成乖、提岛经济效益的柞用.本丈就足喝于社骑机=I可转TiT球閒矿的4:产丄艺筍点+采用现代汁‘能桂制刖论和方法來逊齐g系统的呵究与实现,搖下来将详细介绍"下锻舞机一冋转空J求团矿生产r艺流珂以仪生球和成晶咏的质居指标.2.1球团矿生产工艺流程加团卩■!产匸艺流理人慎对分为以卜'儿个0介丹-即诙粘1旷的配料、十煤、瑕瞅与觴涧土的配科、混介造球、■!球棉分、巾料.U水的I'煤、预処,I球的缸化灯烧. 诫品球的冷如、输附製f 叽忆工艺漩桎如图Z(所示・[ 讣II说酢[ 砂丨—t _ —Q* HA]I —I' ____ _ *...[-J SO-—4_.?c 1I H~I--- !西甘帀飙] I何書煤也]t t 「--_?ZZI 0K氏卜*_「將厲可I 闻定烯I__-OW A J J -、"Tn朿5厂[人良理!I咸;俭]出匕I I启iO苛图Fig- ?.] The How chart rf icchnics2.1.1铁稍矿的干燥、辗®、与膨润土配料、混合系统球团旷生产所需的含诙療料上要仃赤铁箱矿、磁饮将矿和渴饮辅矿驾.征生产开始I:介段,原料进入饮矿配料仓中.通过给料机和皮带秤完成配料工作.经过配料的饮«矿水分含枪…股在10%尼右,高于理想值9.0%,送祥造球的效果较差.会使空球质鱼难以满足琏畀机一回转窑纶产的耍求,因此爲嬰将饮裕矿送入丁燥系统进行「燥,以降低铁持犷水分含壁.F燥系统一殷采用圆简干燥机.利用环冷机热废气或其它热源,将饿耕矿进行干燥,另外设让了旁路系统,当铁梢矿水分満足造球的耍求时,町山旁路系统将铁箱旷运至下•迪工序.即牠憎系统.当造序川铁晴矿粒度衲,比农面枳小(不大r lOOOcnZ/g)时,般采用髙伍彳址陽丄艺或润序工艺.彊積矿进荷岳UE保皓或润磨的FI的足进・“步改善铁精颗粒农面眾性,提缶比衣而枳,从而改眸铁桔矿粒度,为捉启J物料成球件,i^^高^k球曲i度作保障.经赢压辐磨或润於后的恢1^^广,按一定的工艺比例接受膨润上利除尘>«*< (牛:产中的灰尘)的配料后送往混令室,利用强力泯合机将恢枯矿、膨润七与除尘灰进疔允分而」勺匀的混介.比匸作原理是利用设务混合工H部位的和向运动,使物料也相向运动以实观fj.HI穿轴海透.达到混合均匀的H的.況合看的物料山胶帶运输机运至造球轧球⑷厂所便川的粘结剂町分为何机粘结剂利无机粘结剂两类.通常使川的足无机粘结剂中的膨树土(包含钙莖膨涧土、钠肚膨润土两种),它可捉周生球的落F强A,在造球过程中起调节水分的作用,并提為生球的爆裂温度.怖入膨润上的先决条件,必鎮是合适的原料水分和佳的加入址•根iK矿石种类和相文的不同,一股心原料水分为8〜10%的怙况下.购润七加入g约为0・5〜1.0%。
烧结矿和球团矿 转鼓强度的测定方法标准

烧结矿和球团矿转鼓强度的测定方法标准1. 测定原理转鼓强度是评价烧结矿和球团矿冶金性能的重要指标之一,通过测定转鼓强度可以了解矿物的机械性质、耐磨性、抗压强度等。
转鼓强度测试的原理是将一定量的试样置于转鼓内,在规定的转速下旋转一定时间,然后测定试样的破损率或失重率,以此评价试样的强度。
