紫外激光加工技术在硅片晶圆中的应用
激光-硅片作用机理
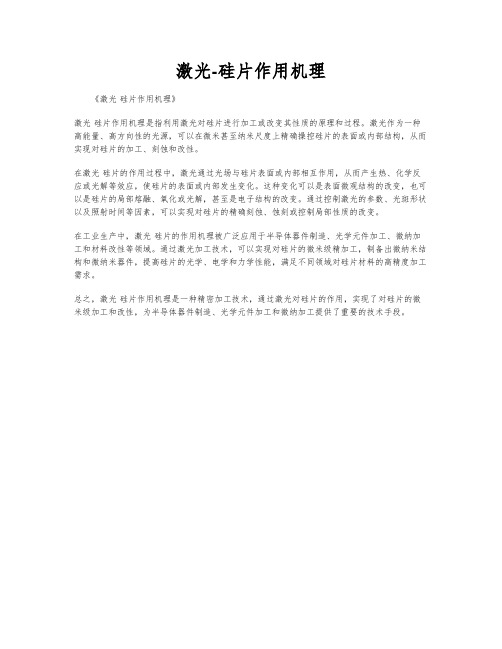
激光-硅片作用机理
《激光-硅片作用机理》
激光-硅片作用机理是指利用激光对硅片进行加工或改变其性质的原理和过程。
激光作为一种高能量、高方向性的光源,可以在微米甚至纳米尺度上精确操控硅片的表面或内部结构,从而实现对硅片的加工、刻蚀和改性。
在激光-硅片的作用过程中,激光通过光场与硅片表面或内部相互作用,从而产生热、化学反应或光解等效应,使硅片的表面或内部发生变化。
这种变化可以是表面微观结构的改变,也可以是硅片的局部熔融、氧化或光解,甚至是电子结构的改变。
通过控制激光的参数、光斑形状以及照射时间等因素,可以实现对硅片的精确刻蚀、蚀刻或控制局部性质的改变。
在工业生产中,激光-硅片的作用机理被广泛应用于半导体器件制造、光学元件加工、微纳加工和材料改性等领域。
通过激光加工技术,可以实现对硅片的微米级精加工,制备出微纳米结构和微纳米器件,提高硅片的光学、电学和力学性能,满足不同领域对硅片材料的高精度加工需求。
总之,激光-硅片作用机理是一种精密加工技术,通过激光对硅片的作用,实现了对硅片的微米级加工和改性,为半导体器件制造、光学元件加工和微纳加工提供了重要的技术手段。
极紫外光刻的原理及应用

极紫外光刻的原理及应用1. 引言极紫外光刻(又称EUV光刻)是一种先进的微影技术,它使用极紫外(EUV)光源进行光刻,并广泛应用于半导体制造中。
本文将介绍极紫外光刻的原理,以及它在半导体行业中的应用。
2. 极紫外光刻的原理极紫外光刻使用的光源是极紫外辐射,其波长为13.5纳米,远远短于传统光刻技术所使用的193纳米深紫外光。
极紫外光源的产生涉及复杂的物理过程,包括激光产生等离子体、从等离子体中产生极紫外光等步骤。
极紫外光刻使用的掩模还需要比传统光刻技术更高的反射率和更低的光散射率。
这是因为极紫外光源的波长很短,对掩模上细微缺陷的敏感度更高。
因此,制造高质量掩模对于极紫外光刻的成功应用至关重要。
3. 极紫外光刻的应用3.1 半导体制造极紫外光刻在半导体行业中有重要的应用。
随着半导体器件的尺寸越来越小,传统光刻技术已经无法满足制造高密度芯片的需求。
而极紫外光刻技术通过使用更短的波长,可以实现更高的分辨率和更小的线宽。
因此,它被广泛应用于半导体制造中,特别是在制造7纳米及以下尺寸的芯片中。
3.2 光刻机制造极紫外光刻技术的发展也推动了光刻机制造行业的发展。
光刻机是进行光刻过程的装置,它将掩模上的图形投影到光刻胶上,形成图案。
随着极紫外光刻技术的普及,对于光刻机的性能和稳定性的要求也越来越高。
因此,光刻机制造商需要不断改进技术,以适应极紫外光刻的要求。
