现代特种加工技术的发展及超声波加工的应用
超声波加工的应用

超声波加工的应用及发展前景摘要:随着生产发展和科学实验的需要,很多工业部门,尤其是国防工业部门,要求尖端科学技术向着高精度、高温、高压、大功率、小型化等方向发展。
因此,特种加工作为一个时代强音等上舞台,它就具备了上述特点。
超声波加工是利用工具断面的超声振动,通过磨料悬浮液加工脆硬材料的一种成型方法。
特别对于一些常规加工方式无法完成的或者加工精度无法达到要求的工件。
目前经过几十年的发展,超声波加工技术已逐步成熟,并已在一些要求条件高、加工工艺复杂、精度要求高的领域逐步发展起来,相信随着技术的发展它的应用围及领域会越来越广。
关键词:超声波;研究前沿;应用领域;超声加工的应用引言:超声波随着技术的发展越来越为人们所应用,他通过自身的一些特性一步步奠定自己在切削、拉丝模、深小孔加工等的地位。
特别在现代这个迅猛发展的社会它的地位越来越重要,我们应该加快它的发展速度,为我们所用。
超声波加工(USM)是利用工具端面作超声频振动,通过磨料悬浮液加工硬脆材料的一种加工方法。
超声波加工是磨料在超声波振动作用下的机械撞击和抛磨作用与超声波空化作用的综合结果,其中磨料的连续冲击是主要的。
加工时在工具头与工件之间加入液体与磨料混合的悬浮液,并在工具头振动方向加上一个不大的压力,超声波发生器产生的超声频电振荡通过换能器转变为超声频的机械振动,变幅杆将振幅放大到0.01~0.15mm,再传给工具,并驱动工具端面作超声振动,迫使悬浮液中的悬浮磨料在工具头的超声振动下以很大速度不断撞击抛磨被加工表面,把加工区域的材料粉碎成很细的微粒,从材料上被打击下来。
虽然每次打击下来的材料不多,但由于每秒钟打击16000次以上,所以仍存在一定的加工速度。
与此同时,悬浮液受工具端部的超声振动作用而产生的液压冲击和空化现象促使液体钻入被加工材料的隙裂处,加速了破坏作用,而液压冲击也使悬浮工作液在加工间隙中强迫循环,使变钝的磨料及时得到更新。
一、超声波加工的原理1.1 超声波概述“超声波”这个名词术语,用来描述频率高于人耳听觉频率上限的一种振动波,通常是指频率高于16kHz以上的所有频率。
超声波加工技术的研究与应用

超声波加工技术的研究与应用超声波是指频率大于20 kHz的机械波,因其具有易于调节、浅表性加工等优势,近年来在加工领域得到广泛应用,成为一种重要的新兴加工技术。
本文将从超声波加工技术的原理、特点、研究现状以及应用领域四个方面进行阐述。
一、超声波加工技术的原理超声波加工技术的核心原理是利用超声波传导的机械振动引起物体的微小位移,从而实现加工目的。
超声波加工技术通常采用高频振荡器产生超声波,其能量通过声波振幅传递到加工工具,再通过工具的振动作用于被加工物体。
这种超声波传导的振动能量有强烈的破坏性,可以使材料迅速产生渐进性断裂,从而进行相应的加工。
超声波加工技术可分为振动智能控制,超声冲击波加工控制,超声波整理和超声波车削几类。
二、超声波加工技术的特点超声波加工技术具有以下特点:(1)易于调节。
由于超声波频率可随意变换,所以加工过程中易于调控,不会对材料本身造成过大的损伤。
(2)针对表面加工。
由于超声波加工的振动频率大,因此只能实现浅表性的加工,通常用于表面修整、去毛刺、去污等精细处理。
(3)高效节能。
