钢板厚度检测作业指导书
钢板超声波检测复验作业指导书

钢板超声波检测复验作业指导书2.1适用范围:适用于板厚6-250mm的碳素钢、低合金钢板材的超声波检测。
奥氏体不锈钢、镍及镍合金板材及双相不锈钢的超声波检测,也可参照本条执行。
2.2检测工艺卡检测工艺卡的编制应与本检测作业指导书要求相符。
2.2.1超声波检测工艺卡由具有II级UT资质人员编制,2.2.2检测工艺卡由具有UTIII资质人员或UT检测责任师审核批准。
2.3检测器材2.3.1选用数字式超声波检测仪或A型脉冲反射式超声波检测仪,其工作频率范围为0.5-10MHz,水平线性误差不大于1%,垂直线性误差不大于5%。
2.3.2探头钢板厚度为6-20mm时,选用双晶直探头,公称频率为5MHz,晶片面积不少于150mm2,钢板厚度为20mm-40mm 时,选用单晶直探头,公称频率为5MHz,圆晶片直径为14-20mm,钢板厚度为40mm-250mm时,选用单晶直探头,公称频率为2.5MHz,圆晶片直径为20-25mm。
2.3.3试块a、用双晶直探头检测壁厚小于或等于20mm的钢板时,采用JB/T4730.3-2005规定的CBI标准试块。
b、用单晶直探头检测壁厚大于20mm的钢板时,采用JB/T4730.3-2005规定的CBII标准试块。
2.4耦合剂:浆糊或机油等透声性好,且不损伤检测表面的藕合剂。
2.5工艺参数2.5.1检测频率一般采用2.5MHz或5MHz,根据板厚选定。
2.5.2扫描时基线调节厚度小于或等于20mm时,应使荧光屏出现5次底波,厚度大于或等于20mm时,应是荧光屏出现至少2次底波。
2.6检测灵敏度:2.6.1钢板厚度小于或等于20mm时,用阶梯试块调节灵敏度,将试块上与工件等厚部位的第一次底波高度调整到满刻度的50%,再提高10dB作为检测灵敏度。
2.6.2壁厚大于20mm时,用平底孔试块调节灵敏度,将φ5平底孔第一次反射波波高调整到满刻度的50%作为检测灵敏度。
2.6.3壁厚不小于探头的3倍近场区时,也可取无缺陷的完好部位的第一次底波调节灵敏度,但其结果应与2.6.2条的要求一致。
SPHE钢种作业指导书)

1.钢种说明1.1产品用途:主要用于普通级酸洗钢板的生产。
1.2规格范围:厚度:0.8~3.0mm宽度:900~1600mm1.3热轧及冷轧以SPHE挂牌。
2.质量要求2.1熔炼成分(质量分数%)2.2机械性能2.3厚度及宽度允许偏差2.3.1根据需方要求,在供方满足生产要求的条件下按相应要求执行。
2.4 表面质量2.4.1钢带表面不得有裂纹、结疤、折叠、气泡和夹杂等对使用有害的缺陷,不得有分层。
2.4.2由于在连续生产过程中,钢带表面的局部缺陷不易发现和去除,因此,钢带允许带缺陷交货,但有缺陷的部分应不超过每卷总长度的6%3.炼钢工艺控制4.1铁水预处理铁水处理后S≤0.010%,铁水扒渣干净。
4.2 转炉控制4.2.1参考装入量控制:总装入量315t±1.5t,目标出钢量290t;4.2.2 转炉终点控制:出钢温度:1650~1680℃,C:0.03%~0.050%;4.2.3 出钢时间控制:出钢时间≥6分钟;4.2.4 脱氧合金化:出钢过程不进行脱氧合金化;4.3 精炼控制4.3.1RH精炼控制4.3.1.1真空控制:最高真空度≤2mbar(真空阀后压力),真空处理时间8-15min,纯脱气时间≥2min。
4.3.1.2 吹氧控制:进站温度≥1580℃,不吹氧,进站温度≤1570℃进行吹氧升温,1570-1580℃根据真空温降情况可选择吹氧升温;4.3.1.3合金化:RH真空处理,除补铝外,不进行合金化操作;4.3.1.4温度控制:钢水进站温度≥1580℃,出站温度≥1550℃。