3.3 研究和发展极紫外光刻作为一项新的微影技术,也需要不断的研究和发展。
许多研究机构和企业致力于提高极紫外光刻的性能和稳定性,以推动其应用的进一步发展。
此外,极紫外光刻在其他领域的应用也正在受到研究者的关注,如光学元件制造、生物医学和纳米技术等领域。
4. 极紫外光刻的优势和挑战极紫外光刻相比于传统光刻技术具有以下优势: - 更高的分辨率,可以制造更小的芯片尺寸。
- 更高的工艺容差,可以制造更复杂的器件结构。
- 更低的成本,可以提高生产效率。
然而,极紫外光刻也面临着一些挑战: - 极紫外光源的稳定性和可靠性需要进一步提高。
紫外光刻机技术的研究与发展趋势

紫外光刻机技术的研究与发展趋势一、背景介绍紫外光刻技术是一种高精度、高分辨率的制造微电子器件的重要方法之一。
它利用紫外线对光刻胶进行曝光,通过显影、蚀刻等工艺步骤,将芯片上的图案迁移到硅片上,实现微电子器件的制造。
近年来,紫外光刻机技术在半导体制造、集成电路、显示器件等领域得到了广泛应用。
二、技术发展趋势1. 高分辨率化随着科技的不断进步,对微电子器件的制造要求也越来越高,尤其是对分辨率的要求。
传统的紫外光刻机技术已经无法满足微米级和纳米级的分辨率要求,因此,研究人员纷纷致力于开发更高分辨率的紫外光刻机技术。
包括多光束、电子束和极紫外光刻等新技术应运而生,努力提高分辨率,满足市场需求。
2. 多级曝光技术随着半导体器件尺寸的不断缩小,传统的单级曝光技术已经无法满足需求。
多级曝光技术通过多次曝光和对位,将一个芯片的图案分成多个子图案逐步曝光,最后形成一个完整的图案。
这种技术在提高整体曝光效率的同时,还可以提高分辨率并减小误差。
3. 高速刻蚀技术为了满足大规模集成电路的制造需求,紫外光刻机的刻蚀速度需要得到提高。
高速刻蚀技术通过优化刻蚀气体、调节蚀刻条件等方式,实现更高效的刻蚀过程。
同时,还可以提高刻蚀平坦度和减小副反应,降低产生缺陷的风险。
4. 绿色环保技术随着社会环保意识的增强,绿色环保技术成为紫外光刻机研究的一个重要方向。
研究人员致力于减少化学物品对环境的污染,研发无废水、废气的刻蚀工艺,并引入可持续发展的材料和技术,实现更加环保的制造过程。
5. 智能化与自动化随着人工智能和自动化技术的发展,紫外光刻机技术也逐渐向智能化和自动化方向发展。
通过引入智能控制系统、自动对位对焦技术等,提高生产线的自动化程度,降低人力投入和人为误差,并提高生产效率和产品质量。
三、结论紫外光刻机技术是现代微电子制造领域不可或缺的重要技术。
随着科技的不断进步和应用需求的增加,对紫外光刻技术的要求也越来越高。
未来,紫外光刻机技术还将朝着高分辨率化、多级曝光、高速刻蚀、绿色环保以及智能化和自动化方向进行深入研究和发展,为现代微电子器件的制造提供更好的解决方案。
硅片到晶圆过程
