质量风险管理工具PHA初步危害分析
危险有害因素识别原则:PHA、安全检查表等十大工具

危险有害因素识别原则:PHA、安全检查表等十大工具危险、有害因素的识别原则在工业生产和工程项目中,危险和有害因素是导致事故和职业病的主要原因。
为了预防这些风险,需要对危险和有害因素进行识别和评估。
以下是常见的危险、有害因素的识别原则:1.预先危险性分析(Preliminary Hazard Analysis,PHA)2.PHA是一种在活动开始之前对可能的危险和有害因素进行识别、评估和分类的过程。
它主要用于初步筛选可能存在的高风险操作或设备。
3.安全检查表(Safety Checklist)4.安全检查表是一种用于识别潜在危险的标准化工具,通常由一系列问题或检查项组成,旨在评估特定设备、系统或操作的安全性。
5.故障类型及影响分析(Failure Modes and Effects Analysis,FMEA)6.FMEA是一种系统化的故障分析工具,用于识别系统或过程中潜在的故障模式,并评估其对系统性能的影响。
7.故障树分析(Fault Tree Analysis,FTA)8.FTA是一种逻辑图解方法,用于识别和分析系统中可能的故障路径。
它通过将高级故障(顶层)分解为更低级(中间和底级)的故障类型来识别潜在的危险因素。
9.事件树分析(Event Tree Analysis,ETA)10.ETA是一种系统化的风险分析工具,用于识别特定事件链可能导致的事故后果。
它通过从初始事件开始,分析并识别可能产生的后续事件来识别潜在的危险因素。
11.作业危害分析(Job Hazard Analysis,JHA)12.JHA是一种针对特定作业任务进行的风险评估方法,用于识别作业过程中可能面临的危害因素。
13.定量风险评估(Quantitative Risk Assessment,QRA)14.QRA是一种使用数学模型对危险因素进行量化和评估的方法,以确定其可能导致的损失或影响。
15.定性风险评估(Qualitative Risk Assessment,QRA)16.定性风险评估是一种基于经验和判断的方法,用于评估危险因素的性质、严重程度和可能性。
工艺危害分析PHA---易安-安全从业-安全生产-安全

工艺危害分析(PHA )工艺危害分析是PSM 的核心要素,它是有组织的、系统的对工艺装置或设施进行危害辨识,为消除和减少工艺过程中的危害、减轻事故后果提供必要的决策依据。
工艺危害分析关注设备、仪表、公用工程、人为因素及外部因素对于工艺过程的影响,着重分析着火、爆炸、有毒物泄漏和危险化学品泄漏的原因和后果。
工艺危害分析方法有很多种,PSM 推荐的危害分析方法有:1)如果……,会怎么样?”提问法;2)安全检查表;3)“如果…… ,会怎么样?”提问法结合安全检查表;4)危险性与可操作性研究;5)故障模式与后果分析;6)故障树分析;7)或者等效的其他方法。
工艺危害分析是件很耗费时间的工作,但是意义重大。
工厂需要根据自身工艺的特点选择适当的危害分析方法。
对于化工厂和石化工厂,目前最普遍采用的危害分析方法是HAZOP ,同时辅助采用安全检查表法弥补HAZOP 方法的某些不足。
HAZOP 是20 世纪70 年代由帝国化学公司(ICI)发明的一种定性危害分析方法,也是针对工艺过程最系统、有效的危害分析方法之一。
在进行工程设计时,主要是依靠各种标准、规范、设计指南以及设计人员的经验和知识来实现工艺系统的安全与可靠性。
上述标准、规范或设计指南主要反映的是“正常工况下工艺系统需要满足的情况。
由于设备故障、人为错误或外部影响等原因,工艺系统在运行过程中可能偏离正常工况,导致工艺安全事故。