超声波加工技术的加工效率高,同时由于其加工方式具有局部性,因此能够充分利用能量,达到高效节能的目的。
三、超声波加工技术的研究现状目前,国内外对于超声波加工技术的研究大部分集中于超声波加工的机理、材料性能变化、加工参数优化等方面。
近年来,超声波加工技术在新材料加工领域得到广泛应用,如新型金属材料、高强度焊接材料等都可以用超声波加工来进行修整、加工、处理等。
此外,超声波加工技术还在精密加工、微机械加工等领域得到广泛应用,其中最典型的应用就是超声波打孔技术,多用于石英和陶瓷等硬质材料的加工。
四、超声波加工技术的应用领域超声波加工技术具有广泛的应用领域。
其中,应用最广的无疑是超声波手术刀,已成为现代微创手术的首选器械。
同时,在汽车、航空、航天、军工等领域,超声波加工技术也得到了广泛的应用,如超声波焊接、超声波清洗、超声波测厚等。
超声加工技术的应用及发展趋势
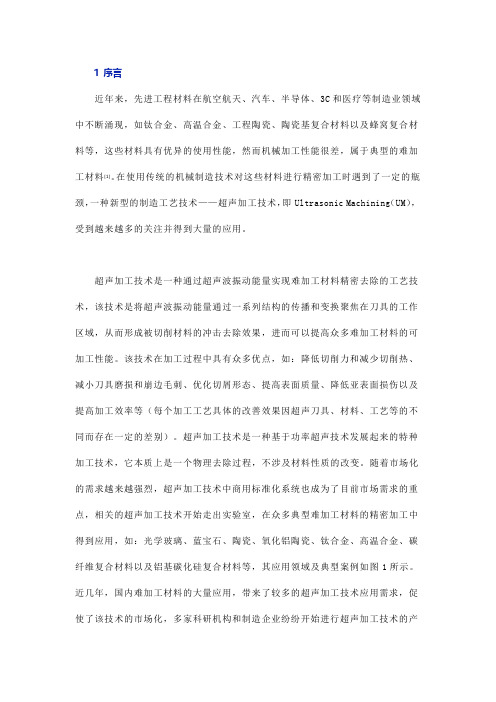
1 序言近年来,先进工程材料在航空航天、汽车、半导体、3C和医疗等制造业领域中不断涌现,如钛合金、高温合金、工程陶瓷、陶瓷基复合材料以及蜂窝复合材料等,这些材料具有优异的使用性能,然而机械加工性能很差,属于典型的难加工材料[1]。
在使用传统的机械制造技术对这些材料进行精密加工时遇到了一定的瓶颈,一种新型的制造工艺技术——超声加工技术,即Ultrasonic Machining(UM),受到越来越多的关注并得到大量的应用。
超声加工技术是一种通过超声波振动能量实现难加工材料精密去除的工艺技术,该技术是将超声波振动能量通过一系列结构的传播和变换聚焦在刀具的工作区域,从而形成被切削材料的冲击去除效果,进而可以提高众多难加工材料的可加工性能。
该技术在加工过程中具有众多优点,如:降低切削力和减少切削热、减小刀具磨损和崩边毛刺、优化切屑形态、提高表面质量、降低亚表面损伤以及提高加工效率等(每个加工工艺具体的改善效果因超声刀具、材料、工艺等的不同而存在一定的差别)。
超声加工技术是一种基于功率超声技术发展起来的特种加工技术,它本质上是一个物理去除过程,不涉及材料性质的改变。
随着市场化的需求越来越强烈,超声加工技术中商用标准化系统也成为了目前市场需求的重点,相关的超声加工技术开始走出实验室,在众多典型难加工材料的精密加工中得到应用,如:光学玻璃、蓝宝石、陶瓷、氧化铝陶瓷、钛合金、高温合金、碳纤维复合材料以及铝基碳化硅复合材料等,其应用领域及典型案例如图1所示。
近几年,国内难加工材料的大量应用,带来了较多的超声加工技术应用需求,促使了该技术的市场化,多家科研机构和制造企业纷纷开始进行超声加工技术的产业化应用。
图1超声加工应用领域及典型案例2 超声加工技术发展现状“工欲善其事,必先利其器”,超声加工技术是针对难加工材料精密加工的利器。
在大多数切削加工领域,超声加工更确切的名称应该为“超声辅助精密加工”,即在传统切削加工技术上辅助超声振动,从而实现特殊的材料去除效果。
超声波加工技术在制造业中的应用及发展
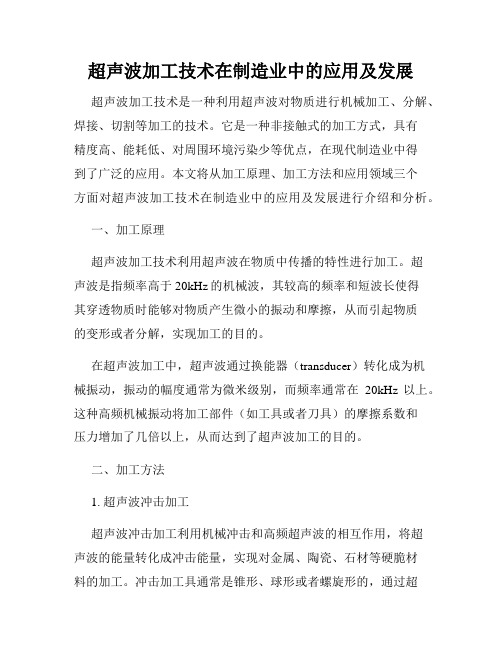
超声波加工技术在制造业中的应用及发展超声波加工技术是一种利用超声波对物质进行机械加工、分解、焊接、切割等加工的技术。
它是一种非接触式的加工方式,具有精度高、能耗低、对周围环境污染少等优点,在现代制造业中得到了广泛的应用。