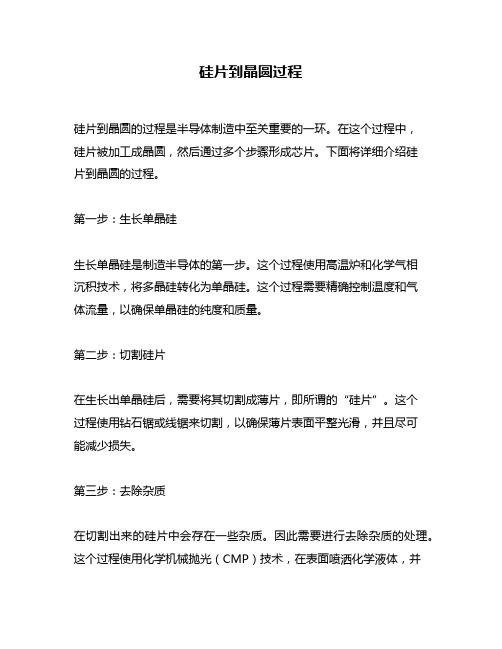
硅片到晶圆过程硅片到晶圆的过程是半导体制造中至关重要的一环。
在这个过程中,硅片被加工成晶圆,然后通过多个步骤形成芯片。
下面将详细介绍硅片到晶圆的过程。
第一步:生长单晶硅生长单晶硅是制造半导体的第一步。
这个过程使用高温炉和化学气相沉积技术,将多晶硅转化为单晶硅。
这个过程需要精确控制温度和气体流量,以确保单晶硅的纯度和质量。
第二步:切割硅片在生长出单晶硅后,需要将其切割成薄片,即所谓的“硅片”。
这个过程使用钻石锯或线锯来切割,以确保薄片表面平整光滑,并且尽可能减少损失。
第三步:去除杂质在切割出来的硅片中会存在一些杂质。
因此需要进行去除杂质的处理。
这个过程使用化学机械抛光(CMP)技术,在表面喷洒化学液体,并使用旋转机械进行抛光。
这样可以使硅片表面更加平整,去除杂质。
第四步:涂层在去除杂质后,需要将硅片表面涂上一层光刻胶。
这个过程使用旋涂机器将光刻胶均匀地涂在硅片表面,然后通过烘干和曝光来固化胶层。
第五步:曝光在固化了光刻胶之后,需要进行曝光。
这个过程使用掩膜对硅片进行遮盖,并使用紫外线照射来形成芯片的图案。
这个过程需要精确控制曝光时间和强度,以确保芯片的精度和质量。
第六步:蚀刻在完成曝光之后,需要进行蚀刻。
这个过程使用化学反应来去除未被固化的部分光刻胶,并将芯片图案暴露出来。
然后使用等离子体技术或湿式蚀刻技术来将芯片图案转移到硅片表面。
第七步:清洗在完成蚀刻之后,需要对芯片进行清洗以去除残留的化学物质和杂质。
这个过程通常使用纯水或溶剂进行清洗。
第八步:检验在完成清洗之后,需要对芯片进行检验。
这个过程使用显微镜和其他测试设备来检查芯片的质量和精度。
如果发现问题,需要返回前面的步骤进行修正。
第九步:切割晶圆在完成检验之后,硅片被切割成晶圆。
这个过程使用钻石锯或线锯来切割,并且需要精确控制切割角度和深度,以确保晶圆质量。
最后,晶圆通过多个步骤形成芯片。
这些步骤包括沉积、扩散、离子注入、蚀刻等等。
每个步骤都需要精确控制温度、气体流量和时间等参数,以确保芯片的质量和性能。
苏大维格光刻机的原理
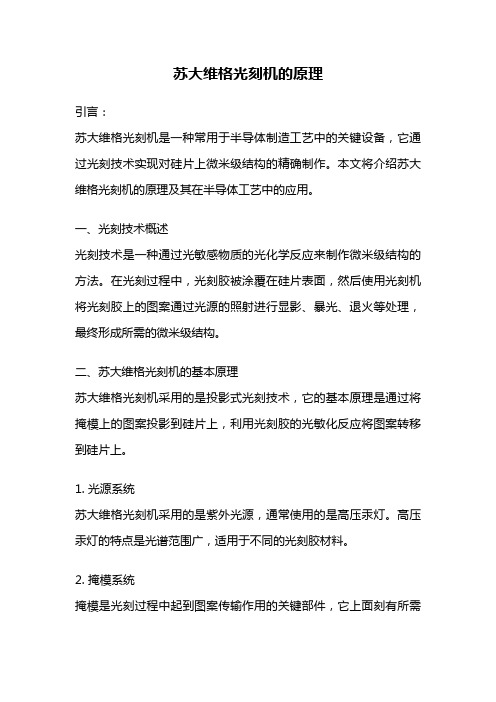
苏大维格光刻机的原理引言:苏大维格光刻机是一种常用于半导体制造工艺中的关键设备,它通过光刻技术实现对硅片上微米级结构的精确制作。
本文将介绍苏大维格光刻机的原理及其在半导体工艺中的应用。
一、光刻技术概述光刻技术是一种通过光敏感物质的光化学反应来制作微米级结构的方法。
在光刻过程中,光刻胶被涂覆在硅片表面,然后使用光刻机将光刻胶上的图案通过光源的照射进行显影、暴光、退火等处理,最终形成所需的微米级结构。