此外,在项目工期紧张的情况下,设计人员的压力很大,容易犯错误,需要在工艺设计阶段就进行周全的考虑。
HAZOP 可以应用于不同行业、不同规模和复杂程度各异的工艺系统,只要是包含工艺流程的系统。
对新建项目的工艺设计、现有工艺系统的变更以及当前正在运行的装置都可以应用。
利用HAZOP 方法进行危害分析是有组织的头脑风暴活动,通常需要由一个包括不同专业人员所组成的分析小组来完成。
将复杂的工艺系统划分成不同的部分,称为节点(Node),然后针对每个节点进行具体的分析。
预先危险性分析报告(PHA)

预先危险性分析(PHA)(一)定义预先危险性分析(PHA)也可称为危险性预先分析,是在每项工程、活动之前(如设计、施工、生产之前),或技术改造之后(即制定操作规程前和使用新工艺等情况之后),对系统存在的危险因素类型、来源、出现条件、导致事故的后果以及有关防范措施等作一概略分析的方法。
通过预先危险性分析,力求达到4项基本目标:(1)大体识别与系统有关的一切主要危险、危害。
在初始识别中暂不考虑事故发生的概率;(2)鉴别产生危害的原因;(3)假设危害确实出现,估计和鉴别对人体及系统的影响;(4)将已经识别的危险、危害分级,并提出消除或控制危险性的措施。
分级标准如下:工级――安全的,不至于造成人员伤害和系统损坏;Ⅱ级――临界的,不会造成人员伤害和主要系统的损坏,并且可能排除和控制;Ⅲ级――危险的,会造成人员伤害和主要系统损坏,为了人员和系统安全,需立即采取措施;Ⅳ级――破坏性的,会造成人员死亡或众多伤残,及系统报废。
(二)分析步骤(见图9―6)(三)基本危害的确定系统中可能遇到的一些基本危害有:(1)火灾;(2)爆炸;(3)有毒气体或蒸气、窒息性气体不可控溢出;(4)腐蚀性液体的不可控溢出;(5)有毒物质不加控制地放置;(6)噪声、粉尘、放射性物质、高温、低温等危害;(7)电击、淹溺、高处坠落、物体打击等危险。
(四)预先危险性分析表基本格式预先危险性分析的结果一般采用表格的形式。
表格的格式和内容可根据实际情况确定。
表9―7、表9―8为两种基本的格式。
(五)应用示例例1某乙烯厂环氧乙烷/乙二醇(EO/EG)在役装置安全评价预先危险性分析按表9―8的形式,对EO/EG装置进行预先危险性分析,分析结果见表9―9。
通过预先危险性分析可以得知,本装置存在着火灾、爆炸、中毒、高温灼伤的危险、危害因素,但主要危险为火灾、爆炸,其危险等级为Ⅳ级(破坏性的)。
引发火灾爆炸的主要因素是环氧乙烷、乙二醇等物料故障泄漏。
例2某新建化工码头安全预评价预先危险性分析对某新建化工码头项目进行劳动安全卫生预评价,对码头装卸作业进行预先危险性分析并提出了防范措施,分析结果见表9―10。
质量风险管理工具
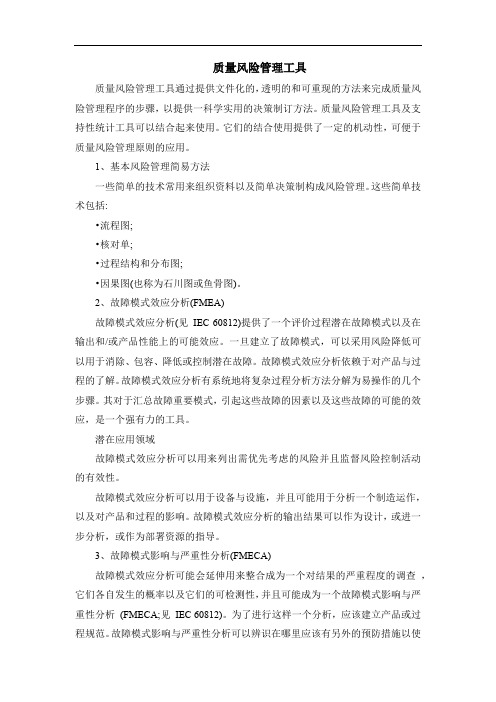
质量风险管理工具质量风险管理工具通过提供文件化的,透明的和可重现的方法来完成质量风险管理程序的步骤,以提供一科学实用的决策制订方法。
质量风险管理工具及支持性统计工具可以结合起来使用。
它们的结合使用提供了一定的机动性,可便于质量风险管理原则的应用。
1、基本风险管理简易方法一些简单的技术常用来组织资料以及简单决策制构成风险管理。
这些简单技术包括:•流程图;•核对单;•过程结构和分布图;•因果图(也称为石川图或鱼骨图)。
2、故障模式效应分析(FMEA)故障模式效应分析(见IEC 60812)提供了一个评价过程潜在故障模式以及在输出和/或产品性能上的可能效应。
一旦建立了故障模式,可以采用风险降低可以用于消除、包容、降低或控制潜在故障。
故障模式效应分析依赖于对产品与过程的了解。
故障模式效应分析有系统地将复杂过程分析方法分解为易操作的几个步骤。