本文将从加工原理、加工方法和应用领域三个方面对超声波加工技术在制造业中的应用及发展进行介绍和分析。
一、加工原理超声波加工技术利用超声波在物质中传播的特性进行加工。
超声波是指频率高于20kHz的机械波,其较高的频率和短波长使得其穿透物质时能够对物质产生微小的振动和摩擦,从而引起物质的变形或者分解,实现加工的目的。
在超声波加工中,超声波通过换能器(transducer)转化成为机械振动,振动的幅度通常为微米级别,而频率通常在20kHz以上。
这种高频机械振动将加工部件(如工具或者刀具)的摩擦系数和压力增加了几倍以上,从而达到了超声波加工的目的。
二、加工方法1. 超声波冲击加工超声波冲击加工利用机械冲击和高频超声波的相互作用,将超声波的能量转化成冲击能量,实现对金属、陶瓷、石材等硬脆材料的加工。
冲击加工具通常是锥形、球形或者螺旋形的,通过超声波的震动驱动,加工部分会发生爆炸性的形变和裂纹,从而实现加工的目的。
超声波冲击加工的优点是能够进行精细加工,但加工速度较慢,只适用于小加工量的生产。
2. 超声波切割加工超声波切割加工是利用超声波在物质中产生的高频振动,通过对切割工具施加高频振动,实现对材料的切割。
切割工具通常是金属薄板、金属丝、钻头和锯片等。
切割时,超声波的能量通过切割工具传递到材料中,使其发生振动和变形,从而实现切割的目的。
超声波切割加工的优点是能够进行高速切割,不会产生粉尘和机床磨损,但是对材料有一定的厚度限制。
3. 超声波焊接超声波焊接是利用超声波在物质中产生的高频振动,通过对金属表面施加振动,从而实现金属的焊接。
焊接时,将金属部分挤压在一起,在部件接触面上施加高频振动,使金属表面微观颗粒之间不断摩擦和碰撞,达到焊接的目的。
超声加工技术的应用现状及其发展趋势
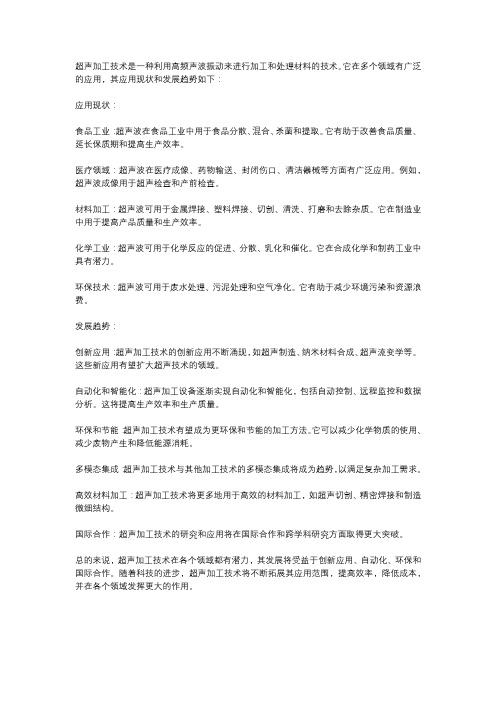
超声加工技术是一种利用高频声波振动来进行加工和处理材料的技术。
它在多个领域有广泛的应用,其应用现状和发展趋势如下:应用现状:食品工业:超声波在食品工业中用于食品分散、混合、杀菌和提取。
它有助于改善食品质量、延长保质期和提高生产效率。
医疗领域:超声波在医疗成像、药物输送、封闭伤口、清洁器械等方面有广泛应用。
例如,超声波成像用于超声检查和产前检查。
材料加工:超声波可用于金属焊接、塑料焊接、切割、清洗、打磨和去除杂质。
它在制造业中用于提高产品质量和生产效率。
化学工业:超声波可用于化学反应的促进、分散、乳化和催化。
它在合成化学和制药工业中具有潜力。
环保技术:超声波可用于废水处理、污泥处理和空气净化。
它有助于减少环境污染和资源浪费。
发展趋势:创新应用:超声加工技术的创新应用不断涌现,如超声制造、纳米材料合成、超声流变学等。
这些新应用有望扩大超声技术的领域。
自动化和智能化:超声加工设备逐渐实现自动化和智能化,包括自动控制、远程监控和数据分析。
这将提高生产效率和生产质量。
环保和节能:超声加工技术有望成为更环保和节能的加工方法。
它可以减少化学物质的使用、减少废物产生和降低能源消耗。
多模态集成:超声加工技术与其他加工技术的多模态集成将成为趋势,以满足复杂加工需求。
高效材料加工:超声加工技术将更多地用于高效的材料加工,如超声切割、精密焊接和制造微细结构。
国际合作:超声加工技术的研究和应用将在国际合作和跨学科研究方面取得更大突破。