二、苏大维格光刻机的基本原理苏大维格光刻机采用的是投影式光刻技术,它的基本原理是通过将掩模上的图案投影到硅片上,利用光刻胶的光敏化反应将图案转移到硅片上。
1. 光源系统苏大维格光刻机采用的是紫外光源,通常使用的是高压汞灯。
高压汞灯的特点是光谱范围广,适用于不同的光刻胶材料。
2. 掩模系统掩模是光刻过程中起到图案传输作用的关键部件,它上面刻有所需的微米级图案。
苏大维格光刻机的掩模系统采用了高精度的掩模台,能够对掩模进行精确的定位和对准。
3. 投影系统苏大维格光刻机的投影系统采用了光学透镜和反射镜的组合,通过将掩模上的图案投影到硅片上。
投影系统的关键是保证光学系统的分辨率和光学畸变控制。
4. 显影系统在光刻胶上暴光后,需要进行显影处理。
苏大维格光刻机的显影系统采用了旋涂式显影装置,通过旋转硅片来实现显影剂的均匀覆盖和显影。
5. 定位系统苏大维格光刻机的定位系统采用了双重定位技术,即通过视觉定位和机械定位相结合的方式来实现对硅片和掩模的精确定位。
三、苏大维格光刻机在半导体工艺中的应用苏大维格光刻机在半导体工艺中有着广泛的应用,主要包括以下几个方面:1. 制作光刻胶图案苏大维格光刻机能够将掩模上的图案投影到光刻胶上,并通过显影、暴光等处理形成所需的微米级结构。
这些结构可以用于制作晶体管、电容器等微电子器件。
2. 制作光掩膜光掩膜是半导体工艺中常用的掩模,用于传输图案到硅片上。
苏大维格光刻机能够将掩模上的图案进行投影,通过显影、暴光等处理形成所需的图案。
12寸硅片晶圆 -回复
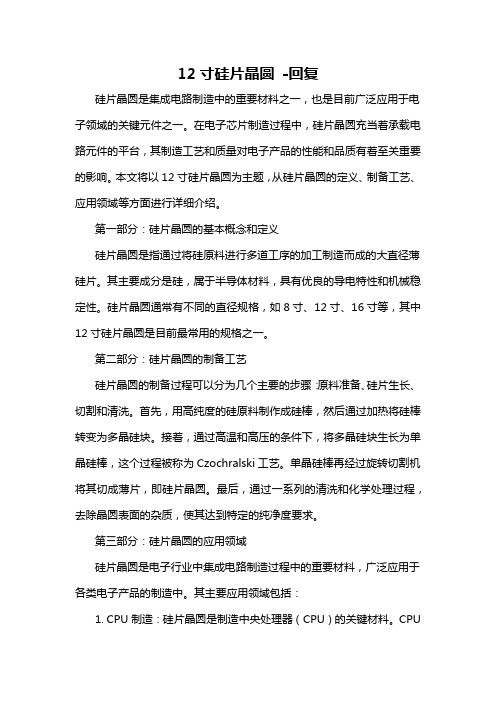
12寸硅片晶圆-回复硅片晶圆是集成电路制造中的重要材料之一,也是目前广泛应用于电子领域的关键元件之一。
在电子芯片制造过程中,硅片晶圆充当着承载电路元件的平台,其制造工艺和质量对电子产品的性能和品质有着至关重要的影响。
本文将以12寸硅片晶圆为主题,从硅片晶圆的定义、制备工艺、应用领域等方面进行详细介绍。
第一部分:硅片晶圆的基本概念和定义硅片晶圆是指通过将硅原料进行多道工序的加工制造而成的大直径薄硅片。
其主要成分是硅,属于半导体材料,具有优良的导电特性和机械稳定性。
硅片晶圆通常有不同的直径规格,如8寸、12寸、16寸等,其中12寸硅片晶圆是目前最常用的规格之一。
第二部分:硅片晶圆的制备工艺硅片晶圆的制备过程可以分为几个主要的步骤:原料准备、硅片生长、切割和清洗。
首先,用高纯度的硅原料制作成硅棒,然后通过加热将硅棒转变为多晶硅块。
接着,通过高温和高压的条件下,将多晶硅块生长为单晶硅棒,这个过程被称为Czochralski工艺。
单晶硅棒再经过旋转切割机将其切成薄片,即硅片晶圆。
最后,通过一系列的清洗和化学处理过程,去除晶圆表面的杂质,使其达到特定的纯净度要求。