其对于汇总故障重要模式,引起这些故障的因素以及这些故障的可能的效应,是一个强有力的工具。
潜在应用领域故障模式效应分析可以用来列出需优先考虑的风险并且监督风险控制活动的有效性。
故障模式效应分析可以用于设备与设施,并且可能用于分析一个制造运作,以及对产品和过程的影响。
故障模式效应分析的输出结果可以作为设计,或进一步分析,或作为部署资源的指导。
3、故障模式影响与严重性分析(FMECA)故障模式效应分析可能会延伸用来整合成为一个对结果的严重程度的调查,它们各自发生的概率以及它们的可检测性,并且可能成为一个故障模式影响与严重性分析(FMECA;见IEC 60812)。
为了进行这样一个分析,应该建立产品或过程规范。
故障模式影响与严重性分析可以辨识在哪里应该有另外的预防措施以使风险昀小化。
潜在应用领域故障模式影响与严重性分析在制药业界里的应用昀可能是用于与制造过程相关的故障以及风险;然而,它并不局限于这方面的应用。
故障模式影响与严重性分析的输出是对于每个故障模式给出一个相对风险的“分值”,其被用于在风险基础上对这些模式进行排序。
化工企业预先危险性PHA、故障模式和影响FMEA、风险矩阵法LS、作业条件危险性分析评价法(LEC)

作业条件危险性分析评价法(简称LEC)。L(likelihood,事故发生的可能性)、E(exposure,人员暴 露于危险环境中的频繁程度)和C(consequence,一旦发生事故可能造成的后果)。给三种因素的不同等级 分别 确定 不同 的分 值, 再以 三个分 值的 乘积 D(danger,危 险性 )来评 价作 业条 件危 险性 的大 小, 即:D=L×E×C。D值越大,说明该作业活动危险性大、风险大。
主要功能包括: ——识别与系统有关的一切主要危害; ——鉴别产生危险的原因; ——估计事故出现后产生的后果; ——提出消除或控制危险性的防范措施。 E.3 预先危险性分析评价
分析评价步骤如下: a) 危害辨识; b) 通过经验判断、技术诊断等方法,查找系统中存在的危险、有害因素; c) 确定可能事故类型; d) 根据过去的经验教训,分析危险、有害因素对系统的影响,分析事故的可能类型; e) 针对已确定的危险、有害因素,制定预先危险性分析表; f) 确定危险、有害因素的危害等级,按危害等级排定次序,以便按计划处理; g) 制定预防事故发生的安全对策措施。
1
能发生事故或事件。
表 G.2 事件后果严重性(S)判别准则
等级 5 4 3 2
法律、法规 及其他要求
人员
直接经济损失
停工
企业形象
违反法律、法规和标准 死亡
100万元以上
部分装置(>2 套)或 重大国际影响 设备
潜在违反法规和标准
丧失劳动能力 50万元以上
不符合上级公司或行业 截肢、骨折、
的安全方针、制度、规定 听力丧失、慢 1万元以上
风险值 20-25 15-16 9-12
风险等级
应采取的行动/控制措施
工艺危害分析(PHA)管理规范

工艺危害分析(PHA)管理规范工艺危害分析 (PHA) 管理规范是制定和管理各类工艺危害分析活动的指导方针。
PHA 是一种系统性的评估方法,用于识别和评估工艺过程中可能产生的安全和环境风险,以及采取适当的控制措施进行风险管理。
以下是一些制定和管理 PHA 的规范和步骤:1. PHA 管理团队的组建:应该由具备相关专业知识和经验的成员组成,包括工艺工程师、安全专家、环境专家和操作人员等。
团队应该具备全面和多样化的技能,以便全面评估和分析工艺风险。
2. PHA 分析方法的选择:根据工艺的复杂性和特点,选择适合的分析方法,如哈萨德和危险分析关键控制点 (Hazard Analysis and Critical Control Point, HACCP)、故障模式与影响分析 (Failure Mode and Effects Analysis, FMEA)、事件树分析(Event Tree Analysis, ETA) 等。