总的来说,超声加工技术在各个领域都有潜力,其发展将受益于创新应用、自动化、环保和国际合作。
随着科技的进步,超声加工技术将不断拓展其应用范围,提高效率,降低成本,并在各个领域发挥更大的作用。
现代特种加工技术的发展及超声波加工的应用

现代特种加工技术的发展及超声波加工的应用摘要:简述了现代特种加工技术的特点及发展趋势,并在本文中论述超声波加工的应用。
关键词:特种加工技术超声波加工超声复合加工0 引言自20世纪50年代以来,随着生产和科学技术迅速发展,很多工业部门,尤其是国防工业部门要求尖端科技产品向高精度、高速度、耐高温、耐高压、大功率、小型化等方向发展、对机械制造部门提出了需要解决各种难切削材料、各种特殊复杂表面和各种超精、光整或具有特殊要求零件的加工问题。
欲解决上述一系列工艺问题,仅仅依靠传统的切削方法很难实现,甚至根本无法实现。
工艺师们独辟蹊径,借助各种能量形式,探寻新的工艺途径,于是各种异于传统切割加工方法的新型特种加工应运而生。
目前,特种加工技术已成为先进制造技术中不可缺少的分支,在难切割、复杂型面、精细表面、优质表面、低刚度零件及模具加工等领域中已成为重要的工艺方法。
1 现代特种加工技术的特点现代特种加工(special machining,SM)技术是借助电能、热能、光能、声能、电化学能、化学能及特殊机械能等多种能量或其复合以实现切除材料的加工方法。
与常规机械加工方法相比,它具有如下的特点。
●不受材料强硬度等限制。
特种加工技术主要不依靠机械力和机械能去除材料,而是主要用其他能量(如电、化学、光、声、热等)去除金属和非金属材料。
它们瞬时能量密度高,可以直接有效地利用各种能量,造成瞬时、局部熔化,以强力、高速爆炸、冲击去除材料。
其加工性能与工件材料以强硬度力学性能无关,故可以加工各种超强硬材料、高脆性及热敏材料以及特殊的金属和非金属材料。
●以柔克刚。
由于工具与工件不直接接触,加工时无明显的强大机械切削力,所以加工脆性材料和精密微细零件、薄壁零件、弹性元件时,工具硬度可低于被加工材料的硬度。
●向精密加工方向发展。
当前已出现了精密特种加工,许多特种加工方法同时又是精密加工方法、微细加工方法,如电子束加工、离子束加工、激光束加工等就是精密特种加工;精密电火花加工的加工精密可达微米级0.5一1μm,表面粗糙度可达镜面Ra0.02μm。
简述超声波加工的特点和应用范围

简述超声波加工的特点和应用范围
超声波加工是一种利用超声波来进行物体加工和处理的技术。
这种技
术具有许多独特的特点和应用范围,下面将对其进行简要介绍。
一、特点
1. 高精度:超声波可以精确地控制物体表面的处理程度,从而实现高
精度的加工效果。
2. 高效率:超声波加工速度快、效率高,可以大大提高生产效率。
3. 低损耗:超声波可以在不损坏物体表面的情况下进行处理,因此不
会造成物体的损耗,保持物体完整性。
4. 处理范围广泛:超声波可以用于处理各种材料,如金属、陶瓷、塑料、纸张等。
5. 节能环保:超声波加工不需要使用化学物质或其他有害物质,可以
减少环境污染,因此具有良好的节能环保效果。
二、应用范围
1. 加工生产:超声波加工可用于制造各种零部件及产品的加工,如飞机、汽车、电器等产品。
2. 精密加工:超声波加工可用于精密的加工领域,例如制造电子元件、医疗器械、钟表等精密产品。
3. 清洗处理:超声波还可用于清洗处理,例如清洗机器零件、玻璃器