第三部分:硅片晶圆的应用领域硅片晶圆是电子行业中集成电路制造过程中的重要材料,广泛应用于各类电子产品的制造中。
其主要应用领域包括:1. CPU制造:硅片晶圆是制造中央处理器(CPU)的关键材料。
CPU是电子产品中的核心组件,需经过高精度的工艺制造。
而使用12寸硅片晶圆能够提高芯片的制造效率和晶圆利用率,降低制造成本,进一步提升CPU性能。
2. 存储器生产:硅片晶圆也用于制造各种类型的存储器,如内存芯片、闪存芯片等。
随着计算机技术的不断发展,存储器的容量和速度都在不断提高,而12寸硅片晶圆能够满足更高集成度和更大容量的存储器芯片的制造需求。
3. 太阳能电池板制造:硅片晶圆还可以用于太阳能电池板的制造。
太阳能电池板利用光能直接发电,其关键元件就是硅片晶圆。
半导体晶圆检测关键连续波深紫外激光光源研制

第53卷第4期2024年4月人㊀工㊀晶㊀体㊀学㊀报JOURNAL OF SYNTHETIC CRYSTALS Vol.53㊀No.4April,2024简㊀㊀讯半导体晶圆检测关键连续波深紫外激光光源研制徐国锋,王正平,王树贤,武㊀奎,梁㊀飞,路大治,张怀金,于浩海(山东大学晶体材料研究院,晶体材料国家重点实验室,济南㊀250100)深紫外激光是半导体领域的关键光源㊂基于非线性频率变换的全固态深紫外激光具有结构紧凑㊁价格低廉等优势,有广泛需求㊂受限于晶体非线性系数较线性介电常数小数个数量级,深紫外激光通常以具有高峰值(千瓦级)的脉冲形式获得,连续波深紫外激光效率较低,其实用化极其困难㊂高峰值的紫外激光通常会对半导体表面及内部产生损伤,限制了半导体晶圆缺陷等装备的应用和发展㊂当前,晶圆检测用关键瓦级连续波深紫外激光器制备技术被国外极少数几家企业高度垄断,我国相关研究和产业化技术急需发展㊂在我国多个项目的持续支持下,基于前期研究,山东大学晶体材料国家重点实验室于浩海教授㊁张怀金教授相关团队提出了瓦级连续波深紫外激光器设计方案,并解决了稳定性㊁高效输出及紫外损伤的系列工程化难题,研制出国内首台瓦级连续波深紫外激光器整机(见图1),激光波长为261nm,功率波动RMS <1%,达到实用化要求,稳定性等关键指标达到国际文献报道最优水平㊂与国外高度垄断的266nm 激光器相比,该激光器具有结构更紧凑㊁波长更短㊁效率更高㊁分辨率更高等优势,填补了国内市场空白,为我国晶圆检测装备的全国产化自主研发奠定了关键光源基础㊂同时,针对SiC㊁GaN 等宽禁带半导体的检测需求,也研制出了瓦级320nm 连续波深紫外激光器整机(见图2),可服务于我国第三代半导体产业的高速发展㊂目前,上述成果的核心技术已转让到有维光电有限公司,着力开展批量化生产㊂图1㊀瓦级261nm 连续波深紫外激光器㊂(a)整机照片;(b)激光光谱及功率稳定性(RMS =0.66%)图2㊀瓦级320nm 连续波深紫外激光器㊂(a)整机照片;(b)激光光谱及功率稳定性(RMS =0.81%)。