4.3.2 LF精炼控制4.3.2.1精炼时间控制:精炼时间>40min;4.3.2.2温度控制:LF精炼出站按照1575-1590℃控制,根据连铸浇注断面以及钢包状况可适当进行调整。
4.3.2.3软吹及钙处理①软吹:一次软吹≥5min,二次软吹≥8min,软吹标准:渣面微动,钢水裸露直径≤500mm。
②钙处理标准:RH出站Ca控制标准20-30ppm。
板材探伤作业指导书
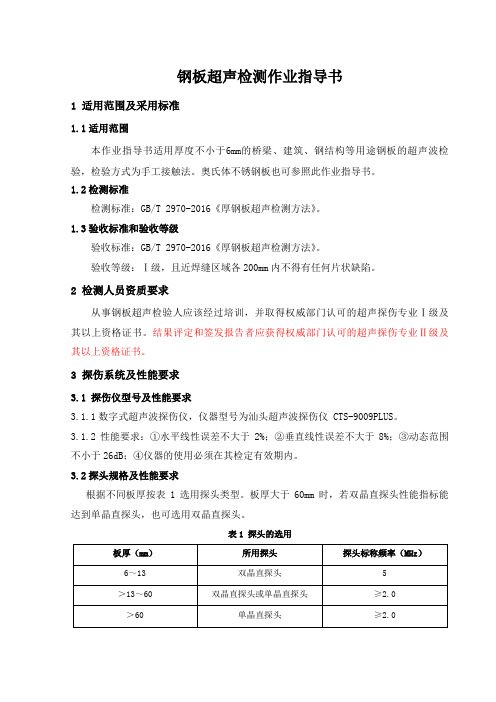
钢板超声检测作业指导书1 适用范围及采用标准1.1适用范围本作业指导书适用厚度不小于6mm的桥梁、建筑、钢结构等用途钢板的超声波检验,检验方式为手工接触法。
奥氏体不锈钢板也可参照此作业指导书。
1.2检测标准检测标准:GB/T 2970-2016《厚钢板超声检测方法》。
1.3验收标准和验收等级验收标准:GB/T 2970-2016《厚钢板超声检测方法》。
验收等级:Ⅰ级,且近焊缝区域各200mm内不得有任何片状缺陷。
2 检测人员资质要求从事钢板超声检验人应该经过培训,并取得权威部门认可的超声探伤专业Ⅰ级及其以上资格证书。
结果评定和签发报告者应获得权威部门认可的超声探伤专业Ⅱ级及其以上资格证书。
3 探伤系统及性能要求3.1 探伤仪型号及性能要求3.1.1数字式超声波探伤仪,仪器型号为汕头超声波探伤仪 CTS-9009PLUS。
3.1.2性能要求:①水平线性误差不大于2%;②垂直线性误差不大于8%;③动态范围不小于26dB;④仪器的使用必须在其检定有效期内。
3.2探头规格及性能要求根据不同板厚按表1选用探头类型。
板厚大于60mm时,若双晶直探头性能指标能达到单晶直探头,也可选用双晶直探头。
表1 探头的选用3.3试块3.3.1 采用双晶直探头检测厚度不大于60mm的钢板时,采用如图1所示的对比试块。
3.3.2 采用单晶直探头检测的钢板时,对比试块应符合图2、表2和表3的规定。
图1 板厚≤60mm的双晶直探头检测用对比试块(单位:mm)图2 单晶直探头检测用对比试块(垂直度a随试块厚度的变化见表3)(单位:mm)表2 单晶直探头用对比试块表3 垂直度a随试块厚度变化3.4 耦合剂化学浆糊或清水。
4 检测条件和方法4.1 检验时间和检测面4.1.1检验时间原则上在钢板加工完毕后进行,也可在轧制后进行。
4.1.2 检测面可以从钢板任一轧制面进行检验,被检表面应平整、光滑、厚度均匀,不应有液滴、油污、腐蚀和其他污物;应清理影响检验的氧化皮、腐蚀、油污等。
钢板超声波检测作业指导书

检
尺寸
测 距 离 - 波 幅 曲 线 1、 将探头置于试块有槽的一面,使主声束对准槽的宽边,找出第一个全跨距反射
的确定
的最大波幅,调整仪器,使该反射波的最大波幅为满刻度的 80%,在显示屏上
记录下该信号的位置。
2、 不改变仪器的调整状态,移动探头,得到第二个全跨距信号,并找出信号最大
反射波幅,在显示屏上记录下该信号的位置。
3、 板材探头在钢板边缘或剖口预定线两侧检测区域 1 、、最大单个缺陷指示长度 Lmax>30mm 2 、最大单个缺陷指示面积 S>100mm² 3 、在任意 1m 检测长度内,单个缺陷指示长度为 15mm<L≤30mm,评定范围
内缺陷个数>3 个。
编制(资格): X X X
(UT-Ⅱ) 2016 年 12 月 21 日
合格级别 II 级
耦合剂 化学浆糊
扫描调节
声程 1:2
检测时机
下料前
纵 探头型
2.5P30Z
试块型号 2#对比试块
波号
订正:
/
订正:3#对比试块