皿、金属零件等。
4. 软物料处理:超声波可用于软物料的加工处理,如医用棉、食品、生物学样品等。
5. 医疗领域:超声波在医疗领域的应用范围也很广泛,如超声波胶囊内镜、超声治疗、透析等。
总之,超声波加工成为现代工业生产中不可或缺的一种技术。
其应用范围广泛,能够提高生产效率、降低成本,同时还有良好的节能环保效果。
随着技术的不断发展,相信超声波加工在未来还会发挥更加重要的作用。
超声加工技术的现状及其发展计划趋势

超声加工技术的现状及发展趋势前言:超声波加工是利用超声振动工具在有磨料的液体介质中或干磨料中产生磨料的冲击、抛磨、液压冲击及由此产生的气蚀作用来去除材料,或给工具或工件沿一定方向施加超声频振动进行振动加工,或利用超声振动使工件相互结合的加工方法。
超声波加工技术是一种涉及面广且更新快的机械加工技术。
结合近年来超声加工技术的发展状况,综述了超声振动系统的研究进展和超声加工技术在深小孔加工、拉丝模及型腔模具研磨抛光、难加工材料的加工、超声振动切削、超声复合加工等方面的最新应用,并阐述了超声加工技术的发展趋势。
关键词:超声波加工、超声振动、声复合加工、应用、发展、正文:1、超声振动系统的研究进展及其应用超声振动系统由换能器、变幅杆和工具头等部分组成,是超声设备的核心部分。
在传统应用中,超声振动系统大都采用一维纵向振动方式,并按“全调谐”方式工作。
但近年来,随着超声技术基础研究的进展和在不同领域实际应用的特殊需要,对振动系统的工作方式和设计计算、振动方式及其应用研究都取得了新的进展。
日本研究成功一种半波长弯曲振动系统,其切削刀具安装在半波长换能振动系统细端,该振动系统换能器的压电陶瓷片采用半圆形,上下各两片,组成上下两个半圆形压电换能器(压电振子),其特点是小型化,结构简单,刚性增强。
日本还研制成一种新型“纵-弯”型振动系统,并已在手持式超声复合振动研磨机上成功应用。
该系统压电换能器也采用半圆形压电陶瓷片产生“纵-弯”型复合振动。
日本金泽工业学院的研究人员研制了加工硬脆材料的超声低频振动组合钻孔系统。
将金刚石中心钻的超声振动与工件的低频振动相结合,制造了一台组合振动钻孔设备,该设备能检测钻孔力的变化以及钻孔精度和孔的表面质量,并用该组合设备在不同的振动条件下进行了一系列实验。
实验结果表明,将金刚石中心钻的超声振动与工件的低频振动相结合是加工硬脆材料的一种有效方法。
另一种超声扭转振动系统已在“加工中心”用超声扭转振动装置上应用。
- 1、下载文档前请自行甄别文档内容的完整性,平台不提供额外的编辑、内容补充、找答案等附加服务。
- 2、"仅部分预览"的文档,不可在线预览部分如存在完整性等问题,可反馈申请退款(可完整预览的文档不适用该条件!)。
- 3、如文档侵犯您的权益,请联系客服反馈,我们会尽快为您处理(人工客服工作时间:9:00-18:30)。
现代特种加工技术的发展及超声波加工的应用摘要:简述了现代特种加工技术的特点及发展趋势,并在本文中论述超声波加工的应用。
关键词:特种加工技术超声波加工超声复合加工0 引言自20世纪50年代以来,随着生产和科学技术迅速发展,很多工业部门,尤其是国防工业部门要求尖端科技产品向高精度、高速度、耐高温、耐高压、大功率、小型化等方向发展、对机械制造部门提出了需要解决各种难切削材料、各种特殊复杂表面和各种超精、光整或具有特殊要求零件的加工问题。