紫外激光晶圆划片及其优点介绍
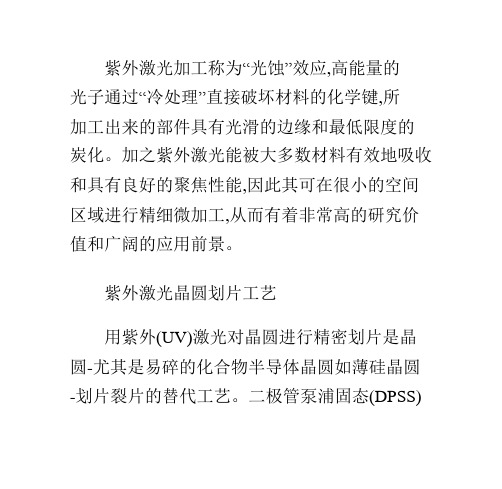
力夹在了那本书里,还给了袁慕野。木子不再是那个什么不懂的小女孩了,她知
时间变长,因为必须对每一个裸片进行单独的对 准操作以保证自动测试的正确进行。有时会因为 裸片没有对准而对成品率发生影响。激光划片工 艺允许晶圆在薄膜片上进行测试,这就大大地缩 短了测试时间,使所有的裸片都能通过自动测试 工序。
在所有窄带紫外光源中准分子激光器所提 供的功率最大、波长最短(351,308,248,193,以 及 157nm)。准分子激光的光子成本低于 DPSS 激
光,但是,其系统的复杂度较高且存在维护难和 其他问题,因此并不是晶圆切割工艺的理想选 择。准分子激光的优势在于微机械加工、大面积 图案转移和大量平行区域的分步重复工艺。而紫 外 DPSS 激光则更适于晶圆划片应用。借助于准 分子激光(193nm),JPSA能在一个小时内处理3片 晶圆,每片成本为 8 美元,系统正常运行时间为 97%。这是准分子激光系统所能达到的非常好的 性能状态。而一个优化的紫外 DPSS 激光(266nm) 系统每小时能处理 7 到 10 片晶圆,每片成本低于 1.50 美元,正常运行时间﹥99.9%。这两种工艺已 经在多台设备上,每周 7 天/每天 24 小时地连续
力集中,但这种应力很容易消除。
激光工艺的优点
在划片-裂片工艺中,PCM 图形必须设计有直 通式划片槽。金刚石划片工艺不能通过 PCM 图形 进行连续划片。因而 PCM 图形必须设计有划片槽。 这就带来了 PCM 图形测试的问题。但是,对于激 光划片工艺,PCM 图形设计已不再是一个问题了。 PCM 图形可以设计成有助于当前正在完成的测试 项目,而不是有助于裂片方法的要求。即使没有 划片槽,激光划片工艺也不会中断。
- 1、下载文档前请自行甄别文档内容的完整性,平台不提供额外的编辑、内容补充、找答案等附加服务。
- 2、"仅部分预览"的文档,不可在线预览部分如存在完整性等问题,可反馈申请退款(可完整预览的文档不适用该条件!)。
- 3、如文档侵犯您的权益,请联系客服反馈,我们会尽快为您处理(人工客服工作时间:9:00-18:30)。
武汉元禄光电技术有限公司
紫外激光加工技术在硅晶圆中的应用
硅材料是地壳中最为丰富的元素半导体,是电子器件中主要的原材料,广泛应用于大规模集成电路领域,我们所熟知的产品有晶圆。
晶圆是半导体行业中最前沿的技术产品,一切的半导体技术从晶圆开始,晶圆我们常称之为硅晶片或硅晶圆。
晶圆的加工是半导体制程中的重要环节,其加工制成也体现着一个国家的先进技术,代表着国家的竞争力。