检 基准灵 测 敏度调
深度 85mm 的Φ5 平底孔反射波调至 80%
节
订正:在 3#对比试块上绘制Φ5 平底孔的距离-波幅曲线,并以此曲线作为基准灵敏度
扫查方 式1
3、 在显示屏上将上述内容所确定的点连成一直线,此线即为距离-波幅曲线。
S 1、 白点、裂纹等危害性缺陷, 不允许缺陷 2、 板材中部检测区域
①、最大单个缺陷指示面积 S>100mm² ②、在任意 1m×1m 检测面积内,单个缺陷指示面积为 50mm²<S≤100mm², 评定范围内缺陷个数>10 个
75 75
6000
钣金厂检验作业指导书

钣金厂检验作业指导书钣金厂检验作业指导书一、目的规范钣金结构件的检验标准,以使各过程的产品质量得以控制。
二、适用范围本标准适用于各种钣金结构件的检验,图纸和技术文件并同使用。
当有冲突时,以技术规范和客户要求为准。
三、引用标准本标准的尺寸未注单位皆为mm,未注公差按以下国标it13级执行gb/t1800.3-1998 极限与配合标准公差和基本偏差数值表gb/t1800.4 -1998 极限与配合标准公差等级和孔、轴的极限偏差表gb/1804-2000 一般公差未注公差的线性和角度尺寸的公差未注形位公差按gb/t1184 ╟1996 形状和位置公差未注公差值执行。
四、原材料检验标准1.金属材料1.1钣材厚度及质量应符合国标,采用的钣材需出示性能测试报告及厂商明。
1.2材料外观:平整无锈迹,无开裂与变形。
1.3 尺寸:按图纸或技术要求执行,本司未有的按现行国标执行。
2.塑粉2.1塑粉整批来料一致性良好,有出厂证明与检验报告,包含粉号、色号以及各项检验参数。
2.2试用后符合产品要求(包括颜色、光泽、流平性、附着力等)。
3通用五金件、紧固件3.1外观:表面无绣迹、无毛刺批锋,整批来料外观一致性良好。
3.2尺寸:按图纸与国标要求,重要尺寸零缺陷。
3.3性能:试装配与使用性能符合产品要求。
五、工序质量检验标准1.冲裁检验标准1.1对有可能造成伤害的尖角、棱边、粗糙要做去除毛刺处理。
1.2图纸中未明确标明之尖角(除特别注明外)均为r1.5。
1.3冲压加工所产生的毛刺,对于门板、面板等外露可见面应无明显凸起、凹陷、粗糙不平、划伤、锈蚀等缺陷。
1.4毛刺:冲裁后毛刺高l≤5%t(t为板厚)。
1.5划伤、刀痕:以用手触摸不刮手为合格,应≤0.1。
1.6平面公差度要求见表一。
附表一、平面度公差要求表面尺寸(mm)3以下大于3小于30大于30小于315大于315小于1000大于1000小于2000大于2000小于31502.折弯检验标准2.1 毛刺:折弯后挤出毛刺高l≤10%t(t为板厚)。
防火涂层厚度检测作业指导书

防火涂层厚度检测作业指导书
一、检测前准备。
1.检测仪器:钢板厚度计、磁力涂层厚度计等。
2.选择检测点:对于涂层较厚的区域,应均匀选择检测点,重点关注尖锐部位、角落等易受损的区域。
3.检测仪器校准:确认检测仪器是否已经校准,保证准确性。
二、检测操作步骤。
1.准备工作。
提前将被检测的区域清理干净,清除油污、杂质等物质,保证检测时的准确性。
2.检测钢板厚度。
使用钢板厚度计,首先在待检测的区域上沾上润滑油,然后将钢板厚度计抵住钢板进行测试。
钢板厚度计的使用方法:将弹性腕一端固定在指针位置,随后按压到待测物体上,释放手指使弹性腕回缩,观察指针指向的值,即为测量值。
3.检测磁力涂层厚度。
使用磁力涂层厚度计测试磁性涂层,方法为将涂层厚度计置于被检测的区域上,随后将探头贴紧测量表面。
然后从表面撤离测量器,在按下磁力涂层厚度计的“测量”键,即可得出测量结果。
4.记录数据和评估结果。