欲解决上述一系列工艺问题,仅仅依靠传统的切削方法很难实现,甚至根本无法实现。
工艺师们独辟蹊径,借助各种能量形式,探寻新的工艺途径,于是各种异于传统切割加工方法的新型特种加工应运而生。
目前,特种加工技术已成为先进制造技术中不可缺少的分支,在难切割、复杂型面、精细表面、优质表面、低刚度零件及模具加工等领域中已成为重要的工艺方法。
1 现代特种加工技术的特点现代特种加工(special machining,SM)技术是借助电能、热能、光能、声能、电化学能、化学能及特殊机械能等多种能量或其复合以实现切除材料的加工方法。
与常规机械加工方法相比,它具有如下的特点。
●不受材料强硬度等限制。
特种加工技术主要不依靠机械力和机械能去除材料,而是主要用其他能量(如电、化学、光、声、热等)去除金属和非金属材料。
它们瞬时能量密度高,可以直接有效地利用各种能量,造成瞬时、局部熔化,以强力、高速爆炸、冲击去除材料。
其加工性能与工件材料以强硬度力学性能无关,故可以加工各种超强硬材料、高脆性及热敏材料以及特殊的金属和非金属材料。
●以柔克刚。
由于工具与工件不直接接触,加工时无明显的强大机械切削力,所以加工脆性材料和精密微细零件、薄壁零件、弹性元件时,工具硬度可低于被加工材料的硬度。
●向精密加工方向发展。
当前已出现了精密特种加工,许多特种加工方法同时又是精密加工方法、微细加工方法,如电子束加工、离子束加工、激光束加工等就是精密特种加工;精密电火花加工的加工精密可达微米级0.5一1μm,表面粗糙度可达镜面Ra0.02μm。
●可同时实现粗、精加工。
特种加工中的能量易于实现转换和控制,工件在一次装夹中可实现粗、精加工,有利于保证加工精度,提高生产率。
●用简单运动加工复杂形面。
特种加工技术只需简单的进给运动即可加工出三维复杂形面。
特种加工技术已成为复杂形面的主要加工手段。
●可以获得良好的表面质量。
由于在特种加工过程中,工件表面不会产生强烈的弹、塑性变形,故有些特种加工方法可获得良好的表面粗糙度。
热应力、残余应力、冷作硬化、热影响区及毛刺等表面缺陷均比机械切割表面小。
●各种加工方法可以任意复合。
各种加工方法的任意复合可扬长避短,形成新的复合工艺方法,更突出其优越性,便于扩大应用范围。
由于特种加工技术具有其他常规加工技术无法比拟的优点,在现代加工技术中,占有越来越重要的地位。
表面粗糙度Ra<0.01μm的超精密表面加工,非采用特种加工技术不可。
如今,特种加工技术的应用已遍及从民用到军用的各个加工领域。
2 超声波加工技术的发展历程超声加工起源于20世纪50年代初。
最早研究超声加工技术的国家是日本。
70年代中期,日本对振动切削与超声磨削方面的研究已相当深入且已应用于生产。
日本研究超声振切最有权威的代表人物主要有两位:一位是中央大学的岛川正憲,他出版的是《超音波工学——理论和实际》;另一位是宇都宫大学的隈部淳一郎教授,他在1956年提出了系统的振动切削理论,发表了大量的论文,出版了《精密加工、振动切削基础及应用》专著,首先把振动切削理论成功地应用于车、刨、铣、钻、镗、铰、拉、磨削、螺纹加工、齿轮加工、抛光、珩磨、拉伸与挤压等冷热加工领域,取得了意想不到的效果与显著的经济效益。
20世纪50年代末60年代初,原苏联对超声加工研究也发表过很有价值的论文。
其在超声车削、磨削、光整加工、复合加工等方面均有生产应用,并取得了良好的经济效益。