2. 测定步骤2.1 样品准备将待测的烧结矿或球团矿破碎至一定粒度,然后按照规定的取样方法,从不同部位取一定量的试样,混合均匀。
将试样分成两份,一份用于测定转鼓强度,另一份用于制备标准样品。
2.2 转鼓试验将试样放入转鼓内,调整好转速和旋转时间。
旋转过程中,试样会受到冲击和摩擦力,导致颗粒破裂或磨损。
旋转结束后,将试样取出,并测量其破损率或失重率。
2.3 结果计算根据测得的破损率或失重率,计算出试样的转鼓强度。
具体计算方法可以根据相关标准或规定进行。
3. 试验报告试验报告应包括以下内容:3.1 试验目的;3.2 试验原理;3.3 试验步骤;3.4 试验结果;3.5 结果分析。
4. 注意事项4.1 在进行转鼓试验时,应注意安全,避免试样飞溅造成伤害;4.2 试样的粒度和取样方法应符合相关规定,以保证测试结果的准确性;4.3 在测试过程中,应保持转鼓的清洁,避免杂质的干扰;4.4 对于不同种类的烧结矿和球团矿,应采用不同的测试条件和参数。
5. 方法精密度该测定方法的精密度取决于多个因素,如试样的粒度、取样方法、转鼓的转速和旋转时间等。
一般来说,该方法的相对标准偏差为1%~3%。
6. 方法应用范围该测定方法适用于各种类型的烧结矿和球团矿的转鼓强度测定,可以用于评估矿物的机械性质、耐磨性、抗压强度等性能指标。
此外,该方法还可以用于研究矿物的结构和性质之间的关系,以及优化矿物的加工工艺。
- 1、下载文档前请自行甄别文档内容的完整性,平台不提供额外的编辑、内容补充、找答案等附加服务。
- 2、"仅部分预览"的文档,不可在线预览部分如存在完整性等问题,可反馈申请退款(可完整预览的文档不适用该条件!)。
- 3、如文档侵犯您的权益,请联系客服反馈,我们会尽快为您处理(人工客服工作时间:9:00-18:30)。
冶金104班,109124183
郑伟伟
实验1 保护性炉渣粘度测定实验
一、实验目的:
1)通过实验掌握炉渣粘度的测定方法和原理。
2)不同炉渣成分粘度和温度数据分析比较。
3)了解炉渣组成对粘度及熔化性的影响。
二、实验原理:
采用旋转式热矩粘度计测定炉渣粘度的依据是:用一根制作的标钼。
其上端固定于作匀旋转的轴上。
下端为测头。
钼杆下部放于渣中并证转。
由于渣的粘度,钼棒上端相矩传递给传感器,扭距大小等比于熔渣粘度。
所以电信号下比于粘度。
Y=k·v y=k(t-t0)
三、实验仪器、设备
旋转式扭矩粘度计、铂丝炉、控制柜、单电机数据采集系统四:实验步骤:
1. 装备样品:将炉渣破碎到1mm以下用磁铁吸收其中残铁,混匀然后称180g。
2. 将渣样装入外套有石墨坩埚内,然后将其放入钼丝炉内的恒然带。
然后检查气路保护系统及冷却水系统是否正常。
方可通电升温。
3. 严格按铂丝炉升温制度逐渐增加透入钼丝炉的电压。
渣化后搅拌。
温度不超过1500℃然后将钼杆测头放入渣中指定位置。
待温度稳定5~10min后,可测粘度。
4.