将测得的数据记录下来,根据防火涂层厚度的要求,评估结果,进行整体的防火涂层管理策略。
三、注意事项。
1.检测前应将被检测区域清洁干净,确保测试结果准确。
2.在使用仪器之前,要想仔细阅读使用说明书,并根据相关要求进行校准。
3.多次测量同一点位并取平均值,可提高测量的准确性。
4.使用过程中,需要注意安全。
如果涂层很厚,应该避免下沉,防止检测仪器在被损坏。
5.检测结果不符合要求或者结果存在问题,应该及时向相关部门或领导反映问题,并采取相应的措施。
冷轧钢板检验作业指导书word格式
±0.09
±0.09
±0.11
1.10~1.20
±0.09
±0.10
±0.10
±0.12
1.20~1.40
±0.10
±0.12
±0.11
±0.14
1.40~1.50
±0.11
±0.13
±0.12
±0.15
1.50~1.80
±0.12
±0.14
±0.14
±0.16
1.80~2.00
±0.13
±0.15
±0.15
±0.17
2.00~2.50
±0.14
±0.17
±0.16
±0.18
2.50~3.00
±0.16
±0.19
±0.18
±0.20
10.1.2钢板的宽度允许偏差应符合表3的规定
表3:钢板的宽度允许偏差单位:mm
公称宽度
宽度允许偏差
≤1000
+6
>1000
+10
10.1.3钢板的长度允许偏差应符合表4的规定
4.5复验
当某一项试验结果不符合标准规定时,应从同一批钢板中任取双倍数量的试样进行不合格项目的复验(白点除外)。复验结果均应符合标准,否则为不合格,则整批不得交货。
5、包装
表1:冷轧薄钢板的包装和标志
品
种
包装
包装材料
箱重(t)
标志
冷
轧
钢
板
1、用垫木或其他材料组成托架;
2、用气相防锈纸(不锈钢高温合金等推荐采用)、塑料薄膜依次包裹;
A、表6所列的不平度适用于抗拉强度σb下限不大于485N/mm2(50Kgf/ mm2)的钢板,对于抗拉强度σb下限大于485N/mm2(50Kgf/ mm2),但不大于585N/mm2(60Kgf/ mm2)的钢板不平度的最大值允许比表规定值增加30%。对于抗拉强度σb下限大于585N/mm2(60Kgf/ mm2)的钢板的不平度最大值允许比表规定值提高50%。
(完整版)钢筋工程作业指导书
钢筋工程作业指导书一、施工准备(一)、材料准备:1、在确保材料及时供应的情况下,根据施工进度和材料计划分期分批进场。
2、材料进场必须有合格证,严禁不合格的材料进场。
材料进场后按规范要求取样送到具有相应资质的试验室进行冷拉、冷弯试验,试验合格才可用于主体工程结构。
3、本工程所用所有钢筋均采用现场加工的方式,然后运到绑扎部位进行绑扎。
(二)、技术准备:(三)、人员准备:(四)、作业条件:1 、加工配制好的钢筋进场后,应检查是否有出厂证明、复试报告,并按施工平面图中指定位置,按规格、部位、编号分别加垫木堆放。
2、钢筋绑扎前,应检查有无锈蚀现象,除锈之后再运至绑扎部位。
3、熟悉图纸,按设计要求检查已加工好的钢筋规格、形状、数量是否正确。
4、做好抄平放线工作注明水平标高,弹柱、墙的外皮尺寸线。
5、根据弹好的外皮尺寸线,检查下层预留搭接钢筋的位置、数量、长度,如不符合要求时,应进行处理。
绑扎前先整理调直下层伸出的搭接筋,并将锈皮、水泥浆等污垢清除干净。
6 、根据标高检查下层伸出搭接筋处的混凝土表面标高(柱顶、墙顶)是否符合图纸要求,如有松散不实之处要剔凿,清理干净。
7、模板安装完办理预检,并清理净模内木屑及杂物。
8、按要求搭好脚手架。
9、根据设计图纸要求和工艺标准向班组进行技术交底。