1973年,前苏联召开了一次全国性的讨论会,充分肯定了超声加工的经济效果和实用价值,对这项新技术在全国的推广应用起到了积极的作用。
美国于20世纪60年代初开始对超声加工进行研究。
由于当时超声加工技术还不是很成熟,包括声振系统、换能器、发生器的设计制造和质量都较差,因此停止了其研究工作。
在20世纪70年代中期,其超声钻中心孔、光整加工、磨削、拉管和焊接等方面,已处于生产应用阶段;超声车削、钻孔、镗孔已处于试验性生产设备原形阶段;通用超声振动切削系统已供工业应用,目前已形成部分标准。
我国超声加工的研究始于20世纪50年代末,由于当时超声波发生器、换能器、声振系统的不成熟,缺乏合理的组织和持续的研究工作,很快就冷了下来。
目前,吕正兵、徐家文对工程陶瓷超声加工进行了基础的实验研究,得出了工程陶瓷超声加工的一些规律,为今后工程陶瓷的应用提供了更为广阔的前景;王超群等人利用改装后的数控超声加工装置对Al2O3进行了工艺试验,其数控超声加工是对传统超声加工的技术创新,具有传统超声加工所无法比拟的特点,初步掌握了对Al2O3的加工工艺规律。
梁晶晶等人用超声加工技术对陶瓷进行的加工中,介绍了超声加工的原理和特点,综述了国内外超声加工在陶瓷材料加工方面的应用研究,并对二维超声振动磨削加工技术在陶瓷加工中的可行性进行了分析,为拓展超声加工应用领域与技术发展提供借鉴。
郑建新等人通过数学物理模型分析超声加工声学系统的动力学规律,探讨工具杆的局部共振现象,得出当工具杆发生局部共振时,变幅杆和工具杆连接处为位移节点,且此时系统处于谐振状态的结论;并推导了超声波发生器的可调频率范围与刀具杆的磨损率关系。
随着超声加工设备的不断完善和理论研究的不断深入,它将在我国技术进步和社会主义现代化建设中起到重要的作用。
3 超声加工技术的应用目前超声加工主要应用于:超声切削加工、超声磨削加工、超声光整加工、超声塑性加工、磨料冲击加工、超声焊接等,随着超声加工研究的不断深入,它的应用范围还将继续扩大。
3.1 超声振动切削日本学者隈部淳一郎在20世纪50-60年代首先发表了许多振动切削方面的论文,系统地提出了振动切削理论,并成功地实现了振动车削、振动铣削、振动镗削、振动刨削、振动磨削等。
随后,美国也对振动切削进行了研究,到20世纪70年代中叶,振动车削、振动钻孔、振动磨削、光整加工等均已达到实用阶段,超声加工在难加工材料和高精度零件的加工方面显示了很大的优越性,并在生产中得到推广应用。
日本学者采用低频率(3000-5000Hz)振动切削方法,并用于切削纤维型材料(如金属短纤维)。
程雪利等人在对超声振动切削SiCp/Al复合材料的刀具磨损进行研究中,分别采用了超声切削和普通切削两种方式对SiCp/Al复合材料进行了车削试验,研究了切削参数对硬质合金YG6刀具磨损的影响规律,并在同等条件下与聚晶金刚石( PCD )刀具进行了对比。
研究发现,超声切削的刀具磨损量要小于普通切削的刀具磨损量;超声切削时,PCD刀具的磨损量约为YG6刀具磨损量的1/10,这点和普通切削十分相似。
丁黎光、李建光在超声振动切削夹片的应用研究中,利用振动切削机理,针对锚具夹片精加工存在的问题,研究将超声振动切削用于夹片加工。
实验分析表明,该方法不仅保证了加工质量,还可提高加工效率、减轻劳动强度和降低产品成本等。