选择的方法应满足所需的目标和要求。
3. 工艺信息收集和整理:收集和整理与工艺相关的各类信息,如流程图、工艺参数、物料安全数据表 (Material Safety Data Sheets, MSDS)、工艺控制系统信息等。
这些信息对于准确评估工艺风险和制定控制措施至关重要。
4. 风险识别和评估:通过分析和讨论工艺过程中的各个步骤和环节,识别所有可能导致事故和危害的因素。
对每个识别出来的风险进行定量或定性评估,包括潜在的影响、概率和风险等级。
评估应基于可靠性和可操作性,确保风险分析结果的准确性和可行性。
5. 风险控制措施的制定:根据风险评估结果,制定风险控制措施和应急预案。
风险控制措施应酌情考虑使用工程、管理和行为控制方法,并与操作规程和标准操作程序相结合。
应急预案应考虑事故应对、紧急撤离和事故恢复等方面。
6. PHA 报告和记录管理:编写详细的 PHA 报告,记录分析过程、评估结果和制定的控制措施。
预先风险性分析PHA

储罐破裂与 工艺设备的 连接过程中 发生泄漏
中毒
3 4 12 建立检查规程
※ 预先危险分析举例(氯气干燥岗位 危险性分析)
危险危 害因素
触发事件
现象
原因事件
事故情况
结果
危险 等级
措施
硫酸泄 1.设备、阀 硫酸 1.地坪及周 1.地坪周围 人 员 漏 门 、 管 道 溢出 边 设 备 不 设 备 受 腐 伤 害
级
有气 安全阀不动 爆炸 泡作
伤亡、 3 损失
火咀熄灭, 燃气 不打火花 煤气线开 漏
燃气爆 伤亡、 3
炸
损失
排气口关 CO充 人在室内 CO中毒 伤亡 2
闭
满
措施
装爆破片、定期检 查安全阀 火源燃气线联锁, 定期检查通风,气 体报警器 CO检测器、通风设 施
排气口关 闭
…
排气 火嘴连续燃 火灾 口着 烧 火
2 5 10 连通阀平时保持关闭状态, 并上锁,由站长负责保管
2
5
10
完善卸油操作规程,悬挂 在作业现场
2 4 8 加油前再次询问顾客
热水器PHA分析记录表
序 危险 号 因素
1 水压 高
2 燃气
3 燃烧 不完 全
4 排气 口高 温
……
触发事件
燃气连续 燃烧
现象 事故原因分 危害事 结果 风
析
件
险
等
案例
氯乙 烯 单 体 生 产流 程 图
乙烯循环
焚烧 炉
氯化
二氯乙
VCM 产 品
乙 烯
反应 器
EDC
烯
VCM 分离器
(EDC)
裂解
质量风险管理常用工具的概念和模板

质量风险管理常用工具的概念和应用模板(一)预先危害分析:1、概念:1.1.严重性的定义和排列:严重,主要,次要,可忽略;1.2.发生频次(可能性)的定义和排列:频繁,可能,偶尔,罕见;1.3.风险的水平和定义:高:此风险必须降低;中:此风险必须适当地降低至尽可能低;低:考虑收益和支出,降低至尽可能低;微小:通常可以接受的风险。
2.初步危害分析的矩阵表:xxxxxxx的质量风险管理一、文件编号:FG-CFSS-002二、目的:三、组织:质量风险管理小组组长:组员:四、法条依据:GMPxxxxxxx条。
五、管理工具:预先危害分析(PHA)。
六、风险分析表:七、沟通:意见书面通知总经理和设备工程部,建议召开专题研讨会。
八、审核:进行中接受:不接受:整改后接受:十、资料保存地点:本资料输出二份,总经理一份,质保部一份,模板资料保存于质保部电脑软件中。
4、潜在应用领域:4.1.当实际情况不允许使用更进一步的技术来分析现存系统或对危害源进行有限排序时,可应用PHA。