①安铂杆在传感器上
②开动电机使钼杆交融转动
③开启计算机系统电源
④运行测定粘度软件WKW
⑤逐步降低电炉电压
四、实验数据及结果分析
测得结果后重新加大电压,使渣面再次熔化并将钼丝测头从渣中提出。
但仍保持在炉内。
逐渐减小炉子电压,待炉温到800℃
时,关电源降温,当T=150℃时,关闭冷却水及保护气。
实验2 球团矿的性能测试
一、球团矿与烧结矿冶金性能的比较
目前国内普遍认为球团矿比烧结矿在冶金性能上有以下优点:
(1)粒度小而均匀,有利于高炉料柱透气性的改善和气流的均匀分布。
通常球团粒度在8~16mm的占90%~95%以上。
这一点即使整粒最好的烧结矿也难以相比。
(2)冷度强度(抗压和抗磨)高。
在运输、装卸和贮存时产生粉末少。
(3)铁粉高和堆密度大,有利于增加高炉料柱的有效重量,提高产量和降低焦比。
(4)还原性好,改善煤气化学能的利用。
测定表明,在用低二氧化硅的优质原料时,球团矿与烧结矿的还原性相差不大,而使用二氧化硅较高的优质原料时,球团的还原性由于烧结矿。
二、球团矿的生产
球团矿的生产工艺主要有以下三种:竖炉法、带式焙烧机法和链蓖机一回转窑法。
1、竖炉球团法
现今有两种主要炉型。
一种炉型的特点是高炉身、无外部冷却器, 另一种是矮炉身,带单独的球团冷却器和热交换器。
竖炉法主要是为处理磁铁精矿而提出来的, 通过研完使用各种不同精矿之后认为;精矿的磁铁含量要尽量保持高些。
在一定条件下, 配入少量赤铁矿是可以容许的, 但是,在任何情况下, 精矿内的二价铁含量都应高于20%。
2、带式焙烧机球团法
对于带式焙烧机法来说, 最重要的一项进展可能就是带式机有效面积的增大, ,而仍旧保持鼓风干燥、,抽风干燥、抽风预热、抽风焙烧和鼓风冷却各工艺段的作用, 同时设计保持较高的工艺供热流的辅助设备。
近些年来, 向焙烧机提供热源的燃烧器有了改进。
现在, 在带式焙烧机上采用吸引式烧咀利用从焙烧系统回收的显热, 这已成为标准操作方式。
根据球团厂厂址的不同, 带式焙烧机一般采用的燃抖有天燃气或者6号燃油。
由子天燃气与燃油缺乏,目前,正在研究用煤作燃料。
3、链蓖机一回转窑法
与带式焙烧机法的情况相同, 链篦机一回转窑的重大进展, 也是设备规格的增大。
第一套工业性链蓖机一回转窑是用赤铁精矿作原料的, 设计能力为33万吨一年。
目前, 处理同类原料的链蓖机一回转窑球团厂, 单套机组的生产能力可超过400万吨/年。
如果焙烧磁铁矿,则同一套设备的产量会大大超过这一数字。
目前, 世界链蓖机一回转窑球团厂总生产能力估计约为9700万吨/年。
三、球团矿冶金性能的影响因素
(1)铁精矿的矿物类型。
生产球团矿常用的原料有磁铁矿和赤铁矿二种。
就成球性而言,
赤铁矿优于磁铁矿,就焙烧固结性能而言,则相反。
磁铁矿更易固结的原因有二:一为
焙烧过程中,磁铁矿发生氧化和晶变二为氧化放热效应。
赤铁矿则全靠高温下的再结晶,故要求更高的焙烧温度。
铁精矿中含有脉石,有的数量不多,但对焙烧固结有重要影响。
脉石矿物品种很多,其对球团固结的影响机理,不外乎能否与铁矿物反应,是否能成为液相,以及液相对铁矿物的润湿能力。
为了研究脉石的影响,以常见的石英和长石为例。
石英熔点甚高,在氧化气氛中,不与赤铁矿反应。
长石熔点较低,在焙烧温度下成为液相,并对赤铁矿润湿性强,极易渗入铁矿晶粒间隙。
现取极纯的赤铁矿精矿(含SiO2仅0.15%)分,别配以不同数量的石英粉、长石粉,在空气中以1250℃焙烧30分钟,然后测定其强度,并在显微镜下观察其结构,其结果见图1.石英不参与反应,故对强度无明显的影响,而长石熔融,渗入赤铁矿晶粒之间,形成液相渣键,只要有2%,便对固结影响显著。