马春翔、胡德金对超声椭圆振动切削技术进行了研究,阐述了超声波椭圆振动切削原理和刀具椭圆振动系统,分析了超声波椭圆振动切削运动特性,介绍了超声波椭圆振动切削的实际切削效果。
随着科学技术的发展和进步,超声波振动切削作为一种新技术正在逐步渗透到各个领域,对超声波振动切削的研究和开发也越来越受到人们的普遍重视。
显然,加强对超声波振动切削技术的研究、推广和应用,对提高机械制造业的加工水平和加快新产品开发具有十分重要的意义。
3.2 超声磨削加工超声磨削加工是一种复合特种加工过程,其利用工件的脆性,使电镀金刚石的工具磨头以超声频(20kHz左右)和一定的振幅(20μm或更大)振动,并加以高速旋转,通过磨削液中的磨粒对工件进行高速撞击、超声空化、电镀金刚石砂轮磨粒的磨削,达到材料去除的目的。
其优点是加工效率高,缺点是加工变质层较深。
日本学者对传统无心磨削进行改进,提出一种超声辅助磨削的加工方法——超声制动无心磨削。
该方法是利用带超声振动的制动块端部产生椭圆形轨迹对工件旋转速度进行控制和支撑,能加工出直径小于100μm和大长径比的圆柱形工件。
于思远等人做了超声磨削加工工程陶瓷小孔的实验研究,李瑜等人在对纳米ZrO2陶瓷二维超声磨削温度影响因素分析中,采用了人工热电偶法,通过普通磨削和二维超声振动磨削的对比实验,回归分析了磨削深度、砂轮速度、工作台速度等磨削参数对纳米ZrO2陶瓷磨削温度的影响。
另外,对纳米ZrO2陶瓷这种非线性材料的磨削加工进行有限元仿真,比较实验测量数据与仿真结果,确定了仿真分析对实际情况的指导作用。
目前,许多学者在对工程陶瓷加工技术进行研究,而以超声磨削技术研究为最多。
超声磨削技术加工能有效抑制砂轮堵塞,因此可使用普通的金属结合剂砂轮,这可减少金刚石砂轮的消耗,降低成本。
超声振动磨削最显著的特点是加工效率比普通磨削高一倍以上:一是可采用较大磨削用量;二是明显减少了砂轮修整时间。
因而利用超声振动磨削技术加工工程陶瓷具有广阔的研究和应用前景。
3.3 超声光整加工超声光整加工的应用目前包括超声珩磨、超声珩齿、超声抛光、超声研磨、电火花超声复合加工、超声强化等等。
已有研究证明:将电解加工、机械研磨及超声加工相复合形成一种新型的光整加工技术——电化学超精密研磨,选取适当的工艺参数进行光整加工,可以获得表面粗糙度Ra0.025μm,效率较普通研磨提高10倍以上。
祝锡晶、王爱玲等人采用超声珩磨在发动机缸套光整加工中的应用研究中发现,由于普通珩磨导致油石堵塞,加工效率低,尤其是在珩磨铜、铝、钛合金等韧性材料管件时,油石极易堵塞,从而导致油石寿命的过早结束,零件加工表面质量差,加工效率很低。
而采用的新型特种加工方法——超声珩磨技术,相对普通珩磨具有珩磨力小、珩磨温度低、精度高、表面质量高及油石磨损小、效率高等特点。
丁金福等人在对超声振动的挤滚压光整加工变幅特性分析及应用中得出,利用超声振动挤滚压装置以车削式加工方法代替磨削及抛光两道加工工序,极大地提高了生产效率,降低了生产成本,并在一定程度上达到了表面强化的效果,对提高工件表面强度、耐磨性及耐蚀性起到了积极的作用。
鉴于超声光整加工应用在解决韧性材料、硬脆材料加工问题上开辟了一条新的途径,具有广阔的应用前景。
特别是超声珩磨加工工艺,能高效地加工出高精度、高表面质量、高耐磨性的缸套(尤其是薄壁缸套),对我国提升汽车、拖拉机、摩托车等行业的加工水平大有益处。