四、施工工艺(一)、钢筋进场及堆放钢筋的进场必须根据工程进度有计划地运进施工现场,由专业工长根据项目计划进度和实际情况,将材料规格、数量上报项目材料组,由项目材料组联系供货商将材料运进现场。
钢筋运至施工现场后,要严格按批分等级、牌号、直径、长度挂牌堆放,所有进场的钢筋都必须有出厂证明书和检验报告,每捆(盘)钢筋必须有标牌,钢筋设专人管理并建立严格的验收,保管与领取的管理制度。
钢筋在指定场地堆放整齐,并将各规格、型号加以标识,分组挂牌。
存放钢筋场地为现浇混凝土地坪,并设有排水坡度。
堆放时,钢筋下面要垫以垫木,离地面不得少于 20cm,以防钢筋锈蚀和污染。
钢材的力学性能试验作业指导书
钢材的力学性能试验作业指导书1、钢材标准、试验方法标准、检验项目及取样:1.1钢材应有出厂质量证明书或检验报告单,每批(捆)钢材均应有标牌,进厂时应按同一牌号、同一炉罐(批)号、同一规格、同一交货状态分批进行验收,验收内容包括查对标牌和外观检查,并按有关标准的规定抽取试样做力学性能试验,合格后方可使用。
1.2检验规则1.2.1钢板的检查、验收、复检与判定:应按GB/T247《钢板和钢带检验、包装、标志及质量证明书的一般规定》执行,每批钢板应是同一牌号、同一炉罐、同一规格、同一交货状态。
1.2.2从每批钢板中选取一张进行力学性能试验,取样应按GB/T2975《钢及钢产品力学性能试验取样位置及试样制备》执行,先取3个试样进行抗拉强度、弯曲和伸长率的试验,结果如有一项不合格,再从末检验过的钢板中抽取一张进行复检,如仍有一项不合格,则该批即判定为不合格。
如试验合格再抽取一张进行复检合格则该批判定为合格。
1.2.3型钢的检验则应按GB2102《型钢验收、包装、标志及质量证明书的一般规定》执行,型钢按GB/T2975标准取样,从每根型钢中取3个试样进行抗拉强度、弯曲和伸长率的试验,当有一项试验结果不符合规定时,应另取双倍数量的试样重做各项试验,当仍有一个试样不合格时,则该批型钢为不合格。
双倍数量的试样重做各项试验均合格则该批判定为合格。
2、钢材力学性能试验方法:2.1收样:2.1.1样品挂牌编号,送检单编号。
2.1.2测量样品尺寸。
2.1.3技术标准:必须符合GB/T228《金属材料室温拉伸试验方法》与GB/T232《金属弯曲试验方法》。
2.2拉伸试验:试验目的:试验测定钢材的屈服强度、抗拉强度、伸长率等,是为了评定钢材质量。
2.3仪器设备:2.3.1 WDW-100微机控制电子万能试验机,示值误差在±1%,达到试验机检定的1级精度;有加载调速装置;有数据记录或显示装置;由计量部门定期进行检定。
2.3.2标点划分器、游标卡尺2.4试验步骤:钢材拉伸与弯曲试验框图2.5性能的测定:2.5.1屈服强度的测定:对有显著屈服现象的钢材应测定其屈服强度。
试验检测作业指导书
试验检测作业指导书(一)测试前的准备工作1.工程名称及设计、施工、监理(或监督)和建设单位名称。
2.结构或构件名称、外形尺寸、数量及混凝土强度等级。
3.水泥品种、强度等级、安定性、厂名、砂石种类、粒径、外加剂或掺合料品种、掺量、混凝土配合比等。
4.施工时材料计量情况、模板类型、浇筑、养护情况及成型日期。
5.必要的设计图纸和施工纪录。
6.结构或构件存在的质量问题,混凝土试块抗压报告等。
1.按单个构件检测时,应在构件上均匀布置测区,且不少于10个;2.当对同批构件抽样检测时,构件抽样数应不少于同批构件的30%,且不少于4件,每个构件测区数不少于10个;3.对长度小于或等于2m的构件,其测区数量可适当减少,但不应少于3个。
4.测区的布置应在构件混凝土浇筑方向的侧面;5.测区应均匀分布,相邻两测区间距不宜大于2m,,测区宜避开钢筋密集区和预埋件。