还原性实验表明,石英对于球团矿的低温(550℃)、中温(900℃)还原性没有影响,只恶化其高温(1250℃)还原性。
长石将孔隙堵塞,并且封闭了部分赤铁矿表面,使球团矿的还原性全面降低。
铁精矿粒度和粒度组成对于固结的影响,与对成球性的影响一致。
粒度小,比表面积大,不仅有利于气一固相反应,而且有利于固一固相反应,它使磁铁矿氧化迅速,表面晶格缺陷较多,易于进行固相扩散反应。
所以原料粒度细,球团矿强度高。
此外粒度对气孔率和气孔大小有关,强度高的球团矿,其气孔必然小而均匀。
(2)焙烧温度的影响。
焙烧温度水平,对于球团矿固结影响最大。
一般认为温度愈高,反应速度愈快,对磁铁矿氧化反应如此,对赤铁矿扩散、再结晶也如此。
实际上,预热温度到达900°~1000℃以上,再提高温度对加速磁铁矿氧化作用不大。
赤铁矿或磁铁矿再结晶和晶粒长大的速度,主要决定于焙烧温度。
图2是焙烧温度对于球团矿抗压强度的影响。
由图可见,在1000℃以下,球团矿的强度增长缓慢。
只有更高的温度。
才能使其强度迅速提高。
对不同的原料制成的球团矿,适宜的焙烧温度各异。
在图2中,焙烧磁铁矿球团的适宜温度尚不及1200℃,这可能因为磁铁矿氧化成亦铁矿放热反应,使球团矿内部温度高于焙烧介质温度。
(3)加热速度的影响。
焙烧球团矿时,加热速度可以在120℃/分至57℃/分范围内变动。
对不同原料,要通过实验探求适宜的加热速度。
升温过快会使磁铁矿球团中心得不到充分氧化,升温过慢使设备生产率降低。
此外,球团矿导热性不良,升温过快使沿半径方向温差升高,因膨胀差异而产生裂纹,降低了球团矿的强度。
实验证明,降低加热速度到57~80℃/分,保持总焙烧时间不变,可使球团的强度,由88千克力/个(862.9852牛/个)增加到222千克力/个(2177.0763牛/个)。
图3是对我国某地球团矿实验的结果。
(4)高温下持续的时间。
球团矿固结过程中,一系列物理及化学变化,均需一定时间才能完成,因此必须在高温下持续一定时间。
为了研究球团矿在高温下持续时间的影响,以赤铁矿做成球团矿,其实验结果见图4.对于每一个温度水平,都有一相应的临界时间。
超过此时间,球团矿的强度不会再升高。
在1350℃以下,随温度水平升高,临界时间缩短。
(5)焙烧气氛的影响。
焙烧气氛的性质按含氧量而定,分类如下:
含O>8%: 强氧化气氛
含O:4~8%: 氧化性气氛
含O:1.5~4%: 弱氧化气氛
含O:1~1.5%: 中性气氛
焙烧气氛的性质,对于磁铁矿球团十分重要,它关系到磁铁矿的氧化。
为了使焙烧介质中含氧量达到需要的程度,应当使用高发热值燃料。
焙烧赤铁矿球团,虽然不存在氧化的要求,但要求较高的焙烧温度,故仍不能降低对燃料的要求。
(6)冷却的影响。
冷却是焙烧球团矿过程中的一个环节。
它虽然不直接作用于焙烧固结过程,却严重影响焙烧固结的后果。
过快的冷却速度,造成沿球团矿半径收缩不均,产生应力,使球团矿的强度降低。
见图5其中1-实验室试验;2-工业试验。
为了研究冷却对球团矿强度的影响,将磁铁矿精矿球团在1250℃下焙烧,然后分别以不同速度冷却。
结果发现,冷却速度为70~80℃/分时,球团矿的强度最高。
在工业生产中,为了获得高强度的球团矿,应以100℃/分的冷却速度,使球团矿降到运输皮带可以承受的温度,用喷水激冷,会严重破坏球团矿的强度。
参考文献:1、F e O 一51 0 2 一C a O 一M g O 系高镁炉渣粘度的测定,中南工业大学学报第二十八卷四期
2、高炉炉渣粘度的测定方法,马钢研究所,徐荣。