早在四月份,国内就出现半导体技术被欧美国家卡脖子的情况,引起了大家的广泛关注,同时,也激起了发愤图强,发展半导体技术的口号与行动。
在半导体领域中,前沿的晶圆加工技术是重中之重,如光刻显影技术,我们国家也一直在奋力追赶,引进了7nm工艺的ASML 光刻机,提升工艺制程的品质。
那么你知道在晶圆工艺制程中还有那些重要制程吗?元禄光电带大家了解紫外激光加工技术在硅晶圆工艺制程中的应用。
硅晶圆(图片源自网络)
紫外激光加工技术应用到硅晶圆中的设备有紫外激光切割机以及紫外激光打标机,分别对应的是晶圆划线以及晶圆打标。
硅晶圆激光切割
硅晶圆在制作过程中通常是制作成分成6/8/12/18寸等多规格晶圆,包含了大量的晶片,应用到半导体制程中需要将晶圆中的晶片切割成一个个小片,再封装到半导体元器件中。
这个工艺制程就需要用到紫外激光切割机,对晶圆进行划片,在裂片的方式加工。
传统的加工方式采用的是刀片的加工模式,而随着晶圆制程的改进,以及碳粉材料参杂的应用,晶圆的硬度越来越高,对加工的要求越来越高,紫外激光技术的应用很好的解决了这种缺陷,尤其是12寸晶圆加入碳粉后,硬度更高,紫外激光切割机的技术优势也就更明显。
武汉元禄光电技术有限公司
目前,紫外激光切割机应用到晶圆中采用的是高功率紫外激光器,利用物镜作为光斑聚焦镜,通过高密度高能量光束实现对晶圆的划线,在裂片方式加工。
激光作为先进加工技术的打标,其技术的扩展能力高,可随着晶圆加工工艺制程的提高,而提升激光切割技术工艺品质,可根据需求导入皮秒紫外激光切割机以及飞秒紫外激光切割机,未来紫外激光切割技术在晶圆切割领域将大有可为。
硅晶圆激光打标
随着工艺制程技术水平的提升,对晶圆品质的要求越来越高,因此对品质控制更加严格,为了方便追溯晶圆品质管理,在晶圆表面的空白区域或晶片表面标记处文字或二维码。
硅晶圆1*1mm二维码激光打标案例
在晶圆表面或晶片表面标记出的二维码和文字与我们常见的激光打标二维码没有本质的区别,不过加工的品质以及工艺的要求更加严格、也更加精细。
通常对二维码的大小要求在
1*1mm以下,字符大小要求在0.8mm以下,也就表明对激光打标设备提出来更高的要求。
为了满足在硅晶圆上的精细激光打标要求,元禄光电开发出了微细精密UV紫外激光打标技术,专门针对硅晶圆、晶片表面打标,这种技术采用相机定位,直线电机把控精度,小于10微米的超细聚焦光斑,能有效的满足加工工艺需求,并保证二维码的评级达到A级,满足设备读取,实现产品品质控制的目的。
硅晶圆的工艺制程是先进技术的代表,标志着一个国家的先进水平,想要不出现被卡脖子的现状,唯有发展自己的技术,才能跳出这个泥潭,作为激光从业者,元禄光电就致力于晶圆表面加工技术,做到极致,为国家的进步做贡献,实现国产化生产,提升国家竞争力。