6.测区尺寸为200mm某200mm,相对的两个200mm某200mm方块应视为一个测区。
7.测试面应清洁、平整、干燥,不应有接缝、饰面层、浮浆和油垢,并避开蜂窝、麻面部位,必要时可用砂轮片清除杂物和磨平不平整处,并擦净残留粉尘。
回弹测试、数据计算及修正均与回弹法测试混凝土强度相同。
(四)操作的注意事项1.操作回弹仪时,回弹仪的轴线始终应与测试面垂直。
2.超声声时测量时,换能器与混凝土之间的良好耦合是十分必要的。
3.同批构件的条件是:混凝土强度等级相同;混凝土原材料、配合比、成型工艺、养护条件及龄期基本相同;构件种类相同;在施工阶段所处状态相同。
(五)超声声速值的测量与计算1.超声声时值的测量超声测点应布置在回弹测试的同一测区呢,在每个测区内的相对测试面上,应布置三个测点。
应保证换能器与混凝土耦合良好,且发射和接受换能器的轴线应在同宜直线上。
浇筑面超声测点图2-1-1超声测点布置2.声速值计算声速值按照下式计算:vltmtm式中:v-测区声速值(km/);l-超声测距(mm);(t1t2t3)3。
- 1、下载文档前请自行甄别文档内容的完整性,平台不提供额外的编辑、内容补充、找答案等附加服务。
- 2、"仅部分预览"的文档,不可在线预览部分如存在完整性等问题,可反馈申请退款(可完整预览的文档不适用该条件!)。
- 3、如文档侵犯您的权益,请联系客服反馈,我们会尽快为您处理(人工客服工作时间:9:00-18:30)。
一、编制目的
为保证钢结构钢板厚度检测项目的顺利开展,确保检测工作的规范性,特制定本作业指导书。
二、适用范围
本作业指导书适用于钢结构钢板厚度检测项目。
三、引用标准
1、《建筑结构检测技术标准》(GB/T 50344-2004);
2、《钢结构施工质量验收规范》(GB 50205-2001);
3、《热轧钢板和钢带的尺寸、外形、重量及允许偏差》
(GB/T709-2006)
四、检验仪器设备
1、TT110+42513420超声波测厚仪
五、操作程序
1、在承接检测时应向委托方索取工程图纸及相关技术资料。
2、检测人员应根据技术资料要求,确定检测标准、检测部位,及检测等级、检测比例、合格级别。
3、清洁表面,测量前,应清除表面上的任何附着物质,如尘土、油脂及腐蚀物质等覆盖层物质。
4、检查电源
5、将测头置于开放空间,按一下“on”键,开机。
●开机后,出现“5900m/s”可以正常使用,反之则应校准仪器。
6、仪器的校准
给仪器标准块上涂抹耦合剂,使探头与标准块垂直接触,轻按住探头,仪器显示〈4.0mm〉,即完成探头校准。
7、测量
首先在钢板测试面位置涂抹耦合剂,然后迅速将探头与测试面垂直地接触并轻轻压住,屏幕显示测量值,提起测头可进行下次测量;如果在测量中测头放置不稳,显示一个明显的可疑值,可挪动探头或左右旋转探头,最后选取最小测量数值。
每个构件检测5处,每处测量三次,取平均值。
8、关机
在无任何操作的情况下,大约2~3min后仪器自动关机。
六、原始记录及报告
1、原始数据记录在记录表格中,并由现场检测人员签字。
2、检测报告内容必须包括必要的检测信息,符合标准、规范、规程的要求,并与相应的原始记录一致。
检测报告主要包括:标题、检测单位的名称、报告唯一性编号和每页的标识、委托单位名称、工程名称、所用检测方法的标识或说明、检测样品的状态描述和编号、委托日期、检测日期、报告日期、检测结果、检测人员、报告编写人员、报告审核人员以及批准人的签名等。
3、如检测报告的内容是有关复检检测的内容,检测报告上应有明确的标记。
凡分包项目的检测报告可在备注栏中注明必要的说明。