4.2.它也可被用于产品、工艺和设备的设计,也可用于评估从某一类别的产品,到某一级别的产品,直至某种产品的危害种类。
4.3.PHA最长应用于项目的早期开发阶段,此时在设计的细节以及运行程序方面的信息比较缺乏,因此,它经常成为进一步分析的基石。
(二)失败模式效果分析:1、概念:1.1.风险得分:严重性×可能性×可测定性=风险得分1.2.失效模式效果分析图:失效模式效果分析评分(3级法)1.3.失效模式效果分析的矩阵图:(3级法)失效模式效果分析矩阵2、失败模式效果分析模板:xxxxxx的质量风险管理一、文件编号:FG-WL-01-001二、目的:对物料管理的目的、范围、内容进行合理的规定,避免遗漏、混淆和差错。
三、组织:质量风险管理小组组长:组员:四、法条依据:GMP 第xxx条。
五、质量风险管理工具:失效模式及影响分析(FMEA)。
- 1、下载文档前请自行甄别文档内容的完整性,平台不提供额外的编辑、内容补充、找答案等附加服务。
- 2、"仅部分预览"的文档,不可在线预览部分如存在完整性等问题,可反馈申请退款(可完整预览的文档不适用该条件!)。
- 3、如文档侵犯您的权益,请联系客服反馈,我们会尽快为您处理(人工客服工作时间:9:00-18:30)。
1 2 3 4 5 严重性 1 2 3 4 5
严重——死亡或严重的对外 影响 高 ——损工事故或现场发生 泄漏 中——第一急救事故或泄漏 低——小伤害或局部漏洞 无
XXX 产品
如果(What Ifs) 投加 XXX、活性灰(5kg)产生粉尘 后果 1.职业伤害 2.静电爆炸 S 1 L 3 RR 3 建议改进措施(Recommendation) 1.局布排风 2.先投加固体,再投加液体 3.人孔上面做一个不锈钢漏斗,并接地 1.使用气动桶泵 2.控制抽料速度(小于7m/s),用金属管(接地) 3.用水验证抽料速度与时间,并写入操作规程 1.职业暴露 2.静电燃爆 3.管道脱落 4.桶泵不防爆 4.桶泵和抽料(专用)管使用后存放在工具间 1 3 3 5.搅拌前静置,惰化,桶用静电接地夹接地 6.加料前用氮气置换2次,恢复常压(真空表0) 7.甲醇桶内是否喷漆,甲醇水分0.1以下(质量) 8.局布排风; 9.快速接头 10.使用 J 型管 1.产生 HCl 酸雾 2.职业暴露 3.静电燃爆 1.产生 HCl 酸雾 2.职业暴露 3.静电燃爆 1.使用桶架+鸭嘴阀+车轮或者换小包装乙酰氯 2 3 6 2.加料漏斗每次使用后清洗(质量) 3.分料间使用 DFB 1.滴加完后使用甲醇冲洗 1 3 3 2.配戴全面具、防化手套 3..漏斗使用玻璃钢,加盖 责任人 工程 生产 工程 工程 生产 生产 生产 生产 生产 质量 工程 工程 工程 工程 生产 工程 生产 生产 工程 2 4 7 2 4 7 2 4 7 时间结点 S 2 L 4 RR 7
抽取甲醇(插桶泵)
乙酰氯分料
投加乙酰氯(1.8kg 左右)
Байду номын сангаас
注: 1 2 3 4 5
紫色背景需要修改 P&ID 图; 风险大小为定性指标,仅供参考; 责任人只注明了部门,没有指名具体姓名,请各部门第一负责人分配责任人; 时间节点需要在 XXX 项目确定之后才能确定; 每项工作中可能涉及不止一个部门,由责任人协调其他部门完成。 风险评分矩阵表(仅供参考)
L S
1 1 2 3 4 5
2 2 4 6 7 8
3 3 6 7 8 9 说明
4 4 7 8 9 10
5 5 8 9 10 10 可能性 1 2 3 4 5 说明 极高——前 12 个月内发生过 高 ——前三年内发生过 中——前十年内发生过 低—— 不太可能发生 无 注: S——严重性; L——可能性。 RR——风险等级